中频表面淬火工艺技术报告
高频感应加热表面淬火实验报告
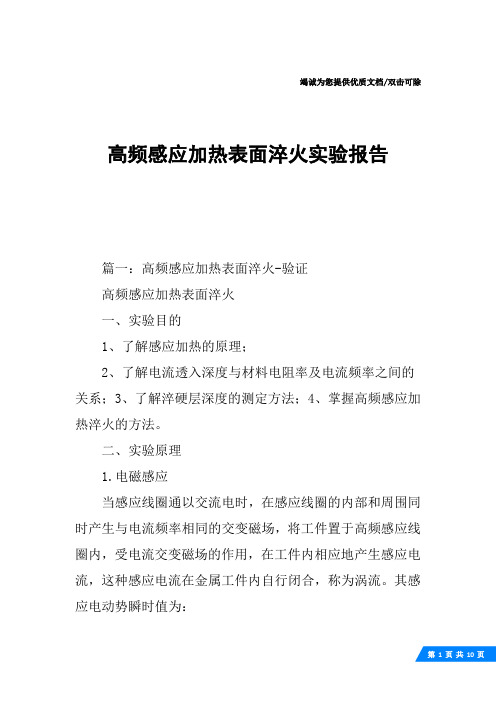
竭诚为您提供优质文档/双击可除高频感应加热表面淬火实验报告篇一:高频感应加热表面淬火-验证高频感应加热表面淬火一、实验目的1、了解感应加热的原理;2、了解电流透入深度与材料电阻率及电流频率之间的关系;3、了解淬硬层深度的测定方法;4、掌握高频感应加热淬火的方法。
二、实验原理1.电磁感应当感应线圈通以交流电时,在感应线圈的内部和周围同时产生与电流频率相同的交变磁场,将工件置于高频感应线圈内,受电流交变磁场的作用,在工件内相应地产生感应电流,这种感应电流在金属工件内自行闭合,称为涡流。
其感应电动势瞬时值为:d?e??Kd?式中,K-比例系数;ф-工件上感应电流回路包围面积上的总磁通;dф/dτ-磁通量变化率;负号表示感应电动势方向与磁通量变化率方向相反。
工件中感应出来的涡流方向,在每一瞬时和感应线圈中的电流方向相反。
涡流强度If取决于感应电动势(e)及工件涡流回路的电抗(Z),而电抗Z由电阻R和感抗(xL)组成,则涡流强度:eeIf??Z2R2?xL2.表面效应涡流强度If随高频电磁场强度由工件表面向内层逐渐减小而相应减小的规律称为表面效应或集肤效应。
离表面x 处的涡流强度:x?Ix?I0?e式中,I0-表面最大的涡流强度;x-到工件表面的距离;Δ-与工件材料物理性质有关的系数。
所以,当x=0时,Ix=I0当x>0时,Ix<I01?0.368(:高频感应加热表面淬火实验报告)I0e工程规定,当涡流强度从表面向内层降低到表面最大涡流强度的36.8%(即1I0?)时,由该处到表面的距离Δ称为电流透入深度。
e 在感应加热实践中,钢中电流透入深度的计算常常使用下列简化公式:20在20℃时:?20?(mm)f500在800℃时:?20?(mm)f?当x=Δ时,Ix?I0?式中,f-感应线圈交流电频率。
3.淬硬层深度工件经感应加热淬火后的金相组织与加热温度沿截面分布有关,一般可分为淬硬层、过渡层及心部组织三部分。
大齿圈中频表面淬火热处理工艺探讨

收稿日期:2008-12-29作者简介:李 圣(1980-),男,河南洛阳人,助理工程师,从事热处理工艺研究和科研开发工作。
大齿圈中频表面淬火热处理工艺探讨李 圣,酒艳平(中信重工机械股份有限公司,河南洛阳 471039)摘 要:主要阐述大直径、大重量的齿圈的轮齿进行中频沿齿槽表面淬火的热处理工艺研究,中频沿齿槽表面淬火后的变形问题和机械校正工艺,以提高该齿圈轮齿的弯曲和接触疲劳强度和整套产品的制造质量。
关键词:大齿圈;中频沿齿槽连续表面淬火;变形;校正中图分类号:TG 61 文献标识码:B 文章编号:1005-2798(2009)03-0050-04如图1所示,直径将近7000mm 且结构复杂的半齿圈,总重量高达10,t 给中频沿齿槽淬火及其解决淬火后的变形问题都带来了很大的难度。
以前中信重工机械股份有限公司制造的都是软齿面或中硬齿面的这种类型的齿圈,疲劳强度相对较低,为了提高整套产品的质量和使用寿命,在总结国内外半齿圈铸件制造的先进经验和本公司以前成功地对直径是3m 焊接齿轮的中频沿齿槽连续表面淬火经验的基础上,提出对大尺寸大重量齿圈采取中频沿齿槽连续表面淬火的热处理攻关试验,来提高齿圈上轮齿的弯曲疲劳强度和接触疲劳强度、提高耐磨性和具有一定的冲击韧性等综合机械性能。
为此中信重工机械股份有限公司研制了适合该齿圈齿形结构的感应器,成功地完成了这类齿圈中频沿齿槽连续表面淬火的工艺研究。
图1 直径7000mm 的齿圈示意1 直径是7000mm 大齿圈制造的技术要求该大齿圈为传动零件,其结构形式如图1所示。
1.1 齿轮的参数和尺寸齿圈的材料为ZG42C r M o ;齿数为216齿;法面模数m n 为32mm;法面压力角A n 为20b ;齿高系数h a /h f 为1/1.4;齿宽b 为486mm ;法面固定弦齿厚s cn 为38.62mm;重量为19628kg 。
1.2 齿圈的技术要求1) 表面淬火前预处理为正火处理,硬度应为H B210~250;机械性能指标分别是强度极限R b \690MPa 、屈服极限R s \490MPa 、延伸率D 5\11%、断面收缩率W \25%、冲击韧性值A k \30J ;轮齿感应淬火,硬度为HRC50~55;有效硬化层深度\3~5mm 。
齿圈的中频淬火技术
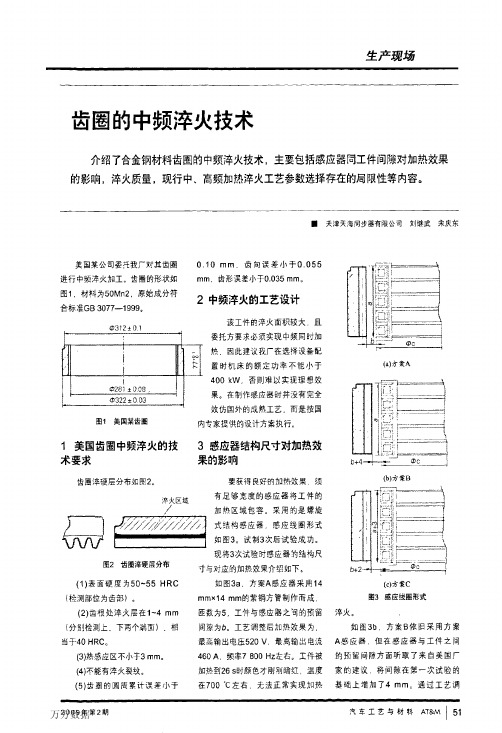
万方数据金属加工生产现场整,最终加热效果为最大输出电压570V,最大输出电流520A,频率8000Hz左右。
被加热到26s时工件加热区域亮红,完全达到淬火所需温度。
试验过程中对加热后的工件进行了金相检验.结果符合工艺要求。
但在对其加工后的工件进行尺寸检验时发现齿形,齿向还不能满足工艺要求,于是又进行了第三次试验。
如图3c.方案C考虑到导磁体对磁场分布的影响因素.将感应器的直径增大使感应器与工件之间的间隙在第二次试验的基础上减小了2mm.同时调整了感应器的高度。
通过工艺调整最终加热效果为.最高输出电压540V.最高输出电流430A。
频率8000Hz左右,工件加热到22s时被加热区域已经亮红,完全达到淬火所需温度。
金相检验、尺寸检验完全符合工艺要求。
此次试验最为成功。
4齿圈工艺淬火的工艺质量问题4.1硬化层深度在感应器最终确定以后通过工艺调整齿根部硬化层深度可以达到2.5~4.0mm淬硬层带,满足工艺要求。
试样淬硬层的宏观解剖如图4。
中频淬火工艺定型后的齿根层深如表1。
铲’1一’’…’…一”‘…7~”一r、i’7啊;表1中频淬火工艺定型后的齿层深;位置ABC齿根淖硬层353037深度/rob10—15mm10~15mm测量位置图示|,l…r{,。
7,7…{叫ABC跳动控制在O.05mm以内。
齿形跳动控制在O.04mm以内,圆周累计控制在0.1mm以内。
完全符合图纸的设计要求。
该工件的检测报告如图5。
工件的表面硬度主要取决于淬火过程中金属组织相变的质量。
该加工过程中,工件受热较为均匀,冷却介质流量充足且冷却覆盖面大于工件的加热面积,故此工件的表面硬度很均匀,如表2。
该齿圈的材质为50Mn2.由于中碳钢中加入合金元素使得其淬透性大大提高,其淬火裂纹的倾向还是较大。
为此,选用了美国好富顿公司提供的AQ251淬火介质.配比浓度控制在9%~13%。
采用合理的加工工艺后.在加工过程中对避免出现淬火裂纹控制收到实效。
中频表面淬火工艺技术报告

关于中频表面淬火工艺的技术报告热处理是机械制造中热加工工艺的一种。
它对保证机械产品的质量,延长使用寿命,有着重大的作用。
钢的热处理就是利用钢在加热、保温和冷却作用下,其内部发生组织状态(晶体结构、组织形态)、物理状态(比容、残余内应力等)和化学成分分布的变化,而使工件具有预期的工艺性能、机械性能、物理性能和化学性能,以达到便于冷热加工,提高使用寿命,充分发挥材料潜力的目的。
钢的热处理基本工艺包括退火、正火、淬火、回火和化学热处理等。
根据在车间实习和工作情况,我将主要负责车间中频表面淬火工序的工艺编制。
所以将重点放在中频表面淬火工序上。
一、感应加热原理及分类中频加热是感应表面加热的一种。
感应表面加热是利用导体(零件)在高频磁场作用下产生的感应电流(涡流损耗)以及导体内磁场的作用(磁滞损耗)引起导体自身发热而进行加热的。
根据设备的频率不同分为:①高频加热,频率为100~500千赫。
淬硬层深度为0.3~3㎜,加工工件最小直径为Φ28㎜;②中频加热,一般采用8000赫兹和2500赫兹二种,淬硬层深度:8000赫兹 1.3-5.5㎜,加工工件最小直径为Φ16㎜;2500赫兹 2.4-10㎜,加工工件最小直径为Φ28㎜;③工频加热,频率为50赫兹,淬硬层深度为17-70㎜,加工工件最小直径为Φ200㎜。
目前,我车间使用的设备是中频立式淬火机床,频率为8000赫兹。
而多年不用的高频淬火机床在车间搬、拆迁过程中已经拆除了。
二、感应加热表面淬火工艺及选择感应加热工艺参数包括着热处理参数和电参数。
热处理参数包括加热温度、加热时间、加热速度以及淬火层深度。
电参数包括设备的频率、零件单位面积功率等。
感应加热淬火工艺中几个主要问题:1、确定零件的技术要求表面淬火零件的技术要求包括:表面硬度、淬火层深度及淬硬区分布、淬火层组织等。
⑴.表面硬度:感应淬火后零件的表面硬度要求与材料的化学成分和使用的条件有关。
⑵.淬火层深度:淬火层深度主要是根据零件的机械性能确定的。
转盘轴承齿圈连续中频感应淬火工艺

复杂 , 齿轮模数小 , 淬火冷却速度快 , 5 %。
3 . 3 感应 加热 设 备选择
( 1 )
齿 轮淬火 加热 功率 为
P总=A P S,
间隙 E = 3~ 5 m m, 如 图 2所示 。
一
式 中: P总 为齿 轮加 热所 需总 功率 , k W; △ P为齿 轮 加 热 的功率 因数 , k W/ c m , 根 据 淬 硬层 深 度 要 求 ,
表 1 常用 齿 轮 中频 表 面 感 应 淬 火 技 术
淬火方式 特点 适用 范围( 齿轮模数 )
选用 P A G有机淬火介质 , 其可以完全溶于水 , 同时具有 一定 的防锈 性 。使 用 该淬 火 介 质 高温 区 冷却速度快 , 低温区冷却速度慢 , 可 以通过调节淬 火介 质浓 度实 现不 同的低 温冷 却 速度 。合理 的低
法, 将 全齿 回转 加 热淬 火 的 大 型齿 圈 进行 分 割 , 对
几个齿 同 时进 行 感应 加 热 淬 火 , 以降 低 功耗 , 简 化
感应器设 计 , 便于对 温度 、 操作及淬 火质量 的控制 。
3 沿齿 顶 圆连 续加 热 淬 火工 艺
3 . 1 齿轮 的预 处 理
转 盘轴 承齿 圈 在 粗 车 后 进 行 调 质 处 理 , 为 淬 火做 好组 织 上 的准 备 , 同 时保 证 非 淬 火 区 的 硬 度 达 到要求 , 最 大 限度消 除 锻造 、 粗车 等 前 工序 中产
图1 某型 号转 盘 轴 承 齿 圈结 构 示 意 图
盾构轴承内圈多面中频淬火工艺研究
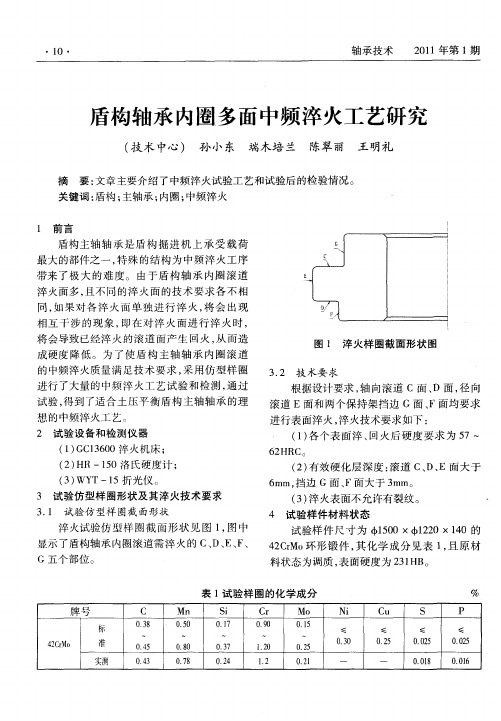
盾构 主轴 轴 承 是 盾 构 掘 进 机 上 承 受 载 荷 最 大的部件 之一 , 殊 的结 构 为 中频 淬火 工 序 特
带来 了极 大 的 难 度 。 由于 盾 构轴 承 内 圈 滚 道
淬 火面多 , 且不 同 的淬火 面 的技 术 要求 各 不 相 同 , 果 对 各 淬 火 面单 独 进 行 淬 火 , 会 出现 如 将 相 互 干 涉 的 现象 , 在对 淬 火 面 进 行 淬 火 时 , 即 将 会导致 已经淬 火 的滚 道 面产 生 回火 , 而造 从 成 硬度 降 低 。为 了使 盾 构 主 轴 轴 承 内圈 滚 道 的中频淬 火质量 满 足技 术要 求 , 用仿 型 样 圈 采 进 行 了大 量 的中频 淬火 工 艺试 验 和 检测 , 过 通 试 验 , 到 了适合 土 压平 衡 盾 构 主轴 轴承 的理 得 想 的 中频 淬火工艺 。
滚 道 E 小 轴 向 滚 道 D 和保 持 架 小 挡 边 F 因淬 、 , 火 面相互 连接 , 了解决 各淬 火 面相互 干涉 的 问 为 题 , 火 时采用 仿形感 应 器 ( 图 2 对 五个 平 面 淬 见 ) 同时进行 连续 加热淬 火 。
5 1 2 试验 工艺 ..
5 1 2 1 预 热工艺 及 淬火工 艺 .. . 中频淬 火试 验 采 用 的预 热 工 艺 及 淬 火 工 艺 参 数 见表 2 。
4 CMo环形 锻 件 , 化 学 成 分 见 表 1 且 原 材 2r 其 ,
料状 态为调质 , 面硬度为 2 1 。 表 3 HB
表 1 验样 圈的化 学成 分 试
牌 号
标
4 CY 2 ro l 准
%
N i
≤
03 .O
C
国外某型机车曲轴中频感应淬火工艺
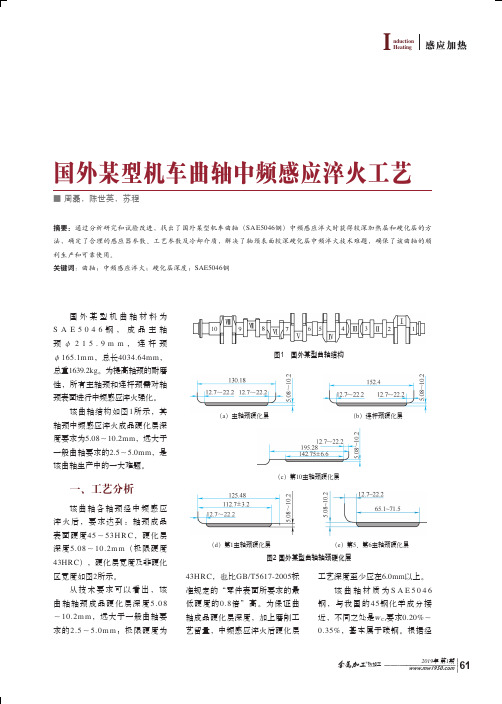
2019年 第1期热加工61国外某型机车曲轴中频感应淬火工艺■ 周磊,陈世英,苏程摘要:通过分析研究和试验改进,找出了国外某型机车曲轴(SAE5046钢)中频感应淬火时获得较深加热层和硬化层的方法,确定了合理的感应器参数、工艺参数及冷却介质,解决了轴颈表面较深硬化层中频淬火技术难题,确保了该曲轴的顺利生产和可靠使用。
关键词:曲轴;中频感应淬火;硬化层深度;SAE5046钢国外某型机曲轴材料为 S A E 5046钢,成品主轴颈φ215.9m m ,连杆颈φ165.1mm ,总长4034.64mm ,总重1639.2kg 。
为提高轴颈的耐磨性,所有主轴颈和连杆颈需对轴颈表面进行中频感应淬火强化。
该曲轴结构如图1所示,其轴颈中频感应淬火成品硬化层深度要求为5.08~10.2mm ,远大于一般曲轴要求的2.5~5.0mm ,是该曲轴生产中的一大难题。
一、工艺分析该曲轴各轴颈经中频感应淬火后,要求达到:轴颈成品表面硬度45~53H R C ,硬化层深度5.08~10.2m m (极限硬度43HRC ),硬化层宽度及非硬化区宽度如图2所示。
从技术要求可以看出,该曲轴轴颈成品硬化层深度5.08~10.2m m ,远大于一般曲轴要求的2.5~5.0m m ;极限硬度为43HRC ,也比GB/T5617-2005标准规定的“零件表面所要求的最低硬度的0.8倍”高。
为保证曲轴成品硬化层深度,加上磨削工艺留量,中频感应淬火后硬化层工艺深度至少应在6.0mm 以上。
该曲轴材质为S A E 5046钢,与我国的45钢化学成分接近,不同之处是w Cr 要求0.20%~0.35%,基本属于碳钢。
根据经图1 国外某型曲轴结构(a )主轴颈硬化层 (b )连杆颈硬化层(c )第10主轴颈硬化层(d )第1主轴颈硬化层 (e )第5、第6主轴颈硬化层图2 国外某型曲轴轴颈硬化层图3 高低浓度AQ251及清水冷却特性曲线对比表3 第一次试验的检验结果试样名称编号淬火硬度HRC 回火硬度HRC硬化层深度/mm硬化层宽度/mm主轴颈试样1-158.248.3 5.6099.0主轴颈试样2-158.748.7 5.4066.0主轴颈试样3-159.048.8 5.40146.0连杆颈试样4-158.248.7 5.20117.0主轴颈试样5-158.649.5 5.4593.0图4 第1主轴颈硬化层宏观照片图5 第5、第6主轴颈硬化层宏观照片图6 第10主轴颈硬化层宏观照片图7 连杆颈硬化层宏观照片图8 主轴颈硬化层宏观照片热加工2019年 第1期 热加工根据化学成分对其淬透性进行了计算,淬透性曲线如图11所示。
中频淬火工艺参数

中频淬火工艺参数是指在中频感应加热设备中进行淬火时所设定的关键参数,以确保工件达到所需的硬度和性能。
这些参数会因不同工件的材料、形状和尺寸而有所不同。
以下是一些常见的中频淬火工艺参数:
中频淬火温度:工件在达到临界温度时需要进行淬火,这个温度因材料而异。
中频淬火冷却介质:常见的冷却介质包括水、油和聚合物溶液。
选择合适的冷却介质取决于工件的材料和尺寸。
中频淬火冷却速率:冷却速率对工件的硬度和性能有着重要影响。
通常通过控制冷却介质的流量和温度来实现。
中频淬火保温时间:保温时间是指在温度达到设定值后需要持续保持工件在冷却介质中的时间。
保温时间的长短也会影响工件的硬度和性能。
这只是一些常见的中频淬火工艺参数,实际参数的设定需要根据具体的工作要求、工件材料和设备性能来确定。
对于具体的淬火工艺参数,我建议您咨询相关领域的专业人士或参考相关的文献资料以获取更准确的信息。
- 1、下载文档前请自行甄别文档内容的完整性,平台不提供额外的编辑、内容补充、找答案等附加服务。
- 2、"仅部分预览"的文档,不可在线预览部分如存在完整性等问题,可反馈申请退款(可完整预览的文档不适用该条件!)。
- 3、如文档侵犯您的权益,请联系客服反馈,我们会尽快为您处理(人工客服工作时间:9:00-18:30)。
关于中频表面淬火工艺的技术报告
热处理是机械制造中热加工工艺的一种。
它对保证机械产品的质量,延长使用寿命,有着重大的作用。
钢的热处理就是利用钢在加热、保温和冷却作用下,其内部发生组织状态(晶体结构、组织形态)、物理状态(比容、残余内应力等)和化学成分分布的变化,而使工件具有预期的工艺性能、机械性能、物理性能和化学性能,以达到便于冷热加工,提高使用寿命,充分发挥材料潜力的目的。
钢的热处理基本工艺包括退火、正火、淬火、回火和化学热处理等。
根据在车间实习和工作情况,我将主要负责车间中频表面淬火工序的工艺编制。
所以将重点放在中频表面淬火工序上。
一、感应加热原理及分类
中频加热是感应表面加热的一种。
感应表面加热是利用导体(零件)在高频磁场作用下产生的感应电流(涡流损耗)以及导体内磁场的作用(磁滞损耗)引起导体自身发热而进行加热的。
根据设备的频率不同分为:①高频加热,频率为100~500千赫。
淬硬层深度为0.3~3㎜,加工工件最小直径为Φ28㎜;②中频加热,一般采用8000赫兹和2500赫兹二种,淬硬层深度:8000赫兹 1.3-5.5㎜,加工工件最小直径为Φ16㎜;2500赫兹 2.4-10㎜,加工工件最小直径为Φ28㎜;③工频加热,频率为50赫兹,淬硬层深度为17-70㎜,加工工件最小直径为Φ200㎜。
目前,我车间使用的设备是中频立式淬火机床,频率为8000赫兹。
而多年不用的高频淬火机床在车间搬、拆迁过程中已经拆除了。
二、感应加热表面淬火工艺及选择
感应加热工艺参数包括着热处理参数和电参数。
热处理参数包括加热温度、加热时间、加热速度以及淬火层深度。
电参数包括设备的频率、零件单位面积功率等。
感应加热淬火工艺中几个主要问题:
1、确定零件的技术要求
表面淬火零件的技术要求包括:表面硬度、淬火层深度及淬硬区分布、淬火层组织等。
⑴.表面硬度:感应淬火后零件的表面硬度要求与材料的化学成分和使用的条件有关。
⑵.淬火层深度:淬火层深度主要是根据零件的机械性能确定的。
⑶.淬硬区分布:按零件的几何形状与工作条件的不同,各种表面淬火零件的硬化区部分和尺寸有不同的要求。
⑷.金相组织:按零件的材料及工作条件,规定各格的等级范围。
按评级标准进行金相评级。
2、加热温度的选择
感应加热速度快,与一般加热相比,必须选用较高的加热速度,适宜的加热温度是与钢材的化学成分、原始组织状态及加热速度等因素有关。
我车间由于设备的限制,只能采取目测加热温度的方法。
3、设备频率的选择
频率的选择主要是根据淬火层深度和零件的尺寸大小来确定。
当设备给定或选定以后,设备的频率就是一个不可调的参数。
我车间的设备只有立式淬火机床一台,故工艺选择中不再考虑设备频率。
4、感应加热方法及工艺操作
感应加热方法基本分为两种:
⑴.同时加热法,这种加热法是被加热的表面同时共热升温,零件需要加热的整个部分都被感应器包围着。
在大批量生产时,为充分发挥设备潜力,提高生产效率,只要设备输出功率足够的条件下,尽可能采用同时加热。
⑵.连续加热法,零件表面的加热和冷却时连续不断进行的。
连续加热生产率较低,但加热面积减小,设备的功率可以降低,因而扩大了设备的应用范围。
5、感应加热后的冷却方式
冷却方法有喷射冷却、浸液冷却、埋油淬火等。
⑴.喷射冷却,是常用的方法。
我车间采用的是将冷却液通过感应器上的许多小孔,喷射到加热面上,进行冷却。
⑵.浸液冷却,主要是用于同时加热。
零件表面同时加热完毕后,立即将淬火部分浸入淬火槽中,进行冷却。
如3B151-2-381锤头,要求Φ60×110处表淬。
加热后直接进入水中冷却。
⑶.埋油淬火,当采用连续加热法时,为避免喷油时产生油烟,可将感应器降至油面以下,进行油面以下的连续加热和冷却。
我车间就有我厂自行制造的埋油淬火机床。
6、感应淬火后的回火
感应加热淬火后,应力分布不均,组织不稳定。
为了降低拉应力,稳定组织,达到所要求的机械性能,有必要进行回火。
回火方法有:炉内回火,自回火和感应加热回火。
⑴.炉内回火:
在电炉内回火,回火时间一般为1~2小时,回火温度按图纸技术要求选择。
⑵.自回火
对于形状简单,大量生产的零件可采用自回火。
⑶.感应加热回火
感应加热回火时,为了达到回火要求,回火时的加热层深必须大于淬火层深,且必须采用相当慢的加热速度,故生产效率较低。
如我车间承制的天车轨道,原来就采用感应加热回火,但效率太低,影响进度,所以自行设计、制作了专用轨道回火炉,生产效率大大提高了。
感应加热淬火,加热速度快,生产效率高,产品质量好,但是技术含量也相对较高。
所以只有将理论知识与生产实践知识良好的结合起来才能够很好的进行以后的工作。