数控铣削切削参数计算与选择
铣削加工切削用量的选择
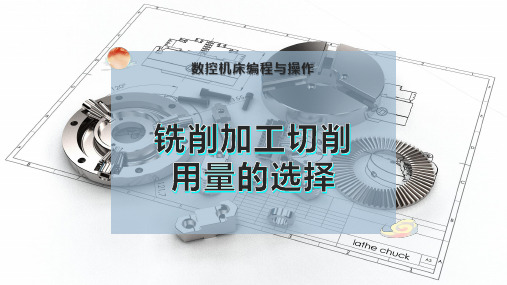
数控机床加工的切削用量
(3)确定进给速度
进给速度是数控机床切削用量中的重要参数。主要根 据零件的加工精度和表面粗糙度要求以及刀具、零件的材 料性质来选取。当加工精度和表面粗糙度要求高时,进给 速度应该选择得小些。一般应该在20mm/min~50mm/min 范围内选取。最大进给速度受机床刚度和进给系统的性能 的影响,并与数控系统中脉冲当量的大小有关。
总之,切削用量的具体数值应根据机床性能、相关的 手册并结合实际经验用类比法来确定,同时使主轴转速、 铣削深度以及进给速度三者能够相互适应,以形成最佳的 切削用量。在选择进给速度时,还应该注意零件加工中的 特殊因素。例如在轮廓加工中,当零件轮廓有拐角时,刀 具容易产生“超程”和“欠程”现象,从而导致加工误差。
数控机床编程与操作
数控机床加工的切削用量
切削用量主要包括:铣削深度、铣削速度、进给速度。 对于不同的加工方法,需要选用不同的切削用量,合理选择 切削用量的原则是:粗加工时,一般以提高生产率为主,但 也应该考虑经济性和加工成本;半精加工和精加工时,一般 应在保证加工质量的前提下,兼顾切削效率、经济性和加工 成本。具体选用数值应该根据机床说明书、切削用量手册, 并结合实际经验而定。 (1)铣削深度
数控机床编程与操作
效措施还是应该尽可能采取大的铣削深度。因为切削速度v 与刀具耐用度的关系成反比,所以切削速度v 的选取主要取
决于刀具耐用度。切削用量的选取可根据实际经验或参阅有 关手册。
主轴转速n(r/min)由切削速度v 来选定:
n= 1000v /(πd)
式中:v ——切削速度mm /min,由刀具耐用度决定;
在机床、工件和刀具刚度允许的情况下,应以最小的进 给次数切除待加工余量,最好一次切除待加工余量,以提高 生产效率。为了保证零件的加工精度和表面粗糙度,可留少 许余量留待最后加工。数控铣床的精加工余量一般可取 (0.2~0.5mm)。
数控机床铣削切削参数的优化与调整技巧
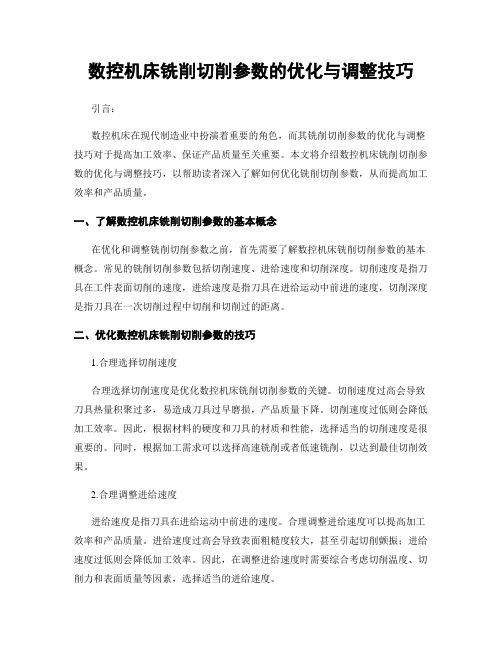
数控机床铣削切削参数的优化与调整技巧引言:数控机床在现代制造业中扮演着重要的角色,而其铣削切削参数的优化与调整技巧对于提高加工效率、保证产品质量至关重要。
本文将介绍数控机床铣削切削参数的优化与调整技巧,以帮助读者深入了解如何优化铣削切削参数,从而提高加工效率和产品质量。
一、了解数控机床铣削切削参数的基本概念在优化和调整铣削切削参数之前,首先需要了解数控机床铣削切削参数的基本概念。
常见的铣削切削参数包括切削速度、进给速度和切削深度。
切削速度是指刀具在工件表面切削的速度,进给速度是指刀具在进给运动中前进的速度,切削深度是指刀具在一次切削过程中切削和切削过的距离。
二、优化数控机床铣削切削参数的技巧1.合理选择切削速度合理选择切削速度是优化数控机床铣削切削参数的关键。
切削速度过高会导致刀具热量积聚过多,易造成刀具过早磨损,产品质量下降。
切削速度过低则会降低加工效率。
因此,根据材料的硬度和刀具的材质和性能,选择适当的切削速度是很重要的。
同时,根据加工需求可以选择高速铣削或者低速铣削,以达到最佳切削效果。
2.合理调整进给速度进给速度是指刀具在进给运动中前进的速度。
合理调整进给速度可以提高加工效率和产品质量。
进给速度过高会导致表面粗糙度较大,甚至引起切削颤振;进给速度过低则会降低加工效率。
因此,在调整进给速度时需要综合考虑切削温度、切削力和表面质量等因素,选择适当的进给速度。
3.合理确定切削深度切削深度是指刀具在一次切削过程中切削过的距离。
合理确定切削深度可以提高加工效率和产品质量。
切削深度过大会增加切削力和切削温度,降低切削稳定性,造成切削颤振,甚至导致刀具断裂;切削深度过小则会降低加工效率。
因此,在确定切削深度时需要综合考虑刀具性能、切削稳定性和加工需求等因素,选择合适的切削深度。
三、常见问题及解决方案1.切削温度过高切削温度过高会导致刀具早期磨损和产品质量下降。
解决方案包括选择适当的切削速度和进给速度,适当降低切削深度和刀具进给量,使用冷却液进行冷却等。
数控机床铣削切削参数的优化方法

数控机床铣削切削参数的优化方法数控机床是现代制造业中不可或缺的重要设备,而铣削是数控机床的一项常见加工工艺。
优化数控机床铣削切削参数,可以提高加工效率、降低生产成本,并且保证零件的质量。
本文将介绍数控机床铣削切削参数的优化方法。
首先,在选取数控机床铣削切削参数时,需要考虑工件材料的性质以及加工要求。
工件材料的硬度、韧性和切削性是影响切削参数选择的关键因素。
硬度高的材料需要选用较低的切削速度和切削深度,以减小切削力和切削温度,保证刀具寿命和工件表面质量。
韧性较高的材料则需要较大的切削速度和切削深度,以提高切削效率。
此外,加工要求也是选择切削参数的重要参考,比如加工精度要求高的零件需要选用较小的进给速度和进给量。
其次,合理选择刀具和切削液也是数控机床铣削切削参数优化的关键。
刀具的几何形状、材料和涂层会直接影响到切削力、表面粗糙度和加工效率。
在选择刀具时,应根据加工材料的不同选用合适的刀具材料和涂层,比如硬质合金刀具适用于铸铁和普通钢的铣削,而涂层刀具则适合高硬度材料的加工。
切削液的选择也十分重要,它可以降低切削温度、减小切削力、延长刀具寿命和提高表面质量。
常用的切削液有水溶性切削液和油基切削液,选择时需根据材料和加工要求综合考虑。
此外,切削力的控制也是数控机床铣削切削参数优化的重要环节。
切削力的大小直接关系到刀具的寿命和加工精度。
过大的切削力会导致刀具的磨损加剧,降低加工质量,甚至损坏刀具。
因此,在选取切削参数时,应尽量控制切削力的大小。
切削力与切削速度、进给速度和切削深度有关,一般来说,切削速度和进给速度越小,切削力也会相应减小。
同时,还可以采用刀具径向远离刀尖的切削方式,以减小切削力,提高切削稳定性。
此外,根据实际加工情况,需要通过试切试验来确定最佳的切削参数组合。
试切试验是通过不断调整切削速度、进给速度和切削深度,观察工件表面粗糙度、刀具磨损情况和加工前后尺寸误差的变化,从而找到最佳的切削参数组合。
数控铣削加工工艺范围及铣削方式

数控铣削加工工艺范围及铣削方式铣削是铣刀旋转作主运动,工件或铣刀作进给运动的切削加工方法。
铣削的主要工作及刀具与工件的运动形式如图所示。
在铣削过程中,根据铣床,铣刀及运动形式的不同可将铣削分为如下几种:(1)根据铣床分类根据铣床的结构将铣削方式分为立铣和卧铣.由于数控铣削一个工序中一般要加工多个表面,所以常见的数控铣床多为立式铣床。
(2)根据铣刀分类根据铣刀切削刃的形式和方位将铣削方式分为周铣和端铣.用分布于铣刀圆柱面上的刀齿铣削工作表面,称为周铣,如图6—2(a)所示;用分布于铣刀端平面上的刀齿进行铣削称为端铣,如图6—2(b)所示。
图中平行于铣刀轴线测量的切削层参数ap为背吃刀量.垂直于铣刀轴线测量的切削层参数ac为切削宽度,fz是每齿进给量.单独的周铣和端铣主要用于加工平面类零件,数控铣削中常用周、端铣组合加工曲面和型腔。
(3)根据铣刀和工件的运动形式公类根据铣刀和工作的相对运动将铣削方式分为顺铣和逆铣。
铣削时,铣刀切出工件时的切削速度方向与工件的进给方向相同,称为顺铣如图(6—3)a 所示;铣削时,铣刀切入工件时的切削速度方向与工件进给方向相反,称为逆铣,如图(6-3)b所示。
顺铣与逆铣比较:顺铣加工可以提高铣刀耐用度2~3倍,工件表面粗糙度值较小,尤其在铣削难加工材料时,效果更加明显。
铣床工作台的纵向进给运动一般由丝杠和螺母来实现,采用顺铣法加工时,对普通铣床首先要求铣床有消除进给丝杠螺母副间隙的装置,避免工作台窜动;其次要求毛坯表面没有破皮,工艺系统有足够的刚度。
如果具备这样的条件,应当优先考虑采用顺铣,否则应采用逆铣.目前生产中采用逆铣加工方式的比较多。
数控铣床采用无间隙的滚球丝杠传动,因此数控铣床均可采用顺铣加工.数控铣削主要特点(1)生产率高(2)可选用不同的铣削方式(3)断续切削(4)半封闭切削数控铣削主要加工对象(1)平面类零件加工面平行或垂直水平面,或加工面与水平面的夹角为定角的零件为平面类零件.目前,在数控铣床上加工的绝大多数零件属于平面类零件。
数控铣削加工中切削参数确定的研究

擐 火的彬响就足 县状况 。所以这 我们针 对玎 搠耗 和加J效 率米选择刀具参数 二 刀具损 耗卡l 袭现为破损和崩报两种膨式 。艘损 义 1 婴 - 要寝现为崩 、馓裂 碎断等打式 .是 其受 力条件决定
的 .魁 常 她 的 大 破 出 垭 叉 n 避 免 n 非 常 l 耗 而膪 捌 f q 捌
收耩 日期 ; O6 1一2 o— O 刊
耐川艘
■■I互】●■
维普资讯
业信 息化
裹 1 刀具切削速度 y选择裹
\
~ ~
刀 具 材 料 、\
、\
( m n m/ i )
TC iN
粉末
TC iN涂 层
工 件 材 料 及 硬 度~~、 ——
— \
高 涂层 速钢
高速钢
3 5 03 2~O 53 l— O 52 3—5 54 3—0 04 2一0 O 3
高速钢 粉末
高速钢
3~0 0 4 2—5 5 3 l— 5 5 2 3—0 5 5 3—5 0 4 2-5 0 3
刀具 参 数 琏 掸 主 要需 考 虑 工 件 加 工 质 量 刀具 损 耗 和
3数 铣加 工过程 中切削用■的确定试验及经
验 数 据
本 文强过 试验 .建 r人t i t与川 }f 用 f 戈的数 』! J『 I J 『
加 工效率 力嘣的 索 ,加 ‘ , r黄腊如 水考虑编
成操作者 枉大概 范围内选择 切 参数 .再在加 』 中根据 加 l :
情 况对 所 选 的 切 削 参敬 进 行 判 断 手 -憾 . 即 切 削 参数 的 l 】 闹
选栉 主要还 屉依赖 于操作 人员的素质和经验 ,i 伯 仃一 定 孟 的阿¨性 .社往会使褂数控 机床不能 在台理 的叫削参数
数控机床切削参数的选择与优化
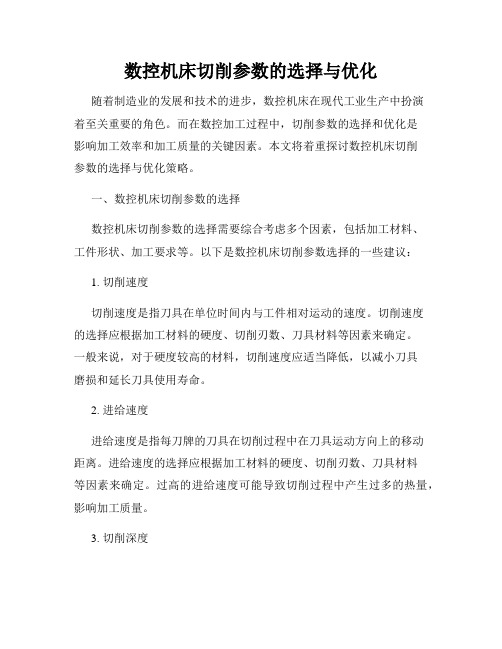
数控机床切削参数的选择与优化随着制造业的发展和技术的进步,数控机床在现代工业生产中扮演着至关重要的角色。
而在数控加工过程中,切削参数的选择和优化是影响加工效率和加工质量的关键因素。
本文将着重探讨数控机床切削参数的选择与优化策略。
一、数控机床切削参数的选择数控机床切削参数的选择需要综合考虑多个因素,包括加工材料、工件形状、加工要求等。
以下是数控机床切削参数选择的一些建议:1. 切削速度切削速度是指刀具在单位时间内与工件相对运动的速度。
切削速度的选择应根据加工材料的硬度、切削刃数、刀具材料等因素来确定。
一般来说,对于硬度较高的材料,切削速度应适当降低,以减小刀具磨损和延长刀具使用寿命。
2. 进给速度进给速度是指每刀牌的刀具在切削过程中在刀具运动方向上的移动距离。
进给速度的选择应根据加工材料的硬度、切削刃数、刀具材料等因素来确定。
过高的进给速度可能导致切削过程中产生过多的热量,影响加工质量。
3. 切削深度切削深度是指刀具在切削过程中与工件接触的最大深度。
切削深度的选择应考虑加工材料的硬度、切削刃数、刀具材料等因素。
较小的切削深度可以减小切削力和切削温度,提高加工精度。
4. 切削方式切削方式包括铣削、车削、钻削等。
选择合适的切削方式可以提高加工效率和加工质量。
对于不同形状的工件,应选择适合的切削方式,以确保切削过程的稳定和切削力的均匀分布。
二、数控机床切削参数的优化除了选择合适的切削参数外,优化切削参数也能提高加工效率和加工质量。
以下是一些常用的数控机床切削参数优化策略:1. 刀具润滑刀具润滑是切削过程中的重要环节,它能减小切削力和摩擦,并提高刀具的使用寿命。
选择合适的切削液类型和使用方法有助于减少切削过程中的热量积累和切削力的产生。
2. 切削力监测与控制通过切削力的监测和控制,可以实时了解加工过程中的切削负荷情况,从而优化切削参数的选择。
采用合适的传感器和控制系统,能够更好地预测和调节切削过程中的切削力,提高加工效率和加工质量。
切削用量的合理选择
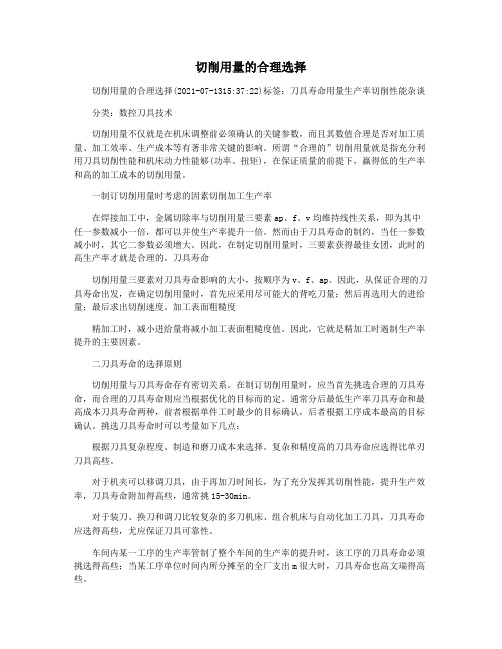
切削用量的合理选择切削用量的合理选择(2021-07-1315:37:22)标签:刀具寿命用量生产率切削性能杂谈分类:数控刀具技术切削用量不仅就是在机床调整前必须确认的关键参数,而且其数值合理是否对加工质量、加工效率、生产成本等有著非常关键的影响。
所谓“合理的”切削用量就是指充分利用刀具切削性能和机床动力性能够(功率、扭矩),在保证质量的前提下,赢得低的生产率和高的加工成本的切削用量。
一制订切削用量时考虑的因素切削加工生产率在焊接加工中,金属切除率与切削用量三要素ap、f、v均维持线性关系,即为其中任一参数减小一倍,都可以并使生产率提升一倍。
然而由于刀具寿命的制约,当任一参数减小时,其它二参数必须增大。
因此,在制定切削用量时,三要素获得最佳女团,此时的高生产率才就是合理的。
刀具寿命切削用量三要素对刀具寿命影响的大小,按顺序为v、f、ap。
因此,从保证合理的刀具寿命出发,在确定切削用量时,首先应采用尽可能大的背吃刀量;然后再选用大的进给量;最后求出切削速度。
加工表面粗糙度精加工时,减小进给量将减小加工表面粗糙度值。
因此,它就是精加工时遏制生产率提升的主要因素。
二刀具寿命的选择原则切削用量与刀具寿命存有密切关系。
在制订切削用量时,应当首先挑选合理的刀具寿命,而合理的刀具寿命则应当根据优化的目标而的定。
通常分后最低生产率刀具寿命和最高成本刀具寿命两种,前者根据单件工时最少的目标确认,后者根据工序成本最高的目标确认。
挑选刀具寿命时可以考量如下几点:根据刀具复杂程度、制造和磨刀成本来选择。
复杂和精度高的刀具寿命应选得比单刃刀具高些。
对于机夹可以移调刀具,由于再加刀时间长,为了充分发挥其切削性能,提升生产效率,刀具寿命附加得高些,通常挑15-30min。
对于装刀、换刀和调刀比较复杂的多刀机床、组合机床与自动化加工刀具,刀具寿命应选得高些,尤应保证刀具可靠性。
车间内某一工序的生产率管制了整个车间的生产率的提升时,该工序的刀具寿命必须挑选得高些;当某工序单位时间内所分摊至的全厂支出m很大时,刀具寿命也高文瑞得高些。
教案中职《数控加工工艺》数控铣削切削用量的确定

《数控铣削切削用量的确定》教案新课引入:(4min )提问:同学们还记得之前学习车削时,切削三要素是什么吗? 答:切削速度vc 、进给量f 、背吃刀量ap今天我们要学习铣削的切削用量,让我们一起看看和车削要素有什么差别吧新课教学:(20min ) 一、切削用量在铣削过程中所选用的切削用量称为铣削用量。
铣削用量的要素包括铣削速度vc 、进给量f 、背吃刀量ap 和铣削宽度ae 。
2.计算公式师生对话式,引起将旧知识和新知识建立起联系,让学生了解学习内容,提高学习热情积极性。
结合图片讲解透彻各个要素,采取启发、引导等方法讲授【讨论】1.铣刀直径是D=100mm,齿数是Z=12,铣削速度为V=26m/min ,进给量为0.06mm/z ,求铣床的主轴转速?求每分钟进给量? 【解析】二、切削用量的选择1.背吃刀量或铣削宽度的选取(1)在工件表面粗糙度值要求较大时,如果圆周铣削的加工余量小于5mm ,端铣的加工余量小于6mm ,则粗铣一次进给就可以达到要求。
但在加工余量较大,工艺系统刚度较差或机床动力不足时,可多分几次进给完成。
(2)在工件表面粗糙度值要求较小时,可分粗铣和半精铣两步进行。
粗铣时背吃刀量或铣削宽度选取同前。
粗铣后留0.5~1.0mm 的余量,在半精铣时切除。
(3)在工件表面粗糙度值要求很小时,可分粗铣、半精铣和精铣三步进行。
半精铣时背吃刀量或铣削宽度取 1.5~2mm ;精铣时圆周铣铣削宽度取0.3~0.5mm ,端铣背吃刀量取0.5~1mm 。
2.进给量与进给速度的选取进给量与进给速度是衡量切削用量的重要参数,根据零件的表面粗糙度、加工精度要求、刀具及工件材料等因素,参考有关切削用量手册选取。
3.切削速度的选择通过练习分析让学生开动脑筋,将公式结合实际应用,加深理解公式含义,同时激发学生学习专业课的兴趣和动力教会学生查表,依据已知条件,确定切削用量。
f=n×Z×0.06 =82.76×12×0.06 =59.59mm/minV=π×D×n/1000 26=3.1416×100×n/1000n=82.76 r/min铣削用量的要素包括铣削速度vc、进给量f、背吃刀量ap和铣削宽度ae。
- 1、下载文档前请自行甄别文档内容的完整性,平台不提供额外的编辑、内容补充、找答案等附加服务。
- 2、"仅部分预览"的文档,不可在线预览部分如存在完整性等问题,可反馈申请退款(可完整预览的文档不适用该条件!)。
- 3、如文档侵犯您的权益,请联系客服反馈,我们会尽快为您处理(人工客服工作时间:9:00-18:30)。
25~50
0.089
d0/2
20-37
25~
50
0.075-
0.102
d0
21~24
25~50
0.075
中碳钢
0.5
34-49
10
0.025
0.75
26~29
10
0.018
1.5
26-37
10
0.05
3
24~27
10
0.025
175
d0/4
23-32
10
0.025
d0/2
21~24
10
0.013
d0/2
20-27
10
0.018
d0
18~20
10
275
0.5
34-49
12
0.05
0.75
26~29
12
0.025-0.038
1.5
26-37
12
0.075
3
24~27
12
0.05-0.063
d0/4
23-32
12
0.05
d0/2
21~24
12
0.025
d0/2
20-27
12
0.025
d0
18~20
<HRC
36
0.03~0.08
0.07~0.12
0.05~0.12
0.12~0.25
HRC 35~
46
0.04~0.10
0.10~0.20
HRC 46~
56
0.03~0.08
0.07~0.10
铝镁合金
95~100
0.05~0.12
0.20~0.30
0.08~0.30
0.15~0.38
数控铣削切削参数选择范围
0.15~0.30
0.10~0.20
0.20~0.40
220~300
0.03~0.10
0.10~0.15
0.08~0.15
0.15~0.30
可锻铸铁
110~160
0.08~0.20
0.20~0.40
0.12~0.20
0.20~0.50
160~200
0.07~0.20
0.20~0.35
0.10~0.20
110~115
150~225
15~21
60~110
230~290
9~18
45~90
300~320
5~10
21~30
可锻铸铁
110~160
42~50
100~200
160~200
24~36
83~120
200~240
15~24
72~110
240~280
9~11
40~60
铸 钢
低炭
100~150
18~27
68~105
18
0.063
225
d0/2
20-37
18
0.05-
0.075
d0
21~24
18
0.05
0.5
52-64
25~
50
0.102-
0.13
0.75
30~34
25~50
0.102
1.5
38-49
25~
50
0.13-0.15
3
29~32
25~50
0.13
d0/4
34-43
25~
50
0.102-
0.13
d0/2
工件材料
硬度/HB
高速钢铣刀
硬质合金铣刀
立铣刀
端铣刀
立铣刀
端铣刀
低炭钢
<150
0.04~0.20
0.15~0.30
0.07~0.25
0.20~0.40
150~200
0.03~0.18
0.15~0.30
0.06~0.22
0.20~0.35
中、高炭钢
<220
0.04~0.20
0.15~0.25
0.06~0.22
数控铣削
切削参数计算选择与计算
2020.05.20 编辑
主轴转速的计算
1000Vc
n
D
式中Vc——切削速度N——主轴转速;D——刀具直径
工件材料
硬度/HB
铣削速度mm/min
高速钢铣刀
硬质合金铣刀
低、中炭钢
<220
21~40
60~150
225~290
15~36
54~115
300~425
9~15
36~75
10
0.038
d0/4
34-43
10
0.025
d0/2
26~29
10
0.018~
0.025
d0/2
20-37
10
0.018
d0
21~24
10
0.013
0.5
52-64
12
0.05
0.75
30~34
12
0.038
1.5
38-49
12
0.075
3
29~32
12
0.063
d0/4
34-43
12
0.05
d0/2
高炭钢
<220
18~36
60~130
225~325
14~21
53~105
325~375
8~21
36~48
375~425
6~10
35~45
合金钢
<220
15~35
55~120
225~325
10~24
37~80
325~425
5~9
30~60
工具钢
200~250
12~23
45~83
灰铸铁
110~140
24~36
0.15~0.35
225~235
0.03~0.15
0.10~0.20
0.05~0.20
0.12~0.25
325~425
0.03~0.12
0.08~0.15
0.04~0.15
0.10~0.20
灰铸铁
150~180
0.07~0.18
0.20~0.35
0.12~0.25
0.20~0.50
180~220
0.05~0.15
铣削平面及凸台
铣削槽
材料
铣削 深度(mm)
铣削速 度v(m/min)
铣刀 直径d0 mm
每齿进给 量
fa (mm/z)
铣削深度(mm)
铣削速 度v(m/min)
槽宽
d0(mm)
每齿进给 量
Fz (mm/z)
0.5
52-64
10
0.025
0.75
30~34
10
0.025
1.5
38-49
10
0.05
3
29~32
12
0.018
0.5
34-49
18
0.075
0.75
26~29
18
0.05-0.075
0.20~0.40
200~240
0.05~0.15
0.15~0.30
0.08~0.15
0.15~0.30
240~280
0.0பைடு நூலகம்~0.08
0.10~0.20
0.05~0.10
0.10~0.25
合金钢
<220
0.05~0.18
0.15~0.25
0.08~0.20
0.12~0.40
220~280
0.05~0.15
26~29
12
0.038
低碳钢
d0/2
20-37
12
0.025
d0
21~24
12
0.025
0.5
52-64
18
0.075-
0.102
0.75
30~34
18
0.075
1.5
38-49
18
0.102-
0.13
3
29~32
18
0.102
HB:1
25
d0/4
34-43
18
0.075-
0.102
d0/2
26~29
中炭
100~160
18~27
68~105
160~200
15~21
60~90
200~240
12~21
53~75
钢炭
180~240
9~18
53~80
铝合金
180~300
360~600
铜合金
45~100
120~190
镁合金
180~270
150~600
进给速度的计算
f Fzz N
式中Fz——每齿进给量Z——刀具刃数;N——主轴转速。
0.12~0.20
0.06~0.15
0.10~0.30
280~320
0.03~0.12
0.07~0.12
0.05~0.12
0.08~0.20
320~380
0.02~0.10
0.05~0.10
0.03~0.10
0.06~0.15
工具钢
退火状态
0.05~0.10
0.12~0.20
0.08~0.15
0.15~0.50