单轴和多轴疲劳准则下的车轮疲劳强度分析
《铝合金车轮双轴疲劳试验数值模拟研究》

《铝合金车轮双轴疲劳试验数值模拟研究》篇一一、引言随着汽车工业的快速发展,车轮作为汽车的重要组成部分,其性能直接关系到汽车的行驶安全与舒适性。
铝合金车轮因其轻量化、耐腐蚀、高强度等优点,逐渐成为市场上的主流选择。
然而,车轮在实际使用过程中会受到各种复杂载荷的作用,尤其是双轴疲劳载荷,对其性能产生重大影响。
因此,对铝合金车轮进行双轴疲劳试验数值模拟研究具有重要意义。
本文将通过对铝合金车轮双轴疲劳试验的数值模拟,深入探讨其疲劳性能及影响因素。
二、铝合金车轮材料与结构特点铝合金车轮相比传统钢制车轮,具有轻量化、耐腐蚀、高强度等优点。
其材料组成主要为铝、铜、镁等元素,通过合金化处理提高材料的综合性能。
铝合金车轮的结构设计需满足强度、刚度、轻量化等多方面要求,通常采用复杂的断面设计和优化处理方法。
三、双轴疲劳试验原理及方法双轴疲劳试验是一种模拟车轮在实际使用过程中所受复杂载荷的试验方法。
该方法通过在试验机上施加双向旋转力矩和制动力矩,模拟车轮在实际行驶过程中的受力情况。
在双轴疲劳试验中,通过观察和分析车轮的应力分布、变形情况以及疲劳裂纹的产生和扩展,评估车轮的疲劳性能。
四、数值模拟方法及模型建立为了更准确地分析铝合金车轮的双轴疲劳性能,本文采用数值模拟方法。
首先,根据铝合金车轮的实际结构,建立精确的三维有限元模型。
其次,根据双轴疲劳试验的实际情况,设定合理的材料参数、边界条件和载荷条件。
最后,通过有限元分析软件对模型进行求解,得到车轮在双轴疲劳试验过程中的应力分布、变形情况以及疲劳寿命等数据。
五、数值模拟结果分析通过对铝合金车轮双轴疲劳试验的数值模拟,我们得到了以下结果:1. 应力分布:在双轴疲劳试验过程中,车轮的应力分布不均匀,存在明显的应力集中现象。
这些应力集中区域往往是裂纹产生的源头。
2. 变形情况:随着双轴疲劳试验的进行,车轮的变形逐渐增大。
在一定的循环次数后,变形达到一定程度,导致车轮失效。
3. 疲劳寿命:通过数值模拟,我们可以得到车轮的疲劳寿命。
材料的疲劳强度分析

材料的疲劳强度分析疲劳是材料在循环载荷下产生的疲劳变形和疲劳破坏的一种失效形式。
在实际使用中,许多工程材料常处于交变或脉动载荷的作用下,例如机械零件、飞机翼、车轮等。
因此,了解材料的疲劳强度十分重要,可以有效预测材料在长期使用中的寿命和安全性。
材料的疲劳强度是指材料在循环载荷下能够承受的最大应力。
疲劳是一种累积性失效,慢慢积累的微小裂纹会逐渐扩展,最终导致材料断裂。
而裂纹的扩展速度与波动应力的强度、应力幅值以及加载频率有关。
在进行材料的疲劳强度分析时,通常需进行以下几个步骤:一、制备测试样品:根据研究的材料和结构形式,制备出代表性的材料测试样品。
例如,对于金属材料,可以选择制备标准的疲劳试样,如疲劳断裂试样。
二、加载测试样品:将测试样品放置于疲劳试验机中,对其施加循环载荷。
载荷可以是完全反转载荷、不完全反转载荷或只有一方向载荷等。
同时,需记录测试样品所受的载荷幅值、频率等参数。
三、监测实时数据:在加载过程中,需要实时监测样品的应变和应力变化。
这可以通过应变片、应变计或者压电传感器等装置来实现。
实时数据的监测可以帮助研究人员了解材料的疲劳行为。
四、分析测试结果:通过分析实验数据,可以得到材料的疲劳强度曲线。
通常使用S-N曲线表示材料的疲劳寿命,即循环载荷下材料能够承受的应力幅值与寿命的关系。
此外,还可以通过计算疲劳裂纹扩展速率来评估材料的疲劳性能。
五、疲劳寿命预测:利用得到的疲劳强度曲线和实际应力情况,可以用来预测材料的疲劳寿命。
疲劳寿命预测对于工程设计和材料选择非常重要,可以保证工程结构的可靠性和安全性。
综上所述,材料的疲劳强度分析是通过实验测试和数据分析,来评估材料在循环载荷下的疲劳性能和寿命。
准确了解材料的疲劳强度对于工程设计、寿命预测和安全性评估具有重要意义。
通过科学的方法和有效的测试,可以为材料的疲劳强度分析提供可靠的数据支持。
HXD3B型大功率机车车轮疲劳强度分析
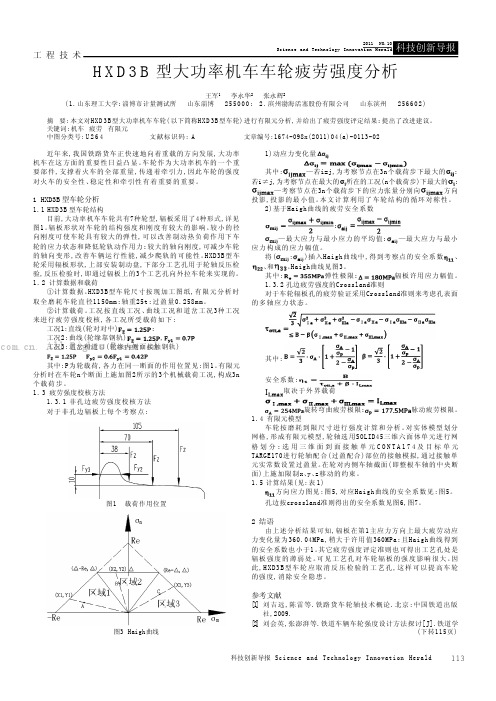
近年来,我国铁路货车正快速地向着重载的方向发展,大功率机车在这方面的重要性日益凸显。
车轮作为大功率机车的一个重要部件,支撑着火车的全部重量,传递着牵引力,因此车轮的强度对火车的安全性、稳定性和牵引性有着重要的重要。
1 HXD3B 型车轮分析1.1HXD3B 型车轮结构目前,大功率机车车轮共有7种轮型,辐板采用了4种形式,详见图1。
辐板形状对车轮的结构强度和刚度有较大的影响。
较小的径向刚度可使车轮具有较大的弹性,可以改善制动热负荷作用下车轮的应力状态和降低轮轨动作用力;较大的轴向刚度,可减少车轮的轴向变形,改善车辆运行性能,减少爬轨的可能性。
HXD3B型车轮采用辐板形状,上部安装制动盘,下部分工艺孔用于轮轴反压检验,反压检验时,即通过辐板上的3个工艺孔向外拉车轮来实现的。
1.2计算数据和载荷①计算数据。
HXD3B型车轮尺寸按现加工图纸,有限元分析时取全磨耗车轮直径1150mm;轴重25t;过盈量0.258mm。
②计算载荷。
工况按直线工况、曲线工况和道岔工况3种工况来进行疲劳强度校核,各工况所受载荷如下:工况1:直线(轮对对中);工况2:曲线(轮缘靠钢轨),工况3:道岔和道口(轮缘内侧面接触钢轨)其中:P为轮载荷,各力在同一断面的作用位置见:图1。
有限元分析时在车轮n个断面上施加图2所示的3个机械载荷工况,构成3n个载荷步。
1.3疲劳强度校核方法1.3.1非孔边疲劳强度校核方法对于非孔边辐板上每个考察点:1)动应力变化量其中:—若i=j,为考察节点在3n个载荷步下最大的;若i≠j,为考察节点在最大的所在的工况(n个载荷步)下最大的;—考察节点在3n个载荷步下的应力张量分别向方向投影,投影的最小值。
本文计算利用了车轮结构的循环对称性。
2)基于Haigh曲线的疲劳安全系数;—最大应力与最小应力的平均值;—最大应力与最小应力构成的应力幅值。
将(:)插入Haigh曲线中,得到考察点的安全系数、、和。
Haigh曲线见图3。
《铝合金车轮双轴疲劳试验数值模拟研究》范文
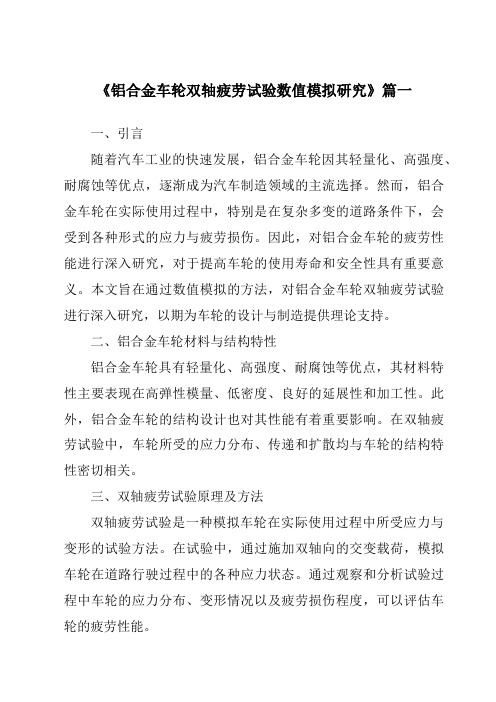
《铝合金车轮双轴疲劳试验数值模拟研究》篇一一、引言随着汽车工业的快速发展,铝合金车轮因其轻量化、高强度、耐腐蚀等优点,逐渐成为汽车制造领域的主流选择。
然而,铝合金车轮在实际使用过程中,特别是在复杂多变的道路条件下,会受到各种形式的应力与疲劳损伤。
因此,对铝合金车轮的疲劳性能进行深入研究,对于提高车轮的使用寿命和安全性具有重要意义。
本文旨在通过数值模拟的方法,对铝合金车轮双轴疲劳试验进行深入研究,以期为车轮的设计与制造提供理论支持。
二、铝合金车轮材料与结构特性铝合金车轮具有轻量化、高强度、耐腐蚀等优点,其材料特性主要表现在高弹性模量、低密度、良好的延展性和加工性。
此外,铝合金车轮的结构设计也对其性能有着重要影响。
在双轴疲劳试验中,车轮所受的应力分布、传递和扩散均与车轮的结构特性密切相关。
三、双轴疲劳试验原理及方法双轴疲劳试验是一种模拟车轮在实际使用过程中所受应力与变形的试验方法。
在试验中,通过施加双轴向的交变载荷,模拟车轮在道路行驶过程中的各种应力状态。
通过观察和分析试验过程中车轮的应力分布、变形情况以及疲劳损伤程度,可以评估车轮的疲劳性能。
四、数值模拟方法及模型建立数值模拟是研究铝合金车轮双轴疲劳试验的有效手段。
通过建立精确的有限元模型,可以模拟双轴疲劳试验过程中车轮的应力分布、变形情况以及疲劳损伤程度。
在模型建立过程中,需要考虑材料的非线性、弹塑性等特性,以及边界条件、接触关系等因素。
此外,还需要对模型进行验证和优化,以确保模拟结果的准确性。
五、数值模拟结果分析通过对铝合金车轮双轴疲劳试验的数值模拟,可以得到车轮在各种工况下的应力分布、变形情况以及疲劳损伤程度。
通过对模拟结果的分析,可以得出以下结论:1. 铝合金车轮在双轴疲劳试验中,应力主要集中在轮辐与轮盘的连接处以及轮盘的外缘部分。
这些区域的应力集中现象会导致车轮的疲劳损伤加速。
2. 在不同的工况下,铝合金车轮的应力分布和变形情况有所不同。
《铝合金车轮双轴疲劳试验数值模拟研究》范文

《铝合金车轮双轴疲劳试验数值模拟研究》篇一一、引言随着汽车工业的快速发展,车轮作为汽车的重要组成部分,其性能的优劣直接关系到汽车的安全性和舒适性。
铝合金车轮因其轻量化、耐腐蚀、散热性好等优点,在汽车制造领域得到了广泛应用。
然而,车轮在实际使用过程中会受到各种复杂载荷的作用,尤其是双轴疲劳载荷,对其性能提出了严峻的挑战。
因此,对铝合金车轮双轴疲劳试验进行数值模拟研究,对于提高车轮的性能和延长其使用寿命具有重要意义。
二、铝合金车轮的特性和应用铝合金车轮具有轻量化、耐腐蚀、散热性好等优点,使得其在汽车制造领域得到了广泛应用。
铝合金车轮的制造过程包括材料选择、设计、铸造、机械加工等多个环节,每个环节都对车轮的性能产生影响。
铝合金车轮的力学性能、抗疲劳性能和抗冲击性能等是其应用的关键因素。
三、双轴疲劳试验概述双轴疲劳试验是一种模拟车轮在实际使用过程中所受复杂载荷的试验方法。
通过双轴疲劳试验,可以了解车轮在复杂载荷作用下的力学性能、疲劳寿命和失效模式等信息。
双轴疲劳试验主要包括加载方式、试验条件、数据采集与分析等环节。
四、数值模拟方法及模型建立数值模拟是研究双轴疲劳试验的重要手段。
通过对铝合金车轮的双轴疲劳试验进行数值模拟,可以了解车轮在复杂载荷作用下的应力分布、变形情况以及疲劳损伤等情况。
在数值模拟过程中,需要建立准确的有限元模型,包括材料属性、边界条件、加载方式等。
同时,还需要选择合适的数值模拟方法,如有限元法、边界元法等。
五、模拟结果与分析通过对铝合金车轮双轴疲劳试验的数值模拟,可以得到车轮在复杂载荷作用下的应力分布、变形情况以及疲劳损伤等信息。
这些信息可以帮助我们了解车轮的性能和失效模式,为优化设计提供依据。
同时,通过对比模拟结果和实际试验结果,可以验证数值模拟方法的准确性和可靠性。
六、优化设计与应用前景基于数值模拟结果,可以对铝合金车轮进行优化设计,提高其性能和延长其使用寿命。
优化设计主要包括材料选择、结构设计、制造工艺等方面的改进。
《铝合金车轮双轴疲劳试验数值模拟研究》范文

《铝合金车轮双轴疲劳试验数值模拟研究》篇一一、引言随着汽车工业的飞速发展,铝合金车轮因其轻量化、耐腐蚀等优势得到了广泛应用。
为了确保铝合金车轮在实际使用中的安全性和可靠性,双轴疲劳试验成为一种重要的性能测试方法。
然而,传统的双轴疲劳试验往往耗时耗力,且难以全面反映车轮在复杂工况下的性能表现。
因此,本文采用数值模拟的方法,对铝合金车轮双轴疲劳试验进行了深入研究。
二、铝合金车轮的有限元模型本研究的首要任务是建立铝合金车轮的有限元模型。
通过对车轮进行细致的几何建模和网格划分,我们得到了一个高精度的有限元模型。
该模型充分考虑了车轮的几何形状、材料属性以及边界条件等因素,为后续的数值模拟奠定了基础。
三、双轴疲劳试验的数值模拟在获得铝合金车轮的有限元模型后,我们开始进行双轴疲劳试验的数值模拟。
首先,我们设定了与实际双轴疲劳试验相同的加载条件和边界条件,然后通过有限元软件对模型进行求解。
在模拟过程中,我们重点关注车轮的应力分布、应变以及疲劳损伤等关键参数。
四、结果分析通过对数值模拟结果的分析,我们得到了铝合金车轮在双轴疲劳试验下的应力-时间曲线、应变-时间曲线以及疲劳损伤分布图等关键数据。
这些数据可以帮助我们全面了解车轮在双轴疲劳试验中的性能表现。
首先,我们发现铝合金车轮在双轴加载条件下,应力主要集中在轮辐与轮盘的连接处以及轮盘的边缘部位。
这些部位的应力值随着时间的变化而发生变化,呈现出明显的周期性。
其次,车轮的应变主要发生在轮盘的局部区域,且在长时间的加载过程中逐渐累积。
最后,通过分析疲劳损伤分布图,我们发现车轮的疲劳损伤主要发生在应力集中的区域,这些区域在长时间的循环加载下容易发生裂纹扩展和断裂。
五、结论通过本文的数值模拟研究,我们得到了铝合金车轮在双轴疲劳试验下的应力、应变以及疲劳损伤等关键数据。
这些数据不仅可以帮助我们全面了解车轮在复杂工况下的性能表现,还可以为车轮的设计和优化提供有价值的参考。
此外,数值模拟方法具有耗时短、成本低等优势,可以大大提高双轴疲劳试验的效率和准确性。
《铝合金车轮双轴疲劳试验数值模拟研究》
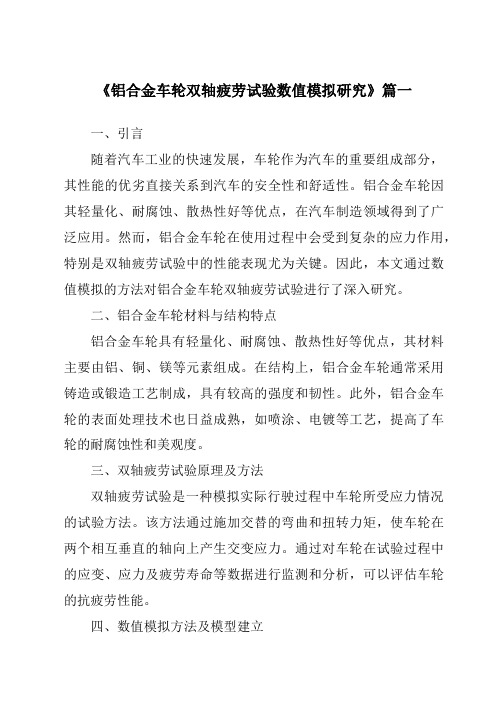
《铝合金车轮双轴疲劳试验数值模拟研究》篇一一、引言随着汽车工业的快速发展,车轮作为汽车的重要组成部分,其性能的优劣直接关系到汽车的安全性和舒适性。
铝合金车轮因其轻量化、耐腐蚀、散热性好等优点,在汽车制造领域得到了广泛应用。
然而,铝合金车轮在使用过程中会受到复杂的应力作用,特别是双轴疲劳试验中的性能表现尤为关键。
因此,本文通过数值模拟的方法对铝合金车轮双轴疲劳试验进行了深入研究。
二、铝合金车轮材料与结构特点铝合金车轮具有轻量化、耐腐蚀、散热性好等优点,其材料主要由铝、铜、镁等元素组成。
在结构上,铝合金车轮通常采用铸造或锻造工艺制成,具有较高的强度和韧性。
此外,铝合金车轮的表面处理技术也日益成熟,如喷涂、电镀等工艺,提高了车轮的耐腐蚀性和美观度。
三、双轴疲劳试验原理及方法双轴疲劳试验是一种模拟实际行驶过程中车轮所受应力情况的试验方法。
该方法通过施加交替的弯曲和扭转力矩,使车轮在两个相互垂直的轴向上产生交变应力。
通过对车轮在试验过程中的应变、应力及疲劳寿命等数据进行监测和分析,可以评估车轮的抗疲劳性能。
四、数值模拟方法及模型建立本文采用有限元分析方法对铝合金车轮双轴疲劳试验进行数值模拟。
首先,根据实际车轮的几何尺寸和材料属性建立有限元模型。
其次,根据双轴疲劳试验的加载条件和边界条件,设置有限元模型的载荷和约束。
最后,通过求解有限元模型,得到车轮在双轴疲劳试验过程中的应力、应变及疲劳寿命等数据。
五、模拟结果分析通过对铝合金车轮双轴疲劳试验的数值模拟,我们得到了以下结果:1. 应力分布:在双轴疲劳试验过程中,车轮的应力分布呈现不均匀性,主要集中在轮辐和轮辋的连接处以及轮辐的弯曲部位。
2. 疲劳寿命:根据数值模拟结果,铝合金车轮在双轴疲劳试验中的疲劳寿命与实际使用情况相符,验证了数值模拟方法的可靠性。
3. 影响因素:通过对不同参数的模拟分析,我们发现材料属性、结构尺寸、加载条件等因素对铝合金车轮的双轴疲劳性能具有显著影响。
铁路车辆轮轨结构疲劳分析研究

铁路车辆轮轨结构疲劳分析研究1. 引言铁路交通作为一种重要的交通方式,在现代社会中发挥着不可替代的作用。
铁路车辆轮轨结构是铁路交通系统中重要的组成部分,其安全性和稳定性直接影响着列车的运行效果和乘客的出行安全。
因此,对铁路车辆轮轨结构进行疲劳分析研究具有重要意义。
2. 轮轨疲劳机制分析轮轨疲劳是由于车辆通过轨道时产生的载荷作用下,轮轨结构遭受重复应力而导致疲劳破坏的一种现象。
该疲劳机制主要包括弯曲疲劳、挤压疲劳和滚动疲劳。
弯曲疲劳是指车辆的重力和侧向力引起的弯矩作用下产生的疲劳破坏;挤压疲劳是由于轨道弹性变形引起的轮轨接触区表面产生的挤压应力引起的疲劳破坏;滚动疲劳是由于车辆轮轴和轨道之间的滚动接触引起的疲劳破坏。
3. 疲劳试验及数值模拟为了深入研究轮轨结构的疲劳特性,需要进行疲劳试验和数值模拟。
疲劳试验可以通过在实际环境中模拟车辆通过轨道的载荷作用,对轮轨结构进行加载,观察和记录其疲劳破坏的情况。
数值模拟则可以通过建立相应的数学模型和计算方法,模拟车辆通过轨道时的应力分布、受力情况和轮轨接触的变化,以预测轮轨结构的疲劳寿命。
4. 疲劳寿命评估方法疲劳寿命评估是研究轮轨结构疲劳分析的重要内容。
常用的评估方法包括基于滚动接触疲劳理论的Wöhler曲线方法和基于应力范围的Palmgren-Miner疲劳损伤累积法。
Wöhler曲线方法通过实验获得不同载荷下的疲劳寿命数据,根据统计学原理建立疲劳寿命曲线,以预测轮轨结构在不同工况下的疲劳寿命。
Palmgren-Miner疲劳损伤累积法则则通过计算每个应力循环对应的疲劳寿命损伤分数,累加所有应力循环的损伤分数,以评估轮轨结构的疲劳寿命。
5. 疲劳分析中的参数考虑在进行轮轨疲劳分析时,需要考虑一系列参数对疲劳寿命的影响。
其中包括车辆质量、速度、载荷分布情况、轨道几何形状、轨道材料等因素。
车辆质量和速度的大小直接影响轮轨结构受力情况和疲劳破坏的可能性;载荷分布情况主要包括垂向载荷和侧向载荷,不同的载荷分布对疲劳寿命的影响也不同;轨道几何形状和轨道材料的选择和使用直接影响轮轨接触的情况和疲劳寿命。
- 1、下载文档前请自行甄别文档内容的完整性,平台不提供额外的编辑、内容补充、找答案等附加服务。
- 2、"仅部分预览"的文档,不可在线预览部分如存在完整性等问题,可反馈申请退款(可完整预览的文档不适用该条件!)。
- 3、如文档侵犯您的权益,请联系客服反馈,我们会尽快为您处理(人工客服工作时间:9:00-18:30)。
爿÷ 收 稿 日期 :2208702);辽宁省高等学校优秀人才支持计划 (LJQ2013052) 作者简介 :王悦东 (1977一),男 ,副教授 ,博士 ,主要从 事车辆结构分析与现代设计方法 的研究
E·mall:wydstar@ 163.eom.
48
大 连 交 通 大 学 学 报
第 37卷
向应 力状 态转 换 为单 向应力 状态 . 首 先 确定 车 轮 在 不 同载 荷 工 况 作 用 下 的 主
应 力值 和 方 向 ,将 所 有 载 荷 工 况 作 用 下 的 最 大 主 应 力方 向确 定 为 基 本 应 力 分 布 方 向 ,其 值 为 计算最大主应力 ,计算其 与结构基准 (节 点位置 与车 轮 轴 线 组 成 的 平 面 )的 夹 角 ,如 图 1(a)所 示 ;将 在 其 它 载 荷 工 况 作 用 下 的 主 应 力 投 影 到 最 大 主应 力 方 向 上 ,其 投 影 值 最 小 的应 力 值 确 定 为 最 小 主 应 力 ,如 图 1(b)所 示 .由该 位 置 的 最 大 和 最 小 主 应 力 值 计 算 平 均 应 力 和 应 力 幅 , 如 下 式 所示 .然 后用 Haigh形 式 的 Goodman疲 劳 曲线 评 定 车 轮 的疲 劳强 度 .
第 37卷 第 2期 2016年 4月
大 连 交 通 大 学 学 报
JOURNAL OF DALIAN JIAOTONG UNIVERSITY
文 章 编 号 :1673-9590(2016)02—0047—06
Vo1.37 No.2 Apr.2016
单 轴 和 多轴 疲劳 准则 下 的车 轮 疲 劳 强 度 分 析
王 悦 东 ,盛 杰 琼
(大连交通大 学 交通运输工程 学院,2-7 大连 116028)采
摘 要 :为 了分析城 际动 车组 车轮的疲劳强度 ,首 先建立城 际动 车组车 轮的有 限元模 型 ,依据 国际铁 路 联盟 的 UIC510—5标 准以及欧洲的 EN标准模拟车轮在直线 、曲线和道岔工况下 的应力 ;并 依据车轮 的 单轴疲 劳准则 Haigh形式 的 Goodman曲线 图分析评估 城际动 车组车轮 的疲 劳强 度 ,以及利用 多轴疲 劳 准则 Crossland曲线来评估 辐板孔的疲劳强 度.结果表 明 ,城际动 车组车 轮能满 足静强度 和疲 劳强度 性 能要求 .疲劳强度 的薄弱部位 是垂 直或者平行于车轮半 径的辐板 孔 的孔 边缘 中间位置 或 中间位置连 线 上 的点 ,以及辐板与轮毂过 渡部位 . 关键 词 :车轮 ;辐板 孔 ;有 限元 ;疲劳强度 ;疲劳准则 文 献 标 识 码 :A
0 引 言
车轮 是保 证 列 车 运 行 安 全 的重 要 部 件 之 一 , 其工况比较复杂 ,由于机车车辆通过 曲线 、道岔导 致车 轮 承载工 况 恶 劣 ,其 疲 劳 强 度 方 面 的 问题 日 益 凸显 ,车轮失 效 的主要 形 式是 疲劳 断裂 .其 中车 轮辐 板孔 裂纹 问题 对 车轮 的疲 劳强 度有 很大 的影 响 ,因此 依据 国 际标 准 对 车 轮 进 行 强 度分 析 与评 估 具 有重 要 的意义 ¨J.
1 单 轴 及 多轴 疲 劳 准 则
1.1 单轴 疲 劳准则 有关 文献 指 出 ,结 构 产 生疲 劳 裂 纹 方 向与最
大 主应力 方 向相 互垂 直 ,因此 可 以假 设 车 轮 的疲 劳破 坏是 由最 大 主应 力方 向 的应 力 造 成 的.参 照 UIC510—5和 BS EN 13979—1—2003标准 ,将三
析 .张澎 湃 、刘 金 朝 等 提 出 了修 正 的 Crossland 疲劳 准则 ,确定 准 则 中应 力 张量 第 1应 力 不变 量 最 大值 的系数 ,以轴 对 称 车 轮 和非 轴 对 称 车 轮 为 研究对象 ,对主应力法和修正的 Crossland疲劳准 则评 定 方 法 进 行 了 比 较 分 析 .刘 旭 采 用 基 于 UIC510—5标 准 中 的单 轴疲 劳 理论 的 车轮 疲 劳 强 度评 定准 则 和 Dang—Van多 轴 高 周 疲 劳 评 定 准 则这 2种 疲 劳评价 方法 对 同一车 轮进 行疲 劳强度 计算 ,并选取关键点进行应力分析 ,比较 2种方法 的安 全度 和适 用范 围以及评 估 车轮 的疲劳 薄弱 部 位 .本 文 以城 际动 车组 车轮 为 研究 对 象 ,运 用 Hy. permesh软 件 对 车轮 进 行 建 模 ,基 于 ANSYS软 件 对 车轮进 行有 限元 分 析 ,根据 UIC510—5标准 中 单轴 疲劳 准 则 以及 Crossland曲线 多 轴 疲 劳准 则 对 车轮强 度进 行疲 劳强 度分 析评 价.