中英文对照施工方案
钢结构施工方案(中英文对照)
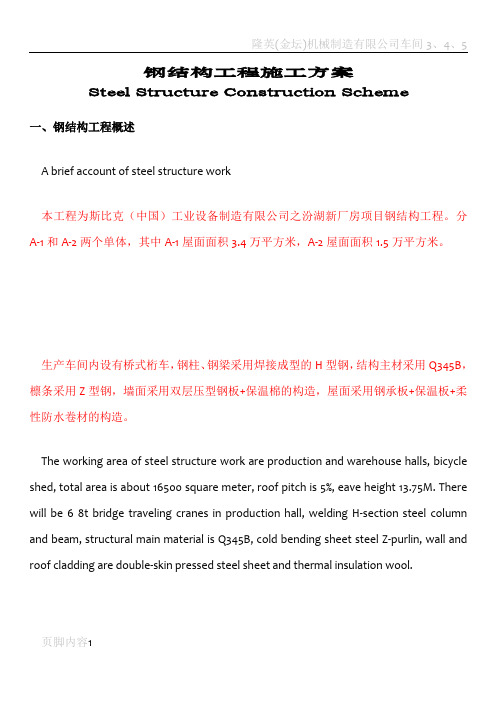
钢结构工程施工方案Steel Structure Construction Scheme一、钢结构工程概述A brief account of steel structure work本工程为斯比克(中国)工业设备制造有限公司之汾湖新厂房项目钢结构工程。
分A-1和A-2两个单体,其中A-1屋面面积3.4万平方米,A-2屋面面积1.5万平方米。
生产车间内设有桥式桁车,钢柱、钢梁采用焊接成型的H型钢,结构主材采用Q345B,檩条采用Z型钢,墙面采用双层压型钢板+保温棉的构造,屋面采用钢承板+保温板+柔性防水卷材的构造。
The working area of steel structure work are production and warehouse halls, bicycle shed, total area is about 16500 square meter, roof pitch is 5%, eave height 13.75M. There will be 6 8t bridge traveling cranes in production hall, welding H-section steel column and beam, structural main material is Q345B, cold bending sheet steel Z-purlin, wall and roof cladding are double-skin pressed steel sheet and thermal insulation wool.二、钢结构工程的特点Characteristic of steel structure work1、该工程单坡最大跨度为18m,钢柱高度大,单榀框架的平面外刚度极小,吊装过程中做好保证结构平面外的稳定作为安全技术控制的重点。
The single span of the work is 18m, the height of steel column is large, single frame plane external rigidity is very small, so the key point of safety technical control is to guarantee the stability outside the structural plane.2、厂房最大连续24跨,长度方向252m,制作安装时应注意误差累计,做好测量控制点,保证整个厂房的安装精度。
中英文对照安全施工方案

Part 8 Safety Plan安全方案1. General 概述The purpose of this project Safety Plan is to describe how we will manage and control EHS aspects of the project. It is needed to protect the work area from accident and to protect harm to the environment.本项目的安全方案将引导本项目的环境、健康及安全目标的实现,保证施工区域远离事故危害及环境免受破坏。
As comply with Client’s safety requirements, it is not an alternative to ensuring legislative compliance and the specific legislative obligation associated with our activities in practice. The EHS plan is intended as a tool to support those requirements.在遵守业主及业主安全要求的同时,保证按照当地政府要求和与工作相关的规定执行工作、环境、健康及安全计划是实施这些要求的有力支持。
2. Principle of Safety Plan 安全方案总则2.1 In order to standardize the site safety management, ensure the safety ofworking people’s life and ensure the construction equipment can be used normally, following rules will be made.为规范施工现场的安全管理,保证施工员工的生命安全,保障施工设备的正常使用,特制定本规定。
商场工程施工方案中英文

商场工程施工方案(中英文)1. 项目概况(Project Overview)1.1 项目背景(Background)该项目是商场工程施工方案的编制。
商场作为一个综合性购物中心,为顾客提供丰富的商业、休闲和娱乐设施。
本施工方案的目标是确保项目的顺利实施,按时交付,并保证施工安全和质量。
The project at hand is the construction plan for a shopping mall. As a comprehensive shopping center, the mall provides customers with a wide range of commercial, leisure, and entertainment facilities. The objective of this construction plan is to ensure the smooth implementation of the project, timely delivery, and guarantee construction safety and quality.1.2 项目目标(Project Objectives)•完成商场工程的施工,按时交付。
•确保施工安全,遵循相关法规和标准。
•保证施工质量,符合设计要求和顾客期望。
•Complete the construction of the shopping mall and deliver it on time.•Ensure construction safety, following relevant regulations and standards.•Guarantee construction quality, meeting design requirements and customer expectations.2. 施工组织(Construction Organization)2.1 施工团队(Construction Team)我们将组建一个经验丰富的施工团队,包括工程管理人员、工程师、技术人员和施工工人。
幕墙施工方案 中英对照
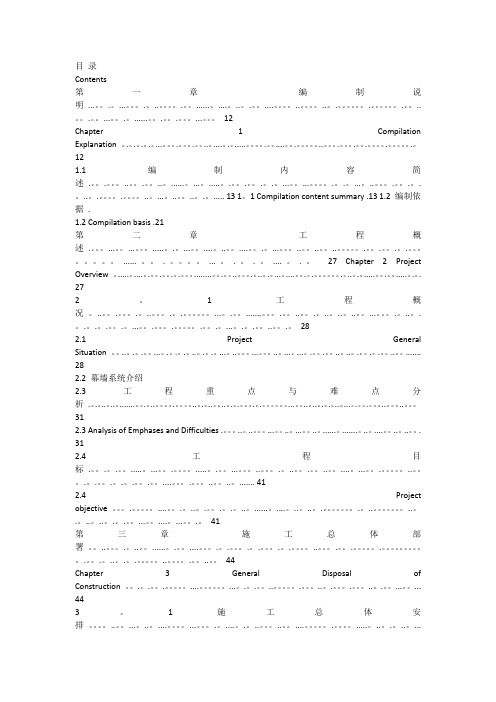
目录Contents第一章编制说明...。
.。
...。
.。
..。
.。
......。
....。
..。
.。
....。
..。
..。
.。
.。
.。
..。
.。
...。
.。
......。
.。
.。
...。
12Chapter 1 Compilation Explanation 。
.。
.。
.。
.。
...。
.。
.。
..。
....。
.。
.....。
.。
....。
.。
..。
.。
.。
.。
.。
.。
121.1 编制内容简述.。
.。
..。
.。
..。
......。
...。
.....。
.。
.。
.。
.。
...。
...。
.。
.。
...。
..。
.。
.。
.。
..。
.。
.。
..。
...。
..。
..。
.。
..... 13 1。
1 Compilation content summary .13 1.2 编制依据.1.2 Compilation basis .21第二章工程概述.。
...。
...。
.....。
.。
...。
....。
..。
....。
.。
...。
..。
..。
..。
.。
.。
.。
.。
......。
.。
...。
.。
.。
....。
.。
27 Chapter 2 Project Overview 。
.....。
....。
.。
.。
.。
.。
........。
.。
..。
.。
..。
.。
...。
....。
.。
.。
.。
..。
.。
.....。
.。
.....。
.。
.272。
1 工程概况。
..。
.。
.。
..。
.。
.。
...。
.。
.......。
.。
..。
.。
..。
..。
..。
...。
.。
..。
.。
.。
.。
.。
.。
...。
.。
.。
.。
.。
...。
.。
.。
..。
.。
282.1 Project General Situation 。
..。
.。
.。
...。
.。
.。
.。
..。
.。
.。
...。
..。
...。
..。
...。
...。
.。
.。
..。
..。
.。
.。
.。
..。
.......282.2 幕墙系统介绍2.3 工程重点与难点分析.。
.。
..。
..。
.......。
.。
..。
.。
项目改造施工方案(中英文版) 2

糖厂1×45t/h CFB锅炉改造方案The Upgrade Project of 1×45 t/h CFB Boiler一工程概况:1。
Project Overview本项目为一台1×45t/h CFB锅炉改造,其主要工程项目为:更换二次风机,引风机;对锅炉二次风管部分管道进行改造,增加二次风管风门调节阀,送料风调节阀,密封风调节阀,圆形碳钢给料管改为方形不锈钢给料管,螺旋给料机检查门改为快开式;This project is a renovation of 1 × 45t/h CFB boiler,and its main projects are as follows: to replace the secondary fan and induced—draft fan;to transform partial pipeline of boiler secondary air duct,to increase the throttle valve of secondary air duct,throttling valve of both the feeding airflow and the sealing airflow, to change the feeding pipe from round carbon—steel intosquare stainless and to change the inspection door of spiral feeder into quick-opening type。
100t/h大气热力式除氧器钢架与平台制作,安装一台100t/h大气热力式除氧器和一台Ø800连续排污器,增加锅筒连续排污装置;安装取样器4个,Fabrication of steel frame of 100 t/h atmospheric thermal deaerator and its platform;installation of a 100t / h atmospheric thermal deaerator and a Ø800 continuous blowdown device;increase of continuous blowdown device for boiler drum;and installation of four samplers。
中英文对照工程施工方案

第八章各分部分项工程的施工方案Chapter 8 Construction Scheme of Subprojects8.1 土建施工方案8.1 Civil Engineering Construction Scheme8.1.1 工程测量8.1.1 Engineering Surveying1)测量概述1) Measurement Overview为满足工程施工特点,该工程的测量控制网按照“从整体到局部,高精度控制低精度”的原则,由高到低设置三级控制网,各级控制网相互衔接,统一为整体系统。
In order to meet the characteristics of construction, the survey control networks of the project have three levels from high to low in accordance with the principle “From the whole to the part; High precision controls low precision”. Control networks at all levels should be connected, thus forming the overall system.1、测量注意事项1. Measurement Considerations建筑物占地面积超大,这对轴线控制网的布设和投测带来难度,需要充分利用高精度电子全站仪进行轴线控制网的布设及细部测量放线,钢尺作为辅助;轴线投测时,仪器要架设在建筑物两端,以减少投测误差。
As the buildings occupy a large area, which brings difficulty to the layout design and measurement of the axis control network, the electronic total station with high precision should be used to lay the network and do detailed survey with steel rulers as assistive devices. When transfer of building lines is conducted, instruments should be erected on both ends of the buildings to minimize measuring errors.2、测量前准备工作2. Preparations before measurement(1)、测量仪器检定:本工程使用的所用测量仪器及工具(包括专业分包的测量仪器)均应经国家计量单位检校合格并在有效时间之内。
桩基施工方案-中文英文对照
塞拉利昂水泥厂项目桩基施工方案Cement terminal project pile foundation construction program in Sierra Leone 一、旋挖成孔灌注桩施工Rotary drilling hole pile construction1.工程量1000M3砼The project amount 1000M3 concrete2.施工技术Construction Technology本工程项目桩基施工采用旋挖成孔工程钻机,在施工前须对场地进行清表、清障、平整、压实,使场地表面耐力不小于100Kpa。
施工时设置泥浆池、沉定池、泥浆循环系统和废浆池,沉淀池的容积两倍于一根桩的体积,储浆池容积大于16m3,以满足钻孔需要.Pile Foundation Construction of the project use a rotary drilling rig,before construction,we need to cleared the table , wrecker , leveling ,compaction venue to make sure the surface endurance is not less than 100Kpa.During construction,we need to set Mud pools , sedimentation tanks , mud circulation system and waste slurry pond。
To meet drilling demand,Sedimentation tank volume is twice the volume of a pile ,storage slurry pond volume should be greater than 16m33.工艺流程Process4.操作工艺Operation process(1)测量定位Measurement Positioning(a)采用全站仪按照图纸测定位置并做好标色。
施工方案_英文(3篇)
第1篇1. IntroductionThis construction project proposal aims to provide a comprehensive plan for the construction of a new office building in the city center. The project is expected to be completed within 18 months, with a total budget of $5 million. The following sections will outline the project scope, design, schedule, cost estimation, and risk management plan.2. Project Scope2.1 Project DescriptionThe project involves the construction of a new office building, which will be a seven-story structure with a total area of 30,000 square meters. The building will accommodate approximately 500 employees and will include the following facilities:- Reception area- Conference rooms- Office spaces- Restrooms- Breakout areas- Parking facilities2.2 Project Objectives- To construct a modern, sustainable office building that meets the needs of the company and its employees.- To ensure the safety and well-being of all workers on the construction site.- To complete the project within the specified budget and time frame.3. Design3.1 Architectural DesignThe architectural design of the building will be modern and functional, with a focus on sustainability and energy efficiency. The exterior of the building will be made of glass and steel, providing a sleek and contemporary look. The interior design will be spacious and comfortable, with natural lighting and ventilation to promote a healthy work environment.3.2 Structural DesignThe structural design of the building will be based on the latest engineering principles and will ensure the safety and stability of the structure. The building will be constructed using a reinforced concrete frame, with steel columns and beams to support the weight of the floors and roof. The foundation will be designed to withstand the seismic activity in the area.3.3 Mechanical, Electrical, and Plumbing (MEP) DesignThe MEP design will ensure that the building is equipped with the necessary systems for heating, ventilation, air conditioning, lighting, and power. The building will be equipped with a state-of-the-art energy management system to optimize energy consumption and reduce costs.4. Schedule4.1 Project PhasesThe project will be divided into the following phases:- Phase 1: Site preparation and foundation construction- Phase 2: Construction of the building structure- Phase 3: Installation of MEP systems- Phase 4: Finishing works and commissioning4.2 Project DurationThe total duration of the project is 18 months, with the following breakdown:- Phase 1: 3 months- Phase 2: 6 months- Phase 3: 3 months- Phase 4: 6 months5. Cost Estimation5.1 Direct CostsThe direct costs of the project include the following:- Labor: $2 million- Materials: $1.5 million- Equipment: $500,000- Contingency: $500,0005.2 Indirect CostsThe indirect costs of the project include the following:- Insurance: $200,000- Permits and fees: $100,000- Contingency: $200,0005.3 Total Project CostThe total project cost is $5 million, which includes both direct and indirect costs.6. Risk Management Plan6.1 Identification of RisksThe following risks have been identified for the project:- Construction delays- Material shortages- Labor disputes- Weather conditions- Design changes6.2 Risk Mitigation StrategiesTo mitigate the identified risks, the following strategies will be implemented:- Regular monitoring of the construction schedule to identify and address potential delays.- Maintaining a sufficient inventory of materials to avoid material shortages.- Establishing clear communication channels between the contractor and the labor force to prevent disputes.- Implementing a contingency plan to address weather-related delays.- Conducting regular design reviews to minimize the need for design changes.7. ConclusionThis construction project proposal outlines the scope, design, schedule, cost estimation, and risk management plan for the construction of a new office building. The project is expected to be completed within 18 months and will provide a modern, sustainable work environment for the company and its employees. By following the outlined plan and implementing the risk management strategies, the project is expected to be completed on time and within budget.第2篇1. IntroductionThis construction project proposal aims to provide a comprehensive plan for the construction of a new office building in the city center. The project will be carried out by XYZ Construction Company, which has extensive experience in the construction industry. This proposaloutlines the project objectives, scope, methodology, schedule, and budget.2. Project ObjectivesThe primary objective of this project is to construct a new office building that meets the requirements of the client, providing a modern, functional, and aesthetically pleasing workspace. The following specific objectives are set:- To ensure the project is completed within the agreed timeframe.- To adhere to the specified budget and quality standards.- To minimize disruptions to the client's business during construction.- To maintain a safe and healthy work environment for all stakeholders.3. Project ScopeThe project scope includes the following:- Design and construction of a new office building with a total area of 10,000 square meters.- Construction of parking facilities for 200 vehicles.- Installation of all necessary mechanical, electrical, and plumbing systems.- Landscape design and implementation.4. MethodologyThe construction methodology will be based on the following principles:- Phased construction to minimize disruption to the client's business.- Use of modern construction techniques and materials to ensure quality and efficiency.- Regular communication with the client and stakeholders to ensure their satisfaction and address any concerns promptly.5. Project ScheduleThe project schedule is divided into several phases:- Phase 1: Design and approval (3 months)- Phase 2: Construction of foundation and superstructure (12 months)- Phase 3: Installation of mechanical, electrical, and plumbing systems (6 months)- Phase 4: Landscape design and implementation (3 months)- Phase 5: Final touches and handover (2 months)The total duration of the project is 26 months.6. BudgetThe estimated budget for the project is as follows:- Design and approval: $500,000- Construction of foundation and superstructure: $5,000,000- Installation of mechanical, electrical, and plumbing systems:$2,000,000- Landscape design and implementation: $500,000- Contingency: $1,000,000Total estimated budget: $9,500,0007. Quality ControlTo ensure the quality of the construction, XYZ Construction Company will implement the following quality control measures:- Regular site inspections by a qualified project manager and engineer.- Third-party quality assurance inspections at critical stages of the project.- Use of high-quality materials and equipment.- Compliance with local building codes and standards.8. Safety and HealthXYZ Construction Company is committed to providing a safe and healthy work environment for all stakeholders. The following safety and health measures will be implemented:- Compliance with all relevant local and national safety regulations.- Provision of safety training for all workers.- Regular safety audits and risk assessments.- Implementation of emergency response plans.9. CommunicationRegular communication with the client and stakeholders will be maintained throughout the project. The following communication channels will be used:- Project meetings: Held bi-weekly to discuss progress, address concerns, and make decisions.- Progress reports: Sent weekly to provide an overview of the project's status.- Email and phone calls: Used for daily communication and quick responses to inquiries.10. ConclusionThis construction project proposal outlines the plan for theconstruction of a new office building in the city center. XYZ Construction Company is confident in its ability to deliver a high-quality, on-time, and within-budget project. By following the proposed methodology, schedule, and budget, we are committed to achieving the project objectives and ensuring the satisfaction of our client and stakeholders.第3篇Project Title: Residential Complex DevelopmentClient: XYZ Real Estate DevelopersLocation: City Center, Metropolitan CityProject Duration: 24 Months1. IntroductionThis document outlines the construction project proposal for the development of a residential complex in the city center of Metropolitan City. The project aims to provide high-quality residential units that cater to the diverse needs of the urban population. The proposal includes a detailed description of the project scope, design, methodology, timeline, and cost estimation.2. Project ScopeThe residential complex will consist of the following components:- Residential Buildings: Eight residential buildings, each with 12 floors, totaling 96 units.- Parking Facilities: A parking structure with 200 parking spaces for residents and visitors.- Common Areas: Clubhouse, swimming pool, gymnasium, children's play area, and landscaped gardens.- Supporting Infrastructure: Electrical, plumbing, and HVAC systems, along with fire safety and security measures.3. Design and ArchitectureThe architectural design of the residential complex will be modern and contemporary, with a focus on sustainability and energy efficiency. The buildings will feature:- Energy-Efficient Design: High-performance glass facades, solar panels, and green roofs to reduce energy consumption.- Spacious Living Spaces: Open floor plans with large windows to maximize natural light and ventilation.- Quality Finishes: Premium materials and finishes for durability and aesthetic appeal.- Accessibility: Elevators and ramps for disabled access, along with ample storage spaces.4. Construction MethodologyThe construction methodology will follow a phased approach to ensure efficient progress and minimize disruption. The following steps will be implemented:4.1. Pre-construction Phase- Site Survey and Analysis: Conduct a thorough site survey to assesssoil conditions, topography, and existing utilities.- Design Approval: Finalize the architectural and engineering designs with the client and relevant authorities.- Contractor Selection: Shortlist and select qualified contractors for various construction activities.- Material Procurement: Source high-quality construction materials from reputable suppliers.4.2. Site Preparation Phase- Clearing and Grading: Clear the site of debris and vegetation, and grade the land to create a level surface.- Utility Connections: Establish connections for water, electricity, and gas supply.- Temporary Infrastructure: Set up temporary construction facilities, such as fencing, lighting, and access roads.4.3. Construction Phase- Foundations: Construct the foundations using reinforced concrete to ensure stability and durability.- Structural Framing: Erect the steel and concrete frames for the buildings.- Building Envelope: Install the facades, roof, and windows.- Interior Finishing: Complete the interior finishes, including walls, floors, and ceilings.- Mechanical, Electrical, and Plumbing (MEP): Install HVAC, electrical, and plumbing systems.- Landscaping: Develop the common areas, including gardens, swimming pool, and playgrounds.4.4. Post-construction Phase- Quality Assurance: Conduct inspections and tests to ensure compliance with design specifications and quality standards.- Final Handover: Complete all construction activities and hand over the residential complex to the client.- Maintenance and Support: Provide ongoing maintenance and support services for the first year post-handover.5. Project TimelineThe project is scheduled to be completed in 24 months, with thefollowing milestones:- Month 1-3: Pre-construction phase (site survey, design approval, contractor selection, material procurement).- Month 4-12: Site preparation phase (clearing, grading, utility connections, temporary infrastructure).- Month 13-24: Construction phase (foundations, structural framing, building envelope, interior finishing, MEP, landscaping).- Month 25-26: Post-construction phase (quality assurance, final handover, maintenance and support).6. Cost EstimationThe estimated cost of the project is as follows:- Land Acquisition: $5,000,000- Architectural and Engineering Fees: $1,200,000- Construction Costs: $30,000,000- Material Costs: $5,000,000- Contingency and Contingency: $2,000,000- Total Cost: $53,200,0007. ConclusionThis construction project proposal outlines the detailed plan for the development of a residential complex in the city center of Metropolitan City. The project aims to deliver high-quality, energy-efficient, and sustainable residential units that meet the needs of the urban population. By following a phased construction methodology and adhering to stringent quality standards, the project is expected to be completed successfully within the specified timeline and budget.We look forward to the opportunity to work with XYZ Real Estate Developers and contribute to the successful completion of this prestigious project.。
保温施工方案 中英文对照版SPECIFICATION FOR HOT INSULATION
2.2 Preparation
Prior to the installation of insulation all steel surfaces shall be dry, clean and free from grease, and dirt. Partially insulated surfaces shall be fully painted, and fully insulated surfaces shall be fully primed, in accordance with *****-ED-N-0001.
1.2 本说明书不应用在由制造商(机械,阀门等)提供的成套设备。
1.3 该规范涵盖了热保温的最低技术要求,包括热环境的容器、热交换器,仪 器仪表保温和操作温度范围 0℃至 600℃的管道。它的目的是与项目有关的 所有项目中使用。
1.4 In this specification the word “shall” indicates a requirement that is to be adopted in order to comply with the specification while the word “should” indicates recommended practice.
1.0 SCOPE 2.0 TECHNICAL REQUIREMENTS
2.1 Workmanship 2.2 Preparation 2.3 Testing 2.4 Extent of Insulation 2.5 Selection of Materials 2.6 Thickness of Insulation 2.7 Application 2.8 Appendices
施工部署中英文对照版050110(金陵)
第三章施工部署Chapter III Construction Arrangement1.0 施工总体部署General construction arrangement(一)指导方针Guiding principles全面控制持续创新诚挚服务顾客满意All-round control, sustained innovation, cordial service, and satisfaction to customers——是全体员工信守的准则is the guideline abided by the whole staff (二)施工部署Construction Arrangement(1)执行国家建委基本建设项目经理管理法,并贯彻公司对项目工程实行项目总承包的原则,项目经理部统一组织对内、对外的协调指挥,集中公司优势力量,组织会战。
在合同工期内,高速、安全、优质建成该项目,确保开车投产一次成功。
To enforce the Project Manager Administrative Law of Fundamental Construction Projects of the National Construction Committee, and implement the principle that the company acts as the overall contractor of project construction works. The project manager shall be responsible to organize the internal and external coordination and commanding works in unison, and concentrate superior forces on the construction, so as to complete this project quickly, safely, with high quality and within the contracted construction period, and to ensure the success start-up and operation in single time.(2)在现场附近就近设置储罐预制厂,以减少运输工作量,最大限度为本工程服务。
- 1、下载文档前请自行甄别文档内容的完整性,平台不提供额外的编辑、内容补充、找答案等附加服务。
- 2、"仅部分预览"的文档,不可在线预览部分如存在完整性等问题,可反馈申请退款(可完整预览的文档不适用该条件!)。
- 3、如文档侵犯您的权益,请联系客服反馈,我们会尽快为您处理(人工客服工作时间:9:00-18:30)。
中英文对照施工方案目录Contents1. 工程概况 General2. 编制依据 References3. 施工顺序 Construction Sequence4. 施工方法 Construction Method5. 安全与环境保护施工措施 HSE6. 劳动力计划 Manpower Mob. Schedule7. 机具计划 Equipment/Tools Mob. Schedule8. 施工作业计划 Construction Schedule1. 工程概况General该项目为珠海PTA二期工程,本方案主要是为PTA二期变电所结构而编制的施工技术措施。
主体结构三层钢筋砼框架,局部为二层钢筋砼框架结构,变压器区域采用钢筋砼墙体。
This method statement is compiled to describe the substation structure construction method of Zhuhai PTA No.2 Project, which major structure is three-layer reinforced concrete frame and partial structure is two-layer reinforced concrete frame and transformer area is reinforced concrete wall.2. 编制依据References2.1. 施工图纸Construction Drawings REV.2 6092-BCO.01-DW-1741-01 to 252.2 工程测量规范Code for Engineering Surveying GB50026-932.3 混凝土结构工程施工质量验收规范Code for Quality Acceptance for Concrete Structure GB50204-20022.4 混凝土泵送技术规程Technical Codes for Concrete Casting by Concrete Pump JGJ/T10-952.5 建筑工程施工质量验收统一标准Unified Standard for Construction Quality Acceptance of Construction GB50300-20012.6 钢筋焊接及验收规程Code for Acceptance of Re-bar Welding JGJ18-20032.7 建筑施工高处作业安全技术规范Safety Technical Code for Work at Height During Construction JGJ80-912.8 施工现场临时用电安全技术规范Electricity Safety Technical Code for Temporary Power Supply on Construction Site JGJ46-88 2.9 混凝土强度检验评定标准Assessment and Acceptance for Concrete Strength GBJ107-873. 施工顺序Construction Sequence4. 施工方法Construction Method4.1脚手架工程Scaffolding work4.1.1 框架外的双排脚手架由架业公司搭设。
Double scaffold outside the structure will be built by scaffolding company.4.1.2梁和板底搭设满堂脚手架。
脚手架立杆基土应平整、密实,且所有立杆底部应加设宽度大于200mm,厚度大于50mm,长度4m的垫木。
Full scaffold shall be used for beam and slab bottom. Pole foundation soil shall level and dense, and size more than 4m(L)×200mm(W)×50mm(T) wood block shall be set for all pole bottom。
4.1.3满堂脚手架的立杆间距1.2m,横杆间距为1.6m。
每隔12m设置一道剪力撑。
搭设方法见下图。
立杆与纵、横向扫地杆连接固定,纵横向立杆应在同一条直线;纵、横杆搭接接头不要大于50%,即杆件接头要错位搭接。
立杆搭设时应通过吊垂线保证其垂直度,垂直误差不得大于20mm。
Spacing between poles of full scaffold is 1.2m, and set cross bridging for every 12m, and method please see following sketch. Poles shall be erected as per the location, and fasten the poles with longitudinal and transverse bottom pole, and longitudinal and transverse poles shall be at the same straight line. Overlap junctions of longitudinal and transverse poles shall be not more than 50%, that is, pole junctions shall be overlapped staggered. Verticality shall be ensured by plumb line when, and tolerance of verticality shall be not more than 20mm.4.1.4端头各设置一道剪刀撑,每道连接不少于4根立杆,纵向轴线除两端各设置一道剪刀撑外,按间距12m设置剪刀撑;剪刀撑接长必须用搭接,且搭接长度不小于1m,转扣不少于3个,每组剪刀撑的宽度不小于4跨,且不小于6m,斜杆与地面的夹角45°~60°Cross bridging shall be installed at the ends of transverse axis, and each connection shall be not less than four poles. Besides cross bridging installed at the ends of the longitudinal axis, it also installed as per 12m spacing. Overlap must be used for cross bridging spreading, and overlap length shall be not less than 1m, and rotary button shall be less than three, and each cross bri dging’s width shall be not less than four spans and shall be not less than 6m. Separation angle between diagonal pole and ground is 45°~60°.4.1.5 脚手架平面布置及上下通道平面位置见附图1。
Make the sketch for detail plane of scaffolding including access way. Please see sketch No.-1.4.1.6脚手架搭设好后,必须经过IPMT/CFCS/HSSE验收合格后方可投入使用。
After completion of scaffolding work, it must be inspected and accepted by IPMT/CFCS/HSSE.4.2模板工程Formwork4.2.1梁、柱和墙板采用δ=18mm的胶合模,板采用组合钢模板。
φ48*3.5的标准脚手架钢管加固。
模板安装前,应将模板面残留砼清理干净、且在钢模板上均匀涂刷隔离剂。
δ=18mm plywood form shall be used for beam, column and wall, and combined form shall be used for base slab, and reinforced by φ48*3.5scaffold steel pipe. Forms shall be cleaned and remove the residual concrete, and also separant shall be painted on the steel form evenly before form installation.4.2.2柱模板Column form1)安装顺序:柱轴线投点、放支模线→搭设柱四周井字架→控制标高→绑扎柱钢筋、墙拉结筋、安放钢筋保护层垫块→拼装柱模板→柱模板校正并加固In stallation sequence: mark out the column axis and form line→build “井” shape rack around the column→control elevation→column rebar work, wall binding rebar work, install the cushion block→install the column form→column form adjustment and reinforcement2)将柱轴线、标高线复测投点,弹出柱支模线,将柱脚支模处用1:2 水泥砂浆找平,每根柱周围搭设井字架,在井字架上抄测标高控制线。
Resurvey the column axis and elevation line, and mark out the column form line, 1:2 cement mortar will be used to leveling at the column bottom. “井” shape rack will be set around each column, and mark elevation control line on it.3)绑扎柱筋,垫保护层垫块,安放埋件、墙拉结筋。