液蜡及氯化石蜡简介
氯化石蜡

氯化石蜡产品性质:氯化石蜡又名氯烃,是石蜡经氯化后所得产品,是石蜡烃的氯化衍生物。
按其含氯量不同主要有氯化石蜡-42,氯化石蜡-52,氯化石蜡-70三种,由于其具有良好的电绝缘性、耐火及阻燃等特性以及价格便宜的特点,故其广泛应用于生产电缆料、地板料、软管、人造革、橡胶等制品以及应用于涂料、润滑油等的添加剂。
在我国增塑剂系列中,氯化石蜡是仅次于DOP、DBP产量占第三位的品种。
氯化石蜡-42:又名氯烃-42,分子式是C25H45CL7,分子量594(平均值),含氯量为42±2%。
氯化石蜡-42是浅黄色清澈粘稠液体,无味、无毒、不燃不爆,挥发性极微,无毒。
不溶于水和乙醇。
但与水混合形成稳定的乳液。
能溶于大多数有机溶剂。
凝固点-30℃以下,热分解温度120℃,分解生成氯化氢气体。
遇锌、铁等金属氧化物会促进其分解。
氯化石蜡-52:又名氯烃-52,分子式是C15H26CL6,分子量420(平均值),含氯量为50±2%。
氯化石蜡-52是浅黄色清彻粘稠液体,无味、无毒、不燃烧。
不溶于水,微溶于醇,能溶于苯、醚。
相对密度1.235~1.255(d425),凝固点-30℃以下,热分解温度140℃,折光率1.505~1.515。
氯化石蜡-70:又名氯烃-70,分子式是C25H30CL22,分子量401.42(平均值),含氯量为70±2%。
氯化石蜡-70为白色或淡黄色粉末状树脂,相对密度1.65~1.70,软化点≥95℃(95~120℃)不溶于水和低级醇,可溶于矿物油、苯、二甲苯等芳烃溶剂,不易燃烧。
应用领域:适用于各类产品阻燃之用。
应用在塑料、橡胶、纤维等工业领域作增塑剂,织物和包装材料的表面处理剂,粘接材料和涂料的改良剂,高压润滑和金属切削加工的抗磨剂,防霉剂、防水剂,油墨添加剂等。
广泛用于生产电缆料、地板料、软管、人造革、橡胶等制品。
包装及贮存:塑料编织袋包装,每袋25公斤,于阴凉通风、干燥处贮存。
氯化石蜡介绍

氯化石蜡产品介绍1、产品介绍中文名称:氯化石蜡—52英文名称:Chloro Paraffin—52分子式:C15H26Cl6分子量:419性状:本品为浅黄色至黄色透明液体,不溶于水,不燃、不爆、无毒,不挥发,阻燃,能溶于许多溶剂,不溶于水及乙醇。
与聚氯乙烯、天然橡胶、聚氨酯等高聚物有较好的相溶性,绝缘性好,加热见光发生分解颜色加深。
受热超过一定温度时(通常为120℃)会缓缓分解,放出氯化氢气体。
用途:主要作为聚氯乙烯、天然橡胶、聚氨酯等高聚物的增塑剂,纤维防水浸渍剂,润滑油抗凝剂、抗极压剂。
2、市场概况(1)生产现状氯化石蜡是石蜡烃的氯化衍生物,与PVC树脂、天然橡胶等具有良好的相容性;尤其是氯化石蜡具有不燃性、介电性好等优点,使其成为一种独特的阻燃型增塑剂;还可以用作油类添加剂、纺织润滑剂、耐火防火纺织品涂覆剂、1、2丁腈橡胶与氯丁橡胶的黏接剂等。
氯化石蜡-52是一种浅黄色至黄色的油状黏稠液体,凝固点低于-20℃,溶于苯、醚,微溶于醇,不溶于水。
氯化石蜡-52主要用作阻燃剂和聚氯乙烯的助增塑剂,其挥发性低、电性能好,广泛应用于电缆料、地板、压延板材、塑胶质鞋类制品,也可用于橡胶制品;与聚氯乙烯等黏合剂制成磁漆,可用作防火涂料。
在我国增塑剂系列中,氯化石蜡是仅次于DOP、DBP 产量占第三位的品种。
氯化石蜡主要品种有氯蜡-52、氯蜡-42和氯蜡-70等,其中前两种产量占氯化石蜡的90%以上。
氯化石蜡作为辅助增塑剂和阻燃剂,广泛应用于塑料制品、涂料、输送带、塑胶等领域,消费结构为:增塑剂63%、润滑油15%、阻燃剂8%、橡胶2%、其他7%。
我国塑料增塑剂DOP、DBP价格高,许多塑料生产厂家转向价格相对较低的氯化石蜡。
氯化石蜡是企业平衡氯气的主要产品,所需的生产原料相对宽松易得,近年来氯化石蜡需求发展过快,国内市场竞争也较为激烈。
我国是氯化石蜡生产大国,2007年总产能为70万吨/年,产量48万吨/年。
氯化石蜡用途
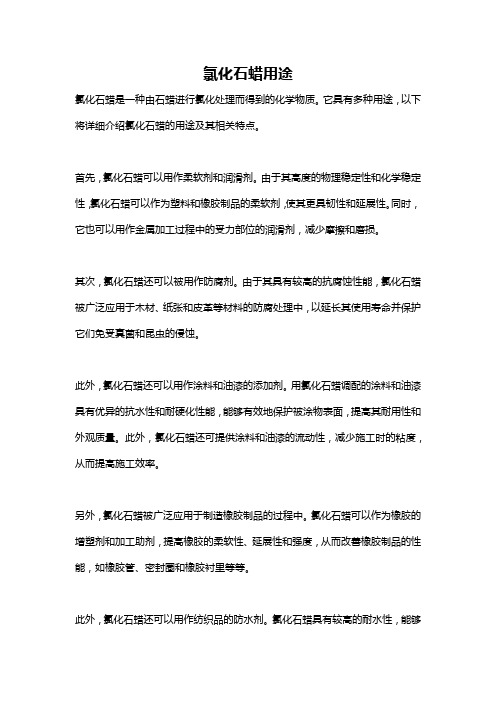
氯化石蜡用途氯化石蜡是一种由石蜡进行氯化处理而得到的化学物质。
它具有多种用途,以下将详细介绍氯化石蜡的用途及其相关特点。
首先,氯化石蜡可以用作柔软剂和润滑剂。
由于其高度的物理稳定性和化学稳定性,氯化石蜡可以作为塑料和橡胶制品的柔软剂,使其更具韧性和延展性。
同时,它也可以用作金属加工过程中的受力部位的润滑剂,减少摩擦和磨损。
其次,氯化石蜡还可以被用作防腐剂。
由于其具有较高的抗腐蚀性能,氯化石蜡被广泛应用于木材、纸张和皮革等材料的防腐处理中,以延长其使用寿命并保护它们免受真菌和昆虫的侵蚀。
此外,氯化石蜡还可以用作涂料和油漆的添加剂。
用氯化石蜡调配的涂料和油漆具有优异的抗水性和耐硬化性能,能够有效地保护被涂物表面,提高其耐用性和外观质量。
此外,氯化石蜡还可提供涂料和油漆的流动性,减少施工时的粘度,从而提高施工效率。
另外,氯化石蜡被广泛应用于制造橡胶制品的过程中。
氯化石蜡可以作为橡胶的增塑剂和加工助剂,提高橡胶的柔软性、延展性和强度,从而改善橡胶制品的性能,如橡胶管、密封圈和橡胶衬里等等。
此外,氯化石蜡还可以用作纺织品的防水剂。
氯化石蜡具有较高的耐水性,能够使纺织品表面形成一层防水薄膜,防止水分渗透,保持纺织品的干燥性和舒适性。
此外,氯化石蜡还可以用于制造蜡烛。
由于其具有不易燃烧的特点,氯化石蜡在制造蜡烛时可以起到调节燃烧速度和防止滴蜡的作用,使蜡烛更加安全和稳定。
最后,氯化石蜡还可以用于制造涂料和印刷油墨的添加剂,用于制造脱脂剂,用于制造医药产品以及化妆品的添加剂等等。
综上所述,氯化石蜡具有广泛的用途,包括柔软剂和润滑剂、防腐剂、涂料和油漆添加剂、橡胶制品、纺织品防水剂、蜡烛制造、涂料和印刷油墨添加剂等等。
随着科学技术的不断发展,氯化石蜡的应用领域将继续扩展,并在各个领域中发挥重要作用。
氯化石蜡安全技术说明书
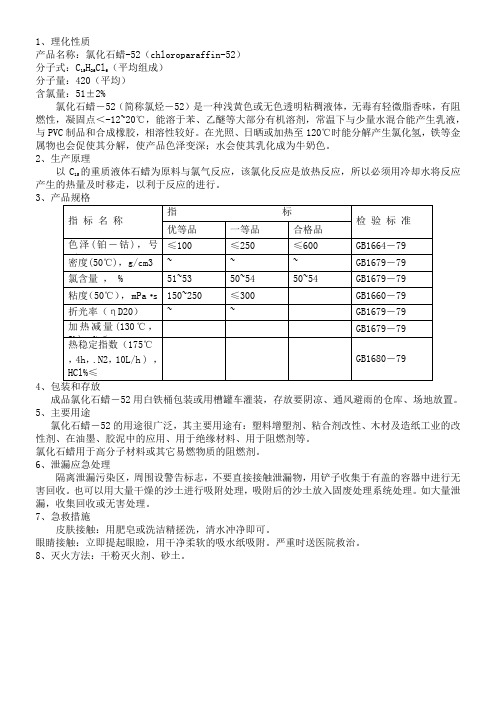
1、理化性质
产品名称:氯化石蜡-52(chloroparaffin-52)
分子式:C 15H 26Cl 6(平均组成)
分子量:420(平均)
含氯量:51±2%
氯化石蜡-52(简称氯烃-52)是一种浅黄色或无色透明粘稠液体,无毒有轻微脂香味,有阻燃性,凝固点<-12~20℃,能溶于苯、乙醚等大部分有机溶剂,常温下与少量水混合能产生乳液,与PVC 制品和合成橡胶,相溶性较好。
在光照、日晒或加热至120℃时能分解产生氯化氢,铁等金属物也会促使其分解,使产品色泽变深;水会使其乳化成为牛奶色。
2、生产原理
以C 15的重质液体石蜡为原料与氯气反应,该氯化反应是放热反应,所以必须用冷却水将反应
产生的热量及时移走,以利于反应的进行。
3
4 成品氯化石蜡-52用白铁桶包装或用槽罐车灌装,存放要阴凉、通风避雨的仓库、场地放置。
5、主要用途
氯化石蜡-52的用途很广泛,其主要用途有:塑料增塑剂、粘合剂改性、木材及造纸工业的改性剂、在油墨、胶泥中的应用、用于绝缘材料、用于阻燃剂等。
氯化石蜡用于高分子材料或其它易燃物质的阻燃剂。
6、泄漏应急处理
隔离泄漏污染区,周围设警告标志,不要直接接触泄漏物,用铲子收集于有盖的容器中进行无害回收。
也可以用大量干燥的沙土进行吸附处理,吸附后的沙土放入固废处理系统处理。
如大量泄漏,收集回收或无害处理。
7、急救措施
皮肤接触:用肥皂或洗洁精搓洗,清水冲净即可。
眼睛接触:立即提起眼睑,用干净柔软的吸水纸吸附。
严重时送医院救治。
8、灭火方法:干粉灭火剂、砂土。
液蜡及氯化石蜡简介

液蜡及氯化石蜡简介1、前言石油蜡类产品是一类附加值很高的石油产品,由于其具有许多特殊的理化性质,被广泛应用于社会生活各个领域。
随着科学技术的不断发展,对石油蜡类产品的要求愈来愈高,一方面对产品质量要求不断提高,另一方面由于应用领域不断拓宽,石油蜡类产品的功能用途也在不断扩大。
液蜡又称石蜡油,无色、无臭、无味,无萤光的油状液体,由重油经减压蒸馏而获得。
熔点在40℃以下的从C10到C18的各种正构烷烃组成的混合物。
主要用途是可以做为生产氯化石蜡的原料,还有洗涤剂原料、化妆品、日用品稀释剂、溶剂等。
2、液蜡产品及生产工艺液蜡产品有三种,即C10-C13正构烷烃(轻蜡I);C11-C14正构烷烃(轻蜡II)和C14-C17重液蜡;C9以下为轻蜡;C17以上为重蜡。
液蜡下游产品氯化石蜡是石蜡经氯化后所得产品,是石蜡烃的氯化衍生物。
适用于各类产品阻燃之用,应用在塑料、橡胶、纤维等工业领域作增塑剂,织物和包装材料的表面处理剂,粘接材料和涂料的改良剂,高压润滑和金属切削加工的抗磨剂,防霉剂、防水剂,油墨添加剂等。
广泛用于生产电缆料、地板料、软管、人造革、橡胶等制品。
我国重液蜡的生产有分子筛脱蜡(典型的分子筛脱蜡工艺有Molex法和ISO 一SIV法)和异丙醇-尿素脱蜡(IUDW)两种生产工艺。
此外也有用溶剂脱蜡和压榨脱蜡法生产一部分质量较低的液蜡。
3、液蜡主要生产工艺对比分析3.1、分子筛法和尿素脱蜡法实验对比分析(1)1975年大岛洋三经过试验室认真研究证明,异丙醇-尿素脱蜡的液蜡比分子筛脱蜡纯度高。
(2)分子筛脱蜡能耗较大,因现在分子筛催化剂价格昂贵,消耗量大,每生产1t液蜡产品能耗3.2万MJ左右,而异丙醇-尿素脱蜡能耗为2.5万MJ左右。
(3)异丙醇-尿素脱蜡不需要预处理,即可生产重液蜡,也可生产轻液蜡,对市场的适应性更强。
(4)异丙醇-尿素脱蜡工艺流程较复杂,但投资费用低,建设周期短,在工艺上较成熟。
氯化石蜡用途

氯化石蜡用途氯化石蜡是一种合成材料,由石蜡经过氯化反应得到。
它具有许多重要的用途,被广泛应用于各个领域。
氯化石蜡在塑料工业中有着重要的地位。
它可以作为增塑剂,用于改变塑料的性能和加工工艺。
通过添加适量的氯化石蜡,可以提高塑料的柔软度、延展性和耐热性,同时改善塑料的加工性能。
氯化石蜡还可以提高塑料的耐寒性,使其在低温环境下仍能保持良好的性能。
因此,氯化石蜡在塑料制品中的应用非常广泛,包括塑料薄膜、塑料管材、塑料包装等。
氯化石蜡在涂料工业中也有着重要的用途。
它可以作为涂料的添加剂,用于改善涂料的性能。
氯化石蜡可以提高涂料的附着力和耐久性,增加涂层的硬度和耐磨性。
同时,它还可以改善涂料的流平性和抗结皮性,使涂料施工更加方便和美观。
因此,氯化石蜡被广泛应用于各类涂料,包括建筑涂料、汽车涂料、木器涂料等。
氯化石蜡还在橡胶工业中发挥着重要作用。
它可以作为橡胶的增塑剂,改善橡胶的柔软度和可加工性。
氯化石蜡可以提高橡胶的抗老化性能和耐候性,延长橡胶制品的使用寿命。
同时,它还可以改善橡胶的硬度和强度,提高橡胶制品的耐磨性和耐油性。
因此,氯化石蜡在橡胶制品中的应用非常广泛,包括橡胶密封件、橡胶管件、橡胶轮胎等。
氯化石蜡还可以用作蜡烛的添加剂,提高蜡烛的燃烧性能和稳定性。
氯化石蜡可以增加蜡烛的燃点和燃烧时间,使蜡烛更加明亮和持久。
同时,它还可以改善蜡烛的燃烧性能,减少烟雾和残渣的产生。
因此,氯化石蜡在蜡烛制造中被广泛使用。
氯化石蜡具有广泛的用途,被应用于塑料工业、涂料工业、橡胶工业和蜡烛制造等领域。
它可以改善材料的性能和加工工艺,提高产品的质量和性能。
随着科技的不断进步,氯化石蜡的用途还将不断拓展和创新,为各行各业带来更多的发展机遇。
氯化石蜡项目机会分析报告
一、氯化石蜡简介氯化石蜡又称氯烃,是石蜡烃的氯化衍生物,具有挥发性低、阻燃、电绝缘性良好、价廉等优点,可用作阻燃剂和聚氯乙烯助增塑剂,广泛用于塑料、电缆料、地板料、软管、人造革、橡胶等制品,也作为涂料、润滑油等的添加剂。
由于其原料来源于丰富的石油,又具有阻燃、成本低等各种优良性能,成为不可缺少的大吨位精细化工产品,同时也是氯碱工艺平衡氯气的重要产品。
氯化石蜡-42,又名氯烃-42,分子式是C25H45Cl7,平均分子量594,含氯量为42±2%。
氯化石蜡-42是浅黄色清澈粘稠液体,无味、无毒、不燃不爆,挥发性极微,无毒,不溶于水和乙醇,但与水混合形成稳定的乳液,能溶于大多数有机溶剂,凝固点-30℃以下。
热分解温度120℃,分解生成氯化氢气体,遇锌、铁等金属氧化物会促进其分解。
氯化石蜡-52,又名氯烃-52,分子式C15H26C l6,平均分子量419.09。
含氯量为52±2%。
浅黄色至黄色黏稠液体,相对密度1.235~1.255,凝固点<-30℃,折射率1.505~1.515。
热分解温度140℃,溶于甲苯、环己酮、醋酸乙酯、氯化溶剂及烃类,微溶于乙醇,不溶于水,不燃,无毒。
氯化石蜡-70,又名氯烃-70,分子式是C25H30Cl22,平均分子量401.42,含氯量为70±2%。
氯化石蜡-70为白色或淡黄色粉末状树脂,相对密度1.65~1.70,软化点≥95℃(95~120℃)不溶于水和低级醇,可溶于矿物油、苯、二甲苯等芳烃溶剂,不易燃烧。
二、氯化石蜡主要应用(1)增塑剂氯化石蜡在PVC树脂软件制品生产中,广泛用作辅助增塑剂,也称为聚合物添加剂。
(2)润滑油添加剂各种氯化石蜡产品都可以用来改进工艺润滑油,如切削油、压延油和轴承油等的性能,润滑油(脂)中添加微量的氯化石蜡,可使其凝固点降低10~15o C,提高其耐压能力和耐腐蚀性。
(3)阻燃剂氯化石蜡也可用作塑料、橡胶和纺织品的阻燃剂,它与含锑或磷增效剂形成高效阻燃剂,以提高塑料、橡胶和纺织品的耐火性能(4)涂料氯化石蜡广泛应用于以过氯乙烯树脂、氯化橡胶和其他聚合物为基础制造的化学性能稳定、耐火耐水的涂料,能改善涂料的成膜性,防止油膜干后龟裂。
液蜡及氯化石蜡简介
液蜡及氯化石蜡简介1、前言石油蜡类产品是一类附加值很高的石油产品,由于其具有许多特殊的理化性质,被广泛应用于社会生活各个领域。
随着科学技术的不断发展,对石油蜡类产品的要求愈来愈高,一方面对产品质量要求不断提高,另一方面由于应用领域不断拓宽,石油蜡类产品的功能用途也在不断扩大。
液蜡又称石蜡油,无色、无臭、无味,无萤光的油状液体,由重油经减压蒸馏而获得。
熔点在40℃以下的从C10到C18的各种正构烷烃组成的混合物。
主要用途是可以做为生产氯化石蜡的原料,还有洗涤剂原料、化妆品、日用品稀释剂、溶剂等。
2、液蜡产品及生产工艺液蜡产品有三种,即C10-C13正构烷烃(轻蜡I);C11-C14正构烷烃(轻蜡II)和C14-C17重液蜡;C9以下为轻蜡;C17以上为重蜡。
液蜡下游产品氯化石蜡是石蜡经氯化后所得产品,是石蜡烃的氯化衍生物。
适用于各类产品阻燃之用,应用在塑料、橡胶、纤维等工业领域作增塑剂,织物和包装材料的表面处理剂,粘接材料和涂料的改良剂,高压润滑和金属切削加工的抗磨剂,防霉剂、防水剂,油墨添加剂等。
广泛用于生产电缆料、地板料、软管、人造革、橡胶等制品。
我国重液蜡的生产有分子筛脱蜡(典型的分子筛脱蜡工艺有Molex法和ISO 一SIV法)和异丙醇-尿素脱蜡(IUDW)两种生产工艺。
此外也有用溶剂脱蜡和压榨脱蜡法生产一部分质量较低的液蜡。
3、液蜡主要生产工艺对比分析3.1、分子筛法和尿素脱蜡法实验对比分析(1)1975年大岛洋三经过试验室认真研究证明,异丙醇-尿素脱蜡的液蜡比分子筛脱蜡纯度高。
(2)分子筛脱蜡能耗较大,因现在分子筛催化剂价格昂贵,消耗量大,每生产1t液蜡产品能耗3.2万MJ左右,而异丙醇-尿素脱蜡能耗为2.5万MJ左右。
(3)异丙醇-尿素脱蜡不需要预处理,即可生产重液蜡,也可生产轻液蜡,对市场的适应性更强。
(4)异丙醇-尿素脱蜡工艺流程较复杂,但投资费用低,建设周期短,在工艺上较成熟。
氯化石蜡化学品安全说明书
氯化石蜡化学品安全说明书一、产品概述氯化石蜡是一种有机化合物,分子式为C26H49Cl,外观为白色晶体状固体。
其主要用途包括塑料材料的增塑剂、橡胶的保护剂、润滑油的添加剂等。
然而,氯化石蜡对人体和环境都具有一定的危害性,因此需严格遵守安全操作规程,以免造成安全事故。
二、物理和化学性质氯化石蜡的熔点为75℃,沸点为一般分子量的225~240℃,相对密度为0.97。
它难溶于水,但易溶于有机溶剂。
氯化石蜡的加热分解产生的刺激性气味是其被意识到对生命的危险的原因之一。
三、安全措施1.避免接触:氯化石蜡具有刺激性和腐蚀性,尤其是对皮肤、眼睛和粘膜有刺激作用,因此在操作过程中需要采取有效的工作保护措施,如戴防护手套、护目镜和口罩等。
2.防止火灾:氯化石蜡是易燃物质,遇到明火或高温会导致爆炸和火灾。
因此,在储存和使用时需注意防火防爆。
3.避免误食:氯化石蜡具有毒性,误食会对人体产生危害。
因此,在储存和使用时应将其放置在儿童无法触及的地方。
4.确保通风:氯化石蜡在使用时会产生有害气体,因此应保持良好的通风条件,避免将其吸入肺部引发呼吸道疾病。
5.安全处理废弃物:在处理废弃物时,需遵守环保相关规定,采取安全的处理方式。
四、急救措施1.吸入氯化石蜡的气味时,应立即移动到通风良好的地方,保持呼吸顺畅,如有呼吸困难,应立即送往医院抢救。
2.皮肤接触氯化石蜡时,应立即用大量清水冲洗至少15分钟,并去掉被污染的衣物和鞋袜,立即送往医院治疗。
3.如果不慎将氯化石蜡误入口中,应立即用大量清水漱口,并送往医院治疗。
五、包装和储存氯化石蜡的包装应符合国家规定的危险化学品包装标准。
在储存时,应避免阳光直射、高温、潮湿和火源。
储存过程中需要定期检查包装是否完好,是否存在泄漏等危险。
六、环境保护在使用氯化石蜡时,应遵守国家法律法规、规范、标准和行业标准,避免对环境造成污染。
废弃氯化石蜡应安全处理,避免直接倾倒到地面、水源、下水道等处,以免对环境造成影响。
中链氯化石蜡 液质
中链氯化石蜡液质
中链氯化石蜡是一种液体形态的物质,属于氯代烃类,其分子中碳链长度介于长链氯化石蜡和短链氯化石蜡之间。
中链氯化石蜡具有良好的阻燃性、热稳定性和化学稳定性,因此被广泛应用于塑料、橡胶、涂料、油漆、油墨、胶黏剂、纺织品等领域,作为增塑剂、阻燃剂、软化剂、润滑剂等使用。
需要注意的是,中链氯化石蜡在环境中的持久性和生物累积性较强,可能对人体健康和生态环境造成不利影响。
因此,在使用中链氯化石蜡时,需要遵守相关的环保法规和安全操作规程,控制其使用量,减少对环境的影响。
此外,中链氯化石蜡的液质可能因生产方法和用途不同而有所差异,具体需要根据实际情况进行分析和评估。
- 1、下载文档前请自行甄别文档内容的完整性,平台不提供额外的编辑、内容补充、找答案等附加服务。
- 2、"仅部分预览"的文档,不可在线预览部分如存在完整性等问题,可反馈申请退款(可完整预览的文档不适用该条件!)。
- 3、如文档侵犯您的权益,请联系客服反馈,我们会尽快为您处理(人工客服工作时间:9:00-18:30)。
液蜡及氯化石蜡简介
1、前言
石油蜡类产品是一类附加值很高的石油产品,由于其具有许多特殊的理化性质,被广泛应用于社会生活各个领域。
随着科学技术的不断发展,对石油蜡类产品的要求愈来愈高,一方面对产品质量要求不断提高,另一方面由于应用领域不断拓宽,石油蜡类产品的功能用途也在不断扩大。
液蜡又称石蜡油,无色、无臭、无味,无萤光的油状液体,由重油经减压蒸馏而获得。
熔点在40℃以下的从C10到C18的各种正构烷烃组成的混合物。
主要用途是可以做为生产氯化石蜡的原料,还有洗涤剂原料、化妆品、日用品稀释剂、溶剂等。
2、液蜡产品及生产工艺
液蜡产品有三种,即C10-C13正构烷烃(轻蜡I);C11-C14正构烷烃(轻蜡II)和C14-C17重液蜡;C9以下为轻蜡;C17以上为重蜡。
液蜡下游产品氯化石蜡是石蜡经氯化后所得产品,是石蜡烃的氯化衍生物。
适用于各类产品阻燃之用,应用在塑料、橡胶、纤维等工业领域作增塑剂,织物和包装材料的表面处理剂,粘接材料和涂料的改良剂,高压润滑和金属切削加工的抗磨剂,防霉剂、防水剂,油墨添加剂等。
广泛用于生产电缆料、地板料、软管、人造革、橡胶等制品。
我国重液蜡的生产有分子筛脱蜡(典型的分子筛脱蜡工艺有Molex法和ISO 一SIV法)和异丙醇-尿素脱蜡(IUDW)两种生产工艺。
此外也有用溶剂脱蜡和压榨脱蜡法生产一部分质量较低的液蜡。
3、液蜡主要生产工艺对比分析
3.1、分子筛法和尿素脱蜡法实验对比分析
(1)1975年大岛洋三经过试验室认真研究证明,异丙醇-尿素脱蜡的液蜡比分子筛脱蜡纯度高。
(2)分子筛脱蜡能耗较大,因现在分子筛催化剂价格昂贵,消耗量大,每生产1t液蜡产品能耗3.2万MJ左右,而异丙醇-尿素脱蜡能耗为2.5万MJ左右。
(3)异丙醇-尿素脱蜡不需要预处理,即可生产重液蜡,也可生产轻液蜡,对市场的适应性更强。
(4)异丙醇-尿素脱蜡工艺流程较复杂,但投资费用低,建设周期短,在工艺
上较成熟。
3.2、分子筛法和尿素脱蜡法技术经济对比分析
目前国内分子筛脱蜡和尿素脱蜡生产液蜡主要技术经济指标比较见表1和表2。
表1 分子筛脱蜡及异丙醇尿素脱蜡物料平衡
表2 加工每吨原料的消耗指标
从表1、表2数据可看出,异丙醇尿素脱蜡装置液蜡损失、能耗都较分子筛脱蜡低。
用户也反映,异丙醇尿素脱蜡产品杂质少,质量较好。
近年来,抚顺石油化工研究院在改进溶剂回收方法方面取得较好结果,有可能简化现有工艺过程减少原材料消耗,进一步降低异丙醇尿素脱蜡成本。
目前新建分子筛脱蜡工艺和尿素脱蜡工艺生产液蜡装置主要技术经济指标比较见表3。
表3 引进的两种脱蜡工艺投资及消耗比较
从表3数据看,引进国外分子筛脱蜡技术生产能耗低,用户反映产品质量稳定,但引进投资费用相当高,且分子筛脱蜡工艺不适于生产干点高于280℃的重液蜡。
而异丙醇尿素脱蜡工艺既可生产轻液蜡,也可生产重液蜡,对市场应变能力强。
通过国内外液蜡生产工艺技术经济比较可以看出,异丙醇尿素脱蜡工艺在投资、产品品种、质量、价格、装置灵活性等方面都占优势。
从技术发展看,采用异丙醇尿素脱蜡工艺比较现实可行。
4、液蜡市场分析
4.1、国内现有液体石蜡生产概况
目前我国主要企业液蜡产能约在44.3万吨/年左右。
我国现有十几套重液蜡生产装置,主要分布于辽宁、黑龙江、湖北、山东、江苏等省,详见表4。
表4 我国液蜡生产企业情况
4.2、我国液体石蜡进出口金额及数量情况
我国液蜡2003和2004年进口量达到2.3万吨以来,2005-2008年一直保持在不到2万吨的水平。
2009年我国液蜡进口出现猛增势头,5月份单月进口量就达0.5万吨左右,2009年1-10月我国液蜡累计进口达到2.45万吨高于2003年全年2.33万吨的历史最高水平;相比2008年同期的1.27万吨,同比增长92.91%;从进口价格来看2009年1-10月均价为1086.73美元/吨,比2008年全年均价1599.62美元/吨,下降了32.1%,这个可以作为解释2009年液蜡进口数量猛增的主要原因之一。
2002年至2009年10月我国液体石蜡及重质液体石蜡进出口数量及金额情况见表5:
表5 2002-2009年我国液体石蜡进出口金额及数量情况表
单位:万吨;万元(美元)
4.3、我国石蜡供需现状
2005-2008年我国石蜡表观消费情况见表6:
表6 2005-2008年中国石蜡表观消费量
单位:万吨
据业内人士统计,2003-2008年,全球石蜡年贸易量一直保持500万吨左右。
我国每年出口的石蜡以60万吨计,约占全球石蜡贸易量的12%。
5、氯化石蜡市场分析
氯化石蜡,是指由高级石蜡烃经深度氯化制成的氯化产物,是一种耗氯量大,产量较大的精细化工产品,具有优异的阻燃性和稳定的化学性质,为市场上的长期紧俏产品,也是PVC生产中大量使用的增塑剂的第二大品种。
氯化石蜡做作为辅助增塑剂和阻燃剂,广泛应用于塑料制品、涂料、输送带、塑胶等领域。
我国塑料工业主要增塑剂DOP、DBP价格高,许多塑料生产厂家转向价格相对较低的氯化石蜡。
氯化石蜡又是各氯碱企业平衡氯气的主要产品,所需的生产原料相对宽松易得,近年来氯化石蜡需求不断增加,具有广阔的发展前景。
我国是世界上的主要氯化石蜡生产国和出口国之一,出口的品种主要为氯烃-42、氯烃-52和氯烃-70。
2000-2009年我国“其他人造蜡及调制蜡”进出口(我国氯化石蜡进出口海关编码归置于“其他人造蜡及调制蜡”范畴)详细情况参见表7:
表7 1995-2009年我国其他人造蜡及调制蜡进出口数量及金额情况表
单位:万吨;万元(美元)
6、结论
专家预言,21世纪初期将是石蜡基原油走俏的年代。
因为美国、欧洲、中东等地的原油是贫蜡原油,这对上述地区的炼油业,将是一个严重的挑战,而对于含蜡原油极为丰富的我国却提供了一个大好的发展机遇。
因此,我们应该充分珍视这个独有的资源优势和可贵机遇,在特种蜡、微晶蜡及高熔点石蜡等产品上加大科技投入,提高特种蜡、微晶蜡及高熔点石蜡的比例,充分发挥石蜡的特性
优势,使产品结构与市场衔接,从而达到改善产品结构,提高企业经济效益之目的。
从国外文献看,各国对液蜡的综合利用开发方兴未艾,而有关液蜡的加工、合成、改性、调制的专利报道层出不穷。
相比之下,我国液蜡在产品产量、质量、综合利用方面都显不足。
我国在液蜡利用方面尚处萌芽状态,需迎头赶上。
为此建议:
一、我国液蜡生产有两种工艺,其中一套异丙醇法尿素脱蜡装置运转近40年,证明有经济效益;分子筛脱蜡国内已有几套装置,但分子筛不抗水蒸汽,使用寿命短,能耗大,液蜡成本高。
与引进的Molex脱蜡工艺相比,显然差距较大。
建议近年内有条件的炼厂或采用尿素脱蜡工艺、或引进Molex工艺,建设若干套液蜡生产装置,以满足石油化工发展的急切需要。
二、氯化石蜡是液蜡最主要用途之一,国内有多家生产厂生产,其中有不少是有氯气资源的电化厂,但这些厂都没有液蜡资源。
因此,若新建液蜡生产装置,建议可选择一家或几家有氯气资源的电化厂或组成股份公司,这可能是较现实的方案之一。
这样既保证了液蜡的市场出路,若合股资金雄厚还可进一步合作开发液蜡下游高科技产品,如热熔粘合剂、香料等。
根据市场需要,建立通用化氯化石蜡生产装置,积极开发氯化石蜡系列产品和专用牌号,搞氯化石蜡“产品树”,提高装置开工率,增加市场应变能力。
建议开发的产品如下:①氯化石蜡系列产品和专用精细牌号;②溴氯化石蜡和溴化石蜡系列产品;③环氧改性氯化石蜡(环氧氯化石蜡,可作主增塑剂);④改性氯化石蜡(有机酸、胺、脲等改性);⑤氯化石蜡复合抗磨极压剂(改善锈蚀性);⑥在润滑油添加剂方面,我国应用不多,如果开发得好,将是氯化石蜡销售的第二大市场,目前已有不少润滑油生产企业把氯化石蜡作为润滑油的耐压添加剂销售,取得十分理想的效果,氯化石蜡作为金属加工中冷拨、冷轧、冷压的润滑“拉伸油”亦取得了良好的效果。
在国际市场上,高质量的氯化石蜡缺口较大,国内产品在国际市场上有很强的价格优势。
另外,国内氯化石蜡的需求增长也较快,2005年国际市场需求达8万吨,国内市场需求为2万吨,发展氯化石蜡市场前景广阔。
三、近年来,美国、日本及西欧一些国家都进口大量的液蜡。
这说明国外液
蜡的应用范围和需用量还在加大,我们也应扩大我国液蜡的数量,提高质量,拓展用途。
我国原油特点之一是含蜡量高,并且国产高蜡原油正构烷烃含量高,具有扩大生产液蜡的资源条件。
因此应抓住这一历史机遇。
扩大液蜡生产,象固体蜡一样打进国际市场。
四、前苏联70年代在石油蛋白生产方面,液蜡消费量 650kt,占76.5%;日本1973年用于石油蛋白生产的液蜡量为390kt。
我国微生物发酵技术虽已有很大进步,但石油蛋白的生产还是空白的。
因此,应加强这方面的研究工作,以扩大我国液蜡消费。
五、我国原油多为石蜡基原油,石蜡资源十分丰富,尤其是沈北原油C14-20。
含量约占原油的8.3%,是生产重液蜡的优质原油,应充分利用现有重液蜡装置,提高产量和质量,满足国内市场需求。