冲压模具设计与制造(2-4)
模具设计与制造试题四及答案

模具设计与制造试题四及答案一、填空题(20分,每空1分)1.模具设计有两个基本条件,即和。
2.常用的冲压材料主要有、和。
3.弯曲变形过程可以分为、和三个阶段。
4.拉深可分为和。
5.空心坯料胀形的方法一般分为和。
6.根据成型工艺的性能不同,塑料可分为和。
7.常见的压铸机按压射室的特点可分为和两类。
8.模具中常用的成形铣削加工方法有和。
9.注射模的浇注系统可分为和两大类。
二、判断题(10分,每题1分)1.冲压模具的导柱和导套大都使用高碳钢制造。
()2.相对弯曲半径大,弯曲变形程度小,则弯曲后的回弹量就小。
()3.材料硬化指数值越大,拉深性能就越差,越容易拉裂。
()4.落料时,应以凸模为基准配制凹模。
()5.外缘翻边时应力应变的分布是不均匀的,在变形区内切向的拉应力和应变在中部最小,向两端逐渐增大。
()6.带有活动镶件的注射模具生产效率高,一般用于大批量生产。
()7.当工件表面有硬皮,或机床的进给机构有间隙时,尽量采用顺铣。
()8.材料的应力状态中,压应力的成分越大,拉应力的成分越小,越有利于材料塑性的发挥。
()9.在压力机的一次行程中,能完成两道或两道以上的冲压工序的模具称为级进模。
()10.刀具半径补偿的目的在于编程时可以不考虑刀具的半径,只要在实际加工中输入刀具半径即可。
()三、选择题(16分,每题2分)1.缩口变形区的材料主要受()。
A、两向拉应力B、两向压应力C、径向拉应力和切向压应力D、径向压应力和切向拉应力2.在注射模中,为便于凝料从主流道中拉出,需要将主流道设计成圆锥形,锥度一般为()。
A、2°~6°B、6°~10°C、10°~16°D、16°~20°3.在注射成型的每个周期中,将塑件及浇注系统凝料从模具中脱出的机构称为()。
A、导向机构B、顶件机构C、抽芯机构D、推出机构4.金属熔体从进入内浇口至充满型腔和溢流槽所需的时间称为()。
冲压模具设计与制造

第一章 冲压模具设计与制造基础
内容简介:
本章讲述冲压模具设计与制造的基础知识。 涉及冲压和冲模概念、冲压工序和冲模分类;常见冲压设备及工作原理、选用原则;冲压成形基本原理和规律;冲压成形性能及常见冲压材料;模具材料种类、性能、选用原则及热处理方法;模具制造特点、模具零件加工方法及应用等 。
第一章 冲压模具设计与制造基础
一、冲压与冲模概念
1.基本概念(续)
冲压模具:
在冲压加工中,将材料加工成零件(或半成品)的一种特殊工艺装备,称为冲压模具(俗称冲模)。
第一章 冲压模具设计与制造基础
第一节 冲压成形与模具技术概述 冲压与冲模概念 基本概念(续) 合理的冲压工艺 先进的模具 高效的冲压设备 冲压生产的三要素
第一章 冲压模具设计与制造基础
多工位精密级进模
第一章 冲压模具设计与制造基础
冲压成形产品示例一——日常用品
第一章 冲压模具设计与制造基础
冲压成形产品示例二—— 高科技产品 汽车覆盖件 飞机蒙皮
第一章 冲压模具设计与制造基础
数控高速铣削加工
高效 、高精度 、高的表面质量 、可加工高硬材料
第一章 冲压模具设计与制造基础
五、冲压技术现状与发展方向(续)
第一节 冲压成形与模具技术概述
多品种、少批量,更新换代速度快
计算机技术、制造新技术
第一章 冲压模具设计与制造基础
(1)冲压成形理论及冲压工艺
加强理论研究,开展CAE技术应用。 开发和应用冲压新工艺。
2.冲压技术发展方向
满足产品开发在T(Time)、Q(Quality)、 C(Cost)、S(Service)、E(Environment)的要求。
1.我国冲压技术现状 技术落后、经济效益低。 主要原因:①冲压基础理论与成形工艺落后; ②模具标准化程度低; ③模具设计方法和手段、模具制造工艺及设备落后; ④模具专业化水平低。 所以,结果导致我国模具在寿命、效率、加工精度、生产周期等方面与先进工业发达国家的模具相比差距相当大。
《冲压模具设计与制造》课程教学大纲DOC

《冲压模具基础》课程教学大纲课程编号:课程英文译名:课内总学时:72学时学分:4。
5学分课程类别:必修课开课对象:汽车制造与装配技术专业执笔人:编写日期:一、课程性质、目的和任务《冲压模具设计与制造》是汽车制造及汽车整形专业的一门主干专业技术课,它是一门将冲压成形加工原理、冲压设备、冲压工艺、冲模设计与冲模制造有机融合,综合性和实践性较强的课程。
其目的是使学生了解冲压变形规律,认识冲压成形工艺方法,冲压模具结构,冲压模具制造方法与手段,掌握冲压模具设计与计算方法,掌握冲压工艺与模具设计方法,冲压模具制造工艺方法,能进行中等冲压零件的冲压工艺编制,冲模设计与冲模制造工艺编制,并培养学生发现问题、分析问题和解决问题的能力,培养学生逻辑思维能力,为毕业设计及毕业以后从事专业工作打下必要的基础。
二、教学基本要求本课程是冲压模具设计与计算,冲压模具结构,模具制造工艺方法为重点。
学外本课程应达到以下基本要求:1、能应用冲压变形理论,分析中等复杂冲压件变形特点,制定合理冲压工艺规程的能力。
2、协调冲压设备与模具的关系,选择冲压设备的能力。
3、熟悉掌握冲模设计计算方法,具备中等复杂冲模结构选择和设计的能力,所设计的冲模应工作可行、操作方便、便于加工和装配,技术经济性好。
4、具备正确选择冲压模具加工方法,制定中等复杂冲模制造工艺和装配工艺的能力.5、初步具备进行多工位级进模设计和制造的能力。
6、初步具备进行分析和处理试模过程中产生的有关技术问题的能力。
三、教学内容及要求:第1章冲压模具设计与制造基础1.1 冲压成形与模具技术概述掌握冲压与冲模概念;冲压工序的分类;冲模的分类;冲模设计与制造的要求;了解冲压现状与发展方向。
1.2 冲压设备及选用了解常见冲压设备;掌握冲压设备的选用;模具的安装。
1.3 冲压变形理论基础掌握塑性变形的概念;理解塑性力学基础;掌握金属塑性变形的一些基本规律;冲压材料及其冲压成形性能.1.4 模具材料选用掌握冲压对模具材料的要求;冲模材料的选用原则;冲模常见材料及热处理要求。
冲压模具设计方法与步骤(精)

冲压模具设计的方法与步骤1、冲压零件的冲压工艺性分析冲压零件必须具有良好的冲压工艺性,才能以最简单、最经济的方法制造出合格的冲压零件,可以按照以下的方法完成冲压件的工艺性分析:a. 读懂零件图;除零件形状尺寸外,重点要了解零件精度和表面粗糙度的要求。
b. 分析零件的结构和形状是否适合冲压加工。
c. 分析零件的基准选择及尺寸标注是否合理,尺寸、位置和形状精度是否适合冲压加工。
d. 冲裁件断面的表面粗糙度要求是否过高。
e. 是否有足够大的生产批量。
如果零件的工艺性太差,应与设计人员协商,提出修改设计的方案。
如果生产批量太小,应考虑采用其它的生产方法进行加工。
2、冲压工艺方案设计及最佳工艺规程设计:a. 根据冲压零件的形状尺寸, 初步确定冲压工序的性质,如:冲裁、弯曲、拉深、胀形、扩孔。
b. 核算各冲压成形方法的变形程度,若变形成度超过极限变形程度,应计算该工序的冲压次数。
c. 根据各工序的变形特点和质量要求,安排合理的冲压顺序。
要注意确保每道工序的变形区都是弱区, 已经成形的部分 (含已经冲制出的孔或外形在以后的工序中不得再参与变形, 多角弯曲件要先弯外后弯内, 要安排必要的辅助工序和整形、校平、热处理等工序。
d. 在保证制件精度的前提下,根据生产批量和毛坯定位与出料要求。
确定合理的工序组合方式。
e. 要设计两个以上的工艺方案,并从质量、成本、生产率、模具的刃磨与维修、模具寿命及操作安全性等各个方面进行比较,从中选定一个最佳的工艺方案。
f. 初步确定各个工序的冲压设备。
3、冲压零件毛坯设计及排样图设计:a. 按冲压件性质尺寸,计算毛坯尺寸,绘制毛坯图。
b. 按毛坯性质尺寸,设计排样图,进行材料利用率计算。
要设计多种排样方案, 经过比较选择其中的最佳方案。
4、冲压模具设计:a. 确定冲压加工各工序的模具结构形式,并绘制模具简图。
b. 对指定的 1— 2个工序的模具进行详细的结构设计,并绘制模具工作图。
冲压模具设计与制造考试复习题.doc
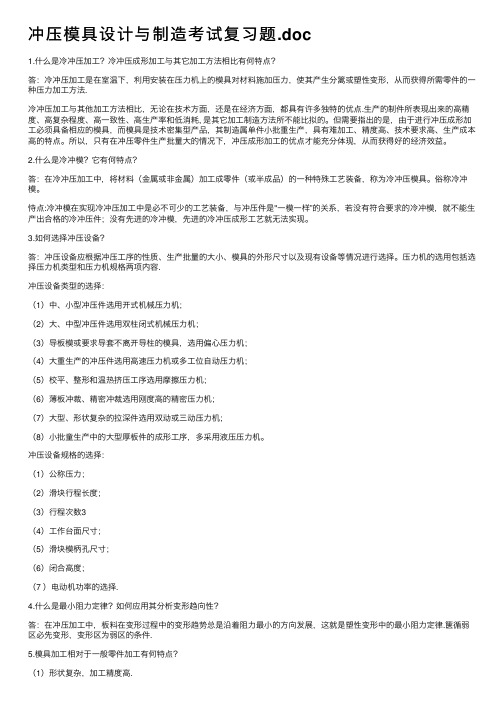
冲压模具设计与制造考试复习题.doc1.什么是冷冲压加⼯?冷冲压成形加⼯与其它加⼯⽅法相⽐有何特点?答:冷冲压加⼯是在室温下,利⽤安装在压⼒机上的模具对材料施加压⼒,使其产⽣分篱或塑性变形,从⽽获得所需零件的⼀种压⼒加⼯⽅法.冷冲压加⼯与其他加⼯⽅法相⽐,⽆论在技术⽅⾯,还是在经济⽅⾯,都具有许多独特的优点.⽣产的制件所表现出来的⾼精度、⾼复杂程度、⾼⼀致性、⾼⽣产率和低消耗, 是其它加⼯制造⽅法所不能⽐拟的。
但需要指出的是,由于进⾏冲压成形加⼯必须具备相应的模具,⽽模具是技术密集型产品,其制造属单件⼩批重⽣产,具有难加⼯、精度⾼、技术要求⾼、⽣产成本⾼的特点。
所以,只有在冲压零件⽣产批量⼤的情况下,冲压成形加⼯的优点才能充分体现,从⽽获得好的经济效益。
2.什么是冷冲模?它有何特点?答:在冷冲压加⼯中,将材料(⾦属或⾮⾦属)加⼯成零件(或半成品)的⼀种特殊⼯艺装备,称为冷冲压模具。
俗称冷冲模。
恃点:冷冲模在实现冷冲压加⼯中是必不可少的⼯艺装备,与冲压件是"⼀模⼀样”的关系,若没有符合要求的冷冲模,就不能⽣产出合格的冷冲压件;没有先进的冷冲模,先进的冷冲压成形⼯艺就⽆法实现。
3.如何选择冲压设备?答:冲压设备应根据冲压⼯序的性质、⽣产批量的⼤⼩、模具的外形尺⼨以及现有设备等情况进⾏选择。
压⼒机的选⽤包括选择压⼒机类型和压⼒机规格两项内容.冲压设备类型的选择:(1)中、⼩型冲压件选⽤开式机械压⼒机;(2)⼤、中型冲压件选⽤双柱闭式机械压⼒机;(3)导板模或要求导套不离开导柱的模具,选⽤偏⼼压⼒机;(4)⼤重⽣产的冲压件选⽤⾼速压⼒机或多⼯位⾃动压⼒机;(5)校平、整形和温热挤压⼯序选⽤摩擦压⼒机;(6)薄板冲裁、精密冲裁选⽤刚度⾼的精密压⼒机;(7)⼤型、形状复杂的拉深件选⽤双动或三动压⼒机;(8)⼩批童⽣产中的⼤型厚板件的成形⼯序,多采⽤液压压⼒机。
冲压设备规格的选择:(1)公称压⼒;(2)滑块⾏程长度;(3)⾏程次数3(4)⼯作台⾯尺⼨;(5)滑块模柄孔尺⼨;(6)闭合⾼度;(7 )电动机功率的选择.4.什么是最⼩阻⼒定律?如何应⽤其分析变形趋向性?答:在冲压加⼯中,板料在变形过程中的变形趋势总是沿着阻⼒最⼩的⽅向发展,这就是塑性变形中的最⼩阻⼒定律.箧循弱区必先变形,变形区为弱区的条件.5.模具加⼯相对于⼀般零件加⼯有何特点?(1)形状复杂,加⼯精度⾼.(2)模具材料性能优异,硬度⾼,加⼯难度⼤.(3)模具⽣产批童⼩,⼤多具有单件⽣产的特点。
冲压模具的设计与制造分析
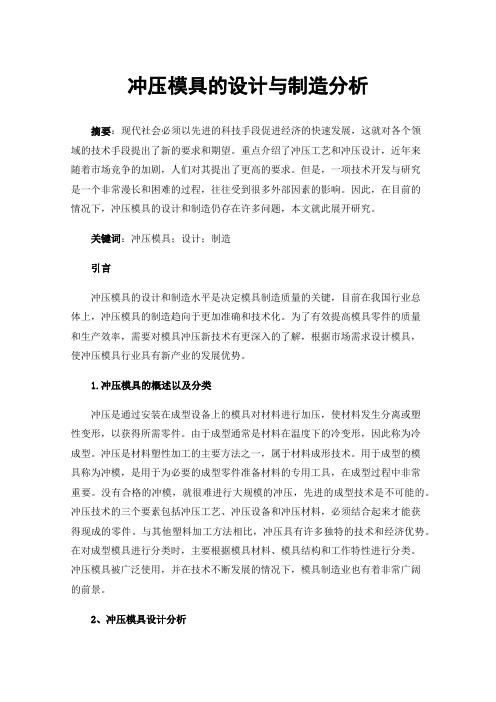
冲压模具的设计与制造分析摘要:现代社会必须以先进的科技手段促进经济的快速发展,这就对各个领域的技术手段提出了新的要求和期望。
重点介绍了冲压工艺和冲压设计,近年来随着市场竞争的加剧,人们对其提出了更高的要求。
但是,一项技术开发与研究是一个非常漫长和困难的过程,往往受到很多外部因素的影响。
因此,在目前的情况下,冲压模具的设计和制造仍存在许多问题,本文就此展开研究。
关键词:冲压模具;设计;制造引言冲压模具的设计和制造水平是决定模具制造质量的关键,目前在我国行业总体上,冲压模具的制造趋向于更加准确和技术化。
为了有效提高模具零件的质量和生产效率,需要对模具冲压新技术有更深入的了解,根据市场需求设计模具,使冲压模具行业具有新产业的发展优势。
1.冲压模具的概述以及分类冲压是通过安装在成型设备上的模具对材料进行加压,使材料发生分离或塑性变形,以获得所需零件。
由于成型通常是材料在温度下的冷变形,因此称为冷成型。
冲压是材料塑性加工的主要方法之一,属于材料成形技术。
用于成型的模具称为冲模,是用于为必要的成型零件准备材料的专用工具,在成型过程中非常重要。
没有合格的冲模,就很难进行大规模的冲压,先进的成型技术是不可能的。
冲压技术的三个要素包括冲压工艺、冲压设备和冲压材料,必须结合起来才能获得现成的零件。
与其他塑料加工方法相比,冲压具有许多独特的技术和经济优势。
在对成型模具进行分类时,主要根据模具材料、模具结构和工作特性进行分类。
冲压模具被广泛使用,并在技术不断发展的情况下,模具制造业也有着非常广阔的前景。
2、冲压模具设计分析2.1 设定目标尺寸在设计模具图的过程中,第一步是根据产品图的尺寸分析确定最终产品的尺寸。
具体而言,在可接受的产品公差范围内,最终产品尺寸值由冲头和模具的磨损趋势决定。
例如,在选择内径时,选择最大值,在考虑冲击器磨损和毛刺等因素的情况下设置外径,然后选择最小值。
总的来说,目标大小的选择与设计人员的工作经验、专业技能水平、产品预测等密切相关。
汽车车门外板冲压模具设计
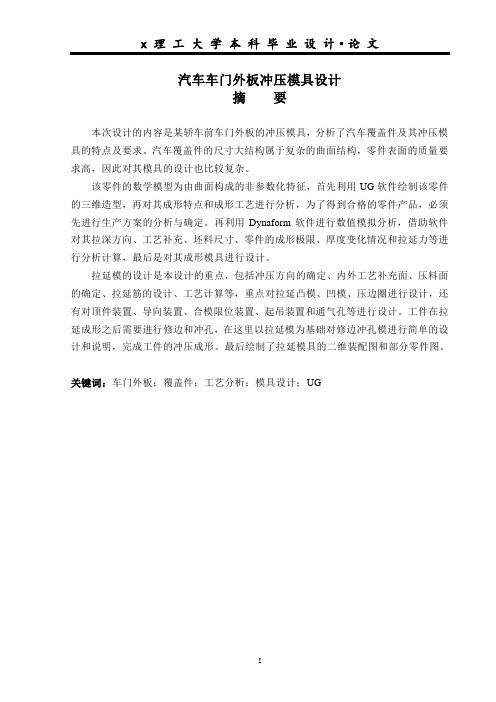
汽车车门外板冲压模具设计摘要本次设计的内容是某轿车前车门外板的冲压模具,分析了汽车覆盖件及其冲压模具的特点及要求。
汽车覆盖件的尺寸大结构属于复杂的曲面结构,零件表面的质量要求高,因此对其模具的设计也比较复杂。
该零件的数学模型为由曲面构成的非参数化特征,首先利用UG软件绘制该零件的三维造型,再对其成形特点和成形工艺进行分析,为了得到合格的零件产品,必须先进行生产方案的分析与确定。
再利用Dynaform软件进行数值模拟分析,借助软件对其拉深方向、工艺补充、坯料尺寸、零件的成形极限、厚度变化情况和拉延力等进行分析计算,最后是对其成形模具进行设计。
拉延模的设计是本设计的重点,包括冲压方向的确定、内外工艺补充面、压料面的确定、拉延筋的设计、工艺计算等,重点对拉延凸模、凹模、压边圈进行设计,还有对顶件装置、导向装置、合模限位装置、起吊装置和通气孔等进行设计。
工件在拉延成形之后需要进行修边和冲孔,在这里以拉延模为基础对修边冲孔模进行简单的设计和说明,完成工件的冲压成形。
最后绘制了拉延模具的二维装配图和部分零件图。
关键词:车门外板;覆盖件;工艺分析;模具设计;UGThe design of car door panels stamping dieAbstract: The content is designed for a car before the car door panel stamping dies, analyzes and stamping automotive panel characteristics and requirements. Large size structure of an automobile covering parts are complex surface structure, high quality requirements of the part surface, so the design of their molds more complicated.Mathematical model of the part of the grounds of non-parametric feature curved surface, the first use of UG software to draw three-dimensional modeling of the part, and then analyzed the characteristics shaping and forming processes, in order to get qualified parts products must be produced programs Analysis and determination. Reuse Dynaform numerical simulation analysis software, with the software to its drawing direction, forming limit addendum, blank size, part thickness changes and drawing force of analysis and calculation, and finally the design of its mold.Drawing die design is the focus of this design, including stamping direction is determined, both inside and outside addendum, binder determination drawbead design, process calculation, focusing on drawing punch, die, blankholder ring design, as well as for top pieces of equipment, guides, clamping stopper, lifting device and the vent, etc. design. After forming the workpiece drawing needed trimming and punching, drawing die in here with the basis for trimming punching die design and simple instructions to complete the stamping workpiece shape. Finally, draw the two-dimensional drawing die assembly drawing and some parts Fig.Key words:car door panels;cover;process pnalysis;mold design;UG目次摘要................................................ 错误!未定义书签。
螺栓垫片冲压工艺及冲压模具设计设计
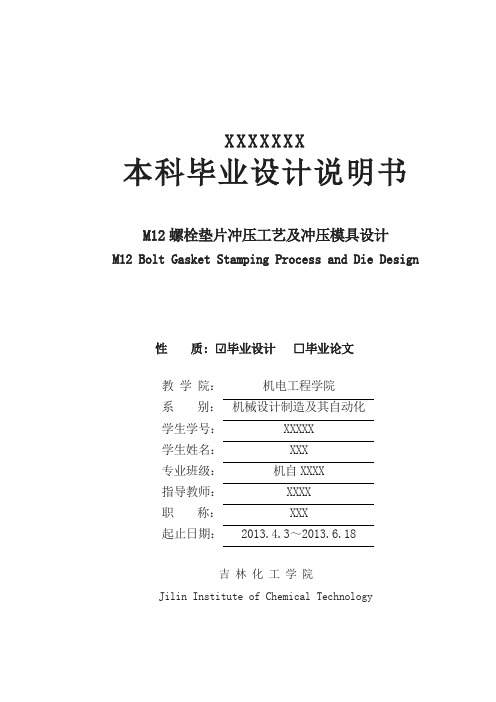
X X X X X X X本科毕业设计说明书M12螺栓垫片冲压工艺及冲压模具设计M12 Bolt Gasket Stamping Process and Die Design性质: □√毕业设计□毕业论文教学院:机电工程学院系别:机械设计制造及其自动化学生学号:XXXXX学生姓名:XXX专业班级:机自XXXX指导教师:XXXX职称:XXX起止日期:2013.4.3~2013.6.18吉林化工学院Jilin Institute of Chemical Technology精选资料摘要螺栓垫片冲压工艺及冲压模具设计,通过对冲压件的分析和有关冲压工艺的资料阅读,大量了解有关模具设计的基本概况,确定合理的冲压工艺方案,设计冲压工序的模具,使用标准的模架,使用UG三维绘图软件绘制模具三维图,对冲压机构进行工艺分析。
明确了设计思路,确定冲压成型工艺过程对各个具体部分进行计算和校核,这样设计出来的结构可确保模具工具运行可靠,保证了其他部件的配合,根据三维图绘制模具的二维图和零件图。
通过止动垫片的设计,巩固和深化了所学知识,并对有关模具设计的国内外发展有了充分的了解。
关键词:冲压工艺;止动垫片;模具设计;冲压模具XXX:M12螺栓垫片冲压工艺及冲压模具设计AbstractThe bolt and gasket stamping die stamping process design,By stamping parts stamping process analysis and information about reading, a lot of information about the basic overview of mold design, stamping process to determine a reasonable solution Stamping die design process, using a standard mold base, the use of three-dimensional graphics software to draw UG mold three-dimensional images of the stamping process analysis institutions Clear design ideas, stamping process to determine the specific part of each calculation and verification This structure can be designed to ensure reliable operation die tools to ensure the cooperation of other parts, according to three-dimensional two-dimensional graph drawing dies and parts diagram Through the stop gasket design, consolidate and deepen the knowledge, and domestic and international developments related to mold design has been well understood.Keywords: stamping process; stop pads; mold design; stamping dieII精选资料摘要 (I)Abstract (II)第一章绪论 (1)1.1 课题来源及研究意义 (1)1.2 螺栓止退垫片工作原理与设计要求 (3)1.3 模具行业的发展现状及市场前景 (3)1.4 冲压工艺介绍 (4)1.5 冲压工艺的种类 (5)1.6 冲压行业阻力和障碍与突破 (5)第二章止退垫片冲模总体方案的确定 (9)2.1 设计题目及主要参数 (9)2.1.1 设计题目 (9)2.1.2 止退垫片主要参数 (9)2.2 冲压工艺与模具设计 (10)2.2.1 冲压件工艺分析 (10)2.2.2 工艺方案及模具结构类型 (10)2.3 排版设计 (11)2.3.1 步距 (11)2.3.2 条料宽度 (11)2.3.3 确定条料的宽度 (12)2.3.4 材料的经济利用 (13)2.4 冲压力和压力中心计算 (14)2.4.1 冲压力的计算 (14)XXX:M12螺栓垫片冲压工艺及冲压模具设计2.4.2工作零件刃口尺寸计算 (17)2.4.3 工作零件结构尺寸 (19)2.4.4 其他模具零件结构尺寸 (20)2.4.5 冲床选用 (21)第三章模具制造 (22)3.1 主要模具零件加工工艺过程 (22)3.1.1 落料凹模加工工艺过程 (22)3.1.2 冲孔凸模加工工艺过程 (23)3.1.3 凸凹模加工工工艺过程 (23)3.1.4 凸模固定板加工工艺 (24)3.1.5 缺料板加工工艺过程 (24)3.1.6 上垫板加工工艺过程 (25)3.1.7 空心垫板加工工艺过程 (26)3.1.8 上模座加工工艺过程 (26)3.1.9 下模座加工工艺过程 (27)3.1.10 推件块加工工艺过程 (27)结束语 (29)参考文献 (30)致谢 (31)IV精选资料第一章绪论1.1 课题来源及研究意义本设计说明书是止退垫片冲模设计的基本要求、主要内容及相关的技术资料而编写的。
- 1、下载文档前请自行甄别文档内容的完整性,平台不提供额外的编辑、内容补充、找答案等附加服务。
- 2、"仅部分预览"的文档,不可在线预览部分如存在完整性等问题,可反馈申请退款(可完整预览的文档不适用该条件!)。
- 3、如文档侵犯您的权益,请联系客服反馈,我们会尽快为您处理(人工客服工作时间:9:00-18:30)。
孔距尺寸: Ld =L±=18±0.125×2×0.09 = (18±0.023)mm 落料:
DA Dmax x0
A
0
0.025 0.025 (36 0.5 0.62)0 mm 35.690 mm
0 DT D A Z min t (35.69 0.04 ) 0 mm 35 . 65 0.016 0.016 mm
1 e凹 (15 0.5 0.12 ) 0.12 mm 14.94 0.015mm 8
第二章 冲裁工艺与冲裁模设计
落料凸、凹模尺寸 a) 落料凹模尺寸 b) 落料凸模尺寸
二、凸、凹模刃口尺寸的计算方法(续)
1.按凸模与凹模图样分别加工法
(1)落料
DA Dmax x0
A
0 0
DT D A Z min T Dmax x Z min T
(2)冲孔 0 d T d min x T
d A dT Z min 0
e 150 0.12 mm
第二章 冲裁工艺与冲裁模设计
第四节 凸模与凹模刃口尺寸的确定
三、例2(续)
由公差表查得: 尺寸80mm,选x = 0.5;尺寸15 mm,选x = 1;其余尺寸均选 x = 0.75。 落料凹模的基本尺寸计算如下: 第一类尺寸:磨损后增大的尺寸
a凹 (80 0.5 0.42 )
第二章 冲裁工艺与冲裁模设计
第四节 凸模与凹模刃口尺寸的确定
三、例1(续)
故:
0.012 DA 35.690 mm
DT 35.650 0.008 mm
第二章 冲裁工艺与冲裁模设计
第四节 凸模与凹模刃口尺寸的确定
三、例2
如图2.4.3所示的落料件,其中 a 800.42 mm 0 b 400 mm c 35 0.34 0.34 mm
第二章 冲裁工艺与冲裁模设计
第四节 凸模与凹模刃口尺寸的确定
一、凸、凹模刃口尺寸计算原则(续)
计算原则(续): 3.冲裁(设计)间隙一般选用最小合理间隙值(Zmin)。 4.选择模具刃口制造公差时,要考虑工件精度与模具精度的 关系,即要保证工件的精度要求,又要保证有合理的间隙值。
5.工件尺寸公差与冲模刃口尺寸的制造偏差原则上都应按“入 体”原则标注为单向公差。但对于磨损后无变化的尺寸,一般标 注双向偏差。
T A ≤ Z max Z min的条件,并且还可放大基准件的制造公差,
使制造容易。
第二章 冲裁工艺与冲裁模设计
第四节 凸模与凹模刃口尺寸的确定
二、凸、凹模刃口尺寸的计算方法(续)
2.凸模与凹模配作法(续) (1)根据磨损后轮廓变化情况,正确判断出模具刃口尺寸类型: 磨损后变大,变小还是不变。 (2)根据尺寸类型,采用不同计算公式。 磨损后变大的尺寸,采用分开加工时的落料凹模尺寸计算公式。 磨损后变小的尺寸,采用分开加工时的冲孔凸模尺寸计算公式。 磨损后不变的尺寸,采用分开加工时的孔心距尺寸计算公式。 (3)刃口制造偏差可按工件相应部位公差值的1/4来选取。对于 刃口尺寸磨损后无变化的制造偏差值可取工件相应部位公差值的 1/8并冠以(±)。
第二章 冲裁工艺与冲裁模设计
第四节 凸模与凹模刃口尺寸的确定
三、例2(续)
第二类尺寸:磨损后减小的尺寸
0 d凹 (22 0.14 0.75 0.28) 0 mm 22 . 07 1 0.070 mm 0.28
4
第三类尺寸:磨损后基本不变的尺寸 落料凸模的基本尺寸与凹模相同,分别是79.79mm, 39.75mm,34.75mm,22.07mm,14.94mm,不必标注公差,但 要在技术条件中注明:凸模实际刃口尺寸与落料凹模配制,保证 最小双面合理间隙值 Z min 0.10mm 落料凹模、凸模的尺寸如图2.4.4。
1 8
A
d min x Z min 0
A
(3)孔心距
Ld =L±
第二章 冲裁工艺与冲裁模设计
第四节 凸模与凹模刃口尺寸的确定
二、凸、凹模刃口尺寸的计算方法(续)
1.按凸模与凹模图样分别加工法(续)
为了保证可能的初始间隙不超过Zmax,即
T A
+Zmin≤Zmax,选取必须满足以下条件: T A ≤ Z max Z min
360 为IT14级,取x = 0.5; 0.62 mm 设凸、凹模分别按IT6和IT7级加工制造,则
0 0 d d x ( 6 0 . 75 0 . 12 ) 6 . 09 min 0.008 0.008 冲孔: T T 0
d A dT Zmin 0
第二章 冲裁工艺与冲裁模设计
第四节 凸模与凹模刃口尺寸的确定
重要性:
凸模和凹模的刃口尺寸和公差,直接影响冲裁件的尺寸精度。 模具的合理间隙值也靠凸、凹模刃口尺寸及其公差来保证。
一、凸、凹模刃口尺寸计算原则
生产实践发现的规律: 1.冲裁件断面都带有锥度。 光亮带是测量和使用部位,落料件的光亮带处于大端尺寸, 冲孔件的光亮带处于小端尺寸;且落料件的大端(光面)尺寸等 于凹模尺寸,冲孔件的小端(光面)尺寸等于凸模尺寸。
校核:0.016 + 0.025 = 0.04 > 0.02(不能满足间隙公差条件) 因此,只有缩小,提高制造精度,才能保证间隙在合理范围内, 由此可取: T ≤ 0.4Z max Z min =0.4×0.02=0.008mm A ≤ 0.6Z Z =0.6×0.02=0.012mm max min
第二章 冲裁工艺与冲裁模设计
第四节 凸模与凹模刃口尺寸的确定
三、例1
冲制图示零件,材料为Q235钢,料厚 t=0.5mm。计算冲裁凸、凹模刃口尺寸及 公差。 解:由图可知,该零件属于无特殊要求 的一般冲孔、落料。 0.12 2 6 mm mm 外形 360 由落料获得, 0 0.62
1 0.42 4 0
0.105 mm 79 .79 0 mm
0.085 mm 39.750 mm
0.085 mm 34.75 0 mm
b凹 ( 40 0.75 0.34 )
c凹 (35 0.75 0.34 )
1 0.34 4 0
1 0.34 4 0
0
d = 22±0.14mm 板料厚度t=1mm,材料为10号钢。试计算 冲裁件的凸模、凹模刃口尺寸及制造公差。 解:该冲裁件属落料件,选凹模为设计基准件,只需要计算落料 凹模刃口尺寸及制造公差,凸模刃口尺寸由凹模实际尺寸按间隙 要求配作。 由表2.3.3查得: Z 0.10mm, Z 0.14mm min max
第二章 冲裁工艺与冲裁模设计
第四节 凸模与凹模刃口尺寸的确定
二、凸、凹模刃口尺寸的计算方法
加工方法: 1.分开加工
具有互换性、制造周期短,但Zmin不易保证,需提高加工精 度,增加制造难度。
2.配合加工 Zmin易保证,无互换性、制造周期长。
第二章 冲裁工艺与冲裁模设计
第四节 凸模与凹模刃口尺寸的确定
和18±0.09由冲孔同时获得。查表2.3.3得, Z min 0.04mm, Z max 0.06mm,则
Z max Z min (0.06 0.04)mm 0.02mm
第二章 冲裁工艺与冲裁模设计
第四节 凸模与凹模刃口尺寸的确定
三、例1(续)
0.12 mm 由公差表查得: 2 60 为IT12级,取x = 0.75;
A
0.012 0.012 (6.09 0.04)0 mm 6.130 mm
校核: ≤ Z Z T A max min
0.008 + 0.012 ≤ 0.06 - 0.04 0.02 = 0.02(满足间隙公差条件)
第二章 冲裁工艺与冲裁模设计
第四节 凸模与凹模刃口尺寸的确定
凸、凹模的制造公差,可按IT6~IT7级来选取,也可 查表2.4.1选取,但需校核。或取
T ≤ 0.4Z max Z min A ≤ 0.6Z max Z min
第二章 冲裁工艺与冲裁模设计
第四节 凸模与凹模刃口尺寸的确定
二、凸、凹模刃口尺寸的计算方法(续)
2.凸模与凹模配作法 配作法就是先按设计尺寸制出一个基准件(凸模或凹模), 然后根据基准件的实际尺寸再按最小合理间隙配制另一件。 特点: 模具的间隙由配制保证,工艺比较简单,不必校核
2.凸模轮廓越磨越小,凹模轮廓越磨越大,结果使间隙越用越大。
第二章 冲裁工艺与冲裁模设计
第四节 凸模与凹模刃口尺寸的确定
一、凸、凹模刃口尺寸计算原则(续)
计算原则: 1.设计落料模先确定凹模刃口尺寸。以凹模为基准,间隙取 在凸模上,即冲裁间隙通过减小凸模刃口尺寸来取得。 设计冲孔模先确定凸模刃口尺寸。以凸模为基准,间隙取 在凹模上,冲裁间隙通过增大凹模刃口尺寸来取得。 2.根据冲模在使用过程中的磨损规律,设计落料模时,凹模 基本尺寸应取接近或等于工件的最小极限尺寸; 设计冲孔模时,凸模基本尺寸则取接近或等于工件孔的最 大极限尺寸。 模具磨损预留量与工件制造精度有关。