材料成型专业毕业论文:锌合金底盘座铸件压铸模具设计
锌合金压铸技术3篇
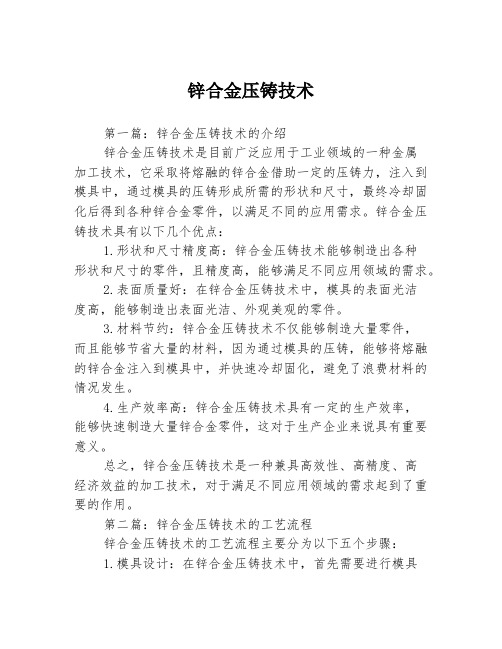
锌合金压铸技术第一篇:锌合金压铸技术的介绍锌合金压铸技术是目前广泛应用于工业领域的一种金属加工技术,它采取将熔融的锌合金借助一定的压铸力,注入到模具中,通过模具的压铸形成所需的形状和尺寸,最终冷却固化后得到各种锌合金零件,以满足不同的应用需求。
锌合金压铸技术具有以下几个优点:1.形状和尺寸精度高:锌合金压铸技术能够制造出各种形状和尺寸的零件,且精度高,能够满足不同应用领域的需求。
2.表面质量好:在锌合金压铸技术中,模具的表面光洁度高,能够制造出表面光洁、外观美观的零件。
3.材料节约:锌合金压铸技术不仅能够制造大量零件,而且能够节省大量的材料,因为通过模具的压铸,能够将熔融的锌合金注入到模具中,并快速冷却固化,避免了浪费材料的情况发生。
4.生产效率高:锌合金压铸技术具有一定的生产效率,能够快速制造大量锌合金零件,这对于生产企业来说具有重要意义。
总之,锌合金压铸技术是一种兼具高效性、高精度、高经济效益的加工技术,对于满足不同应用领域的需求起到了重要的作用。
第二篇:锌合金压铸技术的工艺流程锌合金压铸技术的工艺流程主要分为以下五个步骤:1.模具设计:在锌合金压铸技术中,首先需要进行模具设计。
模具的设计要考虑到锌合金压铸的工艺特点,尽可能的减少模具使用寿命和生产成本,同时满足零件的形状和尺寸等要求。
2.锌合金熔炼:将锌合金熔炼成一定温度的熔融状态,以便于注入到模具内。
3.注入模具:在锌合金熔炼完成后,需要借助一定的压铸力,将熔融的锌合金注入到模具中,按照所需的形状和尺寸进行压铸。
4.卸模、清理:待压铸完成后,将模具卸下,将形成的锌合金零件取出,并进行清理。
5.后处理:在锌合金压铸完成后,还需要进行热处理、机加工、表面处理等后续处理,以使得锌合金零件能够满足不同应用领域的需求。
以上就是锌合金压铸技术的工艺流程,对于使用锌合金压铸技术的企业来说,需要掌握这些工艺流程,以便在生产过程中更好地进行管理。
第三篇:锌合金压铸技术的应用领域锌合金压铸技术是一种使用广泛的金属加工技术,其应用领域非常广泛。
压铸模具设计范文

压铸模具设计范文压铸模具设计是指为了生产压铸件而设计的模具,其主要任务是将液态金属注入模具中,并在模具中冷却、凝固,最终得到所需形状的金属零件。
压铸模具设计的主要工作包括设计模具的结构、选材、计算模具的合理尺寸和形状等。
一、压铸模具结构设计1.模具整体结构设计:根据压铸件的形状和尺寸,确定模具的整体结构。
一般情况下,压铸模具采用上下模结构,上模为固定模,下模为活动模。
针对复杂形状的压铸件,可能需要设计多个滑模和拉杆。
2.模腔设计:根据压铸件的形状和尺寸,确定模腔的几何形状和尺寸。
模腔的设计应保证在模具关闭时,模腔中的液态金属能够充满整个腔体,并且在冷却凝固过程中,金属能够均匀收缩,避免产生缩孔和其他缺陷。
3.浇口和导流系统设计:浇口和导流系统的设计对于压铸件的质量和生产效率有着重要的影响。
浇口的设计应尽量避免金属的湍流流动,避免气泡的产生。
导流系统的设计应考虑金属的顺序填充和排气,以及冷却和凝固过程中的温度控制。
二、压铸模具选材压铸模具的选材应根据金属的性能和压铸工艺的要求来确定。
通常情况下,模具会选用高强度和耐磨损的合金钢作为材料,以保证模具的使用寿命和精度。
同时,还需要考虑模具的热传导性能,以确保压铸件能够快速冷却、凝固。
三、压铸模具尺寸和形状计算1.模具尺寸计算:模具尺寸的计算包括模腔尺寸、模板尺寸、滑模尺寸、导流系统尺寸等。
模具尺寸的计算需要考虑压铸件的最终尺寸、缩孔和收缩率等因素。
2.模具形状计算:模具的形状计算主要是指模腔内部的曲面和棱角的设计。
对于复杂形状的压铸件,需要使用CAD软件进行三维建模和形状优化,以确保模具的制造精度和压铸件的质量。
压铸模具设计需要充分考虑压铸件的形状和尺寸、材料的性能、压铸工艺要求等因素,通过合理的结构设计、选材和计算,能够提升压铸件的质量和生产效率。
在设计过程中,还需要考虑模具的制造难度和制造成本,以确保模具的可行性和经济性。
模具压铸论文【范本模板】

压铸成型工艺与模具设计课程论文学生姓名:张胜军学号:20114024330所在学院:工程学院专业:机械设计制造及其自动化中国·大庆2014年06镁合金压铸模具发展现状张胜军(工程学院设计11—3班)摘要:本文针对镁合金压铸模具发展现状,阐述了作者的观点。
通过对压铸镁合金其高温、延展以及耐腐蚀的研究,分析其使用性能。
设计压铸模具并改造压铸方式以及利用新型计算机模拟设计提高生产效率.关键词:压铸研究;压铸方式;压铸设计;应用前景。
引言镁合金材料1808年面世, 1886年开始用于工业生产。
镁合金压铸技术从1916年成功地将镁合金用于压铸件算起,至今也经历了八十余年的发展.人类在认识和驾驭镁合金及其制品的生产技术方面,经历了漫长的探索历程。
从1927年推出高强度MgAl9Zn1开始,镁合金的工业应用获得了实质性的进展。
1936年德国大众汽车公司开始用压铸镁合金生产“甲壳虫”汽车的发动机传动系统零件,1946年单车使用镁合金量达18kg左右。
美国在1948~1962年间用热室压铸机生产的汽车用镁合金压铸件达数百万件。
尽管如此,过去镁合金作为结构材料主要用于航空领域,在其它领域,世界上镁的主要用途是生产铝合金,其次用于钢的脱硫和球墨铸铁生产。
1 压铸镁合金的研究镁合金的密度小于2g/cm3,是目前最轻的金属结构材料,其比强度高于铝合金和钢,略低于比强度最高的纤维增强塑料;其比刚度与铝合金和钢相当,远高于纤维增强塑料;其耐腐蚀性比低碳钢好得多,已超过压铸铝合金A380;其减振性、磁屏蔽性远优于铝合金;鉴于镁合金的动力学粘度低,相同流体状态下的充型速度远大于铝合金,加之镁合金熔点、比热容和相变潜热均比铝合金低,故其熔化耗能少,凝固速度快,镁合金实际压铸周期可比铝合金短50%。
此外,镁合金与铁的亲和力小,固溶铁的能力低,因而不容易粘连模具表面,其所用模具寿命比铝合金高2~3倍。
常用的压铸镁合金大多是美国牌号AZ91,AM60,AM50,AM20,AS41和AE42,分别属于Mg—Al—Zn,Mg-Al-Mn,Mg—Al—Si和Mg-Al-RE四大系列。
压铸工艺与模具设计毕业论文

压铸工艺与模具设计毕业论文一、选题的依据及意义本课题来源于江铃汽车集团公司骨干企业,江铃汽车集团公司车厢饰件厂的全资子公司,江铃有色金属压铸厂。
该公司成立于2002年5月。
工厂总投入资金为四千万元人民币,自建立起就本着高起点,现代化的原则,工厂以生产铝合金压铸件及其加工为主,已为江铃汽车、奇瑞汽车及中华汽车配套生产变速器及发动机零部件,产品已出口欧洲,工厂还可生产路灯灯罩、电梯踏板、电机壳体等其它铝合金压铸件。
产品图如下所示:压力铸造是近代金属加工工艺中发展较快的一种少无切削的特种铸造方法。
它是将熔融金属在高压高速下充填铸型,并在高压下结晶凝固形成铸件的过程。
高压高速是压力铸造的主要特征。
常用的压力为数十兆帕,填充速度(浇口速度)约为16~80米/秒,金属液填充模具型腔的时间极短,约为0.01~0.2秒。
压力铸造特点如下:一、优点:(1)可以制造形状复杂、轮廓清晰、薄壁深腔的金属零件。
(2)压铸件的尺寸精度较高,可达IT11~IT13级,有时可达IT9级,表面粗糙度达Ra0.8~3.2um,有时达Ra0.4um,互换性好。
(3)材料利用率高。
(4)可以将其他材料的嵌件直接嵌铸在压铸件上。
(5)压铸件组织致密,具有较高的强度和硬度。
(6)可以实现自动化生产。
二、缺点:(1)由于高速充填,快速冷却,形腔中气体来不及排出,致使压铸件常有气孔及氧化夹杂物存在,从而降低了压铸件质量。
(2)压铸机和压铸模质量昂贵,不适合小批量生产。
(3)压铸件尺寸受到限制。
(4)压铸合金种类受到限制。
在此之上还发展出多种特殊压铸工艺,以解决压铸件的气孔和疏松问题。
迄今为止主要有真空压铸、充氧压铸、精速密压铸、半固态压铸等。
由于用这种方法生产产品具有生产效率高,工序简单,铸件公差等级较高,表面粗糙度好,机械强度大,可以省去大量的机械加工工序和设备,节约原材料等优点,且其缺点可以通过特殊压铸得到有效的克服,所以现已成为我国铸造业中的一个重要组成部分。
压铸模具设计毕业设计说明书

目录第一章压铸合金与压铸件的设计......................................1.1 压铸合金.....................................................1.1.1 工件的材料性能.........................................2.2 压铸机的型号及主要参数.......................................2.3 压铸机的选用................................................2.3.1 压铸机的基本参数选择...................................2.3.2 计算压铸机的锁模力....................................2.3.3 压室容量的校核........................................2.4 压铸工艺....................................................2.4.1 压射压力的选择.........................................第四章成型零件与模架设计...........................................4.1成型零件的结构设计...........................................4.2 成型零件的成型尺寸的计算.....................................4.3 模架的设计...................................................4.4 加热与冷却系统设计(该模具不采用加热冷却系统,略)...........第五章抽芯结构设计.................................................参考文献............................................................设计了立式冷室压铸机,压铸技术有了一个很大的进步,使得铝、镁、铜等合金均可采用压铸生产。
锌合金材质冷室压铸模具设计
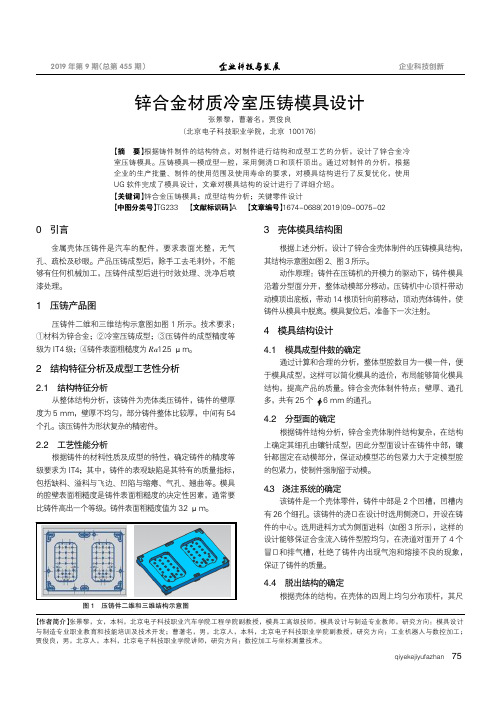
qiyekejiyufazhan图1压铸件二维和三维结构示意图【摘要】根据铸件制件的结构特点,对制件进行结构和成型工艺的分析,设计了锌合金冷室压铸模具。
压铸模具一模成型一腔,采用侧浇口和顶杆顶出。
通过对制件的分析,根据企业的生产批量、制件的使用范围及使用寿命的要求,对模具结构进行了反复优化,使用UG 软件完成了模具设计,文章对模具结构的设计进行了详细介绍。
【关键词】锌合金压铸模具;成型结构分析;关键零件设计【中图分类号】TG233【文献标识码】A 【文章编号】1674-0688(2019)09-0075-020引言金属壳体压铸件是汽车的配件,要求表面光整,无气孔、疏松及砂眼。
产品压铸成型后,除手工去毛刺外,不能够有任何机械加工,压铸件成型后进行时效处理、洗净后喷漆处理。
1压铸产品图压铸件二维和三维结构示意图如图1所示。
技术要求:1〇材料为锌合金;2〇冷室压铸成型;3〇压铸件的成型精度等级为IT4级;4〇铸件表面粗糙度为Ra 12.5μm 。
2结构特征分析及成型工艺性分析2.1结构特征分析从整体结构分析,该铸件为壳体类压铸件,铸件的壁厚度为5mm ,壁厚不均匀,部分铸件整体比较厚,中间有54个孔。
该压铸件为形状复杂的精密件。
2.2工艺性能分析根据铸件的材料性质及成型的特性,确定铸件的精度等级要求为IT4;其中,铸件的表观缺陷是其特有的质量指标,包括缺料、溢料与飞边、凹陷与缩瘪、气孔、翘曲等。
模具的腔壁表面粗糙度是铸件表面粗糙度的决定性因素,通常要比铸件高出一个等级。
铸件表面粗糙度值为3.2μm 。
3壳体模具结构图根据上述分析,设计了锌合金壳体制件的压铸模具结构,其结构示意图如图2、图3所示。
动作原理:铸件在压铸机的开模力的驱动下,铸件模具沿着分型面分开,整体动模部分移动,压铸机中心顶杆带动动模顶出底板,带动14根顶针向前移动,顶动壳体铸件,使铸件从模具中脱离。
模具复位后,准备下一次注射。
4模具结构设计4.1模具成型件数的确定通过计算和合理的分析,整体型腔数目为一模一件,便于模具成型,这样可以简化模具的造价,布局能够简化模具结构,提高产品的质量。
压铸工艺及模具设计
压铸工艺及模具设计在工业生产中,压铸工艺及模具设计是常见且重要的工艺制造方法。
压铸工艺以其高效、高质量和高精度的特点,被广泛应用于汽车、摩托车、电子、机械和家电等行业。
压铸工艺是指将金属材料经过加热熔化后,通过高压注入模具中,使金属凝固成型的工艺过程。
压铸工艺的主要特点是能够快速、高效地生产复杂形状、高精度的零部件。
压铸工艺通常分为冷室压铸和热室压铸两种方式。
冷室压铸适用于铝合金、镁合金和铜合金等高熔点金属的铸造,而热室压铸适用于低熔点金属如锌合金、铅合金和锡合金等的铸造。
模具设计在压铸工艺中起到了至关重要的作用。
模具设计的质量直接影响到产品的质量、生产效率和成本。
压铸模具通常包括上模、下模、模芯和顶针等零件组成。
对于复杂形状的产品,还需要考虑模具的结构、冷却系统和顶出机构等技术要求。
模具设计要考虑到产品的材料、几何复杂度、尺寸精度和表面质量等因素,充分利用材料的力学性能和热传导性能,以满足产品的工程要求。
1.材料选择:压铸工艺适用于铝合金、镁合金、铜合金、锌合金等多种金属材料。
不同的材料有不同的熔点、流动性和固化速度等特点,需要根据产品的要求选择合适的材料。
2.模具结构:模具的结构包括上模、下模和模芯等组成部分,需要考虑产品的几何形状、尺寸精度和表面质量等工程要求。
同时,模具还要具备良好的刚性和稳定性,以确保产品的精度和质量。
3.冷却系统:在压铸过程中,金属材料需要快速冷却和固化,以保证产品的密实性和准确性。
因此,模具中需要设置合理的冷却系统,以提高铸件的冷却速度和冷却效果。
4.顶出机构:对于出模困难的产品,需要设计合适的顶出机构,以确保产品能够顺利脱模。
顶出机构通常包括顶针、顶杆和顶出板等部件。
5.加工工艺:压铸工艺需要考虑金属材料的熔化温度、注射压力和注射速度等因素。
在模具设计中要合理设置熔化炉、喷嘴和压机等设备,确保加工工艺的可行性和稳定性。
在压铸工艺及模具设计中,需要综合考虑产品的功能要求、表面效果、生产批量和成本等因素,以找到最优的工艺和设计方案。
底座铸造毕业设计
底座铸造毕业设计底座铸造毕业设计毕业设计是每个大学生的重要任务,它不仅是对所学知识的综合运用,更是对个人能力和专业素养的一次全面检验。
作为一名机械工程专业的学生,我选择了底座铸造作为我的毕业设计课题。
底座是机械设备的重要组成部分,它承载着整个设备的重量,并提供稳定的支撑。
底座的质量和结构设计直接影响着设备的稳定性和使用寿命。
因此,我决定通过铸造的方式来制造底座,以确保其质量和性能。
首先,我进行了底座的结构设计。
通过对不同类型设备的分析和研究,我确定了底座的形状和尺寸。
底座需要具备足够的强度和刚性,以承受设备的重量和外部力的作用。
同时,底座还需要考虑到设备的布线和维修保养的便利性。
在结构设计中,我采用了CAD软件进行三维建模和仿真,以确保底座的结构合理性和稳定性。
接下来,我进行了底座的材料选择。
底座需要具备高强度、耐磨损和耐腐蚀等特性。
在材料选择上,我综合考虑了铸造工艺的可行性和材料的性能要求。
最终,我选择了一种高强度铸铁材料作为底座的材料。
这种材料具有良好的铸造性能和机械性能,能够满足底座的使用要求。
然后,我进行了底座的铸造工艺设计。
铸造是将熔融金属注入到模具中,经过冷却凝固形成所需零件的一种制造方法。
在底座的铸造过程中,我需要考虑到金属的熔化温度、浇注温度和冷却速度等因素。
通过合理控制这些参数,可以获得高质量的底座铸件。
为了提高铸件的表面质量和减少缺陷,我还采用了一些先进的铸造技术,如真空铸造和气体保护铸造。
最后,我进行了底座的加工和装配。
铸造得到的底座铸件需要进行后续的加工和装配,以满足设备的安装和使用要求。
在加工过程中,我采用了数控加工技术和精密测量设备,以确保底座的尺寸和形状的精度。
在装配过程中,我还进行了一系列的功能测试和质量检验,以确保底座的性能和可靠性。
通过这次底座铸造的毕业设计,我不仅学到了很多有关铸造工艺和机械设计的知识,更锻炼了自己的实践能力和解决问题的能力。
我深刻体会到了工程实践的重要性和挑战性,也更加明确了自己未来的发展方向。
压铸模具论文
目录一、摘要 (1)二、支架压铸件的结构分析 (3)2.1压铸件结构 (3)2.2尺寸精度 (3)2.3材料 (3)三、支架压铸件的成型工艺参数 (3)3.1压力参数 (3)3.2速度参数 (5)3.3时间参数 (6)3.4温度参数 (6)四、支架压铸件的模具概述 (7)4.1分型面的确定 (7)4.2浇注系统的设计 (8)4.3顶出系统设计 (8)4.4成型零件尺寸计算 (11)4.5压铸件装配图 (12)五、总结 (13)1二、支架压铸件的结构分析2.1压铸件结构该压铸件结构比较简单,但在三个方向均有侧面凹孔,因此压铸时要采用侧向抽芯机构抽芯。
压铸件的表面大部分为曲面,用一般的机械加工法加工模具型腔比较困难,因此型腔部分宜用电脉冲机床加工。
铸件壁厚基本均匀,但B-B刨面处壁略厚,容易出现热节。
2.2尺寸精度该零件全部尺寸均未注公差。
按图中要求,其公差IT12级,用压铸方法生产该零件完全能达到尺寸要求。
2.3材料压铸件材料为YZAISi12,为压铸铝合金,可以用作压铸该零件的材料。
查表得,其平均收缩率取0.7%。
2三、支架压铸件的成型工艺参数3.1压力参数压铸压力是压铸工艺中主要的参数之一。
压铸工程中的压力是由泵产生的,泵借蓄压器通过工作液体传递给压射活塞,然后由压射活塞经压射冲头施加于压室内的金属液上。
作用于金属液上的压力是获得组织致密和轮廓清晰的铸件的主要因素,所以,必须了解并掌握压铸过程中作用在液态金属上的压力的变化情况,以便正确利用压铸过程中个阶段的压力,并合理选择压力的数值。
压铸过程中的压力可以用压射力和压射比压两种形式来表示。
(1)压射力压铸机压射缸内的工作液作用于压射冲头,使其推动液态金属充填模具型腔的力。
其大小随压铸机的规格而不同,它反映了压铸机功率的大小。
压射力计算公式为[3];(7.1)式中F——压射力(N);p——压射缸内工作液的压力(MPa);A——压射冲头截面积(2mm);3D——压射缸直径(mm)。
我的压铸模具论文
锌合金底盘座铸件压铸模具设计The Die-casting Mold Design of ZincSubbase Casting学院:材料科学与工程学院专业班级:材料成型及控制工程0606班学号:050201130学生姓名:朱墨指导教师:李晨希(教授)2010 年07 月摘要压力铸造是目前成型有色金属铸件的重要成型工艺方法。
压铸的工艺特点是铸件的强度和硬度较高,形状较为复杂且铸件壁较薄,而且生产率极高。
压铸模具是压力铸造生产的关键,压铸模具的质量决定着压铸件的质量和精度,而模具设计直接影响着压铸模具的质量和寿命。
因此,模具设计是模具技术进步的关键,也是模具发展的重要因素。
根据零件的结构和尺寸设计了完整的模具。
设计内容主要包括:浇注系统设计、成型零件设计、抽芯机构设计、推出机构设计以及模体结构设计。
根据铸件的形状特点、零件尺寸及精度,选定了合适的压铸机,通过准确的计算并查阅设计手册,确定了成型零件以及模体的尺寸及精度,在材料的选取及热处理要求上也作出了详细说明,并在结合理论知识的基础上,借助于计算机辅助软件绘制了各部分零件及装配体的立体图和工程图,以保障模具的加工制造。
根据有关资料,采用扁平侧面浇注系统,降低了浇注时金属液对型芯的冲击,确定了铸造工艺参数:铸件加工余量取0.1~0.75mm,收缩率为0.4~0.7﹪,脱模斜度为25′~45′。
模具整体尺寸为900×640×835mm,符合所选压铸机安装空间。
抽芯采用斜滑块机构,拼合形式为两瓣式。
推出机构采用4根端面直径26mm的圆截面推杆,推杆兼复位杆作用。
经计算,推杆受力符合要求。
通过电脑模拟显示,模具能够正常工作,开启灵活。
关键词:压力铸造;压铸模具;锌合金铸件;底盘座AbstractDie-casting molding technology is playing a key role in non-ferrous metal structure forming processes. Die-casting process’s features are the strength and hardness of die casting on high, thin-walled castings with complex shape can be cast, and the production is efficient. The die-casting die is the key for the process of die casting, its quality decides the quality and accuracy of castings, and the design of the die-casting die affects its quality and operating life directly. Therefore, designing the die-casting die is the key to technological progress; it is also an important factor in the development of mold.Based mainly on parts of the design integrity of the structure and size, it scheme out the required spare parts. Design elements include: design of gating system, forming part design, core-pulling mechanism design, the ejector design and the mold body structure design. According to the shape of features , parts size and accuracy, the author selected the appropriate die casting machine, through the exactly calculate and consult design handbooks, confirm the size and accuracy of the forming part and mold body structure, it also makes particular instruction on the material selection and the requirements of the heat treatment, with theoretical basis, plotting out pictorial drawing and casting drawing of the parts by using computer software to ensure the manufacture of die-casting die.Based on the datum, use flat side gating system which can reduce pouring molten metal on the impact of cores, it ensure the technological parameter of the mold: the allowance of the casting was 0.1~0.75mm, shrinkage rate was 0.4~0.7﹪, draft angle was 25′~45′. The size of the die-casting mold was 900×640×835mm, which satisfy the space of the die casting machine which is chosen. The core-pulling mechanism of the mold was optional side slider core-pulling mechanism, Introduced organizations selected two push plate. The diameter of the ejector pin with a cylindrical head was 26mm, and was also used as return pin. The stress of the ejector pin was conformance to the requirement by calculate. The simulation by computer shows that the mold works function normally, and it can dexterous and quickly to open.Keywords: die casting; die-casting mold; zinc alloy castings; subbase目录摘要 (I)Abstract (III)第1章绪论 (1)1.1课题意义 (1)1.1.1 压力铸造的特点 (1)1.1.2压铸模具设计的意义 (2)1.2压铸发展历史、现状及趋势 (2)1.2.1压铸的发展历史 (2)1.2.2我国压铸产业的发展 (3)1.2.3压铸产业的发展趋势 (4)1.3毕业设计内容 (5)第2章压铸模具的整体设计 (7)2.1 铸件工艺性分析 (7)2.1.1 铸件立体图及工程图 (7)2.1.2 铸件分型面确定 (8)2.1.3 浇注位置的确定 (8)2.2 压铸成型过程及压铸机选用 (9)2.2.1 卧式冷室压铸机结构 (9)2.2.2 压铸成型过程 (10)2.2.3压铸机型号的选用及其主要参数 (11)2.3 浇注系统设计 (11)2.3.1 带浇注系统铸件立体图 (11)2.3.2 内浇口设计 (12)2.3.3 横浇道设计 (12)2.3.4 直浇道设计 (14)2.3.5 排溢系统设计 (14)2.4 压铸模具的总体结构设计 (14)第3章成型零件及斜滑块结构设计 (17)3.1 成型零件设计概述 (17)3.2浇注系统成型零件设计 (17)3.3 铸件成型零件设计 (19)3.3.1 成型收缩率 (19)3.3.2 脱模斜度 (20)3.3.3 压铸件的加工余量 (20)3.3.4铸件成型尺寸的计算 (20)3.4 成型零件装配图 (23)3.5 斜滑块机构设计 (24)3.5.1 侧抽芯系统概述 (24)3.5.2 斜滑块机构基本结构 (25)3.5.3 斜滑块的拼合形式 (26)3.5.4 斜滑块的导滑形式 (26)3.5.5 斜滑块尺寸设计 (26)3.5.6 斜滑块抽芯机构表面粗糙度和材料选择 (28)3.5.7 弹簧限位销设计 (28)3.5.8 斜滑块抽芯机构立体图和装配图 (28)第4章推出机构和模体设计 (30)4.1 推出机构设计 (30)4.1.1 推出机构概述 (30)4.1.2 推杆设计 (30)4.1.3 推板导向及限位装置设计 (32)4.1.4 复位机构设计 (32)4.1.5 推出、复位零件的表面粗糙度、材料及热处理后的硬度 (34)4.1.6 推出机构装配工程图及立体图 (34)4.2 模体设计 (36)4.2.1 模体设计概述 (36)4.2.2 模体尺寸 (37)4.2.3模板导向的尺寸 (37)4.2.4模体构件的表面粗糙度和材料选择 (38)4.3 模具总装图及工作过程模拟 (38)4.3.1 模具总装立体图 (38)4.3.2 模具工作过程模拟图 (38)第5章结论 (41)参考文献 (42)致谢 (44)附录 (45)第1章绪论1.1课题意义1.1.1 压力铸造的特点高压力和高速度是压铸中熔融合金充填成型过程的两大特点。
- 1、下载文档前请自行甄别文档内容的完整性,平台不提供额外的编辑、内容补充、找答案等附加服务。
- 2、"仅部分预览"的文档,不可在线预览部分如存在完整性等问题,可反馈申请退款(可完整预览的文档不适用该条件!)。
- 3、如文档侵犯您的权益,请联系客服反馈,我们会尽快为您处理(人工客服工作时间:9:00-18:30)。
锌合金底盘座铸件压铸模具设计The Die-casting Mold Design of ZincSubbase Casting摘 要压力铸造是目前成型有色金属铸件的重要成型工艺方法。
压铸的工艺特点是铸件的强度和硬度较高,形状较为复杂且铸件壁较薄,而且生产率极高。
压铸模具是压力铸造生产的关键,压铸模具的质量决定着压铸件的质量和精度,而模具设计直接影响着压铸模具的质量和寿命。
因此,模具设计是模具技术进步的关键,也是模具发展的重要因素。
根据零件的结构和尺寸设计了完整的模具。
设计内容主要包括:浇注系统设计、成型零件设计、抽芯机构设计、推出机构设计以及模体结构设计。
根据铸件的形状特点、零件尺寸及精度,选定了合适的压铸机,通过准确的计算并查阅设计手册,确定了成型零件以及模体的尺寸及精度,在材料的选取及热处理要求上也作出了详细说明,并在结合理论知识的基础上,借助于计算机辅助软件绘制了各部分零件及装配体的立体图和工程图,以保障模具的加工制造。
根据有关资料,采用扁平侧面浇注系统,降低了浇注时金属液对型芯的冲击,确定了铸造工艺参数:铸件加工余量取0.1~0.75mm ,收缩率为0.4~0.7﹪,脱模斜度为25′~45′。
模具整体尺寸为900×640×835mm ,符合所选压铸机安装空间。
抽芯采用斜滑块机构,拼合形式为两瓣式。
推出机构采用4根端面直径26mm的圆截面推杆,推杆兼复位杆作用。
经计算,推杆受力符合要求。
通过电脑模拟显示,模具能够正常工作,开启灵活。
关键词:压力铸造;压铸模具;锌合金铸件;底盘座AbstractDie-casting molding technology is playing a key role in non-ferrous metal structure forming processes. Die-casting process’s features are the strength and hardness of die casting on high, thin-walled castings with complex shape can be cast, and the production is efficient. The die-casting die is the key for the process of die casting, its quality decides the quality and accuracy of castings, and the design of the die-casting die affects its quality and operating life directly. Therefore, designing the die-casting die is the key to technological progress; it is also an important factor in the development of mold.Based mainly on parts of the design integrity of the structure and size, it scheme out the required spare parts. Design elements include: design of gating system, forming part design, core-pulling mechanism design, the ejector design and the mold body structure design. According to the shape of features , parts size and accuracy, the author selected the appropriate die casting machine, through the exactly calculate and consult design handbooks, confirm the size and accuracy of the forming part and mold body structure, it also makes particular instruction on the material selection and the requirements of the heat treatment, with theoretical basis, plotting out pictorial drawing and casting drawing of the parts by using computer software to ensure the manufacture of die-casting die.Based on the datum, use flat side gating system which can reduce pouring molten metal on the impact of cores, it ensure the technological parameter of the mold: the allowance of the casting was 0.1~0.75mm, shrinkage rate was 0.4~0.7﹪, draft angle was 25′~45′. The size of the die-casting mold was 900×640×835mm, which satisfy the space of the die casting machine which is chosen. The core-pulling mechanism of the mold was optional side slider core-pulling mechanism, Introduced organizations selected two push plate. Thediameter of the ejector pin with a cylindrical head was 26mm, and was also used as return pin. The stress of the ejector pin was conformance to the requirement by calculate. The simulation by computer shows that the mold works function normally, and it can dexterous and quickly to open.Keywords: die casting; die-casting mold; zinc alloy castings; subbase目录摘要 (I)Abstract (II)第1章绪论 (1)1.1课题意义 (1)1.1.1 压力铸造的特点 (1)1.1.2压铸模具设计的意义 (2)1.2压铸发展历史、现状及趋势 (2)1.2.1压铸的发展历史 (2)1.2.2我国压铸产业的发展 (3)1.2.3压铸产业的发展趋势 (4)1.3毕业设计内容 (5)第2章压铸模具的整体设计 (7)2.1 铸件工艺性分析 (7)2.1.1 铸件立体图及工程图 (7)2.1.2 铸件分型面确定 (8)2.1.3 浇注位置的确定 (8)2.2 压铸成型过程及压铸机选用 (9)2.2.1 卧式冷室压铸机结构 (9)2.2.2 压铸成型过程 (10)2.2.3压铸机型号的选用及其主要参数 (11)2.3 浇注系统设计 (11)2.3.1 带浇注系统铸件立体图 (11)2.3.2 内浇口设计 (12)2.3.3 横浇道设计 (12)2.3.4 直浇道设计 (14)2.3.5 排溢系统设计 (14)2.4 压铸模具的总体结构设计 (14)第3章成型零件及斜滑块结构设计 (17)3.1 成型零件设计概述 (17)3.2浇注系统成型零件设计 (17)3.3 铸件成型零件设计 (19)3.3.1 成型收缩率 (19)3.3.2 脱模斜度 (20)3.3.3 压铸件的加工余量 (20)3.3.4铸件成型尺寸的计算 (20)3.4 成型零件装配图 (23)3.5 斜滑块机构设计 (24)3.5.1 侧抽芯系统概述 (24)3.5.2 斜滑块机构基本结构 (25)3.5.3 斜滑块的拼合形式 (26)3.5.4 斜滑块的导滑形式 (26)3.5.5 斜滑块尺寸设计 (26)3.5.6 斜滑块抽芯机构表面粗糙度和材料选择 (28)3.5.7 弹簧限位销设计 (28)3.5.8 斜滑块抽芯机构立体图和装配图 (28)第4章推出机构和模体设计 (30)4.1 推出机构设计 (30)4.1.1 推出机构概述 (30)4.1.2 推杆设计 (30)4.1.3 推板导向及限位装置设计 (32)4.1.4 复位机构设计 (32)4.1.5 推出、复位零件的表面粗糙度、材料及热处理后的硬度 (34)4.1.6 推出机构装配工程图及立体图 (34)4.2 模体设计 (36)4.2.1 模体设计概述 (36)4.2.2 模体尺寸 (37)4.2.3模板导向的尺寸 (37)4.2.4模体构件的表面粗糙度和材料选择 (38)4.3 模具总装图及工作过程模拟 (38)4.3.1 模具总装立体图 (38)4.3.2 模具工作过程模拟图 (38)第5章结论 (41)参考文献 (42)致谢 (44)附录 (45)第1章绪论1.1课题意义1.1.1 压力铸造的特点高压力和高速度是压铸中熔融合金充填成型过程的两大特点。
压铸中常用的压射比压在几兆帕至几十兆帕范围内,有时甚至高达500MPa。
其充填速度一般在0.5~120m/s范围内,它的充填时间很短,一般为0.01~0.2s,最短的仅为千分之几秒。
因此,利用这种方法生产的产品有着其独特的优点。
可以得到薄壁、形状复杂但轮廓清晰的铸件。
其压铸出的最小壁厚:锌合金为0.3mm;铝合金为0.5mm。
铸出孔最小直径为0.7mm。
铸出螺纹最小螺距0.75mm。
对于形状复杂,难以或不能用切削加工制造的零件,即使产量小,通常也采用压铸生产,尤其当采用其他铸造方法或其他金属成型工艺难以制造时,采用压铸生产最为适宜。