DFMEA(09P1601Y-R1)-改善前
DFMEA工具培训学习课件
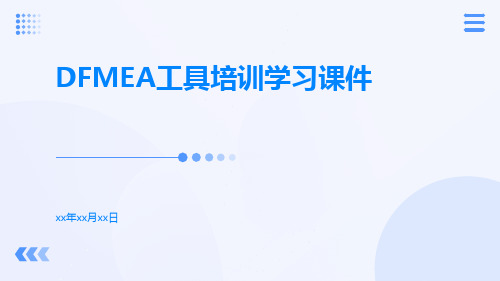
人工智能技术
人工智能技术的不断发展,为DFMEA工具带来更多创新可能 ,如机器学习和深度学习等技术将被广泛应用于缺陷分析、 风险评估等领域。
大数据技术
大数据技术的不断发展,为DFMEA工具带来更高效的数据处 理和分析能力,有助于更准确地进行缺陷预测和风险评估。
DFMEA工具的应用前景
汽车行业
DFMEA工具将继续在汽车行业中得到广泛应用,进一步降低汽车产品的缺陷 率和提高产品质量。
其他行业
除了汽车行业,DFMEA工具也将不断拓展到其他行业中,如电子产品、机械 设备等领域,为更多行业提供质量保障支持。
06
总结与回顾
本次培训的主要内容回顾
DFMEA工具的概念 和原理
DFMEA是一种以故障模式与影 响分析(FMEA)为基础的质量 工具,用于在产品设计过程中识 别和解决潜在的设计问题。
电子行业DFMEA应用 案例
某电子制造企业在生产过程中遇到了 一个严重的质量问题,导致产品批量 报废。通过应用DFMEA工具,企业 发现故障原因为原材料质量不过关, 及时更换供应商并采取其他质量控制 措施,避免了类似事件的再次发生。
04
DFMEA工具的进阶技巧
如何提高DFMEA工具的效率
01
熟练掌握快捷键
03
DFMEA工具的应用案例
DFMEA工具在汽车行业的应用
汽车行业应用背景
随着汽车行业的不断发展,产品复杂度不断提高,市场竞争日益激烈。应用DFMEA工具 可以帮助汽车制造企业更好地分析产品设计、生产和制造过程中潜在的风险,提高产品质 量和安全性。
DFMEA在汽车行业的应用流程
DFMEA工具在汽车行业的应用主要包括以下步骤:制定项目计划、收集相关数据和信息 、进行故障模式分析、建立故障影响矩阵、制定改进措施、跟踪和监督实施情况等。
(DFMEA)汽车行业设计失效模式分析
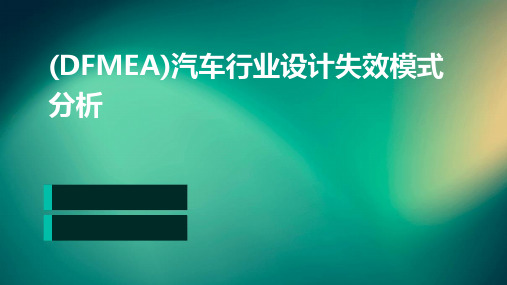
性能下降
随着使用时间的增加,发动机性能可能会逐渐下 降,导致汽车动力不足、加速缓慢等问题。这可 能是由于发动机内部零件磨损、燃油系统堵塞或 点火系统故障等原因引起的。
振动过大
发动机振动过大可能会对车辆的舒适性和稳定性 产生不良影响,同时也会增加零部件的磨损和疲 劳破坏。振动过大的原因可能包括发动机平衡性 差、零部件松动或损坏等。
不断更新表格,以反 映产品设计的更改和 改进。
确保表格内容完整、 准确,为后续分析提 供基础数据。
绘制设计流程图
01 详细绘制产品设计的流程图,包括各个组件的相 互关系和作用。
02 明确各个设计阶段的输入和输出,以便更好地理 解设计的整体流程。
03 分析流程图,找出可能存在的设计缺陷和失效模 式。
优化方法
采用先进的优化算法和仿真技术,对设计方案进行多目标优化。
优化过程
充分考虑制造工艺、材料特性等因素,确保优化方案的可行性。
提高制造质量
制造工艺
采用先进的制造工艺,提高零部件和整车的制造 精度和质量。
质量控制
建立严格的质量控制体系,确保每个环节的制造 质量符合要求。
质量检测
采用多种质量检测手段,如无损检测、功能检测 等,确保产品合格率。
03
基于影响评估,为每个故障模式制定相应的改进措施
和优先级。
03 汽车行业中的设计失效模 式
发动机系统
总结词
发动机系统是汽车的核心部分,其设计失效模式 主要表现在性能下降、过热、振动过大等方面。
过热
发动机过热是常见的失效模式之一,可能导致拉 缸、润滑油变质等严重后果。过热的原因可能包 括冷却系统故障、发动机负荷过大、散热器堵塞 等。
传动系统
DFMEA标准教材PPT课件

9
DFMEA实施
团队方法:DFMEA是由一个多方论证(跨职能)的小组来开 发和维护的。小组通常由负责设计的工程师领导。
设计及制造等相关工作人员
ห้องสมุดไป่ตู้
团队要求
- 经验/过去问题处理积累的知识,转变为公司的无形资产;
- 有效的团队管理;
- 对所有活动的结果文件化;
多方参与应用DFMEA,有助于理清产品和过程分析、评审的 思路
2020年3月29日
1
课程目的
掌握DFMEA的概念 和运用时机
发现、评价产品设计中 潜在的失效及其后果
找到能够避免或减少这 些潜在失效发生的措施
2020年3月29日
将上述过程总结形成文 件
2
DFMEA
Design Potential Failure Model And Effect Analysis
DFMEA应用的主要行业 -- 航空业 ——复杂的体系,产品和过程, 小批量生产 -- 汽车业——复杂的体系,产品和过程, 大批量生产 -- 其它行业
2020年3月29日
3
DFMEA发展简史
• 正式使用DFMEA技术是美国六十年代的 阿波罗登月计划。
能否预测人类第一次登月会出现 的后果以及提前采取对策。
有效运用 DFMEA 可减少事后追悔
2020年3月29日
7
DFMEA介绍
• 及时性是成功实施DFMEA的最重要因素之一。 • 它是“事前的预防”而不是“事后的追悔”。 • 事先花时间进行DFMEA分析,能够容易且低成本地对产
品设计或制程进行修改,从而减轻事后修改的危机。 • DFMEA能够减少或消除因修改而带来更大损失的机会,
30
常用的一种DFMEA结构
汽车空调系统设计DFMEA案例分析

汽车空调系统设计DFMEA案例分析DFMEA简介DFMEA(Design Failure Mode and Effects Analysis,设计失效模式与影响分析)是一种常用的质量管理工具,用于在产品设计阶段识别并解决潜在的失效模式及其影响。
本文将以汽车空调系统设计为案例,探讨如何应用DFMEA来提高汽车空调系统设计的安全性和可靠性。
一、设计失效模式与影响分析(DFMEA)DFMEA是一种以系统化和有序方式对产品设计进行评估和分析的方法。
它的主要目的是识别可能的失效模式、评估其严重程度以及制定相应的纠正和预防措施。
下面我们将根据DFMEA的步骤,对汽车空调系统进行案例分析。
1. 制定DFMEA团队与范围首先,确定参与DFMEA的团队成员,包括汽车空调系统设计的工程师、质量控制专家、测试工程师等。
明确DFMEA的范围和目标,以汽车空调系统各个子系统为分析对象。
2. 识别失效模式对汽车空调系统设计进行全面的分析,列举可能的失效模式。
比如,制冷剂泄漏、温度控制失效、空调系统过热等。
3. 确定失效模式的可能原因针对每个失效模式,分析其潜在的原因,如设计不当、材料选择不当、制造工艺缺陷等。
以制冷剂泄漏为例,可能的原因包括密封件老化、接口松动等。
4. 评估失效的严重程度对每个失效模式进行严重程度评估,考虑其对汽车空调系统性能、安全性和可靠性的影响。
以温度控制失效为例,可能导致车内温度无法调节,对车内乘客的舒适度产生较大影响。
5. 确定控制措施针对每个失效模式确定相应的预防和纠正措施,以减少失效概率和降低失效的严重程度。
比如,在设计阶段增加密封件的检测和更换计划,严格控制安装过程中的接口紧固力矩。
6. 跟踪执行和评估效果实施控制措施后,跟踪其执行情况,并对效果进行评估。
通过实际数据的反馈,不断优化和改善汽车空调系统的设计。
二、汽车空调系统DFMEA案例分析以下是针对汽车空调系统的DFMEA案例分析,以帮助读者更好地理解DFMEA方法的应用。
9条必读的DFMEA实践经验

9条必读的DFMEA实践经验
众所周知,DFMEA(Design Failure Mode and Effects Analysis)是一种用于评估设计过程中潜在失效模式及其对产品性能和可靠性的影响的方法。
本文,深圳天行健六西格玛咨询公司着重讲述进行DFMEA时需要注意的9条实践经验。
1. 确定评估的范围和目的
在开始DFMEA之前,需要明确评估的范围和目的,以确保团队的工作有针对性和有效性。
2. 组建跨职能团队
DFMEA需要涵盖多个领域的知识和专业背景,因此组建一个跨职能团队是必要的,以确保全面的评估和分析。
3. 收集和整理产品信息
收集和整理与产品相关的信息,包括设计规范、功能要求、
制造过程、材料特性等。
这些信息将有助于识别潜在的失效模式。
4. 识别潜在失效模式
通过团队的讨论和分析,识别出可能导致产品失效的潜在模式。
5. 评估失效的严重性
对于每个潜在的失效模式,评估其对产品性能和可靠性的影响程度,并分配相应的严重性等级。
6. 分析失效的原因
确定导致每个失效模式的根本原因,以便采取相应的改进措施。
7. 确定预防和控制措施
针对每个失效模式,确定预防和控制措施,以减轻其对产品
的影响或防止其发生。
8. 实施措施并跟踪效果
将预防和控制措施纳入产品的设计和制造过程中,并跟踪其实施效果,确保其有效性。
9. 定期复审和更新
定期对已实施的DFMEA进行复审和更新,以确保其与产品的演进和变化保持一致。
以上是进行DFMEA时需要注意的9条实践经验。
通过遵循这些经验,可以帮助企业提前预防和控制潜在的失效模式,提高产品的可靠性和性能。
dfmea案例
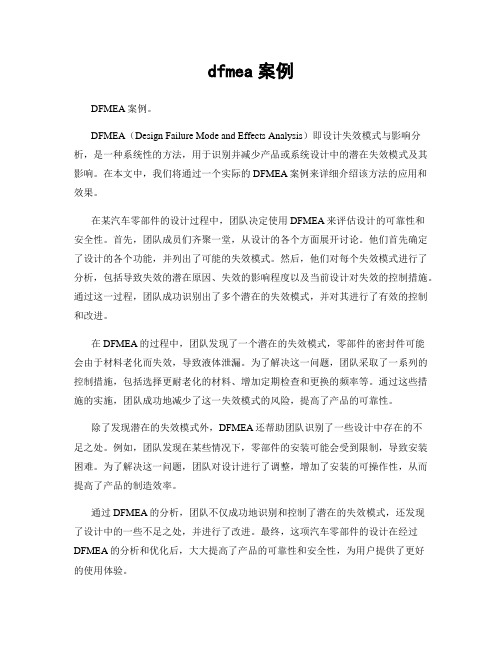
dfmea案例DFMEA案例。
DFMEA(Design Failure Mode and Effects Analysis)即设计失效模式与影响分析,是一种系统性的方法,用于识别并减少产品或系统设计中的潜在失效模式及其影响。
在本文中,我们将通过一个实际的DFMEA案例来详细介绍该方法的应用和效果。
在某汽车零部件的设计过程中,团队决定使用DFMEA来评估设计的可靠性和安全性。
首先,团队成员们齐聚一堂,从设计的各个方面展开讨论。
他们首先确定了设计的各个功能,并列出了可能的失效模式。
然后,他们对每个失效模式进行了分析,包括导致失效的潜在原因、失效的影响程度以及当前设计对失效的控制措施。
通过这一过程,团队成功识别出了多个潜在的失效模式,并对其进行了有效的控制和改进。
在DFMEA的过程中,团队发现了一个潜在的失效模式,零部件的密封件可能会由于材料老化而失效,导致液体泄漏。
为了解决这一问题,团队采取了一系列的控制措施,包括选择更耐老化的材料、增加定期检查和更换的频率等。
通过这些措施的实施,团队成功地减少了这一失效模式的风险,提高了产品的可靠性。
除了发现潜在的失效模式外,DFMEA还帮助团队识别了一些设计中存在的不足之处。
例如,团队发现在某些情况下,零部件的安装可能会受到限制,导致安装困难。
为了解决这一问题,团队对设计进行了调整,增加了安装的可操作性,从而提高了产品的制造效率。
通过DFMEA的分析,团队不仅成功地识别和控制了潜在的失效模式,还发现了设计中的一些不足之处,并进行了改进。
最终,这项汽车零部件的设计在经过DFMEA的分析和优化后,大大提高了产品的可靠性和安全性,为用户提供了更好的使用体验。
综上所述,DFMEA作为一种系统性的方法,能够帮助团队全面地识别并减少产品或系统设计中的潜在失效模式及其影响。
通过对失效模式的分析和控制,团队不仅可以提高产品的可靠性和安全性,还能够发现设计中的不足之处,并进行相应的改进。
DFMA产品设计生产改善检查表范例

试模
工程试装最后工程办
试产
生产开
始
A 01 刮花A 02漏油A 03批伤A 04顶白A 05盲孔A 06水口披锋A 07缩水A 08熔接痕A 09夹水纹A 10缺胶A 11烧焦
A 12裂开A 13发白
A 14烫日期印深浅不均匀A 15变形A 16杂色A 17开位A 18超声溢胶A 19铁轴波花外露A 21电池箱无字唛标识A 22错位A 23彩盒有凸起
A 24光洁度 (工模表面处理)
B 01打胶水B 02打润滑油B 03电线贴胶纸固定
B 04打黄胶B 05批披锋B 06剪电线B 07剪锡点
B 08剪短橡胶按制脚
C 01拉长(矫正)弹弓
C 02剪弹弓C 03剪铁轴C 04切胶
C 05裁内卡C 06钻孔
C 07加PVC介子增高柱位
C
加工工序
辅助工序
外观
A
加工工序
C
B
项目
违反条例
违反事项
文字描述
备注
编号
工程试
装最后工
程办
试产
生产开
始
项目违反
条例
违反事项文字描述备注编
号
试模
工程试
装最后工
程办
试产
生产开
始
项目违反
条例
违反事项文字描述备注编
号
试模
试模工程试
装
最后工
程办
试产
生产开
始
项目违反
条例
违反事项文字描述备注编
号
人:审核:
准:
QAE工程师。
DFMEA失效模式分析报告-范例
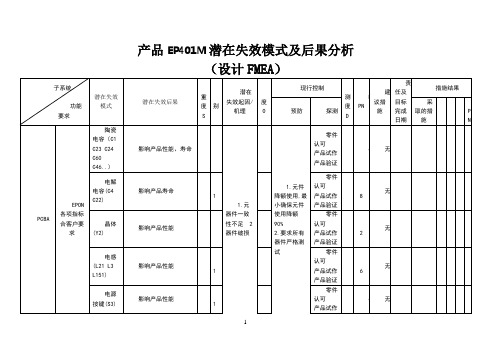
子系统
潜在失效模式
潜在失效后果
严重度 S
级别
潜在失效ቤተ መጻሕፍቲ ባይዱ因/机理
频度O
现行控制
探测度D
RPN
建议措施
责任及目标完成日期
措施结果
功能要求
预防
探测
采取的措施
S
O
D
RPN
PCBA
EPON各项指标合客户要求
陶瓷电容(C1 C23 C24 C60 C46..)
影响产品性能、寿命
1
1
1.元器件一致性不足2器件破损
2
1.元件降额使用,最小确保元件使用降额90% 2.要求所有器件严格测试
零件认可 产品试作 产品验证
3
6
无
电解电容(C4 C22)
影响产品寿命
3
1
2
零件认可 产品试作 产品验证
3
18
无
晶体(Y2)
影响产品性能
3
1
2
零件认可 产品试作 产品验证
2
12
18
无
PCBA
EPON各项指标合客户要求
FLASH(U30)
影响产品性能
2
1
1.元器件一致性不足 2.器件破损
2
1.元件降额使用,最小确保元件使用降额90% 2.要求所有器件严格测试
零件认可 产品试作 产品验证
3
12
无
DDR(U400)
影响产品性能
2
1
2
零件认可 产品试作 产品验证
2
8
无
网口接口(J2)
影响产品组装
2
- 1、下载文档前请自行甄别文档内容的完整性,平台不提供额外的编辑、内容补充、找答案等附加服务。
- 2、"仅部分预览"的文档,不可在线预览部分如存在完整性等问题,可反馈申请退款(可完整预览的文档不适用该条件!)。
- 3、如文档侵犯您的权益,请联系客服反馈,我们会尽快为您处理(人工客服工作时间:9:00-18:30)。
编制: 钟吉军 日期:2009-7-10 制程名稱:Process Name:09P1601Y-R1 制程名稱 FMEA 小組成員 小組成員Team member: RoHS专案 专案 孙咏朝 刘利胜 品质部 陈跃、陈战兵 生产部 物控 检测 采购 工艺质量室 李爱民 谭青青、范溅彬、尹亮 刘丽 邹峰 評分依據Ranking Guidelines: 評分依據 嚴重度: 嚴重度 (Severity of failure effect) 發生率: 發生率 (Occurrence of failure cause) 難檢度: 難檢度 (Detection of failure cause) 風險優先數 (RPN) = Risk Priority Number (RPN) 审核: 日期: 批准: 日期:
發生率
(O)Occurrence of cause
現行控制措施
Current Process Control(s)
難檢度
(D)Detection of cause (S*O*D)
建議控制措施
Recommended Action(s)
責任人
Responsible Person
完成日期
Completion Date
保护膜位置不对
影响装配
10
机器调位不对
2
机器调位,增加检验
1
20
来料控制、调位控制、培训
范贱彬
15-05-09
包装
脏污、划伤
影响镜片外观效果
4
员工操作失误
4
生产前进行培训
3
48
生产前培训,加强检验力度
谭青青
15-05-09
HV-WI/EN-023 R0 2009-7-10
BYD料號 料號H.W.P/N: ABBA Main Window 料號
制程負責人Process responsible:邹峰 制程負責人 邹峰 DFMEA負責人 負責人FMEA Responsible:钟吉军 負責人 钟吉军 品工Quality Engineer:刘利胜 品工 刘利胜
文件編號(Worksheet Document No): 文件編號 1 = 幾乎無影響 (1=Minor/No effect) 1 = 幾乎不可能 (1=Remote/Unlikely) 1 = 幾乎可檢出 (1=Very high/Almost certainly) 嚴重度 * 發生率 * 難檢度 (Severity * Occurrence * Detection) RPN 10 = 极具危險性 (10=Very high/Hazardous) 10 =幾乎不可避免 (10=Very high/Almost inevitable) 10 = 幾乎不可能檢查出來 (10=Very low/Unlikely) 版次REV: 版次 制訂日期Date (Orig.): 制訂日期 變更日期Date (Rev.): 變更日期 頁碼Page: 1/1 頁碼
狀態 Status 已採取之措施
Action Taken [S] [O] [D] RPN
来料
来料板材中有隐性划伤
影响外观效果
1
材料来料不良
5
IQC提高AQL抽检等级
5
25
与供应商沟通,要求改善
刘丽
17-05-09
开料
开料中有白点
影响成品率
2
开料中机器斩切时有压伤白点
4
清洁斩切台面,脏污
2
16
保持机台清洁度贺礼ຫໍສະໝຸດ 17-05-09印刷
有尘点
影响镜片外观效果
5
环境造成尘点
3
标准检验
5
75
增强净化度,过除尘机
刘科
20-05-09
印刷
板材变形
影响镜片外观效果
1
工艺指标执行不到位
1
工艺检验
1
1
检验烘箱,定义烘烤温度
康佳琳
15-05-09
覆膜
材料划伤
影响镜片外观效果
2
覆膜机有脏污
5
清洁覆膜机
10
100
定期清洁覆膜机
1
改善后 Action Results
過程描述
PROCESS Descripti on
預估失效模式
Potential Failure Mode
預估失效影響
Potential Effect(s) of Failure
嚴重度
(S)Severity of effect
預估失效原因
Potential Cause(s) of Failure
康佳琳
15-05-09
钻切割定位 孔
表面划伤
影响镜片外观效果
4
钻孔有碎硝
2
更换刀具,加快速度
5
40
加强检验
贺礼
15-05-09
切割
外形尺寸超差
影响装配
1
机床精度不够
1
增加机器保养
1
1
加强抽检
贺礼
15-05-09
撕膜
产品刮伤
影响镜片外观效果
10
员工操作失误
2
员工掊训
1
20
定期培训
贺礼
15-05-09
包装