道路施工方案中英文IV Construction Method
【施工方案】中英文对照施工方案
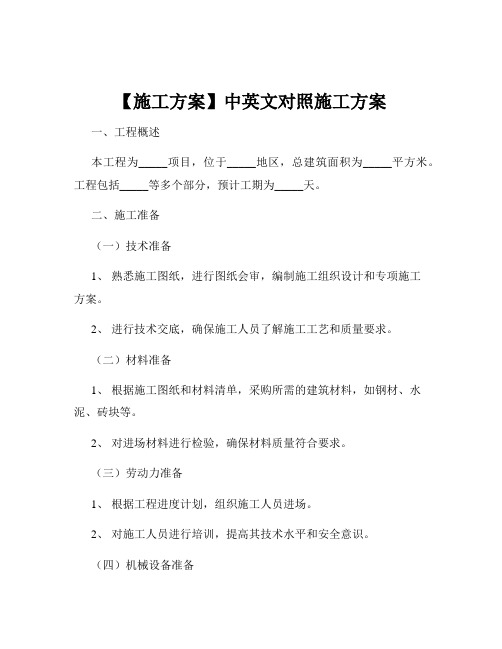
【施工方案】中英文对照施工方案一、工程概述本工程为_____项目,位于_____地区,总建筑面积为_____平方米。
工程包括_____等多个部分,预计工期为_____天。
二、施工准备(一)技术准备1、熟悉施工图纸,进行图纸会审,编制施工组织设计和专项施工方案。
2、进行技术交底,确保施工人员了解施工工艺和质量要求。
(二)材料准备1、根据施工图纸和材料清单,采购所需的建筑材料,如钢材、水泥、砖块等。
2、对进场材料进行检验,确保材料质量符合要求。
(三)劳动力准备1、根据工程进度计划,组织施工人员进场。
2、对施工人员进行培训,提高其技术水平和安全意识。
(四)机械设备准备1、配备所需的施工机械设备,如塔吊、搅拌机、电焊机等。
2、对机械设备进行调试和维护,确保其正常运行。
三、施工流程(一)基础工程1、土方开挖根据设计要求和地质条件,确定土方开挖方案。
采用机械开挖和人工清理相结合的方式,确保基底平整。
2、基础钢筋绑扎按照设计图纸,进行基础钢筋的加工和绑扎。
保证钢筋的规格、数量和间距符合要求。
3、基础混凝土浇筑浇筑前,清理基底杂物和积水。
采用商品混凝土,分层浇筑,振捣密实。
(二)主体结构工程1、钢筋工程钢筋加工在现场进行,严格按照设计要求和规范进行。
柱、梁、板钢筋的绑扎要牢固,位置准确。
2、模板工程选用合适的模板材料,如木模板、钢模板等。
模板安装要牢固,拼缝严密,防止漏浆。
3、混凝土工程混凝土搅拌要均匀,严格控制配合比。
浇筑时,要注意分层浇筑和振捣,避免出现蜂窝、麻面等质量问题。
(三)装饰装修工程1、内外墙抹灰基层处理要干净,浇水湿润。
抹灰要平整,厚度均匀,无空鼓、裂缝。
2、地面工程基层平整、牢固,无杂物。
地砖铺设要平整,缝隙均匀,颜色一致。
3、门窗工程门窗框安装要牢固,位置准确。
门窗扇安装要灵活,关闭严密。
四、质量控制措施(一)建立质量管理体系成立质量管理小组,明确各部门和人员的质量职责。
(二)加强原材料和构配件的质量控制对进场的原材料和构配件进行严格检验,不合格的产品不得使用。
新修马路施工计划范本
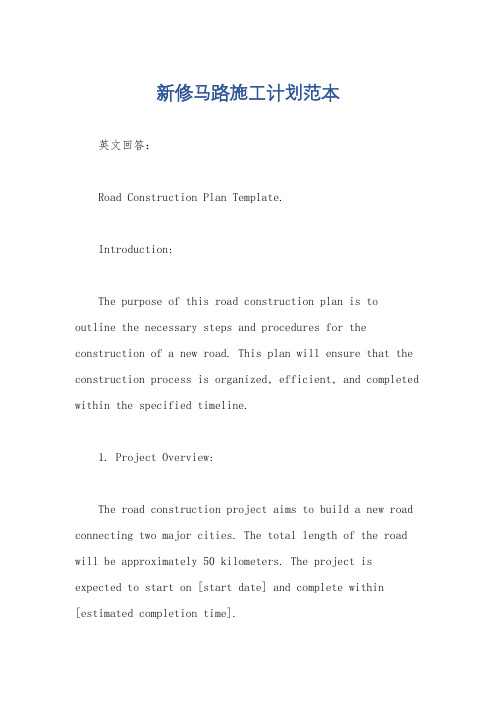
新修马路施工计划范本英文回答:Road Construction Plan Template.Introduction:The purpose of this road construction plan is tooutline the necessary steps and procedures for the construction of a new road. This plan will ensure that the construction process is organized, efficient, and completed within the specified timeline.1. Project Overview:The road construction project aims to build a new road connecting two major cities. The total length of the road will be approximately 50 kilometers. The project is expected to start on [start date] and complete within [estimated completion time].2. Site Preparation:Before commencing the construction work, site preparation activities need to be carried out. Thisincludes clearing the land, removing any existing structures, and leveling the ground. Site preparation will begin [start date] and is estimated to be completed within [estimated duration].3. Earthwork and Grading:The next step in the construction process is earthwork and grading. This involves excavating the soil, levelingthe ground, and creating a stable foundation for the road. Earthwork and grading activities will start on [start date] and are expected to be finished within [estimated duration].4. Drainage System Installation:To ensure proper water flow and prevent flooding, a drainage system will be installed along the road. Thisincludes the construction of culverts, ditches, and stormwater drains. The installation of the drainage system will begin on [start date] and is estimated to be completed within [estimated duration].5. Road Construction:The actual construction of the road will involve laying the base, sub-base, and wearing course layers. This will be done using appropriate construction materials such as asphalt or concrete. Road construction activities willstart on [start date] and are expected to be finishedwithin [estimated duration].6. Signage and Markings:Once the road is constructed, signage and markings will be installed for proper guidance and safety. This includes road signs, lane markings, and pedestrian crossings. Signage and marking activities will begin on [start date] and are estimated to be completed within [estimated duration].7. Quality Control and Inspection:Throughout the construction process, regular quality control and inspection will be conducted to ensure that the road meets the required standards. This will involvetesting the materials, checking the road's alignment, and monitoring the construction activities. Quality control and inspection activities will be carried out continuouslyuntil the completion of the project.Conclusion:This road construction plan provides a comprehensive outline of the necessary steps and procedures for the construction of a new road. By following this plan, we can ensure that the construction process is well-organized, efficient, and completed within the specified timeline.中文回答:马路施工计划范本。
Method Statement for Road Works (道路施工方案英文)

METHOD STATEMENT FOR ROAD WORKSTABLE OF CONTENTS1.0 SCOPEThe purpose of this Method Statement is to describe the Methodology involved in construction of Road Works in accordance with project technical specifications, international standards and codes, local rules and regulations (QCS-2010). This method statement will cover the following works:❖Earth Works Preparation to Road Formation❖Granular Sub-base Preparation Works❖Asphalt Works2.0 PERMITS AND LICENSESThe Permits and License required for commencement of the work shall be obtained prior starting any site activities, the permits and license shall be obtained from the Following:❖Electricity and Water Authority❖Tel-communication Operator❖Municipality Government❖Ministry of Environment❖Public Work Authority (Roads)3.0 SEQUENCE OF WORKS FOR ROADS3.1 Site preparation❖Prior to commencement of work, the contractor shall obtain the relevant work permits from Client❖The contractor shall under take clearing of site in order to remove any existing vegetation; steel, concrete, unused buildings identified for demolition, piping debris, loose windblown sand and other foreign materials.❖All existing structures, foundations, etc. as indicated above shall be entirely demolished, removed, transported and disposed of by the contractor to a debris yard designated by Client. All soft spots left shall be filled with suitable material and compacted as perspecification.❖Excavated material, if any, and suitable and approved by Client for backfilling shall be transported and placed in fill areas within the limits of the work.3.2 Survey and Setting Out3.2.1 Survey Markers❖Survey Markers shall be durable, appropriate to location and intended use.❖Survey Markers shall be clearly identifiable and protected from construction traffic. For installation of a Survey Marker into reinforced concrete, the JV's will ensure that steel reinforcement bars are to be avoided.❖Either removable anchors or epoxy adhesive shall be used as the methods of fixing Benchmarks are a particular type of Survey Markers used in the control of elevation.❖Benchmarks shall have a domed surface for unambiguous staff placement. Primary Benchmarks shall comprise a stainless steel bolt securely placed vertically into aconcrete slab, or horizontally into a column.❖The protrusion shall not pose a safety hazard. Survey Markers used for horizontal control shall have an unambiguous point above (or below) which a survey instrument can be precisely centered.❖The point shall comprise either a punch mark or the intersection of 2 lines forming a cross. Cross-headed road nail (75mm long) complete with a colored washer shallgenerally be used as a Survey Marker.3.2.2 Control Observation, Adjustment and Presentation❖Homogeneous horizontal and vertical survey control is required prior to any setting out.Survey control shall evolve from the whole to the parts. Where practical, all survey points within a horizontal survey control network shall be occupied and observed from.❖Forced centering techniques shall be used throughout. A round of angular observations shall comprise the mean of observations taken on both faces of the total station. A minimum number of 4 rounds of horizontal and vertical angles shall be observed at each instrument set up.❖For control work, the angular spread of horizontal angles shall not exceed 3’’ of arc.Distances shall be measured in both directions. All raw data pertaining to each set up shall be electronically recorded. Survey control shall include redundant observations.Observation networks shall be processed using the method of least squaresadjustment and the resulting residuals to the observations shall be inspected formagnitude.❖Any large residuals or error ellipses shall be examined and appropriate remedial action shall be taken. Precise leveling shall be double run using equal back and fore sights at each instrument set up. Leveling sights shall never exceed 30 meters. On the ground surface, the Contractor shall establish stable bench marks adjacent to the site so that the distance between adjacent benchmarks does not exceed 250 meters.❖Height datum transfer accuracy shall be better than 2mm in a 30m deep shaft. The transfer of height datum shall be by various independent means. azimuth transfer from surface to underground shall be better than 3“ of arc and point transfer shall beaccurate to within 2mm. Such transfers shall be by various independent means.❖ At 3 month intervals, the Contractor shall conduct a complete survey of all existing survey control. A bound, A4 size survey control report shall be submitted to theEngineer for acceptance within 2 weeks of completing the field work.❖The convention adopted shall comprise Station Name, Easting, Easting, Northing and Elevation reading from left to right report shall contain the following information report shall contain the following information: dates of survey, fixed survey control and values, specification of instrumentation used, calibration status of instrumentation used,observational acceptance criteria, list offinal adjusted co-ordinates findings andconclusion.❖Attached to the report shall be the observations (A4 print out of electronic booking sheet or customized spread sheet), adjustment with residuals and station error ellipses, table of differences in mm from previous co-ordinates and elevations (if applicable),a drawing clearly showing layout of scheme and measured quantities and final co-ordinates in tabular form.3.2.3 General Setting Out❖The Contractor shall carry out a comprehensive level survey of the Contract area before any work commences on the site that may alter original ground levels.❖Pre-computation shall be carried out prior to any setting out. For rail projects, the effects of cant and throw shall be incorporated into pre-computation wherever relevant.❖ All pre-computation shall be readily available in a spread sheet format for use on site.The method of setting out for each particular element of the work shall commensurate with the required accuracy, the method of construction, and shall be appropriate for site conditions.❖In the setting out process, all elevation transfer conducted by leveling shall start on an established benchmark and finish on a different benchmark. If a significant disclosure is detected, the reason shall be determined and the necessary corrective action taken.❖After the erection of the formwork and prior to concreting, a survey check shall be carried out on the formwork to ensure that the setting out has been done correctly.❖ A spreadsheet shall be used in all instances to tabulate the difference (or offset) in mm between the actual set out (or as-built) co-ordinates from the design co-ordinates. In cases where the design is an alignment, offsets to the alignment shall be computed for each surveyed point.3.3Earth Works3.3.1Earthwork General❖The JV will carry out all earth work in such a manner as to prevent erosion or slips and shall limit working faces to safe slopes and height.❖The JV will ensure that all surfaces have at all times sufficient gradients to enable them to shed water without causing erosion.❖Hauling of material from cuttings or the importation of fill material to the embankments or other areas of fill shall proceed only when sufficient compaction plant is operating at the place of deposition to ensure compliance with the requirements of Client.❖Construction traffic other than that required for the excavation and trimming shall not use the surface of the bottom of a cutting unless the cutting is in Rock or the Contractor maintains the level of the bottom surface at least 300 mm above formation level.❖Any damage to the sub-grade arising from such use of the surface shall be made good by the Contractor at his own expense with material having the same characteristics as the material which has been damaged.❖The JV will arrange for the rapid dispersal of water shed on to the earth works or completed formation during construction, or which enters the earth works from any source❖The JV will provide where necessary temporary water courses, ditches, drains, pumping or other means of maintaining the earth works free from water❖The JV will take special care that naturally occurring materials within the site are not rendered unsuitable by his method of working. Areas of cuttings and excavation shall be so worked that rainfall is conducted rapidly away from the exposed material and at times of expected heavy rain that the cutting areas are protected by appropriatemethods of working and drainage provisions.3.3.2Classification of Earth Work MaterialThe following definitions of earth works shall apply to this and other clauses of the Specification in which reference is made to the definitions:❖ Top Soil' shall mean the top layer of soil that can support vegetation.❖ Suitable Material' shall comprise all that is acceptable in accordance with the Contract for use in the works and which is capable of being compacted in the manner specified in project Technical Specifications to form a stable fill having side slopes as indicated on the drawings.❖ Not Suitable Material' shall mean other than suitable material and shall include :•Material from swamps, marshes or bogs;•Peat, logs, stumps or other organic matter and perishable and toxic materials;•Material susceptible to spontaneous combustion.•Clay of liquid limit exceeding 80 and/or plasticity index exceeding 55.❖‘Rock' shall mean hard material found in ledges or masses in its original position,which would normally have to be loosened either by blasting or by pneumatic tools, or if excavated by hand, by wedges and sledge hammers. ‘Rock’ shall also includeall solid boulders or detached pieces of rock exceeding 0.10 m 3 in size in trenchesor exceeding 0.20 m 3 in general excavation.3.3.3 Excavation❖Excavation will be carried out to the dimensions, lines, levels and slopes as indicated on the IFC Drawings.❖If the JV excavates deeper than the depths shown on the Drawings or as instructed by the Client, then he shall fill in such excessive depths with acceptable materials to the satisfaction of the Client.❖The bottom of all excavations shall be free from mud and water, trimmed clean, protected from the effects of weather and thoroughly compacted and consolidated❖The JV will be responsible to excavate to the top of soft or defective soil below the formation level and backfill with Suitable Material. Such backfill will be well compacted in layers of accepted thickness by approved manners and means.3.3.4Cuttings and Cut Slopes❖Unless otherwise specified, no portion of the earth cutting shall vary from the specified or ordered formation level by an amount exceeding 150mm.❖In the case of cut slopes, no portion of the completed slope shall vary by an amount exceeding 100mm (measured at right angles to the slope).In all cuttings, whether in earth or rock, undulations in the general plane of the slope will not be permitted.Unless otherwise specified, excavation in rock shall extend to at least150mm below the specified formation level and backfilled with approved materials.❖Any overhanging, loose or unstable material shall be removed. The excavation shall be so arranged that the working areas are adequately drained throughout the period of construction.❖In cutting where the strata consists of earth overlaying rock which is required to be cut to a slope of 1 (H): 2 (V) or steeper, the face of the rock shall be given its appropriate slope up to the junction of the rock and earth and the latter shall be stripped to form a bench 900mm wide and sloped to the gradient as specified.3.3.5Maintenance of Excavated Area❖ Continuously monitor the dimensions / level of excavation to avoid over Cutting if any accidental over cutting takes place, fill and compact with Suitable material to thedesired level.❖ Remove any undesirable material (vegetation, organic soils etc.)Encountered duringexcavation and fill with approved granular material.❖ Take necessary measures to keep the excavation free from water by De-wateringwherever required.❖ Arrange shoring so that it does not interfere with the progress of work andFunctioning of nearby facilities as work proceeds, remove the shoring carefullywithout causingany danger to the excavation.❖ If any accidental slips or settlement occurs in the excavated area, Properly fill byselected fill or with mass concrete.3.3.6Sloping the Sides of Excavation❖ Wherever there are chances of sliding, properly slope sides of Excavation.❖ Trim the slopes by hand to uniform batters as shown on the IFC Drawings.❖ Trim any rock or boulder appearing in the face of the slope, and remove italtogether, if it seems unstable.❖ If any rock is removed, fill the resulting void with compacted material.❖‘Imported Rock Fill' shall be clean well-graded quarry waste provided by the Contractor from sources outside the Site. It shall be resistant to weathering, to the acceptance of the Client.❖ The maximum size particles in the material shall pass through a rigid 200mm square grid and the largest dimension of any particle shall not exceed 300 mm. The material shall not have more than 10% of its particles passinga0.75 mm BS sieve.❖‘Fill Material' shall mean Suitable Material for backfilling with the exc eption of Rock and Imported Rock Fill❖‘Special Fill Material’ shall mean Suitable Material of which at least 95 per cent shall pass a 125mm BS sieve and at least 90 percent shall pass the 75mm BS sieve. Up to 5 per cent of the material may be made up from isolated boulders of maximum dimensions not exceeding half the thickness of the layer of material being placed.Liquid limit not exceeding 35❖plasticity index not exceeding 12(h) ‘Selected Fill' shall be well graded granular natural sands, gravel, crushed rock, crushed concrete, well burnt shale or othermaterialsaccepted by the Client. The material passing a 425 micron BS sieve, when tested inaccordance with BS 1377, shall have a plasticity index of less than 6%.❖‘Imported Fill Material' shall be Fill Material supplied by the Contractor from a source outside the Site and accepted by the Client's.3.3.7 Compacting and Levelling the Fill❖ During compaction, maintain the M.C of fill material, usually +/- 3 Percent of OMC. If Required, add clean water to the fill material in order To maintain the necessary M.C❖ Achieve minimum density of specified M.D.D. of soil, by using roller / Plate compactor or any other approved equipment.❖ Around new (or existing remaining) concrete foundations or other Substructures do Not compact by rolling. Instead, use mechanical Rammers or plate compactors to Compact the space in vicinity of Concrete structure.❖ After compaction, level the surface free from undulations using suitable Equipment.3.4 Materials forSub-base3.4.1Fine Aggregate for Sub-Base❖Fine aggregate (Passing the 4.75 mm sieve) shall consist of crushed mineral aggregate and/or natural sand.❖The fine aggregate shall be clean and free from organic matter, clay — balks and other extraneous or detrimental materials.❖The ratio of aggregates passing the 0.075 ram sieve shall not exceed 66% of the portion passing the 0.425 mm sieve.❖The material passing the 0.425 mm sieve shallhave a maximum liquid limit of 25% and the plasticity index shall not exceed 6%.Where the source of fine aggregate does not meet the above requirements, with the Engineer's approval, add fine aggregate and filler to correct the gradation or to change the characteristics of the material passing the 0.42 mm sieve so as to meet the requirements. Such additional material shall be added in a manner which ensures a completely homogeneous material3.4.2Coarse Aggregate for Sub-Base❖Coarse aggregate (retained on the 4.75 mm sieve) shall consist of crushed stone crushed gravel with minimum of 50% by weight having at least one fractured face.❖The flakiness index of the aggregate shallnot exceed 35% when tested in accordance with BS 812.❖The Los Angeles Abrasion Loss, as defined by ASTM C131/C535, shallbe 40% maximum.❖The aggregate type for the sub-base shall be crushed limestone.170-7.5.66 ❖The coarse aggregate shall be hard and durable and free from organic matter, clay and other extraneous or detrimental materials.❖Coarse aggregate shall have a maximumloss of 20% by the magnesium sulphate soundness test when performed as per ASTM C88 for 5 cycles.❖The minimum CBR value obtained when preparing samples of aggregate base and aggregate Sub-base at optimum moisture content and at 100% relativecompaction and soaking them for 4 days shall be 80% and 60%; respectively. The maximum permitted swell shall he 0.5% and 1.0%; respectively3.4.3 Mix Design for Sub-base❖ Aggregates sub-base shall consist of crashed mineral aggregates or natural mineral aggregates of the designated gradation and thickness.❖The maximum dry density and the Optimum moisture content of the material shall ascertained as per the test procedure given in CML 12- 97 andthis shall beused to assess the degree of compaction of the mix after rolling❖The pavement layer designated as sub-base, the material shall conform to Class B or Class C❖The particle size shall be determined by the washing and sieving method of BS 812: Part. 103.❖Fine and coarse aggregates for sub-base shall be combined gradation of material that meets the requirements of the specification for density and other properties,❖The aggregate bases shall conform to the class A or class B gradation and the aggregate sub-base shall conform to the class C gradation, as given in the following Table:❖Immediately comply with such instructions without being entitled to any indemnities or extensions as a result of such instructions. Any equipment or plant shall not be used beforeobtainingthe approval of the Client and to engage skilled And trained operators, mechanics and labour to carry out the works.3.5 Plant Generally❖ The machinery and tools used in constructing the various items involved in asphaltworks shall be in good workingcondition and free of oil and fuel leaks This variousitems shall be maintained and preserved for the whole duration of the work. TheClient shall approve the machinery and tools before works begin and supply of such machinery with adequate quantities in order to execute the work with due speed and precision.❖ For the Client if required, the manufacturer's catalogues, specifications and other published data for the equipment and machinery shall be supplied.❖ On first erecting a batching plant and at least once each three months thereafter, the plant shall be calibrated by a calibration service organization approved by theCentral Materials Laboratory. Production shall not be permitted if the weigh batch calibration does not comply with the requirements of BS 5328.❖ The Client shall have the right to stop the use of any equipment or plant which he deems to be inferior to the quality required or detrimental to the permanent works and to instruct the removal of such equipment and to have it replaced by suitable equipment❖Immediately comply with such instructions without being entitled to any indemnities or extensions as a result of such instructions. Any equipment or plant shall not be used beforeobtainingthe approval of the Client and to engage skilled. And .trained operators, mechanics and labor to carry out the works.3.6 Inspection and Testing Control❖For verification of plant weights and measures, character of materials used in the preparation of the mixes, testing and other quality control requirements, the Engineer shall at all times be provided access to all portions of the mixing plant, aggregate plant, storage yards, crushers and other facilities used for producing and processing the materials of construction❖The Engineer shall have authority to take samples and perform tests on any material supplied to the site from any source whatsoever in order to establish complianceandtoaccept or reject as he deems necessary. Samples shall also be taken from completedwork to determine compliance. The frequency of all sampling and testing shall be asdesignated by the Engineer.❖Suitable facilities at the quarry or plant shall be provided to carry out all necessarytests on the raw materials and mixes.❖For obtaining specimens of materials and samples taken from stockpiles shall be arranged, including the provision of any necessary equipment and plant. This work shall be performed in the presence of the Engineer if so directed by the Engineer.❖Materials that are not in compliance shall be rejected and removed immediately from the site of the works times otherwise instructed by the Engineer.❖Where defects in the material or the completed work have been corrected, until approval has been given by the Engineer subsequent work shall not proceed.❖Materials which require drying before performing any of the designated tests shall be dried out at temperatures not greater than 100 OC.3.7Installation Procedure for Sub-base❖Before commencing the construction of the sub-base, written approval for the Engineer must be obtained thatthe sub-grade is in compliance.❖Before starting the sub-base all the structures have to be installed like kerbs, dropped kerbs, barrier’s foundations, median b arriers, channel block andgully's pre-cast concrete part with road gully pot.❖If the naturalmoisture content is less than the optimum moisture content, the necessary amount of water must be added to obtain the optimum content.❖Allowance shall be made for the quantity of moisture which may be lost by evaporation in the process of raking, leveling and compacting, depending on atmospheric temperature❖The compacted layer shall have moisture content within. ±2% of the optimummoisture content.❖The moisture content shall be uniform in all parts of the section where the work is being carried out and in the various depths of the layer thicknessCompaction shall start immediately afterthe material has been laid.❖Work on the sub-base courses shall not continue during rainy weather.❖Material shall be spread as 2 layers to a thickness that would result in layers not more than 150 mm thick after compaction❖The course shall not be rolled when the underlying material is soft or yielding or when the rolling causes a wave like motion in this course.❖When the rolling develops irregularities, the irregular surface shall be loosened, then refilled with the same kind of material as used in constructing the course and again rolled.❖Rolling must continue until a relative density of not less than 100 % of the maximum dry density has been obtained as determined by the moisture density relationship in CML 12-97❖Care shall be taken so that layers already compacted under the layer being executed are not damage, or that the formation is not damaged❖Any such damage resulting in mixing the various layers constituting the different sub-grades and sub- base courses shall be carefully made good by our own expense and to the satisfaction of the Engineer.❖Any material that fails to meet test requirements shall either be reworked or removed and replaced and then retested to check for compliance. Also the corrective actions and protection shall be done accordance with QCS section 6 parts 4.7 and 4.8.❖All testing shall be can-led out in accordance with AASHTO T96, AASHTO T104 and the relevant parts of BS 1377 or CML Standard Methods of test❖The sub-base shall be compacted and tested for acceptance in accordance with SML 12-97 and BS 1377 to attain a minimum density of 100 % of the maximum city density ofthe material. Two tests every 500 m2 shall be carried out unless otherwise directed bythe Engineer.❖Whenever the degree of compaction is found to be less than required, the area of sub-base involved shall be satisfactorily corrected.❖The gradation of the placed material shall be checked by taking samples from an area0.5x0.5 m from the full depth of the layer for every 1000 m3 of laid material. Thegradation shall be tested in accordance with BS 812: Part 101❖Wherever the gradation is found to be outside the designated limits, the area of sub-baseinvolved shall be scarified, removed or reworked to provide a gradation incompliance.❖The final surfaces of the sub-base shallbe tested by means of a 4 meter long straightedge. And no rises or depressions in excess of 10 mm shall appear inthe surface.❖The finished surface shall be checked by dips or spot levels and shall be constructed to the designated grade levels to within ± 10 mm.❖Where these requirements are not met, the full extent of the area which is out of tolerance shall be determined and shall make good the surface of the course by scarifying to a minimum depth of 75 mm or4 times the maximum particle size. Whichever is greater, reshaping by adding or removing material as necessary, adding water if necessary and re-compacting.3.8 Protection of the Surface❖The sub-base course shall be protected sothat it shall be maintained sound during work progress, after its completion and before receiving the bituminous layers orbefore laying the surface overlay thereon.❖Any damage caused to the layer if exposed to traffic or natural conditions resulting in damage to its surface shall be made good according to the satisfaction of theEngineer.❖The Engineer has the right to stop all hauling over completed or partially completed sub-base course when there is any proof such hauling is causingdamage.❖Following the completion of the sub-base course, all maintenance work necessary shall be performed to keep the course in a condition for priming.3.9 Materials for Asphalt Work❖Fine aggregate is that portion of the mineral aggregate passing the 2.36 mmBS Sieve.❖Fine aggregate shall be non-plastic and chemically stable.❖Unless permitted elsewhere in the contract, the aggregate type for the wearing and intermediate courses shall be Gabbro.❖Fine aggregate shall be clean and free from organic matter, clay, cemented particles and other extraneous or detrimental materials.❖Sampling of fine aggregate shall be in accordance with BS 598 part 100.6❖Fine aggregate shall be consist of crushed hard durable rock and shall be of such Gradation that it will meet the required gradation Wadi beach or dune sand won't be Used.❖Individual stockpiles of crushed -fine ag g re g ate shall have a sand equivalent of not less than 30.❖The loss by the magnesium sulphate soundness test, as determined by ASTM C88, shall be a maximum of 18 %❖The maximum acid-soluble chloride content shall be 0.1% and the maximum acid- soluble sulphate content shall be 0.5 %.❖The fine aggregate shall havea maximum plasticity index of 4 % when sampled form stockpiles and shall be non-plastic when sampled from hot bins.3.10 Coarse Aggregate for Asphalt Work❖ Coarse aggregate is that portion of the mineral aggregate retained on the 2.36 mm BSSieve. Coarse aggregate shall consist of crushed natural stones and gravel. Crushedparticles shall be cubic and angular in shape and shall not be thin, flakyor elongated.❖ The source of crushed aggregate is considered to the crushing site from which it is produced. Sampling of coarse aggregate shall be in accordance with BS 598 : part 100.❖Coarse aggregate shall be clean and free from organic matter, clay, cemented particles and other extraneous or detrimental material The degree of crushingshallbe such that a minimum of 99 % by weight of aggregate (each stockpile) having at least one fractured face and 85 % having at least two fracturedfaces. No rounded or sub-rounded particles shall be used_ The flakinessindex (of each stockpile) shall not exceed 25 % for wearing course and 30 % for intermediate and base courses and the elongation index (of each stockpile) shall not exceed 25 % for the wearing course and 30 % for the intermediate and base courses.❖The loss by magnesium sulphate soundness test, as determined by ASTM C88, shall be a maximum of 10 % for aggregate used in wearing and intermediatecourses and a maximum of 15 % for aggregate used in base course.。
公路工程施工方案英语版

1. IntroductionThis project plan aims to outline the detailed construction process and procedures for the road construction project. The project involves constructing a new road with a total length of 10 kilometers, connecting two major cities. The road will have a two-lane design with a width of 12 meters, including two 3.5-meter-wide carriageways and two 1-meter-wide sidewalks. This project plan covers the pre-construction, construction, and post-construction phases.2. Pre-construction Phase2.1 Site Investigation and SurveyBefore the construction begins, a thorough site investigation and survey will be conducted. This will include geological, hydrological, and topographical studies to identify potential risks and challenges. The survey will provide accurate measurements of the existing terrain, water bodies, and infrastructure, which will be essential for the design and construction process.2.2 Design and ApprovalBased on the site investigation and survey results, a detailed design will be prepared, including road alignment, cross-section, and materials specifications. The design will be submitted to the relevant authorities for approval, ensuring compliance with local regulations and standards.2.3 Land Acquisition and DisplacementThe project team will work closely with the local government to acquire the necessary land for the road construction. Proper compensation and relocation plans will be developed for affected landowners and residents to minimize displacement and ensure their well-being.3. Construction Phase3.1 Excavation and GradingExcavation work will begin by removing the topsoil and any existing structures or obstacles. The site will be graded to achieve the desiredroad alignment and cross-section. Proper soil stabilization techniques will be employed to ensure stability and prevent erosion.3.2 Foundation ConstructionA stable foundation is crucial for the road's long-term performance. The construction team will lay a subgrade layer of compacted soil, followed by a base course of crushed stone. This layer will provide a solid foundation for the road surface.3.3 Road Surface ConstructionThe road surface will be constructed using asphalt concrete. The construction process includes the following steps:a. Subbase Preparation: The subbase will be compacted and leveled to ensure a stable foundation for the asphalt layer.b. Asphalt Mix Design: A suitable asphalt mix design will be developed based on traffic volume, climate, and other factors.c. Bitumen Application: Bitumen will be applied to the subbase to ensure proper adhesion between layers.d. Asphalt Paving: The asphalt mix will be laid and compacted using pavers and rollers to achieve the desired thickness and smoothness.e. Surface Treatment: Optional surface treatments, such assealcoating or chipseal, may be applied to enhance the road's longevity and skid resistance.3.4 Drainage and Safety MeasuresProper drainage systems will be installed to prevent water accumulation on the road surface. This includes the construction of culverts, ditches, and stormwater management facilities. Safety measures, such as guardrails, signage, and lighting, will also be implemented to ensurethe road's usability and safety.4. Post-construction Phase4.1 Construction Completion and HandoverUpon completion of the construction work, the project will be inspected to ensure compliance with the approved design and specifications. Any deficiencies or defects will be rectified. Once the road is deemed ready for use, it will be handed over to the relevant authorities.4.2 Maintenance and MonitoringA maintenance and monitoring program will be established to ensure the road's long-term performance and safety. Regular inspections and maintenance activities will be conducted to identify and address any issues promptly.In conclusion, this road construction project plan provides a comprehensive outline of the construction process and procedures. By following this plan, the project team can ensure the successful completion of the road construction project, meeting the needs of the community and providing a safe and efficient transportation network.。
施工方案的英文

施工方案的英文Construction SchemeIntroduction:The construction scheme is a comprehensive plan that outlines the entire construction process, including the scope of work, project schedule, budget, and resources required. It serves as a roadmap for the construction team, ensuring efficient and timely completion of the project while maintaining high-quality standards.Scope of Work:The construction scheme includes a detailed description of all the work that needs to be completed. This may include excavation, foundation construction, structural work, electrical and plumbing installations, and finishing work like painting and tiling. Each task is listed separately with its estimated duration and resources required.Project Schedule:The project schedule is a crucial component of the construction scheme. It outlines the start and end dates for each task, allowing for proper resource allocation and coordination. Critical milestones are identified to ensure that the project stays on track and any delays can be mitigated. The schedule may also include contingency plans in case of unforeseen circumstances. Budget:The budget section of the construction scheme outlines the estimated cost of the project. It includes expenses for labor, materials, equipment, and any other resources required. Abreakdown of costs is provided for each task, allowing for better cost control and monitoring throughout the project. Any potential cost overruns or savings are identified, and strategies for cost optimization may be included.Resources:The construction scheme identifies the resources required for the project. This includes human resources, such as the size and composition of the construction team and their specific roles and responsibilities. It also includes the equipment and machinery needed for each task and their availability and maintenance schedule. Material requirements are specified, including their quality standards and procurement plan.Quality Control:Quality control measures are an important part of the construction scheme. It includes inspections and tests to ensure that the construction work meets the required standards and specifications. Quality control guidelines are provided, including the use of certified materials, adherence to industry best practices, and compliance with relevant regulatory codes and standards. The scheme may also include provisions for continuous improvement and feedback mechanisms.Health and Safety:The construction scheme prioritizes health and safety considerations. It outlines the necessary safety measures to be implemented to protect workers, visitors, and the general public. It includes provisions for protective equipment, emergency response plans, and regular safety briefings. The scheme may alsoincorporate environmental sustainability measures, such as waste management and energy-efficient practices.Conclusion:The construction scheme is a comprehensive plan that guides the construction team from start to finish. It ensures that all necessary work is completed within the specified timeframe and budget, while meeting the required quality and safety standards. The scheme serves as a valuable tool for communication, coordination, and monitoring of the construction project, ultimately leading to its successful completion.。
公路工程施工方案英语

公路工程施工方案英语1. Project OverviewThe highway engineering project focuses on the construction of a new highway which will connect two major cities, and improve the transportation efficiency in the region. The total length of the new highway is 100 kilometers, and it will pass through urban areas, suburban areas, and rural areas. The construction project aims to promote economic development, enhance regional connectivity, and improve the overall transportation network.2. Project ObjectivesThe main objectives of the highway engineering construction project are as follows:To construct a new, high-quality highway that meets the national standards for road design and constructionTo ensure the safety of the construction process and the future use of the highwayTo minimize the environmental impact of the construction project and promote sustainable developmentTo complete the construction project within the specified time frame and budgetTo provide employment opportunities and promote local economic development through the construction project3. Project ScopeThe scope of the highway engineering construction project includes the following key components:Road design and planning: This includes the determination of the route, alignment, and specifications for the new highway, as well as the necessary surveys and studies to support the design process.Land acquisition and preparation: This involves the acquisition of land for the new highway, as well as the preparation of the land for construction activities.Earthwork and grading: This includes the excavation, filling, and compaction of the roadbed, as well as the construction of embankments, cut slopes, and other earthwork activities.Pavement construction: This involves the construction of the highway pavement, including the placement of subbase, base, and wearing course materials.Bridge and culvert construction: This includes the construction of bridges, culverts, and other structures to facilitate the crossing of water bodies, railways, and other obstacles.Traffic control and safety measures: This involves the implementation of traffic control measures and safety precautions to ensure the safety of construction workers and the traveling public.Environmental protection and mitigation: This includes the implementation of measures to protect the natural environment and mitigate the impact of construction activities on the surrounding area.Quality control and assurance: This involves the implementation of quality control measures to ensure that the construction activities meet the specified standards and specifications.4. Project ScheduleThe highway engineering construction project will be divided into multiple phases, with each phase focusing on specific aspects of the construction process. The project schedule will be as follows:Phase 1: Preliminary studies and planning (6 months)Phase 2: Land acquisition and preparation (12 months)Phase 3: Earthwork and grading (18 months)Phase 4: Pavement construction (24 months)Phase 5: Bridge and culvert construction (18 months)Phase 6: Traffic control and safety measures (6 months)Phase 7: Environmental protection and mitigation (12 months)Phase 8: Quality control and assurance (6 months)Phase 9: Final inspection and completion (3 months)5. Project BudgetThe total budget for the highway engineering construction project is estimated to be $100 million. This budget will cover the cost of land acquisition, design and planning, construction materials, labor, equipment, and other expenses associated with the project. The budget will be allocated to the various phases of the project based on the specific requirements and priorities of each phase.6. Project ManagementThe highway engineering construction project will be managed by a dedicated project management team, which will be responsible for overseeing all aspects of the project from planning and design to construction and completion. The project management team will becomposed of experienced professionals with expertise in civil engineering, project management, construction, and other relevant fields.The project management team will be responsible for coordinating the activities of all stakeholders involved in the project, including government agencies, contractors, suppliers, and local communities. The team will also be responsible for monitoring the progress of the project, managing the project budget, and ensuring that the project is completed on schedule and according to the specified quality standards.7. Health and Safety MeasuresThe health and safety of construction workers and the traveling public are of utmost importance in the highway engineering construction project. The project management team will implement a comprehensive health and safety program to ensure that all construction activities are conducted in a safe and responsible manner.The health and safety program will include the following key components:Identification and assessment of potential health and safety hazards associated with the construction activitiesImplementation of measures to control and mitigate health and safety risksProvision of necessary personal protective equipment and training for construction workersRegular monitoring and inspection of construction activities to ensure compliance with health and safety regulationsEmergency preparedness and response procedures for various potential hazardsThe project management team will work in close collaboration with relevant government agencies and other stakeholders to ensure that the health and safety program is implemented effectively and that all health and safety regulations are strictly adhered to throughout the construction process.8. Environmental Protection and MitigationThe highway engineering construction project will be conducted in compliance with all applicable environmental regulations and standards to minimize the impact of construction activities on the natural environment. The project management team will implement a range of measures to protect the environment and mitigate any adverse effects of construction.Key environmental protection and mitigation measures will include:Identification and assessment of potential environmental impacts associated with construction activitiesImplementation of measures to prevent soil erosion, sedimentation, and other forms of environmental degradationProper disposal of construction waste and management of hazardous materials Protection of wildlife habitats and preservation of natural resourcesImplementation of measures to reduce noise, dust, and other forms of pollution associated with construction activitiesThe project management team will also work in collaboration with environmental agencies and other relevant stakeholders to ensure that the environmental protection and mitigation measures are implemented effectively and that the project complies with all environmental regulations and standards.9. Quality Control and AssuranceThe highway engineering construction project will be subject to stringent quality control measures to ensure that all construction activities meet the specified standards and specifications. The project management team will implement a comprehensive quality control and assurance program to monitor and assess the quality of construction activities throughout the project.Key components of the quality control and assurance program will include: Establishment of quality control guidelines and procedures for construction activities Regular inspection and testing of construction materials and workmanship Identification and resolution of any quality issues or deficiencies in construction activities Documentation and record-keeping of all quality control measures and findingsThe project management team will work in close collaboration with construction contractors, suppliers, and other stakeholders to ensure that the quality control and assurance program is implemented effectively and that all construction activities meet the specified quality standards.10. ConclusionThe highway engineering construction project represents a significant investment in the transportation infrastructure of the region. The project will contribute to economic development, regional connectivity, and improved transportation efficiency. The project will be implemented with a focus on safety, environmental protection, and quality, and will be managed by a dedicated project management team. Through careful planning, efficient execution, and strict adherence to regulatory standards, the project aims to deliver a high-quality, sustainable highway that will benefit the region for years to come.。
施工方案英语
施工方案英语一、介绍施工方案是指在工程建设过程中,为了实现工程目标,按照工程设计方案和相关规范要求,针对工程的特点和实际情况,制定的一套具体施工措施和方法。
施工方案的编制是工程施工的重要环节之一,其质量直接影响工程的安全、质量和进度。
本文档将介绍施工方案的相关英语表达,以帮助工程领域人士和英语学习者更好地理解和应用施工方案。
二、施工方案相关术语1.Construction scheme - 施工方案2.Construction project - 建筑工程3.Engineering design - 工程设计4.Specifications - 规范要求5.Construction measures - 施工措施6.Methods - 方法7.Safety - 安全8.Quality - 质量9.Progress - 进度10.Preparation - 准备工作11.Site investigation - 现场勘测12.Construction site - 施工现场13.Materials - 材料14.Equipment - 设备15.Structural elements - 结构元素16.Foundation - 基础17.Concrete pouring - 混凝土浇筑18.Welding - 焊接19.Installation - 安装三、施工方案编制过程施工方案的编制过程一般包括以下几个步骤:1.需求分析:了解工程项目需求,根据工程设计和规范要求,确定施工目标和要求。
2.资料收集:收集工程相关资料,包括设计图纸、规范文件、勘测报告等。
3.现场勘测:对施工现场进行实地勘测,了解环境特点和地质情况,为制定施工方案提供依据。
4.技术研究:根据工程的特点和要求,进行技术研究和方案比较,确定最佳的施工措施和方法。
5.方案编制:根据前述工作,编制详细的施工方案,包括施工措施、工序安排、材料使用、设备配置等。
土方明挖英文施工方案constructionmethodstatement
土方明挖英文施工方案constructionmethodstatement1. MAIN DAM FOUNDATION EXCAVATION1.1OBJECTIVEThe main objective of this method statement is to describe in detail the sequence of works and establish priorities of work to allow embankment filling to start by scheduled in the baseline programme on 17-Jan-2003. An immediate objective will be to expedite works and expose the plinth at the dam foundation for geotechnical investigation.This method statement and includes the following:Haul roads and disposal areas,Preparation of secondary river crossings,Dewatering,Preparation of loading platform, andEarth/rock excavation for integrated cofferdam foundation.1.2ZONING OF WORK AREAS:From the d rawing, …by drawing a line connecting the highest point of the ridges of both left and right banks, the main dam work area is divided into the followingwork zones:Area 1: From downstream face of auxiliary cofferdam to the dam axis of integrated cofferdam;Area 2: From the dam axis of integrated cofferdam to the main dam axis, below elevation 130m for the right bank, below elevation 140 for the left bank, andincluding the riverbed.Area: From the main dam axis to the down stream limit of Main Dam, below elevation 130m for the right bank, below elevation 140 for the left bank, andincluding the riverbed downstream of MD Axis.Area 4: From the dam axis of integrated cofferdam to downstream limit of the Main Dam, above elevation 130m for the right bank, above elevation 140 forthe left bank.Each work zone is is further divided into sub-areas, each subdivision is basicallydefined into left abutment, riverbed and right abutment sections.Please refer to drawing no. MDEX-MS-001 (Attachment 1)1.3METHODOLOGY1.3.1P REPARATION OF H AUL R OADS &D ISPOSAL A REAS1.3.1.1Haul RoadsThe following haul roads shall be prepared for haulage of excavatedmaterial:Road R1: Main haul roadRoad R1-1: Connects right abutment at EL 210 to R1.Road R1-2: From loading platform at Right Abutment @EL 130, to the upstream face of auxiliary cofferdam, and connected to R2 at Down Stream.Road R2: From loading platform at Right Abutment @EL 70, to the disposal areas near W4, and Northern side of W6.Road L2: From riverbed EL 50 to disposal areas near W4, and Northern side of W6.Please refer to “Access Road Arrangement for Main Dam/Power HouseExcavation--- First Stage” (Attachment 2)1.3.1.2Disposal AreasThe designated disposal areas will be as follows:Upstream face of auxiliary cofferdam: Designated as disposal area and at the same time a 20m-width access road across the river is to be constructedadjacent to the auxiliary cofferdam.Near W4: Disposal area at low line areas adjacent to W4.Northern side of W6: Disposal area at low line areas at Northern side of W6.W 14, andW 15.Please refer to Attachment 3”Disposal Area & Temporary Stockpil e forMain Dam and Powerhouse Excavation” for the layout plan of theaforesaid disposal areas.1.3.2M ETHOD OF O VERBURDEN E XCAVATIONThe following loading platforms shall be prepared to collect the material(earth/rock) pushed from the higher elevation:Top platform –for the interfacing with the main dam excavation:o Right Abutment: EL 130o Left Abutment: EL 140The above platforms shall be at least 15m width. It shall be prepared byforming temporary slope from higher elevation and shall be benched deeper into the design formation of slightly weathered/sound rock layer.As for the Main Dam excavation above elevation EL 130 (Right) and EL140 (Left), the aforesaid platforms will serve as loading platforms to collect excavated material pushed downslopes from higher elevation workingareas.Intermediate platform –This will serve as an intermediate collecting point for excavated material to control the overall dozing distance within 30m ~ 40m.o Right Abutment: EL 100 and EL 70Following the topography and terrain at the right abutment where there arewell-defined mountain ridges and gullies, intermediate platforms will beconstructed in between ridges. The area will be cleared from logs orundergrowth, slopes trimmed to provided wider area, and filling to form the platform.o Left Abutment: NilThere are no apparent ridges at left abutment. In addition, the thickness of overburden at the left bank is comparatively thinner and the original slope is comparatively steeper than the right bank. Hence, intermediate platforms becomes unfeasible at this area.Final platform – Located at the riverbed at approximately EL 50. Formed by the excavated material pushed towards the riverbed during the process offoundation excavation, will served as the final loading platform before theriverbed is to be excavated up to the required rock strata. This platform will mainly serve to load and haul overburden pushed downslopes from the leftbank excavations.Pleas refer to drawing MDEX-MS-001 (Attachment 1).1.3.3F ILLING OF S ECONDARY C ROSSINGS/B UNDS.Secondary crossings will be constructed across, by filling the riverbed with suitable material taken from excavation works forming a crossing to both banks, and, also, sectionalise the riverbed work areas. This is to minimize interference of works when excavation works of riverbed and upper elevation are carried out simultaneously at alternate zones.These crossings will also serve containment bunds to prevent excavated material from contaminating the integrated cofferdam work areas.By forming these crossings, the river is “transformed into ponds”, and these allows dewatering of the river to be segmentalized.1.3.4D EWATERINGA combination of 10?? and 14” water pumps will be stationed at separate segmentsof riverbed. Two -720,000 gallons per day pumps will be installed at the downstream side of the river. Smaller pumps may be installed at the river sections formed by the riverbund, to keep and maintain the area dry during riverbed excavation and plinth construction.1.4IMPLEMENTATION PROGRAM1.4.1T IME F RAMEThe time frames for respective zones are summarized as follows:o Zone 1 25-Aug-03 to 07-Oct-03o Zone 2 20-Aug-03 to 19-Dec-03o Zone 3 01-Oct-03 to 15-Jan-04o Zone 4 01-Dec-03 to 20-Dec-04.Please refer to Work Program on Main Dam Excavation (Attachment 4) fordetails.1.4.2R ESOURCESRefer to Attachment 5: Table of Work Areas and Processes” andAttachment 6: “Main Dam Excavation –Equipment”1.5SAFETYAs a safety barrier, gabion wall in 2-1 arrangement shall be built (if necessary) as protective armor at the upper platforms (mentioned in Section 1.3.2) to prevent materials pushed downslopes from causing injuries to works at the lower sections of the dam. These gabions will also serve to contain excavated materials, sludges, debris and other objects from contaminating embankment work andpermanent excavation slopes. The gabion walls will be “wrapped” with geotexti les to allow clean water pass through to the cut off drains.Also, cut off trenches, of sufficient shall also be provided at the upper platforms which will also prevent runoff carrying silt from contamination the dam foundation at lower elevation.Kindly refer to Attachment 7: Section View of Typical Work Sequence.2. POWER HOUSE FIRST STAGE EXCA V ATION ABOVEELEV ATION70M2.1OBJECTIVEThis method statement is prepared to strengthen the Overall Method Statement that submitted earlier for further elaborating in detailed the sequence of excavationworks that related to the overburden and rock excavation forthe Powerhouse.This method statement is to cover the following contents:i.Haul roads;ii.Overburden excavation;iii.Rock excavation;iv.Slope protection works;v.Dewatering;ix. Foundation preparation;2.2ZONINGBy considering the accessibility and haul road arrangement, the powerhouse can be divided in the following work zones: Area 1: From elevation 190m to elevation 145m;Area 2: From elevation 145m to elevation 115m;Area 3: From elevation 115m to elevation 70m.Please refer to drawing no. PHEX-MS-001 (Attachment 8)2.3METHODOLOGY2.3.1P REPARATION OF H AUL R OADS &D ISPOSAL A REAS2.3.1.1Haul RoadsThe following haul roads shall be prepared for haulage of excavatedmaterial:Road L2-2: Trunk haul road for Powerhouse excavation at Area 3 (Downstream)Road L1-1: Trunk haul road for Powerhouse excavation at Area 2 (Upstream)Please refer to “Access Road Arrangement for Main Dam/Power HouseExcavation--- F irst Stage” (Attachment 2)2.3.1.2Disposal AreasThe designated disposal areas will be as follows:Near W4: Disposal area at low line areas adjacent to W4.Northern side of W6: Disposal area at low line areas at Northern side of W6.The extracted rock from Powerhouse that suitable for embankment fill forthe Main Dam will be directly utilized for the main dam filling or will betemporary stockpile at the following designated stock yards: Platform next to the Adit for the diversion tunnels;The platform between W4 and existing access road.Please refer to Attachment 3”Disposal Area & Temporary Stockpile forMain Dam and Powe rhouse Excavation” for the layout plan of theaforesaid disposal areas.2.3.2M ETHOD OF O VERBURDEN/R OCK E XCAVATION2.3.2.1Overburden/Rock Excavation – Area 1At Area 1, the excavation of overburden will be started from the …twin peaks? apart; the working platforms are relatively smaller and more congested. The most suitable method for overburden excavation at this stage is suggested to be by way of throwing down the said materials by hydraulic excavator and bulldozer from the top of the cut slope in stages to form the benches for rock blasting. The materials will be subsequently **************************************************** and loading by hydraulic excavators then disposed off using 20 tons/30 tons dump trucks in later stage.At this stage, all materials including earth and rock will be pushed down to lower elevation, and due to no access road (due to very steep terrain,), the segregation of usable and unusablematerial is not feasible. It is inevitable that all excavated materials from area 1 will be contaminated and will therefore be hauled to disposal area at W6 or W4.2.3.2.2Overburden/Rock Excavation – Area 2At Area 2, excavation will be done by the conventional method of direct load and haul. The excavated material shall be collected by bulldozer, loaded using hydraulic excavator/wheel loader, and hauled to by 30t/20t dumper.Haul road L 1-1 will be used as trunk access road for the haulage. Theprofile and alignment for haul road L 1-1 may be branched from time totime in accordance to the overall elevation of excavation.2.3.2.3Overburden/Rock Excavation – Area 3With reference to the drawings, the …twin peak?of powerhouse excavation will be merged as a larger area of excavation at el. 130m. As such the excavation can be done by the conventional method of direct load and haul.The excavated material shall be collected with bulldozer, loaded with hydraulic excavator/wheel loader and hauled by 30t/20t dumper.Haul road L 2-2 will be used as trunk access road for the haulage. The profile and alignment for haul road L 2-2 maybe branched from time to time in accordance to the overall elevation of excavation.In order to expedite excavation of overburden at this stage, there will be substantial degree of pushing down of overburden material downslopes, to the loading platform at riverbed area. These overburden materials shall be disposed of at a later stage to W6. Rock that can be used for embankment filling oraggregates will be will be salvaged and transported separately to the designated stockpile areas, crushing plant or directly be utilized as main dam filling.2.3.3 Temporary Diversion and DrainagePrior to the excavation of spillway, the existing creek between two ridges of this area will cause the major impact to the powerhouse excavation. Withreference to the design drawings, in order to integrate with the permanentberm drain design, a temporary drain is to be provided to join with thepermanent berm drain at el. 130. The runoff of the said creek will then becollected and diverted through the slope drains and discharged to BatangBalui through the berm drain at el.70m.Should the said berm drain have failed to cater the runoff from the existingcreek, dimension and size of the berm drains at el.130 shall be reviewed andmodified to suit the actual site condition and to satisfy the drainagerequirement.Precipitation and wastewater during the period of construction will bedischarged through the berm drains and slope drains. Reference is made toAttachment 8: Drainage System Layout2.4SLOPE PROTECTIONWorks for slope protection will follow closely excavationworks. As a general rule, as soon as one berm layer is excavated, slope protection works will be carried out as per construction drawings prior to continuing with excavation of the next bench.As a general method, each berm (15meters) will be bench blasted into 3 stages or layers ( 5 meters per layer). This is to allow a working platform for the equipment, and slope protection works can proceed without need of scaffolding.In cases where the slope has been cut into its full bench, scaffolding will have to be installed for slope protection works.2.5 IMPLEMENTATION PROGRAM2.5.1T IME F RAMEThe time frames for respective zones are summarized as follows:o Area 1 10-Aug-03 to 06-Oct-03o Area 2 04-Oct-03 to 20- Nov-03o Area 3 04-Nov-03 to 18-Jan-04Please refer to the attachment 9: WORK SCHEDULE2.5.2R ESOURCESRefer to Attachment 10: Manpower and Equipment。
施工方案双语(3篇)
第1篇Project Name: Urban Residential ComplexClient: XYZ Real Estate Development Co., Ltd.Location: Downtown, City of ADuration: 24 months1. IntroductionThis proposal outlines the construction plan for the Urban Residential Complex, a high-rise residential building designed to provide modern living spaces in the heart of the city. The project will include residential units, recreational facilities, and commercial spaces. The following sections detail the construction methodology, safety measures, quality control, and project timeline.2. Construction Methodology2.1 Site Preparation- Clearing the site of debris, vegetation, and any existing structures.- Establishing temporary construction offices, storage areas, and access roads.- Conducting a detailed site survey to identify underground utilities and other obstacles.2.2 Foundation Construction- Excavating the foundation pit according to the architectural drawings.- Installing formwork and reinforcing steel for the foundation.- Casting the concrete foundation slab and walls.- Conducting quality tests on the concrete mix to ensure compliance with standards.2.3 Superstructure Construction- Installing steel columns and beams according to the structural drawings.- Constructing the concrete floors using formwork and reinforcing steel.- Installing the precast concrete units for walls and partitions.- Carrying out regular structural inspections to ensure the integrity of the framework.2.4 Facade and Roofing- Installing the facade system, which includes cladding, insulation, and waterproofing.- Constructing the roof structure with steel trusses and roofing materials.- Ensuring the roof is watertight and meets the required insulation standards.2.5 Interior Finishing- Installing electrical, plumbing, and HVAC systems according to the design specifications.- Laying tiles, carpet, or hardwood flooring in the residential units.- Painting walls and ceilings, and installing doors and windows.- Conducting final inspections to ensure all interior finishes meet quality standards.2.6 Miscellaneous Works- Constructing recreational facilities such as swimming pools, gyms, and playgrounds.- Installing security systems, including surveillance cameras and access control.- Setting up commercial spaces for retail or office use.- Coordinating with utility companies for the connection of water, electricity, and gas supplies.3. Safety Measures3.1 Health and Safety Policy- Implementing a comprehensive health and safety policy in accordance with local regulations.- Conducting regular safety training for all workers.- Ensuring the availability of first aid kits and emergency response plans.3.2 Personal Protective Equipment (PPE)- Providing appropriate PPE to all workers, including helmets, gloves, safety shoes, and eye protection.- Ensuring the use of fall protection equipment on all elevated work areas.3.3 Safety Inspections- Conducting daily safety inspections on the construction site.- Reporting any hazards or accidents to the project manager immediately.4. Quality Control4.1 Materials and Workmanship- Ensuring the use of high-quality materials and adherence to the latest construction standards.- Conducting periodic quality checks throughout the construction process.- Obtaining certifications for materials and finishes used in the project.4.2 Testing and Inspections- Conducting tests on concrete, steel, and other materials to ensure compliance with specifications.- Inspecting the workmanship at each stage of the construction process to ensure quality.5. Project Timeline5.1 Phase 1: Site Preparation and Foundation Construction (3 months)- Clearing the site and establishing temporary facilities.- Excavating the foundation pit and casting the foundation.- Installing formwork and reinforcing steel for the superstructure.5.2 Phase 2: Superstructure Construction (9 months)- Constructing the steel framework and concrete floors.- Installing precast concrete units and conducting structural inspections.- Erecting the facade and roofing systems.5.3 Phase 3: Interior Finishing and Miscellaneous Works (6 months)- Installing electrical, plumbing, and HVAC systems.- Laying flooring and painting walls.- Constructing recreational facilities and commercial spaces.5.4 Phase 4: Final Inspections and Handover (3 months)- Conducting final inspections and obtaining necessary certifications.- Cleaning the site and preparing the building for handover to the client.6. ConclusionThe Urban Residential Complex project is expected to be completed within the stipulated timeframe and budget. By following the outlinedconstruction methodology, safety measures, and quality control procedures, we aim to deliver a high-quality residential building that meets the needs of our clients and the community. We look forward to the opportunity to work with XYZ Real Estate Development Co., Ltd. and contribute to the development of the city.---施工方案项目名称:城市住宅综合体客户: XYZ房地产开发有限公司地点: A市市中心工期: 24个月1. 引言本方案概述了城市住宅综合体的施工计划,该综合体是一座高层住宅楼,旨在市中心提供现代化的居住空间。
道路工程施工流程英文步骤
1. Project Planning and DesignThe first step in road construction is project planning and design. This involves analyzing the project requirements, preparing detailed design plans, and obtaining necessary permits. The project manager, along with the design team, works on the following activities:- Identifying project objectives and scope- Conducting feasibility studies- Preparing design plans and specifications- Obtaining environmental clearances and permits- Establishing project timelines and budget2. Site PreparationOnce the project is approved, the site preparation phase begins. This involves clearing the site of any vegetation, debris, and existing structures. The following activities are carried out:- Excavating and removing topsoil- Establishing temporary construction facilities, such as a site office, storage sheds, and labor camps- Constructing access roads and temporary utilities3. Substructure ConstructionThe substructure is the foundation of the road, providing support to the surface layers. This phase involves the following activities:- Excavating and preparing the subgrade- Laying down subgrade base courses, which may include gravel, crushed stone, or concrete- Compacting the base course using rollers or compactors- Laying down the subbase course, which provides additional support to the road structure- Compacting the subbase course4. Roadway ConstructionThe roadway construction phase involves laying down the various layers of the road, including the subgrade, base course, subbase course, and surface course. The following activities are carried out:- Excavating and preparing the subgrade- Laying down and compacting the base course- Laying down and compacting the subbase course- Laying down the surface course, which may include asphalt or concrete- Compacting the surface course using rollers or compactors5. Roadside ConstructionRoadside construction includes the construction of features such as guardrails, signage, and drainage systems. The following activities are carried out:- Constructing guardrails and barriers- Installing signage and road markings- Constructing and maintaining drainage systems, including culverts and stormwater management facilities6. Road Opening and MaintenanceOnce the road construction is complete, the road is opened for traffic. The following activities are carried out during this phase:- Conducting road opening ceremonies- Ensuring the road is safe for traffic- Providing maintenance services, such as road repairs and routine maintenance7. Project Completion and HandoverThe final phase of the road construction project is completion and handover. This involves:- Ensuring all project deliverables are completed- Conducting final inspections and quality control checks- Submitting project documentation and reports- Handing over the road to the client or local authority- Conducting post-construction surveys and assessmentsIn conclusion, the road construction project execution process involves several critical steps, from planning and design to project completion and handover. Each phase requires careful planning, execution, and coordination to ensure the successful completion of the project. Proper execution of these steps will result in a safe, durable, and functional road that meets the needs of the community.。
- 1、下载文档前请自行甄别文档内容的完整性,平台不提供额外的编辑、内容补充、找答案等附加服务。
- 2、"仅部分预览"的文档,不可在线预览部分如存在完整性等问题,可反馈申请退款(可完整预览的文档不适用该条件!)。
- 3、如文档侵犯您的权益,请联系客服反馈,我们会尽快为您处理(人工客服工作时间:9:00-18:30)。
IV Construction Method, Technical Measurement of Road Works
道路工程施工方法及技术措施
1、Road Structure
道路构造:
Heavy load road
重型道路:
Soil compacting—150 mm thick 12% lime soil—220mm thick fly-ash—200mm thick C30 concrete
素土压实--150厚碎石基层。
---300mm厚二灰结石---150mm厚C 20砼(内配钢筋) –C15予制砼平石、侧石安放-----60mm厚粗粒式沥青砼---30mm厚细粒式沥青砼-
Light load road
轻型道路:
Soil compacting—200mm thick 12% lime soil—220mm thick fly-ash—200mm thick C30 concrete
素土压实--150厚碎基层。
---50mm粗砂找平层---150mm厚C30砼面层。
Pavement
人行道:
Soil compacting—200mm thick fly-ash bedding—30mm thicksand—precast cement tile C30
素土压实,100厚碎石基层---50MM厚粗砂上铺彩色予制人行道砖。
2、Road working procedure
道路施工流程
2.1 Plain soil compacting-----soil density teat-----pipe embedding under the road---150*2mm thick 12% lime soil bedding---lime soil test--------220mm thick fly-ash beddng---220mm thick C30 concrete finish-----concrete curing----curbs paving 素土压实-----土密实度侧试-----路基下管线埋设---150*2厚12%石灰土基层。
---灰土试验---------220mm厚二灰结石---220mm厚C30砼面层。
-----砼养护----路
沿石施工
2.2、Main Construction Method
主要施工方法
2.2.1、Setting-out: to line road central pile and edge piles based on plane coordinates control points and shop drawing
施工放线:根据平面坐标控制点及设计施工图,测放出道路中心线桩及边线桩。
2.2.2、Plumbing Identification: Before starting the road construction work, to arrange the position &level of underground plumbing and concealed facilities. To erect signs around expose well mouths so that they won’t be embedded during construction.
管线标志:在道路工程开工前,安排专人认真复核地下管线和地下隐蔽设施的位置和标高,对外露的各种井口设置标志杆牌,以免埋没或堵塞。
2.2.3、Road compaction
路基压实
2.2.
3.1、When compacting road base, to abide the rules as follows: first light second heavy, first table second vibrate, first slow second quick, first edge second center, first high second low. And compaction roller should exceed construction joints.
路基碾压时,应遵循先轻后重、先稳后振、先慢后快、先边后中、先高后低以及轮迹要重叠等原则,且碾压轮应超过分段施工的接缝。
2.2.
3.2、When compacting road, to first compact stably then 4~5 times of vibrating compaction last stably compact again.
路基压实时先稳压一遍,再振动碾压四~五遍,最后再稳压一遍(碾压遍数现场试验后再作调整)。
2.2.
3.3、To compact longitudinally, and first edge side them central part.
碾压顺道路纵方向进行,且先边后中;轮迹重叠>30cm。
2.2.
3.4、After compaction, to test compaction coef., through frequency &quantity for quality control.
碾压速度均匀,轮迹重叠,压路机碾压不到的部位,应采用小型机夯实或
人力夯认真夯实,夯击面在纵横方向均应相互重叠一半,防止漏夯。
路基压实后不得有松散、弹簧、翻浆及表面不平整现象,若下层未达到压实度要求,不得铺筑上层。
2.2.
3.5、Take the soil density test after compaction to judge the quality of the compacted soils.
土路基碾压后,按规定频率,数量进行土的密实度试验,以判断碾压质量。
〔进行环刀试验〕
2.3Construction of fly-ash bedding
二灰结石的施工:
1、The fly-ash will be supplied by as the finished product and delivered on site for paving
二灰结石的材料由供货商成品生产后及时运往工地,铺设施工。
2、The material mixing scale is strictly comply with the national standard (JTJ034-2000), producing after approval by testing ,
材料级配严格按照设计要求进行配合比设计,试验确定后生产执行。
配比为:熟石灰:粉煤灰:碎石=1:2:3
3、Lime: cinder: aggregate= 5:15:18
三灰碎石混合料配比为:石灰;粉煤灰;集料=5:15:18
4、The fly-ash paving after road compaction, use machine for construction, leveling, compacting and sloping, we will strictly fulfill the regulation and code during construction.
在道路基土压实,测试合格进行二灰结石的施工,施工用机械化施工,铺设平整(适当放坡)压实密实,严格按规范要求进行。
5、Must care for the curing after fly-ash paving, no vehicles pass through during curing period, set barricade for separation.
施工完成后的二灰结石,必须确保养期,在保养期内禁止车辆通行,采取道路隔离措施。
6、The material inspection will be carried out strictly according to the related code or regulation during the fly-ash construction period.
所有二灰结石的整个施工过程包括材料及测试将严格按照相关规定实施。