当代高炉炼铁技术的发展趋向
中国高炉炼铁现状及未来技术展望
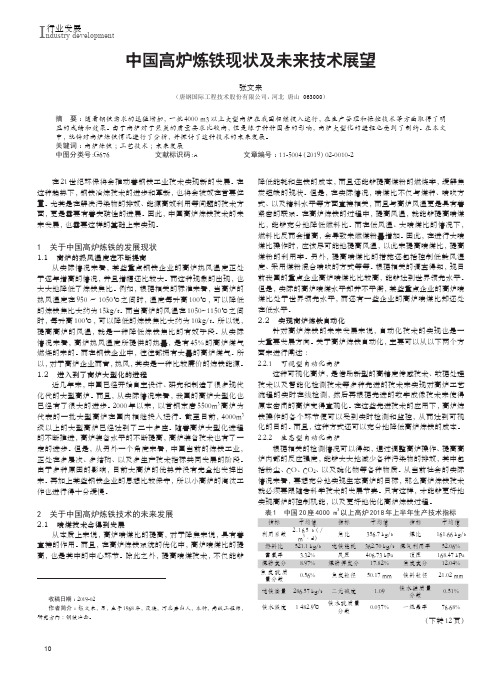
5 拜尔法处理三水软铝石的蒸发工艺 我国的铝土矿主要是一水硬铝石和一水软铝石,而三水软
铝石主要是进口的铝土矿,现在处理三水软铝石的氧化铝生产 企业主要集中在山东地区,由于交通便利山东地区的氧化铝生 产企业大量进口来自其他国家的三水软铝石生产氧化铝。三水 软铝石生产氧化铝工艺的特点是其铝酸钠溶液的浓度相对较 低,蒸发原液中的碱含量只有 110g/L~130g/L 左右,而蒸发母 液的碱含量在 160g/L~180g/L 之间。利用三水软铝石生产工艺 中铝酸钠溶液的蒸发技术同样可以利用六效管式降膜蒸发器 组加上强制循环排盐蒸发器形式。其中最常用的蒸发器机组的 蒸水能力在 240t/h~280t/h,蒸发机组的组成也与六效管式降 膜蒸发器一样,蒸发器组处理铝酸钠溶液碱浓度较低,汽水比 约在 0.19~0.2 左右。由于三水软铝石生产氧化铝工艺流程中的 铝酸钠溶液的浓度低可利用的温差范围更宽,所以除了可以采 用较普遍的六效管式降膜蒸发器外,还可以使用七效管式降膜 蒸发器。
近几年来,中国已经开始自主设计、研究和制造了很多现代 化代的大型高炉。而且,从实际情况来看,我国的高炉大型化也 已经有了很大的进步。2000 年以来,以首钢京唐 5500m3 高炉为 代表的一批大型高炉在国内相继投入运行。截至目前,4000m3 级以上的大型高炉已经达到了二十多座。随着高炉大型化进程 的不断推进,高炉装备水平的不断提高,高炉装备技术也有了一 定的进步。但是,从另外一个角度来看,中国当前的炼铁工业, 正处在多层次、多结构、以及多生产技术指标共同发展的阶段。 由于多种原因的影响,目前大高炉的优势并没有完全地发挥出 来。再加上某些钢铁企业的思想比较保守,所以小高炉的淘汰工 作也进行得十分缓慢。
中,就针对高炉炼铁情况进行了分析,并探讨了这种技术的未来发展。
高炉炼铁存在的问题及技术发展路径分析

高炉炼铁存在的问题及技术发展路径分析目录1 .高炉炼铁存在的问题 (1)2 .高炉炼铁技术发展路径展望 (2)1.高炉炼铁存在的问题1)要重视烧结矿强度,更要重视其冶金性能。
作为我国高炉的主要含铁原料一一烧结矿,其质量不仅仅包括强度、粒度、品位等宏观物理化学性能,更须要关注烧结矿在高炉冶炼过程中,所表现的高温物理化学性能即烧结矿的冶金性能,如还原性、软化熔融性能等。
2)要全面评价和考核块矿的性能,尤其是冶金性能。
目前块矿在使用过程中暴露出的主要问题包括:含粉率高,还原性及高温软化熔融性能不理想,热裂性能及检测不具备代表性,有害元素及含量超标等。
这些问题都对块矿的使用及高炉冶炼过程造成影响,块矿的性能评价体系有必要进一步完善。
3)原燃料市场价格畸变,更要重视焦炭质量。
煤与焦炭的价格上涨,导致部分企业为了降低成本不惜牺牲焦炭质量,造成炼铁技术经济指标下滑。
这种现象也足以说明焦炭质量对于高炉冶炼的重要性。
4)在高效长寿高炉方面。
高炉长寿技术是个系统工程,要采取综合技术措施。
我国高炉长寿发展很不均衡,平均寿命仅为5~10年,与国外高炉相比还存在较大差距。
近些年高炉炉缸侧壁温度异常升高甚至炉缸烧穿的案例明显增加,说明我国高炉炉缸长寿还存在着较大问题。
值得注意的是,2010年以来,随着高炉冶炼的强化,有些钢铁企业出现了铜冷却壁损坏的问题,值得进一步研究和改进。
5)在提高热风温度方面。
提高风温能有效降低焦比和燃料比、降低生产成本,是当前钢铁行业可持续发展、实现低碳冶炼的关键技术。
2016年钢协会员单位有36家企业热风温度下降,有27家企业热风温度提高。
目前尚有5家企业热风温度低于1100℃,距离比较理想的1280±20C高风温还有很长的路要走,须要继续推广高风温技术。
6)在降低燃料比、实现低碳炼铁方面。
一方面,我国中小高炉过度强化是其燃料比高的主要原因之一,客观分析,所谓小高炉效率高只是一种假象。
建议使用炉缸面积利用系数来评价高炉生产效率,这样有利于适当控制产能,避免盲目强化、盲目高产、盲目竞争,从而实现炼铁节能减排,降低燃料消耗,符合低碳、节能、环保的要求。
高炉炼铁产业发展趋势

高炉炼铁产业发展趋势高炉炼铁产业发展趋势近年来,随着中国经济的快速发展,高炉炼铁产业也得到了蓬勃的发展。
高炉炼铁是指通过高温将铁矿石还原为金属铁的一种工艺。
作为炼铁产业的核心环节,高炉炼铁在我国的工业生产中具有重要地位。
本文旨在对高炉炼铁产业的发展趋势进行探讨和分析,以期为该行业的发展提供参考。
一、发展历程与现状高炉炼铁技术起源于20世纪初,经过百年的发展,已成为当今炼铁产业的主流工艺。
在我国,高炉炼铁产业经历了起步阶段、扩张阶段和优化阶段三个发展阶段。
起步阶段(20世纪初至20世纪60年代):我国高炉炼铁产业在本阶段逐步建立起炼铁技术体系和生产基地。
20世纪初,我国开始引进和消化吸收国外的高炉炼铁技术。
到20世纪50年代,我国已具备自主研发高炉炼铁技术的能力,并开始大规模建设高炉。
到20世纪60年代,我国高炉炼铁产能稳步增长,但存在一些技术问题和设备落后的情况。
扩张阶段(20世纪70年代至21世纪初):我国高炉炼铁产业在本阶段实现了快速发展。
70年代初,我国高炉炼铁产能再次扩大,技术水平也有了一定的提高。
80年代初,我国高炉炼铁产能突破5000万吨,成为世界第一大炼铁国。
90年代至21世纪初,我国高炉炼铁产能进一步提升,技术水平逐步接近国际先进水平。
优化阶段(21世纪至今):我国高炉炼铁产业在本阶段实施了一系列的技术创新和产业升级。
21世纪初,我国高炉炼铁产量再次出现大幅增长,技术水平和设备质量也有了明显提高。
在优化阶段,我国高炉炼铁产业始终围绕提高效能、降低能耗、减少环境污染等方面进行升级改造。
现在,我国高炉炼铁技术已基本达到国际先进水平,生产效益和环保水平也有了明显提高。
二、发展趋势与问题1. 产量稳步增长:随着国内经济的持续发展和钢铁需求的增加,我国高炉炼铁产业的总体产能仍然保持稳步增长的态势。
根据统计数据,我国高炉炼铁产量在过去十年中基本保持在4亿吨以上。
未来,我国高炉炼铁产量仍有望继续增长,但增速可能会逐渐放缓。
面向未来的低碳绿色高炉炼铁技术的发展方向
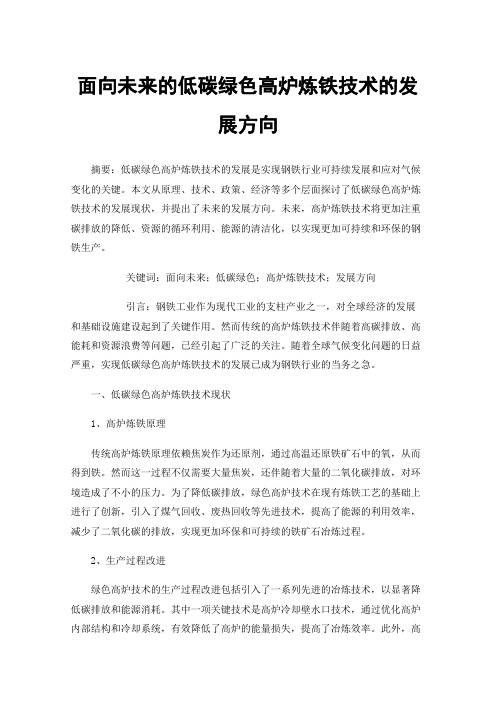
面向未来的低碳绿色高炉炼铁技术的发展方向摘要:低碳绿色高炉炼铁技术的发展是实现钢铁行业可持续发展和应对气候变化的关键。
本文从原理、技术、政策、经济等多个层面探讨了低碳绿色高炉炼铁技术的发展现状,并提出了未来的发展方向。
未来,高炉炼铁技术将更加注重碳排放的降低、资源的循环利用、能源的清洁化,以实现更加可持续和环保的钢铁生产。
关键词:面向未来;低碳绿色;高炉炼铁技术;发展方向引言:钢铁工业作为现代工业的支柱产业之一,对全球经济的发展和基础设施建设起到了关键作用。
然而传统的高炉炼铁技术伴随着高碳排放、高能耗和资源浪费等问题,已经引起了广泛的关注。
随着全球气候变化问题的日益严重,实现低碳绿色高炉炼铁技术的发展已成为钢铁行业的当务之急。
一、低碳绿色高炉炼铁技术现状1、高炉炼铁原理传统高炉炼铁原理依赖焦炭作为还原剂,通过高温还原铁矿石中的氧,从而得到铁。
然而这一过程不仅需要大量焦炭,还伴随着大量的二氧化碳排放,对环境造成了不小的压力。
为了降低碳排放,绿色高炉技术在现有炼铁工艺的基础上进行了创新,引入了煤气回收、废热回收等先进技术,提高了能源的利用效率,减少了二氧化碳的排放,实现更加环保和可持续的铁矿石冶炼过程。
2、生产过程改进绿色高炉技术的生产过程改进包括引入了一系列先进的冶炼技术,以显著降低碳排放和能源消耗。
其中一项关键技术是高炉冷却壁水口技术,通过优化高炉内部结构和冷却系统,有效降低了高炉的能量损失,提高了冶炼效率。
此外,高炉富氧燃烧技术也被广泛应用,通过增加炉内氧气供应,提高了还原反应效率,减少了废气中的二氧化碳排放。
这些生产过程改进措施在实践中已经取得了积极的成果,为绿色高炉技术的发展提供了坚实的基础。
3、废弃物资源化利用在绿色高炉技术中,废弃物资源化利用是一项重要的现状。
通过先进的废渣处理和回收技术,高炉产生的废渣得以充分利用。
废渣中的有用物质可以被回收,再次用于冶炼过程,降低了对新鲜原材料的需求,减少了资源浪费。
对炼铁技术发展方向的几点认识

对炼铁技术发展方向的几点认识摘要炼铁工艺已经形成高炉系统和非高炉系统两大系列。
高炉系统的技术发展方向是:①扩大资源的利用范围与水平;②进一步改进工艺,节能降耗;③余能余热的回收利用与环保。
非高炉系统重点谈谈粉矿熔融还原走向商业化需要改进的方向与方法设想。
关键词高炉资源工艺节能环保熔融还原炼铁技术经过数百年的研究开发,现已形成高炉炼铁系统和非高炉(熔融还原、直接还原)系统两烁列。
以下对它们的技术发展方向谈点初浅的认识埔批评指正。
l高炉炼铁系统高炉炼铁系统经过不断地研究改进,成绩斐然。
现今,为了进一步提高效益,技术发展方向有以下三个方面:1.1扩大资源经济合理利用的范围与水平在铁矿石中,褐铁矿的经济合理利用已取得很大进展,又出现了经济合理利用菱铁矿的开发研究。
含铁尘泥中对瓦斯泥和高炉干法除尘灰的利用也出现新的苗头,只要有害杂质不超标,如锌负荷利用后的综合负荷在200g/t以下,完全可以直接回收利用;在高风温、富氧条件下,还可与煤粉混合向高炉喷吹。
在煤炭中,有很多新技术既保证焦炭质量又扩大了炼焦配煤中弱粘结性煤种和非炼焦煤种的比例,回收废焦油等,做型煤粘结剂,合理利用也有新的进展。
近几年,我国在资源利用方面有很大进展,但与世界先进水平相比,总体上还有差距。
炼铁系统使用的资源是不可再生的,必须合理利用与回收再利用,所以对资源利用的研究,将是一个长期需要研究开发的课题。
1.2改进工艺技术,进一步节能降耗其一是降低炼铁的燃料比。
现在高炉降低燃料比还有多大潜力目前一般高炉的直接还原率为35%一40%,,比最低燃料比相适应的直接还原率高3%一10%左右,但最低燃料比的合适直接还原率不是定值,它随单位生铁的全部热量消耗与供热方式变化而变化。
一般每公斤生铁全部热量消耗每减少836kJ/kg,最低燃料比合适的直接还原率平均应高6%左右,每提高100℃风温应高1.5%左右。
本钢1958年12月~1959年3月,分析结果是每公斤生铁全部热消耗为12540kJ时,合适的直接还原率25%左右;而热量消耗降为10450kJ/kg时,合适直接还原率可升高到近35%。
中国现代高炉炼铁发展简介

中国现代高炉炼铁发展简介以中国现代高炉炼铁为视点,简介中国高炉炼铁目前的发展现状。
分析总结中国现代高炉技术的缺陷,挖掘中国现代高炉炼铁技术存在的问题。
结合目前高炉炼铁的行业形势,探究未来高炉炼铁趋势。
标签:现代高炉;高炉炼铁;发展趋势0 前言钢铁不论是在楼层建造还是在铁路建设中,都是不可缺少的一种重要资源。
对于钢铁的制造而言有着基本有两个流程,其中一项重要的流程生产生铁,高炉炼铁即是目前中国主要使用的炼铁工艺。
近些年,中国的高炉炼铁技术快速发展,不断向自动化、大型化、高效化前进,以低成本、低消耗、低污染为目标。
但相较于国外先进的高炉炼铁技术却有着一些阻碍中国高炉炼铁技术发展的不良因素。
1 中国高炉炼铁现状(1)高炉炼铁现状。
目前中国的高炉炼铁行业以近于饱和,尽管有着世界最高的产量,但不论是生产成本还是经济收益都差于世界水平,从而导致在世界市场的竞争力不足,对高炉炼铁的可持续发展铺满障碍。
其中先进的高炉炼铁厂与落后的高炉炼铁厂共存,并且中小型高炉过多,存在着不符合规定的高炉炼铁厂,在生产上无法做到低成本、低消耗、低污染,无视市场的饱和状态,最终导致供大于求,成品低廉。
由于这种不良的市场环境,使得中国的高炉炼铁在环保能源问题上存在缺陷。
而我国也作出了相应的对策:为化解过剩的产能,在2016年各种政策方案相继颁布,大力推进供给侧结构性改革,使钢铁价格稍有回升,不过并未能解决产量过剩这一问题,在经济收益上稍有改观,根本问题却依然存在。
(2)高炉炼铁技术指标。
由我国的行业标准规定大于4000m3高炉为大型高炉,而大型高炉生产率是小型高炉的数倍,所以我国的大型高炉为高炉炼铁技术起到了带动作用。
在其中大高炉的平均炉容约为4568.75m3,平均利用系数约为2.085t/(m3.d).大高炉的平均焦比与煤比分别为349.4kg/t、159.76kg/t,平均富氧率为3.36%。
由于中国目前的矿石品位较低,因此为保证大型高炉的稳定性,大多采用外国进口的原料,其中烧结矿、球团矿和块矿的比例为约为71.5%、19.7%、8.7%。
高炉炼铁的发展现状与展望

高炉炼铁的发展现状与展望高炉炼铁是一种重要的钢铁生产工艺,自19世纪初期发明以来,已有超过200年的历史。
高炉炼铁以铁矿石、焦炭和煤粉为原料,通过还原反应生成铁水,再经过凝固、锻造等工序制成钢铁产品。
本文将详细介绍高炉炼铁的发展现状、关键技术及未来展望。
全球市场规模随着全球经济的发展,钢铁行业的需求不断增加,高炉炼铁作为钢铁生产的主要方式,其市场规模也在不断扩大。
根据数据统计,2020年全球高炉炼铁产量超过15亿吨,预计到2025年,全球高炉炼铁产量将达到18亿吨。
市场前景在全球范围内,高炉炼铁的市场前景仍然广阔。
一方面,新兴市场国家的基础设施建设和工业化进程将带动钢铁需求的增长;另一方面,随着环保技术的不断进步,高炉炼铁的环保性能得到提升,有助于提高其在钢铁生产中的比重。
政策环境在全球范围内,各国政府普遍环境保护和能源消耗问题,因此,钢铁行业的政策环境也发生了变化。
许多国家政府对高炉炼铁的环保性能提出更高要求,鼓励发展清洁能源和循环经济。
在中国,政府提出了《中国制造2025》和《钢铁行业转型升级计划》,以推动高炉炼铁的节能减排和转型升级。
焦炭和煤粉焦炭和煤粉是高炉炼铁的主要原料,通过与铁矿石进行还原反应生成铁水。
焦炭和煤粉的品质和稳定性对高炉炼铁的生产效率和产品质量有重要影响。
目前,许多企业采用新型焦炭和煤粉制备技术,以提高原料的利用率和产品质量。
喷吹技术喷吹技术是一种将煤粉、焦炭等原料喷入高炉内的技术。
通过喷吹技术,可以增加高炉内的反应速度和还原程度,提高铁水产量和质量。
目前,许多企业采用先进的喷吹技术,如富氧喷吹、超高压喷吹等,以进一步提高生产效率。
环保技术随着环保意识的提高,许多企业在高炉炼铁过程中采用环保技术,如烟气脱硫、废弃物再利用等。
这些技术的应用可以减少高炉炼铁过程中的污染物排放,提高钢铁产品的环保性能。
鞍钢集团是中国最大的钢铁企业之一,也是高炉炼铁领域的领军企业。
近年来,鞍钢集团通过引进先进技术和设备,不断优化高炉炼铁工艺,提高生产效率和产品质量。
国内外高炉炼铁技术的发展现状和趋势

国内外高炉炼铁技术的发展现状和趋势
国内外高炉炼铁技术的发展现状和趋势
一、发展现状
1、国内
(1)钢铁厂炼铁技术的改造力度加大,已实现超低碳、超低强度、超低消耗的可持续发展。
(2)新型储能灶的兴起,使煤的消耗大大减少,同时也提高了炼铁设备的智能度。
(3)智能化技术的广泛应用,大大提升了传统炼铁技术的能源利用率。
2、国外
(1)德国、日本、西班牙等国在炼铁方面都有着非常成熟的技术,通过智能化技术的大量应用,以及不断提升设备抗磨损能力,使炼铁设备的性能得到持续提升。
(2)美国的炼铁技术也在不断发展,尤其是节能技术的提升,使温室气体排放量大幅减少,符合可持续发展的要求。
二、发展趋势
1、储能灶的广泛应用:储能灶的智能化技术可以大大减少给炉内喷射的煤,从而提高炼铁效率。
2、球化技术的提升:通过提高炉内样品的球化度,大大提升炼铁炉设备的耐板材性和智能度。
3、炼铁技术创新:不断创新和应用抗磨损、节能、轻量化、小型化等技术,提高设备的使用效率和产量。
4、炉前技术的完善:通过构建智能、优化的炉前技术,可以有效将煤、矿石等进料质量提高。
5、可持续发展:国内外高炉炼铁技术都趋向于节能、低碳、环境友好的可持续发展方向。
- 1、下载文档前请自行甄别文档内容的完整性,平台不提供额外的编辑、内容补充、找答案等附加服务。
- 2、"仅部分预览"的文档,不可在线预览部分如存在完整性等问题,可反馈申请退款(可完整预览的文档不适用该条件!)。
- 3、如文档侵犯您的权益,请联系客服反馈,我们会尽快为您处理(人工客服工作时间:9:00-18:30)。
-
3.未来高炉炼铁的发展目标
1. 燃料比≤500kg/t,先进高炉燃料比应≤480kg/t;入炉焦 比 应 ≤ 300kg/t , 先 进 高 炉 焦 比 应 ≤ 280kg/t ; 煤 比 ≥180kg/t,先进高炉煤比应达到200~250kg/t,喷煤率达 到45%~50%。
进入21世纪以来,高炉炼铁工艺再次受到自然资源短缺、 能源供给不足以及环境保护等方面的制约,面临着较大的发展 问题。面对当前严峻的形势和挑战,21世纪高炉炼铁工艺要实 现可持续发展,必须在高效低耗、节能减排、循环经济、低碳 冶金、清洁环保等方面取得显著突破,需要进一步提高风温、 降低燃料比,以提高高炉炼铁技术的生命力和竞争力。
利用低品质煤气 实现1250℃高风
温综合技术
提高理论燃烧温 度和拱顶温度
采用合理热风炉 结构,降低拱顶 温度与风温差值
采取有效措施, 抑制晶间应力腐 蚀和管道破损
4. 热 风 温 度 达 到 1200~1250℃ , 大 型 高 炉 风 温 应 达 到 1250~1300℃。
5. 高炉富氧率达到3%~5%,先进高炉富氧率应达到5%~10%。
二、高效长寿高风温技术
采用高效格子砖, 提高热量储备和
换热效率
高温热风的稳定 输送,构建“无 过热-低应力”
的管道体系
当代高炉炼铁技术的发展趋向
主要内容
一、当代高炉炼铁技术发展现状 二、高效长寿高风温技术 三、高富氧大喷煤技术 四、值得关注的几个技术问题 五、结论
一、当代高炉炼铁技术发展现状
1.当代高炉炼铁技术的发展环境
自然资源短缺 能源供给不足 生态环境制约
• 生产成本升高 • 经济效益下降 • 市场竞争力不足 • 可持续发展受阻
欧洲高炉主要技术指标的发展趋势
3.中国高炉炼铁技术发展现状
进入新世纪以来,我国高炉大型化和高炉现代化带动了高炉 炼铁技术进步。2000年2000m3以上的高炉仅有18座,到2010年 2000m3以上的高炉已发展到109座,其中3000m3以上的高炉为35 座,2000~3000m3高炉为74座。一批4000-5800m3的特大型高炉 相继建成投产,标志着中国高炉大型化已经步入国际先进行列。
2. 高炉有效容积利用系数达到2.0~2.3t/(m3•d),原燃料条 件好、技术装备水平高的大型高炉应达到2.5t/(m3•d)。
3. 高炉一代炉役寿命≥15a,高炉一代炉役单位容积产铁量应 达到10000~15000t/m3;技术装备水平高、原燃料条件好的 大型高炉,一代炉役寿命要力争达到20a以上,高炉单位容 积产铁量达到15000t/m3以上;热风炉寿命要大于或等于高 炉的一代炉役寿命。
2.日本、欧洲炼铁技术发展现状
20世纪70年代,以日本为代表的工业发达国家,相继建成了 一批容积5000m3以上的巨型高炉,引领了国际高炉炼铁大型化发 展的潮流。目前日本运行高炉的数量由1990年的65座减少到28座, 高炉数量降低了56.9%,高炉平均容积由1558m3提高到4157m3, 增长幅度达到166.8%,平均单炉产量达到350万t/a。
日本28座高炉平均燃料比已降低到500kg/t以下,煤比达到 120kg/t以上,焦比降低到380kg/t以下。
日本高炉主要技术指标的发展趋势
近20年来,欧洲在役高炉数量由1990年的92座减少到2009 年的58座,下降幅度为37%。但是高炉的平均工作容积由1690m3 ( 有 效 内 容 积 约 为 2150m3 ) 上 升 到 2063m3 ( 有 效 内 容 积 约为 2480m3),上升幅度为22%。
平均单座高炉产量由104万t/a增加到154万t/a,增长幅度 为48%。欧洲高炉燃料比降低到496kg/t,煤比达到123.9kg/t以 上,重油天然气为20.3kg/t,焦比降低到351.8kg/t。
以日本、欧洲为代表的国外高炉炼铁技术总体发展趋势是: 高炉座数减少,高炉平均容积增加,单座高炉产量增加,燃料 比呈现显著的下降趋势。
迁钢 3号 4000 1280 4.42 503 291 36 176 2.39 1205
宝钢 3号 4350 1236 3.94 491 288 18 185 2.50 974
宝钢 4号 4747 1254 1.16 488 292 26 170 2.02 1035
武钢 8号 3800 1192 6.47 532 322 33 177 2.69 1082
高炉
高炉有效容积/m3 平均风温/℃ 富氧率/% 燃料比/(kg·t-1) 入炉焦比/(kg·t-1) 焦丁/(kg·t-1) 煤比/(kg·t-1) 利用系数/(t·m-3·d-1) 吨铁风耗/(m3·t-1)
京唐1号 2010-3 5500 1300
3.81 480 269 36 175 2.37 917
构建高效率、低消耗、低成本、低排放生产体系
可持续发展 支撑技术
提高风温 精料技术 低碳冶炼 富氧喷煤 延长寿命 优化操作
高效低耗 节能减排 循环经济 ห้องสมุดไป่ตู้碳冶炼 清洁环保 安全长寿
• 生产成本约占钢铁制造成本的70%-75% • 能源消耗约占钢铁综合能耗的70% • 高炉是钢铁制造流程中关键生产工序 • 铁素物质流转换的关键单元 • 能源转换和能量流网络的核心单元
目前,我国重点钢铁企业的高炉燃料比已降低到520kg/t以 下,焦比降低到370kg/t,煤比达到150kg/t以上,炼铁工序能耗 降低到410kgce/t以下,热风温度达到1160℃。2005年以后,随 着我国1080m3以上大型高炉数量的快速增加,高炉燃料比和入炉 焦比等指标显著降低。
中国部分先进大高炉主要技术经济指标(2011年1-6月)
沙钢 5800m3
5800 1230 9.47 502 293
48 161 2.21 855
太钢 5号 4350 1243 4.97 502 305 10 187 2.50
-
马钢 1号 4000 1225 3.63 514 302 36 140 2.22 1065
鲅鱼 圈1号 4038 1225 2.93