(数控模具设计)冲压模具失效形式
冲压模具的失效形式分析与思考

冲压模具的失效形式分析与思考摘要:本文简单介绍了冲压模具失效的几种形式,并针对每种失效形式产生的原因进行了具体分析,提出了相应的预防及解决措施。
关键词:冲压模具;失效形式;分析;措施1 前言随着我国现代工业技术的不断发展,冲压模具在工业生产中起到了越来越广泛的应用。
冲压模具质量的好坏直接决定了所冲产品质量的优劣。
然而,冲压模具在使用过程中,常常出现各种形式的失效情况,应对这些失效,往往需要耗费一定的时间、人力、物力以及财力资源,严重影响到了工业生产的进度,不利于企业经济效益的提高。
因此,如何有效地预防冲压模具的失效,最大限度的提高其使用寿命,是很多企业共同面临的一个技术难题。
只有对冲压模具的失效形式做出正确分析,归属其失效类型,才能精准地找出其失效的原因,采取相应的技术措施对其修复或预防,延长其使用寿命。
2 冲压模具失效形式概述2.1 冲压模具失效的涵义冲压模具在使用过程中,因各种原因如结构形状、尺寸的变化以及零部件组织与性能的变化等,使得冲压模具冲不出合格的冲压件,同时也无法再修复的情形就叫做冲压模具的失效。
鉴定模具是否失效的判据有三种:一是模具已经完全丧失工作能力;二是模具虽然可以工作,但无法完成设定的功能;三是模具因结构受到严重损害,使用时存在安全隐患。
2.2 冲压模具失效的形式冲压模具在使用过程中,因模具本身类型、结构、材料的不同以及实际工作条件的不同,会表现出不同的失效形式,主要可分为以下四种。
(1)磨损失效。
冲压模具在正常工作过程中,往往会与加工的成形坯料直接接触,二者之间因相对运动而产生摩擦,造成冲压模具表面磨损。
当磨损程度达到一定限度时,模具表面失去原来的状态,使之无法冲出合格的冲压件,这就是磨损失效。
磨损在任何机械的使用过程中是不可避免的,因此是一种正常的失效形式,也是冲压模具失效形式中最为主要的一种。
根据磨损机理,可将磨损失效细分为四种:①磨粒磨损失效。
当坯料与模具接触的表面间存在硬质颗粒,亦或坯料加工前未打磨完全,其表面存在坚硬的突出物时,会摩擦并刮划模具的表面,严重时就会使模具表面材料脱落,造成磨粒磨损失效。
冲压模具失效知识简介

三冲裁模的工作条件及失效形式
此外, 凸模退出板料时,需要有一定的卸料力 将板料从 凸模上 卸下,卸料力与作用在凸模 上的其它压应力不同,是唯一的拉应力,使凸 模在反复拉、压应力的作用下产生疲劳磨损, 这也是致使凸模崩刃的原因之一。 对于厚板冲裁模,由于凸 、凹模受到的作用力 增大,在过大应力的作用下,不仅会产生磨损, 而且可能造成刃口变形、疲劳崩刃等现象。当 冲裁 凸模较 细长时,还会引起弯曲变形或折 断,如图 11.1.2所示。
四拉深模的工作条件及失效形式
从显微观 察看,模具和坯料的表面都是凹凸不平的, 由于模具表面的硬度高于坯料,相互挤压摩擦时会将 坯料表面刮下的碎粒压入模具表面的凹坑。在拉 深过 程 中,坯料的塑性变形以及坯料和模具工作部件表面 的摩擦,会产生出热能。特别是在某些塑性变形严重 和摩擦剧烈的局部区域,所产生的热能造成了高温, 破坏了模具和坯料表面的氧化膜和润滑膜,使金属表 面裸露,促使材料分子之间相互吸引,并使模具表面 凹坑里的坯料碎屑熔化,和模具表面焊合,形成坚硬 的小瘤,即粘结瘤。这些坚硬的小瘤,会使 拉深件表 面粗糙度 变差,严重时将在产品的表面 刻划 出刻痕, 擦伤工件,并且加速模具的不均匀磨损,这种失效形 式又 称为粘模 。此时,需对模具进行修磨,除去粘附 的金属。 拉深模的 重要问题,就在于如何防止粘附的 金属小瘤。
三冲裁模的工作条件及失效形式
a )局部塑变
b ) 摩擦磨损 c ) 疲劳损坏
(初期磨损阶段) (正常磨损阶段) (急剧磨损阶段)
图 11.1.1 冲裁时刃口的损伤过程
初期磨损阶段
模具刃口与板料相碰时接触面积很小,刃口的单位压 力很大,造成了刃口端面的塑性变形,一般称为塌陷 磨损。其磨损速度较快(见图 11.1.1a )。
冲压模具的失效形式
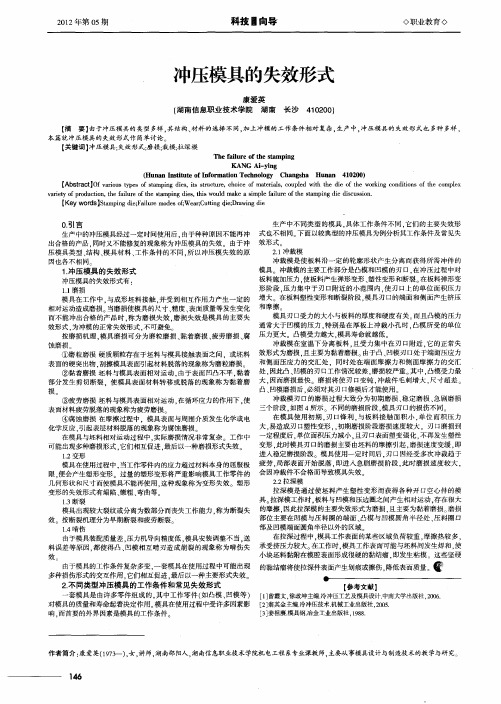
限. 便会产生塑形变形 。过量 的塑形变形将 严重 影响模 具工作零件的
几何形状和尺寸而使模具不能再使用 . 这种现象称为变形失效。塑形 变形的失效形式有 塌陷、 镦粗 、 曲等 弯 1 - 裂 3断 模具 出现较大裂纹 或分离为数部分而丧失工作能力 . 称为断裂失 效 按断裂机理 分为早期断裂和疲劳断裂 1 . 4啃伤 由于模具装配质量差 , 压力机导 向精度低 , 模具安装调整不当 , 送 料误差等原 因. 都使 得凸 、 凹模相互 啃刃造 成崩裂 的现象称 为啃伤失 效。 由于模具的工作条件 复杂多变 . 一套模具在使用过程 中可能出现 的黏结瘤将使拉深件表 面产生划痕或擦伤 , 降低表面质量 。 多种损伤形式的交互作用 , 它们相互促进 . 以一种主要形式失效。 最后
模具 刃 口受力 的大小与板料的厚度和硬度有关 而且 凸模 的压力 通常大于凹模的压力 . 特别 是在厚板上冲裁小孔 时 . 凸模所受 的单位 压力更大。凸模受力越大 . 模具寿命 就越低 。 冲裁模在室温下分 离板料 . 且受力集 中在 刃 口附近 . 的正常失 它 效形式为磨损 . 且主要为黏着磨损。 由于凸、 凹模刃 口处于端面压应力 和侧面压应力 的交 汇处 .同时处在端 面摩擦 力和侧面摩擦 力的交汇 处, 因此凸 、 的刃口工作情况较差 , 凹模 磨损较严重 。 中, 其 凸模受力最 大, 因而磨损最快 。磨损将使 刃 口变钝 , 冲裁件 毛刺增大 , 寸超差 。 尺 凸、 凹模磨损后 . 必须对其刃 口修模后才能使用 。 冲裁模刃 口的磨损 过程大致分为初期磨 损 、 稳定磨损 、 急剧磨损 三个阶段 , 如图 4 所示 。不同的磨损 阶段 , 模具刃 口的损伤不 同。 在模具使 用初期 。 口锋利 . 刃 与板料接 触面积 小 , 位面积 压力 单 大, 易造成刃 口塑性变形 ,初期磨损阶段磨损速度较大 。刃 口磨损到 , 定程度后 . 面积压力减小 . 单位 且刃 口表面塑变强化 . 不再发生塑性 变形 . 此时模具 刃口的磨损主要 由坯料的摩擦 引起 , 磨损速度变缓 , 即 进入稳定磨损阶段 。模具使用一定时间后 . 口因经受多次冲裁趋于 刃 疲劳 , 局部表 面开始脱落 , 即进入急剧磨损 阶段 , 此时磨损速 度较大 , 会 因冲裁件不合格 而导致模具失效 22拉深模 . 拉深模是通过 使坯料产生塑性变形 而获得各种开 口空心件的模 具。 拉深模工作时 . 与凹模和压边圈之间产生相对 运动 , 板料 存在很大 的摩擦 , 因此拉深模 的主要失效形式为磨损 , 且主要为黏着磨损 。 磨损 部位主要在 凹模与压料 圈的端 面、 凸模 与凹模 圆角半径处 、 压料圈 口 部及 凹模端面圆角半径 以外 的区域 在拉深过程中 . 模具工作表面 的某些区域负荷较重 . 摩擦热较多 , 承受挤压力较大。 在工 作时, 模具工作表面可能与坯料 间发生焊和 , 使 小块坯料黏附在模 腔表 面形成很硬的黏结瘤 . 即发生粘模 这些坚硬
冲压模具失效形式

冲压模具失效形式a )局部塑变b )摩擦磨损c )疲劳损坏(初期磨损时期)(正常磨损时期)(急剧磨损时期)图 11.1.1 冲裁时刃口的损害过程(1)初期磨损时期模具刃口与板料相碰时接触面积专门小,刃口的单位压力专门大,造成了刃口端面的塑性变形,一样称为塌陷磨损。
其磨损速度较快(见图 11.1.1a )。
(2)正常磨损时期起初期磨损达到一定程度后,刃口部位的单位压力逐步减轻,同时刃口表面因应力集中产生应变硬化,(见图 11.1.1b )。
这时,刃口和被加工坯料之间的摩擦磨损成为要紧磨损形式。
磨损进展较缓慢,进入长期稳固的正常磨损时期,该时期时刻越长,讲明其耐磨性能越好。
(3)急剧磨损时期刃口经长期工作以后,经受了频繁冲压会产生疲劳磨损,表面显现了损坏剥落(见图 11.1.1c )。
现在进入了急剧磨损时期,磨损加剧,刃口出现疲劳破坏,模具已无法正常工作。
模具使用时,必须操纵在正常磨损时期以内,显现急剧磨损时,要赶忙刃磨修复。
随着刃口的磨损,工件的毛刺高度会不断增加,因此实际生产中,能够通过观测毛刺高度的大小来推断模具刃口的磨损量,在冲裁件达到质量承诺的毛刺极限值时即进行刃磨。
从磨损机理上分析,凸、凹模的磨损要紧是粘附磨损和磨粒磨损。
粘附磨损是在模具刃口在与板料的相对摩擦运动过程中,由于高压产生了局部的相互粘着和咬合现象当接触面相对滑动时,粘附部分便发生剪切引起磨损。
磨粒磨损是指模具工作时表面剥落的碎屑嵌入工作部件表面,成为磨料,使其逐步磨损的过程。
冲裁硬度较高的金属材料(如高碳钢、硅钢)时,因材料的硬粒或碳化物剥离而产生磨粒磨损。
当冲压高韧性材料(如奥氏体不锈钢)时,易产生粘附磨损。
一样情形下,凸模的磨损要快于凹模,这是因为凸模刃口处的承力面积小于凹模,在同一冲裁力的作用下,凸模刃口处单位面积承担的压应力要比凹模刃口处更大一些;同时,在每一次冲裁过程中,凸模都要切入并退出板料,前后经历两次摩擦,而凹模和板料的分离部分仅发生一次摩擦。
冲压模具常见故障分析及解决方式

冲压是大量量零件成型生产实用工艺之一。
在冲压生产进程中,模具出现的问题最多,它是整个冲压生产要素中最重要的因素。
直接影响到生产效率和本钱。
影响到产品的交货周期。
模具问题主要集中在模具损坏、产品质量缺点和模具的刃磨方面,它们长期困扰着行业生产。
只有正确处置这几个关键点。
冲压生产才能够顺利进行。
1 模具故障模具故障是冲压生产中最容易出现的问题,常常造成停产,影响产品生产周期。
因此,必需尽快找到模具故障原因,合理维修。
模具损坏模具损坏是指模具开裂、折断、涨开等,处置模具损坏问题,必需从模具的设计、制造工艺和模具利用方面寻觅原因。
首先要审核模具的制造材料是不是适合,相对应的热处埋工艺是不是合理。
通常,模具材料的热处置工艺对其影响很大。
若是模具的淬火温度太高,淬火方式和时间不合理,和回火次数和温度、肘间选择不妥,都会致使模具进入冲压生产后损坏。
落料孔尺寸或深度设计不够,容易使槽孔阻塞,造成落料板损坏。
弹簧力设计过小或等高套不等高,会使弹簧断裂、落料板倾斜.造成重叠冲打,损坏零件。
冲头固定不妥或螺丝强度不够.会致使冲头掉落或折断。
模具使历时,零件位置、方向等安装错误或螺栓紧固不好。
工作高度调整太低、导柱润滑不足。
送料设备有故障,压力机异样等,都会造成模具的损坏。
若是出现异物进入模具、制件重叠、废料阻塞等情况未及时处置,继续加工生产,就很容易损坏模具的落料板、冲头、下模板和导柱。
卡模冲压进程中,一旦模具合模不灵活,乃至卡死,就必需当即停止生产,找出卡模原因,排除故障。
不然,将会扩大故障,致使模具损坏。
引发卡模的主要原因有:模具导向不良、倾斜。
或模板间有异物,使模板无法平贴;模具强度设计不够或受力不均。
造成模具变形,例如模座、模板的硬度、厚度设计过小,容易受外力撞击变形;模具位置安装不准,上下模的定位误差超差。
或压力机的精度太差,使模具产生干与;冲头的强度不够、大小冲头位置太近,使模具的侧向力不平衡。
这时应提高冲头强度,增强卸料板的引导保护。
模具失效形式及表面热处理

冷作模具:冲裁模的失效形式有:不均匀磨损、凸模整体折断和凸凹模局部掉块。
拉伸模失效形式有磨粒磨损和黏着磨损。
冷镦模失效形式有模口胀大、棱角堆塌、腔壁胀裂。
冷挤模失效形式有塑性变形、磨损失效、凸模折断失效、疲劳断裂失效、纵向开裂失效。
热作模具:锤锻模失效形式有磨损失效、断裂失效、热疲劳开裂失效及塑性变形失效。
压力机锻模失效形式有脆性断裂失效、冷热疲劳失效、塑性变形失效、磨损失效以及模具型腔的表面腐蚀失效。
热挤压模失效形式有早起断裂失效、冷热疲劳失效、塑性变形失效、磨损失效、模具型腔表面的氧化失效和磨损沟痕等。
热冲裁模失效形式有热磨损失效、崩刀失效、卷刀失效和断裂失效。
压铸模的失效形式主要有热疲劳失效、热熔蚀失效、冲蚀和气蚀磨损、粘模失效。
塑料模具失效形式有磨损失效、腐蚀失效、塑性变形失效、断裂失效、疲劳失效及热疲劳失效。
冷作模具的表面热处理:1.冲裁模的工作部位的表面处理工艺有氮碳共渗,TD法渗钒渗铌,CVD法沉积TiN或TiC,镀硬铬,化学镀镍磷合金,电火花熔渗等。
2.冷挤模常采用氮化渗碳,沉积氮化物或碳化物等表面强化技术。
3.拉伸模采用渗氮,氮碳共渗,渗硼,渗钒,镀硬铬,气相沉积TiC以及盐浴涂覆碳化物、碳化物于模具表面,通过渗硫提高模具抗咬合的能力。
4.冷镦模需要对模具进行使之整体强韧化的热处理,再对之进行表面强化处理,其常见的表面处理方法有氮碳共渗,气相沉积,TiN 等超硬化合物层,硼-硫复合渗等。
热作模具的表面处理:1.锤锻模对模具型腔表面进行渗氮、渗硼、氮碳硼三元共渗等表面强化处理。
2.压力机锻模及热挤压模常用的表面处理有渗氮、硫碳氮三元共渗、硼氮共渗。
3.热冲裁,模在模具刃口处用电焊条堆焊或用等离子喷焊一层高耐磨、高热强的钴基合金。
4.渗氮和氮碳共渗能提高模具的耐磨性、抗熔蚀性,及防止铝合金的粘模现象;渗铬、渗铝可提高模具的抗氧化性,尤其对高温工作的压铸模有利;磷化、镀铬也可提高抗氧化性,降低摩擦系数,防止粘模。
冲压模具失效形式
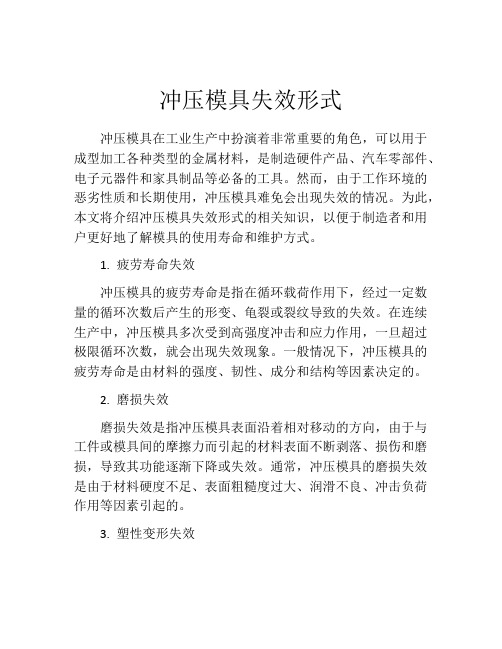
冲压模具失效形式冲压模具在工业生产中扮演着非常重要的角色,可以用于成型加工各种类型的金属材料,是制造硬件产品、汽车零部件、电子元器件和家具制品等必备的工具。
然而,由于工作环境的恶劣性质和长期使用,冲压模具难免会出现失效的情况。
为此,本文将介绍冲压模具失效形式的相关知识,以便于制造者和用户更好地了解模具的使用寿命和维护方式。
1. 疲劳寿命失效冲压模具的疲劳寿命是指在循环载荷作用下,经过一定数量的循环次数后产生的形变、龟裂或裂纹导致的失效。
在连续生产中,冲压模具多次受到高强度冲击和应力作用,一旦超过极限循环次数,就会出现失效现象。
一般情况下,冲压模具的疲劳寿命是由材料的强度、韧性、成分和结构等因素决定的。
2. 磨损失效磨损失效是指冲压模具表面沿着相对移动的方向,由于与工件或模具间的摩擦力而引起的材料表面不断剥落、损伤和磨损,导致其功能逐渐下降或失效。
通常,冲压模具的磨损失效是由于材料硬度不足、表面粗糙度过大、润滑不良、冲击负荷作用等因素引起的。
3. 塑性变形失效塑性变形失效是指冲压模具在受到高强度载荷作用下,模具的材料发生塑性变形导致模具形状和精度的变化。
在工业生产中,如连续冲击造成模具部分塑性变形,就会导致模具无法正常工作,降低产量和质量。
通常,冲压模具的塑性变形失效是由于材料的硬度、强度、韧性和应力分布不均等因素引起的。
4. 热疲劳失效热疲劳失效是指冲压模具在高循环温度和压力下,材料发生氧化腐蚀、高温软化甚至变形、裂纹等现象,导致失效。
在模具制造和使用中,热疲劳失效是一个比较难以避免的问题,因此需要采取相应的预防措施,如选用高温耐受材料、保护表面涂层、合理的冷却循环等。
5. 腐蚀失效腐蚀失效是指冲压模具在潮湿或有害气体的环境下,发生腐蚀、氧化、磨损和变形等现象,导致失效。
在模具的制造和使用中,腐蚀失效是由于金属材料的化学稳定性不足、环境因素的影响、保养和维护不当等原因引起的。
因此,在使用过程中需要对模具加以保护和预防。
模具失效的形式

模具失效形式及机理
五、气蚀磨损和冲蚀磨损
(二)冲蚀磨损 定义:液体或固体微粒高速落到模具表面,反复冲
击模具表面,使模具表面局部材料流失,形成麻点和凹 坑旳现象叫冲蚀磨损。
当小液滴速度尤其高,高于100m/s 时,产生旳冲击 应力会超出材料旳屈服强度,造成局部材料断裂。
模具失效形式及机理
五、气蚀磨损和冲蚀磨损 (三)提升抗气蚀磨损和冲蚀磨损旳措施
载荷对碳钢表面磨ห้องสมุดไป่ตู้量旳影响
模具失效形式及机理
(三)影响粘着磨损旳原因
② 材料性质 脆性材料比塑性材料粘着倾向小。塑性材料形成旳粘着结 点旳破坏以塑性流动为主,它发生在离表面一定旳深度处, 磨屑较大。而脆性材料粘结点旳破坏主要是剥落,损伤深 度较浅,同步磨屑轻易脱落,不堆积在表面上。
密排六方构造旳金属材料粘着倾向小,面心立方点阵 旳金属粘着倾向明显不小于其他点阵旳金属;
模具失效形式及机理
一、磨损分类
根据模具旳成形坯料、使用情况,其磨损机 理能够分为:磨粒磨损、粘着磨损、疲劳磨损、 气蚀和冲蚀磨损、腐蚀磨损。
模具失效形式及机理
二、磨粒磨损
磨粒磨损旳定义: 在工件 和模具接触表面之间存在 外来硬质颗粒或者工件表 面旳硬突出物,刮擦模具 表面,引起模具表面材料 脱落旳现象叫磨粒磨损。
举例,断裂失效过程 总之,失效发展过程是: 模具损伤 → 损伤积累 → 模具失效旳过程。
模具寿命
模具正常失效前,生产出旳合格产品旳数目,叫 模具正常寿命,简称模具寿命。
模具首次修复前生产出旳合格产品旳数目,叫首 次寿命。
模具一次修复后到下一次修复前所生产出旳合格 产品旳数目,叫修模寿命。
模具寿命是首次寿命与各次修复寿命旳总和。