弯曲工况下车轮强度、疲劳分析方法对比
高速列车轮对不同工况下应力及疲劳强度分析

高速列车轮对不同工况下应力及疲劳强度分析高速列车轮对不同工况下应力及疲劳强度分析一、引言随着高速铁路的发展,高速列车成为人们出行的重要方式之一。
高速列车的安全和可靠性是保障乘客出行的重要因素。
在运行过程中,轮对是高速列车中非常重要的部件之一,它承受着列车的重量和运行时产生的应力。
轮对在运行过程中面临着各种工况,包括加速、减速、制动、过弯等。
不同的工况会对轮对产生不同的应力,从而可能导致疲劳破坏。
因此,对高速列车轮对在不同工况下应力及疲劳强度进行分析,对于确保列车的安全和可靠运行具有重要意义。
二、高速列车轮对应力分析在高速列车运行过程中,轮对承受着来自列车本身重量以及运行时产生的动力学载荷。
这些载荷会导致轮对表面上的应力分布产生变化。
2.1 轮对静载荷分析:轮对承受的静载荷主要来自于列车本身的重量。
通过分析轮对在静态状态下的承载力和应力分布,可以得到轮对的最大接触应力和应力分布情况。
2.2 轮对动力学载荷分析:轮对在运行过程中,除了静载荷外,还要承受来自于列车运行时产生的动力学载荷,包括加速度、减速度、制动力等。
这些载荷会导致轮对表面应力分布产生动态变化。
三、高速列车轮对疲劳强度分析轮对在运行过程中所承受的应力会导致疲劳损伤,进而可能导致疲劳破坏。
因此,对轮对的疲劳强度进行分析,可以提前预测轮对的寿命,并采取相应的措施来延长轮对的使用寿命。
3.1 疲劳损伤计算:利用疲劳损伤累积理论,可以计算轮对在不同工况下的疲劳损伤量。
通过考虑应力幅值、循环次数以及材料的疲劳性能指标等参数,可以得到轮对在不同工况下的疲劳寿命。
3.2 疲劳强度分析:在获得轮对的疲劳寿命后,可以进一步分析轮对的疲劳强度。
通过比较轮对的疲劳寿命和实际使用寿命,可以评估轮对的疲劳强度,并采取相应的维修措施,以确保列车的安全和可靠运行。
四、应力及疲劳强度分析案例分析为了验证上述分析方法的准确性和有效性,可以选取一个具体的应力及疲劳强度分析案例进行分析。
混凝土路面弯曲疲劳试验及寿命评估

混凝土路面弯曲疲劳试验及寿命评估一、引言混凝土路面作为道路交通建设中常见的路面形式,其弯曲疲劳试验及寿命评估显得尤为重要。
混凝土路面在使用过程中,由于外界因素的影响,如温度变化、交通荷载等,会引起路面的弯曲变形,从而影响道路的使用寿命和安全性能。
因此,对混凝土路面的弯曲疲劳特性和寿命评估进行研究,对于保障道路交通的安全和长期可持续发展具有重要意义。
二、混凝土路面弯曲疲劳试验2.1 试验原理混凝土路面弯曲疲劳试验是利用试验机进行的一种模拟路面受到交通荷载后的弯曲变形情况的试验。
试验原理基于混凝土材料的弹性和塑性变形特性,通过施加不同幅值、不同频率的交通荷载,对混凝土路面进行弯曲变形试验,得出路面在不同荷载作用下的弯曲变形曲线及其变形特性参数。
2.2 试验方法混凝土路面弯曲疲劳试验通常采用四点弯曲试验方法,试验设备主要包括试验机、加载头、传感器、数据采集系统等。
试验流程如下:(1)制备试件:根据设计要求制备混凝土路面试件,尺寸和厚度应符合规范要求。
(2)试件安装:将试件放置在试验机上,根据试验要求设置试件边界约束条件,如固定端、自由端等。
(3)施加荷载:按照试验方案要求,通过加载头对试件进行施荷,记录下荷载大小、频率等参数。
(4)数据采集:利用传感器和数据采集系统记录试件变形情况,计算出试件的弯曲变形曲线及其特性参数。
2.3 试验结果分析混凝土路面弯曲疲劳试验得出的试验结果主要包括弯曲变形曲线、极限荷载、疲劳寿命等参数。
通过对试验结果的分析,可以得出以下结论:(1)随着荷载幅值的增加,路面的弯曲变形呈现出明显的非线性变化。
(2)随着荷载频率的增加,路面的弯曲变形呈现出明显的加速变化。
(3)路面的极限荷载随着试验次数的增加逐渐降低,疲劳寿命随着试验次数的增加逐渐缩短。
三、混凝土路面寿命评估3.1 寿命评估方法混凝土路面寿命评估主要采用疲劳寿命预测方法和寿命试验评估方法两种方法。
其中,疲劳寿命预测方法主要采用材料力学模型,通过对混凝土路面弯曲疲劳试验数据的分析和处理,预测路面的疲劳寿命。
轮齿弯曲疲劳强度和齿面接触疲劳强度-(机械设计齿轮传动章节课件2)-2020329

(10-8),同时引入载荷系数
KH(见下一页),可得:
=
4 −
3
(公式10-9)
1 ± 1
2
=
1
1 ± 1
1
齿轮传动的计算
上式中:
-接触疲劳强度计算的载荷系数, = ,即PPT一开始提到的4个载荷系数;
载荷分布系数Kβ。
= α
(公式10-2)
齿轮传动的计算
1,使用载荷系数KA
是考虑齿轮啮合时外部因素引起的附加载荷影响的系数。这种附加载荷取决
于原动机和从动机械的特性、联轴器类型以及运动状态等。KA的实用值应针
对设计对象,通过实践确定。
1),原动机包括:电动机、均匀运转的蒸汽机、燃气轮机;蒸汽机、燃气轮机液压装置;
当接触位置连续改变时,显然对于零件上任一点处的接触应力只能在材料许用接触应力的范围内改变,因此接触变应
力是一个脉动循环变应力。在做接触疲劳计算时,极限应力也应是一个脉动循环的极限接触应力。
接触应力也称为赫兹应力,是为了纪念首先解决接触应力计算问题的科学家赫兹(H.Hertz)。
齿轮传动的计算
+用于外啮合
多缸内燃机;单缸内燃机。
2),载荷状态分为:均匀平稳、轻微冲击、中等冲击、严重冲击。
工作状态外在因素越恶劣, KA的取值越大。
齿轮传动的计算
使用载荷系数KA
原动机
载荷状态
工作机器
电动机、均匀运转的
蒸汽机、燃气轮机
蒸汽机、燃气
轮机液压装置
多缸内燃机
单缸内燃机
均匀平稳
发动机、均匀传送的带式输送机或板式输送机、
I-DEAS车轮弯曲疲劳分析教程
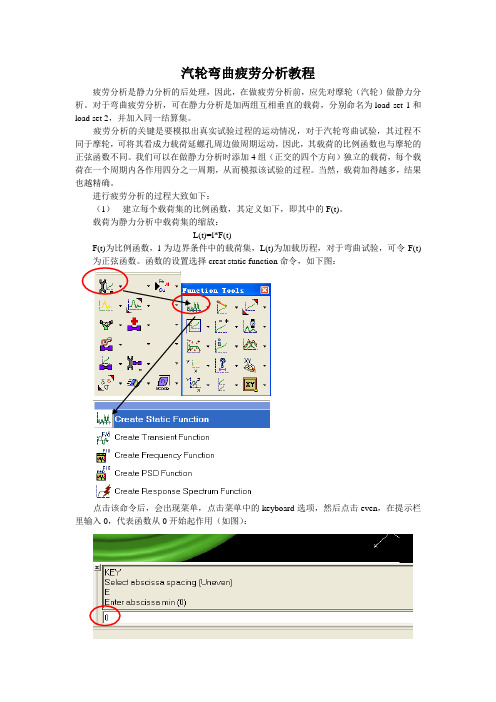
汽轮弯曲疲劳分析教程疲劳分析是静力分析的后处理,因此,在做疲劳分析前,应先对摩轮(汽轮)做静力分析。
对于弯曲疲劳分析,可在静力分析是加两组互相垂直的载荷,分别命名为load set 1和load set 2,并加入同一结算集。
疲劳分析的关键是要模拟出真实试验过程的运动情况,对于汽轮弯曲试验,其过程不同于摩轮,可将其看成力载荷延螺孔周边做周期运动,因此,其载荷的比例函数也与摩轮的正弦函数不同。
我们可以在做静力分析时添加4组(正交的四个方向)独立的载荷,每个载荷在一个周期内各作用四分之一周期,从而模拟该试验的过程。
当然,载荷加得越多,结果也越精确。
进行疲劳分析的过程大致如下:(1)建立每个载荷集的比例函数,其定义如下,即其中的F(t)。
载荷为静力分析中载荷集的缩放:L(t)=l*F(t)F(t)为比例函数,l为边界条件中的载荷集,L(t)为加载历程,对于弯曲试验,可令F(t)为正弦函数。
函数的设置选择creat static function命令,如下图:点击该命令后,会出现菜单,点击菜单中的keyboard选项,然后点击even,在提示栏里输入0,代表函数从0开始起作用(如图):然后输入步长1:最后,输入函数的总数据点数,默认1024,数据点越多,你所描述的函数越精确:接着,系统要求你输入函数的值了,比如,x=0时,函数值为1,那就输入1,直到输完21个点的值,然后保存该函数到任意的文件中:可以用下面的命令察看函数的图:对于汽轮的其他三组载荷可分别设置如下:(2)建立疲劳事件,和动态响应一个命令点击第一个问号,将每个载荷集依次选中加入事件中;然后对每一个载荷集,点击第二个问号,选择其对应的加载函数。
(3)Fatigue tools里面将I-DEAS的材料库调入,如下:(4)评估疲劳损伤/寿命各点疲劳寿命与额定寿命比值输入额定循环次数可显示各点的疲劳寿命以上所有设置好之后点击进行评估就可以得出结果了,关于结果的含义可以参考Tutorial里面对应的帮助练习来看。
曲轴滚压力与疲劳强度分析

曲轴滚压力与疲劳强度分析作者:文/ 黄中顺蒲鹰邓玉婷来源:《时代汽车》 2020年第13期黄中顺蒲鹰邓玉婷桂林福达曲轴有限公司广西桂林市 541199摘要:曲轴是发动机的核心零部件,在发动机工作过程中它承受连杆传来的力,并将其转变为转矩通过曲轴输出并驱动发动机上其他附件工作。
曲轴受到旋转质量的离心力、周期变化的气体惯性力和往复惯性力的共同作用,使曲轴承受弯曲扭转载荷的作用。
因此要求曲轴有足够的强度和刚度,随着国内市场对小排量、增压发动机性能的要求不断提高,曲轴结构在轻量化的同时也要求具有较高的疲劳强度,而对强度影响最大的就是曲轴的强化方式及参数,因此,研究曲轴的滚压力与疲劳强度的关系是每个新型号曲轴开发过程中必不可少的一项工作。
关键词:曲轴滚压力疲劳强度Analysis of the Crankshaft Rolling Pressure and Fatigue StrengthHuang Zhongshun,Pu Ying,Deng YutingAbstract:The crankshaft is the core component of the engine. During the operation of the engine, it bears the force transmitted by the connecting rod and converts it into torque to output through the crankshaft and drive otheraccessories on the engine to work. The crankshaft is subjected to the centrifugal force of the rotating mass, the periodically changing gas inertia force and the reciprocating inertia force, so that the crank bearing is subjected to the bending and torsional load. Therefore, the crankshaft is required to have sufficient strength and rigidity. With the continuous improvement of the domestic market's requirements for small displacement and supercharged engine performance, the crankshaft structure is required to have high fatigue strength while being lightweight, which has the greatest impact on strength. It is the strengthening method and parameters of the crankshaft. Therefore, studying the relationship between the rolling pressure and fatigue strength of the crankshaft is an indispensable task in the development of each new type of crankshaft.Key words:crankshaft, rolling pressure, fatigue strength本文通过对我公司目前加工的一款小排量发动机曲轴采用不同滚压力进行试验,以验证滚压力对曲轴疲劳强度的影响,该款曲轴排量为1.0T,材料为球墨铸铁QT700-2。
基于改进的Goodman曲线的车轮疲劳强度评估方法研究

第14卷第4期 铁道科学与工程学报 Volume 14 Num b e r4 2017 年 4 月Journal of Railway Science and Engineering April 2017基于改进的Goodman曲线的车轮疲劳强度评估方法研究王悦东,张佳宇(大连交通大学交通运输工程学院,辽宁大连116028)摘要:传统的Haigh型式的G o o d m a n曲线计算方法比较简单,疫劳评估结果往往不能完整反应车轮的疫劳状况。
为了弥 补Haigh型式的G o o d m a n曲线法在计算车轮疲劳强度过程中的不足和提高车轮疲劳强度安全系数计算的准确性,在Haigh 型式的G o o d m a n曲线法的基础上进行改进,完善车轮疫劳的计算工况及计算方法,将安全系数作为疫劳评估的关键参数。
以多个不同类型的车轮为对象,进行有限元仿真分析,并分别运用Haigh形式的G o o d m a n曲线法、Crossland准则和改进的 G o o d m a n曲线法对车轮的幅板和福板孔等关键位置进行疲劳强度计算与评估。
对比计算结果表明:3种方法的计算结果趋势 基本一致,在车轮的一些评估位置改进的G o o d m a n曲线法计算的安全系数欠要小于Haigh型式的G o o d m a n曲线方法的计算结 果,说明改进的G o o d m a n曲线计算方法更加安全有效。
但是,对于非轴对称车轮的福板孔等位置,仍必须使用Crossland 准则评估疲劳强度,以保证车轮的运行安全。
关键词:车轮;疲劳强度;G o o d m a n曲线法;疲劳强度评估准则中图分类号:U270.33 文献标志码:A文章编号:1672-7029(2017)04-0827-06Assessment method for fatigue strength of wheel based on improved Goodman curveW A N G Y uedong,Z H A N G Jiayu(Department of Traffic and Transportation Engineering, Dalian Jiaotong University, Dalian 116028, China)A b s tr a c t:D u e to the simplicity of traditional Haigh-Goodman method,the fatigue assessment usually cannot reflect the fatigue condition of wheels.To m a k e up the shortage of Haigh-Goodman method in calculating process of the wheel fatigue strength and improve the accuracy of the calculation of the wheel fatigue strength safety factor,the Haigh-Goodman method was improved,which included putting the safety factor as the key of fatigue assessment and improving the main method of calculation.Taking different types of wheels as objects,the finite element models were carried out.The fatigue strength of the key positions of the wheel was evaluated by the ways of the Haigh-Goodman method,improved G o o d m a n method and Crossland pared with the results, the three methods are basically identical.In m a n y positions of the wheel,the safety factor of the improved G o o d m a n method compared with Haigh-Goodman method are smaller,but for the plate holes of the non-axisymmetrical wheels,Crossland criterion s t i l l be used to evaluate the fatigue strength of wheels,to ensure the safe operation of wheels.K e y w o r d s:wheel;fatigue strength;G o o d m a n curve method;the evaluate criterion of fatigue strength收稿日期:2016-05-14基金项目:国家自然科学基金资助项目(51208072);铁路总公司科学计划项目(2012G002-11);辽宁省教育厅优秀人才资助项目(LGQ2013052) 通信作者:王悦东(1977-),男,黑龙江桦南人,副教授,博士,从事车辆工程结构疲劳可靠性研宄;E-mail: wydstar@828铁道科学与工程学报2017年4月车轮作为转向架关键部件之一,保证了列车运行的安全性。
机械零件疲劳对比试验方法和结果判定

[ 1 4 ] 杨旭 士.基 于 J Q u e r y框架 的 We b查询 视 图设计 与实 现 [ J ] . 计算机与现代化 , 2 0 1 0 , 1 ( 8 ) : 1 2 8 — 1 2 9 .
[ 1 5 ] 张林 , 肖毅 , 聂笑一 . 基于 i Q u e r y的在线 电子名 片制作 系
的大小 。下 面结 合某 型发射装置“ 前盖板 ” 两种结 构的疲劳对 比 试验 , 对疲劳对 比试验 的过程及其结果的判定进行详细介绍 。
1 试 验方 案 的设计
金属材料按破坏循环 次数 的高低将疲劳分 为两类 :高周疲 劳 和低周疲 劳。高周 疲劳作用于零件 、 构 件的应力水平较低 , 破 坏循环次数一般高于 5 x l O 5 次。低周疲劳作用 于零件 、 构件 的应
i n Ni ng x i a Me t e o r o l o g i c a l Ope r a t i o na l S ys t e m
LI Xi nqi ng , CHEN Ha i bo , CHEN Yuhu a
ABS TRACT:I n t h e l i g h t o f t h e d e f e c t s o f We b f r a me wo r k d e s i g n t e c h n o l o g y i n t r a d i t i o n a l me t e o r o l o g i c a l o p e r a t i o n l a s y s t e m s u c h a s g r e a t d e v e l o p me n t d i ic f u l t i e s , n o u n i i f e d d e s i g n s t y l e , a n d p o o r c o mp a t i b i l i t y , e t c . , t h i s p a p e r s t u d i e s t h e
基于数值仿真的全表面轮毂弯曲疲劳试验及疲劳寿命分析

装备环境工程第20卷第5期·70·EQUIPMENT ENVIRONMENTAL ENGINEERING2023年5月基于数值仿真的全表面轮毂弯曲疲劳试验及疲劳寿命分析朱志鹏1,汤永1,李火平2,孙云伟1,邓文1,宋桂秋3(1.中国直升机设计研究所,江西景德镇 333001;2.中国人民解放军92281部队,山东诸城 262200;3. 东北大学机械工程与自动化学院,沈阳 110001)摘要:目的预测钢制全表面轮毂易产生疲劳破坏的危险区域,并分析其弯曲疲劳寿命。
方法针对全表面轮毂的弯曲疲劳试验工况,建立有限元分析模型,综合考虑螺栓拧紧方式、螺栓预紧力以及材料非线性特征的影响,通过在加载轴末端建立局部坐标系,实现载荷的分解,并最终实现弯矩的动态加载。
在此基础上,进行轮毂的受力分析,然后构造适用于轮毂的应力寿命曲线,并使用名义应力法进行疲劳寿命预测。
结果动态弯矩的加载方向变化会显著影响轮辐表面的应力分布特点,螺栓预紧力施加后,螺栓孔附近区域的应力显著增大,在计算中应考虑其影响。
在获得各节点载荷历程后,以高应力幅和平均应力为标准,筛选出了轮毂的危险节点。
结论基于数值仿真的本型全表面轮毂弯曲疲劳试验,危险节点位置均位于轮辐通风孔的内圆角附近区域,可有针对性地对该区域进行相应的优化设计,以进一步提高轮毂的弯曲疲劳寿命。
分析得到当前轮辋弯曲疲劳寿命约7.6万次,符合国家标准的要求。
关键词:全表面轮毂;弯曲疲劳;数值分析;材料非线性;预紧力影响;寿命预测中图分类号:TH16 文献标识码:A 文章编号:1672-9242(2023)05-0070-10DOI:10.7643/ issn.1672-9242.2023.05.011Bending Fatigue Test and Fatigue Life Analysis of Full-surface Hub Basedon Numerical SimulationZHU Zhi-peng1, TANG Yong1, LI Huo-ping2, SUN Yun-wei1, DENG Wen1, SONG Gui-qiu3(1. China Helicopter Research and Development Institute, Jiangxi Jingdezhen 333001, China; 2.Unit 92281 of Chinese People’sLiberation Army, Shandong Zhucheng 262200, China; 3. School of Mechanical Engineering & Automation,Northeastern University, Shenyang Liaoning 110001, China)ABSTRACT: The work aims to predict the dangerous areas prone to fatigue damage and analyze the bending fatigue life of steel full-surface hubs.A finite element analysis model was established for the bending fatigue test condition of the full-surface hub. The method of bolt tightening, the impact of bolt preload on the hub, and the nonlinear characteristics of the material were收稿日期:2023–03–20;修订日期:2023–04–20Received:2023-03-20;Revised:2023-04-20基金项目:航空科学基金(2018ZF02005)Fund:Aviation Science Foundation (2018ZF02005)作者简介:朱志鹏(1989—),男,博士。
- 1、下载文档前请自行甄别文档内容的完整性,平台不提供额外的编辑、内容补充、找答案等附加服务。
- 2、"仅部分预览"的文档,不可在线预览部分如存在完整性等问题,可反馈申请退款(可完整预览的文档不适用该条件!)。
- 3、如文档侵犯您的权益,请联系客服反馈,我们会尽快为您处理(人工客服工作时间:9:00-18:30)。
弯曲工况下车轮强度、疲劳分析方法对比
车轮主要由轮辋和轮辐组成。
轮辋是支撑轮胎的基座,轮辐是作为车轮和车轮轮毂的连接件,主要起传递载荷(垂直力、侧向力和切向力转矩)的作用[1]。
轮辋与轮辐焊接后与轮胎组成一个整体,共同承受汽车的重力、制动力、驱动力、汽车转向时产生的侧向力及所产生的力矩,还要承受路面不平产生的
冲击力。
车轮工作条件严酷,其质量直接影响汽车行驶过程的安全性,因此,
应有一定的强度、刚度和工作耐久性能。
在汽车车轮的实际使用过程中,80% 以上的车轮破坏是由疲劳破坏引起的,而在衡量疲劳性能的径向疲劳试验中,
又以弯曲疲劳失效率最高。
国外建立了JWL、DOT 和ISO 等相关车轮弯曲疲
劳试验标准,这些标准都是模拟车轮在弯矩作用下的受载情况。
我国《GB/T 5334-2005 乘用车车轮性能要求和试验方法》对于乘用车车轮的试验方法进行了规定。
该试验是使车轮在一个固定不变的弯矩下旋转,或是车轮静止不动承
受一旋转弯矩,以车轮不能继续承受载荷(如结构失稳)和出现侵入车轮断面
的可见疲劳裂纹为失效标准。
本文利用5 种建模方式对车轮进行离散,对弯曲工况车轮的强度与疲劳分析结果进行对比,寻找简单且结果准确的建模方式。
1 模型描述本文利用HyperMesh 软件分别采用以下五种方式进行建模。
1.1 模型1(壳单元离散,不考虑接触与预紧力)轮辋、轮辐与焊缝均使用壳单元模拟,总装件的螺栓连接与加载轴均用KINCOUP 刚性单元模拟,加载圆盘使用
B31 模拟,如图1 所示。
1.2 模型2 (体单元离散,不考虑接触与预紧力)轮辋、轮辐、焊缝使用实体单元模拟,总装件的螺栓连接与加载轴均用KINCOUP 刚性单元模拟,加载圆盘使用B31 模拟,如图1 所示。
图1 未考虑预紧力的车轮有限元模型
1.3 模型3(壳单元离散,考虑预紧力,接触对模拟接触)轮辋、轮辐与焊缝。