注塑新产品试模流程(注塑培训)
注塑试模参数设定流程及要求
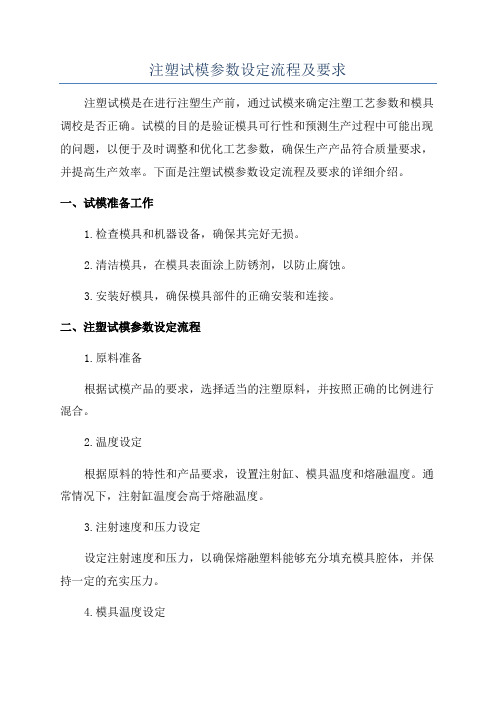
注塑试模参数设定流程及要求注塑试模是在进行注塑生产前,通过试模来确定注塑工艺参数和模具调校是否正确。
试模的目的是验证模具可行性和预测生产过程中可能出现的问题,以便于及时调整和优化工艺参数,确保生产产品符合质量要求,并提高生产效率。
下面是注塑试模参数设定流程及要求的详细介绍。
一、试模准备工作1.检查模具和机器设备,确保其完好无损。
2.清洁模具,在模具表面涂上防锈剂,以防止腐蚀。
3.安装好模具,确保模具部件的正确安装和连接。
二、注塑试模参数设定流程1.原料准备根据试模产品的要求,选择适当的注塑原料,并按照正确的比例进行混合。
2.温度设定根据原料的特性和产品要求,设置注射缸、模具温度和熔融温度。
通常情况下,注射缸温度会高于熔融温度。
3.注射速度和压力设定设定注射速度和压力,以确保熔融塑料能够充分填充模具腔体,并保持一定的充实压力。
4.模具温度设定根据试模产品的要求,设置合适的模具温度,以保证注塑成型后的产品质量。
5.冷却时间设定根据试模产品的要求,合理设定冷却时间,以保证熔融塑料充分冷却和凝固,以获得理想的产品质量。
6.射嘴和注射缸位置调整调整射嘴和注射缸的位置,以确保注塑过程中塑料能够均匀地填充模具腔体。
三、试模要求1.产品尺寸要求试模产品的尺寸要求应与产品设计要求一致,包括长度、宽度、高度和壁厚等。
2.产品外观要求试模产品的外观要求应与最终产品的外观要求一致,包括表面光滑度、色彩和纹理等。
3.产品物理性能要求试模产品的物理性能要求应与最终产品的物理性能要求一致,包括拉伸强度、冲击性能和硬度等。
注塑模具试模作业指导书

注塑模具试模作业指导书注塑模具试模作业指导书1.介绍注塑模具试模作业指导书旨在指导操作人员正确使用注塑模具进行试模操作。
本指导书详细描述了试模前的准备工作、试模步骤、常见问题及解决方法等内容,以确保试模作业的安全、高效进行。
2.准备工作2.1 材料准备2.1.1 确保所需注塑材料已经准备好,并进行质量检测。
2.1.2 检查注塑材料的储存条件,确保其干燥、无杂质。
2.1.3 将注塑材料按照要求放置在指定区域。
2.2 模具检查2.2.1 检查注塑模具的外观,排除表面污垢,确保模具干净。
2.2.2 检查模具零部件,确保其完整、无损。
2.2.3 清洁模具的冷却系统,确保其畅通无堵塞。
2.2.4 涂抹模具专用防锈剂,保持模具的表面光洁。
2.3 设备准备2.3.1 开启注塑机设备并进行预热。
2.3.2 检查注塑机的工作性能,确保其正常运转。
2.3.3 准备好所需的模具安装工具。
3.试模步骤3.1 模具安装3.1.1 将模具安装在注塑机上,并确保模具与机器连接紧密。
3.1.2 安装模具的保护装置,确保操作人员的安全。
3.2 调整注塑参数3.2.1 根据注塑产品的要求,调整注塑机的温度、压力、速度等参数。
3.2.2 进行注塑材料的预热和预塑。
3.3 开始试模3.3.1 打开注塑机的开关,将注塑材料注入模具中。
3.3.2 关注注塑机的工作情况,确保注塑过程顺利进行。
3.3.3 观察试模产品的质量,确保其满足要求。
4.常见问题及解决方法4.1 模具堵塞问题:模具冷却系统堵塞,导致注塑过程中温度过高。
解决方法:清洁模具冷却系统,确保其畅通无堵塞。
4.2 产品质量不合格问题:产品存在短射、气孔等缺陷。
解决方法:调整注塑参数,改善注塑过程中的温度、压力控制。
5.附件本文档附带以下附件供参考:- 注塑模具试模检查表- 注塑参数调整记录表6.法律名词及注释6.1 注塑材料:用于注塑过程中的塑料原材料。
6.2 模具:用于塑料制品成型的工装,包括模具本体及相关零部件。
注塑试模作业指导书
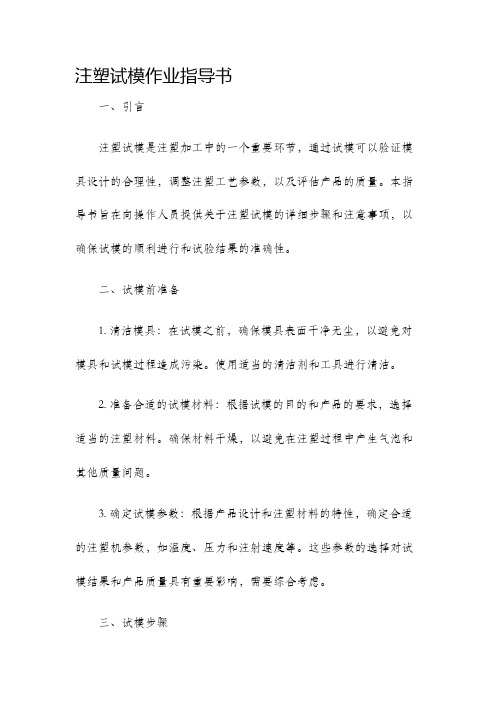
注塑试模作业指导书一、引言注塑试模是注塑加工中的一个重要环节,通过试模可以验证模具设计的合理性,调整注塑工艺参数,以及评估产品的质量。
本指导书旨在向操作人员提供关于注塑试模的详细步骤和注意事项,以确保试模的顺利进行和试验结果的准确性。
二、试模前准备1. 清洁模具:在试模之前,确保模具表面干净无尘,以避免对模具和试模过程造成污染。
使用适当的清洁剂和工具进行清洁。
2. 准备合适的试模材料:根据试模的目的和产品的要求,选择适当的注塑材料。
确保材料干燥,以避免在注塑过程中产生气泡和其他质量问题。
3. 确定试模参数:根据产品设计和注塑材料的特性,确定合适的注塑机参数,如温度、压力和注射速度等。
这些参数的选择对试模结果和产品质量具有重要影响,需要综合考虑。
三、试模步骤1. 安装模具:将试模所需模具安装到注塑机上。
确保模具位置正确,并通过紧固件固定模具,以确保稳定性。
2. 注塑机调试:启动注塑机,根据试模参数进行调试,调整温度、压力和速度等参数,并将试模材料导入注塑机料斗中。
3. 启动试模:按照注塑机操作步骤,启动注塑机进行试模。
注意观察注塑机和模具的运行状态,确保正常运转。
4. 观察注塑过程:在注塑过程中,注意观察注塑材料的熔融状态和充模情况。
根据需要进行调整,确保产品的尺寸和形状符合设计要求。
5. 停机观察:在试模过程中,及时停机观察和检查产品的质量。
尽量保留试模样品,以供后续评估和分析。
6. 试模结束:试模完成后,关闭注塑机,清理模具和注塑机设备。
将试模样品分类保存,并填写试模记录表,以备参考和进一步分析。
四、注意事项1. 安全第一:在进行注塑试模时,一定要遵守注塑机的安全操作规程,佩戴必要的防护装备,确保人身安全。
2. 精确记录:在试模过程中,准确记录注塑机参数、模具状态、试模材料和产品质量等信息。
这些记录是分析和评估试模结果的重要依据。
3. 合理调整:在试模过程中,根据观察和实际情况,及时调整注塑机参数和模具结构等,以获得更好的试模效果。
注塑模具试模流程
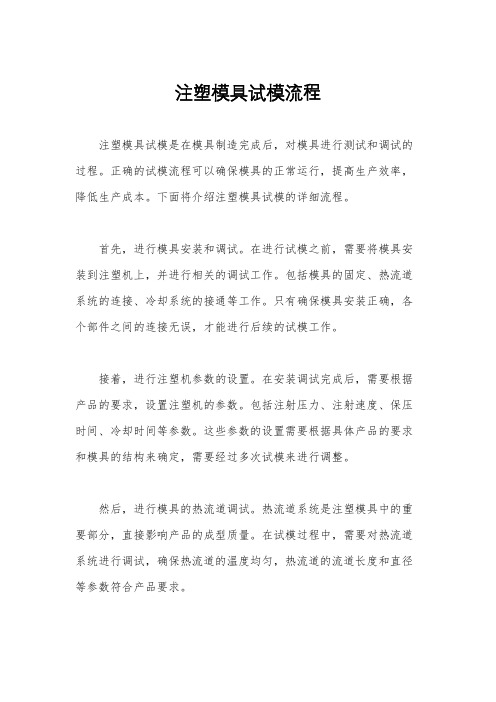
注塑模具试模流程注塑模具试模是在模具制造完成后,对模具进行测试和调试的过程。
正确的试模流程可以确保模具的正常运行,提高生产效率,降低生产成本。
下面将介绍注塑模具试模的详细流程。
首先,进行模具安装和调试。
在进行试模之前,需要将模具安装到注塑机上,并进行相关的调试工作。
包括模具的固定、热流道系统的连接、冷却系统的接通等工作。
只有确保模具安装正确,各个部件之间的连接无误,才能进行后续的试模工作。
接着,进行注塑机参数的设置。
在安装调试完成后,需要根据产品的要求,设置注塑机的参数。
包括注射压力、注射速度、保压时间、冷却时间等参数。
这些参数的设置需要根据具体产品的要求和模具的结构来确定,需要经过多次试模来进行调整。
然后,进行模具的热流道调试。
热流道系统是注塑模具中的重要部分,直接影响产品的成型质量。
在试模过程中,需要对热流道系统进行调试,确保热流道的温度均匀,热流道的流道长度和直径等参数符合产品要求。
接下来,进行模具的冷却系统调试。
冷却系统对模具的寿命和产品的成型质量有着重要影响。
在试模过程中,需要对冷却系统进行调试,确保冷却水的流动畅通,冷却效果良好,避免产品在成型过程中出现热缩等问题。
最后,进行产品的成型试验。
在完成以上调试工作后,就可以进行产品的成型试验。
通过试模,可以检验产品的尺寸精度、表面质量、收缩率等指标,同时也可以检验模具的运行稳定性和生产效率。
总之,注塑模具试模是一个非常重要的环节,直接关系到产品的质量和生产效率。
正确的试模流程可以确保模具的正常运行,提高生产效率,降低生产成本。
因此,对于模具制造厂家和注塑加工厂来说,都需要重视注塑模具试模工作,制定科学合理的试模方案,确保模具的顺利投产。
注塑试模步骤及注意事项

注塑试模步骤及注意事项注塑试模步骤及注意事项注塑试模步骤及注意事项【全球塑胶网20__年3月12日网讯】1.欲试之原料务必先行干燥.2.模具挂上,中心孔要对准确无误,锁模力视模具大小及投射面积大小而进行调整.当射出时分模面不是因为射压过高而产生毛边,可逐渐加大锁模力,直到不起毛边为主,如此可延长模具使用寿命.锁模压力选在50-70之间,不得大于95为佳.3.开关模速度,压力,位置,距离调整妥当,低压保护必须调校好,这是基于对新模不了解,有滑块之模具开关模速不可太快,有抽心的模应用手先行试验其功能是否正常,否则因一时失误,将导致模具的损坏.4.设定成型条件,包括射出料温,压力,速度,时间,位置,计量距离等.射压,速度,计量由低而高依成型状况而定,射出时间,冷却时间由长至短,依成品情形而减速少,如此可防止粘模及过度充填.5.适当选调背压,注意垫料量在0.5CM-1.0CM为宜,这样无论是新模或产品品质及机台的安全使用都有必要.试模步骤及注意事项(二)1.注意肘节十字头是否伸直,以防射出时模具被逼退而溢出毛边造成模具损伤.2.前几模应喷脱模剂,如脱模顺利,不致产品顶白,变形则可免喷.3.依成品需要,修改各成型条件,如对压力,速度调整1-2模便可看出,如对模温,料温调整,要5分钟左右方可看出结果,避免因急燥而不断变更成形条件,影响试模质量.4.试模中应注意模温的上升,试多模时应加冷却水,依据料质选择料温.5.背压依成品状况而调整,松退距离以不介入空气为原则,储料中原料粘度低,转速可较快,原料粘度高应放慢,注意用背压时,转速越快,原料的熔融越均匀,但应注意其有无熔胶过热现象.6.料管的料要完全射完后方可停机,必要时必须清洗料管,吹干模具冷却水路之冷却水,擦干净模腔料屑,喷防锈油.7.填写试模报告,首件确认表,记录各成型条件,当第二次试模时,参考模具不良状况及欲修改的地方,均需作好记录射出成型的操作条件射出成型的操作条件一.关模压:原则上应大于塑胶射入模内的总压,以不出毛边为基准.二.压力和速度有部分相同的关系作用于模内,目的使原料进入模内能均匀,撤底,适量的充满各角落.太低会短射,缩水,太高有毛边,过饱,粘模.烧焦,易损模具及内应力高等不良现象.三.速度:速度的快慢决定原料在模具浇道内及成品中之状况,快有毛边,过饱.烧焦,粘模,慢了出现短射,缩水,结合不良易断等.四.温度:原料不同,温度各异太低溶胶颜色不均,成品内应力增大,因温度过低增压过高,可能引起螺杆断裂,过高,产品有毛边,又因冷却产生温差,引起收缩;原料会分解,变黄,变色,易断裂.冷却时间变长,气不容易排出,会有瓦斯气.五.背压:螺杆在旋转加料时后退之阴力称为背压.其作用使原料在输送压缩中更加紧密.能使原料的空气,水份从螺杆后排出,使溶胶中不含影响成品表面的气体成份.低会有气泡,表面银纹.高会过热,结块,溢胶,周期长,螺杆不退.同时松退的应用很重要:背压高时务必用松退并注意距离,要不介入空气及不溢胶为准则.六.模温高低及冷却时间的长短,影响成品的粘模,缩水,尺寸公差,表面亮度,周期等,应依实际情况而适时调整.另压克力,PC如成品肉厚时要有模温,才不会产生气泡及应力.(因肉厚冷热不均)BMC的成型要点BMC是以特殊途不饱和聚脂为主之热固硬化性树脂,具有优良的电气绝缘特性,耐热性,耐燃性,高机械强度尺寸安定性.耐蚀性,耐水性,收缩稳定性等.为各种热固硬化性成型材料中最高级品.其加工成型条件如下:1.成型温度:成型温度与MBC 热固性聚脂塑胶之流动性及其所选择加工成型机械加工方式有极度大之关系因素.温度在140℃-170℃2.成型时间:加工成型时间与当时模具正确温度及成品的肉厚,形状有关,一般硬化程度可由表面光泽予以段定,3.成型压力:成型压力视而不见所选择加工成型机械与方式而定,材料加工后,成品表面光泽时之压力,其压力在20-200KG/CM24.储存:MBC材料庆置18℃以下之冷暗处,使用后剩余品应予密闭保存,一般正常使用可存放一个月,外在之温度与MBC之软,硬将影响其储存期.如使用冷藏将延长BMC之寿命.5.用途:应用在各种电气产品,通信资问心无愧机零件,汽车类零件,电动工具绝缘披覆,超大型静音马达,食品餐具等均广泛应用.几种特殊原料的成型特性含玻纤的成型要点1.FRTP的流动性低于非强化料,所以常增加管温及模温,射出压力等.同理模子的浇口,横浇道,浇口等的尺寸,也须大天非强化料.2.成型收缩率甚大于非强化树酯,呈方向性的流动,所以浇口方向设法减少配向所致的不良影响.3.成型品的胶接线部强度,常低于其他部份,在设计制品模子时须加注意于熔接部设排气孔,不致包风现象4.模子各部份(特别是浇口)或螺杆组件,熔胶管等磨耗快,宜注意材质及表面的硬度处理低发泡的成型要决在射出计量终了,螺杆后退时,在等待次一射出开始的期间,管内的发泡剂也慢慢开始分解,其气体压力,却使螺杆后退,故宜在射出缸的油压回路设背压调整回路,抑止杆后退.同时射嘴漏料也增多,宜用弹簧阀的控制.模内排气孔不充份时,其花模和光泽不利.螺杆制造宜用稍有混练型的较易有发泡作用.电木尿素等成型1.换装另设计制造的电木射击出用熔胶管及螺杆,射嘴等.用油热循环式的加温,油温控制在80℃-100℃左右,模温控在160℃-180℃左右.2.模子两边各安装圆柱电热管,两面模板装硬质石棉板,它是和塑胶成相反的,必须在高温模内加热成型,所以模子必用用耐高温铁材,并电镀优良,浇口加大排气口加大,料管内绝对不能有滞料存在,一次定射完毕并到底.3.当温度达到开始第一次射入后,螺杆须等15-20秒开始加料动作.加完后把射座暂松退一下,让射嘴与母模暂分开一点,因母模温度高过射嘴,能便射嘴部硬化而射不出料.一模时间在45秒或55秒间(看成品厚薄),才开模取成品,依次完成二次射出.NL-9成型重点1.尼龙的成型,其成型厚度对收缩率有较大影响.模温高,收缩会增大.射压调整很重要,并应注意其前收缩和后收缩.对尺寸要求严格的成品更应重视.2.烘料:因尼龙的吸湿性最大.放置久了,极难烘干,原料应先进先用,避免放置过久.同时未烘干的原料切勿进入下料口.因会使原料在螺牙上卷曲卡住.造成不加料,所以说要常注意烘料桶的料是否低于警界线,如低于就得加料以免料烘不干.3.尼龙属高温水性,易熔解,但固化也快.其融点温度与成型温度相差5-10℃而己,因此造成其变化范围较窄.4.其粘度低,容易流涕,加热温度在控制要注意,防止固化溢料,松退要注意应用.勿用背压.5.尼龙对温度依存性很大,射出速度要快.防止原料的硬化.太薄处易冷化引起充填不饱.结晶化也低.造成成品有透明性.6.尼龙的润滑性好,耐冲击好,但尺寸安定较差,属于工程塑胶.7.尼龙成型螺杆选择上要压缩比大特别留意止逆环的磨损程度应低于5-10条,如磨损过多,造成加料不稳或不加料.影响原料的供输如果磨损要速更换止逆环.以免加长周期影响生产进度及浪费电源8.尼龙加色粉会造成加料不顺,应注意其有无色粉粘于螺牙上,必要时要加滑石粉给予排除,参考用量:1KG+0.5G滑石粉.9.尼龙参考成型条件:模温:60-80度,料管温220-260度,烘料80-110度,2-4H,软化点:220度。
试模的基本步骤

试模的基本步骤步骤1.设置料桶的温度。
这里需要注意的是,初始的料桶温度设置必须依据材料供应商的推荐。
这是因为,不同厂家、不同牌号的相同材料可能具有相当大的差异,而材料供应商往往对自己的材料有着相当深入的研究和了解。
用户可根据他们的推荐进行基本的设置,然后再根据具体的生产情况进行适当的微调。
除此之外,还需要使用探测器测量熔体的实际温度。
因为我们所设定的料桶温度往往由于环境、温度传感器的型号和位置深度不同等原因,并不能保证与熔体温度100%的一致。
有时由于油污的存在或其他原因,熔体的实际温度和料桶的设置温度差别很大(以前,我们曾有过两者温差相差高达30℃的例子)。
步骤2.设置模具的温度。
同样,初始的模具温度设置也必须根据材料供应商提供的推荐值。
需要注意的是,我们所说的模具温度指的是模腔表面的温度,而不是模温控制器上显示的温度。
很多时候,由于环境以及模温控制器的功率选择不当等原因,模温控制器上显示的温度与模腔表面的温度并不一致。
因此,在正式试模之前,必须对模腔表面的温度进行测量和记录。
同时,还应当对模具型腔内的不同位置进行测量,查看各点的温度是否平衡,并记录相应的结果,以为后续的模具优化提供参考数据。
步骤3.根据经验,初步设定塑化量、注射压力的限定值、注射速度、冷却时间以及螺杆转速等参数,并对其进行适当的优化。
步骤4.进行填充试验,找出转换点。
转换点是指从注射阶段到保压阶段的切换点,它可以是螺杆位置、填充时间和填充压力等。
这是注塑过程中最重要和最基本的参数之一。
在实际的填充试验中,需要遵循以下几点:(1)试验时的保压压力和保压时间通常设定为零;(2)产品一般填充至90%~98%,具体情况取决于壁厚和模具的结构设计;(3)由于注射速度会影响转压点的位置,因此,在每次改变注射速度的同时,必须重新确认转压点。
注塑厂试模流程操作规范
注塑厂试模流程操作规范1.目的为促使本公司试模流程规范化,合理化,对新开的模具(或者外厂调入的模具)在量产前进行确认模具的现状与适用机台、原料、模具缩水比例、产品的尺寸﹑外观、结构等问题并加以承认, 让新旧模具尽快地投入量产/生产,达到缩短项目运作的时间提高工作效率,明确规范试模作业程序、方法与安全注意事项﹐以保证试模品质为目的而制定本规范。
2.范围适用于注塑厂所有新模具、改模旧模具、外来试模、生产模具等量产前的试样试模作业过程。
3.职责3.1生产部:负责试模模具的上下模、试模调机,试模操作人员在试模流程中必须按照此规范操作,防止试模操作人员因操作不当造成事故。
3.2工程部权责:由工程部制定本规范并实施与管理,对本规范负责,负责提供模具图纸、产品图纸、产品检测标准、原料物性表、特殊结构等信息,试模跟进、负责提供试模原材料和特殊铺助器械的采购准备工作。
3.3修模组:负责将组装以及确认好的模具拉到生产部指定待试模区域,摆放好以及运输叉车归位,负责维修和确认试模过程中模具的异常处理。
3.4品质部:根据客户提供的产品标准确认试模产品的尺寸、外观、结构、装配、可靠性等。
4.定义试模是指在产品开发和制造流程中在产品完成模具制作后、批量生产前所进行的测试注塑步骤。
模具在完成所有配件并装配完毕后,需要通过实际的注塑并得到注塑样品,然后通过样品检测才能确定模具的制作是否完全符合设计要求。
如果注塑样品完全符合设计要求则表明模具制作没问题可以投入批量注塑生产;否则就需要根据样品反馈的问题进行模具的改模。
根据改模情况的不同,试模可能会在批量生产前多次进行直到模具完全改正所有问题。
5.内容5.1安全执行5.1.1所有人员开动桥门式天车前请佩戴安全帽、戴手套、穿劳保鞋,模具起吊后不得从人员上方经过,在模具吊起范围1.5米中心圈内不可有人员进入。
5.1.2模具吊起前请确认吊环和吊链是否有裂缝、吊环吊链不可使用变形的,变形的吊环吊链请报废到仓库,并领取新的吊环吊链。
注塑模具试模和修模流程
页次注塑模试模及修模作业程序一、目的:1.1为规范塑胶注塑模的使用和保养,减少模具的损坏,确保产品质量满足客户需求.特制定以下规程二、流程说明2.1塑胶部注塑根据工程部所下发的<试模通知单>跟催模具是否到位,并安排架模员,加料员作好试模的准备,并通知试模工程师到现场试模。
2.2试模时需要有品质工程师或专案工程师.工模人员到现场监督,试模完后,架模人员如实填写模具水路图,架模点检表;试模员填写《射出成型参数记录表》,《试模检讨报告》以便存档作为以后量产参考;工程师把试模的《射出成型参数记录表》,《试模检讨报告》经审核后再分发给模具部和工程部参考,试模要试200只左右的良品交给品质工程师确认,同时保存5模样品供工模部修模参考;自己也需保存5模左右产品供试模存档;若试模产品被判定为不合格,应通知工模部重新修模,修好后应重新试模,若在试模过程中发现模具异常则应立即通知工模人员确认并修复后才可试模,重新试模的流程同以前的流程;若试模产品被判定为OK,则工模部应重新检查模具并按要求移交模具(连同模具清单)给生产部移交时须付《模具交接单》.《模具组立检查表》,塑胶部检查OK后予以签收,并做好模具挡案。
页次2.3模具投产后,由架模员把模具从模架上领出至现场.按模具的水路图和架模点检表,技术员或领班按射出成型参数表进行生产,开机生产进行;如实填写模具保养点检表和模具的生产履历表,下模后由架摸员吹清水路喷上防锈剂保养把模具送至模具架上,如实填写模具管制表。
2.4生产中模具发生异常,如需要停机修模而下模维修时,须开立异常通知单。
停线通知单.修模通知单,通知相关人员和相关人员,经审签后需开立模具维修单连同要修模具送至工模部进行维修;修复后再进行试模,技术人员如实填写试模检讨报告,试模产品经品保工程师和研发设计工程师确认,如判定为OK则可投入生产,如判定为NG则移交模具和该模具的试模报告,通知工模检讨,给予维修,如未下机台维修,可不用开立试模检讨报告,由塑胶部依照注塑的封样进行判定OK还是NG。
注塑部试模主要流程
丰茂注塑部试模主要流程1.试模组依据试模申请单上的原料种类、颜色、数量进行领料。
2.试模人员领到料后,依据原料物性干燥,干燥前应确认原料正确无误。
3.需要试模的部门及人员,应提前准备好模具、原材料物性报告、试模申请单。
准备:1.试模人员应在试模前准备好前次试模的成型条件记录,以作为试模调机参考。
2.试模工作由工程师主导,并在试模前协调各单位参与试模,包括品质人员、模具制作人员、模具设计人员,新模/ECM试模需工程师全程参与跟进试模。
3.试模人员试模前应确认成型机无异常情况后,再依据《上落模作业指导书》架模,设定成型条件给予升温,并确认模具水路安装、顶出机构、热流道、原料干燥效果等相关细节。
待各试模条件达到后即可进行试模。
4.新模TO试模,必须参照原料供应商或者客户提供树脂物性作参考,并填写好原料物性表单或试模报告。
5.根据注塑机台能力表,对比模具适合的机台架模,并填写注塑机与模具的参考。
试模1.试模前应确认料管内原料与所需试模用料是否一致并清洗料管2.试模时,试模人员参考《注塑机操作作业指导书》进行调试运行动作。
3.模温机的使用参考《模温机操作作业指导书》。
取样方式1.试模取产品的50%、90%、95%短射样品提供给模具设计、模具制作人员,分析模流以及排气位置确定。
2.调整试模工艺待模具运行状态稳定及成型工艺稳定后,由产品工程师、品质工程师共同确认产品品质符合要求时,按照试模申请单的数量进行取样。
试模记录录入与发放1. 取样完成后由试模人员填写试模报告,详细记录试模过程模具及产品的问题点并第一时间录入试模时的工艺参数和试模报告妥善保存,以作为标准成型条件制定或下次试模时成型条件参考的依据。
试模记录表用纸档的形式传送给相应单位。
试模后工作处理1.试模完成后成型试模人员应将试模用料清理干净,剩余用料则退库,避免混料或错误使用。
试模后不良品应由试模人员及时进行清理或报废,试模后模具应进行清洁,并视情况上油或喷防锈油后下模并放置在指定的区域内。
注塑机基本试模程序
第五步: 找出保压时间 (即浇口冷凝时间) . 每次取2模产品, 然后称重(不含料头).保压时间就是产品 重量开始稳定的时间. 每次加0.5s (小产品的话可以取小)
保压时 第二模 第一模产 第二模产 保压时 第一模产 间 产品 品重(g) 品重(g) 间 (s) 品重(g) (s) 重(g) 1 4 1.5 4.5 2 2.5 3 3.5 5 5.5 6 6.5
第八步: 记录并保存以上工艺参数; 修模. 第九步: 修模后重新试模 尽量采用和上一次相同的工艺参数 . . . . . . . . . . .. ……
第十步: ( 在模具修改完毕后) 在确定的参数基础上生产2小 时, 取产品50模一模一模称重并测量某 一或几个关键尺寸,研究重量和尺寸之间的关系, 确 定可接受的重量控制偏差.
模具温度设定 °C
第三步: 在无保压和保压时间的前提下,作短射填充试验(一级 速度), 找出压力切换点( 即产品打 满95% 的螺杆位置). 目的: 把握熔体流动状态; 验证浇口是否平衡( 注意: 模温不均匀,对 于尤其是热敏性材料及浇口很小的情况下,些微的模温差异都 会造成自然平衡流道的不平衡). 查看熔体最后成型位置排气状况, 决定是否需要优化排气系统
根据如下”产品模重变动范围和参数变动范围的关系”确 定批量生产时参数控制范围
200 - 400 350 - 550 200 - 400 350 - 700 600 - 800 400 - 600
PMMA
ห้องสมุดไป่ตู้PC/ABS
1000 - 1600
800 - 1700
600 - 1000
600 - 800
400 - 800
350 - 500
PBT
700 - 1600
- 1、下载文档前请自行甄别文档内容的完整性,平台不提供额外的编辑、内容补充、找答案等附加服务。
- 2、"仅部分预览"的文档,不可在线预览部分如存在完整性等问题,可反馈申请退款(可完整预览的文档不适用该条件!)。
- 3、如文档侵犯您的权益,请联系客服反馈,我们会尽快为您处理(人工客服工作时间:9:00-18:30)。
文件名稱 :
新產品試模程序
文件編號 :PURP.1.1
版本: 1
頁數:
編輯日期:2012.03.28
相關運作程序/操 作說明書
流程簡述 新模完成入倉
安排試模 開啤辦記錄表
執行部門
審批程序
使用表格
啤机部 /工程 部/QC部
工程部/QC部
《收货單》
工程部/工程 师
工程经理
《試模單》
工程部/工程 工程師填表經理
师
審批
《啤辦記錄表》
試模
注塑部
注塑部技術員
出試模報告
ห้องสมุดไป่ตู้
試模結果
合格
不合格
分析模具問題
出改模通知 改模
注塑部 注塑部
注塑部技術員
《試模要求及記錄 》
机房主管/工程 <模具验收报告評价
师/QC
總結>
工程部
工程部
工程師出資料/ 經理審批
《改模通知》外厂 维修,要老板/总经
办批核
工模部/模厂
安排裝辦
不合格
裝辦結果
合格
入倉備用生产
工程部
工程部/QC 工程部/QC
<模具验收报告評价 總結>
注塑部
模倉簽收 <<模厂發貨單>>
編寫:张开瑞 簽署:
審批:
簽署:
文 文件 件名 編稱 號:: PURP.1.1 一.目的 二.适用范圍 三.定義 四.參考資料 五.職責 六.培訓 七.程序
八.附件/表格
新產 品試
版本:1
彩乐文具有限公司
附件 1 - <發貨單> 附件 2 - <試模單> 附件 3 - <啤辦記錄表> 附件 4 - <試模要求及記錄> 附件 5 - <改模通知> 附件 6 - <PP生產膠件重量與啤塑週期更改通知> 附件 7 - <模具評价總結>
編寫:张开瑞
審批:
簽署: 簽署:
8) 安排裝辦 8.1 如試模效果理想, 工程部對注塑樣辦(膠件/合金件等)進行組裝; 8.2 參照原開模辦,功能手辦,圖紙及其它設計要求,檢查是否符合要求,有問題則出<改模通知> 給工模 部/模厂修模。 9) 入倉備用 9.1 試模合格及樣辦組裝成功後, 工模回倉儲存備用生产, 模倉需簽收 <<模厂發貨單> >,以作記錄。 9.2 如試模結果反映膠件重量或啤塑週期有變, 啤机部發 <PP生產膠件重量與啤塑週期更改通知> (附 件6) 給工程部更正TP﹒
頁 數
模具在生產上滿足注塑要求,工程上滿足原始設計要求. 適用於所有 模具試模程序。
編輯日期:2012.03.28
試模 過 開模樣辦,設計圖紙.
1) 工模部/模厂: 根据工程部樣辦及圖紙要求,依期提供所需模具/图纸;根据工程部改模要求改模, 2) 注塑部: 根据工程部發出試模單安排試模,提出模具注塑問題情況予工程部分析及參考。 3) 工程部: 分析注塑部發現的注塑問題及注塑件結构問題,發出改模資料。 1) 注塑部同事需認識各類注塑問題(如粘模,披鋒,料不齊,水紋,气紋,拖花,拉白,頂白,縮水等) 2) 工模部/模厂同事需掌握看改模資料,工程圖紙. 3) 工程师同事需熟練分析注塑問題与模具問題,注塑件結构相互間關系,并掌握解決方法. 1) 新模完成入倉 1.1 工程部需聯絡工模部(模厂),落實具体模具制造完成期; 1.2 新模完成後工模部需填 <發貨單> (附件1),連同工模交注塑部簽收儲存。 2) 安排試模 2.1 工程師開 <試模單> (附件2)﹐工程經理簽批﹐啤机部 安排試模.﹒ 3) 開啤辦記錄表 3.1 填寫 <啤辦記錄表> (附件3),列明產品名稱,編號,模號,注塑用料,注塑套數(啤數),由經理簽批后發給 注塑部. 3.2 注塑部收到 <啤辦記錄表> ,即 安排試模,并承諾36小時內完成.填寫 <試模要求及記錄>﹐根据試模 情況由机房主管開具<模具验收报告評价總結> (附件7)
4) 試模
5) 出試模報告 5.1 試模時,試模員(技術員)進行調较注塑机并將穩定時的注塑工藝及參數記錄在 <試模要求及記錄> 表上,供工程部分析及日后生產時參考。 5.2 當試模無法正常完成,如出現嚴重粘模,嚴重走料(注塑件殘缺),頂針不退,無法安全碼模等影響模具 使用安全及操作人員安全的嚴重情況,需立即通知工程师到工場檢查并安排解決后再試模. 6) 分析模具問題 6.1 工程部對《試模要求及記錄》進行分析,根据試模結果對模具作出改善要求.如确定存在影響生產情 況,則作出 <改模通知> (附件5). 7) 改模 7.1 工模部/模厂收到 <改模通知> 後需按要求進行改模, 修改完畢再交回注塑部通知工程部再安排試模。