《精益生产方式JIT实务》培训教材
精益生产JIT培训材料课件

交流交际
倾听能力
幽默能力
激励能力
精益生产的前世今生
精益生产的八大理念
卓越班组长的角色认知
班组长的管理原则及要点
素质要求
04
(9) 指导员工的能力:传授必要的知识及方法。(10)培养能力:部下的培养是管理人员的重要任务。(11)控制情绪的能力:当你成为一个管理者的时候,你的情绪已经不单单是自己私人的事情了,会影响到你的下属及其他部门的员工;而你的职务越高,影响力越大。
热爱
走动式管理
教育方法
实干作风
问题意识
精益生产的前世今生
指导员工
培养能力
控制情绪
精益生产的前世今生
精益生产的八大理念
卓越班组长的角色认知
班组长的管理原则及要点
素质要求
04
(12)自我约束的能力:了解自己的长处与短处,在有限的时间内有效地活用,努力增进自己的知识、人格、健康的能力。(13)概念化能力:把握事物的本质,发现问题、了解问题时不可缺少的能力。
自我约束
业务素质
职责方面
改善技术
育人技术
组织领导
精益生产的前世今生
精益生产的八大理念
卓越班组长的角色认知
班组长的管理原则及要点
团队
04
精益生产方式强调生产就如同音乐,有旋律(物流)、有节拍(均衡生产)、还有相互之间的和谐(标准作业),而这些是要靠一支训练有素、协调一致的乐队(团队)来保证的。精益生产方式的“团队”理念主要反映在有利于相助的设备布置形式、设立“接棒区”、“自主研究会”、与协作企业的长期合作关系以及追求全体效率等方面。
确保良品
消除不良
明确目的
各尽其职
精益生产的前世今生
07 精益生产之JIT实务(1)

本講重點工厂中常見的八大浪費什么是JIT生產方式工厂中常見的八大浪費浪費的定義在JIT生產方式中,浪費的含義与社會上通常所說的浪費有所區別。
對于JIT來講,凡是超出增加產品价值所絕對必須的最少量的物料、設備、人力、場地和時間的部分都是浪費。
因此,JIT生產方式所講的浪費不僅僅是指不增加价值的活動,還包括所用資源超過“絕對最少”界限的活動。
各种各樣的浪費現象在很多尚未實行5S活動的企業中普遍存在,如表1-1所示。
為了杜絕工厂中的浪費現象,首先需要發現不合理的地方,然后才是想辦法解決問題,這就需要推行5S、JIT等較為先進的管理方法。
表1-1未實施5S活動的企業中的浪費浪費表現成員儀容不整設備布置不合理設備保養不當物品隨意擺放通道不暢常見的八大浪費危害有損企業形象,影響士气,易生危險,不易識別半成品數目大,增加搬運,無效作業xx故障,增加修理成本,影響品質易混料,尋找費時間,易成呆料作業不暢,xx危險,增加搬運在工厂中最為常見的浪費主要有八大類,分別是﹕不良修理的浪費,過分加工的浪費,動作的浪費,搬運的浪費,庫存的浪費,制造過多?過早的浪費,等待的浪費和管理的浪費。
下面具体分析各類浪費現象。
1.不良、修理的浪費所謂不良、修理的浪費,指的是由于工厂內出現不良品,需要進行處置的時間、人力、物力上的浪費,以及由此造成的相關損失。
這類浪費具体包括﹕材料的損失、不良品變成廢品;設備、人員和工時的損失;額外的修复、鑒別、追加檢查的損失;有時需要降价處理產品,或者由于耽誤出貨而導致工厂信譽的下降。
2.加工的浪費加工的浪費也叫過分加工的浪費,主要包含兩層含義﹕第一是多余的加工和過分精确的加工,例如實際加工精度過高造成資源浪費;第二是需要多余的作業時間和輔助設備,還要增加生產用電、气壓、油等能源的浪費,另外還增加了管理的工時。
作業動作突然停止、作業動作過大、左右手交換、步行過多、轉身的角度太大,移動中變換“狀態”、不明技巧、伸背動作、彎腰動作以及重复動作和不必要的動作等,這些動作的浪費造成了時間和体力上的不必要消耗。
精益生产方式JIT教程
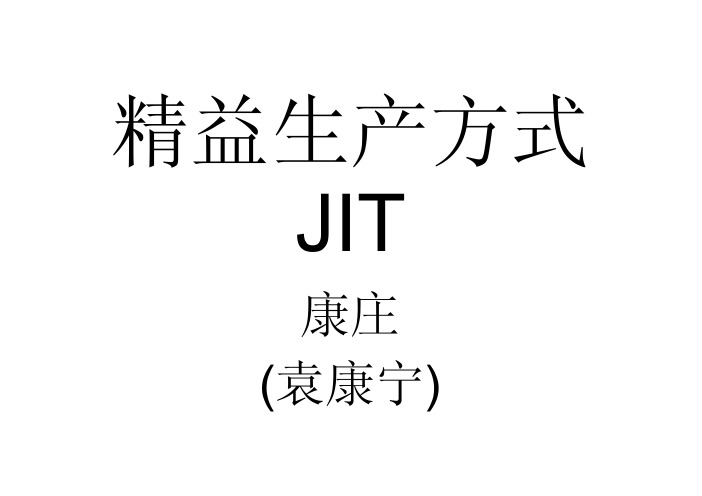
精益生产方式JIT康庄(袁康宁)个人简介•中国咨询培训业联合会•广东省系统工程学会•广东省职业经理人协会•咨询项目总监•高级咨询师一、什么是精益生产?•1.适时:只在需要的时候•2.适量:按需要的量•3.适物:生产所需的产品•其核心有两点:•一、零库存•二、快速应对市场变化手工、批量、精益的比较•19世纪末,开始手工制造汽车(几乎没有相同的两辆车);•一战后,美国福特汽车公司开始大批量生产;•二战后,日本丰田汽车公司以精益生产方式取代大批量生产方式。
精益生产所追求的7个零极限目标•1.零切换•2.零库存•3.零浪费•4.零不良•5.零故障•6.零停滞•7.零灾害1.零切换思考方法与原则•经济批量是否经济•物流方式的JIT•生产计划的标准化•作业管理•标准化作业2.零库存思考方法与原则•库存问题的真正理由•库存与加工批量成正比•适当库存不当•均衡化生产•设备流水化(U形拉)3.零浪费思考方法与原则•不能单纯加强局域生产能力•整体协调•“一个流”将浪费彻底暴露出来•流程线路图4.零不良思考方法与原则•抽检无法杜绝不良•加工批量的大小就是合格与不良批量的大小•零不良才是目标5.零故障思考方法与原则•设备是有生命的东西•为什么会有故障•全面生产维护(TPM)6.零停滞思考方法与原则•同步化•均衡化•Layout流水化•设备小型化、专用化7.零灾害思考方法与原则•安全第一•遵守安全标准•5S安全管理第一步二、什么是浪费?•不增加价值的活动•尽管是增加价值的活动,所用的资源超过了“绝对最少”的界限, 也是浪费。
常见的不良现象或浪费•1.工作人员仪容不整•2.机器设备放置不合理•3.机器设备保养不当•4.原材料、在制品、完成品、待修品、不良品等随意摆放•5.工夹具、量具等杂乱放置•6.通道不明或被占•7.工作场所脏污1.工作人员仪容不整•有损形象,影响塑造良好的工作气氛;•缺乏一致性,不易塑造团队精神;•看起来懒散,影响整体士气;•易生危险;•不易识别管理。
JIT精益生产实务教材

4、标准在制品
为了使生产活动能够重复地持续下去,必须在生产 线内保持有一定的在制品。
有时为了质量检查或下工序加工条件的需要,也必 须设定一定数量的在制品。
如:降温或干燥之后进行下工序加工等。
标准在制品
成品 材料
劳动生产效率=
例
上月:需求 1000台/日 本月:需求 800台/日
工序 10个
工序 10个
人员 10人
人员 8个
问题点:1个工序1个操作者,减员不可能
着眼点:抛弃单一工序操作、定岗定员观念 实行多岗位操作、非定员制观念
7、多工序操作
适合 特点
单工序操作 大批量生产 一人一岗、专业操作 人员作业适应性差 生产及人员难调整 操作者易失去积极性 有时能达到省人化目的
9
8
作业顺序与加工物
7
流同向时:工序间需要1
个在制品。
6 作业顺序与加工物
流逆向时:工序间不需 要在制品。
5、非标准作业处理
标准作业
生产安定化
标准作业
Байду номын сангаас
非标准作业
线上操作者负责 线外“水蜘蛛”负责
对“水蜘蛛”来说 是标准作业
全体标准作业
“水蜘蛛”
将生产岗位的非标准作业内容抽出来,作为 “水蜘蛛”的标准作业内容,以每次供应一套均 衡物料的方式保证生产线的持续作业。
“水蜘蛛”必须动作迅速,头脑清醒灵 活,掌握生产线的瞬间变化并能采取对应措 施。一般有一线骨干或后续一线干部担任。
6、少人化
少人化
用最少的人数、用最低的 成本生产市场需要的产品数量。
JIT培训

JIT培训
TCL移动通讯有限公司
图1-2 降低库存暴露问题
JIT培训
TCL移动通讯有限公司
6.制造过多过早的浪费
• 零件的滥用,资金周转率下降,计划柔软性的阻碍。
• 内容:流程阻碍,不良的发生、库存,半成品的增加,材料、
自我问答:为何要多做?停止机制?换线改善呢?
改善:Full Work System 单品流程 步骤单一化 招牌的彻底实行 单纯化主产
•
TCL移动通讯有限公司 JIT培训
总装部综合组 周睦顺制作
The Creative Life
1
JIT培训
TCL移动通讯有限公司
精益生产之JIT实务
• ——通过本课程,您能学到什么? • 浪费的定义 • 在JIT生产方式中,浪费的含义与社会上通 常所说的浪费有所区别。对于JIT来讲,凡 是超出增加产品价值所绝对必须的最少量 的物料、设备、人力、场地和时间的部分 都是浪费。因此,JIT生产方式所讲的浪费 不仅仅是指不增加价值的活动,还包括所 用资源超过“绝对最少”界限的活动。
JIT培训
TCL移动通讯有限公司
3.动作的浪费
• 内容:两手空闲、单手空闲、作业动作突然停止、作业动作过大、 • 左右手交换、步行过多、转身的角度太大,移动中变换“状态”、 • 不明技巧、伸背动作、弯腰动作以及重复动作和不必要的 • 动作等,这些动作的浪费造成了时间和体力上的不必要消耗。
自我问答:为何要拿放?为何要置换?
JIT培训
TCL移动通讯有限公司
什么是JIT生产方式
• JIT生产方式的基本思想可用现在已经广为 流传的一句话来概括,即“只在需要时, 按需要的量,生产所需的产品”,这也就 是Just In Time一词所要表达的本来含义。 这种生产方式的核心是追求一种零库存、 零浪费、零不良、零故障、零灾害、零停 滞的较为完美的生产系统,并为此开发了 包括看板在内的一系列具体方法,逐渐形 成了一套独具特色的生产经营体系。
精益生产培训教材

3 Shifts TAKT Time CT = C/O Time = DT = Scrap / Rework = # Operators WIP =
# Material Handlers Max Size 2 Shifts 0 Overtime
分析当前状态 设计将来状态
C/O Time = DT = Scrap = WIP =
课程一: 课程一:
精益生产概论
精益生产的发展历史
福特生产系统 •生产线大量生产 •大批量标准化产品 •工人掌握单一技术 丰田生产系统(TPS) 丰田生产系统(TPS) (TPS •JIT生产(按客户需求品种和数量准时生产) •拉动生产 •强调生产数量和库存数量与市场匹配 •按照客户需求定制产品
精益生产的发展历史
消除浪费的四步骤
第一步: 第一步: 了解什么是浪费 了解什么是浪费
第二步: 第二步: 识别工序中哪里存在浪费 识别工序中哪里存在浪费
第四步: 第四步: 实施持续改进措施 实施持续改进措施, 持续改进措施, 重复实施上述步骤
第三步: 第三步: 使用合适的工具来消除 使用合适的工具来消除 已识别的特定浪费
精益生产既是一种以最大限度地减少企业生产所占用的资 源和降低企业管理和运营成本为主要目标的生产方式,同 源和降低企业管理和运营成本为主要目标的生产方式, 时它又是一种理念,一种文化。实施精益生产就是决心追 时它又是一种理念,一种文化。 求完美的历程,也是追求卓越的过程。 求完美的历程,也是追求卓越的过程。
1985年美国麻省理工学院组织了世界上14个国家的专家、 学者,花费了5年时间,耗资500万美元,对日本等国汽车 工业的生产管理方式进行调查研究后总结出来的生产方式, 在日本称为丰田生产方式。
JIT精益生产实务(外企内部培训教材)

等待浪费
搬运浪费
7 不良浪费
大 工
厂
动作浪费
常浪
费 见
加工浪费
的
库存浪费
地下工厂
企业每生产一件产品就在制 造一份浪费。伴随企业运营中各 业务环节不被觉察或不被重视的 浪费,日本企业管理界将之形象 地比喻为“地下工厂〞。
制造过多〔过早〕浪费
Just-In-Tim12e
你知道发现下面的都是那些浪费吗?
单能工
1人同工程多机台操作
传统的合理化方向
Just-In-Tim37e
生产线采用传统的机能别的水平式布置,使得作业员在同一个时间点及同一工作站, 只能操作一种机能别的机器。这种作业人员称为单能工,而传统合理化的方向为了减 少人力需求,往往会以提升设备的自动化或其速度,以达成目标,使一个人能操作更 多相同机器设备,此称为多机台操作。
例如:在制品过多,占用生产空间,产生不必要的储存、保管工作,隐藏了 许多无法预见的问题。同时,生产的优先顺序受到破坏。交期早的产品,仍 在线上等等到满足大批量才要生产;交期晚的订单产品,恰巧碰到该设备在 生产同一类别的产品,而先进行生产了,使得交期早的产品被延误。
Just-In-Tim24e
假效率 真效率
能力 提升
【效率建立在有效需求的根底上】 能力提升是效率提升的根底。但有时能力提 升会造成效率提升的假象。 管理者的责任就是在能力提升的根底上,将 假效率转化成真效率。 所以,“省人化〞是效率的关键。
省人化的两种形式: ☆ 正式工 + 季节工 / 临时工〔变动用工〕 ☆ 固定人员 + 公用人员〔弹性作业人员〕
JIT精益生产实务培训教材 〔1〕JIT根底知识
◆何谓精益生产方式?JIT是什么?
精益生产之JIT实务培训讲义

精益生产之JIT实务培训讲义【课程目录】第一讲推行JIT的必要性1.厂里最罕见的八大糜费2. JIT简介第二讲新经理上任秘籍1.进式控制系统与拉动式控制系统2.JIT消费方案第三讲优秀部门经理角色认知1.看板的机能和运用规那么2.看板的种类3.看板组织消费进程第四讲如何与下属正确相处1.〝一个流〞消费概述2.〝一个流〞消费的八大要素3. 延长作业切换时间第五讲如何率领部属(上)1. 实施柔性化消费所采取的措施2. 弹性的作业人数第六讲如何率领部属〔中〕1. 停止消费平衡化的缘由2. 消费平衡化的益处3. 消费平衡化在企业里的运用第七讲如何率领部属(下)1. 准时制推销的目的2. 准时制推销的特点3.供应商的选择与评鉴第八讲权利与威信1. 传统质量管理与JIT的质量管理2. JIT消费的要求3. 关于设备的保养第九讲如何做优秀的教练1. 适宜推行JIT消费方式的国际企业2. 推行JIT消费方式的要点第十讲抵触处置1. 嘉陵股份JIT消费方式2. 东莞某外资企业推行JIT案例广东某涂料企业JIT不完全推行案例【内容摘要】第1讲推行JIT的必要性【本讲重点】工厂中罕见的八大糜费什么是JIT消费方式工厂中罕见的八大糜费糜费的定义在JIT消费方式中,糜费的含义与社会上通常所说的糜费有所区别。
关于JIT来讲,凡是超出添加产品价值所相对必需的最大批的物料、设备、人力、场地和时间的局部都是糜费。
因此,JIT消费方式所讲的糜费不只仅是指不添加价值的活动,还包括所用资源超越〝相对最少〞界限的活动。
各种各样的糜费现象在很多尚未实行5S活动的企业中普遍存在,如表1-1所示。
为了根绝工厂中的糜费现象,首先需求发现不合理的中央,然后才是想方法处置效果,这就需求推行5S、JIT等较为先进的管理方法。
表1-1设备保养不当易生缺点,添加修缮本钱,影响质量物品随意摆放易混料,寻觅费时间,易成呆料通道不畅作业不畅,易生风险,添加搬运罕见的八大糜费在工厂中最为罕见的糜费主要有八大类,区分是:不良、修缮的糜费,过火加工的糜费,举措的糜费,搬运的糜费,库存的糜费,制造过多?过早的糜费,等候的糜费和管理的糜费。
- 1、下载文档前请自行甄别文档内容的完整性,平台不提供额外的编辑、内容补充、找答案等附加服务。
- 2、"仅部分预览"的文档,不可在线预览部分如存在完整性等问题,可反馈申请退款(可完整预览的文档不适用该条件!)。
- 3、如文档侵犯您的权益,请联系客服反馈,我们会尽快为您处理(人工客服工作时间:9:00-18:30)。
防止品质变异的关键要素: 1、稳定的人员 2、良好的教育训练 3、建立标准化 4、消除环境乱象 5、准确运用统计品管 6、稳定的 供应商 7、完善的机器保养制度
客户感受到的不良
管理的不良
制造过程的不良
客户满意度
交期 销售部门
消 不良 费 者 感性 不良
制造工厂 制程不良
供应商
成品
其 他
人 力
它是一个很好的标准化工具,但不是标准书 目的是短时间提升作业人员的技能
所用地方:
1、工作当中、改善当中或者知识的部分的关键点 2、以前经常发现问题的点 3、改善的重点
动作标准化:动作经济原则的应用示例
第一条原则:双手的动作应同时而对称 。
用一只手:插完30只销子需30S 用双手:插完30只销子只需23S,节约时间29%
作业简单
多能工 培养要点
适当指导 标准作业
整体推广 制定计划
安定二 设备的安定
1 设备的有效运转率管理 可动率设备可以有效运转
(有效产出)的时间 可动率越高越好,理想为100%
运转率(利用率)设备必要的有
效运转(有效产出)时间
2 设备综合效率
作业时间 计划歇停、 管理损失 设备的6大损失
(1)故障 (2)准备、调整 (3)空转、间歇 (4)速度低 (5)工序不良 (6)启动利用率
适用
特点 优点
柔性生产
前后各工序紧密相连 搬运距离短,在制品数量低,生产 周期短,生产空间小,单向“流”
三 流线化生产的八个条件
相关性 (1)单件流动 (2)按工艺流程布置 (3)生产速度同步化 (4)多工序操作 (5)员工多能化 (6)走动作业 (7)设备小型化 (8)生产线U形化 设备 设备 设备
第七条原则:尽量解除手的工作,而以夹具或足踏工具代替
第八条原则:可能时应将两种或两种以上工具合并为一。
第九条原则:手指分别工作时,各指负荷应按其本能予以分配。手柄 的设计应尽可能与手接触面大;机器上的杠杆、手轮的位置应尽 可能使工作者少变动其姿势。
手指 能力顺序 食指 1 右手 中指 无名指 2 4 小指 6 食指 3 左手 中指 无名指 5 7 小指 8
现场改善的三化原则 ⑴ 专业化 ⑵简单化 (3)标准化
特点: 1、代表最好、最容易、最安全的工作; 2、提供一个保存技巧和专业技术的最佳方法; 3、提供了一个衡量绩效的方法; 4、提供维护和改善的基础; 5、作为目标及训练的目的; 6、建立核查或论断的基础。
1、现场改善的安全、品质、效率
2、现场改善的三“公”一“客观” 3、“下一流程”就是顾客
2、浪费的认识
利润在哪里------省则赚的思想
利润主义
售价主义
成本主义
价格 = 成本 + 利润
利润= 价格 - 成本
成本=价格-利润
创造价值和消除浪费
工人作业的实际内容:
1、有附加价值的作业 2、无附加价值的作业 3、浪费
常见现场的三大浪费:
1、库存时间上的浪费 2、搬运空间上的浪费 3、检查上的浪费
技法篇
实践篇
自主实践活动
1、改善的认识
改善的影响 改 善 的 误 区 改 善 的 承 诺
!
现场IE改善
方法研究、作业测定
现场IE改善
工业工程是对人员、物料、机器设备、信息、空间等所 组成的集成系统进行设计、改善和实施的学科。 ——美国工业工程师学会(1955年)
改善是提高效率,降低成本,提升品质, 最终减少企业的浪费和消除浪费,优化整个生产系统的
第十条原则:工具及物料应尽可能事前定位。
2 少人化
用最少的人数、用最低的成本生产市场 需要的产品数量。 对客户消耗效率的认识
单工序操作 大批量生产 一人一岗、专业操作 人员作业适应性差 生产及人员难调整 操作者易失去积极性 有时能达到省人化目的 多工序操作 多品种小批量生产 一人多岗、多技能操作 人员作业适应性强 生产及人员容易调整 能发挥团队效应 能达到少人化目的
配置 作业人员
决定设备 人员数量 单件流动
设定 产距时间 维持管理
样 板 线 制 作
水平推广
迈向 流线化
六 一笔画的工厂布置
一笔画
从提高整体效率的目的出发, 将前后关联的生产线集中布置。
1 由水平布置改为垂直布置 A A A A A A A A A A
B
C C
B
C
B
C
B
C
B
C
B
C
B
C
2 采用U字型生产线
作 业
作 业 作 业 作 业
人 员
四 生产线U形化
Input
1 2 3
空手浪费
Output
4
2 1
3 2 4 1
3
4 5 6
Input
Output
Input
Output
五 、 流 线 化 生 产 的 建 立
全员意识 改革 成立示范 改善小组
12步迈向流线化
选定示范 生产线 现状 调查分析
布置细流 生产线
“体”——即表示体验、实践的意思,精益生产的实践是成功 的关键;仅知道了前面两个而不实践,就落入了“知而不行” 的空谈,惟有知道之后立即加以行动,才能做到“知行合一” 。
内容提要
精益生产概述 意识篇
改善的认识 浪费的认识 效率的认识 库存的认识 第一招——流线化生产 第二招——安定化生产 第三招——平稳化生产 第四招——自动化生产 第五招——超市化生产(JIT)
3 多技能员工
多 工 序 操 作
适合 特点
如何实现多工序操作
1、U型布局 3、专用小型设备 5、走动作业
2、消除离岛式布局 4、设备离人化 6、多能工培养
多能工实施要点
工序操作简单易掌握, 包括更换和调整。 重点培养作业顺序和 内容,一看就明白的作业 标准书。 一人具备多个岗位的 操作技能。 培养多能工意识,举 办竞赛、表扬先进。 多能工技能统计,多 能工培养计划。
设计质量与成本之关系图
售价
金 额
c b
利润
a
成本
水可 准达 到 之 技 术
天下没有白吃的午餐 最小的投资获得最大的报酬
制造质量与成本之关系图
成 本 不 良 損 失
c1
總 費 用
c
c2
管 制 費 用
a+b=c
b
品質均勻度
a
制造质量的好坏直接影响成本
总质量成本曲线划分区域图
管制重心 是维持此一最佳点
负荷时间 运转时间
纯运转时间 价值运 转时间
停止损失
性能损失
不良损失
设备综合效率的计算
精益生产对设备效率评估是以稼动率方式评估,
时间稼动率=(负荷时间-停机时间-保养时间)/负荷时间(目标为95%) (负荷时间=出勤时间-计划停机时间<早会/培训/停电、水/计划> 性能稼动率=(实际总产量x理论C/T)/稼动时间(目标为98%) 总良率=投入数量-不良数量/投入数量(目标为99%) (不良=设备启动后首件不良+制程不良+返工后剩余的)
开发的河流
二.流线化生产与批量生产的差别
1 水平布置与垂直布置
冲压区
包装区
水 平 布 置
攻丝
装配
攻丝区
装配区
冲压
包装
垂 直 布 置
2水平布置与垂直布置比较
项目 方式 水平布置 相同功能设备集中摆放 项目 方式 垂直布置 根据产品类别按照加工顺序排列
适用
特点 缺点
大批量生产
集中生产、集中搬运、 在制品搬运浪费大,等待时间长, 生产周期长,空间占用大,造成“乱 流”
成品 14 13 12
11 10 9 8 7
材料
1
3 2
4
5
6
3 将长屋型 改为 大通铺式
大 通 铺 式 布 置
一 笔 画 布 置
4 整体上呈 一笔画布置
案例讲解
富士康双面作生产线
第二招式——安定化生产
人员安定化管理
设备安定化管理 安定化 生产
品质安定化管理
物量安定化管理 管理安定化管理
安定一 人员的安定
第二条原则:人体的动作应以尽量应用最低级而能得到满意结果为妥。
人 体 动 作 等 级
级别 1 2 3 4 5
运动枢纽 指节 手腕 肘 肩 身体
人体运动部位 手指 手指及手腕 手指、手腕及小臂 手指、手腕、小臂及大臂 手指、手腕、小臂、大臂及肩
第三条原则:尽可能利用物体的动能,曲线运动,弹道式运动
上下型挥动:最佳效果的效率为9.4%。动能未得到利用,为肌肉所制止。
总品质成本曲线
改良计划区域 失敗成本>70% 预防及鉴定成本 <30% 寻求突破之计划 继续进行改良。
1 标准作业与非标准作业
为了将作业人员、机器设备及物流过程作最适当的组合,以有效的 达成生产目标而设立的标准化文件
标准作业
非标准作业
线上操作者负责 线外“水蜘蛛”负责
对“水蜘蛛”来说 是标准作业
生产安定化
全体标准作业
通过标准化获得稳定发展
作业方法
作业指导书
⑴ 确认
⑵清晰明了
(3)异常管理
One Point Lesson
精益生产方式JIT实务
——探讨降成本增效益的新生产技术
主讲:陈鹏
精益生产的称呼
课程概述
本课程的具体内容:心、技、体
“心”——即表示思想观念的改变,精益的思想与传统的生产 观念有很大的不同,必须先从思想意识改革入手; “技”——即表示技法的意思,精益生产的技法包括五个招式 , 精益的实现必须从第一招式演练到第五招式,才能实现目标 ;