基于有限元分析的发动机缸体压铸模具设计【毕业论文(含任务书、外文翻译)】
基于Pro/ENGINEER的缸体侧盖压铸模设计

图3 开模 图
模 具 的 分模 是 模 具 成 型部 分
C DC A /AM与制造业信息化 ・ 0 7 2 0 年第9 45 期
维普资讯
维普资讯
E G N E 中,设置收缩率 的方式有 N I ER
事 先加 以排 除。
2产 品 的 三 维 造 型 .
缸 体侧 盖 为 铝合 金 压 铸 件 ,
由于要求零件 有很好 的密封性 ,所 两种 :按尺寸和按 比例 。这里选择 以 对底 面 的平 行 度 ,对 于筋 与槽 按 比例 方 式 ,设 置 收 缩率 公 式 : 的 尺寸 精 度有 很 高 的要 求 。利 用 S I R = + ,在 收缩率 中填入00 6 .0 : P oE G N E 软件零件设 计模块 中 r/ N I E R
但不大 于00 ml .5 I l 。推杆在推 杆 固定板
中应能灵 活转动 ,但轴 向间 隙不大 于
0 1 mm: .O
( ) 具 所 有 活 动 部件 ,应 保 证 3模 位置 准确 、动作 可靠 ,不得 有歪斜和
模具模 块 中 ,利 用零 件相 关的特性 直 接做模具 元件 ,其作 法于推杆 相似 , 复位杆安装如 图1 所示 。 8
一
图1 8复位杆安装图
三 、总体装配技术要求
() 1在分型 面上 ,定模 、动模镶件 平 面应分别 与定模 框 、动模 框齐 平或 允许略高 ,但高 出量在00 N .O m .5 O1 m 范 围内 ( ) 杆 、复 位 杆 应 分 别 与分 型 2推 面齐 平 ,推 杆允许 凸 出型 面 ,但 不大 于 01 m,复位杆 允 许低 于分型 面 , .m
基于ProE的压铸模具设计及模具变形有限元分析

- 37 -高 新 技 术铸件的压铸成形工艺在现代成形方法中占有十分重要的地位,在生产各种压铸零件时具有很多独特的优势,可以一次成形复杂的精密零件。
其成形件具有尺寸精度高、表面光洁度好、互换性好、生产效率高、成本低等众多优点,在制造业中具有很强的竞争力[1]。
该文研究工具采用的是ProE 软件,通过软件的模拟分析可以实现模具设计、仿真及力学分析,利用ProE 软件中强大的参数化仿真建模、概念构造、运动仿真及具有实际意义的模具设计等分析功能模块,可以快速进行成形工艺的设计。
对于设计分析软件而言,ProE 软件的功能是根据设计者参数化设定及调用单一数据库的特点,优化设计时每一个基本参数认定为可变的独立数据,设计者在前期设计参数建模时可以改变任意基本尺寸,软件会更新出新的建模形状。
基于ProE 软件的功能特性,使设计者能够判断建模时的逻辑关系并修改参数尺寸,如果建模设计需要改变时,仅需要改变几个参数尺寸即可完成,既节省了大量的设计时间,又减少了设计中可能会产生的错误。
ProE 软件提供的设计分析能力也有助于压铸模具设计人员的设计。
通过软件的分析功能,确定最优的加工精度及压铸时的受力变形、受热温度和运动干涉等问题,可以分析所设计的压铸模具结构是否合理,其性能是否满足设计要求,模具流动是否有缺陷,最终实现压铸模具的制造。
因此,设计者要在模具准备生产和加工前找出其存在的问题,优化参数配置,改进设计方法,不仅可以设计出性能优良可靠的模具,而且可以极大地缩短其开发周期,从而大大缩短市场对产品快速更新的需求。
1 电机端盖零件设计与计算该压铸件为电机端盖,端盖零件铸件外径尺寸为110 mm,结构相对简单,沿最大分型面对称,零件上带有4根肋,2个铸孔,其直径为3 mm,8个沉头孔,直径为4 mm。
压铸材料合金的化学成分和力学性能经查表可知,力学性能:强度σb :240 MPa,收缩率δ:1% ,硬度:90 HB,可选的铝合金材料为ZL108[2]。
模具设计与制造专业毕业论文汽缸盖压铸模具设计

摘要本课题主要是针对汽缸盖的模具设计,通过对铸件进行工艺的分析和比较,最终设计出一副压铸模。
该课题从产品结构工艺性,具体模具结构出发,对模具的浇注系统、模具成型部分的结构、顶出系统、冷却系统、压铸机的选择及有关参数的校核、都有详细的设计,同时并简单的编制了模具的加工工艺。
通过整个设计过程表明该模具能够达到此铸件所要求的加工工艺。
根据题目设计的主要任务是汽缸盖压铸模具的设计。
也就是设计一副压铸模具来生产汽缸盖铸件产品,以实现自动化提高产量。
通过模具设计表明该模具能达到盒盖的质量和加工工艺要求。
本文主要运用Pro/ENGINEER wildfire4.0及其AutoCAD2006来完成整个设计工作。
从中学习到了许多的模具设计的知识和对在校所学知识的深化,设计的整个过程实现了无纸化,有利于提高模具的生产效率和节约了生产成本,并大大缩短了生产的周期。
关键词:压铸模具设计;汽缸盖;Pro/ENGINEER wildfire4.0;AutoCAD2006;塑件;AbstractThis thesis is mainly concerned on the mould design of the lampshades,through the technical analysis and comparison of the injection moulded parts ,a plastic injection mould is formed.The issue is based on the product structure’s technical traits and mould structure,it also has a careful checking and design on the choices and parameters of the moulds’ gating system,the structure of the mould forming,ejecting system,cooling system and the injection molding machines,morever,this issue has worked out the processing technics of the moulds.The deisgn demonstrates that the mould can up to the demanding processing technics standard of the injection moulded parts.According to the main task of the design,that is to design a plastic injection mould, to produce a lampshade of plastic injection then to achieve the automation and increase the production.From the structure of the lid,this is point of dual-gate type mould.The design proves the mould can reach the lid’s quality and processing technics standard.The deign is carried through the Pro/ENGINEER wildfire3.0 and AutoCAD2007.By doing this ,I have learned a lot of mould designing knowledge and have deepened the knowledge learned during the college,the paperless of this design can improve the production efficiency and save the production cost,besids,it have shortened the production cycle.Key Words :plastic injection mould deisgn ;lampshade;Pro/ENGINEER wildfire3.0;AutoCAD2007;injection moulded parts.目录中文摘要 (1)英文摘要 (2)1.绪论 (6)1.1选题的依据及意义 (6)1.2国内外研究现状及发展趋势 (7)1.3本课题研究内容 (9)1.4汽缸盖设计任务 (9)1.5汽缸盖模具的设计流程 (10)2.塑件成品、注塑模具设计与构型 (11)2.1概述 (11)2.2模具设计环境和应用软件 (11)2.2.1 Pro/ENGINEER (11)2.2.2 其它软件AutoCAD2007 (11)2.3零件的三维图和二维工程图建模 (11)2.3.1零件的立体图建模 (11)2.3.2零件的二维工程图绘制 (12)2.4零件的基本数据 (13)2.4.1零件工艺性分析 (13)2.4.2零件材质 (13)2.4.3零件结构分析 (13)2.4.4零件体积与质量 (15)3.工艺参数分析与计算 (15)3.1型腔数目的确定及排列方式 (15)3.2注塑机 (16)3.2.1最大注塑量校核 (16)3.2.2注射压力校核 (16)3.2.3锁模力校核 (17)4.工作部分的设计 (19)4.1分型面的设计 (19)4.1.1分型面的设计原则 (19)4.1.2分型面的选择 (19)4.2浇注系统设计 (22)4.2.1主流道和分流道的设计 (22)4.2.2溢流槽 (26)4.2.3排气槽 (26)4.3成型零部件设计 (27)4.3.1成型零部件的结构设计 (27)4.3.2成型零部件工作尺寸的设计 (27)4.4分模 (33)5.结构零部件的设计 (26)5.1支承板的厚度计算 (37)5.2标准件的选用 (37)5.3抽芯机构的设计 (39)5.4推出机构的设计 (40)5.5复位机构的设计 (42)5.6冷却系统的设计 (42)6.模具总装配图 (43)结语 (45)参考文献 (46)后记 (47)引言光阴似梭,大学四年的学习一晃而过,为具体的检验这四年来的学习效果,综合检测理论在实际应用中的能力,除了平时的考试、实验测试外,更重要的是理论联系实际,即此次设计的课题为闹钟后盖的注塑模具。
毕业设计(论文)汽车驱动桥壳UG建模及有限元分析

毕业设计(论文)汽车驱动桥壳UG建模及有限元分析毕业设计(论文)汽车驱动桥壳UG建模及有限元分析JIU JIANG UNIVERSITY毕业论文题目汽车驱动桥壳UG建模及有限元分析英文题目 Modeling by UG and Finite Element Analyzing of Automobile Drive Axle Housing 院系机械与材料工程学院专业车辆工程姓名班级指导教师摘要本篇毕业设计(论文)题目是《汽车驱动桥壳建模UG及有限元分析》。
作为汽车的主要承载件和传力件,驱动桥壳承受了载货汽车满载时的大部分载荷,而且还承受由驱动车轮传递过来的驱动力、制动力、侧向力等,并经过悬架系统传递给车架和车身。
因此,驱动桥壳的研究对于整车性能的控制是很重要的。
本课题以重型货车驱动桥壳为对象,详细论述了从UG软件中的参数化建模,到ANSYS中有限元模型的建立、边界条件的施加等研究。
并且通过对桥壳在不同工况下的静力分析和模态分析,直观地得到了驱动桥壳在各对应工况的应力分布及变形情况。
从而在保证驱动桥壳强度、刚度与动态性能要求的前提下,为桥壳设计提出可行的措施和建议。
【关键词】有限元法,UG,ANSYS ,驱动桥壳,静力分析,模态分析AbstractThis graduation project entitled “Modeling and Finite Element Analyzing of Automobile Drive Axle Housing”. As the mainly carrying and passing components of the vehicle, the automobile drive axle housing supports the weight of vehicle, and transfer the weight to the wheel. Through the drive axle housing, the driving force, braking force and lateral force act on the wheel transfer to the suspension system, frame and carriage.The article studies based on heavy truck driver axle ,discusses in detail from the UG software parametric modeling, establish of ANSYS FEM model, and the boundary conditions imposed, etc. And through drive axle housing of the different main conditions of static analysis and modal analysis, it can access the stress distribution and deformation in the corresponding status of drive axle directly. Thus, under the premise of ensuring the strength of drive axle housing, stiffness and dynamic performance requirements, the analysis can raise feasible measures and recommendations in drive axle housing design.Plans to establish thet hree---dimensional model by UG, to make all kinds of emulation analysis by Ansys.【Key words】 Finite element method,UG,ANSYS,Drive axlehousing,Static analysis,Modal analysis目录前言 1第一章绪论 21.1 汽车桥壳的分类 21.2 国内外研究现状 31.3 有限元法及其理论 51.4 ansys软件介绍 71.5 研究意义及主要内容 91.6 本章小结 10第二章驱动桥壳几何模型的建立 11 2.1 UG软件介绍 112.2 桥壳几何建模时的简化处理 11 2.3 桥壳几何建模过程 122.4 本章小结 24第三章驱动桥壳静力分析 25 3.1 静力分析概述 253.2 静力分析典型工况 253.3 驱动桥壳有限元模型的建立 27 3.3.1 几何模型导入 273.3.2 材料属性及网格划分 283.4 驱动桥壳各工况静力分析 293.4.1 冲击载荷工况 293.4.2 最大驱动力工况 323.4.3 最大侧向力工况 343.5 本章小结 37第四章驱动桥壳模态分析 384.1 模态分析概述 384.2 模态分析理论 384.3 驱动桥壳模态分析有限元模型的建立 40 4.4 驱动桥壳模态分析求解及结果 41 4.5 驱动桥壳模态分析总结 474.6 本章小结 47结论 48参考文献 50致谢 52前言在桥壳的传统设计中,往往采用类比方法,对已有产品加以改进,然后进行试验、试生产。
基于有限元模拟的汽车汽缸头设计优化
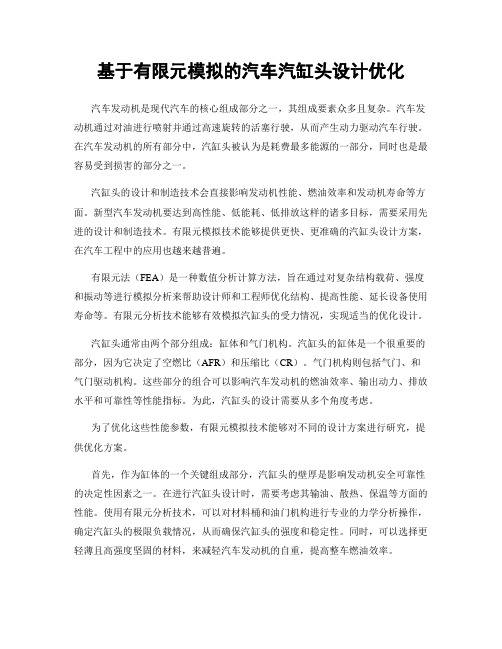
基于有限元模拟的汽车汽缸头设计优化汽车发动机是现代汽车的核心组成部分之一,其组成要素众多且复杂。
汽车发动机通过对油进行喷射并通过高速旋转的活塞行驶,从而产生动力驱动汽车行驶。
在汽车发动机的所有部分中,汽缸头被认为是耗费最多能源的一部分,同时也是最容易受到损害的部分之一。
汽缸头的设计和制造技术会直接影响发动机性能、燃油效率和发动机寿命等方面。
新型汽车发动机要达到高性能、低能耗、低排放这样的诸多目标,需要采用先进的设计和制造技术。
有限元模拟技术能够提供更快、更准确的汽缸头设计方案,在汽车工程中的应用也越来越普遍。
有限元法(FEA)是一种数值分析计算方法,旨在通过对复杂结构载荷、强度和振动等进行模拟分析来帮助设计师和工程师优化结构、提高性能、延长设备使用寿命等。
有限元分析技术能够有效模拟汽缸头的受力情况,实现适当的优化设计。
汽缸头通常由两个部分组成:缸体和气门机构。
汽缸头的缸体是一个很重要的部分,因为它决定了空燃比(AFR)和压缩比(CR)。
气门机构则包括气门、和气门驱动机构。
这些部分的组合可以影响汽车发动机的燃油效率、输出动力、排放水平和可靠性等性能指标。
为此,汽缸头的设计需要从多个角度考虑。
为了优化这些性能参数,有限元模拟技术能够对不同的设计方案进行研究,提供优化方案。
首先,作为缸体的一个关键组成部分,汽缸头的壁厚是影响发动机安全可靠性的决定性因素之一。
在进行汽缸头设计时,需要考虑其输油、散热、保温等方面的性能。
使用有限元分析技术,可以对材料桶和油门机构进行专业的力学分析操作,确定汽缸头的极限负载情况,从而确保汽缸头的强度和稳定性。
同时,可以选择更轻薄且高强度坚固的材料,来减轻汽车发动机的自重,提高整车燃油效率。
其次,气门机构是另一个重要的设计方面。
通过使用有限元分析技术,可以在汽缸头设计中考虑气门的动力特性,例如惯性、罗茨转矩和多向倾斜等因素。
对这些设计参数的分析有助于更好地管理气门运动的流量特性,从而在汽车发动机的最高转速下获得最佳的性能水平。
毕业设计进气风罩压铸成型及有限元分析

摘要目前,我国传统的飞机进气风罩大多是用铝合金钣金件分块组合焊接而成,工序繁琐,生产周期长,而且其焊接质量难以保证,在飞机飞行过程中其焊接部位经常被吹裂。
为了提高飞机进气风罩的使用寿命,降低生产难度,解决生产中因分块组合焊接而带来的质量隐患,本文采用高强度铝合金ZL101A和石膏型熔模精密铸造的工艺来成型进气风罩,并采用ProCAST铸造模拟软件对飞机进气风罩的充型凝固过程进行了数值模拟。
铸造过程的计算机模拟是近几十年迅速发展起来的现代铸造工艺研究方法,这种方法通过对铸件进行计算机试浇及工艺分析,能较快的发现决定铸件质量的内部因素,对可能出现的各种铸造缺陷提出预报,从而在工艺实施前优化所采用的铸造工艺参数,这对于指导铸造工艺设计、提高铸件质量具有重要意义。
所以,为了实现飞机进气风罩的铸造生产方式,本论文对其铸造过程中的充型凝固过程进行了数值模拟。
首先,本文对新型飞机进气风罩的石膏型熔模精密铸造工艺进行了简单的分析。
在此基础之上,建立基于Pro/E的进气风罩三维几何造型。
最后利用ProCAST铸造模拟软件对进气风罩的整个充型凝固过程进行数值模拟,以精确显示其充型凝固过程中的充填不足、冷隔、裹气和热节的位置以及残余应力和变形。
在此次模拟所设置的工艺参数下,铸件填充率可达到98%,这主要是由于铸件在凝固时收缩使浇口处产生塌陷,所以在实际浇注过程中要注意及时补缩。
其他缺陷的数量以及分布也基本符合铸件最终的使用要求,因此,这种新型飞机进气风罩的成形工艺可以应用于工业生产。
通过对模拟的缺陷的分析,还可以对进气风罩的铸造工艺过程进行优化,从而在实际生产前就采取有效的工艺措施减少或避免缺陷的产生。
这种方法对企业的实际生产具有一定的意义。
关键词:进气风罩;石膏型熔模精密铸造;凝固温度场;充型流场;数值模拟AbstractAt present, most of the traditional air intake hoods are welded by the aluminum alloy sheet. Its working procedure is complicated and the production cycle is long. Moreover, the quality of welding is difficult to guarantee. So, during the flight, the welding parts are often blown crack. In order to improve the life of the air intake hood, to lower the production difficulty and to solve the quality risks in the production due to the method of weld, in this article, the high-strength aluminum alloy ZL101A and plaster mould investment casting were used to mold the intake hood, and the filling and solidification process of the air intake hood was simulated by the casting simulation software ProCAST.Computer simulation of casting process is the modern casting study method which developed rapidly in recent decades. The internal factors which determine the quality of the casting can be found quickly by pouring and analyzing the working process by computer. To different kinds of possibly casting defects, the prediction is brought up. Thereby, the process parameters of the casting are optimized before the implementation of the process. It is of great significance to conduct the process design and improve the quality of the casting. Therefore, in order to achieve the air intake hood casting production, simulation of the filling and solidification process in the casting was carried on in this article.First of all, the plaster mould investment casting process of the new air intake hood was simple analyzed in this article. On this basis, the three-dimensional geometric modeling of the air intake hood was established by the software Pro/E. At last, the whole process of filling and solidification of the air intake hood was simulated by the casting simulation software ProCAST. The lack of filling, wrapped cold insulation, the location of the gas and the hot spot and the residual stress and deformation were accurately displayed in this process. Under the process parameters of this simulation, the filling rate of the casting was 98%, the number and the distribution of other defects could basically meet the final using requirements of the casting. So, the modeling working process of the new air intake hood can be considered into the application of the industrial production. Also, the casting process of the air intake hood can be optimized by the analysis of the defects. Thereby, the effective measures can be taken before the actual production to reduce or avoid the defects. It is of certain significance to the actual production of the enterprises.Key Words:air intake hood; plaster mould investment casting; solidification temperature field; filling flow field; numerical simulation目录摘要 (i)Abstract (ii)第1章绪论 (3)1.1课题研究背景 (3)1.2新型进气风罩的研究现状 (3)1.3铸造充型凝固过程数值模拟的研究现状 (4)1.3.1铸造充型过程数值模拟的发展 (5)1.3.2铸造凝固过程数值模拟的发展 (7)1.4本文研究的主要内容及意义 (9)第2章新型进气风罩铸造工艺设计 (10)2.1石膏型熔模精密铸造的特点 (10)2.2模具制造过程 (11)2.3生产工艺控制过程 (11)2.4小结 (13)第3章基于Pro/E的新型飞机进气风罩几何造型和数学建模 (14)3.1Pro/E软件介绍 (14)3.2进气风罩的Pro/E曲面造型设计 (15)3.3曲面造型技巧 (18)3.4小结 (19)第4章基于ProCAST的进气风罩充型凝固过程的数值模拟及仿真 (20)4.1 ProCAST软件介绍 (20)4.1.1软件模块 (21)4.1.2模拟过程 (21)4.1.3应用范围 (22)4.2充型凝固过程数值模拟数学模型 (22)4.3充型及凝固过程数值模拟流程 (23)4.4网格的划分 (23)4.4.1面网格的划分 (23)4.4.2体网格的划分 (26)4.5充型凝固过程模拟的前处理 (28)4.5.1充型凝固过程工艺参数 (28)4.5.2充型凝固过程数值模拟前处理操作 (29)4.6求解计算 (30)4.7观测模拟结果 (32)结论 (37)参考文献 (38)致谢 (41)外文科技资料翻译 (42)英文原文 (42)中文译文 (52)第1章绪论1.1课题研究背景进气风罩是铆接在飞机蒙皮外部的部件,在飞机飞行过程中,通过流经其进气风道的高速气流来冷却发动机外壳。
利用有限元分析方法研究汽车发动机缸体的刚度优化设计
利用有限元分析方法研究汽车发动机缸体的刚度优化设计随着汽车科技的不断发展,汽车发动机的性能和效率得到了极大的提升。
作为发动机的核心部件,缸体的刚度优化设计对于提高发动机的工作效率和可靠性至关重要。
本文将利用有限元分析方法来研究汽车发动机缸体的刚度优化设计。
首先,有限元分析是一种广泛应用于工程领域的数值分析方法,可以对结构在不同工况下的力学特性进行模拟和分析。
通过建立一个合适的有限元模型,可以准确地预测缸体在不同受力情况下的应力分布和变形情况。
在进行有限元分析前,需要对缸体的几何形状进行建模。
将缸体分为多个单元,每个单元都具有自己的材料性能和几何形状。
然后,通过在每个单元上应用适当的力和边界条件,可以模拟实际工况下的受力情况。
有限元分析的第一步是对缸体进行网格划分。
合适的网格划分对于结果的准确性和计算效率具有重要影响。
较为典型的划分方法包括四边形单元和六面形单元。
这些单元的尺寸和形状需要根据具体情况进行选择,以保证模拟结果的准确性。
在模拟过程中,我们考虑不同的工况,例如发动机在启动、加速和高速行驶等运行状态下的受力情况。
通过对这些工况下缸体的有限元分析,可以获得缸体的应力和变形情况。
在分析结果的基础上,我们可以对缸体的结构进行优化设计。
例如,在关键应力集中区域加强材料或改变缸体的几何形状,以提高其刚度和强度。
同时,优化设计还需考虑到缸体的质量和成本,以实现一个最佳的设计方案。
通过有限元分析方法进行缸体的刚度优化设计可以带来诸多好处。
首先,准确的应力和变形分析可以帮助工程师更好地理解缸体在不同受力情况下的性能。
其次,优化设计可以提高缸体的刚度和强度,从而提高整个发动机的工作效率和可靠性。
总结而言,利用有限元分析方法进行汽车发动机缸体的刚度优化设计是一种有效的手段。
通过建立合适的有限元模型和进行准确的应力和变形分析,可以实现缸体设计方案的优化。
这种方法为提高汽车发动机的性能和可靠性提供了一种有效的工具。
有限元计算在气缸盖设计中的应用
() 3 对气 缸盖的 计算主要 计算气缸盖在最 危险工况 即气 缸盖在 爆发行程排气上止点时的应 力及气密性计算 ,同时计算气缸盖在吸 气行程时的应力。 注:在 气缸盖有限元计算模型 中假定机体的下端面的位移被全
部 约束 。
13 后 处 理 .
பைடு நூலகம்
f 进 、排气阀装配过盈量为0 l m~ . r 取0 3 m 。 2 ) .m 1 01a 5 m( . r ) 1a
分 。共 划 分 得 四 面体 单 元 8 O 5 ,节点2 9 5 99+ 3 3 点。 其 中气 缸盖零件的 四面体 单元
704 " 77  ̄ ,节 点 2 0 2 。 07点
对2 0 8 柴油机 气缸盖的汁算采用美国I G 司的 I E S7 软 MA 公 D A . 0 件对其进行分析 。气缸盖的有限元计算包括以下儿个部分 :
的装配组合 ( 其计算模型见图1 。 )
R 气缸工测点温度 I 2
平面与气缸盖顶平面之问的接触过盈量为0 5 m( . m 相当与气缸盖螺 7 栓的预 紧伸长 量0 5 m ;设定进排气阀座外柱面 与气缸盖阀座孔 .r ) 7a 柱面之间 的半径方 向接触过盈量 为0 6rm l . 5 相当进排气阀座的装 0 a
一
圈 1 气 缸 盖 有 限 元 计 算 模 型
配过盈 量01m . m);进排气阀座 上平面与 阀座孔接触平 面之间的 3 间隙 为零 ;气缸盖密封环上平面与气缸 盖火 力面之间的问隙为零。
123 气缸盖有限元计算的边界条件加 载 .. ( 对气 缸盖温度场边界条件的加载 。参考 图2 1 ) 气缸盖 火力面的 测点温度及有 关资料 ,用数据 面 ( A A S R A E) D T U F C 方式对气缸 盖计算模 型进行温度加载。 l) 2 气体爆 发压力作 用于气缸盖 火力面 ( 气缸 套密封环 内径 范 围内气缸套上部以及气缸盖密封环 内柱面暴露部分 )。作用于进排 气阀头的气体爆 发压 力折算 为作用于进排气阀座锥面的压力。
基于有限元方法的汽车发动机缸盖结构分析
基于有限元方法的汽车发动机缸盖结构分析汽车发动机是汽车行驶的核心部件之一,而汽车发动机的性能与其各个零部件密切相关。
其中,汽车发动机的气缸盖作为发动机中的重要零部件之一,对于发动机的性能和可靠性起着至关重要的作用。
本文将通过基于有限元方法的汽车发动机气缸盖结构分析,探讨其设计和优化。
1. 汽车发动机气缸盖的功能及特点汽车发动机的气缸盖是一个位于汽缸体上方的零件,其作用是封闭汽缸腔,承载气缸压力和温度变化,同时保证发动机的密封性和冷却效果。
由于汽车发动机工作时需要承受高温高压的工况,气缸盖的材料选择和结构设计至关重要。
2. 有限元方法在汽车发动机气缸盖结构分析中的应用有限元方法是一种常用的结构分析方法,适用于求解复杂的结构力学问题。
在汽车发动机气缸盖结构分析中,有限元方法可以通过建立三维模型、设置边界条件和加载条件等,得到不同工况下气缸盖的应力分布和变形情况。
这可以为气缸盖的设计和优化提供有力的依据。
3. 汽车发动机气缸盖的材料选择汽车发动机气缸盖的材料选择直接影响其性能和可靠性。
常见的气缸盖材料包括铸铁、铝合金等。
不同材料在强度、成本和重量等方面存在差异,因此需要根据具体要求和预算进行选择。
4. 汽车发动机气缸盖的结构设计与优化在气缸盖的结构设计与优化中,考虑到发动机工作时的热膨胀和热应力,需要合理选择结构形式和材料。
同时,还需要充分考虑到不同工况下气缸盖的应力分布和变形情况,以提高其强度和刚度,保证其工作的可靠性和稳定性。
5. 汽车发动机气缸盖的疲劳分析汽车发动机气缸盖在长期工作过程中容易产生疲劳问题,因此需要进行疲劳分析。
通过有限元方法建立疲劳分析模型,可以预测气缸盖的寿命,并通过优化设计和改善材料来延长其使用寿命。
综上所述,基于有限元方法的汽车发动机气缸盖结构分析是一项复杂而重要的工作。
通过对气缸盖的功能、特点、材料选择、结构设计与优化以及疲劳分析等方面进行综合考虑和分析,可以帮助汽车制造商和工程师更好地设计和改进发动机气缸盖,提高汽车发动机的性能和可靠性。
毕业设计(论文)-发动机曲轴连杆机构仿真及有限元分析设计-adams
全套图纸加扣 3012250582曲轴连杆活塞组件虚拟样机的建立学院名称:机械工程学院专业班级:机械设计制造及其自动化0501 班学生姓名:号:学指导教师:2009 年6 月摘要柴油机的气缸、活塞、连杆、曲轴以及主轴承组成一个曲柄连杆机构。
柴油机通过曲柄连杆机构,将活塞的往复运动转换为曲轴的回转运动,使气缸内燃油燃烧所产生的热能转变为曲轴输出的机械功。
可见,曲柄连杆机构是柴油机重要的传力机构。
对其运动和受力情况进行分析和研究,是十分必要的。
这种分析研究既是解决柴油机的平衡、振动和总体设计等课题的基础,也是对其主要零部件在强度、刚度、磨损等方面进行计算和校验时的依据。
本文在曲柄连杆机构理论分析的基础上,利用多体动力学理论,三维造型软件Pro/E 及动力学分析软件ADAMS对内燃机曲柄连杆机构的动力学问题进行了虚拟样机仿真分析。
并以CT484Q柴油机为研究对象,在Pro/E中建立CT484柴油机曲柄连杆机构的虚拟样机模型,导入ADAMS中进行动力学分析,绘制出虚拟样机模型中各连接位置处受力仿真结果曲线。
通过本文的研究,展示了一种简捷、高效的机械设计分析手段,对今后同类型的研究乃至更大规模的仿真分析积累了一些经验。
本文的研究也可以为今后内燃机机构的造型、优化设计提供参考依据。
关键词:内燃机,曲柄连杆机构,ADAMS,虚拟样机,仿真AbstractThe Cylinder, piston, connecting rod, crankshaft and main bearings of diesel engine Compose of a crank-connecting rod mechanism. Through the crank-connecting rod mechanism, Diesel engine convert the piston reciprocating motion to the rotary movement of the crankshaft, and make the cylinder generated by fuel combustion energy into mechanical work output of the crankshaft. This shows that diesel engine crank linkage is an important body for transmission force. It is necessary to analysis and research its movement and force. This analysis is the foundation to solve the balance of diesel engine, vibration and overall design, It is the basis for validate and calculate the strength, stiffness, wear, etc.In this paper, based on the theoretical analysis of crank-connecting rod mechanism, use of multi-body dynamics theory, and use the three-dimensional modeling software, Pro/ E and the dynamic analysis software ADAMS to carry out crank and connecting rod for internal combustion engine body dynamics simulation of a virtual prototype simulation. And study CT484Q Diesel Engine, established linkage of the virtual prototype of diesel engine model In Pro/ E, then do dynamic analysis in ADAMS and draw the connection position of the power curve for the simulation result.Through this paper, the study demonstrated a simple and efficient means of mechanical design and analysis for future research as well as the same type of simulation analysis and accumulate some experience. The study of this paper can provide reference for the modeling and optimal design.Key words: Internal Combustion Engine, Crank-connecting rod mechanism, ADAMS, Virtual Prototyping目录第一章绪论··················································1.1 研究的意义···············································1.2 内燃机曲柄连杆机构的工作特点以及难点·····························1.3 国内外研究及手段···········································1.3.1计算机辅助设计(CAD)·····································1.3.2 多体动力学分析(MBS)···································1.3.3 有限元分析···········································1.3.4优化设计理论··········································1.4 主要研究内容和方法··········································第二章曲柄连杆机构的动力学理论分析·······························2.1 内燃机工作过程分析··········································2.1.1压缩始点气体状态·········································2.1.2压缩终点气体状态········································2.1.3燃烧过程及燃烧终点气体状态·································2.1.4膨胀终点气体状态········································2.2 曲柄连杆机构的运动分析·······································2.3曲柄连杆机构的动力学分析······································2.3.1曲柄连杆机构的质量换算····································2.3.2曲柄连杆机构的惯性力和惯性力矩······························2.3.3曲柄连杆机构的动力学分析··································2.4 内燃机工作过程计算··········································第三章曲轴连杆活塞组件的虚拟样机································3.1Pro/E 系统的建模原理及其特点····································3.1.1参数化设计············································3.1.2 特征建模的基本思想······································3.1.3全相关的单一数据库······································3.2 曲柄、连杆、活塞组件几何模型的建立以及装配··························3.2.1活塞组件的建模·········································3.2.2 连杆组建的建模········································3.2.3曲轴组件的建模·········································3.2.4曲轴连杆活塞组件的总装配···································第四章曲柄连杆机构的运动学和动力学分析·····························4.1ADAMS简介及其基本原理·······································4.1.1 运动学和动力学基本概念···································4.1.2 ADAMS中多刚体动力写方程的建立······························4.2ADAMS 中的运动学和动力学分析···································4.2.1 曲柄连杆机构刚体模型的转化和输入·····························4.2.2 曲轴轴系多刚体动力学仿真分析·······························第五章结论与展望·············································5.1 总结····················································5.2 展望····················································致谢························································参考文献·····················································附录·························································第一章绪论1.1研究的意义内燃机是目前世界上应用最广泛的热动力装置,自1860年法国人设计出第一台煤气发动机以来,内燃机无论是在结构上还是在性能上都较以前有了很大的进步。
- 1、下载文档前请自行甄别文档内容的完整性,平台不提供额外的编辑、内容补充、找答案等附加服务。
- 2、"仅部分预览"的文档,不可在线预览部分如存在完整性等问题,可反馈申请退款(可完整预览的文档不适用该条件!)。
- 3、如文档侵犯您的权益,请联系客服反馈,我们会尽快为您处理(人工客服工作时间:9:00-18:30)。
BI YE SHE JI(20 届)基于有限元分析的发动机缸体压铸模具设计所在学院专业班级材料成型与控制工程学生姓名学号指导教师职称完成日期年月任务下达日期:2016年3月1日毕业设计日期:2016年3月1日至2016年6月12日毕业设计题目:基于有限元分析的发动机缸体压铸模具设计毕业设计主要内容和要求:内容:1、查阅30篇中文文献及10篇左右的英文文献,充分了解设计内容。
2、利用NX10.0建立缸体三维模型,使用Anycasting完成缸体压铸过程模拟分析。
3、参考设计手册和模拟结果完成压铸模具设计,并绘制模具工程图。
4、要求翻译一篇近三年的英文文献,汉字内容应不少于3000字。
要求:1、努力学习、勤于实践、勇于创新,保质保量地完成毕业设计任务。
2、遵守纪律,保证出勤。
因事、因病离岗,应事先向指导老师请假。
否则作为缺席处理。
3、独立完成规定的工作内容。
不弄虚作假,不抄袭和拷贝别人的工作内容。
4、毕业设计必须符合中国矿业大学毕业论文规范化规定,否则不得参加毕业答辩。
院长签字:指导教师签字:本文以某汽车的发动机铝合金缸体压铸件为研究对象,对该缸体压铸件可能铸造缺陷进行分析及预测。
首先利用NX10.0设计该缸体的三维模型,并参照设计手册完成浇注系统和排溢系统的设计。
然后利用铸造模拟软件anycasting v4.0对压铸模具型腔、浇注系统和排溢系统整体进行充填和凝固过程进行模拟研究。
分析目前的工艺和设计的浇注系统、排溢系统的是否存在问题,对重要的压铸工艺参数进行优化,并优化压铸模具浇注系统和排溢系统。
根据以上模拟结果和设计手册,利用NX10.0、AUTOCAD完成其余结构的设计。
使用anycasting v4.0主要完成充型分析,充型过程热分析和热凝固分析,其中重要的工艺参数是冲头快压射速度、浇注温度、冲头高低速转换点和模具预热温度,最后得到一个缺陷比较少的模拟结果。
对一般充型缺陷,可以通过优化设计浇注系统、排气系统改进,对凝固缺陷可以通过修改冷却系统的位置进行改进。
模具设计部分包括模具型芯部分设计、模架设计、侧抽芯系统设计、顶出系统设计、模具厚度核算、动模座板行程校核、最小合模距离与最大开模距离校核和模具最大外形轮廓校核。
最后依据模拟分析结果和模具结构设计,利用NX10.0三维造型软件完成缸体铸件的压铸模具设计。
关键词:铝合金缸体、数值模拟、压铸、模具设计ABSTRACTTaking a car engine cylinder aluminum die castings for the study, the cylinder block casting casting defect may be analyzed and forecast.First, NX10.0 three-dimensional modeling software design of the cylinder model, and complete reference design manual design gating system and overflow discharge system. Then use the casting simulation software anycasting v4.0 of the casting mold cavity, injection system, exhaust system overflow whole process of filling and solidification simulation study, analyze the current process and design of gating system, overflow discharge system if there are problems, important casting process parameters were optimized, and modify the casting mold casting system ,, overflow discharge system design, simulation based on the above results and the design manual, use NX10.0, AUTOCAD complete the remaining structural design. Wherein anycasting v4.0, the analysis is divided into filling filling process analysis and thermal analysis, mold filling analysis and thermal analysis before and after filling, thermal coagulation analysis, simulation-pressure chamber, one of the important process parameters are fast injection speed punch pouring temperature, high and low switch point punch and die preheating temperature. Finally, get a relatively small defect simulation results, the general filling defects by improving pouring system, exhaust system, coagulation defects can modify the position of the cooling system, the use of other cooling methods. Mold design section includes: mold core part of the design, mold design, system design side core pulling, ejection system design, mold thickness calculation, the movable mold base plate stroke check, the minimum distance between the mold and the mold maximum distance check, maximum mold contour check. NX10.0 use three-dimensional modeling software for some institutions shape and mold assembly.KeyWords:Aluminum alloy cylinder;Numerical simulation;die-casting;Mold design目录1 绪论 (1)1.1引言 (1)1.2压铸模拟技术的现状 (1)1.3压铸模具设计技术的现状 (4)1.4本文研究内容 (6)1.5研究的目的和意义 (6)2 压铸模拟分析方法 (8)2.1 Anycasting软件简介 (8)2.1.1 Anycasting模块简介 (8)2.1.2 Anycasting缺陷分析理论基础 (8)2.2 Anycasting模拟研究方法 (10)2.2.1模拟过程设置 (10)2.2.2模拟结果分析 (11)2.3本章小结 (11)3 缸体压铸过程的数值模拟 (12)3.1 数值模拟前处理 (12)3.1.1 三维模型建立 (12)3.1.2 网格划分 (13)3.1.3模拟参数设定 (13)3.2充型过程的模拟分析 (14)3.2.1充型过程的流动分析 (14)3.2.2充型过程的速度分析 (15)3.2.3充型过程的压力分析 (16)3.3凝固过程的模拟分析 (16)3.3.1凝固时间分析 (17)3.3.2冷却速率分析 (17)3.3.3凝固缺陷分析 (18)3.4本章小结 (19)4 压铸模具设计 (21)4.1引言 (21)4.2 压铸机的选择 (21)4.2.1铸件分析 (21)4.2.2 压铸机的类型 (22)4.2.3压铸机选用原则 (22)4.2.4确定压铸机锁模力 (23)4.2.5压室容量的估算 (24)4.2.6开模距离的核算 (24)4.3浇排系统设计 (25)4.3.1直浇道的设计 (25)4.3.2横浇道设计 (25)4.3.3内浇口设计 (26)4.3.4 溢流槽与排气槽设计 (26)4.3.5冷却系统设计 (27)4.4分型面设计 (27)4.4.1分型面选择的原则 (27)4.4.2分型面的类型 (28)4.5成型零件的设计 (28)4.5.1成型零件收縮率的确定 (28)4.5.2镶块设计 (28)4.5.3型芯设计 (29)4.5.4 侧抽芯机构设计 (29)4.6标准件与常用件设计 (30)4.6.1液压油缸设计 (30)4.6.2浇口套设计 (30)4.6.3滑块的设计 (31)4.6.4动、定模模板设计 (31)4.6.5模座的尺寸计算 (32)4.6.6导柱、导套设计 (32)4.6.7推出机构设计 (33)4.7模具的校核 (33)4.7.1模具厚度核算 (33)4.7.2动模座板行程核算 (34)4.7.3最小合模距离与最大开模距离校核 (34)4.7.4模具最大外形轮廓校核 (34)4.8模具整体装配 (34)4.9本章小节 (35)5 总结 (36)参考文献 (37)外文原文 (39)中文译文 (52)致谢 (59)1 绪论1.1引言现在的铸造行业的发展已经是属于全球化,合金压铸工业的发展趋势属于更短的产品研制周期、更复杂的产品和更优的质量。
以往我们都花费大量的人力、物力进行铸件产品的研发,都要在实际的生产的条件下进行反复的试铸,然后不断修改压铸方案和工艺,最后再确定生产工艺的模式,现在已经被逐步抛弃。
利用先进的计算机模拟软件进行相关的铸造模拟的技术在现代化压铸生产工艺上已经逐渐成为主要流程之一。
本文所研究的缸体压铸的铸件为直列四缸的发动机缸体压铸件,选用的材料采用为铸造铝合金,目前发动机材料也已经大量使用铝镁等合金,因为这种的材料可以大幅减轻发动机自身占整车的比重。
由于缸体铸件采用压铸生产,质量问题一直是影响批量生产的关键,在排除了铝合金的熔炼及生产转运过程造成的铝合金的熔液质量不能达标等因素后,一般的毛坯铸件在检测后,会发现其内部仍存在内部气孔、氧化夹渣和缩孔等一般的铸造缺陷。