第七篇 高速轧机主控台控制操作技
轧机主控台岗位职责、操作工艺规程

轧机主控台岗位职责、操作工艺规程—、岗位名称:轧机操作台工。
二、岗位职责:(1) 、热悉和了解轧钢生产工艺流程,全面掌握轧制工艺及控冷工艺的参数。
(2) 、负责控制从1#机架到吐丝机的全工艺过程。
(3) 、负责监视全生产线的机械,电气能源介质供应系统的设备运行状况。
三、操作规程(A)主控台操作规程1、操作工进入岗位前劳保必须穿戴齐全。
2、准时参加班前会,了解上个班的工艺运行状况,必须听清楚班长工作安排。
3、接班时必须交接当前设备、工艺运行状态,数据必须交接清楚,若有异常及时通知相关负责人进行处理。
4、交接班检查严禁启动机械设备,若需试车,必须得到现场指挥人员的指令并确认线内无人检查时方可启动设备。
5、主轧机启动前,润滑系统、液压系统、冷却系统必须处于运行状态,且指示灯亮。
6、主轧机启动前,必须确认面板上未挂检修牌,且经现场调度同意。
7、主轧机启动前,操作台工必须发出启动信号,方可启动设备。
8、过钢前必须确认各设备运行正常(注意观察空载电流);过钢前必须接到现场指挥人员指令,先送上要钢信号灯,并在钢坯出炉前向全线发出警报。
9、在操作过程中,要适时调整修改工艺技术参数,处理好各架次的堆拉关系,主张微张力轧制,以确保产品质量,时刻观察1-18架轧机,精轧机电流变化,夹送辗、吐丝机转数有电流变化值,6个活套的调节量,如有异常及时通知当班班长和机组负责人!10、严格按信号灯指示,过钢生产,发出堆钢、跑钢事故及时卡断并关闭信号灯(参照特殊操作注意事项)。
11、接到正常停车检查指令时必须先确认轧件已出吐丝机,才可以停车,以免造成压车事故。
12、停车后,各辘道、轧机、飞剪等设备开关手柄按钮应打到O 位,关闭电源,以防设备自动运转造成事故。
(B)主控台操作注意事项—、更换轧制规格1、根据轧制规格选用相对应的轧制程序表。
2、看看表里的工作辘径和现在要换的工作總径、延伸系数是否一致。
(必须确认现场原始辐径)。
3、输入目前使用精轧辘环工作辘径。
轧机设备操作规程
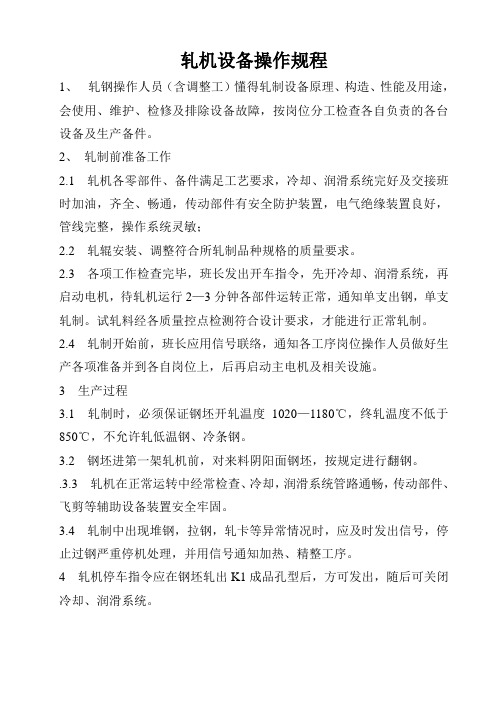
1、轧钢操作人员(含调整工)懂得轧制设备原理、构造、性能及用途,会使用、维护、检修及排除设备故障,按岗位分工检查各自负责的各台设备及生产备件。
2、轧制前准备工作2.1 轧机各零部件、备件满足工艺要求,冷却、润滑系统完好及交接班时加油,齐全、畅通,传动部件有安全防护装置,电气绝缘装置良好,管线完整,操作系统灵敏;2.2 轧辊安装、调整符合所轧制品种规格的质量要求。
2.3 各项工作检查完毕,班长发出开车指令,先开冷却、润滑系统,再启动电机,待轧机运行2—3分钟各部件运转正常,通知单支出钢,单支轧制。
试轧料经各质量控点检测符合设计要求,才能进行正常轧制。
2.4 轧制开始前,班长应用信号联络,通知各工序岗位操作人员做好生产各项准备并到各自岗位上,后再启动主电机及相关设施。
3 生产过程3.1 轧制时,必须保证钢坯开轧温度1020—1180℃,终轧温度不低于850℃,不允许轧低温钢、冷条钢。
3.2 钢坯进第一架轧机前,对来料阴阳面钢坯,按规定进行翻钢。
.3.3 轧机在正常运转中经常检查、冷却,润滑系统管路通畅,传动部件、飞剪等辅助设备装置安全牢固。
3.4 轧制中出现堆钢,拉钢,轧卡等异常情况时,应及时发出信号,停止过钢严重停机处理,并用信号通知加热、精整工序。
4 轧机停车指令应在钢坯轧出K1成品孔型后,方可发出,随后可关闭冷却、润滑系统。
1、精整设备操作人员,懂得设备原理、构造、性能及用途、会使用、维护、检修及排除设备故障。
2、启动精整设备前,必须认真检查各零部件齐全完好,定倍尺装置调整到位,锯片质量和安全装置齐全可靠。
3、冷床/散泠滚道各气缸管路无漏气,电气管线完整,操作系统灵敏,符合正常生产要求。
4、冷床/散泠滚道同步运转良好,发现异常情况及时排除。
5、精整设备运转过程中,经常检查过润滑点的润滑情况及管路无泄漏。
6、当出现成品冲冷床跑槽或吐丝机卡钢时,应立即停止过钢处理、操作控制台及时发出信号通知停止轧制。
主控台操作规程

棒材线主控台工艺技术规程一、主控台控制的区域设备主控台控制的设备有:粗、中、精轧机组,1#、2#、3#飞剪,1#~6#活套器,可移式变频辊道及控冷装置(水冷辊道),夹送辊,冷床输入A、B、C三段变频辊道,裙板上钢装置,步进式冷床。
二、主控台参数设定1、轧制程序设定,根据生产的品种输入标准料型速度参数,在输入数据时应检查确认,防止错误。
2、1#、2#飞剪切头、切尾长度及剪切速度。
3、3#飞剪剪切速度、倍尺长度、附加长度、测量方式、成品机架选择设定,优化功能投入设定。
4、活套器控制高度、起套、落套延迟时间设定。
5、控制水冷线水量、水压、轧件温度等淬火工艺参数设定。
6、冷床输入辊道参数设定,裙板动作周期的设定。
7、热倍尺上冷床制动距离设定。
8、冷床步进动作参数设定。
9、对中间甩机架的参数设置,被甩机架的参数应填写下游机架的参数。
以确保轧制线速度级联关系的传递。
10、轧制中换辊参数设定,在轧制参数表中输入新辊辊径,点击计算计算辊径按钮和计算转速按钮,然后进行下载操作,确保机架线速度不变。
11、参数下载,所有参数输入并检查确认后,应在全线停机状态下进行数据的下载发送操作,数据下载后应在操作台上清“零”。
三、主控台操作按键和操作方式选择。
1、自动或手动出钢选择按键。
2、粗、中、精轧机组启/停按键,停车分为正常和快速两种情况。
3、1#、2#、3#飞剪手动/自动选择开关,启动/停止投入按键。
4、全线设备单动控制或集中控制选择。
6、轧机速度微调选择,选择轧机在线快速调速和慢速调速。
7、报警灯光显示及复位键。
8、1#2#3#飞剪自动或单动控制选择,投入使用按键。
9、程序设定修改使用CRT/键盘。
四、开车前主控台操作准备1、单台设备的启停,在启机前操作人员必须对设备本体及周围进行检查确认,确认无人检修,无碍设备运转具备启动条件后方能启动设备。
2、轧线联动启车,开车前主控操作工必须检查确认,所有选择开关都处于“允许动作”或“自动”位置,各区域设备处于就绪状态。
轧机控制说明

五机架连轧管机组第一机架电控调速使用说明
电控设备面板一共三个按键:“菜单P”、“增加▲”、“减小▼”
1、初始界面显示为“o70”,选择“菜单P”键,显示“P001”,选择“增加▲”
至显示“P51”,选择“菜单P”,显示“0”,按住“增加▲”将数值调至最大(该步含义为获得修改权限)。
2、选择“菜单P”返回至“P51”,按住“增加▲”直到显示“P401”,选择“菜
单P”显示“001”,再按一下“菜单P”即显示电机频率数值,选择“增加▲”
或“减小▼”可进行修改。
3、修改完成后,按“菜单P”返回至“001”,再返回至“P401”,按住“减小▼”
调至最小值“P001”,选择“菜单P”回到初始显示“o70”,操作完成。
注:按住“增加▲”再按“减小▼”时可加快数值变化速度,反之亦然。
轧钢高线主控台操作注意事项
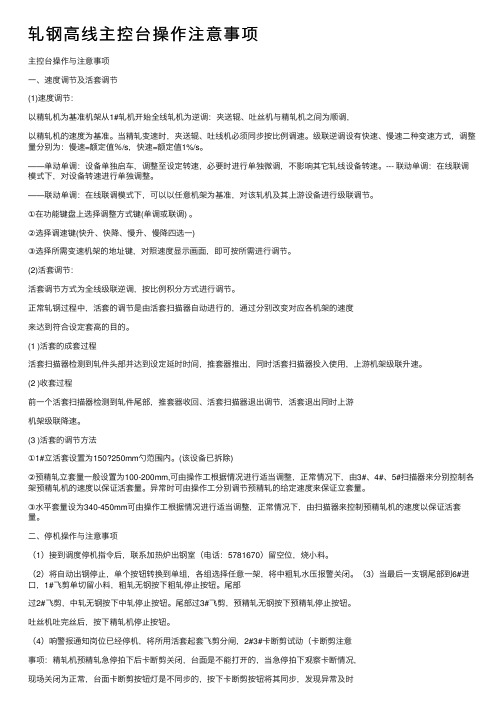
轧钢⾼线主控台操作注意事项主控台操作与注意事项⼀、速度调节及活套调节(1)速度调节:以精轧机为基准机架从1#轧机开始全线轧机为逆调:夹送辊、吐丝机与精轧机之间为顺调,以精轧机的速度为基准。
当精轧变速时,夹送辊、吐线机必须同步按⽐例调速。
级联逆调设有快速、慢速⼆种变速⽅式,调整量分别为:慢速=额定值%/s,快速=额定值1%/s。
――单动单调:设备单独启车,调整⾄设定转速,必要时进⾏单独微调,不影响其它轧线设备转速。
--- 联动单调:在线联调模式下,对设备转速进⾏单独调整。
――联动单调:在线联调模式下,可以以任意机架为基准,对该轧机及其上游设备进⾏级联调节。
①在功能键盘上选择调整⽅式键(单调或联调) 。
②选择调速键(快升、快降、慢升、慢降四选⼀)③选择所需变速机架的地址键,对照速度显⽰画⾯,即可按所需进⾏调节。
(2)活套调节:活套调节⽅式为全线级联逆调,按⽐例积分⽅式进⾏调节。
正常轧钢过程中,活套的调节是由活套扫描器⾃动进⾏的,通过分别改变对应各机架的速度来达到符合设定套⾼的⽬的。
(1 )活套的成套过程活套扫描器检测到轧件头部并达到设定延时时间,推套器推出,同时活套扫描器投⼊使⽤,上游机架级联升速。
(2 )收套过程前⼀个活套扫描器检测到轧件尾部,推套器收回、活套扫描器退出调节,活套退出同时上游机架级联降速。
(3 )活套的调节⽅法①1#⽴活套设置为150?250mm勺范围内。
(该设备已拆除)②预精轧⽴套量⼀般设置为100-200mm,可由操作⼯根据情况进⾏适当调整,正常情况下,由3#、4#、5#扫描器来分别控制各架预精轧机的速度以保证活套量。
异常时可由操作⼯分别调节预精轧的给定速度来保证⽴套量。
③⽔平套量设为340-450mm可由操作⼯根据情况进⾏适当调整,正常情况下,由扫描器来控制预精轧机的速度以保证活套量。
⼆、停机操作与注意事项(1)接到调度停机指令后,联系加热炉出钢室(电话:5781670)留空位,烧⼩料。
钢铁厂轧机主操台安全操作规程

钢铁厂轧机主操台安全操作规程1、交接班时应检查主控台所控制的各种设备的操作牌是否处于安全状态,是否有人尚在作业。
开机前必须检查检修操作牌是否处于安全状态及轧机传动部分是否有人。
2、轧制前应确认与各通讯点通讯无误,全线无影响正常轧制的故障和信号。
3、轧制前应正确设定,核对所使用的轧制程序,确认各主、辅传动设备及各种控制按钮处于正常工作状态。
4、在轧钢前,应全线模拟一遍,以确认各活套、剪机动作正常。
5、例检、检修后开车与出钢均应拉警报(三次)通知全线,班中停机以及取样后再次轧钢要传呼(拉警报)通知全线。
6、根据生产情况控制各工艺的生产节奏,认真执行按炉送钢制度,换炉号应及时、准确通知精整控制台。
7、不允许在“test”状态下轧钢。
8、轧线发生故障时,不允许后续轧件继续进入事故段。
9、检查或处理轧区故障时,应停机处理,在检查完毕或排除故障原因之后,事故信号消除方可启动设备轧钢。
10、严禁带负荷开、停车。
11、当现场发生危及人身、设备的事故时,应启动“紧急停车”键。
12、在处理剪机故障时应切断传动电源,并严禁出钢。
13、当发现所属区域的设施有异常现象时,应及时报告有关部门并采取措施,保证主控台内所管辖区域的各种信号、图像的完好性,如有异常,及时向车间调度反馈。
14、工作时应集中精力,不允许做任何与操作无关的事。
15、全线停轧时,应切断所有主、辅传动电源。
16、在检修期间,应严格执行操作制度,并按检修人员的要求和指令进行试车。
17、操作台应保持清洁,操作台板上禁止放杂物。
严禁在操作台内吸烟、吃零食。
严禁将水泼到各种电器设施上。
高速线材轧机主控台操作技术

⑸、轧制节奏的控制
①粗轧机组出口与飞剪之间:
借助于粗轧机组后热检检测的轧件位置信息,当相 邻轧件的头、尾间隙时间小于5s时,自动启动粗 轧后飞剪碎断轧件,并持续5s;
②斯太尔摩运输段:
当运输段速度小于0.5m/s时,在轧件最后一圈吐出 吐丝机后,自动升速至0.5m/s, 并持续5s。
级联控制是指手动修改主传动系统中某一个轧机的速
度,而自动控制系统将根据以前存在的速度关系来改变其 他上游传动系统的速度与之相适应。级连校正又分上游调 节和下游调节两种形式,调节作用方向视具体机架(基准 机架)而定。
①、上游级联校正。这种方式是控制调节位于本机架及其上 游机架的主传动电机的转速。例如,如果需要调节11号 ~10号机架间张力过大的情况,则应提高第10号机架的 转速。第10号机架升速仅改变了11号~10号机架机架之 间的速度关系,而10→9→8→7→…→1号机架速比不变, 即10号机架升速的同时,10→9→8→7→…→1号机架都 以与10号机架相同的比例升速,这就是上游级联调节。 该种调节方式是逆连轧方向的调速。
高速线材轧机 主控台控制操作技术
培训提纲
一、高速线材主控台的职能和对操作人员素质 要求
二、高速线材轧机对电气传动和自动化控制系 统的要求
三、榆钢高线工艺布置简介 四、榆钢高线主控台主要设备功能介绍 五、榆钢高线人机界面(HMI)功能及基本操作介
绍 六、高速线材轧机工艺参数调整与操作 七、主制台安全操作要点与常见故障分析处理
②下游级联校正。这种方式是控制调节所选定机架下游的轧 机主传动电机的转速。例如,如果需要调节12 号和13号 机架之间的速度配比关系,则应通过改变13号机架的转 速来实现。当选中13号机架做级连校正调节时,13号机 架→精轧机组→夹送辊都以相同的比例变速。下游调节是 顺轧制方向的调速。
高速线材轧机的活套控制
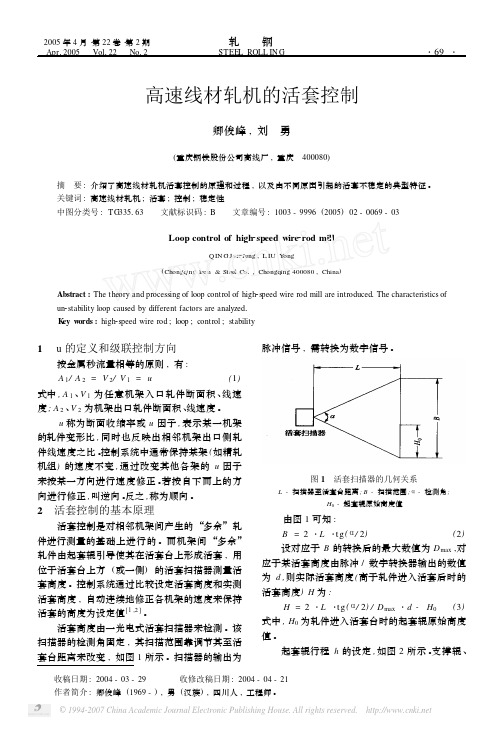
高速线材轧机的活套控制卿俊峰,刘 勇(重庆钢铁股份公司高线厂,重庆 400080)摘 要:介绍了高速线材轧机活套控制的原理和过程,以及由不同原因引起的活套不稳定的典型特征。
关键词:高速线材轧机;活套;控制;稳定性中图分类号:TG 335163 文献标识码:B 文章编号:1003-9996(2005)02-0069-03Loop control of high 2speed wire 2rod millQIN G J un 2feng ,L IU Y ong(Chongqing Iron &Steel Co 1,Chongqing 400080,China )Abstract :The theory and processing of loop control of high 2speed wire rod mill are introduced 1The characteristics of un 2stability loop caused by different factors are analyzed 1K ey w ords :high 2speed wire rod ;loop ;control ;stability收稿日期:2004-03-29 收修改稿日期:2004-04-21作者简介:卿俊峰(1969-),男(汉族),四川人,工程师。
1 u 的定义和级联控制方向按金属秒流量相等的原则,有:A 1/A 2=V 2/V 1=u(1)式中,A 1、V 1为任意机架入口轧件断面积、线速度;A 2、V 2为机架出口轧件断面积、线速度。
u 称为断面收缩率或u 因子,表示某一机架的轧件变形比,同时也反映出相邻机架出口侧轧件线速度之比。
控制系统中通常保持某架(如精轧机组)的速度不变,通过改变其他各架的u 因子来按某一方向进行速度修正。
若按自下而上的方向进行修正,叫逆向。
反之,称为顺向。
- 1、下载文档前请自行甄别文档内容的完整性,平台不提供额外的编辑、内容补充、找答案等附加服务。
- 2、"仅部分预览"的文档,不可在线预览部分如存在完整性等问题,可反馈申请退款(可完整预览的文档不适用该条件!)。
- 3、如文档侵犯您的权益,请联系客服反馈,我们会尽快为您处理(人工客服工作时间:9:00-18:30)。
第七篇高速轧机主控台控制操作技术第一章主控台操作分工与操作技术素质要求主控台是控制全轧线生产的中心操作室,是全厂的中央信息处理站,在高速线材轧机的连轧控制中,主控台对轧制的正常顺利进行起着关键作用。
下面以某钢厂高速线材轧机的主控台为例进行介绍。
一、主控台所管辖的区域设备主控台所管辖的区域设备有:(1)粗轧机组、中轧机组、预精轧机组、精轧机组以及夹送辊、吐丝机。
(2)粗轧机组后的飞剪、预精轧机组前的事故卡断剪、精轧机组前的飞剪、事故卡断剪及轧制平台下的事故碎断剪。
(3)轧线上所有活套控制器。
(4)轧制平台下载运废料的振动运输机。
二、主控台的职能与控制对象主控台的职能与控制对象有:(1)设定、调用、修改轧制程序。
(2)控制上述所有轧制区设备的动作及运行。
(3)监控轧制区的轧制过程,实现轧制工艺参数和程序控制最优化。
(4)控制轧机各机组的轧辊冷却水开与闭。
(5)组织、协调轧制生产工艺,保证生产的正常进行。
(6)担负轧制生产线的日常生产信息传递,进行轧制区物料跟踪方面的操作。
(7)有关生产数据报表的记录与汇总。
(8)监视全生产线的机械、电气、能源介质供应系统的设备运行状况与故障显示。
三、主控台与生产调度室及各操作台(点)的分工和关系1、主控台与生产调度室的关系主控台主要负责生产线上轧制生产的组织与协调,即偏重于轧钢生产人员本身的内部指挥;生产调度室主要负责轧制生产的总体指挥与协调,它的任务有:与公司总调系统的对口联系,与水、电、风、气等外部能源介质供应单位的联系,对高速线材厂(车间)3个专业(轧钢、电气、机修)的指挥与协调,即偏重于轧钢外部的联系。
2、主控台与各操作台(点)的关系根据高速线材生产工艺流程特点,一般说来,轧制生产线上配置有 5个操作台:入炉操作台(负责原料区原料的入炉与计量);加热出钢操作台(负责加热炉加热工艺操作和出钢操作);主控台(负责轧制区的轧制生产工艺操作和轧钢生产协调);冷却控制台(负责冷却工艺操作);卸卷操作台(负责成品盘卷的称量,标牌打印,卸卷等操作)。
主控台对上述4个操作台具有指挥与领导作用,即设备的开、停机命令、轧制生产的节奏与控制指令都是由主控台发出。
四、主控台人员的操作技术素质要求主控台对操作人员的技术素质要求的内容有:(1)较为全面地了解轧钢工艺知识。
(2)具有一定的机械与电控基础知识。
(3)对本厂设备(特别是对轧制区的设备)与功能有一定的了解。
(4)掌握质量控制的基础知识。
第二章电气控制与工艺过程自动化第一节高速线材连轧工艺对电气控制和自动化控制的要求高速线材轧制工艺的基本特点是:(1)全连续式连轧工艺。
(2)较高的成品轧制速度(邢钢高速线材轧机目前最高轧制速度已达到 140m/s)。
(3)表面质量和内部质量全优的成品(公差可达±0.1mm)。
(4)大卷重、高生产率。
(国内最大线材卷重达 2t 左右,最高小时产量达 140t)。
由上述的基本特点,决定了对电气控制和自动化控制技术的高要求。
具体概括为如下3个方面。
一、连轧工艺对主传动特性的要求为动态地满足各机架轧件秒流量相等这一连轧关系的基本原则,在全连轧过程中,要不断用调节有关机架主传动转速来微调轧辊转速,抵消各种外扰因素带来的不利影响。
为此,高速线材连轧机对主传动的要求有:(1)调速范围大。
高速线材连轧机主传动(驱动轧辊的电机)已普遍采用直流电机,以解决调速问题。
直流电机有以下特点:A、优点:可以精确控制速度;速度控制范围大;可以定速运转;可以制造启动转矩非常大的电机;B、缺点:因结构复杂而难以维护;重量大,价格高。
(2)调速精确度高,静态速降小。
实际生产中,为调整产品规格和改变轧件堆拉状况,改善产品尺寸精度,要求主传动的调速精确性达到很高的水平才能准确地设定各架轧制速度,并在连轧过程中准确地纠正已经观察到的过度堆拉钢现象。
现场操作表明:高速线材轧机主传动电机的静态速降不大于±0.1%,当给定控制精度在±0.1%左右时,才能较好地满足控制产品尺寸公差的要求。
(3)动态速降小与恢复时间短。
轧机主传动直流电机在受到突加负载(咬钢)时,会产生转速的降低,由于速度调节系统的作用使电机在转速恢复过程中,转速的变化呈阻尼衰减的波动形状。
其中开始转速下降至最大值称为动态速降值,转速恢复到静态速降的时间称为恢复时间。
轧钢主传动电机在咬钢发生动态速度降低时,连轧相邻机架的金属秒流量暂时失去平衡,产生两方面后果:1)在相邻机架间积累了一个多余的轧件长度(活套)。
2)处于轧辊间变形区的轧件头部因受堆挤而增大(增宽和增厚,主要是增宽)。
为保证轧件全长尺寸的一致性,故需切去轧件头部的增大端(剪机切头长度的确定将在后面提到)。
综上所述,减少主传动动态速降和缩短恢复时间将对稳定转速关系亦即堆拉关系有利,从而能够获得稳定的轧制条件。
(4)调速快。
在高速线材轧机操作中,更换产品、规格后的重新设定主传动转速的调速操作一般在未轧制前进行,因此有足够的时间来改变主传动转速。
但随机调速、调整堆拉关系或补偿转速偏差,因在轧制过程中进行,则需要在尽可能短的时间内完成,以减小轧件中间尺寸变化对线材成品的影响。
这就要求轧机主传动调速能做到快速,纠偏能力大。
现代高速线材轧机在供电和调速方面广泛采用了可控硅整流器,直流电机传动的开环与闭环控制回路也在不断地改进,并引入了计算机控制,以满足轧制高速度对控制系统的调速性能要求。
二、轧制高速度、产品高精度对自动化控制的要求线材生产向着高速化、自动化和高精度方向发展,为实现这些要求必须对生产过程进行严格、精密、准确而又迅速的控制,这种控制只有采用电子计算机才能完成。
随着自动化检测仪表和执行装置的日趋完善,电子计算机已成为高速线材轧制技术不可缺少的组成部分,并对全生产过程进行自动控制。
现代化高速线材轧制技术要求计算机控制完成以下任务:(1)轧制速度与轧制程序的计算、控制与存贮。
(2)根据要求的切头(尾)长度和相应的轧制速度,计算出所有切头飞剪的启动时间,速度超前量大小,并对剪机实行自动控制。
(3)在活套控制系统中计算活套的抬起、下落时间,实现机组和机架间的活套自动调节。
(4)根据预先计算的轧制速度跟踪轧件通过各机组的时间和过程。
(5)水冷段水阀开启数量,水阀的开、闭时间与冷却程序的计算、控制和存贮。
(6)对所有在线的辅助传动装置实行同步运转计算与控制。
(7)在显示屏上以数字形式显示操作人员所需要的数据,如转速、线速度、切头量、超前量、吐丝系数等。
三、生产的高效率对计算机的要求提高轧机效率是使生产得以经济合理的必要措施。
由于电控技术和计算机技术的发展,大大提高了对故障监控与生产管理的自动化程度,在现代化控制中计算机主要完成:(1)采用“目标跟踪”技术,即时刻跟踪轧件所处的位置,并将其相应的数据输入计算机。
计算机按规定指令对诸如钢种、批号、重量、尺寸等参数显示,并按批、按班、按日、按月综合统计成生产报表,并用打印机打印报出。
(2)对在线使用的轧辊(辊环)实行自动管理,内容应包括:轧槽轧制吨位与总轧制吨位,轧槽代号等。
(3)在轧制过程中,显示诸如轧制电流、轧制压力等工艺参数。
(4)对各个系统及各台设备运行状况进行监视,并按区分类对故障显示和报警。
第二节高速线材轧机各机组的主传动特点与参数一、各机组的主传动特点由于高速线材轧机各机组的工艺布置形式和电气控制方式不同,因而各机组采用了不同的主传动布置形式与调速特点。
A 粗、中轧机组粗、中轧机组的主要任务是利用轧件的高温,增加轧件的延伸。
轧件断面相对较大,轧制速度较低,机架间间距也较大。
在该两机组,对每个机架都采用了带有整流装置的直流电机单独传动,各架轧机的转速手动可调以维持连轧关系,每个机架的单独传动装置均采用了重型联合传动装置这一先进的设计,它可以只用一个简单的传动箱就实现总的减速比。
B 预精轧机组预精轧机组由四架或两架轧机组成,采用直流电机单独传动。
机组各机架呈水平垂直交替布置以消除轧件在机架中的扭转。
各架间布置有活套控制器以自动调节轧机转速来保证轧件的无张力轧制。
单独传动的单线预精轧机组,再配合活套控制器,是预精轧机的传动和调速特点。
其优越性是中间轧件表面质量好,断面公差小而保证了废品减少,可满足精轧机组的来料需求。
C 无扭精轧机组无扭精轧机组的传动特点是采用集体传动形式。
这是因为轧件断面越小(如φ5.5 线材,其截面积F=23.8mm2),终轧速度越高(目前大部分终轧速度大于50m/s,最快达140m/s),要靠电气控制来保证连轧条件就越困难。
而且这种轧机机架间距小,在结构上也难以实现单机传动。
成组集体传动,同机组各机架间无法实现速度的互相调节,连轧关系要靠孔型设计,固定速比和正确的辊缝设定来保证。
只有合理的孔型设计与符合要求的红坯来料才能保证预计的微张力轧制效果,得到满意的成品尺寸精度。
二、主传动参数各机架的主传动参数在设计时选定。
各厂家由于所选用的坯料、机架数等工艺参数不同,主传动参数也有所不同,主控台操作人员应熟知主传动参数中的有关数据,以便于得心应手地驾驭轧制过程。
主传动参数中有关的数据包括:电机容量、额定电流、最大允许电流、调速范围等。
第三节高速线材轧机自动检测自动化控制离不开自动检测。
所谓自动检测就是通过电的或机械的(物理或化学的)方法在无人工干预的情况下给出被测目标的信息,在高速线材轧制控制中,主要是给出轧线上轧件的位置信息。
自动检测由检测元件来完成。
用于高速线材轧机的检测元件一般有热金属检测器、活套扫描器、非接触式测温仪、工业电视等几种形式。
一、热金属检测器热金属检测器(又称光电管),是一种把轧件(红钢)放出的红外线用光学原理采集,并将它变换成电信号的装置,在轧钢生产中用于检测轧件的有无。
用于轧钢生产中的热金属检测器有两种:一种是固定式,它是由透镜、光电元件和电子处理单元组成。
工作原理是:具有一定温度的红钢将产生红外辐射。
当红钢进入检测器的视场范围时,由硅材料做成的红外光接受器在这种辐射作用下将改变本身的状态,且通过电子处理单元把这种变化信号变成逻辑电信号送往自动控制系统来检测轧件的有无。
这种检测器对检测温度有一定要求,高速线材厂所用的该种检测器要求的检测温度一般不得低于 600℃。
另一种是光电扫描型,它是由透镜、光电元件和同步电机带动的多面镜鼓以及晶体管放大器等部分构成。
工作原理是:利用旋转的多面镜鼓对视场进行扫描,并将轧件的影像经光电元件处理后,以电信号的形式输入自动控制系统。
这种检测器灵敏度高、视场广,但结构及保护装置较复杂。
二、活套扫描器活套扫描器是一种用于检测活套量大小的检测器,它是利用光电扫描脉冲相位比较原理来实现对活套量大小的检测。
三、非接触式辐射测温仪控制轧制温度是控制轧制的重要内容之一,为此有必要检测轧件温度。