《金属工艺基础》课件—11机械加工工艺规程
金属工艺学教学课件PPT培训金属材料基础

1.1.1 金属材料的力学性能
弹性 E=/
Elastic Modulus,
σ.Σ.sigma ε.Ε.epsilon
固溶体 化合物 机械混合物
铁碳合金状态图
状态图的分析 钢在结晶过程中的组织转变
学习“铁碳合金”的思路:
➢ 铁为什么加碳?
➢ 铁是什么样?
➢ 铁和碳在一起有什么形式?
➢ 铁加多少碳会怎么样?(不同 的碳含量在合金中会体现成什 么形式?不同温度又会如何?)
1.2.1纯铁的晶体结构及转变
金属在固态下一般都是晶体; 晶体—原子在空间呈规律性排列:
10
1.1.1 金属材料力学性能—硬度
硬度:材料表面抵抗局部变形,特别是塑性变形、压痕、划痕的能力 硬度直接影响材料的耐磨性,所以刀具、量具、模具等要求高硬度。 硬度过高则切削困难,所以一般都是“先加工,后热处理提高最终硬度”工艺。
HB 2P(kgf)
D(D- D2 - d2 )
传统的布氏硬度计: 淬火钢球压头、HBS、450HBS以下材料; 新型布氏硬度计: 硬质合金球压头、HBW、650HBW
1.2.1 纯铁结晶——若干概念
晶粒:
每个晶核长成的晶体称为晶粒; 晶粒的外形是不规则的,晶粒的内部原子排列的位向也各不相同; 晶粒之间的接触面叫晶界(薄弱环节)。
金属晶粒的粗细对金属力学性能影响很大:
一般说,同一成分的金属晶粒越细,其强度越高,硬度也越高, 塑性韧性也越好。 晶核越多,晶粒越细。
细化铸态金属晶粒的主要途径:
金属工艺学--机械制造基础

金属工艺学–机械制造基础1. 简介金属工艺学是研究金属材料的加工和成形过程的学科,是机械制造的基础。
机械制造是以金属工艺学为基础,通过金属的加工和成形,将原材料加工成所需的形状和尺寸的零件或产品。
本文将介绍金属工艺学在机械制造中的基础知识和常用工艺。
2. 金属材料的分类金属材料是机械制造中常用的材料之一,根据其组成和结构的不同,可以将金属材料分为以下几类:•铸铁:主要由铁、碳和硅组成,具有良好的铸造性和机械性能。
•钢:主要由铁和碳组成,含有较低的碳含量,具有良好的强度和韧性。
•不锈钢:在钢中添加铬和其他合金元素,提高抗腐蚀性能。
•铝合金:主要由铝和其他合金元素组成,具有低密度和良好的强度。
不同的金属材料适用于不同的机械制造需求,选择适合的材料对产品的质量和性能至关重要。
3. 金属加工工艺金属加工工艺是指通过各种方法和工艺将金属材料加工成所需形状和尺寸的过程。
在机械制造中常用的金属加工工艺包括:3.1 切削加工切削加工是通过在工件上施加相对运动的切削刃,从工件上削除材料来达到所需形状和尺寸的加工方法。
常用的切削加工工艺包括:•铣削:使用铣刀在工件上进行旋转切削,常用于平面、曲面和沟槽的加工。
•钻削:使用钻头在工件上进行切削,常用于孔的加工。
•镗削:使用镗刀在工件上进行切削,常用于加工内孔和外圆。
3.2 成形加工成形加工是通过对金属材料进行变形和塑性加工来达到所需形状和尺寸的加工方法。
常用的成形加工工艺包括:•锻造:将金属材料置于锻压机上,通过施加压力使其发生塑性变形,常用于制造零件和工件。
•压铸:将熔融的金属注入到铸型中,通过压力使其充满整个型腔,并冷却固化,常用于大批量、复杂形状的零件制造。
•深冲:将金属材料放置在冲压机上,通过冲击或压力的作用使其在模具中发生塑性变形,常用于制造薄壁零件。
3.3 焊接加工焊接加工是通过将两个或多个金属材料熔化或塑性加工后,使其连接在一起的加工方法。
常用的焊接加工工艺有:•电弧焊:通过产生电弧在金属接头上加热,使其达到熔化状态,然后冷却固化。
金属工艺学课件(PPT 49页)

(2) 非金属夹杂物
作业:
一、问答题
1、可采用哪些措施提高合金的流 动性?
2、缩孔和缩松是怎样形成的?可 采用什么措施防止?
3、什么是顺序凝固原则和同时凝 固原则?
9、静夜四无邻,荒居旧业贫。。21.3.321.3.3Wednesday, March 03, 2021
10、雨中黄叶树,灯下白头人。。11:40:0211:40:0211:403/3/2021 11:40:02 AM
铸造性能:Foundry Technological Properties
是表示合金铸造成形获得优质铸件的能力, 是一个极其重要的工艺性能。通常用流 动性和收缩性等来衡量。
1. 合金的充型能力
mold filling capacity
⑴ 充型能力的概念(流动性)
液态合金充满型腔,形成轮廓清晰、 形状正确的优质铸件的能力。
1杆:拉应力 Tensile Stress
2杆:压应力: Compression Stress
⑵ 机械应力 Contraction Stress :铸 件冷到弹性状态后,由于受到铸型、 型芯和浇冒口等的 阻碍而产生的应 力为机械应力。
机械应力为 拉应力,如 图:
Tensile Stress
⑶ 减小和消除铸造应力的方法
通过两个途径发生作用:
影响金属与铸型之间的热交换条件, 改变金属液的流动时间;
影响金属液在铸型中的水动力学条 件,改变金属液的流动速度。
2. 合金的收缩性
The Contraction of Alloys
⑴ 收缩的概念: 合金从液态冷却到常温的
过程中,尺寸和体积缩小的现象称为收 缩。
The Conception of the Contraction
金属工艺学课件(PPT 45页)

金属工艺发展历史
春秋时期 战国时期
铁器开始使用 出现炼钢技术
金属工艺发展历史
铸造技术
中国古代三大铸造技术 泥范(砂型)铸造 铁范(金属型)铸造 失蜡铸造
商周(3000年前) 发明失蜡铸造技术 战国中期 出现金属型铸造 隋唐以后 掌握大型铸件生产技术
金属工艺发展历史
铸造技术实例1
河南安阳武官村出土, 体积庞大,重875kg, 花纹精细,造型精美。
•
每天都是美好的一天,新的一天开启 。20.12.820.12.810:5410:54:0010:54:00Dec- 20
•
人生不是自发的自我发展,而是一长 串机缘 。事件 和决定 ,这些 机缘、 事件和 决定在 它们实 现的当 时是取 决于我 们的意 志的。2020年12月8日 星期二 10时54分0秒 Tuesday, December 08, 2020
•
做专业的企业,做专业的事情,让自 己专业 起来。2020年12月上 午10时54分20.12.810:54December 8, 2020
•
时间是人类发展的空间。2020年12月8日星期 二10时 54分0秒10:54:008 December 2020
•
科学,你是国力的灵魂;同时又是社 会发展 的标志 。上午10时54分0秒上 午10时 54分10:54:0020.12.8
锻造技术和焊接技术
锻造技术和焊接技术在中国有着攸久的历史 3000年前,商朝就用锻造技术制作兵刃 战国时期,扩大到日常用品 战国时期,应用了钎焊技术
金属工艺发展历史
锻造技术和焊接技术
秦皇陵中铜车马上的金银饰件用无机粘接挤固 定
金属工艺发展历史
世界上金属加工工艺最早专著-《天工开物》
《金属工艺学》课件
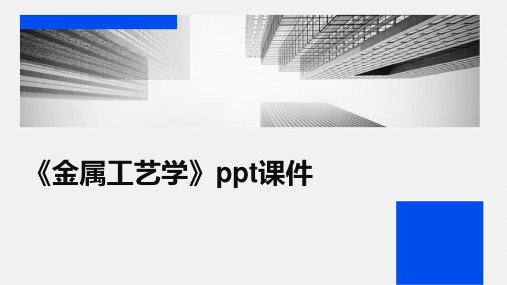
金属工艺学可以根据加工对象和应用 领域分为多种分支,如铸造、锻造、 焊接、切削加工、热处理等。
金属工艺学的应用领域
机械制造业
航空航天业
金属工艺学在机械制造业中应用广泛,涉 及各种零件的加工、装配和维修。
航空航天器制造需要高精度和高性能的金 属材料和加工技术,金属工艺学在航空航 天业中发挥着重要作用。
汽车制造业
电子工业
汽车制造业需要大量金属材料和加工技术 ,包括车身、底盘、发动机等部件的制造 和装配。
电子工业中,金属材料广泛应用于电路板 、连接器、散热器等部件的制造。
金属工艺学的历史与发展
01
古代金属工艺
早在公元前,人类就开始使用金属材料,如青铜、铁等,用于制造工具
、武器和饰品。
02
工业革命时期的金属工艺
退火与正火工艺
退火工艺
退火是一种将金属加热到适当温度,保温一段时间,然后缓慢冷却至室温的热 处理工艺。其主要目的是消除金属内部的应力,提高其塑性和韧性,以便于进 一步加工。
正火工艺
正火是将金属加热到适当温度,保持一定时间后,在静止空气中冷却的热处理 工艺。其主要目的是细化金属的晶粒,提高其机械性能,如强度和韧性。
。
焊接缺陷及防止
03
焊接过程中可能出现气孔、夹渣、裂纹等缺陷,需采取相应措
施进行防止。
金属的切削加工工艺
切削加工原理
通过刀具对金属工件进行切削,以去除多余的金属材料,实现工 件形状和尺寸的加工。
切削加工方法分类
根据切削加工的特点和应用,可分为车削、铣削、钻削、磨削等 。
切削加工技术要求
切削加工过程中需要考虑刀具材料、切削液、切削参数等因素, 以确保加工质量和效率。
机械加工工艺规程培训课件ppt4)

案例三:复杂模具的加工工艺规程
在加工过程中,采用高精度数控机床 和高品质刀具,确保模具的制造精度 和表面质量。
对加工完成的模具进行检测与检验, 确保满足设计要求和装配精度,并进 行必要的试模和修正。
控制切削参数,减少切削振动和热量 产生,防止模具出现热变形和裂纹。
应用自动化生产线和机器人技术, 实现多道工序的连续加工,提高整 体加工效率。
降低生产成本的方法
优化材料利用
合理选择材料、优化下料方案、 减少材料浪费等,降低原材料成
本。
提高设备利用率
合理安排生产计划,提高设备利 用率,降低设备闲置成本。
降低能耗
采用节能技术和设备,优化工艺 参数,降低加工过程中的能源消
织等,以确保达到要求。
注意事项
在光整加工阶段应注意避免过 光整或损伤工件表面。
04
机械加工工艺规程优化与 改进提ຫໍສະໝຸດ 加工效率的方法优化工艺流程
通过减少不必要的工序、合并工 序、调整工序顺序等手段,缩短
加工周期,提高生产效率。
选用高效设备
采用高精度、高刚度、高稳定性的 加工设备,提高单机加工效率。
引入自动化技术
在粗加工阶段应注意保护机床 精度,避免因切削力过大导致
工件变形或机床损坏。
半精加工阶段
半精加工阶段
在粗加工后进行,主要目的是进一步 去除余量,为精加工做准备。
余量去除与形状修正
通过半精加工进一步修正工件形状, 去除大部分余量,为后续精加工提供 基础。
精度控制
在半精加工阶段应控制工件的尺寸精 度、形状精度和表面粗糙度,以满足 精加工要求。
金属加工工艺培训课件(PPT-69页)

三、淬火
❖ 把工件加热到一定温度(临界温度以上), 经过一定时间保温后,在水、油或盐水中急 速冷却的操作过程叫淬火。
❖ 按加热程度不同分为: ❖ 整体淬火和表面淬火。
❖一般分为自由锻和模锻。 ❖常用于生产大型材、开坯等。
一、自由锻
利用冲击力或压力使金属在上下两个 抵铁之间产生变形,从而得到所需形状 及尺寸的锻件。分手工锻造、机械锻造 两种。 工具简单,通用性强,应用广泛。
二、模锻
❖ 按设备不同分为: ❖ 锤上模端、胎膜锻、 压力机上模锻 ❖ 锤上模锻设备有: ❖ 蒸汽空气锤、五砧座锤、高速锤
激光焊接法
某些物质原子中的粒子受光或电刺激, 使
低能级的原子变成高能级原子,辐射出相位 、
频率、方向完全相同的光,具有颜色单纯、
特点: (1)焊接速度快,加工时间短暂 (2)准确性高,被焊金属无需包埋固定,无变
形 (3)不受电磁于扰,可直接在大气中进行焊接
, 操作方便 (4)热影响区小,激光焊接加热区域小、热量
冲孔:利用特殊工具在金属片上冲剪出一定 造型的工艺,大,小批量生产都可以适用。
冲切:与冲孔工艺基本类似,不同之处在于 前者利用冲下部分,而后者利用冲切之后金属 片剩余部分。
切屑成型:当对金属进行切割的时候有切 屑生产的切割方式统称为切屑成型,包括铣 磨,钻孔,车床加工以及磨,锯等工艺。
无切屑成型:利用现有的金属条或者金属 片等进行造型。没有切屑产生。这类工艺包 括化学加工,腐蚀,放电加工,喷砂加工, 激光切割,喷水切割以及热切割等。
优点: 成本低,可用价廉易得的 CO2代替焊剂,焊接成本仅是埋弧 自动焊和手弧焊的40%左右。生产 效率高、操作性好、质量较好。
缺点: CO2的氧化作用使溶滴飞溅 较为严重,因此焊缝成型不够光滑 ,另外焊接烟雾较大,弧光强烈, 如果控制或操作不当,容易产生气
机械加工工艺规程培训课件ppt4

在使用切削液时,应注意安全操作,避免对人体和环境造成危害。同时,还应注意切削液 的储存和运输,避免阳光直射和高温环境,以免影响其使用效果。
夹具设计基础知识
05
与应用实例
夹具类型及特点
通用夹具
适应性强,可用于多种工件的装夹, 如三爪卡盘、四爪卡盘、平口钳等。
专用夹具
为某种特定工件或某道工序专门设计 的夹具,具有结构紧凑、操作方便、 定位精度高等特点。
事故应急处理措施和救援预案
事故应急处理措施
针对可能发生的事故,制定相应的应急处理措施,如立即停机、切断电源、疏散人员等,以减轻事故造成的损失 。
救援预案
建立完善的救援预案,包括救援组织、通讯联络、现场处置、医疗救护等方面的内容,确保在事故发生时能够迅 速有效地进行救援。
THANKS.
焊接设备
用于金属材料的连接,包 括电弧焊、气体保护焊等 ,具有灵活性和高效性。
工艺装备选择依据
加工精度要求
根据加工件的精度要求选 择相应的工艺装备,如高 精度磨具、夹具等。
生产批量大小
根据生产批量的大小选择 适合的工艺装备,如大量 生产可采用自动化生产线 。
加工材料性质
根据加工材料的性质选择 适合的切削工具、夹具和 测量工具等。
磨床夹具
如电磁吸盘、砂轮修整器等,用于装夹工件 进目与方法
外观检测
通过目视、触摸等方式检查产品表面质 量,如颜色、光泽、划痕、气泡等。
力学性能检测
对产品进行拉伸、压缩、弯曲等力学 试验,以检验其强度、硬度、韧性等
性能指标。
尺寸检测
使用卡尺、千分尺等量具测量产品的 尺寸精度,包括长度、宽度、高度、 直径等。
性和加工成本。
- 1、下载文档前请自行甄别文档内容的完整性,平台不提供额外的编辑、内容补充、找答案等附加服务。
- 2、"仅部分预览"的文档,不可在线预览部分如存在完整性等问题,可反馈申请退款(可完整预览的文档不适用该条件!)。
- 3、如文档侵犯您的权益,请联系客服反馈,我们会尽快为您处理(人工客服工作时间:9:00-18:30)。
11.1 概述
1、生产过程和工艺规程
1)机械的生产过程
➢ 指产品由原材料或半成品到成品之间的各个有关劳动过程 的总和。
➢ 其生产过程包括:原材料的运输、保存和准备;毛坯的制 造;毛坯经过机械加工、热处理而成为零件;零件装配成 机械;机械的质量检查及运行试验;机械的油漆和包装。
➢ 划线找正法。该方法是在机床上用划针按钳工在毛坯或 半成品中所划的线找正工件,使工件获得正确的位置。 其特点与直接找正法相似,多用于生产批量小、毛坯精 度较低以及大型零件等不便使用夹具的粗加工中。
➢ 夹具定位。这种方法是用夹具上的定位元件使工件获得 正确位置。其优点是定位迅速方便,定位精度较高,但 增加了设计和制造夹具的费用。故它广泛用于大批大量 生产。
铸造毛坯; ➢ 而尺寸较小时则可考虑熔模铸造件、压力铸造件等。
3)既应根据现有生产、技术条件考虑毛坯生产的可能性, 也应积极创造条件生产出需要的毛坯。 4)根据零件的年生产纲领考虑毛坯生产方法的经济性。一 般情况下生产纲领愈大,毛坯制造方法应愈先进、生产率愈 高、质量愈好。
Ø 选择定位基准
1)定位原则
◆分析产品零件图及有关装配图 了解零件在机械力的作用。在此基础上,进一步审查图纸的完
整性和正确性;检查零件材料的选择是否合理;分析零件的技术 要求及其作用,并从中找出主要的、工艺上难以达到的、对制订 工艺方案起决定性作用的技术要求。从而掌握制定工艺规程时应 解决的主要问题。
◆分析零件的结构工艺性。
零件的结构工艺性是影响零件在加工过程中能否高效低耗地被加 工出来的一项基本特性。对结构工艺性不好的零件,必要时应提出修 改意见。
➢ 走刀——被加工的某一表面,由于余量较大或其它原因,
在切削用量不变的条件下,用同一把刀具对它进行多次加工, 每加工一次,称一次走刀。
2、生产纲领和生产类型
根据国家计划(或市场需求)和本企业生产能力确定的产品年 产量称为年生产纲领。产品中某零件的生产纲领除计划规定的 数以外,还应包括一定的备品率和平均废品率。
2)机械加工工艺过程
➢ 在机械的生产过程中,直接改变原材料(或毛坯)的形状尺 寸和性能,使之变成所需零件的过程称为零件的机械加工 工艺过程,它是机械加工车间生产过程的主要部分。
3)工序
➢ 工序是指一个(或一组)工人在一台设备(或一个工作地点) 上对一个(或同时几个相同的)工件进行加工所连续完成的 那一部分工艺过程。它是确定生产计划的依据。
2)基准及其选择
➢ 定义:工件上用来确定其他点、线、面的位置的那些点、 线、面,一般用中心线、对称线或平面作为基准。
➢ 分类:按照作用的不同,常把基准分为设计基准和工艺基 准两类。
① 设计基准:设计图样上所用的基准。 ② 工艺基准:零件在加工工艺过程中所用的基准。
基准
用于确定零件 上其它点、线、 面位置所依据 的那些点、线 、面。
➢ 毛坯的选择
1)毛坯的材质必须满足零件的使用要求。 ➢ 如特别重要又要求力学性能比较高的零件,应选用具有
合理分布的纤维状组织的锻件毛坯; ➢ 形状比较复杂、承受中等应力载荷的零件应选用铸铁件
毛坯。实际上,某些零件的材料选定以后,毛坯的种类 也随之而定。
2)零件的形状、尺寸应适合所选择的毛坯生产方法。 ➢ 如对形状复杂、尺寸较大的箱体类零件应考虑选用砂型
2、制订工艺规程的原则
保证质量、提高效率、降低成本
3、制订工艺规程内容和步骤
① 零件的工艺分析; ② 确定毛坯; ③ 选择定位基准; ④ 拟定工艺路线; ⑤ 确定各工序所采用的设备; ⑥ 确定各工序所需的工艺装备; ⑦ 确定加工余量; ⑧ 确定切削用量和工时定额; ⑨ 填写工艺文件
➢ 零件的工艺分析
设计图样上所采 用的基准就是设 计基准。
在加工时用于工件
定位的基准,称为
定位基准。
设计基准 工艺基准
定位基准 测量基准
1、粗基准 2、精基准 3、辅助基准 4、主要基准 5、附加基准
加工、测量、 装配过程中使 用的基准。
装配基准件 时采用的基准
在装配时用来确定零
用任x何, y一, z个, x物, 体y, 在z 空表间示直角坐标系中都有 6 个自由度——
要确定其空间位置,就需要限制其 6 个自由度
工件在机床上定位大体有如下三种方式:
➢ 直接找正法。该方法是用百分表、划针或目测在机床上 直接找正工件,以确定工件在机床上的正确位置。其特 点是找正很费时,要求工人技术水平较高,故多用于单 件小批生产及修配。
➢工步——在被加工的表面、切削用量(指切削速度和进给量)、 切削刀具均保持不变的情况下所完成的那部分工序,称工步。
➢ 安装——工件在加工前,在机床或夹具中相对刀具应有一
个正确的位置并给予固定,这个过程称为装夹,一次装夹所完 成的那部分加工过程称为安装。安装是工序的一部分。
★ 在同一工序中,安装次数应尽量少,既可以提高生产效率, 又可以减少由于多次安装带来的加工误差。
N = Q n(1+α% +β% )
式中 Q ——产品年产量(件/年); n ——每台产品中该零件数量(件/台); α ——备品率; β ——废品率。
11.2 机械加工工艺规程的制订
1、定义 从现有生产条件出发,确定出最恰当的工艺过程,并将其
各项内容以文字、图纸、表格等形式固定下来,所形成的工艺 文件。
在工序图上使用的基准。
件或部件在产品中相 对位置所采用的基准
定位基准
1、粗基准 未经机械加工的定位基准。(毛面)
2、精基准 经过机械加工的定位基准。(已加工面) 3、附加基准 因工艺需要而专门设计的定位基准。
如轴类顶尖孔
➢精基准的选择原则
① “基准重合”原则。 应尽量选择主要加工表面的设计基准作为精基准。这样可以避免 因基准不重合而引起的定位误差。 ② “基准统一”原则。 应选择多个表面加工时都能使用的定位基面作为精基准。这样便 于保证各加工表面间的相互位置精度,避免基准变换所产生的误 差,并简化夹具的设计和制造。 ③ “互为基准”原则。 当两个表面相互位置精度要求高,并且它们自身的尺寸与形状精 度都要求很高时,可以采取两者互为基准的原则,反复多次进行 精加工。