靶材质量对大面积镀膜生产的影响
靶材质量对大面积镀膜生产的影响
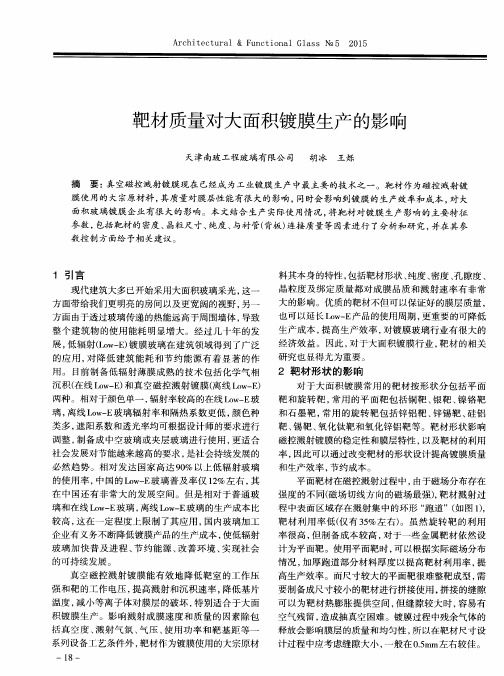
平 面靶 材在磁 控 溅射 过程 中 , 由于磁 场 分布存 在 强 度 的不 同( 磁 场 切 线方 向的磁 场 最强 ) , 靶 材溅 射 过 程 中表面 区域 存 在溅 射 集 中 的环形 “度 上 限制 了其 应 用 , 国 内玻 璃 加 工 企 业有 义 务不 断降低 镀膜 产 品 的生 产成 本 , 使低 辐射 玻璃加快普及进程 、 节约能源 、 改善 环 境 、 实 现社 会
节 功能 。
【 4 ] Hu a n g P Y, Ku r a s c h S , S r i v a s t a v a A, e t a 1 . Di r e c t i ma g i n g o f a t W O — d i me n s i o n a l s i l i c a g l a s s o n g r a p h e n e [ J ] . Na n o L e t t e r s , 2 0 1 2 ,
A rc hi t e c t ur al & F un c ti o n al Gl as s No _ 5 2 01 5
靶材质量对 大面积镀膜生产 的影 响
天津 南玻 工程玻 璃有 限公 司 胡冰 摘 王 烁
要: 真 空磁 控 溅射 镀 膜现 在 已经成 为工 业镀 膜 生产 中最主要 的技 术之 一 。靶 材 作 为磁 控 溅射 镀
靶 和旋 转 靶 , 常用 的平 面 靶 包 括铜 靶 、 银靶 、 镍 铬 靶 和石墨靶 , 常用 的旋 转 靶 包 括 锌 铝靶 、 锌 锡靶 、 硅 铝 靶、 锡靶 、 氧化 钛 靶 和氧 化锌 铝 靶 等 。靶材 形 状影 响 磁 控溅 射镀 膜 的稳 定 性和 膜层 特性 , 以及靶 材 的利用 率, 因此可 以通 过改 变靶 材 的形 状设 计 提高 镀膜 质量
导致脱膜的几个要因素

导致脱膜的几个要因素千万脱膜大致有以下几个因素:原片、水质、真空度、清洗机、工艺气体、靶材。
2.1原片因素2.1.1原片存放因素玻璃表面越新鲜,表面活性越大,与膜层的结合力越强,反之则差。
使用存放期过长的玻璃,由于玻璃表面霉变和附着的污物会大量增加,而且附着力很强,清洗环节很难清除掉,这就造成膜层与基片的结合力大大降低,从而导致脱膜。
建议视季节采用存放期在一个月以内的制镜级或汽车级浮法玻璃。
2.1.2原片切割因素许多原片生产厂家为了提高玻璃的切裁率,在切割刀上注了过多的煤油,这些煤油残留在原片上,在清洗环节难以清除掉,造成脱膜。
在采购玻璃原片时,应要求无油切割。
若不能无油切割,应在正式清洗前用稀盐酸或阴离子去垢剂进行预清洗。
2.2水质因素2.2.1水处理设备水质的好坏对于镀膜是至关重要的。
去离子水纯度应控制在电阻率10M欧姆以上。
若低于该值,则应对阴阳离子交换树脂进行再生,否则,会因水质不纯导致原片清洗不净而脱膜。
2.2.2管道和水箱的杂质连接水处理设备和清洗机水箱的管道应定期吹扫清洗。
因为管道中若残留不流动的水时间久了,会滋生细菌、藻类,在使用时会带到水箱里,使清洗水本身水质不过关,造成镀膜不牢。
2.3清洗机2.3.1清洗刷清洗刷使用一段时间后,上面会残留一些污物,包括油污、絮状物、纸屑、甚至细菌,若不能有效地进行清洗,也会带来污染,造成脱膜。
所以,必须定期用蒸汽清洗机清洗毛刷,必要时,可用双氧水清洗。
2.3.2风机风压大小,风刀角度调整的好坏将影响到原片能否吹干,若吹不干,镀膜后,肯定脱膜。
必须保证进入真空室的玻璃干燥。
2.4真空度真空度必须达到一定标准方可镀膜,否则,会因气体中残留杂质气体,导致膜层成分不纯,结合力不强。
一般应控制在10-3Pa。
2.5扩散泵返油扩散泵冷却水水温偏高,易导致油蒸汽进入镀膜室附着在原片上,这是导致脱膜的生要因素之一。
定期观察扩散泵冷却水水温,做好记录,尤其在炎热的夏季和使用较高溅射功率的时候,更应如此。
溅射镀膜原理

溅射镀膜原理溅射镀膜是一种常见的表面处理技术,它通过溅射材料产生的离子和原子沉积在基底表面形成薄膜。
这种方法可以用于制备光学薄膜、导电薄膜、防腐蚀膜等,具有广泛的应用前景。
下面我们来详细了解一下溅射镀膜的原理。
首先,溅射镀膜的原理基于溅射现象。
在溅射镀膜过程中,通过加速器产生的高能粒子轰击靶材,使得靶材表面的原子或分子被“溅射”出来,形成离子流。
这些离子流沉积在基底表面,最终形成薄膜。
溅射镀膜可以分为直流溅射、射频溅射、磁控溅射等不同类型,但其基本原理都是相似的。
其次,溅射镀膜的原理还与靶材的材料密切相关。
不同的靶材材料会产生不同的离子流,从而形成不同性质的薄膜。
例如,使用金属靶材可以制备导电薄膜,而使用氧化物靶材则可以制备光学薄膜。
因此,在溅射镀膜过程中,靶材的选择对最终薄膜的性能具有重要影响。
此外,溅射镀膜的原理还与沉积过程和基底表面的准备密切相关。
在溅射镀膜之前,需要对基底表面进行清洁和处理,以确保薄膜的附着力和质量。
沉积过程中的工艺参数,如溅射能量、沉积速率、沉积角度等,也会影响薄膜的性能。
总的来说,溅射镀膜的原理是通过溅射材料产生的离子和原子沉积在基底表面形成薄膜。
这种方法可以制备具有特定功能的薄膜,具有广泛的应用前景。
在实际应用中,需要根据具体的要求选择合适的靶材材料和工艺参数,以获得理想的薄膜性能。
通过对溅射镀膜原理的深入了解,我们可以更好地掌握这一表面处理技术的工作原理和应用特点,为相关领域的研究和应用提供理论支持和技术指导。
希望本文能够帮助读者更好地理解溅射镀膜原理,促进该领域的发展和应用。
磁控溅射镀膜公转对镀膜的影响

磁控溅射镀膜公转对镀膜的影响随着科学技术的不断进步,表面涂层技术也在不断创新。
磁控溅射镀膜技术是一种常用的表面涂层技术,它利用磁控溅射装置将固体材料蒸发并沉积在基材表面,以改善基材的性能。
公转是磁控溅射镀膜中的一个重要参数,它对镀膜过程和薄膜性能都有着重要的影响。
本文将从多个方面讨论公转对磁控溅射镀膜的影响。
1. 公转对薄膜均匀性的影响在磁控溅射镀膜过程中,公转是指靶材周围的基材沿着镀膜室轴线进行旋转运动。
公转的速度和方向对于薄膜的均匀性有着重要的影响。
当公转速度过慢时,蒸发材料只会沉积在基材的中心位置,使得薄膜边缘处厚度较薄,中心部位较厚;当公转速度过快时,蒸发材料会向外飞散,也会导致薄膜的厚度不均匀。
合适的公转速度和方向能够使得薄膜的厚度分布更加均匀,提高薄膜的质量和稳定性。
2. 公转对薄膜成分的影响在磁控溅射镀膜过程中,靶材表面的成分、温度和结构都会影响薄膜的成分。
而通过调节公转参数,可以改变靶材表面的成分和温度,进而影响薄膜的成分。
研究表明,适当调节公转速度和方向,可以改善镀膜过程中的靶材表面温度分布和成分分布,使得薄膜的成分更加均匀和稳定。
3. 公转对薄膜微观结构的影响薄膜的微观结构对其性能有着重要的影响。
通过调节公转参数,可以影响薄膜在基材上的晶粒大小、取向和结构。
研究发现,适当的公转参数能够有效地调控薄膜的微观结构,使得薄膜的晶粒更加致密和均匀,提高薄膜的力学性能和耐腐蚀性能。
4. 公转对镀膜速率的影响在磁控溅射镀膜过程中,蒸发材料的沉积速率直接影响着薄膜的厚度和成分。
而公转速度和方向可以调节蒸发材料的沉积速率。
研究表明,适当的公转参数可以提高蒸发材料的沉积效率,使得薄膜的沉积速率更加稳定和均匀。
总结:磁控溅射镀膜公转对镀膜的影响是多方面的,包括对薄膜均匀性、成分、微观结构和沉积速率等方面都有着重要的影响。
通过合理调节公转参数,可以实现对薄膜质量和性能的有效控制,为磁控溅射镀膜技术的应用提供了重要的理论基础和技术支持。
导致脱膜的几个要因素

导致脱膜的几个要因素千万脱膜大致有以下几个因素:原片、水质、真空度、清洗机、工艺气体、靶材。
2.1原片因素2.1.1原片存放因素玻璃表面越新鲜,表面活性越大,与膜层的结合力越强,反之则差。
使用存放期过长的玻璃,由于玻璃表面霉变和附着的污物会大量增加,而且附着力很强,清洗环节很难清除掉,这就造成膜层与基片的结合力大大降低,从而导致脱膜。
建议视季节采用存放期在一个月以内的制镜级或汽车级浮法玻璃。
2.1.2原片切割因素许多原片生产厂家为了提高玻璃的切裁率,在切割刀上注了过多的煤油,这些煤油残留在原片上,在清洗环节难以清除掉,造成脱膜。
在采购玻璃原片时,应要求无油切割。
若不能无油切割,应在正式清洗前用稀盐酸或阴离子去垢剂进行预清洗。
2.2水质因素2.2.1水处理设备水质的好坏对于镀膜是至关重要的。
去离子水纯度应控制在电阻率10M欧姆以上。
若低于该值,则应对阴阳离子交换树脂进行再生,否则,会因水质不纯导致原片清洗不净而脱膜。
2.2.2管道和水箱的杂质连接水处理设备和清洗机水箱的管道应定期吹扫清洗。
因为管道中若残留不流动的水时间久了,会滋生细菌、藻类,在使用时会带到水箱里,使清洗水本身水质不过关,造成镀膜不牢。
2.3清洗机2.3.1清洗刷清洗刷使用一段时间后,上面会残留一些污物,包括油污、絮状物、纸屑、甚至细菌,若不能有效地进行清洗,也会带来污染,造成脱膜。
所以,必须定期用蒸汽清洗机清洗毛刷,必要时,可用双氧水清洗。
2.3.2风机风压大小,风刀角度调整的好坏将影响到原片能否吹干,若吹不干,镀膜后,肯定脱膜。
必须保证进入真空室的玻璃干燥。
2.4真空度真空度必须达到一定标准方可镀膜,否则,会因气体中残留杂质气体,导致膜层成分不纯,结合力不强。
一般应控制在10-3Pa。
2.5扩散泵返油扩散泵冷却水水温偏高,易导致油蒸汽进入镀膜室附着在原片上,这是导致脱膜的生要因素之一。
定期观察扩散泵冷却水水温,做好记录,尤其在炎热的夏季和使用较高溅射功率的时候,更应如此。
azo靶材镀膜参数
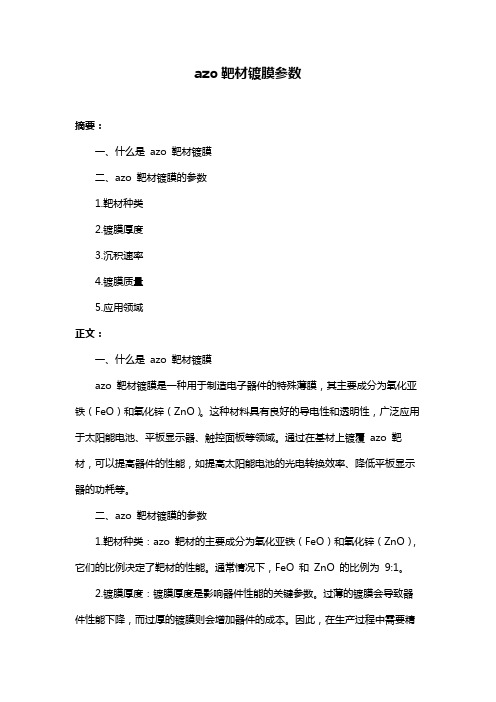
azo靶材镀膜参数摘要:一、什么是azo 靶材镀膜二、azo 靶材镀膜的参数1.靶材种类2.镀膜厚度3.沉积速率4.镀膜质量5.应用领域正文:一、什么是azo 靶材镀膜azo 靶材镀膜是一种用于制造电子器件的特殊薄膜,其主要成分为氧化亚铁(FeO)和氧化锌(ZnO)。
这种材料具有良好的导电性和透明性,广泛应用于太阳能电池、平板显示器、触控面板等领域。
通过在基材上镀覆azo 靶材,可以提高器件的性能,如提高太阳能电池的光电转换效率、降低平板显示器的功耗等。
二、azo 靶材镀膜的参数1.靶材种类:azo 靶材的主要成分为氧化亚铁(FeO)和氧化锌(ZnO),它们的比例决定了靶材的性能。
通常情况下,FeO 和ZnO 的比例为9:1。
2.镀膜厚度:镀膜厚度是影响器件性能的关键参数。
过薄的镀膜会导致器件性能下降,而过厚的镀膜则会增加器件的成本。
因此,在生产过程中需要精确控制镀膜厚度。
3.沉积速率:沉积速率决定了镀膜的生产效率。
提高沉积速率可以缩短生产周期,降低生产成本。
但同时,过高的沉积速率可能会影响镀膜的质量。
4.镀膜质量:镀膜质量是衡量azo 靶材镀膜性能的重要指标。
高质量的镀膜可以提高器件的性能,如提高太阳能电池的光电转换效率、降低平板显示器的功耗等。
5.应用领域:azo 靶材镀膜广泛应用于太阳能电池、平板显示器、触控面板等领域。
随着科技的不断发展,azo 靶材镀膜的应用领域还将不断拓展。
总之,azo 靶材镀膜是一种重要的电子材料,其性能和质量对器件的性能和可靠性具有重要影响。
浅析大面积镀膜中旋转阴极的优缺点
浅析大面积镀膜中旋转阴极的优缺点Dan Crowley, 黄新盈(021‐20902916)磁控溅射旋转阴极在现今大面积玻璃镀膜中广泛采用,与平面阴极相比,各有其优缺点。
本文尝试对旋转阴极的优缺点进行以下分析。
旋转阴极的优点主要有以下几点:1 靶材利用率高,可达90%。
同时也意味着更长的运行时间。
2 溅射速率高(通常是平面阴极的2‐3倍,具体视靶材种类而定)。
3 有效减少打弧和靶面掉渣,工艺稳定性好。
可以消除平面靶较易形成的再沉积区,这些被污染的靶面,极易产生掉渣然后落到玻璃基板上。
同样这些地方很容易产生打弧,打弧又造成了更多掉渣和大颗粒的形成。
所以旋转阴极消除了再沉积区,从而保证了镀膜工艺的长期稳定性。
4 无需“烧靶”,可以节省靶材消耗和烧靶时间。
5 快速便捷的换靶操作,在设计简捷的旋转阴极上可以实现,如SCI等。
这对配备多个旋转阴极的镀膜生产线特别有意义,节省时间意味着产能的提升。
6 低熔点靶材亦能使用高功率溅射。
因为靶材旋转,所以靶面没有一直处于等离子体区内,使溅射速率得以提高。
7 旋转靶材比平面靶材更加昂贵,但其极高的靶材利用率使得旋转靶的性价比更好。
而旋转阴极的缺点主要是:1 旋转阴极更加复杂,需要更多部件,需要驱动系统配合。
所以最初的设备投资要高于平面阴极。
2 旋转阴极有移动部件,生产中真空密封不时会有泄漏,即便是成熟的旋转阴极,能够可以做到简单,最小程度的更换密封,但相比平面阴极而言,仍需要更高的维护成本。
3 旋转阴极增加了系统中的不稳定因素,因为在生产中需要不停的旋转。
结论旋转阴极在大面积玻璃镀膜工业中,特别是Low‐e镀膜中扮演了重要的脚色,光伏和平板显示行业也逐步采用。
因为旋转阴极解决了平面阴极掉渣和靶材利用率的问题,并且提高了溅射速率。
但虽之而来的是增加了阴极机构的复杂性和初期投资。
旋转阴极所带来的好处将在后续的长期生产得到充分体现。
至于靶材成本,需要分别比较分析每种靶材的制造成本,利用率,回收价值…等因素来综合考虑。
镀膜玻璃常见缺陷说明
镀膜玻璃使用过程中常见缺陷的说明在镀膜玻璃的生产和使用过程中,由于生产或安装施工等方面的原因,往往使得上墙上窗后的镀膜玻璃产品存在这样或那样的质量缺陷,比如出现色差、划伤、掉膜、破裂等现象。
为了能更好的区分和界定这类缺陷,分析和鉴定缺陷产生的原因,在此我们对镀膜玻璃产品在安装使用后,常见的一些缺陷进行分类定义,并说明它可能产生的环节和原因,以便客户能更好的使用我们的产品。
一、玻璃的色差定义和说明:用人眼目测观察某些镀膜玻璃的反射颜色同标准样片或整批其它玻璃比较,有较明显的颜色或亮度方面的差异即为色差。
严格的说,玻璃片与片之间或同一片的不同部位都是存在色差的,也就是说它的反射和颜色是肯定存在差异的,但关键是这种差异的大小。
为了能定量的说明这种差异的大小,在国际上一般是用采用CIE1976L*a*b*色度空间值的D E值来判断,国家标准是允许D E£ 3为合格。
但通常来说,伟光镀膜玻璃产品的D E值一般远远小于标准的允许值,这也正是伟光产品的长处和高质量的保证。
因为我们知道,对一些人眼较敏感的颜色,如金色和紫红色等,其D E值在较小范围内,人眼也能很明显观察出来色差的。
产生原因:产生片与片之间或批与批之间的产品色差,其常见原因有:1、生产方面:由于生产工艺调试没有达到稳定状态,或镀膜室真空状态产生波动而引起的。
另外,由于靶材短路、断路以及传送线出现故障等引起靶材跳闸也有可能产生色差。
这些产生色差的原因都是在生产中可以控制和及时发现的,所以出现色差的产品一般是会检验出来的,是不会出厂。
2、原片原因:由于浮法玻璃原片批与批之间本身的颜色或透过率有变化,或混用了不同原片生产厂家的原片。
3、客户在使用中混用了同一型号但厚度不同的镀膜玻璃,或混用了不同生产厂家的镀膜玻璃产品。
4、玻璃受到了污染:比如幕墙部分的开启窗部分,由于长期开启等原因,或某些玻璃局部受污染或灰尘较多而造成色差。
二、划伤或擦伤定义和说明:镀膜玻璃表面和其它较硬的物质相对滑动或磨擦造成的线状或带状的伤痕为划伤或擦伤,主要表现为划伤或擦伤部位的玻璃透光率增高,或膜面脱落透亮。
溅射靶材的厚度标准
溅射靶材的厚度标准溅射靶材在溅射镀膜过程中是一个非常重要的材料,其厚度直接影响到溅射速率、靶材利用率、厚度均匀性、颗粒度、溅射气体消耗、溅射功率、溅射压力和溅射稳定性等方面。
因此,确定溅射靶材的厚度标准是至关重要的。
一、溅射速率溅射速率是指单位时间内从靶材上溅射出的粒子数目的多少。
溅射速率与溅射电流、气体压力、气体组成和靶材的物理性质等因素有关。
在一定的条件下,溅射速率与靶材的厚度成正比,因此,确定靶材的厚度标准需要考虑溅射速率的要求。
二、靶材利用率靶材利用率是指在溅射过程中,靶材的有效利用程度。
在相同的溅射条件下,靶材的厚度越大,其利用率越高。
但是,过厚的靶材会导致溅射速率的降低,同时还会增加制造成本。
因此,在确定靶材的厚度标准时,需要综合考虑溅射速率和靶材利用率的要求。
三、厚度均匀性厚度均匀性是指溅射靶材表面各处的厚度是否一致。
如果靶材的厚度不均匀,会导致溅射速率的不稳定,从而影响镀膜的质量。
因此,在确定靶材的厚度标准时,需要保证其厚度均匀性符合要求。
四、颗粒度颗粒度是指溅射靶材表面的颗粒大小和分布情况。
颗粒度的大小对溅射速率和镀膜质量都有一定的影响。
在确定靶材的厚度标准时,需要考虑其颗粒度是否满足要求。
五、溅射气体消耗溅射气体是用来产生等离子体的气体,其消耗量与靶材的厚度有一定的关系。
在一定的条件下,靶材的厚度越大,所需的溅射气体流量就越大。
因此,在确定靶材的厚度标准时,需要考虑溅射气体的消耗情况。
六、溅射功率溅射功率是指用于产生等离子体的电源功率。
在一定的条件下,靶材的厚度越大,所需的溅射功率就越大。
但是,过高的溅射功率可能会导致靶材表面的熔融和蒸发,从而影响镀膜的质量。
因此,在确定靶材的厚度标准时,需要考虑其与溅射功率的匹配情况。
磁控溅射镀膜靶材料
磁控溅射镀膜靶材料磁控溅射镀膜技术作为一种重要的表面修饰方法,在电子、光电、材料等领域有着广泛的应用。
而作为磁控溅射镀膜技术的核心材料——靶材,其选择和使用直接关系到溅射膜层的质量和性能。
本文将介绍磁控溅射镀膜靶材料的分类、常见材料及其特点,并讨论靶材的制备工艺和质量控制方法,旨在为磁控溅射镀膜相关科研和工业应用提供指导。
首先,磁控溅射镀膜靶材料可以按照化学性质和物理性质进行分类。
从化学性质上看,主要分为金属靶材、合金靶材和化合物靶材等。
金属靶材主要包括铜、铝、钛等,合金靶材常见的有镍铬合金、钴铬合金等,化合物靶材则包括氮化物、氧化物等。
从物理性质上看,靶材可以分为导体靶材和绝缘体靶材。
常见的磁控溅射镀膜靶材包括铝、铜、钛等金属靶材。
这些材料具有较高的导电性和良好的热稳定性,可以在真空环境下长时间稳定地发挥作用。
另外,氮化铝、二氧化硅等绝缘体靶材也广泛应用于磁控溅射镀膜领域。
绝缘体靶材的使用可以改变溅射过程中的离子束能量分布,提高溅射膜层的质量和均匀性。
靶材的制备工艺对镀膜质量及性能起着至关重要的作用。
首先,靶材的制备要求其成分纯净,无杂质。
通常采用电弧熔炼、电子束熔炼等方法制备金属靶材;而化合物靶材的制备则需要采用化学气相沉积、固相反应等特殊工艺。
其次,制备过程中要确保靶材的均匀性,避免出现微观或宏观缺陷。
同时,靶材的密度和结构也需要进行严格控制,以确保其在溅射过程中的稳定性和利用率。
为了保证磁控溅射镀膜的质量,还需要对靶材进行质量控制。
首先,靶材的表面需要进行表面处理,以去除氧化物和杂质,提高溅射效率。
其次,靶材的形状和尺寸需要进行严格控制,以确保靶材与阴极的匹配度和镀膜的均匀性。
最后,溅射过程中需要监测靶材的损耗情况,及时更换和调整靶材,以保证膜层的一致性和稳定性。
综上所述,磁控溅射镀膜靶材是影响溅射膜层质量和性能的重要因素。
不同的靶材具有不同的特点和适用范围,其制备和质量控制工艺也需要注意。
- 1、下载文档前请自行甄别文档内容的完整性,平台不提供额外的编辑、内容补充、找答案等附加服务。
- 2、"仅部分预览"的文档,不可在线预览部分如存在完整性等问题,可反馈申请退款(可完整预览的文档不适用该条件!)。
- 3、如文档侵犯您的权益,请联系客服反馈,我们会尽快为您处理(人工客服工作时间:9:00-18:30)。
靶材质量对大面积镀膜生产的影响The influence of the target equality on the large areacoating glass production胡冰王烁摘要:真空磁控溅射镀膜现在已经成为工业镀膜生产中最主要的技术之一。
靶材作为磁控溅射镀膜使用的大宗原材料,其质量对膜层性能有很大的影响,同时会影响到镀膜的生产效率和成本,对大面积玻璃镀膜企业有很大的影响。
本文结合生产实际使用情况,将靶材对镀膜生产影响的主要特征参数,包括靶材的密度、晶粒尺寸、纯度、与衬管(背板)连接质量等因素进行了分析和研究,并在其参数控制方面给予相关建议。
Abstract:In present,vacuum magnetron sputtering coating has become one of the main techniques of coating industry . Be used as bulk raw materials of the magnetron sputtering coating,targets have a great influence on film quality, efficiency and cost of coating production,have a great influence on large area coating glass industry.In this paper, the main characteristic parameters of the targets, including the grain size , purity, density of target materials and quality of bonding,etc. which influence the quality of the large area coating were analysised and studied combine with the actual production,some advices in the parameters control were given.关键词大面积镀膜Low-E玻璃靶材Key words Large area coating low-emissivity glass targets1 引言现代建筑大多已开始采用大面积玻璃采光,这一方面带给我们更明亮的房间以及更宽阔的视野,另一方面由于透过玻璃传递的热能远高于周围墙体,导致整个建筑物的使用能耗明显增大。
经过几十年的发展,低辐射(Low-E)镀膜玻璃在建筑领域得到了广泛的应用,对降低建筑能耗和节约能源有着显著的作用。
目前制备低辐射薄膜成熟的技术包括化学气相沉积(在线Low-E)和真空磁控溅射镀膜(离线Low-E)两种。
相对于颜色单一,辐射率较高的在线Low-E玻璃,离线Low-E玻璃辐射率和隔热系数更低,颜色种类多,遮阳系数和透光率均可根据设计师的要求进行调整,制备成中空玻璃或夹层玻璃进行使用,更适合社会发展对节能越来越高的要求,是社会持续发展的必然趋势。
相对发达国家高达90%以上低辐射玻璃的使用率,中国的Low-E玻璃普及率仅12%左右,其在中国还有非常大的发展空间。
但是相对于普通玻璃和在线Low-E玻璃,离线Low-E玻璃的生产成本比较高,这在一定程度上限制了其应用,国内玻璃加工企业有义务不断降低镀膜产品的生产成本,使低辐射玻璃加快普及进程,节约能源,改善环境,实现社会的可持续发展。
真空磁控溅射镀膜能有效地降低靶室的工作压强和靶的工作电压,提高溅射和沉积速率,降低基片温度,减小等离子体对膜层的破坏,特别适合于大面积镀膜生产。
影响溅射成膜速度和质量的因素除包括真空度、溅射气氛、气压、使用功率和靶基距等一系列设备工艺条件外,靶材作为镀膜使用的大宗原材料其本身的特性,包括靶材形状、纯度、密度、孔隙度、晶粒度及绑定质量都对成膜品质和溅射速率有非常大的影响。
优质的靶材不但可以保证好的膜层质量,也可以延长Low-e产品的使用周期,更重要的可降低生产成本,提高生产效率,对镀膜玻璃行业有很大的经济效益。
因此,对于大面积镀膜行业,靶材的相关研究也显得尤为重要。
2 靶材形状的影响对于大面积镀膜常用的靶材按形状分包括平面靶和旋转靶,常用的平面靶包括铜靶、银靶、镍铬靶和石墨靶,常用的旋转靶包括锌铝靶、锌锡靶、硅铝靶、锡靶、氧化钛靶和氧化锌铝靶等。
靶材形状影响磁控溅射镀膜的稳定性和膜层特性,以及靶材的利用率,因此可以通过改变靶材的形状设计提高镀膜质量和生产效率,节约成本。
平面靶材在磁控溅射过程中,由于磁场分布存在强度的不同(磁场切线方向的磁场最强),靶材溅射过程中表面区域存在溅射集中的环形“跑道”(如图1),靶材利用率低(仅有35%左右)。
虽然旋转靶的利用率很高,但制备成本较高,对于一些金属靶材依然设计为平面靶。
使用平面靶时,可以根据实际磁场分布情况,加厚跑道部分材料厚度以提高靶材利用率,提高生产效率。
而尺寸较大的平面靶很难整靶成型,需要制备成尺寸较小的靶材进行拼接使用,拼接的缝隙可以为靶材热膨胀提供空间,但缝隙较大时,容易有空气残留,造成抽真空困难。
镀膜过程中残余气体的释放会影响膜层的质量和均匀性,所以在靶材尺寸设计过程中,应考虑缝隙的大小,一般在0.5mm左右较佳。
图1 平面靶溅射环形跑道而对于旋转靶,溅射过程中靶材旋转,溅射区不断更换,几乎不会出现类似于平面靶材的溅射跑道。
但在磁控溅射过程中,磁钢内部磁铁的环形设计使得磁场存在一定的边缘效应,即靶材磁场端部与中间直线区域强度不一致。
由于端部磁场强度大,正交电磁场对溅射离子造成影响,导致端部溅射速率快,产生不均匀刻蚀现象,直筒状的旋转靶材会出现中部材料较厚时,边部溅射穿,利用率普遍较低。
因此,旋转靶材一般设计为狗骨状(即中间直径小,两端直径大,见图2),以提高靶材利用率(利用率可达80%以上),节约生产成本。
图2 旋转靶材形状设计3 靶材相对密度和孔隙的影响靶材的相对密度是靶材实际密度与理论密度的比值,单一成分靶材的理论密度为结晶密度,合金或混合物靶材的理论密度通过各组元的理论密度和其在合金或混合物中所占比例计算得出的。
热喷涂靶材组织疏松多孔,含氧量高(即使是真空喷涂,也难以避免合金靶材中氧化物和氮化物的产生),表面呈现灰色,缺少金属光泽,吸附的杂质、湿气是主要的污染源,妨碍高真空的迅速获得,容易导致溅射过程中放电,甚至烧坏靶材,图3为安装使用初期出现严重放电而烧坏的致密度低的喷涂靶材照片。
图3 放电严重致使烧损的喷涂靶同时,靶材溅射表面瞬间高温容易使松散颗粒团装掉落,污染玻璃表面,影响镀膜质量。
国家对于镀膜玻璃表面点状脱膜有明确的规定,规定见表1,相对密度越高,成膜速率越快,溅射过程越稳定。
根据靶材制备工艺的差异,熔铸靶相对密度应保证在98%以上,粉末冶金靶材应保证在97%以上以满足生产使用。
因此需严格控制靶材致密度以减少掉渣现象的发生。
喷涂靶材密度较低,制备成本也低,当相对密度能保证90%以上时,一般不影响使用,目前国内使用的SiAl靶均为喷涂靶。
表1 镀膜面中心部位的点状缺陷要求缺陷名称说明GB18915要求针孔直径<0.8mm无要求0.8mm≤直径<1.2mm不允许密集1.2mm≤直径<1.6mm允许中部:3*S个;75mm边部8*S个1.6mm≤直径≤2.5mm允许中部:2*S个;75mm边部5*S个直径>2.5mm不允许斑点1.0mm<直径≤2.5mm允许中部:5*S个;75mm边部6*S个2.5mm<直径≤5.0mm允许中部:1*S个;75mm边部4*S个直径>5.0mm不允许1.针孔指观察到完全透光的点;斑点指膜层未完全脱落反射观察仍可见少量膜层;2.针孔密集是指直径100mm范围内超过20个针孔;3.S是以平方米为单位的玻璃板面积,保留小数点后两位。
除致密度外,如果靶材在生产过程中出现异常,如大颗粒脱落或受热出现缩孔,会形成较多气孔(内部缺陷),靶材内部出现较大(熔铸靶>2mm,喷涂靶>0.5mm)或较密集的孔洞都会由于电荷集中而出现放电,影响使用。
密度低和含有气孔的靶材在后续处理、搬运或安装时,极易发生碎裂。
相对密度高、孔隙少的靶材导热率好,溅射靶材表面的热量易于快速传递给靶材内表面或衬管内的冷却水,散热好,从而保证了成膜过程的稳定性。
4 靶材晶粒尺寸和结晶方向的影响同一成分的靶材,晶粒尺寸较小的靶材比晶粒尺寸大的沉积速率快,这主要是由于晶界在溅射过程中更容易受到攻击,晶界越多,成膜就越快。
晶粒尺寸的大小除影响溅射速率外,也会影响成膜质量。
例如在Low-E产品生产过程中,NiCr作为红外反射层Ag的保护层,其质量对镀膜产品有非常大的影响。
由于NiCr膜层的消光系数比较大,所以一般镀的很薄(约3nm左右)。
如果晶粒尺寸过大,溅射时间短,会造成膜层致密性差,降低其对Ag层的保护作用,导致镀膜产品氧化脱膜。
晶粒尺寸对于均匀性的影响则较小,研究表明,同一制备工艺制备的四个同材料金属靶,通过不同的热处理时间使晶粒尺寸从0.5到3.3mm 变化,发现膜层的均匀性并没有差异。
因此晶粒尺寸的大小对成膜的均匀性影响很小或者没有影响。
但是晶粒尺寸的均匀性则会直接影响到成膜的均匀性,鉴于靶材是在不断地消耗,除考虑靶材同一层面的均匀性外,也应考虑靶材厚度方向上的均匀性,要求不同截面的晶粒尺寸尽量一致,进而保证不同时期溅射成膜的均匀性。
图4为不同厂家NiCr 靶的微观组织对比,由晶相照片可以看出靶a的晶粒尺寸大小和均匀性都比靶b的好,靶a对应溅镀成膜的质量更高。
据日本Energy公司研究发现,若将钛靶的晶粒尺寸控制在100 μm以下,且晶粒大小的变化保持在20%以内,其溅射所得薄膜的质量可得到大幅度改善。
a b图4 NiCr靶的微观组织对比对于多晶体,晶体的晶粒在不同程度上会沿着某些特殊的取向排列。
在靶材溅射过程中,低能离子不能从固体表面直接溅射出原子,而是把动量转移给被撞原子,引起晶格点阵上原子连锁碰撞。
这种碰撞将沿着晶体点阵的各个方向进行,但在原子最紧密排列点阵方向上最为有效。
因此,靶表原子容易沿着原子最紧密排列方向择优溅射出来,材料的结晶方向对溅射速率和成膜厚度均匀性有很大影响,常可以通过改变靶材结晶结构的方法来提高的射速率和成膜质量。
例如通过控制硅靶的加工工艺,使其晶粒存在一定的择优取向,可以将膜层的膜厚偏差从10%降低至5%。
不同材料具有不同的结晶结构,应采用不同的成型、热处理方法和条件进行加工,使靶材具有最优的晶粒取向,提高磁控溅射成膜速率和膜层质量。