制造过程能力分析
工序过程能力分析
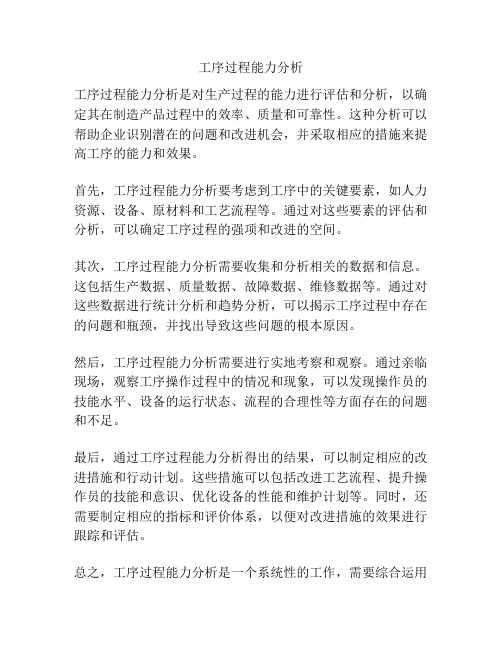
工序过程能力分析工序过程能力分析是对生产过程的能力进行评估和分析,以确定其在制造产品过程中的效率、质量和可靠性。
这种分析可以帮助企业识别潜在的问题和改进机会,并采取相应的措施来提高工序的能力和效果。
首先,工序过程能力分析要考虑到工序中的关键要素,如人力资源、设备、原材料和工艺流程等。
通过对这些要素的评估和分析,可以确定工序过程的强项和改进的空间。
其次,工序过程能力分析需要收集和分析相关的数据和信息。
这包括生产数据、质量数据、故障数据、维修数据等。
通过对这些数据进行统计分析和趋势分析,可以揭示工序过程中存在的问题和瓶颈,并找出导致这些问题的根本原因。
然后,工序过程能力分析需要进行实地考察和观察。
通过亲临现场,观察工序操作过程中的情况和现象,可以发现操作员的技能水平、设备的运行状态、流程的合理性等方面存在的问题和不足。
最后,通过工序过程能力分析得出的结果,可以制定相应的改进措施和行动计划。
这些措施可以包括改进工艺流程、提升操作员的技能和意识、优化设备的性能和维护计划等。
同时,还需要制定相应的指标和评价体系,以便对改进措施的效果进行跟踪和评估。
总之,工序过程能力分析是一个系统性的工作,需要综合运用统计分析、实地观察和经验判断等方法。
通过对工序过程能力的评估和分析,可以发现潜在的问题和改进机会,并采取相应的措施来提高工序的能力和效果。
这将有助于企业提高生产效率,降低成本,提升产品质量和市场竞争力。
工序过程能力分析是企业管理和生产控制中的重要环节。
通过对工序过程的评估和分析,可以确定生产过程中的强项和不足之处,并采取相应的措施来改进和优化工序的能力和效果。
下面将详细介绍工序过程能力分析的相关内容。
1. 收集和整理数据:首先,进行工序过程能力分析需要收集和整理相关的数据和信息。
这些数据包括生产数据、质量数据、设备状态数据等。
通过收集足够的数据,并进行整理和梳理,可以对工序过程进行全面、客观的评估。
2. 统计分析和趋势分析:收集到的数据可以通过统计分析和趋势分析进行进一步的处理。
过程能力指数分析
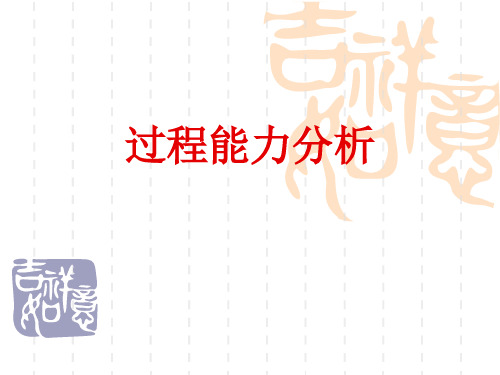
(1)无偏时双向公差过程能力指数
Cp
T
6
TU TL
6ˆ
,ˆ
R d2
S c4
(2) 过程有偏时双向公差过程能力指数。
引用偏移系数
Tu Tl u
则有
K
M u
2
T / 2 T / 2 (Tu Tl ) / 2
T C p上 =
/ 2 3
T
6
(1 2 )
T
T / 2+ Cp下 = 3
C pk
(1 K )Cp
▪ 长期过程能力。是指由偶因和异因之和所引起的总 变异,它实际上反映了“长期”变异,也称实绩变 异。
二、过程能力指数
1.过程能力指数 定义:表示过程能力满足过程质量标准要求程度的量
值。过程质量要求的范围(公差)和过程能力的比值。 公式: ➢ 无偏时双向公差过程能力指数计算 ➢ 过程有偏时双向公差过程能力指数计算 ➢ 单侧公差过程能力指数计算 ➢ 过程能力指数的判断与处置
过程能力分析
一、过程能力
1.过程质量控制的基本概念 ▪ 过程质量(Process Quality) 产品可分割的过程——产品质量特性(尺寸、强度等) 产品不可分割的过程——工艺质量特性(温度、浓度
等) 属于制造质量的范畴 优劣判断:符合性质量
与之相对应的概念有:适用性质量、满意性质量、卓 越质量等。
一、 过程能力
▪ 2.过程能力(Process Capability)
定义:过程在一定时间,处于控制状态(稳定状态)下的实际 加工能力(固有能力/质量保证能力),也就是加工质量满足 技术标准的能力。
——可拓展到服务领域。
稳定状态条件:(1)原材料或上一过程半成品按照标准供应; (2) 本过程按作业标准实施,各影响因素正常条件下进行; (3)过程完成后,产品检测按标准要求进行。
SPC过程能力分析

SPC过程能力分析SPC(过程能力分析)是统计过程控制的缩写。
它是一种统计工具,用于分析并监控一个过程的能力。
SPC过程能力分析是指通过测量和分析过程的输出来评估该过程达到规定要求的能力。
在本文中,我们将探讨SPC过程能力分析的概念、应用以及如何进行过程能力分析。
一、SPC过程能力分析的概念在SPC过程能力分析中,我们通常使用两个指标来评估一个过程的能力,即过程的稳定性和过程的能力。
过程的稳定性是指该过程的输出是否在一个可控制的范围内变动,而过程的能力是指该过程在满足规定要求的情况下能够产生符合要求的输出。
二、SPC过程能力分析的应用1.制造业中的过程能力分析:在制造业中,可以使用SPC过程能力分析来评估生产过程对产品质量的影响。
通过收集和分析产品的相关数据,可以确定生产过程是否稳定,并评估该过程是否满足产品质量要求。
2.服务行业中的过程能力分析:在服务行业中,也可以使用SPC过程能力分析来评估服务过程的能力。
例如,可以通过收集客户满意度调查数据来评估服务过程的质量,并确定提供服务的过程是否稳定。
3.医疗保健中的过程能力分析:在医疗保健领域,SPC过程能力分析可以用于监控和评估医疗过程的能力。
例如,可以通过分析手术成功率或患者满意度来评估手术过程的能力,并提供数据支持来改进手术过程。
三、SPC过程能力分析的步骤进行SPC过程能力分析通常需要以下步骤:1.确定过程的输出变量:首先,需要确定要分析和监控的过程的输出变量。
这些变量可以是产品质量指标、服务质量指标或其他与过程相关的指标。
2.收集数据:收集过程的输出数据,并记录在一个数据集中。
数据可以通过抽样、测量或观察来收集。
3.分析数据:通过分析收集到的数据来了解过程的稳定性和能力。
常用的分析方法包括直方图、控制图和能力指数的计算等。
4.评估过程稳定性:通过控制图来判断过程的稳定性。
控制图通常由平均线(中心线)和上下限线组成。
如果过程的输出数据点在控制限范围内波动,说明该过程是稳定的。
过程能力分析程序
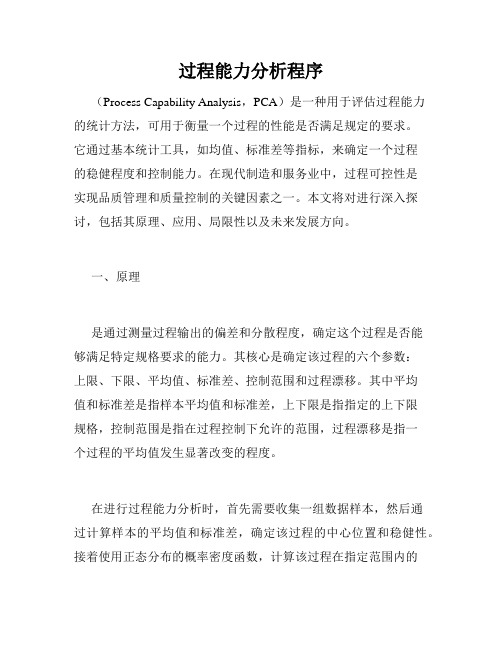
过程能力分析程序(Process Capability Analysis,PCA)是一种用于评估过程能力的统计方法,可用于衡量一个过程的性能是否满足规定的要求。
它通过基本统计工具,如均值、标准差等指标,来确定一个过程的稳健程度和控制能力。
在现代制造和服务业中,过程可控性是实现品质管理和质量控制的关键因素之一。
本文将对进行深入探讨,包括其原理、应用、局限性以及未来发展方向。
一、原理是通过测量过程输出的偏差和分散程度,确定这个过程是否能够满足特定规格要求的能力。
其核心是确定该过程的六个参数:上限、下限、平均值、标准差、控制范围和过程漂移。
其中平均值和标准差是指样本平均值和标准差,上下限是指指定的上下限规格,控制范围是指在过程控制下允许的范围,过程漂移是指一个过程的平均值发生显著改变的程度。
在进行过程能力分析时,首先需要收集一组数据样本,然后通过计算样本的平均值和标准差,确定该过程的中心位置和稳健性。
接着使用正态分布的概率密度函数,计算该过程在指定范围内的百分比,以估算该过程的能力水平。
最后,通过对比该过程的能力指标和规格要求,可以确定该过程是否满足要求。
二、应用是在现代制造和服务业中广泛应用的一种质量控制工具。
它可以帮助企业实现以下目标:1. 帮助企业确定产品或服务的能力水平,以便制定合理的质量目标和规格要求;2. 识别过程中可能存在的问题,从而加以改进和优化;3. 帮助企业确定是否需要更改过程或提高所用的材料和设备的质量等;4. 为企业提供决策依据,帮助其评估供应商和监控其供应链。
三、局限性虽然在质量控制领域中应用广泛,但它存在一些局限性:1. 该方法只能测量特定过程输出的性能,不能识别质量问题的原因;2. 过程能力分析只是一种预测性指标,无法保证过程的控制能力始终得到维持;3. 该方法对过程中的随机性和自然偏差非常敏感,如果样本数量太小,会导致估算的能力水平不准确;4. 过程能力分析只能评估符合正态分布假设的过程,不能评估非正态分布或数据齐全度不足的过程。
过程能力分析CPK
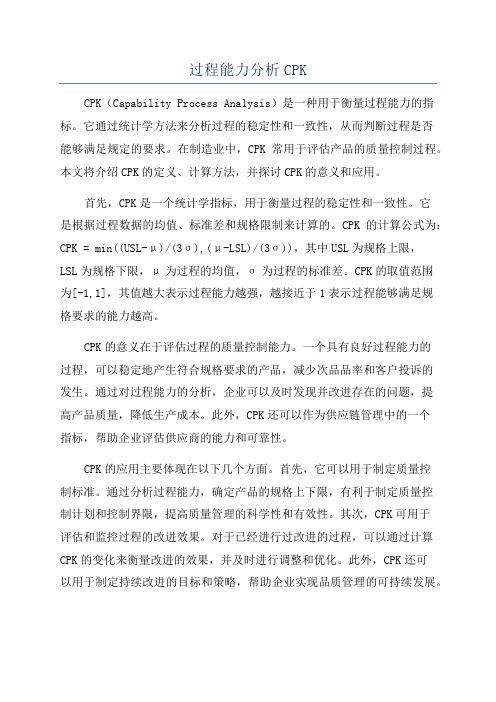
过程能力分析CPKCPK(Capability Process Analysis)是一种用于衡量过程能力的指标。
它通过统计学方法来分析过程的稳定性和一致性,从而判断过程是否能够满足规定的要求。
在制造业中,CPK常用于评估产品的质量控制过程。
本文将介绍CPK的定义、计算方法,并探讨CPK的意义和应用。
首先,CPK是一个统计学指标,用于衡量过程的稳定性和一致性。
它是根据过程数据的均值、标准差和规格限制来计算的。
CPK的计算公式为:CPK = min((USL-μ)/(3σ),(μ-LSL)/(3σ)),其中USL为规格上限,LSL为规格下限,μ为过程的均值,σ为过程的标准差。
CPK的取值范围为[-1,1],其值越大表示过程能力越强,越接近于1表示过程能够满足规格要求的能力越高。
CPK的意义在于评估过程的质量控制能力。
一个具有良好过程能力的过程,可以稳定地产生符合规格要求的产品,减少次品品率和客户投诉的发生。
通过对过程能力的分析,企业可以及时发现并改进存在的问题,提高产品质量,降低生产成本。
此外,CPK还可以作为供应链管理中的一个指标,帮助企业评估供应商的能力和可靠性。
CPK的应用主要体现在以下几个方面。
首先,它可以用于制定质量控制标准。
通过分析过程能力,确定产品的规格上下限,有利于制定质量控制计划和控制界限,提高质量管理的科学性和有效性。
其次,CPK可用于评估和监控过程的改进效果。
对于已经进行过改进的过程,可以通过计算CPK的变化来衡量改进的效果,并及时进行调整和优化。
此外,CPK还可以用于制定持续改进的目标和策略,帮助企业实现品质管理的可持续发展。
在实际应用中,CPK的计算需要大量的数据支撑。
必须收集足够的过程数据,包括过程的样本数据和规格限制,才能准确计算CPK值。
此外,CPK的计算还要求过程数据服从正态分布。
如果过程数据不符合正态分布,可能会导致CPK值的计算误差。
因此,在使用CPK进行过程分析时,需要确保数据收集准确可靠,并对数据是否符合正态分布进行检验。
过程能力与测量系统分析4
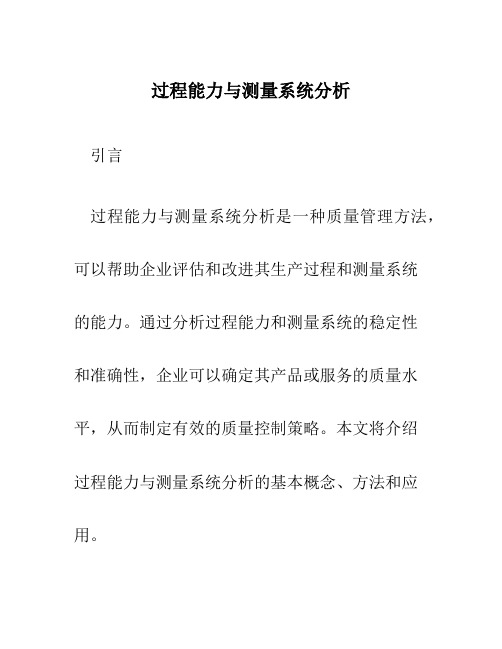
过程能力与测量系统分析引言过程能力与测量系统分析是一种质量管理方法,可以帮助企业评估和改进其生产过程和测量系统的能力。
通过分析过程能力和测量系统的稳定性和准确性,企业可以确定其产品或服务的质量水平,从而制定有效的质量控制策略。
本文将介绍过程能力与测量系统分析的基本概念、方法和应用。
过程能力分析过程能力分析是评估一个生产过程是否稳定、可控和满足质量要求的方法。
通过过程能力分析,企业可以确定生产过程是否具有足够的能力来满足客户的要求,并且可以预测生产过程在未来的一段时间内是否能够保持稳定的性能。
过程能力分析通常包括以下几个步骤:1.收集数据:首先,需要收集与生产过程相关的数据,例如产品的尺寸、重量、时间等。
这些数据可以通过实际生产过程中的测量结果或者控制图等方法获取。
2.统计分析:然后,对收集到的数据进行统计分析,计算得到过程能力指标。
常用的过程能力指标包括Cp、Cpk等,它们可以用来评估生产过程的稳定性和准确性。
3.结果解释:最后,根据得到的过程能力指标,判断生产过程是否能够满足质量要求。
如果过程能力指标高于一定的阈值,则表明生产过程具有足够的能力来满足质量要求;反之,则需要采取相应的改进措施。
过程能力分析可以帮助企业了解其生产过程的性能,发现潜在的问题,并制定改进措施,从而提高产品的质量水平和生产效率。
测量系统分析测量系统分析是评估一个测量系统是否准确和可靠的方法。
一个好的测量系统应该具有足够的准确性和稳定性,以确保测量结果的可靠性。
测量系统分析通常包括以下几个方面:系统的可重复性和再现性。
可重复性是指在相同的条件下进行多次测量时,得到相似的结果;再现性是指在不同的条件下进行多次测量时,得到相似的结果。
2.相关性分析:通过相关性分析,可以确定测量系统与实际值之间的一致性。
相关性分析通常使用皮尔逊相关系数或斯皮尔曼相关系数来度量。
系统是否存在系统性偏差。
偏倚分析通常使用均值差异或标准偏差差异来度量。
过程能力分析
7
过程能力指数的计算
一 计量值 1 双侧规格界限 (1)无偏 (2)有偏 2 单侧规格界限
(1)仅给出规格上限TU(望小值) (2)仅给出规格上限TL(望大值)
二 记数值 1 记件值 2 记点值
8
1 计量值双侧规格界限
双侧规格界限是指既具有规格上限(TU)要求,又有规格下限(TL)要求的情况
(1)无偏——规格中心Tm与分布中心 x重合
过程能力指数:
P2
或:
C pk
(1 k)Cp
(1 k)
T 6S
C pk
T 6S
2eT T 6S
T 2e 6S
当k≥1,即e≥T/2时,
P1 TL Tm
μ TU e
x
规定Cpk=0 (图中,曲线2)
●不合格品率估计:
有偏时过程能力指数与不合格品率
① p 1[(TU x ) (TL x )]
完全不同的概念。过程能力强并不等于对规格要求的满足程度高,相
x 反,过程 能力弱并不等于对规格要求的满足程度低。当质量特性服从
正态分布,而且其分布中心 与规格中心Tm重合时,一定的过程能力
指数将与一定的不合格品率相对应。因此,工序能力指数越大,说明
过程能力的贮备越充足,质量保证能力越强,潜力越大,不合格品率 越低。但这并不意味着加工精度和技术水平越高。
2Φ(2.727) 20.003197 0.006394
10
计量值—双侧规格界限
(2)有偏——规格中心Tm与分布中心 x
不重合
●计算公式:
T f(x)
绝对偏移量 :e Tm x (图中曲线1)
e
SPC过程能力分析报告
SPC过程能力分析报告SPC(统计过程控制)是一种以统计方法来控制过程稳定性和质量的管理工具。
通过在过程中收集数据并进行统计分析,SPC可以帮助企业识别和纠正过程中的变异,以确保产品或服务的一致性和稳定性。
本篇报告将对公司进行SPC过程能力分析,以评估和改进其过程控制能力。
一、背景介绍本次分析的对象是一家电子产品制造公司,其主要产品为手机电池。
公司希望通过SPC过程能力分析来评估和改进其电池生产过程的稳定性和质量,以提高产品一致性并降低缺陷率。
二、数据收集和分析为了进行SPC过程能力分析,我们收集了公司过去六个月的电池生产数据。
主要数据包括每月产量、每月缺陷数量以及每月质量控制检查结果等。
通过对数据进行统计分析,我们得出了以下结论:1.控制图分析我们使用控制图来分析过程的稳定性。
通过绘制产量、缺陷数量和质量控制检查结果的控制图,我们发现产量的控制图显示过程处于可接受的稳定性范围内,而缺陷数量和质量控制检查结果的控制图则显示过程存在明显的非随机变异。
2.批次分析我们对每个批次的电池进行了分析,发现一些批次的电池存在较高的缺陷率。
通过深入分析这些批次的生产数据和质量控制记录,我们发现生产过程中存在一些固定的问题,如材料供应商质量不稳定和操作员技能不足等。
三、问题原因分析基于数据收集和分析结果,我们对电池生产过程中存在的问题进行了原因分析。
主要问题包括以下几个方面:1.材料质量不稳定一些批次的电池缺陷率较高,部分原因是材料供应商质量不稳定。
为了解决这个问题,公司应该与供应商合作,建立更加稳定的供应链,并定期审核供应商的质量体系。
2.过程操作不规范操作员技能和培训不足是导致缺陷率高的原因之一、公司应该加强对操作员的培训,确保其熟悉操作流程和使用设备的规范。
此外,公司还应该建立标准操作程序,并通过培训和审查来确保操作员按照这些程序进行操作。
3.设备维护不及时设备故障和维护不及时也会导致生产过程的不稳定性和缺陷率的升高。
过程能力分析
二)过程能力分析1、过程能力过程能力指产品生产得每个过程对产品质量得保证程度,反映得就是处于稳定生产状态下得过程得实际加工能力,记为B。
获取产品生产得过程能力,就是质量管理中收集样本得目得之一,以便了解过程得生产能力如何,即生产合格品得能力究竟如何。
如果生产能力过低,必需采取措施加以改进。
过程能力越高,稳定性越高,生产能力也强。
过程能力得高低可以用标准差σ得大小来衡量。
σ越小则过程越稳定,过程能力越强;σ越大过程越不稳定,过程能力越弱。
当生产过程稳定,且产品得技术标准为双侧时,B=6σ(见图11—10)。
过程能力包括长期过程能力与短期过程能力。
短期过程能力就是指仅由偶然因素所引起得部分变异,它实际上反映了短期变异情况。
长期过程能力就是指由偶然因素与异常因素所引起得总变异,它实际反映了长期变异情况。
过程能力只与标准差有关,而与产品得技术要求无关,只表示一个过程固有得最佳性能。
标准差决定于质量因素,即人、机、料、法、环,与规范无关。
为了反映与衡量过程能力满足技术要求得程度,引进一个新指标,即过程能力指数。
[例题6] 过程能力得高低可以用标准差σ得大小来衡量。
σ越小则()。
A、过程标准越高B、过程越稳定C、过程越不稳定D、过程能力越强E、过程能力越弱答案:BD2.过程能力指数过程能力指数反映过程加工中质量满足产品技术要求得程度,也即产品得控制范围满足顾客要求得程度。
过程能力指数=技术要求/过程能力(11—14)过程能力指数越大,说明过程能力越满足技术要求,产品质量越有保证。
对于产品特性值分布得平均值μ与规范中心M重合即无偏移时用Cp衡量,对于产品特性值分布得平均值μ与规范中心M不重合即有偏差时用Cpk衡量。
①无偏移双侧规范情况得短期过程能力对于双侧规范情况,无偏移短期过程能力指数Cp得计算公式如下:大得情况,即0≤K<1。
3.过程能力指数与产品不合格率得关系当生产过程处于稳定状态时,过程能力指数Cp与不合格品率P相对应。
过程能力研究报告
过程能力研究报告过程能力研究报告引言过程能力是指一个系统或组织在特定过程中实现目标的能力。
在现代企业管理中,过程能力研究成为重要的课题,因为提高过程能力可以帮助企业提升效率、降低成本、改进质量,进而增强竞争力。
本报告旨在通过对过程能力的研究,从理论和实践两个方面,探究过程能力的重要性以及提高过程能力的方法。
理论研究过程能力的定义过程能力是指一个系统或组织在特定过程中实现目标的能力。
它包括两个方面的要素:过程的可控性和过程的稳定性。
过程的可控性意味着能够对过程进行控制,使其达到预期的结果;过程的稳定性意味着过程能够持续稳定地运行,不受随机因素的干扰。
过程能力的评估可以通过CPK指数来衡量,CPK指数代表了过程性能与规格界限之间的差值。
CPK值越高,说明过程能力越好。
过程能力的重要性过程能力的提高对企业来说非常重要。
首先,过程能力的提升可以帮助企业提高效率。
通过分析和改进各个环节的过程,可以消除浪费,减少资源的浪费,从而使企业更加高效地运营。
其次,过程能力的提高可以降低成本。
通过提高过程的稳定性和可控性,能够减少不良事件的发生,降低质量问题的成本和损失。
最后,过程能力的提高可以改进质量。
通过对过程进行分析和改进,可以减少变异性,提高产品或服务的一致性,从而提高客户满意度。
实践研究过程能力改进的方法1.流程分析与优化:通过对流程进行分析,找出流程中的瓶颈和问题,并进行优化,以提高过程的效率和稳定性。
2.数据收集与分析:对关键指标进行数据收集和分析,通过数据的监控和分析,可以追踪过程的变化和趋势,及时发现问题并采取措施进行改进。
3.培训与技能提升:提供员工培训,提高员工对过程的理解和掌握,增强员工的能力和素质,从而推动过程能力的提升。
4.技术支持与工具应用:通过应用先进的技术和工具,可以提高过程的自动化程度、减少人为干预,从而提高过程的稳定性和可控性。
实践案例分析案例一:制造业流程改进某制造企业的生产流程中存在着很多问题,如物料供应不及时、生产线停机等。
- 1、下载文档前请自行甄别文档内容的完整性,平台不提供额外的编辑、内容补充、找答案等附加服务。
- 2、"仅部分预览"的文档,不可在线预览部分如存在完整性等问题,可反馈申请退款(可完整预览的文档不适用该条件!)。
- 3、如文档侵犯您的权益,请联系客服反馈,我们会尽快为您处理(人工客服工作时间:9:00-18:30)。
例:设零件的尺寸要求(技术标准)为300.023,随机
抽样后计算样本特征值为 x 29.997,C p 1.095 求C pk
解:已知 C p 1.095 1
M (30.023 29.977) 30 2
T 30.023 29.977 0.046
所以
| M x | 30 29.997 0.003
Cp
TU TL 6S
5200 4800 1.075 6 62
16
工序能力指数的计算
2. 分布中心和标准中心不重合的情况下工序能力指数的计算
TL T/2
T/2
M
TU
令=|M-|,这里为分布中 心对标准中心M的绝对偏移
量。把对T/2的比值称为相
对偏移量或偏移系数,记作
K,即
K |M |
T /2 T /2
C
1 k
(C1
C2
Ck )
1 k
k
Ci
i 1
34
工序能力指数的计算
由泊松分布可得:
C C
则
CP C C 3C
35
工序能力指数的计算
例:抽取样本大小为n=50的样本20个,其中瑕疵点数分别 为:1,2,0,3,2,4,1,0,3,1,2,2,1,6,3,5,1,3,2,当允许样本瑕疵点 数C,为6时,求工序能力指数。
所谓稳定状态,应具备以下条件: 原材料或上一道工序半成品按照标准要求供应; 本工序按作业标准实施,并应在影响工序质量各主要 因素无异常的条件下进行; 工序完成后,产品检测按标准要求进行。
5
进行工序能力分析的意义
工序能力的测定和分析是保证产品质量的基础工作; 工序能力的测试分析是提高工序能力的有效手段; 工序能力的测试分析为质量改进找出方向。
17
工序能力指数的计算
又
M
TU
TL 2
,T
TU
TL
故
K
1 2
(TU
TL )
1 2
(TU
TL )
18
工序能力指数的计算
由前面公式可知: 1. 当恰好位于标准中心时,|M- |=0,则K=0,
这就是分布中心与标准中心重合的理想状态; 2. 当恰好位于标准上限或下限时,即= TU或=
TL时, 则K=1; 3. 当位于标准界限之外时,即>T/2,则K>1。
6
工序能力分析的用途
• 预测过程与规格符合的程度 • 帮助产品设计/开发人员选择或修改过程 • 协助设立过程控制的适当抽样区间 • 提供新设备采购的功能需求 • 不同供应商质量能力的评比 • 当不同过程间有相互关系时,可以提供作为规划生
产程序的参考 • 降低制造过程的变异性
7
工序能力分析重要性
在质量控制中收集样本的目的之一便是了解过程(或工 序)的生产能力有多大,即生产合格品的能力究竟有多 大,如果生产能力太低,那必须采取措施加以改进。 过程能力反映本身的生产能力,即过程的稳定程度,稳 定程度越高,那么生产能力就越大,对计量特性来讲, 其标准差的大小可以反映过程稳定程度的高低。
Cp=1.33
μ
40
过程能力的分等—三四级
0.67Cp<1.00
由二项分布可得
nP nP (1 P )
CP (nP) nP 3 nP (1 P )
30
工序能力指数的计算
当以不合格品率P作为检验产品质量指标,并以P作为标 准要求时,CP值可计算如下 如果要求批不合格率为P,取样本k个,每个样本大小分
别为n1,n2,…,nk,其样本平均值 n 与不合格品率平均值 分别为: P
nP 100 0.039 3.9
CP
nP nP 3 nP (1 P )
3
10 3.9
1.0503
3.9(1 0.039)
33
工序能力指数的计算
5. 计点值情况下 C值p的计算
在计点值情况下仍相当于单公差情况,其 C p值计算公式为
C p (TU ) / 3
当以瑕疵点数(或缺陷数)C为检验产品质量指标,并以 C,作为标准要求时,CP值可计算如下 取样本k个,每个样本大小为n,其中瑕疵点数分别为 C1,C2,…,Ck,则样本瑕疵点数的平均值为
2. 分布中心和标准中心不重合的情况下工序能力指 数的计算;
3. 计量值为单侧公差情况下工序能力指数的计算; 4. 计件值情况下工序能力指数的计算; 5. 计点值情况下工序能力指数的计算。
14
工序能力指数的计算
1. 双侧公差而且分布中心和标准中心重合的情况
TL
T
TU
6
Cp
T B
T
6
TU TL
6
n
1 k
(n1
n2ห้องสมุดไป่ตู้
nk )
1 k
k
ni
i 1
k
P
n1P1 n2 P2 nk Pk n1 n2 nk
ni Pi
i 1 k
ni
i 1
31
工序能力指数的计算
这时有: P
则
1 P (1 P )
n
CP 3
P P 1 P (1 P ) n
注意:样本大小n最好为定值,以减小误差
32
制造过程能力分析
1
过程的概念:过程的定义
控制
输入
输出
过程
资源
过程--使用资源将输入转化为输出的活动的系统。
2
过程的概念:过程的定义
输入
输出
过程A
控
控
制
制
输入
过程B
输出 输入
过程D
输出
在质量管理体系中,任何一个 过程都不会孤立地存在,若干 过程之间的相互关系构成过 程网络。
资
源
输入
过程C
输出
在质量管理体系中,过程网络的有效运作 是体系有效运行的重要条件。
C p (TU ) / 3
当以不合格品数nP作为检验产品质量指标,并以(nP), 取样本k个,每个样本大小为n,其中不合格品数分别为: (nP)1,(nP)2,…,(nP)k,则样本不合格品数的平均值为
其中
nP
k
P
(nP)1 (nP)2
(nP)k
(nP)i
i 1
kn
kn
29
工序能力指数的计算
12
24
36
新的装配系统
48 时间(周)
11
工序能力指数的概念
质量标准是指工序加工产品必须达到的质量要求,通常 用标准、公差(容差)等来衡量,一般用符号T来表示。 质量标准(T)与工序能力(B)之比值,称为工序能 力指数,记为Cp。 工序能力指数是衡量工序能力大小的数值。对于技术要 求满足程度的指标,工序能力指数越大,说明工序能力 越能满足技术要求,甚至有一定的能力储备。
可以根据样本方差S来估计
(M)
Cp
T 6S
TU TL 6S
15
工序能力指数的计算
1. 双侧公差而且分布中心和标准中心重合的情况
例 某零件强度的屈服界设计要求为4800-5200kg/cm2,从100个样 品中测得样本标准偏差为62kg/cm2,求工序能力指数。
解:当工序过程处于稳定状态,而样本大小n=100足 够了,可以用S来估计,则工序能力指数为:
8
工序能力
工序能力通常以产品质量特性数据分布的6倍 标准偏差表示。
B = 6σ
9
计算工序能力步骤
从过程中收集一批数据x1,x2,…,xn; 利用这批数据检验过程的输出特性是否服从正态分布; 若过程稳定,则可用这批数据估计输出特性的标准差 ,将其乘以6即得过程能力的估计值。
10
6 [mm]
10.0 8.0 6.0 4.0 2.0
例——某一产品含某一杂质要求最高不能超过12.2 毫克,样本标准差s=0.038,样本均值为12.1。求工 序能力指数。
C p上
TU X
3
12.2 12.1 0.877 3 0.038
28
工序能力指数的计算
4. 计件值情况下 C值p的计算
在计件情况下相当于单公差情况,其C p 值计算公式为
20
工序能力指数的计算
C pk
T /2 3
T
6
(1 2 )
T
因为 K 2
T
T
C pk 6 (1 K )
又因为
T
6
CP
CPk CP (1 K )
当K=0, Cpk= Cp,即偏移量为0,修正工序能力指数就是 一般的工序能力指数。当K>=1时, Cpk=0,这时Cp实际上 也已为0。
21
工序能力指数的计算例子
C
1 k
k
Ci
i 1
1 (1 2 20
2) 2.25
CP
C 3
C C
6 2.25 3 2.25
0.833
36
练习
某零件图纸尺寸要求为30+0.2mm,样本标准偏差
S为0.038, =X=30.1,其规格上限T=30.2,求
工序能力指数。
已知某零件尺寸为
50
0.3 0.1
m,m取样实测后求得
Cp
T B
T
6
12
基本假定
过程是稳定的,即过程的输出质量特性值X服从 正态分布。
N(, 2)
产品的规格限(下规格限TL和上规格限TU)能 准确反映顾客(下道工序的工人,使用者等) 的要求。 这两个假定分别说明过程的情况及顾客的要求。
13
几种情况
1. 计量值为双侧公差而且分布中心和标准中心重合 的情况;
工序能力指数的计算