无碳小车底板夹具设计说明书
(完整版)无碳小车设计说明书
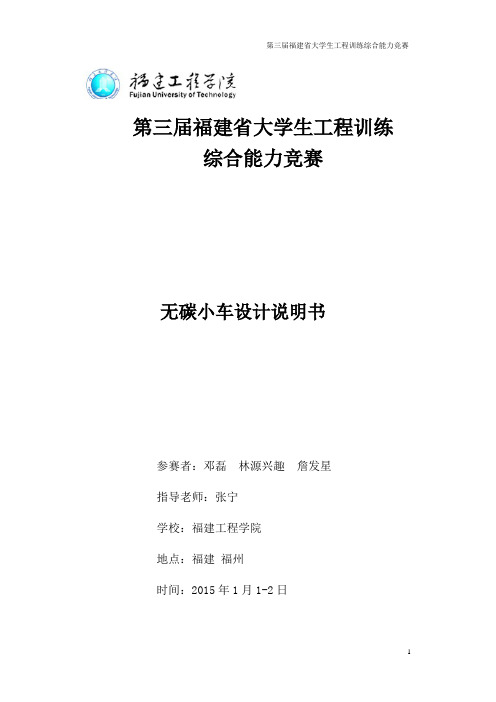
第三届福建省大学生工程训练综合能力竞赛无碳小车设计说明书参赛者:邓磊林源兴趣詹发星指导老师:***学校:福建工程学院地点:福建福州时间:2015年1月1-2日摘要第三届福建省大学生工程训练综合能力竞赛命题主题为“无碳小车越障竞赛”,并为接下来的第四届国赛做好准备。
我们在设计小车过程中特别注重设计的方法,力求通过对命题的分析得到清晰开阔的设计思路;作品的设计做到有系统性规范性和创新性;设计过程中综合考虑材料、加工、制造成本等给方面因素。
我们借鉴了参数化设计、优化设计、系统设计等现代设计发发明理论方法;采用了MATLAB、PROE、CATIA等软件辅助设计。
我们把小车的设计分为三个阶段:方案设计、技术设计、制作调试。
通过每一阶段的深入分析、层层把关,是我们的设计尽可能向最优设计靠拢。
方案设计阶段根据小车功能要求我们根据机器的构成(原动机构、传动机构、执行机构、控制部分、辅助部分)把小车分为车架、原动机构、传动机构、转向机构、行走机构、微调机构六个模块,进行模块化设计。
分别针对每一个模块进行多方案设计,通过综合对比选择出最优的方案组合。
我们的方案为:车架采用三角底板式、原动机构采用了锥形轴、传动机构采用齿轮、转向机构采用曲柄连杆、行走机构采用双轮驱动、微调机构采用微调螺母螺钉。
其中转向机构利用了调心轴承、关节轴承。
技术设计阶段我们先对方案建立数学模型进行理论分析,借助MATLAB分别进行了能耗规律分析、运动学分析、动力学分析、灵敏度分析。
进而得出了小车的具体参数,和运动规律。
接着应用PROE软件进行了小车的实体建模和部分运动仿真。
在实体建模的基础上对每一个零件进行了详细的设计,综合考虑零件材料性能、加工工艺、成本等。
小车大多是零件是标准件、可以购买,同时除部分要求加工精度高的部分需要特殊加工外,大多数都可以通过手工加工出来。
对于塑料会采用自制的‘电锯’切割。
因为小车受力都不大,因此大量采用胶接,简化零件及零件装配。
无碳小车设计说明书

无碳小车设计说明书小组成员:指导教师:学校:一. 设计思路:1.根据设计要求,为达到无碳小车走8字形轨迹重叠的目的,无碳小车应具备重力势能的转换和周期性的转向的功能,即小车分为传动机构和导向机构两部分。
其中传动机构要求能量损耗少、传动比精确,故优先选用齿轮和皮带轮传动。
导向机构要求方向控制度高、摩擦损失小,选用凸轮直线滑块机构。
2.为减轻车身质量同时保证小车刚度要求,小车采用尼龙作为底板材料,上面安装轴承座以支撑输入轴、驱动轴、吊挂重物的立杆等,小车导向机构中的滑块也需固定在底板上。
4.通过计算并确定两齿轮的传动比i,并实现小车驱动轮每行走i个周长长度,转向机构运动实现一个周期,小车也行走一个完整的8字路线。
为了使小车适应不同间距桩,我们采用凸轮机构,控制小车走重叠的8字,使得小车的工作效率更高。
二. 工作原理:当重物下落时,细绳绕过立杆定滑轮带动驱动后轮上面的绕线轮,驱动中间齿轮转动驱动后轮前进,同时通过齿轮啮合传动带动凸轮旋转,带动转向前轮周期性左右转向,从而实现小车在前进过程中自动转向。
这样小车便能在重力势能驱动下沿着“8”形路线前进,并能自动绕过障碍物。
三、设计说明我们可以将小车行走路线简化为余弦曲线和两段圆弧来处理,通过小车的传动比以及驱动轮的大小我们可以计算出该余弦曲线的幅值,可计算出小车的出发点,我们将小车出发位置定在向左转弯的圆弧中点。
我们以绕8字的两个桩位置方向为X轴,在水平面内垂直于X轴为Y 轴方向,通过计算桩间距,障碍物距离,传动比,驱动轮周长可以得出确定曲线方程,通过数学知识我们可以得出小车在出发点的前轮偏向角度(即凸轮角度),偏向角度可以适当调节。
由此我们便可以得出小车出发时垂直摆桩方向的距离以及此时小车前轮的偏向角度,从而确定小车的理论出发位置。
四、设计总结对于大赛给定的命题,重力势能转换为机械能的能量转换原理是设计的重点之一,小车动力传动结构和摩擦传动装置的设计是最重要的部分。
无碳小车 设计说明资料
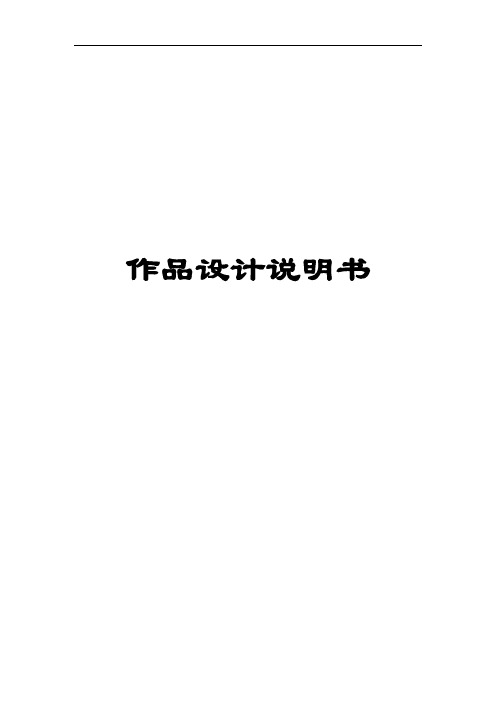
作品设计说明书摘要我们把小车的设计分为三个阶段:方案设计、技术设计、制作调试。
通过每一阶段的深入分析、层层把关,是我们的设计尽可能向最优设计靠拢。
方案设计阶段根据小车功能要求我们根据机器的构成(原动机构、传动机构、执行机构、控制部分、辅助部分)把小车分为车架、原动机构、传动机构、转向机构、行走机构五个模块,进行模块化设计。
分别针对每一个模块进行多方案设计,通过综合对比选择出最优的方案组合。
我们的方案为:车架采用三角底板式、原动机构采用了带轮轴、传动机构采用带轮、转向机构采用凸轮机构、行走机构采用双轮驱动。
技术设计阶段我们先对方案建立数学模型进行理论分析,借助MATLAB分别进行了能运动学分析和动力学分析,进而得出了小车的具体参数,和运动规律y 以及确定凸轮的轮廓曲线;接着应用Solidworks软件进行了小车的实体建模和部分运动仿真。
在实体建模的基础上对每一个零件进行了详细的设计,综合考虑零件材料性能、加工工艺、成本等。
小车大多零件是标准件,可以购买,同时除部分要求加工精度高的部分需要特殊加工外,大多数都可以通过手工加工出来。
调试过程会通过微调等方式改变小车的参数进行试验,在试验的基础上验证小车的运动规律同时确定小车最优的参数。
关键字:无碳小车参数化设计软件辅助设计目录摘要 (2)一绪论 (4)1.1命题主题 (4)1.2小车功能设计要求 (4)1.3小车整体设计要求 (5)1.4小车的设计方法 (6)二方案设计 (7)2.1车架 (8)2.2原动机构 (8)2.3传动机构 (8)2.4转向机构 (9)2.5行走机构 (10)三技术设计 (10)3.1建立数学模型 (11)3.2参数确定 (14)3.3零部件设计 (15)3.4小车运动仿真分析 (18)四小车制作调试及改进 (20)4.1小车制作流程 (20)4.2小车调试方法 (20)4.3小车改进方法 (20)五评价分析 (21)5.1小车优缺点 (21)5.2小车改进方向 (21)六参考文献 (22)一绪论1.1命题主题根据第四届全国大学生工程训练综合能力竞赛主题为“无碳小车越障竞赛”。
无碳小车设计说明书
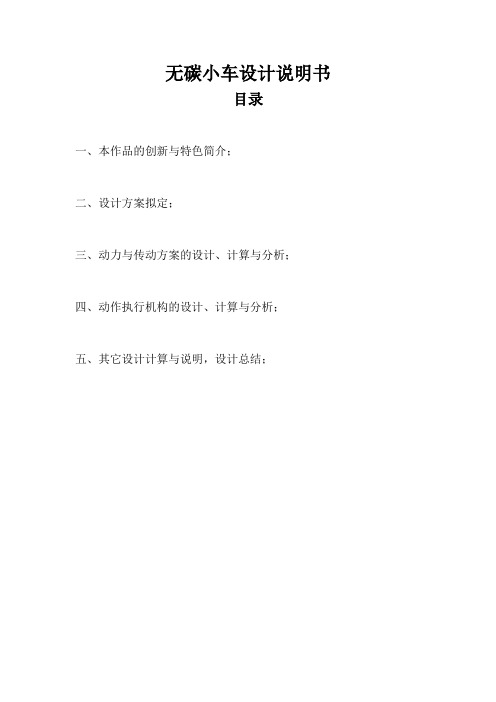
无碳小车设计说明书目录一、本作品的创新与特色简介;二、设计方案拟定;三、动力与传动方案的设计、计算与分析;四、动作执行机构的设计、计算与分析;五、其它设计计算与说明,设计总结;一:本作品的创新与特色简介;①所有的动力来自载荷重物,所纯机械结构,无碳排放;②在转向方面,采用内凸轮连杆机构,使得转向的角度、时间更加精确,并辅助以有图的可调机构,是转向调节更加明确。
③在重物下落阶段,增加了一动滑轮,使得做功行程加长,并合理的利用了扭矩。
④绕桩曲线部分的轨迹无需精确的计算出,由上图的机构可在完成后对中间连杆进行调试,已达到目标要求。
二:设计方案拟定;小车的方案设计关键在于传动部分与转向部分。
①传动部分;传动部分的问题在于是用什么进行传动,齿轮、带轮、直接驱动等。
最后结合传动的效率、制作的难易程度,最终确定了采用二级齿轮进行传动,如有图所示。
此方案的优点在于,以中间轴为主动轴,以小于1的传动比带动后轮,再以大于1的传动比带动凸轮轴,这样就很好的解决了行驶路程与转向周期间的关系,并且将传动比控制在合理数值内。
另外,以一个动滑轮来增加做功行程,减小瞬时扭矩,使小车前进平缓。
缺点在于,采用了二级齿轮组,使得摩擦耗能增加,机械效率降低。
②转向部分;转向部分在于采用什么机构,最大的争议在于是采用内凸轮还是外凸轮。
最终确定是采用内凸轮连杆机构。
原因在于采用外凸轮的话需要在连杆的回程部分提供一个力——增加一个弹簧;如果这样的话,可能会因为的弹簧的弹性系数,及位置的放置问题上增加设计的难度。
而采用内凸轮的话就不存在这些问题,不过增加了整体的重量,但这可以通过将凸轮在合理的条件下将其镂空来解决。
为了使后期调整时有更大的可能性,因此在连杆部分采用了右图的结果,如此便可以使小车的转向更加的准确。
③材料方面;除了前后轮采用有机玻璃之外,其余的材料都采用铝材。
底板:厚3mm的铝板,300*160*3.后轮:直径160的有机玻璃,厚5mm。
《无碳小车设计说明》-公开课件
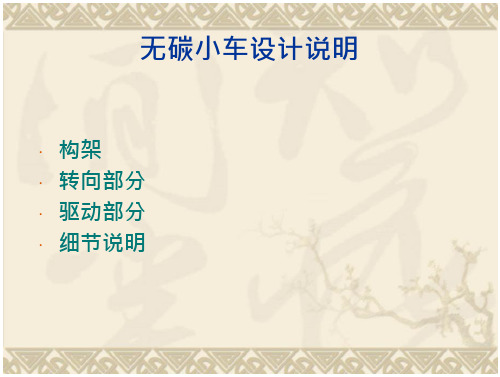
·在整个过程中,重力势能完 全转换为小车运动过程的损
耗。使小车行进的更远.
4.细节设计
· 车身 · 车轮 · 轴承 以减小小车重力和动过程
· 传输功率=转矩X角速度 ,通过一系列的齿 轮,带轮,转轴产生转速比,使作用在后 轮的转矩和阻尼转矩平衡,物块低速匀速 下落。
· 在后轮转轴上安放多个不同半径的带轮, 微调转矩,适应不同的环境下阻力的不同。
· 制作多套后轮,微调转矩。改变后轮时, 也要相应的改变转向传动轮的大小,同时 保持车身水平,适当调整前轮转轴的长度。 (现场可实现)
无碳小车设计说明
· 构架 · 转向部分 · 驱动部分 · 细节说明
1.构架部分
· 小车采用三轮结构(1个转向,2个驱动) · 重物落差0.5米物重1kg.
2.转向
· 转向机构与驱动轴相连
· 小车的转向轮周期性的摆动
· 计算传动机构,使小车行使200厘米时,转 向轮摆动一个周期。
· 确定连杆在转盘有位置,尽量减小转向轮 的摆动角度,从而使小车先驱的实际距离 变大。确定初始位置与摆轮角度的关系。
3.驱动
· 原理:绳拉力为动力。将物块下落的势能 尽可能多的转换为小车的动能,进而克服 阻力做功。物块在下落的过程中不可避免 的要与小车发生碰撞,碰撞过程必然要有 能量损失,所以要解决的问题:1下降过程 中,尽可能的降低下落的速度;2在将要下 降到小车时,改变转速比,使物块减速下 落,进一步减少碰撞损耗。
·
二、小车的起始和结束过程
· 梯形原动轮的设计实现小车的起 动和物块的从低速到减速下落。 减小因碰撞而损失的能量。
梯形原动轮
无碳小车设计说明书
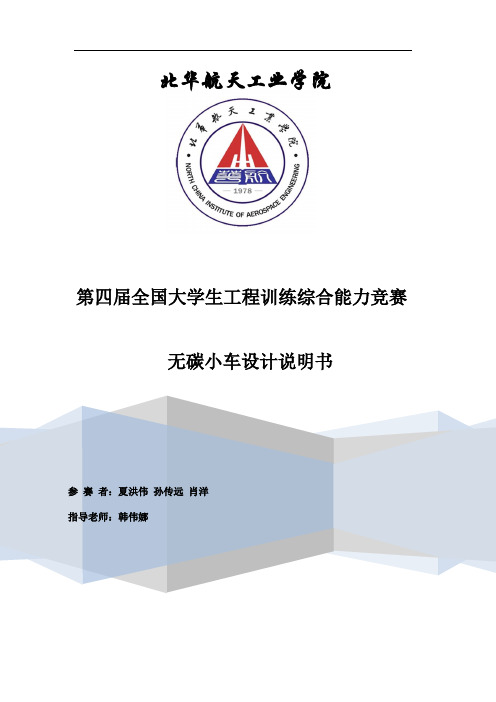
北华航天工业学院第四届全国大学生工程训练综合能力竞赛无碳小车设计说明书参赛者:夏洪伟孙传远肖洋指导老师:韩伟娜第四届全国大学生工程训练综合能力竞赛无碳小车设计说明书参赛者:夏洪伟、孙传远、肖洋指导老师:韩伟娜目录第1章方案设计..................................................................................................... - 1 -1.1 车架................................................................................................................ - 3 -1.2 原动机构...................................................................................................... - 3 -1.3 传动机构...................................................................................................... - 4 -1.4 转向机构........................................................................................................ - 7 -1.5 行走机构........................................................................................................ - 9 -1.6 微调机构........................................................................................................ - 9 -第2章技术设计................................................................................................... - 11 -2.1运动学分析模型........................................................................................... - 11 -2.2参数确定....................................................................................................... - 13 -2.3零部件设计................................................................................................... - 13 -附录................................................................................................................... - 15 -第1章方案设计通过对小车的功能分析,“无碳小车越障竞赛”通常主要由车体、能量转换、传动和转向等部分组成。
小车设计说明书
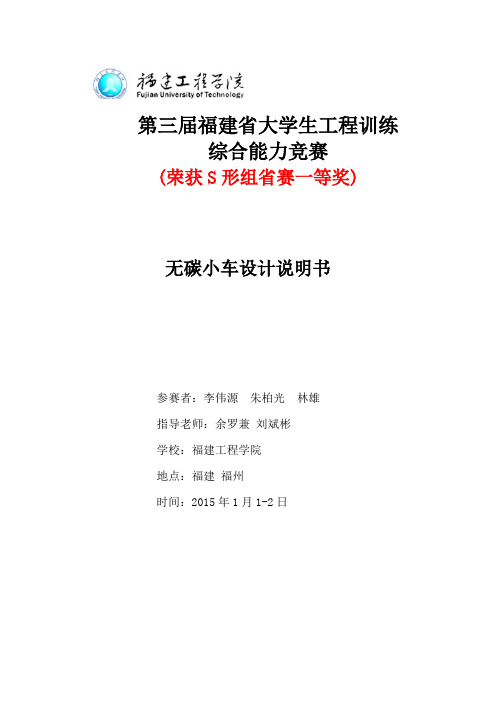
第三届福建省大学生工程训练综合能力竞赛(荣获S形组省赛一等奖)无碳小车设计说明书参赛者:李伟源朱柏光林雄指导老师:余罗兼刘斌彬学校:福建工程学院地点:福建福州时间:2015年1月1-2日一、概要 (3)二、分析 (3)三、原理设计 (4)1、驱动机构 (4)2、转向机构 (5)3、后轮差速 (5)四、参数设计 (6)1、轨迹设计 (6)2、转角设计 (6)3、带轮设计 (7)4、小车部分零件的设计 (8)(1)拨盘 (8)(2)转向轮销 (9)(3)转向轮槽零件图: (11)(4)皮带轮 (12)(5)转向轴 (13)实体图: (13)(6)转向连杆 (15)(7)拨槽 (16)(8)拨槽加工工艺分析 (17)(9)齿轮 (18)(10)底板 (19)(11)后驱动轴零件图: (20)五、小车装配完成图片 (22)“无碳小车”设计说明书一、概要此次无碳小车的设计主要是利用重物下落的重力势能作为原动力,来驱动小车前进以及使小车能按规定绕开障碍物。
重物质量M=1kg,下落高度H=400mm,每个障碍物之间隔0.9米、1米、1.1米。
二、分析1、为使得小车能够行走,首要解决的就是小车驱动,要设计小车的驱动机构;2、为使得小车能够转弯,并能够绕开等距离的障碍物,所以要设计一个能够走S形路线的周期性的转向机构;3、由于只有一个动力源,所以还要设计一套小车的传动机构;4、为了使得小车能够顺利转弯,还要解决小车后轮的差速问题。
三、原理设计1、驱动机构图1左侧部分为我们的驱动简图,考虑到小车的启动时需要较大的启动力矩,同时为使得重物的重力势能能够尽可能大地转化到有利小车行走的方面,与重物下落连线驱动圆锥滚筒设计成为如图所示,再考虑,为使得小车走的路程要长,所以,重物下落的行程要经过一对直齿圆柱齿轮放大。
所以,传动流程:重物→圆锥滚筒→大齿轮→小齿轮→后驱动轮2、转向机构图2为小车的前轮转向部分,为使得小车能够绕开定距离的障碍物,小车前轮转向要设计成具有周期性摆动的转向机构。
无碳小车设计说明书

无碳小车设计说明书一、基本构思通过对小车的功能分析小车需要完成重力势能的转换、驱动自身行走、形成固定路线。
在小车行走时尽量较小摩擦,实现能量较大化的转换。
而且需要灵活绕过障碍物。
在选择方案时综合考虑功能、材料、加工、制造成本等各方面因素,同时尽量避免直接决策,减少决策时的主观因素,使得选择的方案能够综合最优。
二、驱动机构1.通过重物自由下落,将重力势能转化为动能,由重物下落带动绕线轮转动,从而实现能量的转换。
2.为了增加下车的稳定性,在设计重物支撑杆时采用了三根杆,这样在小车转弯的时候控制重物左右摆动的角度。
3.在设计绕线轮时综合考虑到,要让小车跑的稳定,能轻松启动,而且跑得更远,设计成一个半径较小的二阶的绕线轮。
4.为了增加美光和方便,将固定线直接套在轴上,这样减小工作量,而且更美观更便捷。
三、传动机构1.重物的下落通过绕线轮(黄色)带动主动轴转动,然后通过二级齿轮(红色)将动力传递到后轮从动轴,从而驱动后轮转动。
2.二级齿轮实现对能量的储存。
四、转向机构(绿)1.转向机构采用偏心轴+曲柄、连杆机构(蓝色)。
U型槽的圆周运动通过连杆转化为曲柄的前后摆动,从而实现小车前轮的摆动。
(具有简单、高效、摩擦力小、能量损耗小的特点)2.还有可以无极可调。
这实现了创新,也非常符合比赛规则。
五、车身及其后轮等其他机构1.将其中的一个后轮变为从动轮,保证了小车的正常运行,而且增加差速,让下车启动更加轻松容易,跑的的也更加稳定。
2.降低了底板的高度,增加了小车的稳定性3.支撑杆支座的设计,采用尼龙,使车身更轻,更加美光。
4.后轮选用亚克力板,在车轮三割去三个圆形快,减轻车身重量,强度达到要求,美观实用。
- 1、下载文档前请自行甄别文档内容的完整性,平台不提供额外的编辑、内容补充、找答案等附加服务。
- 2、"仅部分预览"的文档,不可在线预览部分如存在完整性等问题,可反馈申请退款(可完整预览的文档不适用该条件!)。
- 3、如文档侵犯您的权益,请联系客服反馈,我们会尽快为您处理(人工客服工作时间:9:00-18:30)。
无碳小车底板夹具设计说明书目录1 零件分析 (1)1.1 零件的作用 (1)1.2 零件的工艺分析 (2)1.3 零件的生产类型 (2)2 确定毛坯类型绘制毛坯简图 (2)2.1 选择毛坯 (3)2.2 确定毛坯的尺寸公差和机械加工余量 (3)2.3绘制毛坯简图 (3)3 工艺规程设计 (4)3.1 定位基准的选择 (4)3.2 拟定工艺路线 (4)3.3设备及工艺装备的选用 (7)3.4加工余量、工序尺寸和公差的确定 (8)3.5 切削用量的计算 (9)3.6 时间定额的计算 (11)4 专用钻床夹具的设计 (13)4.1 夹具设计的任务 (13)4.2 拟定床夹具结构方案与绘制夹具草图 (13)4.3 绘制夹具装配总图 (14)4.4 夹具装配图上标注尺寸、配合及技术要求 (14)5 参考文献 (15)1. 零件分析1.1 零件作用底板是无碳小车的一个主要零件,在无碳小车结构中起着至关重要的作用,它涉及到小车其他零件的安装和定位,用以支承整个车体,在底板上会安装用以支承轴的支撑架和控制转向的摩擦板,它对无碳小车的转向是否准确起着决定性的作用。
1.2零件的工艺分析由零件图中可知,底板的材料为有机玻璃,该材料对支承车体重量和打孔、铣削等加工能够适应,有很好的强度刚度和韧性。
底板从零件图上可以看出,形状较为简单,属于典型的板类零件,为实现底板上其他零件的安装和定位,其上各个孔以及槽的定位有严格的公差要求,加工精度要求高,作为其他零件安装定位的平台,底板本身应具有一定的平面度要求,底板四周为非工作面,不参与定位和安装,因此工艺要求较低,可采用精度较高的材料作为毛坯。
底板中φ8mm的孔用于安装支撑驱动轴及传动轴的支撑架,涉及到驱动轴和传动轴的定位和齿轮的啮合,因此,应保证相应的平行度和对称度,同时,支撑架定位时也应考虑到孔距的公差要求,平行度应达到0.1,对称度达到0.1,定位精度则通过尺寸公差得到保证。
底板中的通槽是为了防止大齿轮在运动过程中与底板发生干涉,因此尺寸精度要求较低,但位置精度要求较高;阶梯槽是为了使8个φ8mm的孔及φ10的孔在同一工作面上,从而保证支撑块架与小车底板的配合精度,因此尺寸精度要求低,槽底面的平行度要求高。
底板的外形端面不参与定位和安装,精度要求较低,故采用铣床粗铣即可完成,底板中心线是底板上孔及槽的定位基准,在加工时应重点给予保证。
阶梯槽的槽底面平行度要求高,可通过精铣来达到相应的要求;φ8mm 孔及φ10mm的孔加工精度较低,可通过一次钻孔完成,φ19±0.021mm的孔要与轴承进行配合并经常进行拆装,因此,加工精度要求较高,可以通过先钻后镗的加工方法进行加工。
通槽加工时应考虑定位精度,可以通过铣削加工完成,保证中心线定位尺寸52±0.046mm;底板中其他表面加工精度较低,不需要进行加工,通过毛坯材料的精度得以保证,主要工作表面加工精度要求不高,可以通过正常的生产条件实现,采用较经济的方法保证质量,通过上述分析可以得出该零件的工艺性较好。
该底板中φ8mm和φ19±0.021mm的孔为主要工作表面,在设计工艺规程时应重点予以保证。
1.3确定零件的生产类型由设计题目可知,该产品的生产类型为中批生产2.确定毛坯类型、绘制毛坯简图2.1 选择毛坯由零件图可知,底板的形状较为规则,结构简单,并且尺寸并不大,生产类型为中批,毛坯选为板材。
因板材已经标准化,则选取厚度与底板相近的规格,底板表面为不加工表面,但应保证一定的平面度要求,选择厚度为10mm的板材,表面粗糙度为12.52.2 确定毛坯的尺寸公差忽然机械加工余量1. 毛坯的公差等级通过分析底板作用和主要加工表面的技术要求,确定该零件的公差等级为一般精度2.毛坯的粗糙度通过分析零件图底板各加工表面中粗糙度的值Ra,最大值为12.5,最小值是3.2,根据上述诸因素,确定板材的尺寸和机械加工余量加工表面零件尺寸机械加工余量毛坯余量底板左右端面 154 5(两端分别为5) 164底板上下端面 300 5 两端分别为5) 3103.工艺规程设计3.1 定位基准的选择定位基准有粗基准和精基准之分,通常先确定精基准,然后再确定粗基准。
1.精基准的选择由零件图分析可以得到,底板的中心线和底板底面是底板上孔和其他工作表面的设计基准,选用底板底面作为基准定位加工孔,以及其他工作表面,实现了设计基准和工艺基准的重合,保证了被加工表面的精度要求。
2.粗基准的选择选择底板的右端面作为粗基准,采用右端面定位加工工作表面可以使孔的加工精度达到要求。
3.2 拟定加工路线工艺路线的拟定是制订工艺规程的总体布局,包括确定加工方法,划分加工阶段,决定工序的集中与分散,加工顺序的安排以及安排热处理处理,检验及其他辅助工序(去毛刺、倒角等)。
它不但影响加工的质量和效率,而且影响工人的劳动强度、设备投资、车间面积、生产成本等。
因此,拟定加工路线是制订工艺规程的关键一步,必须在充分调查研究的基础上提出工艺方案,并加以分析比较,最终确定一个最经济合理的方案。
1.表面的加工方法的确定根据零件图上各加工表面的尺寸精度和表面粗糙度,查表2.25平面加工方案的经济精度和表面粗糙度,查表2.24孔加工方案的经济精度和表面粗糙度,确定各个表面的加工方法。
底板零件各表面加工方案加工表面尺寸偏差尺寸精度表面粗糙度加工方案备注底板下端面300 IT9 6.3 粗铣—半精铣底板左右端面154 IT9 12.5 粗铣底板左右斜面70×37 IT9 12.5 粗铣Φ10孔Φ10IT8 3.2 钻-镗2×φ19±0.021孔φ19IT8 3.2 镗94×15×1阶梯槽94×15×1 IT9 6.3 粗铣12×φ8孔Φ8 IT11 12.5 钻100×4通槽100×4 IT9 6.3 粗铣2.加工阶段划分通过分析底板零件图可知,该零件加工质量要求不高,可将加工阶段划分为粗加工、半精加工两个阶段,在粗加工阶段,首先将精基准加工好,使后续工序都将采用精基准定位加工,保证其他加工表面的精度要求,然后粗铣其他表面,在半精加工阶段进行下端面的半精铣和2×φ19±0.021mm 孔及φ8mm孔的加工。
3.工序的集中与分散通过分析零件图可知,零件外形尺寸较大,无法采用一次加工完成许多加工内容,因此,采用工序分散原则安排加工工序,通过多次装夹完成粗加工阶段,底板四端面铣削,在半精加工阶段,可以采用工序集中原则安排工序,通过一次装夹在加工中心完成所有孔的加工。
4.工序顺序的安排(1)机械加工工序遵循先基准后其他原则,首先加工基准、底板下端面,遵循先粗后精原则为先安排粗加工工序,遵循先主后次原则,先加工主要表面,底板右端面,后加工次要表面,其余外轮廓以及槽的加工,遵循先面后孔原则,先加工零件表面,再加工槽φ19±0.021mm孔及φ8mm孔,由此初拟机械加工工序安排:工序号工序内容简要说明下料1 粗铣、精铣底板下端面先基准后其他原则2 粗铣、精铣底板右端面先基准后其他、先主后次3 粗铣底板其余外轮廓先主后次4 精铣底板其余外轮廓先主后次5 铣阶梯槽先主后次、先基准后其他6 钻φ8孔先面后孔、先粗后精7 钻φ10孔先面后孔、先粗后精8 镗φ19±0.021孔先面后孔、先粗后精9 铣通槽先面后孔、先粗后精(2)辅助工序在加工完成后,安排去毛刺、清洗和终检工序。
综上所述,该零件加工工序的安排顺序是:基准加工——主要表面粗加工——主要表面半精加工——次要表面加工——阶梯槽加工——孔的粗加工及精加工——通槽的加工5.确定工艺路线在综合考虑上述工序安排原则的基础上,拟定底板的机械加工工艺路线,见表表底板机械加工工艺路线工序号工序内容定位基准1 粗铣、精铣底板下端面端面、底板下表面2 粗铣、精铣底板右端面端面、底板下表面3 粗铣底板其他外轮廓右端面、下端面、底板下表面4 精铣底板其他外轮廓右端面、下端面、底板下表面5 铣阶梯槽右端面、下端面、底板下表面6 钻φ8mm孔右端面、下端面、底板下表面7 钻φ10mm孔右端面、下端面、底板下表面8 镗φ19±0.021mm孔右端面、下端面、底板下表面9 铣通槽右端面、下端面、底板下表面10 清洗11 终检3.3加工设备及其工艺设备的选用机床和工艺装备的选择应满足零件加工工艺的需求和可靠地保证零件加工质量的前提下,与生产批量和生产节拍相适应,并应优先考虑采用标准化得工艺装备和充分利用现有条件,以降低生产准备费用。
底板的生产类型为中批生产,可以选用高效的专用设备和组合机床,也可选用通用设备,所选用的夹具均为专用夹具,各工序加工设备及工艺设备的选用见表表加工设备及工艺装备工序号工序内容加工设备工艺设备1 粗铣、精铣底板下端面立式铣床X51 莫氏锥柄立铣刀、游标卡尺、专用铣夹具2 粗铣、精铣底板右端面立式铣床X51 莫氏锥柄立铣刀、游标卡尺、专用铣夹具3 粗铣底板其余外轮廓立式铣床X51 莫氏锥柄立铣刀、游标卡尺、专用铣夹具4 精铣底板其余外轮廓立式铣床X51 莫氏锥柄立铣刀、游标卡尺、专用铣夹具5 铣阶梯槽加工中心TH6350专用夹具6 钻φ8mm孔加工中心TH6350专用夹具7 钻φ10mm孔加工中心TH6350专用夹具8 镗φ19±0.021mm孔加工中心TH6350专用夹具9 铣通槽加工中心TH6350专用夹具10 清洗清洗机11 终检塞规、百分表、卡尺等3.4 加工余量、工序尺寸和公差的确定1.工序7——钻、镗φ19±0.021mm孔由表2.54基准孔7、8、9级孔的加工余量可得,钻孔余量10mm,镗孔余量=9mm。
ZT镗查表2.24孔加工方案的经济精度和表面粗糙度,可依次确定各工序尺寸的加工等级,钻孔IT11,镗孔IT8,根据上述结果,再查标准公差数值表可确定各工步余量镗孔0.058mm,精镗0.022mm综上所述,按入体原则确定各工序各工步的工序尺寸及公差钻孔φ10mm 镗孔φ19±0.021 mm3.5 切削用量的计算1.工序1——粗铣、精铣底板下端面该工序分为两个工步,工步1粗铣下端面,以左端面以及下底面定位,工步2以端面下表面定位,半精铣下端面,这两个工步在一台机床上经过两次走刀加工完成,所以它们选择的切削速度和进给量是不一样,同样背吃刀量也会不同。
(1)背吃刀量工步1的背吃量的确定:毛坯总余量为2mm,这道工序分两个工步完成则可ap=1.5mm,工步2的背吃刀量的确定:工步2的背以确定工步1的背吃刀量为1ap=0.5.吃刀量取决于工步1中背吃刀量的余量,可以算的2(2)进给量X51型立式铣床功率为4.5KW,查表5.8,类比可得莫氏锥柄立铣刀铣削进给量,该工序中工步1的进给量为0.14mm/z ,工步2的进给量为0.1mm/z(3) 切削速度本工序中采用莫氏锥柄立铣刀,D=20mm ,齿数Z=4,查表可得工步1的切削速度1c v =48m/min 则1s n =1000×vc/πd=764.3r/min2c v =56m/min2s n =1000×vc/πd=896.17r/min由于本工序采用X51型立式铣床,查表 3.6取转速1w n =725r/min 2w n =1225r/min 故实际铣削速度1c v =45m/min 2c v =77m/min故当1w n =725r/min 工作台的每分钟进给量1m f 应为406mm/min2w n =1225r/min 工作台的每分钟进给量2m f =90mm/min2.工序2——粗铣、精铣底板右端面该工序分为两个工步,工步1粗铣底板右端面,工步2半精铣底板右端面定位基准均为端面和底面,两个工步在同一台机床上,分两次走刀完成,所选用的切削速度和进给量,背吃刀量都不同。