薄板冲压成型中板料起皱的临界应力分析和预测
冲压工艺中的应力分析与疲劳寿命预测

冲压工艺中的应力分析与疲劳寿命预测近年来,随着工业的发展,冲压工艺在制造业中得到广泛应用。
然而,由于冲压工艺中材料受到重复的应力作用,使得零部件的疲劳寿命成为了厂家关注的焦点。
因此,冲压工艺中的应力分析与疲劳寿命预测成为了工程师需要解决的问题之一。
首先,为了分析冲压工艺中的应力分布情况,我们需要了解材料力学性质和冲压工艺参数的影响。
材料力学性质主要包括弹性模量、屈服强度和延伸率等。
通过实验和模拟软件的辅助,我们可以确定这些参数的具体数值。
而冲压工艺参数包括模具的几何形状、冲压速度和冲压次数等。
这些参数将直接影响到冲压工艺中应力的分布。
因此,我们需要综合考虑这些因素,并采用数学模型来描述应力的变化情况。
其次,冲压过程中材料受到的应力主要包括拉压应力和剪切应力。
拉压应力是由冲压过程中材料的伸长和收缩引起的,而剪切应力则是由材料的剪切变形引起的。
这些应力会导致材料内部出现塑性变形和裂纹的形成,进而影响零部件的疲劳寿命。
因此,准确地预测疲劳寿命成为了必要的工作。
疲劳寿命的预测可以采用许多方法,例如基于应力的SN曲线法和应变的EN曲线法。
其中,SN曲线法是一种常用的方法,它通过实验得到应力和循环寿命之间的关系,在冲压工艺中疲劳寿命的预测中有着重要的应用。
此外,还有一些专门针对冲压工艺的疲劳寿命预测方法,例如采用有限元分析结合材料的疲劳裂纹扩展行为的方法。
这些方法能够更加准确地预测材料在冲压工艺中的疲劳寿命。
此外,针对不同材料和不同冲压工艺的特点,研究者们也进行了大量的实验和数值模拟工作。
例如,对于高强度钢材料的冲压工艺,由于其材料性能高于普通钢材,会对模具产生较大的冲击应力。
因此,针对高强度钢材料的冲压工艺,研究者们需要对冲击应力进行分析,并结合SN曲线法来预测其疲劳寿命。
类似地,对于复杂的三维模具形状以及薄壁件的冲压工艺,需要建立相应的有限元模型,进行应力分析和疲劳寿命预测。
总结起来,冲压工艺中的应力分析与疲劳寿命预测是影响产品质量和寿命的重要因素。
薄板冲压成形中的压边力控制模拟与应用

薄板冲压成形中的压边力控制模拟与应用Ξ谢世坤1,黄菊花1,李慎国2,吴晓军2,黎雪芬1(11南昌大学机电工程学院,南昌330029;21江铃五十铃汽车有限公司,南昌330001)摘要:本文在详细分析了国内外对压边力研究的现状后,提出了压边力研究的两个主要方面:压边力曲线的预测和压边力的优化控制。
并首次提出了根据所获得的压边力曲线采用模糊控制理论对板料的起皱进行跟踪。
关键词:压边力;人工神经网络;模糊控制中图分类号:TG 386 文献标识码:A 文章编号:1001-3881(2004)7-017-3The Simulation and Application of BHF Control in Sheet Metal FormingXIE Shi 2kun 1,H UANGJu 2hua 1,LI Shen 2guo 2,W U X iao 2jun 2,LI Xue 2fen 1(11Mechanical and Electronic Engineering School ,Nanchang University ,Nanchang 330029,China ;21Jiangling -IS UZ U M otors C o.,Ltd.,Nanchang 330001,China )Abstract :Based on the analysis of the trends of BHF research at home and abroad ,tw o main aspects was put forward in BHF research :the predication of BHF curve and the optimized control of BHF.F or the first time ,the fuzzy theory was applied to follow the wrinkle of the blank according to BHF curve.K eyw ords :Blank holder force (BHF );Aritificial neural netw orks (ANN );Fuzzy0 引言薄板冲压成形过程中的压边力(BHF )是板料塑性成形的一个重要的工艺参数[1]。
冲压成型过程中的应力分析与优化

冲压成型过程中的应力分析与优化冲压成型是一种常见的金属加工方法,广泛应用于汽车、电子、家电等行业。
在冲压成型过程中,材料受到外力的作用,会产生应力,如果应力过大,可能导致零件变形、开裂甚至断裂。
因此,对冲压成型过程中的应力进行分析与优化,对于提高产品质量和生产效率具有重要意义。
首先,我们来了解一下冲压成型过程中的应力来源。
在冲压过程中,材料受到冲击力的作用,产生塑性变形。
这种变形是由于材料内部的晶粒滑移和变形引起的,会导致应力的集中和累积。
此外,冲压过程中的摩擦力也会对材料产生影响,增加应力的大小。
因此,在进行应力分析时,需要考虑这些因素的综合作用。
冲压成型过程中的应力分析可以通过有限元分析方法来进行。
有限元分析是一种数值计算方法,可以模拟实际工程中的应力和变形情况。
通过将材料分割成有限个小单元,然后根据力学原理和材料特性进行计算,可以得到每个小单元的应力分布。
通过对所有小单元的应力进行综合,可以得到整个零件的应力分布情况。
应力分析的结果可以用于优化冲压成型过程。
根据应力分布情况,可以确定材料的薄弱点和应力集中区域。
在设计模具时,可以对这些区域进行加强,以提高零件的强度和耐用性。
此外,通过调整冲压力、冲压速度和冲压温度等工艺参数,也可以改变应力分布情况。
例如,增加冲压力可以减小应力集中区域的大小,从而降低零件的变形风险。
除了应力分析,优化冲压成型过程还可以考虑材料的选择和热处理等因素。
不同材料具有不同的力学性能,选择合适的材料可以减小应力的大小。
同时,通过对材料进行热处理,可以改变其晶粒结构和力学性能,从而降低应力的大小和分布不均匀性。
总之,冲压成型过程中的应力分析与优化对于提高产品质量和生产效率具有重要意义。
通过有限元分析和优化工艺参数,可以减小应力集中区域和应力的大小,从而降低零件的变形风险。
同时,选择合适的材料和进行热处理,也可以改善材料的力学性能,提高零件的强度和耐用性。
在实际应用中,需要结合具体情况进行分析和优化,以实现最佳的冲压成型效果。
临界起皱应力

临界起皱应力
临界起皱应力是指当物体受到外力作用时,发生起皱现象所需的最小应力。
起皱现象是指物体表面出现波纹或皱纹的现象。
在材料科学和工程中,临界起皱应力是一个重要的参数,用于评估材料的稳定性和可靠性。
临界起皱应力的大小取决于材料的机械性能、几何形状和加载条件等因素。
一般来说,材料的强度越高,临界起皱应力越大;而材料的刚度越大,临界起皱应力越小。
此外,几何形状和加载条件也会对临界起皱应力产生影响。
例如,在压缩加载条件下,弯曲形状的材料比平板形状的材料更容易起皱。
为了提高材料的抗皱性能,可以采取以下措施:
1. 增加材料的强度和刚度,可以通过选择合适的材料或改变材料的组织结构来实现。
2. 优化材料的几何形状,例如增加材料的厚度或改变材料的表面形状。
3. 优化加载条件,例如改变加载的方向或使用支撑结构来增加材料的稳定性。
总之,临界起皱应力是评估材料性能的重要参数,通过控制加载条件和优化材料的机械性能和几何形状,可以提高材料的抗皱性能。
薄板微冲压成形失稳分析与实验研究

第45卷第1期 2011年1月上海交通大学学报JOU RN AL O F SH AN GH A I JIA OT O N G U N IV ERSIT YVol.45No.1 Jan.2011收稿日期:2010 03 30作者简介:胡 鹏(1981 ),男,湖北省咸宁市人,博士生,主要研究方向为金属薄板微冲压成形性能等.来新民(联系人),男,教授,博士生导师,电话(T el.):021 ********;E mail:xmlai@.文章编号:1006 2467(2011)01 0011 04薄板微冲压成形失稳分析与实验研究胡 鹏, 彭林法, 来新民, 张卫刚(上海交通大学机械系统与振动国家重点实验室,上海200240)摘 要:针对薄板微冲压成形过程中产生的尺度效应现象,以塑性应变梯度理论的本构方程为基础,推导出基于应变梯度的集中性失稳准则,并对薄板微冲压成形过程进行分析,得到冲压成形深度与极限应变值的关系,以及材料发生极限应变时的极限成形深度.同时,设计了相应的微冲压成形实验.结果表明,材料在微冲压成形过程中的成形极限小于宏观成形过程的成形极限,新的失稳准则能够更为准确地预测薄板微冲压成形过程中的成形极限.关键词:微冲压成形;尺度效应;成形极限;破裂准则中图分类号:TG 386.41 文献标志码:AInstability Analysis and Experimental Study of Micro Stam ping Process with Thin SheetH U Peng , PEN G L in f a, L AI X in min, ZH A N G Wei gang(State Key Laboratory of M echanical System and Vibratio n,Shang hai Jiaotong U niv ersity ,Shang hai 200240,China)Abstract:Focusing on the size effect w hich appear s during the process o f m icro scale stamping,a new frac ture criterion w as derived from the co nstitutiv e equation based on strain gradient.T hen,the stamping pro cess of thin sheet w as studied to obtain the relationship betw een the forming depth and strain.As a result,the lim it of forming depth could be predicted accurately.Finally,a series o f m icro stam ping experi m ents w ere conducted,w hich show s that the new fracture cr iterion is available.Key words:micro scale stamping ;size effect;fo rming lim it;fractur e criterion微型产品已广泛用于移动电话、集成电路封装、医疗器械和微型传感器等领域.微细制造通常是指工件在二维尺度上的尺寸至少小于1m m 的工件制造,由于其加工尺度较小而导致微观尺度成形过程中出现了尺度效应,使得传统的宏观成形加工工艺和技术不再适用[1].微冲压成形是微塑性成形领域的一个重要成形工艺,而成形极限是判断微冲压成形性能的一个有效方法.Sao to me 等[2]研究了不同板料厚度和凸模直径对微冲压成形极限的影响,发现极限拉延比(LDR)随着凸模直径与板料厚度的比值增大而减小;Vollertsen 等[3]研究了厚度0.02~ 1.00m m 铝薄板的成形性能,发现与比宏观尺度相比,其微尺度下的LDR 较低;Lee 等[4]研究了板料厚度及晶粒尺寸对其成形性能的影响,发现当板料厚度比晶粒尺寸小时,其LDR 显著减小.这些研究表明,金属薄板微冲压成形极限低于宏观尺度下的成形极限.但是,目前还缺少有效的模型来计算微冲压成形极限.本文以Taylo r 位错模型[5]为基础,建立了基于应变梯度的失稳准则,分析了薄板微冲压成形中的极限成形能力,并进行了相应的实验研究,以验证所推导出分析模型的准确性.1 Taylor 位错模型Taylo r 位错模型[5]是一种基于应变梯度的应力与应变的关系式,它是将流动应力与等效塑性应变以及应变梯度相结合,已用于分析微尺度下的流动应力与应变的关系并取得了与实验相近的结果[6 8].包含等效塑性应变梯度的T aylor 位错模型的数学表达式为flow = ref (f ( p))2+lp(1)式中:l 为内禀材料长度,l =M 2r -!2G 2b ref2M 和r -分别为与材料性能有关的参数,对于面心立方晶体材料,M =3.06,r -=1.9;G 为剪切模量;b 为Burgers 矢量的大小,!为经验系数,取b =0.3nm ,!=0.5;ref 为参考应力;f ( p)为与等效塑性应变有关的函数; p为等效塑性应变梯度.与传统模型的差别在于,该模型引入了等效塑性应变梯度,当l p =0时,即为传统的本构模型.2 基于应变梯度的希尔准则假定 1, 2, 3和 1, 2, 3分别为主应变与主应力, e 为等效应变, e 为等效应力.根据Levy M ises 流动法则,在 1 2> 3=0时,12-∀= 22∀-1=- 31+∀= e21-∀+∀2(2)式中,∀=2/ 1为表示应力状态的参数,且 e = ref (f ( p))2+l p板料在发生分散性失稳之后,如果继续变形,由于分散性失稳亚稳定流动的发展,受载板料影响的最薄弱环节固定在变形区的某一狭窄条带内而无法转移出去,故形成了集中性颈缩并产生集中性失稳.针对这一现象,H ill [9]给出了宏观成形条件下的集中性失稳准则,即希尔准则(H ill criterion),其数学表达式为d ee=-d 3(3)由此可以求得考虑应变梯度而发生集中性失稳时的等效应变为le =21-∀+∀21+∀2n+l n (4)因传统的塑性理论不考虑应变梯度的影响,即=0,故le =21-∀+∀21+∀n(5)式中,n 为应变硬化指数.比较式(4)和(5)可以看出,在微观成形条件下,板料发生集中性失稳的等效应变比宏观条件下的小,其板料更容易破裂且成形性能更差.3 薄板微冲压成形过程分析以U形槽为研究对象,采用所建基于应变梯度的失稳准则分析其成形性能.采用图1(a)所示的多槽成形过程.其中应变值并不容易直接测量,而成形深度则较易测量.为此,通过理论分析得到应变与成形深度之间的关系.(a)冲压成形(b)板料分析图1 冲压成形示意图F ig.1 Schematic of the stamping process3.1 受力分析图1所示为冲压成形示意图.其中:h 为成形深度;r p 为凸模圆角半径;r d 为凹模圆角半径;#为包角;c 为模具间隙.取中间槽的1/2为分析对象,将板料分为5个部分.其中,点C 和D 均为板料与模具的切点,分别对5个区域进行受力分析.在A B 、CD 、EF 区域,板料只收到2个方向的12上 海 交 通 大 学 学 报第45卷作用力,即F B =F A , F D =F CF F =F E , F F =F A(6)BC 、DE 区域为模具圆角与材料接触的区域,参考Lang e[10]的绳索轮模型可得:F C =F B e ∃#, F E =F D e -∃#(7)假设t 为板料厚度,由图1(a)可推导出任意成形的深度与包角的关系:tan #=h -t -(r p +r d )(1-cos #)+t/(cos #)c +(r p +rd )(1-sin #)(8)由此得到图2所示的AF 段拉力分布示意图.可以看出,CD之间拉力最大,即CD 区域为危险区域,材料在C 和D 点处最易发生断裂.图2 拉力分布示意图Fig.2 Schematic o f the st retch distr ibut ion3.2 应变和厚度分析图3所示为取其中一个无限小单元的主方向示意图.设定方向1为沿板料长度的方向,方向2为板料宽度方向,方向3为板料厚度方向,并假设板料足够宽,板料宽度方向的应变 2可以忽略,即为平面应变问题.图3 板料单元的主方向Fig.3 M ain dir ect ion of an element of sheetsliding on the face o f punch取应变比%= 2/ 1作为表示应变状态的参数,3个主应变为1= 12=% 1=0 3=-(1+%) 1=- 1(9)根据Levy M ises 流动法则,应力比∀与应变比%的关系为∀=2%+12+%(10)因%=0,则∀=1/2e =32 1, e =231(11)板料上任意一点的拉力F 与其长度方向上应力 1的关系为F = 1t(12) 板料厚度与厚度方向上应变的关系为t =t 0exp3=t 0ex p (- 1)(13) 将式(1)、(11)、(13)代入式(12),得F =23t 0k23ln t 0t n+l p ex p -lnt 0t (14)对于成形深度为h 的板料,假设AF 沿2个方向的宽度为1个单位,则AF 之间的体积为V =FAt d l =t AB l AB +t B C l BC +t C D l CD +t D E l D E +t E F l EF (15)式中:t AB ,t BC ,t C D ,t D E ,t E F 分别为AB ,BC,CD ,DE,EF 段的平均厚度,可取各段2个端点厚度的平均值而由式(14)计算得到;l AB ,l BC ,l CD ,l D E ,l E F 分别为A B,B C,CD ,DE,E F 段的长度,则l AB =w p2-r p l B C =r p +t BC2∀l D E =r d +t D E2∀l EF =w s2-r d (16)l CD =h -t e -(r p +r d )(1-cos ∀)+t D 2+t C2cos ∀2+c +(r p +r d )(1-sin ∀)-t D 2+t C2sin ∀212(17)式中:w p 为凸模槽宽;w d 为凹模槽宽;w s 为凹模脊背宽度(见图4);t C 和t D 分别为点C 与D 的厚度.13第1期胡 鹏,等:薄板微冲压成形失稳分析与实验研究图4 成形工艺参数示意图F ig.4 Schematic o f the techno lo gical parametersof stamping pro cess变形之前A F的初始体积为V0=w d+w s2t0(18)对于一个多槽的冲压成形,变形前后AF之间的体积保持不变,即V=V0(19) 通过以上分析可知,式(19)是一个隐式的非线性方程,可以使用数学软件进行求解,它只含有2个未知数,即h以及A点的应变 A.如果给定一个h,则可求得 A,进而求得 C;如果 C达到发生失稳的极限应变,则所对应的h即为极限成形深度.4 薄板微冲压成形实验4.1 实验模具与材料按照图1所示设计并加工5槽微成形模具.模具的尺寸分别为:w p=0.7m m;w d= 1.0mm;w s= 0.7mm;r p=0.1mm;r d=0.1m m;c=0.15m m.采用凯强力公司产KQL 2000型加载机构,其最大成形力为10kN,误差0.5%.实验材料选用厚度为0.1m m、尺寸15m m! 20mm的长方形奥氏体不锈钢SUS304,通过拉伸实验得到其拉伸性能曲线为 =1697 0.548,由此可得 ref= 1.697GPa,n=0.548,l=5.57∃m.4.2 实验结果重复5次微冲压实验,分别测量每次的最大成形深度,所得最大成形深度的平均值为0.471m m.在考虑应变梯度以及不考虑应变梯度时,其最大成形深度分别为0.465和0.503mm.由此可见,与传统的弹塑性失稳准则相比,考虑应变梯度的弹塑性失稳准则更接近于实验结果.5 结 语本文基于塑性应变梯度理论的本构方程,建立了分散性失稳准则以及集中性失稳准则,分析了薄板微冲压成形过程中极限应变与冲压深度的关系,并通过微冲压成形实验,验证了所提出的失稳准则的有效性.结果表明,由于成形尺度较小以及受到尺度效应的影响,导致材料本构关系发生变化而引起冲压成形性能出现差异,使得薄板微冲压成形极限低于宏观条件下的板料成形极限.参考文献:[1] Engel U,Eckstein R.M icr ofor ming fr om basic research to its realizat ion[J].Journal of Materials Processing Technology,2002,125 126(1):35 44.[2] Saoto me Y,Kag a H.M icr o deep dr awability of v eryt hin sheet steels[J].Advanced Technology of Plasticity,1990,3:1341 1346.[3] Vo llertsen F,H u Z.O n the draw ing limit in microdeep dr aw ing[J].Journal Technology of Plasticity,2007,32(1):1 11.[4] L ee R S,Chen C H,Gau J T.Effect of thickness tog ra in size r at io on dr awability fo r micr o deep draw ingo f AISI304stainless steel[C]//Proceedings of the9thIC TP Paper.Gy eongju,K o rea:BIA S V erlag,2008:183 188.[5] T ay lo r G I.T he mechanism o f plastic defor mation o fcr ystals:Par t I.T heo retical[J].Proceedings of theRoyal Society of London A,1934,145(2):362 287.[6] Fleck N A,M uller G M,Ashby M F,et al.Str aing radient plasticit y:T heo ry and ex per iments[J].Acta Metallurgica et Materialia,1994,42(2):475 487.[7] Q u S,Huang Y G,P harr G M,et al.T he indentation size effect in the spher ical indentation o f iridium:A study via the conventional theor y of mechanismbased str ain gr adient plasticit y[J].InternationalJournal of Plasticity,2006,22(7):1265 1286.[8] Saha R,Xue Z,H uang Y G,et al.Indentation of aso ft metal film on a hard substrate:Strain g radienthar dening effects[J].Journal of the M echanics andPhysics of Solids,2001,49(9):1997 2014.[9] H ill R.O n discontinuous plast ic states w ith specialr eference to lo calized necking in the sheet[J].Journal of the Mechanics and Physics of Solids,1952,1(1):19 30.[10] Lang e K.H andboo k of met al fo rming[M].Ber lin:Spr ing er V er lag,1985.14上 海 交 通 大 学 学 报第45卷。
薄壁件塑性成形失稳起皱研究3

图4.6压边力
4.7 划分网格
• 划分网格即Mesh模块, 除了板料之外其他的 组件的网格可以不是 很密设置为8即可,板 料由于是发生塑性变 形的所以划分的网格 比较密为3,这样计算 出来的结果才很准确。
Punch 图4.7(a)
图4.7(b) Blank
图4.7(c) Holder
图4.7(d) Die
图5.1(e) 当板料厚度为0.7的应力应变云图
图5.1(f) 当板料厚度为0.8时的应力应变云图
图5.1(g)
图5.1(h)
当板料厚度为0.9的应力应变云图
当板料厚度为1.0的应力应变云图
在其他条件不变的情况下,随着板料厚度的加大,拉深成形过程中发生起皱的现象得到了 明显的改善,当板料厚度为0.5时可以避免产生起皱,当板料厚度大于0.5后,板料厚度对 于起皱的影响就不那么的明显了,这点能从图5.1(d)到(h)看出来。 不同的板料厚度下得到的应力应变云图可以清晰的看出来板料厚度较小时容易出现起皱 的现象,而当板料厚度为0.5时起皱现象得到明显的改善,当板料厚度大于0.5时起皱现象 基本上得到了根本的解决
图4.7(e) Assembly
4.8 创建作业和提交作业
• 先在Job菜单中新建一个作业并且定义名词 性质,注意所创建的作业对应的应该是你 所要模拟的模型,在模型数多于两个时很 容易出现所创建的作业对应的是上一组的 模型,这样新创建的作业运算的结果跟上 一个作业是完全一样的,提交作业,点击 submit提交作业,然后点击Monitor来查看 模拟当中出现的错误和警告,再根据提示 仔细的查找错误的原因来调试程序。
4.9 后处理
• 后处理即Visualization模块,Visualization模块以 下功能:(1)显示变形云图、云纹图和矢量图。 (2)逐格显示各个时间的增量步。(3)通过切 面来观察模型内部的分析结果。(4)设置各种显 示方式的参数。(5)显示节点编号,边界条件。 (6)改变所要显示的场变量。(7)查询节点的 分析结果,并将其写入一个文件。(8)更改背景 颜色,保存图像。(9)显示动画,把动画保存为 AYI文件。(10)显示X-Y曲线图 和路径上的分 析结果。(11)生成数Assembly 模块,从上到下依次为punch、 blank-holder、blank、die。要注意 的是由于我们建立的模型是壳单元 所以在视图中并不能看出来板料的 实际厚度,所以就必须很精准的定 位板料、压边圈、凸模和凹模之间 的相对位置,压边圈和凸模在一个 水平线上,压边圈与凹模之间的距 离应该是板料的厚度值,压边圈和 板料之间的距离应该是板料厚度的 一半,凹模和板料之间的距离也应 该是板料厚度的一半,装配完之后 一定要在不同视角看看是否各个零 件的中心线是在一条线上,以免在 接下来的运算是出现不必要的错误。
冲压起皱的原因

冲压起皱的原因
冲压起皱是指在金属冲压过程中,材料表面出现皱纹的现象。
这种现象通常是由于冲压工艺参数不合理或材料本身的特性导致的。
下面将从材料特性、工艺参数和设备状态三个方面详细介绍冲压起皱的原因。
材料的特性是导致冲压起皱的重要原因之一。
材料的硬度、韧性和表面质量都会影响冲压过程中的起皱情况。
如果材料硬度过高,冲头在冲压过程中容易滑移而导致起皱;如果材料韧性不足,容易发生断裂而产生起皱;如果材料表面质量不好,如有凹陷或磨损,也容易导致起皱。
因此,在冲压起皱问题中,材料的选择和质量是非常重要的。
工艺参数的设置也是冲压起皱的关键因素之一。
工艺参数包括冲头的形状、尺寸和材质,以及冲压速度、冲压力和冲压次数等。
如果冲头形状不合理,如角度过小或过大,都会导致起皱;如果冲压速度过快或过慢,也会影响起皱情况;如果冲压力过大或过小,同样会导致起皱。
因此,合理设置工艺参数对于避免冲压起皱至关重要。
设备状态也会对冲压起皱产生影响。
设备的刚性、精度和稳定性都会直接影响冲压起皱的情况。
如果设备刚性不好,容易产生振动而导致起皱;如果设备精度不高,如冲头位置不准确,也会导致起皱;如果设备稳定性不好,如冲压过程中有杂质或润滑不良,同样会影响起皱情况。
因此,保持设备的良好状态对于避免冲压起皱非常重
要。
冲压起皱是由于材料特性、工艺参数和设备状态等多方面因素共同作用导致的。
在进行冲压过程中,需要选择合适的材料,合理设置工艺参数,并保持设备的良好状态,才能避免冲压起皱的发生。
只有在充分考虑这些因素的基础上,才能获得高质量的冲压产品。
冲压件起皱原因和控制方法的浅析
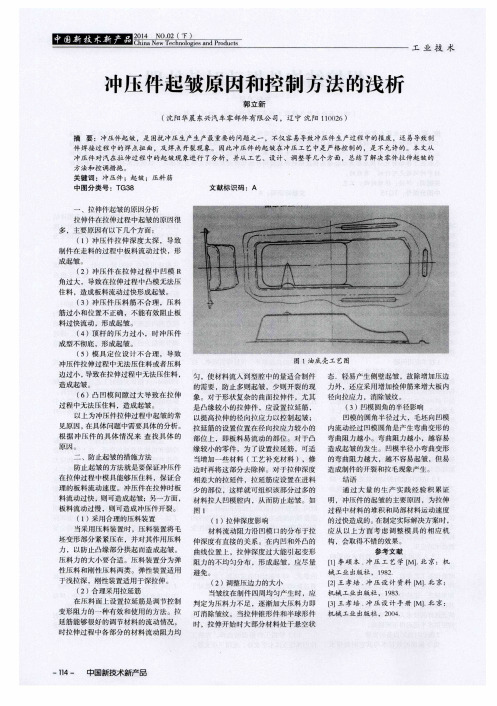
的过快 造成 的 。 在 制定 实 际解决 方案 时 ,
材料 流 动阻 力沿 凹模 口的分 布 于拉 应 从 以 上 方 面 考 虑 调 整 模 具 的 相 应 机 坯变 形 部分 紧 紧压 在 ,并 对其 作 用压 料 伸深 度 有直 接 的 关系 。在 内凹和 外 凸 的 构 ,会 取得 不错 的效 果 。 力 , 以防止 凸缘 部 分 拱起 而造 成 起 皱 。 曲线 位 嚣 上 ,拉伸 深 度过 大 能 引起 变形 参考 文献
压料 力 的 大小 要合 适 。压 料装 置 分 为 弹 阻 力 的不 均匀 分 布 ,形成 起 皱 ,应 尽量 f 1 】 李硕 本 . 冲压 工艺 学 【 M】北 京 :机 性 压 料 和 刚性 压料 两 类 。弹性 装 置适 用 避免 。 械 工 业 出版 社 , 1 9 8 2 于浅 拉深 ,刚性装 置适 用 于深拉 伸 。 ( 2) 调 整压 边力 的大 小 『 2 1 王孝培 . 冲压设 计资料 【 M1 . 北京: ( 2 )合理 采用 拉延 筋 9 8 3 . 当皱 纹 在制 件 四周 均 匀产 生时 ,应 机 械 工业 出版社 ,1 在压 料面 上 设置 托延 筋 是调 节控 制 判定 为 料 力 不 足 ,逐渐 加 大压 料 力 即 I 3 l 王孝 培 . 冲压设 计手册 l M】 . 北京: 变 形 阻力 的一 种有 效 和使 用 的方 法 。拉 可 消除 皱纹 。当拉 伸 锥形 件 和半 球形 件 机 械 工业 出版社 ,2 0 { ) 4 延 筋 能够 很 好 的调 节 材料 的 流动 情 况 , 时 ,拉 伸开 始 时 大部 分材 料 处于 悬 空状
摘 要 :冲压件 起 皱 ,是 困扰 冲压 生产 生产 最 重要 的 问题 之 一 ,不仅容 易导致 冲压 件 生产过 程 中的报 废 ,还 易导致 制
- 1、下载文档前请自行甄别文档内容的完整性,平台不提供额外的编辑、内容补充、找答案等附加服务。
- 2、"仅部分预览"的文档,不可在线预览部分如存在完整性等问题,可反馈申请退款(可完整预览的文档不适用该条件!)。
- 3、如文档侵犯您的权益,请联系客服反馈,我们会尽快为您处理(人工客服工作时间:9:00-18:30)。
4 起皱云图和起皱的预测
要用实验来验证上述理论, 必须精确测量出压 板与板料间的间隙 2∆, 因为这个间隙很小, 而且材 料本身的不平, 很难得到可靠的结果。因此可采用 数值计算方法, 借助于计算机仿真技术, 将利用上 面理论计算得到的板料各处的临界因子 r (它反映 各处发生起皱的难易程度) 用云图描述出来, 临界 因子 r 在数值上等于临界压力与当前实际应力之
第20卷第1期 2003 年 2 月
计算力学学报 Ch inese Journa l of Com puta tiona l M echan ics
V o l. 2 0 , N o. 1 Feb ruary 2003
文章编号: 100724708 (2003) 0120095206
薄板冲压成型中板料起皱的 临界应力分析和预测
Ρ=
1 2
[ (Ρx -
Ρy ) 2+ (Ρy -
Ρz ) 2 +
(Ρz -
Ρx ) 2+
6 (Σx2y +
Σ2 yz
+
Σ2 zx
)
]
(10)
将 (6)、(7)、(8)、(9) 式代入 (10) 式, 并对 x、 y、z 变分, 可求得 Ρ 的最大值 Ρmax, 它只含有一个未 知量N x。板料产生起皱时, 最大等效压应力处的等 效应力值等于材料的屈服极限 Ρs, 即:
Π2D
(1 L0
+
L 0) 2
(5)
此时挠曲面的表达式为
Ξ=
a11 sin
Πx
L0
s in Πy
(6)
可知, 当压力达到临界压力值时, 板料将失稳
96
计算力学学报
第 20 卷
屈曲呈 (6) 式描述的曲面状态, 从 (6) 式可看出, 这 个挠曲状态不是唯一的, 理论上讲挠度 a11 可为任 意正数。根据材料失稳的定义, 当压力达到临界压 力值时, 在挠曲方向施加一很小的横向载荷就可改 变它的挠度大小。
3 受到横向载荷时板料的屈曲
由于薄板冲压成型中, 压板作用力在冲压开始 时就存在, 根据前面的推论, 似乎起皱永远也不会 发生, 但事实并非如此, 这是因为压板与板料之间 并非处处紧密接触, 而且压力也不会均匀分布。如 图 2 所示区域的板料与压板存在间隙 2∆, 以这一区 域的板料为研究对象, 当压应力 N x 达到 (N )x cr0 时, 板料就会失稳, 在振动等扰动作用下, 板料会挠 曲与压板接触。如果此时压应力进一步增大压应力 N x , 在图 2 所示的受力状况, 此时必须有足够的压 力Q 阻抗板料的进一步拱起, 从而保持压板与板料 的相对距离 2∆ 不变。但是随着压应力 N x 的增大, 板料与压板的接触状况也会改变, 由最初的点接触 变成面接触, 此时 (6) 式已不能正确反映板料的真 正曲面, 板料的变形也要转移, 由半个正弦曲线转 向一个正弦曲线。一些学者研究了半个正弦曲线和 一个正弦曲线板料变形时抑制起皱的压板作用力 与应变的关系, 得出两者曲线相交处为板料发生起 皱的临界点, 而计算出起皱的临界应力和预防起皱 的最小压板力[11 ]。
2 无横向载荷时板料的屈曲
如图 1 所示, 设被研究的板料初始为长 L 0、宽 一个单位、厚度为 t 的矩形板, N x 表示沿宽度方向 均布的单位长度的压力。逐渐地增大N x , 受压板的 水平的平衡位置将变为不稳定而开始屈曲。研究这 临界情况, 设屈曲板的挠曲面表达式为
收稿日期: 2001205222; 修改稿收到日期: 20012102301 作者简介: 谢 晖 (19712) , 男, 博士.
谢 晖
(湖南大学 汽车技术研究与开发中心, 湖南 长沙 410082)
摘 要: 针对薄板冲压成型中起皱这一常见的材料失效形式, 运用板料压缩失稳理论, 提出了虚拟刚度变量的概 念和板料产生起皱的临界应力计算方法, 并借助于计算机仿真技术和有限元计算方法, 搜寻并计算得到反映板 料各处发生起皱难易程度的临界因子, 生成起皱云图来观察材料各部分的稳定状态, 预测可能出现起皱的部位, 为修改冲压工艺和修模提供依据, 通过分析起皱云图得出的结论与实际情况非常接近。
谢 晖: 薄板冲压成型中板料起皱的临界应力分析和预测
97
标。对于集中力Q 仅在作用点处的微分面积上 q = Q dx dy , 其余各处 q = 0。在薄板冲压成型中, Ρx、 Ρy、Σxy 为主要应力, Σxz、Σyz 是次要应力, Ρz 是更次要 的应力, 在计算中常常可以忽略。等效应力 Ρ 的表 达式为
W + ∃T 1 = ∃U
进行以下计算: 设 2∆ 为已知 (由仿真计算的核心计算得到) ,
板料失稳后随着压应力 N x 的增大, 假设板料仍保 持理想的正弦曲面状态, 即 (6 ) 式仍成立, 且 a11 = 2∆, 这意味着板料的弯曲刚度将随着变化, 因此假 设虚拟刚度变量
DN =
N (N x
x
)
c
D
r0
(7)
根据薄板弯曲理论有:
用能量法进行研究, 挠度曲面可表示成通常的 插值形式:
4
∑ Ξ = N iΞi ( i = 1、2、3、4)
(13)
i= 1
其中插值函数N i 是自然坐标 (局部坐标) 的函数, Ξi 是单元的结点挠度, 是待定参数。这里采用等参 单元, 构造的插值函数为
N 1=
1 4
(1 -
Ν) (1 -
Γ) , N 2 =
关于起皱发生的临界点的确定应考虑以下几 点:
① 起皱由失稳引起但不等同失稳, 一般它应 发生在失稳之后, 失稳的临界值只是决定了起皱的 可能性;
② 发生起皱时板料内应伴随有塑性变形, 如 果在板料失稳时材料未屈服, 则只有当板料内至少 有一处的等效应力值大于或等于材料的屈服极限
Ρs 时, 起皱才会发生; ③ 如果在板料失稳前材料已经局部屈服, 则
2N
xy
5Ξ 5x
5Ξ 5y
]dx
dy
(16)
N x、N y 为单元X 、Y 方向的正应力, N xy 为剪应 力, 对于满足已知的边界条件, 欲求临界应力 (膜 力) , 可设弯矩M x、M y 不变, 如果 N x、N y、N xy 不是 常量, 可设 N x、N y、N xy 的表达式中有一公因子 r, 逐渐增大公因子 r 可使板料趋近于屈曲状态, 而使 板料屈曲的最小 r 决定了临界载荷。
以 ∃U 表示弯曲应变能, D 1、D 2、D k 为刚度,
98
计算力学学报
第 20 卷
κ ∃U =
1 2
[D 1 ( 55x2Ξ2 ) 2 +
2D
1v 2
52 Ξ 5x 2
52Ξ 5y 2
+
D 2 ( 552yΞ2 ) 2 +
4D
k
(
52 Ξ 5x 5y
)
2
]dx
dy
(17)
则力的临界值由下列方程得到:
∞∞
∑∑ Ξ =
m=
1
n=
am n
1
sin m Πx
L0
s in n Πy
(1)
用能量法计算板料屈曲的临界压力, 即板料达到临 界屈曲状态时弯曲应变能等于压力所作的功。D 表 示板料的弯曲刚度, 弯曲应变能为
∑∑ ∃V =
Π4L 8
0D
∞ m= 1
∞ n= 1
am2
n
(m L
2
2 0
+
n2) 2
(2)
此时, 虚拟刚度 D N 虽然为变量, 但我们感兴 趣的只是起皱发生时的虚拟刚度值, 若各应力分量 按 同一比例因子 t 变化趋近临界状态, 则板料处于 起皱临界状态时, 虚拟刚度变量
D N = tD
(12)
将 (12) 式代入 (7) 式, 可求出 t 值, 临界压力 (N )x cr 就可得 (N )x cr = t (N x ) cr0。同理, 可求得其它 各临界应力分量。
关键词: 失稳; 起皱; 云图; 计算机仿真 中图分类号: T G386. 41 文献标识码: A
1 引 言
起皱是薄板冲压成型过程中常常遇到的一个 难题。 起皱严重时, 可能导致坯料难以通过凸凹模 间隙而被拉断; 轻微的起皱即使不致于阻碍坯料通 过间隙, 也可能在拉深件上留下皱痕而影响其表面 质量。 定性地讲起皱是压缩失稳的表现形式, 一般 来说当切向压应力达到或超过板料的临界应力时, 起皱就可能发生; 但在薄板冲压成型中, 由于板料 各部分的受力不同而且很复杂, 使得产生起皱的临 界应力的计算相当棘手。本文运用板料压缩失稳理 论, 从较简单的力学模型出发, 提出了板料起皱的 临界应力的计算方法。为了较精确地描述板料各部 分发生起皱的可能程度, 本研究从 16 个单元区域 的起皱分析入手, 初步得到各单元的起皱临界因 子, 然后进一步进行区域搜索或选定区域计算, 找 到包含某单元最可能发生起皱的区域, 得到能反映 各单元起皱发生难易程度的临界因子, 并用云图将 它描述出来, 从而较精确、直观地预测起皱的发生。
(N )x cr0 =
Π2L 20D
m2
(m L
2
2 0
+
1) 2
(4)
它表示板料屈曲时在 y 方向只有一个半波, 在 x 方向可以有 m 个半波, (N )x cr0 值与板料的长宽 比、屈曲的半波个数 m 值有关, 若 L 0 约等于 1, 则 m = 1 时得临界压力的最小值:
(N )x cr0 =
M x= -
DN
(
52 Ξ 5x 2
+
Λ 552yΞ2 ) ,M y= -
DN
(
52 Ξ 5y 2
+
Λ 55x2Ξ2 ) ,