第二章 液态金属加工
金属材料成型基础之金属液态成型

(2) 凝固收缩 从凝固开始到凝固终止温度间的收缩。 T液 — T固
(3) 固态收缩 从凝固终止温度到室温间的收缩。 T固 — T室
体收缩率:
体收缩率是铸件产生缩 孔或缩松的根本原因。
线收缩率:
线收缩率是铸件产生应 力、变形、裂纹的根本
原因。
书山有路勤为径, 学海无涯苦作舟
书山有路勤为径, 学海无涯苦作舟
7.0
白口铸铁: P+Fe3C+Le
(wC+wSi)%
麻口铸铁: P+Fe3C+G+Le 灰口铸铁:
珠光体灰口铸铁: P+G片
6.0
白 5.0 口
铸 4.0 铁
10 20
珠光体+铁素体灰口铸铁: P+F+G片 铁素体灰口铸铁: F+G片
灰口铸铁
30 40 50 60 70
3.麻口铸铁: 组织中既存在石墨、又有莱氏体,是白口和灰 口之间的过渡组织,因断口处有黑白相间的麻 点,故而得名。
书山有路勤为径, 学海无涯苦作舟
根据铸铁中石墨形态的不同,灰口铸铁又可分为:
1.普通灰口铸铁 : 简称灰口铸铁,其石墨呈片状。如图a所示 2.可锻铸铁: 其石墨呈团絮状。。如图b所示。 3.球墨铸铁: 其石墨呈球状。如图c所示。
2.缩孔与缩松
液态合金在冷凝过程中, 若其液态收缩和凝固收缩所缩减的容积 得不到补充, 则在铸件最后凝固的部位形成一些孔洞 。大而集中的 称为缩孔, 细小而分散的称为缩松。
1)缩孔和缩松的形成
书山有路勤为径, 学海无涯苦作舟
2)缩孔和缩松的防止
防止缩孔和缩松常用的工艺措施就是控制铸件的凝固 次序, 使铸件实现“顺序凝固”。
材料加工工艺习题【考研】【复习】

《材料加工工艺》考研习题第一章绪论第二章液态金属成形1.金属及合金的结晶包括哪两个基本过程?什么是均质形核和非均质形核?在实际铸造生产中铸造合金结晶的形核是以哪种形核为主,为什么?2.什么是液态金属的充型性能,它与哪些因素有关?铸造合金流动性的好与差对铸件质量有何影响?影响铸造合金流动性的主要因素有哪些?生产中如何采取措施提高铸造合金的流动性?3.铸造合金由液态冷却到室温时要经过哪三个收缩阶段?收缩对铸件质量有什么影响?其收缩大小与哪些因素有关?4.缩孔、缩松是铸件中的常见缺陷之一,哪些因素影响其形成?生产中如何采取措施进行防止?5.什么是铸造应力?铸造应力大小对铸件质量有什么影响?热应力是如何形成的?哪些因素影响其大小?生产中常采取哪些措施来防止和减小应力对铸件的危害?6.铸造合金中的气体主要来源于哪些方面?又以哪些形式存在于铸造合金中?对铸件质量有什么影响?7.铸造合金中的夹杂物是如何分类的?对铸件质有什么影响?如何防止和减小其对铸件的危害?8.湿型粘土砂的主要成分是什么?它有哪些优缺点?适合生产哪些铸件?9.湿型粘土砂的造型方法有哪些?试比较应用震击、压实、射压、高压、气冲和静压等各种造型方法的紧实的砂型紧实度分布(沿砂箱高度方向)。
为什么需要用高密度湿粘土砂型生产铸件?10.树脂自硬砂、水玻璃砂与粘土砂比较有哪些优点?各适用于哪些铸件的生产?11.砂芯的作用是什么?经常使用哪些粘结剂来制芯?常用的制芯工艺有哪些?12.砂型和砂芯涂料的作用是什么?其主要组成有哪些?13.什么是顺序凝固原则?什么是同时凝固原则?各需采用什么措施来实现?上述两种凝固原则各适用于哪些场合?14.铸件的壁厚为什么不能太薄,也不能太厚,而且应尽可能厚薄均匀?为什么要规定铸件的最小壁厚?不同铸造合金要求一样吗?为什么?。
15.为便于生产和保证铸件质量,通常对铸件结构有哪些要求?16.何谓铸件的浇注位置?它是否指铸件上的内绕道位置?铸件的浇注位置对铸件的质量有什么影响?应按何原则来选择?17.试述分型面与分模面的概念?分模造型时,其分型面是否就是其分模面?从保证质量与简化操作两方面考虑,确定分型面的主要原则有哪些?18.试确定图2-116所示铸件的浇注位置及分型面。
参考答案(第2章)

9 × 0.0049
= 9.3 × 10−3 m ⋅ s −1
3、 1、 根据均质形核的公式,得到:
r* =
2σ SLTm 2σ SLTm 2σ SLTmVm 2σ T V × N = = = SL m Fe * A * * Δ H ΔH v ΔT ΔH m × Δ T m × ΔT * ΔH m × ΔT Vm
= 1μ m 的液泡,需要的附加压力为
2σ 2 × 860 × 10−3 p= = = 1.72MPa r 10−6
对于半径 r
= 0.1μ m 的液泡,需要的附加压力为
2σ 2 × 860 × 10−3 p= = = 17.2MPa r 10−7
2、 根据 Stokes 公式,得到:
2r 2 (γ l − γ MnO ) 2r 2 ( ρl − ρ MnO ) g v= = 9η 9η = 2 × ( 0.1 × 10−3 ) × (7500 − 5400) × 9.8
其中 ΔH m 是摩尔原子的结晶潜热,Tm 是凝固点温度, R 是普适气体常数,η 是表面 配位数,ν 是晶体内部配位数,对于不同类型的晶体以及表面的晶面取向不同, 最大为 0.5。 当 α 1). Al
η ν
不同,
≤ 2 ,得到粗糙界面,当 α > 2 ,得到光滑界面。
Al 是 fcc 结构,
η Tm = 933K , ΔH b = 290.93 × 103 J/mol , = 0.5 , 从气态凝结时, ν
2
3
ρ MnO = 5400kg / m3 。若 MnO 为球形,半径为 0.1mm ,求它在钢液中的上浮速度?
3、 金属元素 Fe 的结晶潜热 ΔH m = 15.17 kJ / mol ,熔点 Tm = 1811K ,固/液界面张力
材料加工原理第2章-液态金属

属界面上,向熔池金属内部扩散。
36
二、液态合金的表面张力
(一)表面张力的实质及影响表面张力的因素
(二)表面张力在材料成形生产技术中的意义
37
(一)表面张力的实质及影响表面张力的因素
表面:液体或固体同空气或真空接触的面
表面现象? 露珠
产生原因?
表面张力:液体表面内产生的平行于
表面切线方向且各向大小均等的张力。
4
二、 液体的表观特征
具有流动性 (液体最显著的性质);
可完全占据容器的空间并取得容器内腔的形状 (类似于气
体,不同于固体);
不能够象固体那样承受剪切应力,表明液体的原子或分子 之间的结合力没有固体中强 (类似于气体,不同于固体);
具有自由表面 (类似于固体,不同于气体);
液体可压缩性很低 (类似于固体,不同于气体)。
10-13秒)
U —— 为无外力作用时原子之间的结合能 粘度η随原子间结合能U按指数关系增加,这可 粘度随原子间距δ增大而降低(成反比)。实
26
合金组元(或微量元素)对合金液粘度的影响:
M-H(Moelwyn-Hughes)模型:
H ( X 11 X 22 )1 2 RT
外力的作用,液体密度对流动的影响可以忽略(当采用了运动学粘度 系数ν之后,ν金和ν水两者近于一致。例如铸件浇注系统的设计计算时, 完全可以按水力学原理来考虑) 。
动力学粘度η—— 在外力作用非常小的情况下适用,如夹杂的上浮
过程和凝固过程中的补缩等均与动力粘度系数η有关。
29
流态对流动阻力的影响:
27
化学成分对粘度的影响
液态金属加工中的界面反应与润湿行为

液态金属加工是一种广泛应用于各种工业领域的工艺,其中包括金属铸造、模具制造和微电子制造等。
在这个过程中,液态金属与其接触的表面之间的相互作用,包括界面反应和润湿行为,是影响加工质量的关键因素。
首先,让我们来理解一下液态金属的特性。
液态金属是一种具有高流动性和扩散性的物质,其反应性取决于其成分和环境条件。
当液态金属与表面接触时,可能会发生一系列的化学和物理反应,这些反应可能会影响金属的特性,如硬度、强度和耐腐蚀性。
润湿行为是液态金属与表面相互作用的结果。
如果液态金属能够均匀地铺展在表面上,我们称之为完全润湿。
然而,如果液态金属无法均匀地铺展,而是形成小滴或气泡,我们称之为不完全润湿。
润湿行为取决于液体的表面张力、接触角以及表面的性质。
在液态金属加工中,界面反应和润湿行为的影响是双向的。
一方面,它们影响加工的质量和效率。
如果润湿行为不佳,液态金属可能无法均匀地覆盖表面,导致模具或铸造模型的不均匀,进而影响产品质量。
另一方面,界面反应可能会改变液态金属的特性,如硬度、强度和耐腐蚀性,这可能会影响产品的使用寿命。
为了优化液态金属加工过程中的界面反应和润湿行为,我们可以采取一些措施。
首先,选择合适的表面材料可以降低界面反应的可能性。
其次,可以通过改变液态金属的成分或环境条件来调整其润湿行为。
最后,对加工过程中的参数进行实时监测和调整,以确保最佳的加工效果。
总的来说,液态金属加工中的界面反应和润湿行为是影响加工质量的关键因素。
通过了解这些相互作用,我们可以优化加工过程,提高产品质量,同时降低生产成本。
未来,随着科学技术的进步,我们有望开发出更先进的液态金属加工技术,以满足更高层次的生产需求。
材料成形工艺第二章 液态金属成形过程及控制

第二章 液态金属成形过程及控制
第一节 第二节 第三节 第四节 第五节
液态金属充型过程的水力学特性及流动情况 浇注系统的设计 液态金属凝固收缩过程的工艺分析 冒口设计 冷铁设计
第一节 液态金属充型过程的水力学特性及流动情况
一、液态金属充型流动过程的水力学特性 二、液态金属在浇注系统中的流动情况 三、金属熔体过滤器及浇注系统
1.液态金属在浇口杯中的流动情况
图2-3 浇口杯内液面深度和浇注高度的影响 a)合理 b)、c)不合理
1.液态金属在浇口杯中的流动情况
为了减轻和消除水平旋涡,对于重要的中、大型铸件,常用 带浇口塞的浇口杯。先用浇口塞堵住浇口杯的流出口,然后进 行浇注,当浇口杯被充填到一定高度且熔渣已浮起时,再拔起 浇口塞,使合金液开始流入直浇道。浇口塞可用耐火材料或铸 铁材料制成,其结构应能保证拔起浇口塞时不产生涡流。有时 也用一金属薄片盖住浇口杯的流出口,当浇口杯被充填到一定 的高度时,金属薄片受热熔化,浇口杯的流出口就被打开,如 图2-4所示。
1.液态金属在浇口杯中的流动在浇口杯中的流动情况
浇口杯内出现水平旋涡会带入熔渣和气体,因而应注意防 止。当金属液从各个方向流入直浇道时,各向流量不均衡,某 一流股的流向偏离直浇道中心,就会形成水平涡流。根据水力 学原理,水平涡流越靠近中心部位压力越低,液面越低,这样 浮在液面上的熔渣会沿着弯曲的液面,一边旋转,一边和空气 一同进入直浇道,就有可能形成氧化夹渣等铸造缺陷。
1.液态金属在浇口杯中的流动情况
图2-4 有拔塞、浮塞或铁隔片的浇口杯 a)拔塞式 b)浮塞式 c)铁隔片式
2.液态金属在直浇道中的流动情况
图2-5 砂型中合金液流的充满条件 a)合金液流内任一截面上各点的压力p b)合金液流内任一截面上各点的压力p
金属加工工艺学 第二篇 金属液态成型-铸造

缩松特征:分散性,为细小缩孔,位于铸件壁的轴线区域。
比较缩孔和缩松的特征
缩孔:集中性,位于上部,呈倒锥形,内表面粗糙。
缩松:分散性,位于铸件壁的轴线区域。为细小缩孔,
Ⅱ 缩孔和缩松减小铸件有效承载面积,降低力学性能, 缩松导致铸件渗漏。
Ⅲ 缩孔与缩松的防止
•
可以说,三星堆的发现,是真正颠复性的,它迫使我们不得不重
新认识中国的社会发展史、冶金史、畜牧农耕史、艺术史、文化史、
军事史和宗教史。许多约定俗成的观念都必须改变。比如:中国的青
铜时代,过去一向是从商朝算起,也就是3000多年。河南安阳出土
的中国最重的青铜器--司母戊铜方鼎是最典型的代表,然而"三星堆"
裂纹的产生与预防
裂纹的产生:内应力超过金属的抗拉强度。 分为热裂和冷裂 热裂——高温下形成的,在铸件凝固后接近于固相线
冷裂——较低温下形成, 铸件形状复杂,易形成冷裂
热
冷
裂
裂
• 热裂的形状特征:裂纹短,缝隙宽,形状曲折,缝内呈 氧化色。
• 防止措施:①提高铸型和型芯的退让性,减少机械应 力;
• ②浇冒口的设计要合理;③铸钢件和铸铁件应严格控制 硫的含量;④选择凝固温度小,热裂倾向小的合金。
铸造结构阻碍得到消除(落砂), 机械应力随即消失。
+++ +++
热应力——由于铸件壁厚不均匀,冷速不一, 致使同时期内线收缩不一致而相互牵制所引起。
+- +
- +-
热应力分布规律:厚部(缓冷)——拉应力 薄部(先冷)——压应力
两杆的固态冷却曲线图
《材料加工》原理部分习题
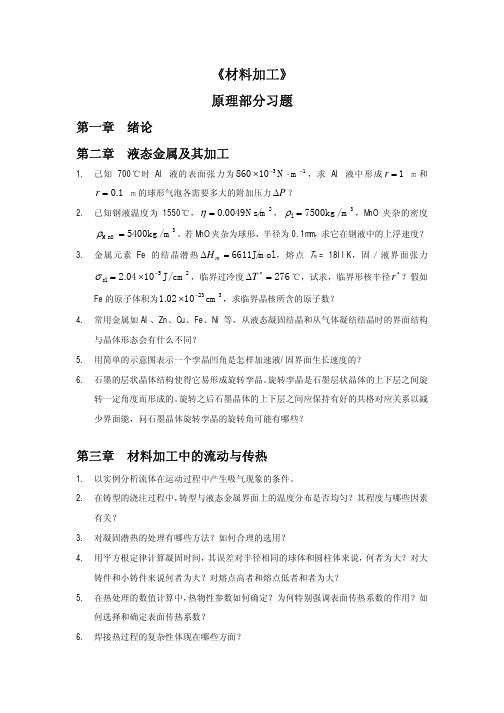
《材料加工》原理部分习题第一章 绪论第二章 液态金属及其加工1. 己知 700℃时Al 液的表面张力为13m N 10860−−⋅×,求 Al 液中形成μm 1=r 和μm 1.0=r 的球形气泡各需要多大的附加压力P ∆?2. 已知钢液温度为1550℃,2Ns/m 0049.0=η,3l m /7500kg =ρ,MnO 夹杂的密度3MnO m /5400kg =ρ。
若MnO 夹杂为球形,半径为0.1mm ,求它在钢液中的上浮速度?3. 金属元素Fe 的结晶潜热J/mol 6611=∆m H ,熔点T m = 18llK ,固/液界面张力25sl cm /J 1004.2−×=σ,临界过冷度276=∆∗T ℃,试求,临界形核半径∗r ?假如Fe 的原子体积为323cm 1002.1−×,求临界晶核所含的原子数?4. 常用金属如Al 、Zn 、Cu 、Fe 、Ni 等,从液态凝固结晶和从气体凝结结晶时的界面结构与晶体形态会有什么不同?5. 用简单的示意图表示一个孪晶凹角是怎样加速液/固界面生长速度的?6. 石墨的层状晶体结构使得它易形成旋转孪晶。
旋转孪晶是石墨层状晶体的上下层之间旋转一定角度而形成的。
旋转之后石墨晶体的上下层之间应保持有好的共格对应关系以减少界面能,问石墨晶体旋转孪晶的旋转角可能有哪些?第三章 材料加工中的流动与传热1. 以实例分析流体在运动过程中产生吸气现象的条件。
2. 在铸型的浇注过程中,铸型与液态金属界面上的温度分布是否均匀?其程度与哪些因素有关?3. 对凝固潜热的处理有哪些方法?如何合理的选用?4. 用平方根定律计算凝固时间,其误差对半径相同的球体和圆柱体来说,何者为大?对大铸件和小铸件来说何者为大?对熔点高者和熔点低者和者为大?5. 在热处理的数值计算中,热物性参数如何确定?为何特别强调表面传热系数的作用?如何选择和确定表面传热系数?6. 焊接热过程的复杂性体现在哪些方面?7. 焊接热源有哪几种模型?焊接传热的模型有哪几种?8. 热源的有效功率4200W q =,焊速s /1cm .0=υ,在厚大件上进行表面堆焊,试求准稳态时A 点(x =-2.0cm ,y =0.5cm ,z =0.3cm )的温度。
- 1、下载文档前请自行甄别文档内容的完整性,平台不提供额外的编辑、内容补充、找答案等附加服务。
- 2、"仅部分预览"的文档,不可在线预览部分如存在完整性等问题,可反馈申请退款(可完整预览的文档不适用该条件!)。
- 3、如文档侵犯您的权益,请联系客服反馈,我们会尽快为您处理(人工客服工作时间:9:00-18:30)。
之差,即Tm-Tn。
62
金属的凝固过程------ 形核,长大
t1 形核
t2 形核并 长大,有新 的晶核形成
t3 长大形 成晶粒
t4 液体消 失,结晶结 束
63
结晶驱动力
△GV= △HV-T △SV≈ △HVT △HV /Tm= △HV (Tm-T)/Tm
2016/11/19
64
2016/11/19
表面相 Ns NL
U
N *:形成大于临界半径的晶核的数目,取决于△G*均; 而 △G*均取决于 能量起伏; f0 :原子由液相到固相的净迁移率,取决于△GA(属扩散激活能U) ;
2016/11/19
71
2016/11/19
f0
Ns
Ns
形核率:
U
U
U
U
2016/11/19
形核率随过冷度增大而增大,超过极大值后,形核率又随过冷 度进一步增大而减小。
G
均
2 16 3Tm 3( Lm T ) 2
G 非 / G
均
2 3 cos cos3 ( ) 4
82
2016/11/19
83
2016/11/19
84
2016/11/19
85
2016/11/19
86
2016/11/9
87
88
2016/11/19
68
【补充】
液态金属凝固,外层原子比内部原子所受束缚少些,因此具有较高 的能量,故将之归为另一相—表面相(两条虚线中间者)。而内部原子 基本为固态晶体排列。表面相由于能量高因而成为凝固的阻力,故尽量 薄一些,以降低表面能。
表面相
r太小,则比表面积很大,表面能(结晶阻力)很大,占优势,故不能长大;只有 r>r*,体相较大,比表面能有所下降,此时才能继续长大。
8
固态晶格原子排列
液态原子排列
2016/11/19
11
2016/11/19
12
17
1200℃时液态金属原子的状态
1500℃时液态金属原子的状态
19
2 液体状态方程
再
再
2.1.3 液态金属的性质
2016/11/19
27
1
2016/11/19
28
F(x)
y
v(y)
57
4
2016/11/19
58
2016/11/19
59
2.2.1 液态金属结晶热力学条件
2016/11/19
60
结晶过程的分析方法 ------热分析
61
金属熔液凝固时的过冷现象 过冷:金属的实际开始凝固温度Tn总是低于理论凝固
温度Tm的现象.
过冷度( Δ T):理论凝固温度与实际开始凝固温度
171
2016/11/19
体相原子 配位数为 υ
因此、总配位数为( η x+A),即可理解为被( ηx +A),跟原子束缚着,因此 表层内每个原子结合能为: H 0 (x A)
当表层铺满时,x=1,此时结合能为:
H0
( A)
2016/11/19
145
S NK x ln x (1 x) ln(1 x)
2016/11/19
160
2016/11/19
161
2016/11/19
162
2016/11/19
163
2016/11/19
164
2016/11/19
165
2016/11/19
166
2016/11/19
167
2016/11/19
168
2016/11/19
169
2016/11/19
假如晶核形状是截自半径为r的圆球的球冠,截面半径为R, 晶核形成时体系总的自由能变化为:
V S
V:晶核体积 ΔGV:单位体积的固液两相自由能之差 ΔGS:晶核形成时体系增加的表面能
77
总界面能变化
增加了晶核与基底的面积:Ans=πR2,因而多出了二者之间的界面能: σnsAns。 增加了晶核与液体的面积:AnL,因而多出了二者之间的界面能:σnLAnL。
x S
2016/11/19
2016/11/19
30
1
1
0
e U / KT
2016/11/19
39
2016/11/19
40
2016/11/19
41
2016/11/19
42
液体粘度的测量
2016/11/19
45
2016/11/19
46
2
2016/11/19
47
89
形核率影响因素:
2016/11/19
90
2016/11/19
91
2016/11/19
92
as
ac
2016/11/19
94
2016/11/19
95
2016/11/19
96
2016/11/19
97
多种衬底共存:
2016/11/19
98
1 ½ 0
00
90 0
1800
θ
在同一过冷度下,具有不同形核能力的物质,θ也不同, θ越小形核能力越强 。 形核能力不强的衬底,由于θ较大,使得f(θ)较大,则可能形核率低,当冷度变大 使ΔW均变小,可以弥补f(θ)的变大,可以形核。
74
金属材料形核率与温度的关系如图所示。形核率 突然增大的温度称为有效形核温度,此时对应的 过冷变称临界过冷度约等于0.2Tm。
75
2.2.3 非均匀形核及其形核率
在液体中,各处形核的概率不同,在杂质处优先形核。
2016/11/19
76
晶核优先依附在现成固体表面上形成。
非均匀形核的临界晶核尺寸及形核功:
减少了基底与液体的面积:Ans=πR2,因而减少了二者之间的界面能 :σLSALS=σLSAns。 因而总界面能变化: G表面 Ans ns Anl nl Asl sl
2016/11/19
由几何学知道:
截圆面积:
Ans R2 (r 2 r 2 cos2 ) r 2 sin 2
2016/11/19
1
主要内容:
2016/11/19
2
2016/11/19
3
2.1.1 液态金属的形成
1 熔化
实践证明,金属熔化从晶界开始。金属吸收的热量,使原子振动频率加大 ,能量升高,从规则的原子排列变为紊乱的非晶状态。该过程中吸收的热量 除了增加了系统的内能外,还使体积膨胀做功。
4
2016/11/19
2016/11/19
146
2016/11/19
147
2016/11/19
148
2016/11/19
149
2016/11/19
150
2016/11/19
151
光滑界面生长形态
2016/11/19
156
2016/11/19
157
2016/11/19
158
2016/11/19
159
f l
f l
f f
f ( N / m) 表面张力系数: l
它们为什么不能沉下去?
2016/11/19
51
2016/11/19
52
2016/11/19
53
2016/11/19
54
补充 :弯曲液面的附加压力的产生
Q点
2016/11/19
2016/11/19
56
3
2016/11/19
2016/11/19
123
由于固、液相均存在温度梯度,因此液相深处的热量传入向界面,到达界面后,又 从界面传到固相中去。当凝固平衡时,传入界面的热量等于传出界面的热量。 液相温 度分布
熔化温度
固相温 度分布
界面产生突 起后的液、 固温度分布
当界面出现小突起时,液相温度曲线斜率变大,这样传出的热量增加;与此同时, 固相温度曲线斜率变小,传出的热量减少,这样界面处就有多余的热量,这些多 余的热量又把小突起熔化。
5
2 液态金属特点
2016/11/19
2016/11/19
2.1.2 液态金属的X射线分析
X射线或中子线分析研究液态金属的原子排列。研究表明: 液态金属中原子的排列在几个原子的间距范围内,与固态的排 列方式基本一致,但由于原子间距的增大和空穴的增多,原子 的配位数略有变化,热运动增强。
2016/11/19
79
体积自由能变化
G体 GVV球冠
V球冠
2016/11/19
3 2 3 cos cos r 3 ( ) 4
总自由能的变化
G总 G体 G面
G总 G体 G面
将前面的结果代入整理:
G总
3 4 2 3 cos cos (- r 3 GV 4r 2 nL) ( ) 3 4
65
2.2.2 均匀形核及其形核率
均匀形核是指在液体每处形核的概率都是一样的。
d ( G ) 4r 2 GV 8r 0 dr
r* 2 GV
GV
Lm T Tm
2 Tm r* Lm T
2016/11/19
66
临界晶核半径随过冷度增大而减小。
球冠面积:
Anl R2 r 2 (2 cos cos3 )
总表面自由能:
G面 Ans ns Anl nl Asl sl G面 Ans ( ns sl ) Anl nl