On measuring fracture toughness under load control in the presence of slow crack growth
仪器压痕法断裂韧性检测方法
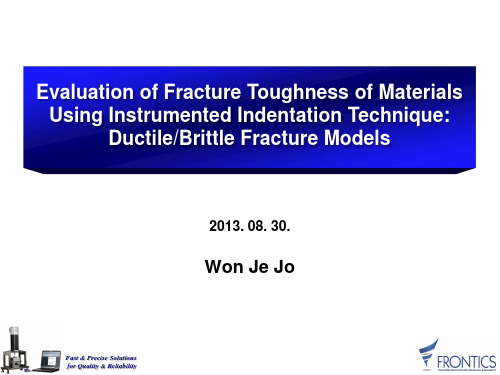
h*
0
L dh Ac
17
K JC
wf E (1 2 )
Fast & Precise Solutions for Quality & Reliability
Hertzelasticcontact th eory
Expandingcavitymodel(elastic- plastic theory)
Fast & Precise Solutions for Quality & Reliability
13
Hertz elastic contact theory
0
Indentation depth (m)
- Inserting determined Pmc into Pm-h curve
(5) Equivalent fracture energy until h*
(6) Indentation fracture toughness (KJC)
wf
1 0 0.0
2.1
0.1 0.2 0.3 0.4 0.5 0.6
3.2
V / Vmax
hmax / R
Triaxiality of crack tip Triaxiality of indentation
Fast & Precise Solutions for Quality & Reliability
sr
1 2 p
2
m
By Von Mises’ yield criterion
y pm C1 s ys
Fast & Precise Solutions for Quality & Reliability
焊接专业英语词汇(焊接及相关工艺英文缩写)
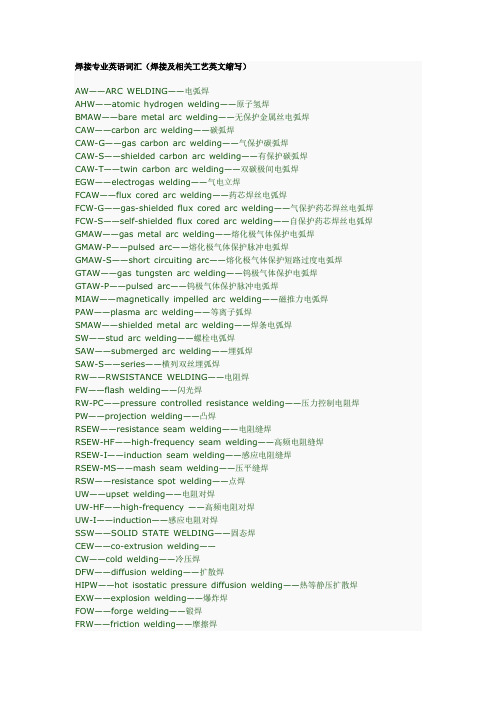
焊接专业英语词汇(焊接及相关工艺英文缩写)AW——ARC WELDING——电弧焊AHW——atomic hydrogen welding——原子氢焊BMAW——bare metal arc welding——无保护金属丝电弧焊CAW——carbon arc welding——碳弧焊CAW-G——gas carbon arc welding——气保护碳弧焊CAW-S——shielded carbon arc welding——有保护碳弧焊CAW-T——twin carbon arc welding——双碳极间电弧焊EGW——electrogas welding——气电立焊FCAW——flux cored arc welding——药芯焊丝电弧焊FCW-G——gas-shielded flux cored arc welding——气保护药芯焊丝电弧焊FCW-S——self-shielded flux cored arc welding——自保护药芯焊丝电弧焊GMAW——gas metal arc welding——熔化极气体保护电弧焊GMAW-P——pulsed arc——熔化极气体保护脉冲电弧焊GMAW-S——short circuiting arc——熔化极气体保护短路过度电弧焊GTAW——gas tungsten arc welding——钨极气体保护电弧焊GTAW-P——pulsed arc——钨极气体保护脉冲电弧焊MIAW——magnetically impelled arc welding——磁推力电弧焊PAW——plasma arc welding——等离子弧焊SMAW——shielded metal arc welding——焊条电弧焊SW——stud arc welding——螺栓电弧焊SAW——submerged arc welding——埋弧焊SAW-S——series——横列双丝埋弧焊RW——RWSISTANCE WELDING——电阻焊FW——flash welding——闪光焊RW-PC——pressure controlled resistance welding——压力控制电阻焊PW——projection welding——凸焊RSEW——resistance seam welding——电阻缝焊RSEW-HF——high-frequency seam welding——高频电阻缝焊RSEW-I——induction seam welding——感应电阻缝焊RSEW-MS——mash seam welding——压平缝焊RSW——resistance spot welding——点焊UW——upset welding——电阻对焊UW-HF——high-frequency ——高频电阻对焊UW-I——induction——感应电阻对焊SSW——SOLID STATE WELDING——固态焊CEW——co-extrusion welding——CW——cold welding——冷压焊DFW——diffusion welding——扩散焊HIPW——hot isostatic pressure diffusion welding——热等静压扩散焊EXW——explosion welding——爆炸焊FOW——forge welding——锻焊FRW——friction welding——摩擦焊FRW-DD——direct drive friction welding——径向摩擦焊FSW——friction stir welding——搅拌摩擦焊FRW-I——inertia friction welding——惯性摩擦焊HPW——hot pressure welding——热压焊ROW——roll welding——热轧焊USW——ultrasonic welding——超声波焊S——SOLDERING——软钎焊DS——dip soldering——浸沾钎焊FS——furnace soldering——炉中钎焊IS——induction soldering——感应钎焊IRS——infrared soldering——红外钎焊INS——iron soldering——烙铁钎焊RS——resistance soldering——电阻钎焊TS——torch soldering——火焰钎焊UUS——ultrasonic soldering——超声波钎焊WS——wave soldering——波峰钎焊B——BRAZING——软钎焊BB——block brazing——块钎焊DFB——diffusion brazing——扩散焊DB——dip brazing——浸沾钎焊EXB——exothermic brazing——反应钎焊FB——furnace brazing——炉中钎焊IB——induction brazing——感应钎焊IRB——infrared brazing——红外钎焊RB——resistance brazing——电阻钎焊TB——torch brazing——火焰钎焊TCAB——twin carbon arc brazing——双碳弧钎焊OFW——OXYFUEL GAS WELDING——气焊AAW——air-acetylene welding——空气乙炔焊OAW——oxy-acetylene welding——氧乙炔焊OHW——oxy-hydrogen welding——氢氧焊PGW——pressure gas welding——气压焊OTHER WELDING AND JOINING——其他焊接与连接方法AB——adhesive bonding——粘接BW——braze welding——钎接焊ABW——arc braze welding——电弧钎焊CABW——carbon arc braze welding——碳弧钎焊EBBW——electron beam braze welding——电子束钎焊EXBW——exothermic braze welding——热反应钎焊FLB——flow brazing——波峰钎焊FLOW——flow welding——波峰焊LBBW——laser beam braze welding——激光钎焊EBW——electron beam welding——电子束焊EBW-HV——high vacuum——高真空电子束焊EBW-MV——medium vacuum——中真空电子束焊EBW-NV——non vacuum——非真空电子束焊ESW——electroslag welding——电渣焊ESW-CG——consumable guide eletroslag welding——熔嘴电渣焊IW——induction welding——感应焊LBW——laser beam welding——激光焊PEW——percussion welding——冲击电阻焊TW——thermit welding——热剂焊THSP——THERMAL SPRAYING——热喷涂ASP——arc spraying——电弧喷涂FLSP——flame spraying——火焰喷涂FLSP-W——wire flame spraying——丝材火焰喷涂HVOF——high velocity oxyfuel spraying——高速氧燃气喷涂PSP——plasma spraying——等离子喷涂VPSP-W——vacuum plasma spraying——真空等离子喷涂TC——THERMAL CUTTING——热切割OC——OXYGEN CUTTING——气割OC-F——flux cutting——熔剂切割OC-P——metal powder cutting——金属熔剂切割OFC——oxyfuel gas cutting——氧燃气切割CFC-A——oxyacetylene cutting——氧乙炔切割CFC-H——oxyhydrogen cutting——氢氧切割CFC-N——oxynatural gas cutting——氧天然气切割CFC-P——oxypropanne cutting——氧丙酮切割OAC——oxygen arc cutting——氧气电弧切割OG——oxygen gouging——气刨OLC——oxygen lance cutting——氧矛切割AC——ARC CUTTING——电弧切割CAC——carbon arc cutting——碳弧切割CAC-A——air carbon arc cutting——空气碳弧切割GMAC——gas metal arc cutting——熔化极气体保护电弧切割GTAC——gas tungsten arc cutting——钨极气体保护电弧切割PAC——plasma arc cutting——等离子弧切割SMAC——shielded metal arc cutting——焊条电弧切割HIGH ENERGY BEAM CUTTING——高能束切割EBC——electron beam cutting——电子束切割LBC——laser beam cutting——激光切割LBC-A——air——空气激光切割LBC-EV——evaporative——蒸气激光切割LBC-IG——inert gas——惰性气体激光切割LBC-O——oxygen——氧气激光切割激光切割laser cutting(LC); laser beam cutting电子束切割electron beam cutting喷气激光切割gas jet laser cutting碳弧切割carbon arc cutting水下切割underwater cutting喷水式水下电弧切割waterjet method underwater arc cutting氧矛切割oxygen lancing; oxygen lance cutting溶剂氧切割powder lancing手工气割manual oxygen cutting自动气割automatic oxygen cutting仿形切割shape cutting数控切割NC (numerical-control) cutting快速切割high-speed cutting垂直切割square cut叠板切割stack cutting坡口切割beveling; bevel cutting碳弧气割carbon arc air gouging火焰气刨flame gouging火焰表面清理scarfing氧熔剂表面修整powder washing预热火焰preheat flame预热氧preheat oxygen切割氧cutting oxygen/ cutting stream切割速度cutting speed切割线line of cut/ cut line切割面face of cut/ cut face切口kerf切口上缘cutting shoulder切口宽度kerf width后拖量drag切割面平面度evenness of cutting surface/ planeness of cutting surface 割纹深度depth of cutting veins/ stria depth切割面质量quality of cut face上缘熔化度shoulder meltability/ melting degree of shoulder切口角kerf angle缺口notch挂渣adhering slag结瘤dross割炬cutting torch/ cutting blowpipe/ oxygen-fuel gas cutting torch割枪cutting gun割嘴cutting nozzle/ cutting tip快速割嘴divergent nozzle/ high-speed nozzle表面割炬gouging blowpipe水下割炬under-water cutting blowpipe水下割条electrode for under-water cutting粉剂罐powder dispenser数控切割机NC cutting machine门式切割机flame planer光电跟踪切割机photo-electric tracing cutting火焰切管机pipe flame cutting machine磁轮式气割机gas cutting machine with magnetic wheels 焊接结构welded structure/ welded construction焊件weldment焊接部件weld assembly组装件built-up member接头设计joint design焊接应力welding stress焊接瞬时应力transient welding stress焊接残余应力welding residual stress热应力thermal stress收缩应力contraction stress局部应力local stress拘束应力constraint stress固有应力inherent stress固有应变区inherent strain zone残余应力测定residual stress analysis逐层切割法Sach’s methodX射线衍射法X-ray stress analysis小孔释放法Mathar method固有应变法inherent strain method消除应力stress relieving局部消除应力local stress relieving应力重分布stress redistribution退火消除应力stress relieving by annealing温差拉伸消除应力low temperature stress relieving机械拉伸消除应力mechanical stress relieving应力松弛stress relaxation焊接变形welding deformation焊接残余变形welding residual deformation局部变形local deformation角变形angular distortion自由变形free deformation收缩变形contraction deformation错边变形mismatching deformation挠曲变形deflection deformation波浪变形wave-like deformation火焰矫正flame straightening反变形backward deformation焊接力学welding mechanics断裂力学fracture mechanics弹塑性断裂变形elasto-plastic fracture mechanics线弹性断裂力学linear elastic fracture mechanics延性断裂ductile fracture脆性断裂brittle fracture应力腐蚀开裂stress corrosion cracking热应变脆化hot straining embrittlement临界裂纹尺寸critical crack size裂纹扩展速率crack propagation rate裂纹张开位移(COD)crack opening displacement拘束度restraint intensity拘束系数restraint coefficient应变速率strain rate断裂韧度fracture toughness应力强度因子stress intensity factor临界应力强度因子critical stress intensity factors应力腐蚀临界应力强度因子critical stress intensity factor of stress corrosion cracking J积分J-integration罗伯逊止裂试验Robertson crack arrest testESSO试验ESSO test双重拉伸试验doucle tension test韦尔斯宽板拉伸试验Well’s wide plate test帕瑞斯公式Paris formula断裂分析图fracture analysis diagram焊接车间welding shop焊接工作间welding booth焊接工位welding post/ welding station焊接环境welding surroundings焊工welder电焊工manual arc welder气焊工gas welder焊接检验员weld inspector焊工培训welders training焊工模拟训练器trainer of synthetic weld焊工考试welder qualification test焊工合格证welder qualification/ welder qualified certification钢板预处理steel plate pretreatment喷沙sand blast喷丸shot blast矫正straighten开坡口bevelling (of the edge)/ chanfering装配assembly/ fitting安装erect刚性固定rigid fixing装配焊接顺序sequence of fitting and welding焊接工艺评定welding procedure qualification(转载自第一范文网,请保留此标记。
焊接方法与几种焊材的中英文对照
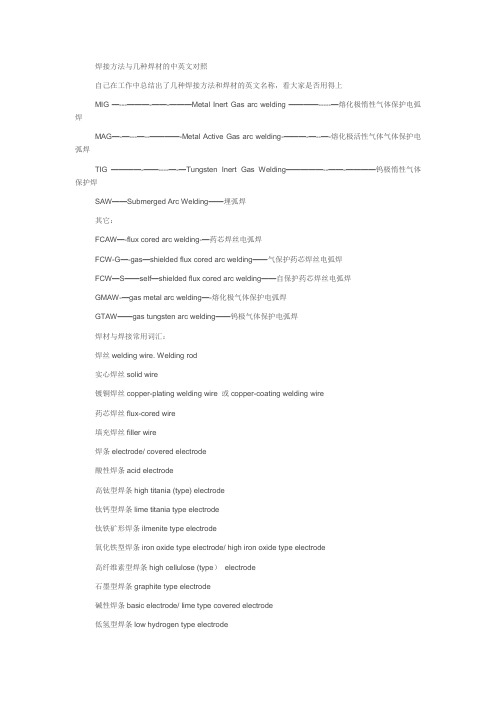
焊接方法与几种焊材的中英文对照自己在工作中总结出了几种焊接方法和焊材的英文名称,看大家是否用得上MIG —---———-——-———Metal Inert Gas arc welding ————-----—熔化极惰性气体保护电弧焊MAG—-—---—--————-Metal Active Gas arc welding-———-—--—-熔化极活性气体气体保护电弧焊TIG ————-——----—-—Tungsten Inert Gas Welding—————--——-————钨极惰性气体保护焊SAW——Submerged Arc Welding——埋弧焊其它:FCAW—-flux cored arc welding-—药芯焊丝电弧焊FCW-G—-gas—shielded flux cored arc welding——气保护药芯焊丝电弧焊FCW—S——self—shielded flux cored arc welding——自保护药芯焊丝电弧焊GMAW-—gas metal arc welding—-熔化极气体保护电弧焊GTAW——gas tungsten arc welding——钨极气体保护电弧焊焊材与焊接常用词汇:焊丝welding wire. Welding rod实心焊丝solid wire镀铜焊丝copper-plating welding wire 或copper-coating welding wire药芯焊丝flux-cored wire填充焊丝filler wire焊条electrode/ covered electrode酸性焊条acid electrode高钛型焊条high titania (type) electrode钛钙型焊条lime titania type electrode钛铁矿形焊条ilmenite type electrode氧化铁型焊条iron oxide type electrode/ high iron oxide type electrode高纤维素型焊条high cellulose (type)electrode石墨型焊条graphite type electrode碱性焊条basic electrode/ lime type covered electrode低氢型焊条low hydrogen type electrode高韧性超低氢焊条high toughness super low hydrogen electrode奥氏体焊条austenitic electrode铁素体焊条ferritic electrode不锈钢焊条stainless steel electrode珠光体耐热钢焊条pearlitic heat resistant steel electrode低温钢焊条low temperature steel electrode/ steel electrode for low temperature 铝合金焊条aluminum alloy arc welding electrode铜合金焊条copper-alloy arc welding electrode铜芯铸铁焊条cast iron electrode with steel core纯镍铸铁焊条pure nickel cast iron electrode球墨铸铁焊条electrode for welding spheroidal graphite cast iron铸芯焊条electrode with cast core wire镍基合金焊条nickel base alloy covered electrode渗铝钢焊条alumetized steel electrode高效率焊条high efficiency electrode铁粉焊条iron powder electrode重力焊条gravity electrode立向下焊条electrode for vertical down position welding水下焊条underwater welding electrode耐海水腐蚀焊条seawater corrosion resistant steel electrode堆焊焊条surfacing electrode耐磨堆焊焊条hardfacing electrode钴基合金堆焊焊条cobalt base alloy surfacing electrode碳化钨堆焊焊条tungsten carbide surfacing electrode高锰钢堆焊焊条high manganese steel surfacing electrode管状焊条flux—cored electrode装焊平台welding platen电磁平台electromagnetic platen焊接翻转机welding tilter焊接回转台floor turnable positioner焊接变位机positioner焊接滚轮架turning rolls焊条保温筒thermostat for electrode焊接参数welding parameter 电压Voltage激光切割laser cutting(LC); laser beam cutting电子束切割electron beam cutting喷气激光切割gas jet laser cutting碳弧切割carbon arc cutting水下切割underwater cutting喷水式水下电弧切割waterjet method underwater arc cutting氧矛切割oxygen lancing;oxygen lance cutting溶剂氧切割powder lancing手工气割manual oxygen cutting自动气割automatic oxygen cutting仿形切割shape cutting数控切割NC (numerical—control) cutting快速切割high-speed cutting垂直切割square cut叠板切割stack cutting坡口切割beveling;bevel cutting碳弧气割carbon arc air gouging火焰气刨flame gouging火焰表面清理scarfing氧熔剂表面修整powder washing预热火焰preheat flame预热氧preheat oxygen切割氧cutting oxygen/ cutting stream切割速度cutting speed切割线lone of cut/ cut line切割面face of cut/ cut face切口kerf切口上缘cutting shoulder切口宽度kerf width后拖量drag切割面平面度evenness of cutting surface/ planeness of cutting surface 割纹深度depth of cutting veins/ stria depth切割面质量quality of cut face上缘熔化度shoulder meltability/ melting degree of shoulder切口角kerf angle缺口notch挂渣adhering slag结瘤dross割炬cutting torch/ cutting blowpipe/ oxygen—fuel gas cutting torch割枪cutting gun割嘴cutting nozzle/ cutting tip快速割嘴divergent nozzle/ high—speed nozzle表面割炬gouging blowpipe水下割炬under—water cutting blowpipe水下割条electrode for under-water cutting粉剂罐powder dispenser数控切割机NC cutting machine门式切割机flame planer光电跟踪切割机photo—electric tracing cutting火焰切管机pipe flame cutting machine磁轮式气割机gas cutting machine with magnetic wheels 焊接结构welded structure/ welded construction焊件weldment焊接部件weld assembly组装件built—up member接头设计joint design焊接应力welding stress焊接瞬时应力transient welding stress焊接残余应力welding residual stress热应力thermal stress收缩应力contraction stress局部应力local stress拘束应力constraint stress固有应力inherent stress固有应变区inherent strain zone残余应力测定residual stress analysis逐层切割法Sach's methodX射线衍射法X—ray stress analysis小孔释放法Mathar method固有应变法inherent strain method消除应力stress relieving局部消除应力local stress relieving应力重分布stress redistribution退火消除应力stress relieving by annealing温差拉伸消除应力low temperature stress relieving机械拉伸消除应力mechanical stress relieving应力松弛stress relaxation焊接变形welding deformation焊接残余变形welding residual deformation局部变形local deformation角变形angular distortion自由变形free deformation收缩变形contraction deformation错边变形mismatching deformation挠曲变形deflection deformation波浪变形wave—like deformation火焰矫正flame straightening反变形backward deformation焊接力学welding mechanics断裂力学fracture mechanics弹塑性断裂变形elasto—plastic fracture mechanics线弹性断裂力学linear elastic fracture mechanics延性断裂ductile fracture脆性断裂brittle fracture应力腐蚀开裂stress corrosion cracking热应变脆化hot straining embrittlement临界裂纹尺寸critical crack size裂纹扩展速率crack propagation rate裂纹张开位移(COD)crack opening displacement拘束度restraint intensity拘束系数restraint coefficient应变速率strain rate断裂韧度fracture toughness应力强度因子stress intensity factor临界应力强度因子critical stress intensity factors应力腐蚀临界应力强度因子critical stress intensity factor of stress corrosion cracking J积分J—integration罗伯逊止裂试验Robertson crack arrest testESSO试验ESSO test双重拉伸试验doucle tension test韦尔斯宽板拉伸试验Well’s wide plate test帕瑞斯公式Paris formula断裂分析图fracture analysis diagram焊接车间welding shop焊接工作间welding booth焊接工位welding post/ welding station焊接环境welding surroundings焊工welder电焊工manual arc welder气焊工gas welder焊接检验员weld inspector焊工培训welders training焊工模拟练习器trainer of synthetic weld焊工考试welder qualification test焊工合格证welder qualification/ welder qualified certification钢板预处理steel plate pretreatment喷沙sand blast喷丸shot blast矫正straighten开坡口bevelling (of the edge)/ chanfering 装配assembly/ fitting安装erect刚性固定rigid fixing装配焊接顺序sequence of fitting and welding 焊接工艺评定welding procedure qualification 焊接工艺规程welding procedure specification 焊接工艺试验welding procedure test焊接工艺卡welding procedure card工序operational sequence焊接材料消耗定额welding consumables quota 焊接工时定额welder-hour quota清渣slag removal清根back gouging/ back chipping锤击peening返修次数number of rewelding焊接工作台welding bench装焊平台welding platen电磁平台electromagnetic platen焊接翻转机welding tilter焊接回转台floor turnable positioner焊接变位机positioner焊接滚轮架turning rolls焊接操作机manpulator焊工升降台welder's lifting platform焊接夹具welding jig/ fixture磁力夹紧器magnetic jig螺旋推撑器screw operated tensioning unit焊丝盘绕机welding wire coiler焊条压涂机welding electrode extrusion press 红外线加热器infra-red heater干燥箱dryer焊条保温筒thermostat for electrode流量计flow meterCO2预热器CO2 heaterCO2干燥器CO2 desiccator焊接电缆welding cable电缆夹头welding connector地线earth lead地线夹头earth clamp焊接参数记录仪welding parameter recorder 焊缝检测规weld gauge喷嘴通针tip cleaner测温笔tempil stick敲渣锤chipping hammer焊接衬垫backing/ welding backing保留垫板fusible backing/ permanent backing临时垫板temporary backing焊剂垫flux backing惰性气体衬垫inert-gas backing引弧板run—on tab/ end tab/ starting weld tab引出板run-off tab/ end tab定位板strong—back加强勒stiffener嵌条insert套环ferrule面罩helmet滤光镜片filter glass/ welding glass防护镜片cover glass/ plain glass气焊眼镜welding goggles焊接机器人welding robot点焊机器人spot welding robot弧焊机器人arc welding robot切割机器人cutting robot焊接机器人生产线robot line for welding焊接机器人工作站welding robot station机器人运动自由degree of free for robot机器人工作空间robot working space轨迹重复精度path repeatability点位重复精度PTP repeatability焊接专家系统welding expert system焊接机器人示数welding robot play back焊接图象识别pattern recognition for welding焊接图象处理welding image processing计算机辅助焊接工艺设计computer—aided welding process programming (CAWPP)计算机辅助焊接结构设计computer—aided design for welding structure焊接烟尘weld fume焊接发尘量total amount of fumes焊接烟尘浓度weld fume concentration焊接烟尘容限浓度threshold limit values of weld fume (TLV)焊接发尘速率weld fume emission rate焊接有害气体welding toxic gases/ weld harmful gases标定卫生空气需要量nominal hygienic air requirement焊工尘肺pheumocomsis of welder焊工锰中毒chronic occupational manganese poisoning of welder焊工氟中毒fluorosis of welder焊工金属烟热metal fume fever of welder电光性眼炎eye-flash (arc eye)电光性皮炎electro—photo dermatitis电弧紫外线灼伤ultraviolet ray burn防电击装置voltage reducing device除尘装置dust collection device焊工手套welding gloves护脚welding spats防护鞋shielding shoes焊接欠缺welding imperfection焊接缺陷weld defect气孔blowhole/ gas pore针尖状气孔pinhole密集气孔porosity条虫状气孔wormhole裂纹crack表面裂纹surface crack咬边undercut焊瘤overlap凹坑pit烧穿burn through塌陷excessive penetration未焊透incomplete penetration/ lack of penetration未熔合lack of fusion/ incomplete fusion未焊满incompletely filled weld根部凹陷root concavity电弧擦伤arc scratch夹渣slag inclusion夹杂物inclusion夹钨tungsten inclusion白点fish eye/ flake错边misalignment/ dislocation试件test piece试样test specimen无损检验nondestructive test破坏检验destructive test外观检查visual examination超声波探伤ultrasonic inspection直射法超声波探伤straight beam method斜射法超声波探伤angle beam method液浸法超声波探伤immersion method射线探伤radiographic inspection/ radiographyX射线探伤X-ray radiographic inspectionγ射线探伤gamma-ray inspectionX射线工业电视探伤X-ray industrial television inspection 磁粉探伤magnetic particle inspection电磁探伤electromagnetic inspection/ eddy current test 探伤灵敏度flaw detection sensitivity渗透探伤penetration inspection荧光探伤flurescent penetrant inspection着色探伤dye penetrant inspection密封性检验leak test气密性检验air tight test枕形气密检验pillow test耐压检验pressure test水压检验hydraulic test气压检验pneumatic test液晶检验liquid crystal test声发射检测acoustic emission testing面弯试验face bend testing背弯试验root bend test侧弯试验side bend test横弯试验horizontal bend test纵弯试验axial bend test压扁试验squeezing test。
ASTM标准.D3433

acting in a direction normal to the crack surface.4.2Load versus load-displacement across the bondline is recorded autographically.The G1c and G1a values are calcu-lated from this load by equations that have been established on the basis of elastic stress analysis of specimens of the type described below.The validity of the determination of G1c and G1a values by this test method depends upon the establishment of a sharp-crack condition in the bondline in a specimen of adequate size.This test method will measure the fracture strength of a bonded joint which is influenced by adherend surface condition,adhesive,adhesive-adherend interactions, primers,adhesive-supporting scrims,etc.,and in which of the above possible areas the crack grows.5.Significance and UseN OTE2—Crack growth in adhesive bond specimens can proceed in two ways:(1)by a slow-stable extension where the crack velocity is dictated by the crosshead rate or(2)by a run-arrest extension where the stationary crack abruptly jumps ahead outrunning the crosshead-predicted rate.The first type of crack extension is denotedflat;the second type peaked because of the appearance of the autographic record.Theflat behavior is characteristic of adhesives or test temperatures,or both,for theseadhesives where there is no difference between initiation,G1c ,and arrest,G1a .For example,the rubber modifiedfilm adhesives testedabove−17.8°C(0°F)all exhibitflat autographic records.Peaked curves are exhibited for all modified materials tested below−73°C(−100°F)and in general for unmodified epoxies.It should be noted that both peaked andflat behaviors are determined from a crack-length-independent specimen.For other specimens or structures where G increases with a at constant load the onset of crack growth would result in rapid complete fracturing whatever the adhesive characteristics.5.1The property G1c(and G1a if relevant)determined by this test method characterizes the resistance of a material to slow-stable or run-arrest fracturing in a neutral environment in the presence of a sharp crack under severe tensile constraint, such that the state of stress near the crack front approaches tritensile plane strain,and the crack-tip plastic region is small compared with the crack size and specimen dimensions in the constraint direction.It has not been proven that tough adhesive systems fully meet this criteria.Therefore,data developed using equations based on this assumption may not represent plane-strain fracture parison of fracture toughness between adhesive systems widely different in brittleness or toughness should take this into consideration.In general, systems of similar type toughness(3,4,7,8,10)can be compared as can the effect of environment on toughness of a single system.A G1c value is believed to represent a lower limiting value of fracture toughness for a given temperature, strain rate,and adhesive condition as defined by manufacturing variables.This value may be used to estimate the relation between failure stress and defect size for a material in service wherein the conditions of high constraint described above would be expected.Background information concerning the basis for development of this test method in terms of linear elastic fracture mechanics may be found in Refs(6)and(7).5.1.1Cyclic loads can cause crack extension at G1values less than G1c value.Furthermore,progressive stable crack extension under cyclic or sustained load may be promoted by the presence of certain environments.Therefore,application of G1c in the design of service components should be made with awareness of the G increase for a prior crack which may occur in service due to slow-stable crack-extension.5.2This test method can serve the following purposes: 5.2.1In research and development to establish,in quantita-tive terms,significant to service performance,the effects of adhesive composition,primers,adherend surface treatments, supporting adhesive carriers(scrim),processing variables,and environmental effects.5.2.2In service evaluation to establish the suitability of an adhesive system for a specific application for which the stress conditions are prescribed and for which maximumflaw sizes can be established with confidence.5.2.3For specifications of acceptance and manufacturing quality control,but only when there is a sound basis for specification of minimum G1c values.The specification of G1c values in relation to a particular application should signify that a fracture control study has been conducted on the component in relation to the expected history of loading and environment, and in relation to the sensitivity and reliability of the crack detection procedures that are to be applied prior to service and subsequently during the anticipated life.6.Apparatus6.1Testing Machine,conforming to the requirements of Practices E4.Select the testing machine such that the cracking load of the specimens falls between15and85%of the full-scale capacity and that is provided with a suitable pair of self-aligning pinnedfixtures to hold the specimen.6.2Ensure that the pinnedfixtures and attachments are constructed such that they will move into alignment with the test specimen as soon as the load is applied.6.3For a discussion of the calculation of separation rates see Annex A1.7.Test Specimens7.1Flat Adherend,conforming to the form and dimensions shown in Fig.1,cut from test joints as in Fig.2,prepared as prescribed in Section8.7.2Contoured Double-Cantilever Beam(CDCB),conform-ing to the form and dimensions shown in Fig.3.7.3The following grades of metals are suggested for the test specimens(Note3):Metal ASTM DesignationBrass B36,Alloy260(6),quarter hard temperCopper B152,cold rolled,Type110,hard temperAluminum B209,Alclad2024,T3temper,millfinishSteel A366,regular mattefinishCorrosion-resisting steel A167,Type304,No.2BfinishTitanium B265,Grade37.4Test at least twelve specimens,representing at least four different joints.N OTE3—Since it is unacceptable to exceed the yield point of the metal inflexure during test,the permissible thickness of the specimen will vary with type of metal,and the general level of strength of the adhesive being investigated.The minimum permissible thickness in a uniform symmetri-cal adherend may be computed from the following relationship:h5Œ6Ta BF ty(2)where:h 5thickness of metal normal to plane of bonding,mm (or in.),F ty 5tensile yield point of metal (or the stress at proportional limit)MPa (or psi),T 5150%of the maximum load to start the crack in the adhesivebond,N (or lbf),a 5crack length at maximum load,mm (or in.),andB 5bond width,mm (or in.).8.Preparation of Test Joints 8.1Cut sheets of the metals or contoured adherends pre-scribed in 7.1-7.3and to recommended size (Figs.2and 3).All edges of the metal panels and specimens must be flat,free of burrs,and smooth (4.1-µm (160-µin.)maximum)before thepanels are surface-treated and bonded.Clean,treat,and dry thesheets or contoured adherends carefully,in accordance with theprocedure prescribed by the manufacturer of the adhesive.Prepare and apply the adhesive in accordance with the recom-mendations of the manufacturer of the adhesive.Apply theadhesive to the faying surface of one or both metal sheets.Thenassemble the sheets,faying surface to faying surface in pairs,and allow the adhesive to cure under conditions prescribed bythe manufacturer of the adhesive.8.2It is recommended that each “flat adherend”test joint bemade with sufficient area to provide at least five test specimens.9.Preparation of Test Specimens 9.1For flat adherend test specimens,trim joint area in accordance with Fig.2.Then cut test specimens,as shown in Fig.1,from the joints,Fig.2(Note 4).Then cut holes for load pins as shown in Fig.1.9.2Contoured double-cantilever specimens are ready for test as bonded.N OTE 4—Do not use lubricants or oils during the cutting process.Foraluminum it is suggested that the specimens be rough cut 3.2mm (1⁄8in.)over-size using a four-pitch band saw traveling at approximately 4.2m/s(800ft/min)followed by finish dimensioning to a 1-in.wide 3.2-µm(125-µin.)surface using a five-blade 15-deg carbide fly cutter at 1115rpmand 0.015to 0.035-m/s (3to 7-in./min)feed rate.10.Procedure 10.1Test specimens,prepared as prescribed in Section 8,in an atmosphere maintained at 5064%relative humidity and 2361°C (73.46 1.8°F).Tests at other than ambient temperature may be run if desired.It is suggested that specimens be conditioned for a minimum of 10min and a maximum of 30min at the temperature of test to assure equilibrium.The manufacturer of the adhesive may,however,prescribe a definite period of conditioning under specific conditions beforetesting.FIG.1Flat AdherendSpecimenFIG.2TestJoint10.2Determine the following test specimen dimensions.10.2.1Distance from center of 6.4-mm (0.25-in.)inside-diameter pin holes to close end of specimen.10.2.2Width of test specimen,b .10.2.3Thickness of test specimen 127mm (5in.)from pinend and 227mm (9in.)from pin end.10.2.4Bond line thickness 125mm (5in.)from pin end and227mm (9in.)from pin end.10.3Load the specimen in the test machine and pin inposition using the 6.4-mm (0.25-in.)inside-diameter pin holes.Balance the recorder or chart,or both.Set the test machine ata crosshead separation rate _˙chosen to keep time-to-fracturein the order of 1min,see 6.1and Annex A1.For example,2mm/min (0.08in./min)gives fracture in 1min for a CDCB1⁄2-in.wide m 590-in.−1aluminum adherend specimen havinga 3-in.long starter crack.10.3.1The chart recording should be such that maximumload occurs on the record and that at least 13mm (1⁄2in.)ofmotion is represented on the abscissa (_)for each 100mm (4in.)of ordinate motion (P ).For load-time records a chart speedrate should be used such that the slope of the load versus timerecord is similar to that specified for load versus load-displacement (for example,5mm/min (0.2in./mm)).10.4Apply load to specimen until Point A is reached.(SeePoint A,Fig.4for flat adherend and Fig.5,Point A forcontoured double-cantilever specimen.)Point A is the load atwhich the crack begins to grow rapidly.Then stop loading andfollow crack growth curve on the chart.When the load hasleveled off at an approximate constant value (the crack hasstopped growing),determine and record the following values:10.4.1Load to start crack,L (max),N (or lbf),10.4.2Load when crack stops,L (min),N (or lbf),and 10.4.3Distance from loading end of specimen to the sta-tionary crack tip in millimetres (or inches).10.5Repeat 10.4to yield five determinations on eachspecimen.FIG.3Contoured Double-Cantilever BeamSpecimenFIG.4Typical Flat AdherendTest11.Calculation11.1Flat Adherend Specimen :11.1.1Calculate the fracture toughness,G1c (from load tostart crack),in joules per square metre or pounds-force per inchas follows:G 1c 5@4L 2~max !#@3a 21h 2#@E B 2h 3#(3)11.1.2Calculate fracture toughness,G1a (from arrest load),as follows:G 1a 5@4L 2~min !#@3a 21h 2#@E B 2h 3#(4)where:L (max)5load to start crack,N (or lb),L (min)5load at which crack stops growing,N (or lb),E 5tensile modulus of adherend,MPa (or psi),B 5specimen width,mm (or in.),a 5crack length,mm (or in.)(5distance fromcrack tip to pin hole centers),and h 5thickness of adherend,normal to plane ofbonding mm (or in.)(512.7mm (0.50in.)unless otherwise specified).11.2Contoured Double-Cantilever Specimen :11.2.1Calculate the fracture toughness,G1c (from load tostart crack),in joules per square metre or pounds-force perinch,as follows:G 1c 5@4L 2~max !#~m !@E B 2#(5)11.2.2Calculate the fracture toughness,G1a (from arrestload),as follows:G 1a 5@4L 2~min !#~m !@E B 2#(6)where:a 5crack length,mm (or in.)(5distance from crack tip to pin hole centers),h 5thickness of adherend,normal to plane of bond-ing,mm (or in.),m 53a 2/h 3+1/h ,(Note 3)(Note 5),L(max)5load to start crack,N (or lbf),L(min)5load at which crack stops growing,N (or lbf),E 5tensile modulus of adherend,MPa (or psi),B 5specimen width,mm (or in.),N OTE 5—The purpose of the contoured double-cantilever specimen is to make the measurement of fracture toughness G 1independent of crack length a .To develop a linear compliance specimen,its height is varied so that the quantity 3a2⁄h3+1⁄h is constant.Hence,3a 2h 311h 5m (7)There are,of course,any number of m values that can be used in designing a specimen.A convenient contour for testing adhesives is m 590in.−1,as shown in Fig.3.The very high m number or low-taper angle would cause a large bending stress on the plane of the crack if the specimen were monolithic.Because of the low modulus of the adhesives compared with that of the adherends,these bending stresses are not significant.If bulk specimens of the adhesive materials are to be tested,the bending stresses tend to cause one or the other arm to break off.This problem is minimized by using lower m numbers,that is,by making the beams stiffer,and adding side grooves to the specimens to direct the crack in the desired plane of extension.When the specimens are made stiffer,the description of m as 53a 2/h 3+1/h is satisfactory for designing linear compliance speci-mens but cannot be used to calculate G 1c because the assumptions used in beam theory become increasingly invalid as the beam height to length ratio increases.In place of m an experimental value determined from compliance calibrations and designated as m 8is required.Hence,the toughness for monolithic specimens having low m values is defined as G 1c 5L 2~max !@8#@m 8#2B n ·Eb (8)where:B n 5specimen width at crack plane,and b 5gross specimen width.12.Report 12.1Report the following information:12.1.1Complete identification of the adhesive tested,in-cluding type,source,date manufactured,manufacturers code number,form,etc.,12.1.2Complete identification of the metal used,its thick-ness,and the method of cleaning and preparing its surfaces prior to bonding,12.1.3Application and bonding conditions used in prepar-ing the specimens,12.1.4Conditioning procedure used for specimens prior to testing,12.1.5Test temperature,12.1.6Loading rate used,12.1.7Time-to-fracture,12.1.8Chart speed used,12.1.9Number of specimens tested,12.1.10Number of joints represented,12.1.11Bondline thickness (Note 4),12.1.12Individual G 1c and G 1a (fracture toughness tostartFIG.5Typical Contoured Double-Cantilever BeamTestcrack and fracture toughness from arrest load)values for each specimen,12.1.13Maximum,minimum,and average values for G1c and G1a,and12.1.14The nature of the failure,including the average estimated percentages of failure in the cohesion of the adhe-sive,contact failure,voids,and apparent adhesion to the metal. N OTE6—Report the average thickness of adhesive layer after formation of the joint within0.01mm(0.0005in.).Describe the method of obtaining the thickness of the adhesive layer including procedure,location of measurements,and range of measurements.13.Precision and Bias13.1The following data should be used for judging the acceptability of results(95%confidence limits)(Note7): 13.1.1Repeatability—Duplicate test results by an indi-vidual should be considered suspect if they differ by more than 10%.13.1.2Reproducibility—The average result reported by one laboratory should be considered suspect if it differs from that of another laboratory by more than10%.N OTE7—These precision data are approximations based on limited data,but they provide a reasonable basis for judging the significance of results.Care must be taken to control variation in bondline thickness and to measure the crack length accurately.The ability to measure the crack tip and its geometry as well as actual variation in the material properties of some adhesive may result in performance which will have greater scatter.14.Keywords14.1adhesive;bonded joint;cleavage;double-cantilever beam;fracture strengthANNEX(Mandatory Information)A1.CALCULATION OF SEPARATION RATESA1.1Fracture tests are generally designed so that the onset of crack extension occurs in about1min from the time monotonically increasing loading begins.Due to compliance and compliance change differences for different specimen geometries specific ranges of separation rate are required to conform this time to fracture specification.Thus,the calcula-tion of separation rates for a particular test specimen shall be done using the following expressions.For contoured double-cantilever beams(CDCB):3200CB/2=m8,D˙,16000CB/2=m8(A1.1) where:D5displacement of the load(load-displacement),mm (or in.),D˙5load-displacement rate,mm(or in.)/min,B5specimen width,m85defined in Section11,C5specimen compliance,MPa(or psi);a function of crack length,namely:C58/EB[(3(a o)2/h3+1/h)+m8(a−a o)]E5tensile modulus(defined in Section11),a5crack length,mm(or in.)(defined in Section11),a o5length of constant-height section of the front part ofthe specimen from the center-line of the loadingholes to the point at which the contoured sectionbegins,andh5adherend thickness,mm(or in.)(defined in Section11).N OTE A1.1—The constants3200and16000are in units of psi=in. and require all units in the equation to be in similar units.If MKS,metric conversion is desirable3200and16000psi=in.are3.51and17.57 MPa·m−3/2.A1.1.1For example,for1⁄2-in.thick,1⁄2-in.wide aluminum m8590-in.−1adherends,the expression for D˙and C becomes84C<D˙<416CC5100/1061144/106~a21.625!(A1.2) A1.1.2For a crack length of3in.a rate of0.08in./min will cause crack growth to occur in1min if G Ic is10lb/in.For a 3-in.long crack,0.025,D˙,0.124(A1.3) and the value of0.08is within the range specified.This expression for D˙in terms of C will give fracture times in the order of1min for G Ic values between1and25.(D˙should be selected for a given adhesive toughness to give time-to-fracture values close to1min.)A1.1.3The value of D˙should be increased periodically as the crack extends such that it conforms to the expression.If the crack were to be at6in.:0.053,D˙,0.26(A1.4) The value of0.08in./min would still be within the above range;however,fracture times would be increased to2min (G Ic510lb/in.).This in itself is not considered a violation of specifications,but if fracture times were to be shortened to1 min,D˙would have to be increased to0.17in./min.A1.1.4In practice,the crack would be run for some dis-tance,for example2in.,and the loading rate increased to reduce the fracture time to an acceptable value.A1.1.5The calculation of D˙for uniform double-cantilever beam specimens can be done in much the same manner;for example:3200CB2Œ3~a10.6h!2h211h,D˙,16000CB2Œ3~a10.6h!2h211h(A1.5)C 58/EB S ~a 10.6h !3h 31a h DA1.1.6For a 3-in.long crack in a 1⁄2-in.thick 1⁄2-in.wide aluminum adherend specimen:0.023,D˙,0.116(A1.6)In order to keep D˙within the tolerance limits crack length would have to be monitored which,of course,would have to bedone to determine initial values of G.A1.2It should also be noted that D ˙,the load-displacement,is not identical with jaw separation,although for low loads using a relatively stiff testing machine they will be close.For those tests where it is determined that there is a substantial difference between D ˙and jaw separation rate the jaw separa-tion rate should be increased to conform with time-to-fracture requirements.Subsequent tests should be made using whatever correction factor is determined for the particular test machine.REFERENCES(1)Ripling, E.J.,Mostovoy,S.and Patrick,R.L.,“Application ofFracture Mechanics to Adhesive Joints,”ASTM STP 360,ASTM ,1963.(2)Ripling,E.J.,Mostovoy,S.,and Patrick,R.L.,“Measuring FractureToughness of Adhesive Joints,”Materials,Research,and Standards,ASTM,V ol 64,No.3,1964.(3)Mostovoy,S.,and Ripling,E.J.,“Fracture Toughness of an EpoxySystem,”Journal of Applied Polymer Science,V ol 10,1966,pp.1351–1371.(4)Mostovoy,S.,and Ripling, E.J.,“Influence of Water on StressCorrosion Cracking of Epoxy Bonds,”Journal of Applied PolymerScience,V ol 13,1969,pp.1082–1111.(5)Mostovoy,S.,Bersch,C.F.,and Ripling,E.J.,“Fracture Toughness ofAdhesive Joints,”Journal of Adhesion,V ol 3,1971,pp.125–144.(6)Ripling,E.J.,Corten,H.T.,and Mostovoy,S.,“Fracture Mechanics:A Tool for Evaluating Structural Adhesives,”Journal of Adhesion,V ol3,1971,pp.107–123.(Also published in SAMPE Journal,1970).(7)Ripling, E.J.,Bersch, C.,and Mostovoy,S.,“Stress Corrosion Cracking of Adhesive Joints,”Journal of Adhesion,V ol 3,1971,pp.145–163.(Also published in SAMPE Journal,1970).(8)Mostovoy,S.,and Ripling,E.J.,“The Fracture Toughness and Stress Corrosion Cracking Characteristics of an Adhesive,”Journal of Applied Polymer Science,V ol 15,1971,pp.641–659.(Also published in SAMPE Journal,1970.)(9)Mostovoy,S.,and Ripling,E.J.“Effect of Joint Geometry on the Toughness of Epoxy Adhesives,”Journal of Applied Polymer Science,V ol 15,1971,pp.661–673.(Also published SAMPE Journal,1970.)(10)Mostovoy,S.,and Ripling,E.J.,“Effect of Temperature on the Fracture Toughness and Stress Corrosion Cracking of Adhesives,Applied Polymer Symposium No.19,1972,pp.395–408.The American Society for Testing and Materials takes no position respecting the validity of any patent rights asserted in connection with any item mentioned in this ers of this standard are expressly advised that determination of the validity of any such patent rights,and the risk of infringement of such rights,are entirely their own responsibility.This standard is subject to revision at any time by the responsible technical committee and must be reviewed every five years and if not revised,either reapproved or withdrawn.Your comments are invited either for revision of this standard or for additional standards and should be addressed to ASTM Headquarters.Your comments will receive careful consideration at a meeting of the responsible technical committee,which you may attend.If you feel that your comments have not received a fair hearing you should make your views known to the ASTM Committee on Standards,100Barr Harbor Drive,West Conshohocken,PA 19428.This standard is copyrighted by ASTM,100Barr Harbor Drive,West Conshohocken,PA 19428-2959,United States.Individual reprints (single or multiple copies)of this standard may be obtained by contacting ASTM at the above address or at 610-832-9585(phone),610-832-9555(fax),or service@ (e-mail);or through the ASTM website().。
ASTM材料与实验标准.E399

Referenced Documents Terminology
Stress-Intensity Factor Plane-Strain Fracture Toughness Crack Plane Orientation
Section 2 3 3.1.1 3.1.2 3.1.3
1 This test method is under the jurisdiction of ASTM Committee E08 on Fatigue and Fracture and is the direct responsibility of Subcommittee E08.07 on LinearElastic Fracture.
1
E 399 – 05
1.6 Specific requirements related to special test procedures:
Fatigue Precracking KIc Specimens Hot-Pressed Beryllium Testing Rapid-Force Testing
This standard has been approved for use by agencies of the Department of Defense.
1. Scope
1.1 This test method covers the determination of fracture toughness (KIc) of metallic materials under predominantly linear-elastic, plane-strain conditions using fatigue precracked specimens having a thickness of 1.6 mm (0.063 in.) or greater2 subjected to slowly, or in special (elective) cases rapidly, increasing crack-displacement force. Details of test apparatus, specimen configuration, and experimental procedure are given in the Annexes.
高分子物理名词解释
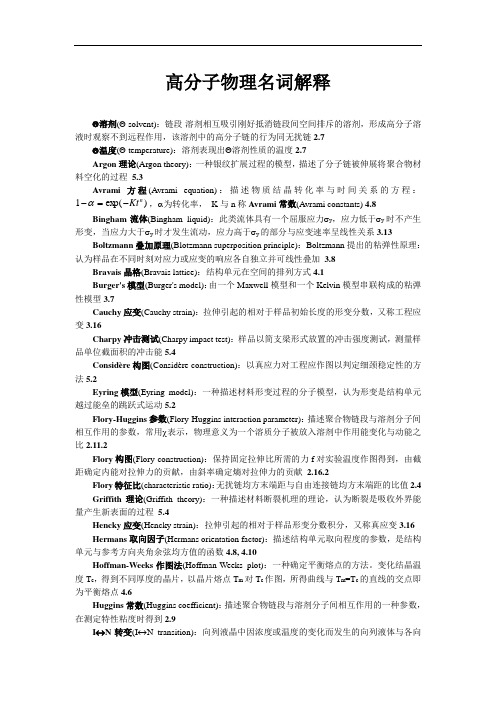
高分子物理名词解释Θ溶剂(Θ solvent):链段-溶剂相互吸引刚好抵消链段间空间排斥的溶剂,形成高分子溶液时观察不到远程作用,该溶剂中的高分子链的行为同无扰链2.7Θ温度(Θ temperature):溶剂表现出Θ溶剂性质的温度2.7Argon理论(Argon theory):一种银纹扩展过程的模型,描述了分子链被伸展将聚合物材料空化的过程5.3Avrami方程(Avrami equation):描述物质结晶转化率与时间关系的方程:--α,α为转化率,K与n称Avrami常数(Avrami constants) 4.8 =Kt1n)ex p(Bingham流体(Bingham liquid):此类流体具有一个屈服应力σy,应力低于σy时不产生形变,当应力大于σy时才发生流动,应力高于σy的部分与应变速率呈线性关系3.13 Boltzmann叠加原理(Blotzmann superposition principle):Boltzmann提出的粘弹性原理:认为样品在不同时刻对应力或应变的响应各自独立并可线性叠加 3.8Bravais晶格(Bravais lattice):结构单元在空间的排列方式4.1Burger's模型(Burger's model):由一个Maxwell模型和一个Kelvin模型串联构成的粘弹性模型3.7Cauchy应变(Cauchy strain):拉伸引起的相对于样品初始长度的形变分数,又称工程应变3.16Charpy冲击测试(Charpy impact test):样品以简支梁形式放置的冲击强度测试,测量样品单位截面积的冲击能5.4Considère构图(Considère construction):以真应力对工程应作图以判定细颈稳定性的方法5.2Eyring模型(Eyring model):一种描述材料形变过程的分子模型,认为形变是结构单元越过能垒的跳跃式运动5.2Flory-Huggins参数(Flory-Huggins interaction parameter):描述聚合物链段与溶剂分子间相互作用的参数,常用χ表示,物理意义为一个溶质分子被放入溶剂中作用能变化与动能之比2.11.2Flory构图(Flory construction):保持固定拉伸比所需的力f对实验温度作图得到,由截距确定内能对拉伸力的贡献,由斜率确定熵对拉伸力的贡献2.16.2Flory特征比(characteristic ratio):无扰链均方末端距与自由连接链均方末端距的比值2.4 Griffith理论(Griffith theory):一种描述材料断裂机理的理论,认为断裂是吸收外界能量产生新表面的过程5.4Hencky应变(Hencky strain):拉伸引起的相对于样品形变分数积分,又称真应变3.16 Hermans取向因子(Hermans orientation factor):描述结构单元取向程度的参数,是结构单元与参考方向夹角余弦均方值的函数4.8, 4.10Hoffman-Weeks作图法(Hoffman-Weeks plot):一种确定平衡熔点的方法。
材料科学与工程专业英语1-19单元课后翻译答案
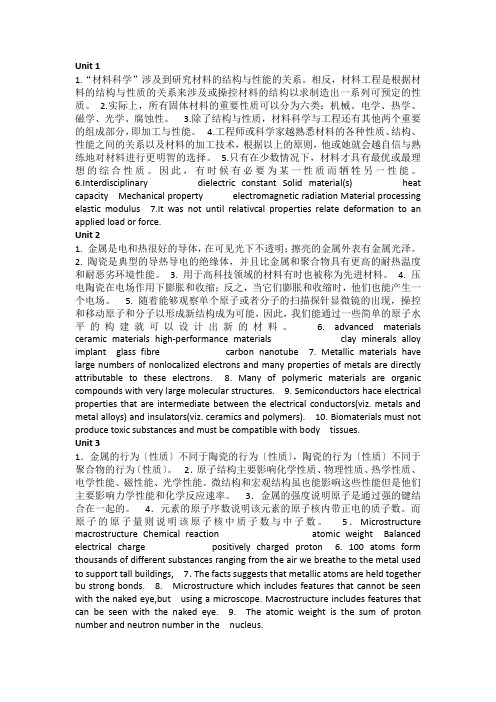
1.“材料科学”涉及到研究材料的结构与性能的关系。
相反,材料工程是根据材料的结构与性质的关系来涉及或操控材料的结构以求制造出一系列可预定的性质。
2.实际上,所有固体材料的重要性质可以分为六类:机械、电学、热学、磁学、光学、腐蚀性。
3.除了结构与性质,材料科学与工程还有其他两个重要的组成部分,即加工与性能。
4.工程师或科学家越熟悉材料的各种性质、结构、性能之间的关系以及材料的加工技术,根据以上的原则,他或她就会越自信与熟练地对材料进行更明智的选择。
5.只有在少数情况下,材料才具有最优或最理想的综合性质。
因此,有时候有必要为某一性质而牺牲另一性能。
6.Interdisciplinary dielectric constant Solid material(s) heat capacity Mechanical property electromagnetic radiation Material processing elastic modulus7.It was not until relativcal properties relate deformation to an applied load or force.Unit 21. 金属是电和热很好的导体,在可见光下不透明;擦亮的金属外表有金属光泽。
2. 陶瓷是典型的导热导电的绝缘体,并且比金属和聚合物具有更高的耐热温度和耐恶劣环境性能。
3. 用于高科技领域的材料有时也被称为先进材料。
4. 压电陶瓷在电场作用下膨胀和收缩;反之,当它们膨胀和收缩时,他们也能产生一个电场。
5. 随着能够观察单个原子或者分子的扫描探针显微镜的出现,操控和移动原子和分子以形成新结构成为可能,因此,我们能通过一些简单的原子水平的构建就可以设计出新的材料。
6. advanced materials ceramic materials high-performance materials clay minerals alloy implant glass fibre carbon nanotube7. Metallic materials have large numbers of nonlocalized electrons and many properties of metals are directly attributable to these electrons.8. Many of polymeric materials are organic compounds with very large molecular structures.9. Semiconductors hace electrical properties that are intermediate between the electrical conductors(viz. metals and metal alloys) and insulators(viz. ceramics and polymers). 10. Biomaterials must not produce toxic substances and must be compatible with body tissues.Unit 31.金属的行为〔性质〕不同于陶瓷的行为〔性质〕,陶瓷的行为〔性质〕不同于聚合物的行为〔性质〕。
CHEMISTRY - PHYSICS AND MECHANICS OF ADHESION SCIENCE
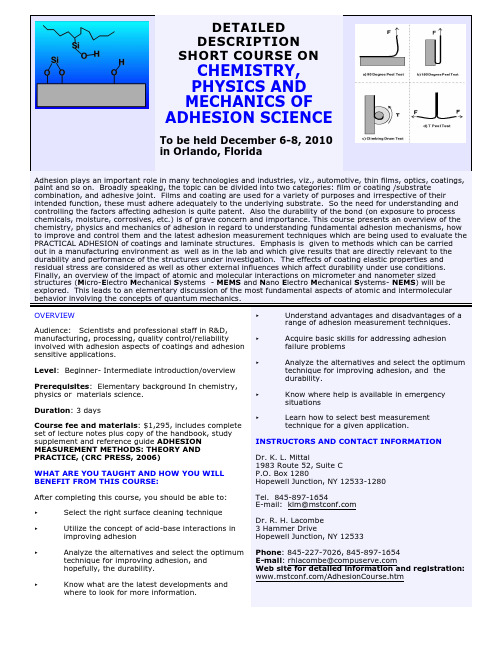
Adhesion plays an important role in many technologies and industries, viz., automotive, thin films, optics, coatings, paint and so on. Broadly speaking, the topic can be divided into two categories: film or coating /substrate combination, and adhesive joint. Films and coating are used for a variety of purposes and irrespective of their intended function, these must adhere adequately to the underlying substrate. So the need for understanding and controlling the factors affecting adhesion is quite patent. Also the durability of the bond (on exposure to process chemicals, moisture, corrosives, etc.) is of grave concern and importance. This course presents an overview of the chemistry, physics and mechanics of adhesion in regard to understanding fundamental adhesion mechanisms, how to improve and control them and the latest adhesion measurement techniques which are being used to evaluate the PRACTICAL ADHESION of coatings and laminate structures. Emphasis is given to methods which can be carriedout in a manufacturing environment as well as in the lab and which give results that are directly relevant to the durability and performance of the structures under investigation. The effects of coating elastic properties and residual stress are considered as well as other external influences which affect durability under use conditions. Finally, an overview of the impact of atomic and molecular interactions on micrometer and nanometer sized structures (M icro-E lectro M echanical S ystems- NEMS) will be explored. This leads to an elementary discussion of the most fundamental aspects of atomic and intermolecular behavior involving the concepts of quantum mechanics.OVERVIEWAudience: Scientists and professional staff in R&D, manufacturing, processing, quality control/reliability involved with adhesion aspects of coatings and adhesion sensitive applications.Level: Beginner- Intermediate introduction/overview Prerequisites: Elementary background In chemistry, physics or materials science.Duration: 3 daysCourse fee and materials: $1,295, includes complete set of lecture notes plus copy of the handbook, study supplement and reference guideMEASUREMENT METHODS: THEORY ANDUnderstand advantages and disadvantages of arange of adhesion measurement techniques.Acquire basic skills for addressing adhesionAnalyze the alternatives and select the optimumtechnique for improving adhesion, and theKnow where help is available in emergencyLearn how to select best measurementtechnique for a given application. INSTRUCTORS AND CONTACT INFORMATIONTOPICS TO BE COVEREDSURFACE CONTAMINATION AND CLEANING<Various Cleaning Techniques<Characterization of Cleanliness<Importance of Cleanliness in Adhesion<Storage of Clean PartsTHEORIES OR MECHANISMS OF ADHESION<Various theories:<Mechanical<Surface<Energetics<Diffusion<Electrostatic<Chemical:<Acid-Base, and Weak BoundaryLayer) with their RelativeValidity and Usefulness.<Special Consideration of Acid-BaseConcepts in AdhesionCONTACT ANGLE, WETTABILITY AND ADHESION<<Contact Angle Measurement and FactorsAffecting it<Determination of Surface Free Energy ofPolymers<Relevance of Wettability and Surface Energetics in AdhesionINVESTIGATION OF INTERFACIAL INTERACTIONS <Application of ESCA in Unraveling Events at an InterfaceSURFACE MODIFICATION TECHNIQUES AND OTHER WAYS TO IMPROVE ADHESION OF ORGANIC COATINGS<Various Surface Modification Techniques<(e.g., Plasma, Flame, Corona, Laser, UV, Ozone, Wet)<Other Ways to Improve Adhesion<Factors Affecting Adhesion of Organic Coatings <Stresses in Coatings and Their Relevance to AdhesionSILANES AND OTHER ADHESION PROMOTERS<Various Aspects of Silane Adhesion Promoters;How to Apply Them and Where to Apply Them? <Examples of Adhesion<Improvement by Use of Silanes<Non-Silane Adhesion Promoters ADHESION ASPECTS OF THIN FILMS1.Various Mechanisms of Adhesion of Thin Films2.Factors Affecting Adhesion of Thin Films andWays to Improve Adhesion (Note: MetallizedPlastics and Cases of Other Thin Films on aVariety of Substrates will be Discussed)ADHESION MEASUREMENT OF FILMS AND COATINGS<Concept of Practical Adhesion<Various Techniques (Ranging from Simple to Sophisticated) for Measuring Adhesion withTheir Potentialities and Limitations<Basics of adhesion measurement:a. Qualitative methodsb. Semi-quantitative methodsc. Fully quantitative methods<Role of residual stress and material mechanical properties on adhesion:a. Effect of coating and substrate elasticpropertiesb. Effect of residual stress<Problem of setting adhesion requirements for coating applications:a. What is a sufficient level of adhesionstrength?b. Avoid over-specifying adhesionrequirements to the detriment of otherproduct requirements.c. Problem of long-term environmentaldegradation.<Adhesion measurement at atomic and molecular level (fundamental adhesion):a.Surface force apparatusb.Atomic force microscopec.Hamaker theoryd.Contact angle behavior<General Applications:<Setting quality control specifications<Provide data base for productengineering design work<Support new product research anddevelopment<Identify and eliminate potential failuremodes early in development cycle<Enable rapid effective response tounforseen failure mechanismsDURABILITY OF ADHESIVE JOINTS PART ONE: OVERVIEW OF TEST METHODS1.Two Aspects of Adhesive Actiona.Interfacial bonding between adhesivesand adherendsb.Bulk thermal-mechanical performance ofadhesives2.Durability of Adhesive Jointsa.Stress and Deformation in MaterialBodies, a quick overviewb.Strength of Materials Theory (SOM)c.Fracture Mechanics3.Direct Measurement of Joint strengthp shear testb.Double cantilever beam testc.Four point bend test4.Measuring Adhesive Thermal-MechanicalPropertiesa.Elastic propertiesb.Viscoelastic propertiesi.Creep behaviorii.Concept of time-temperaturesuperposition5.Role of Residual Stressa.Cantilevered beam methodsb.Ultrasonicsc.Photoelasticityd.Strain relief methods6.Nondestructive Inspectiona.Xrayb.Thermographyc.Shearographyd.Ultrasonics PART TWO: DETAILED LOOK AT SPECIFIC TESTS AND CASE STUDIES1. A Closer Look at Interfacial AdhesionThrough the Peel Testa.Peel testing on a shoe string2.The Peel Test in the Development Lab andManufacturing Linea.Ranking effectiveness of adhesionpromotersb.Evaluating the effect of manufacturingprocedures on bond durabilityc.Developing improved process steps3. A Closer Look at The Thermal-MechanicalProperties of Polymersmon Test methodsi.Dynamic mechanicalexperimentsii.Determination of glassgtransition, Tgiii.Relaxation processes below Tb.Case Study on rubber modified epoxystructural adhesivesi.Time-temperature superpositionfor epoxiesii.Variation of fracture toughnesswith loading rate andtemperature4.Putting it All Together: A Guide to theEvaluation and Prediction of BondDurabilitya.Structures that survive in the long termare in a state of unconditional stabilityb.Stability maps: An engineering tool forputting it all together.c.Case study: Adhering pins to a multi-chip module:i.Pathology of pin failure, outlineof the problemii.Modeling virtual crackpropagationiii.Creating a stability map。
- 1、下载文档前请自行甄别文档内容的完整性,平台不提供额外的编辑、内容补充、找答案等附加服务。
- 2、"仅部分预览"的文档,不可在线预览部分如存在完整性等问题,可反馈申请退款(可完整预览的文档不适用该条件!)。
- 3、如文档侵犯您的权益,请联系客服反馈,我们会尽快为您处理(人工客服工作时间:9:00-18:30)。
Available online at ScienceDirectJournal of the European Ceramic Society35(2015)3155–3166On measuring fracture toughness under load control inthe presence of slow crack growthGoranˇZagar∗,Aparna Singh1,Václav Pejchal,Martin G.Mueller,Andreas Mortensen Laboratory of Mechanical Metallurgy,Institute of Materials,École Polytechnique Fédérale de Lausanne(EPFL),Station12,1015Lausanne,SwitzerlandReceived6March2015;received in revised form1April2015;accepted4April2015Available online25April2015AbstractThe influence of slow crack growth in ceramics on the measurement of their fracture toughness under steadily increasing controlled load(as is generally practiced in microscale testing)is analyzed to identify conditions under which the phenomenon can cause error.The analysis considers the two regimes classically observed,namely a power-law variation of crack growth rate on the stress intensity factor K,and,at higher K values,a regime offixed crack tip velocity up to rapid fracture at K=K c.Results are presented for standard test specimens in a convenient graphical form and also in the form of upper bound expressions for loading rates above which measurements should be valid.It is shown that,when subcritical crack growth is present,chevron-notched samples present advantages over more conventional precracked specimens.©2015The Authors.Published by Elsevier Ltd.This is an open access article under the CC BY license(/licenses/ by/4.0/).Keywords:Fracture toughness;Slow crack growth;Chevron notch;Load control;Loading rate1.IntroductionCeramics,with even partial ionic bonding character,can besusceptible to slow crack growth(SCG)both in ambient andcorrosive environments.SCG is a phenomenon in which a crackinside a stressed material advances at afinite velocity eventhough the stress intensity factor K at its tip is well below thecritical value,K c,for unstable rapid propagation.This is mostoften caused by a stress-dependent breaking of crack tip bondsassisted by interaction with a chemical species present in theenvironment,such as moisture in air[1].The resulting crack behavior can generally be expressed interms of a single-valued dependence of the crack advance ratev≡da/dt(where a is crack length and t is time)on the instan-taneous values of K and parameters describing the environmentand the material system.This dependence can be broadly catego-rized into several successive regimes;Fig.1sketches the typicalslow crack growth behavior,v(K),as documented for a wide∗Corresponding author.Tel.:+410216932913;fax:+410216934664.E-mail address:goran.zagar@epfl.ch(G.ˇZagar).1Present address:Department of Metallurgical Engineering and MaterialsScience,IIT Bombay,Powai,Mumbai400076,India.spectrum of materials and environments[2–6].This behavior is as follows.Below a threshold value,K0there is typically negligible crack advance.Just beyond K0,in Region I,crack propaga-tion is limited by stress-assisted reaction kinetics at the crack tip.The rate of crack advance is then generally linked with the stress-intensity factor via a power law,v=AK n(1) where A and n are constants specific to the material and atmo-sphere at hand.At higher K,in Region II,the crack growth rate becomes limited by the maximal transport rate of reacting species to the crack tip.This causes da/dt to plateau past K=K T at a relatively constant value v T(in many systems there is a slight ascending slope in this region too;however,it is much lower than in Region I and therefore is often neglected).As K increases further and approaches the critical stress intensity fac-tor,K c,the rate of crack advance accelerates rapidly to very high velocities;this is Region III where fast fracture,independent of the environment,occurs.Beyond its many consequences in engineering design and materials performance,the phenomenon has implications in materials testing:slow crack growth is well known to potentially/10.1016/j.jeurceramsoc.2015.04.0040955-2219/©2015The Authors.Published by Elsevier Ltd.This is an open access article under the CC BY license(/licenses/by/4.0/).3156G.ˇZagar et al./Journal of the European Ceramic Society 35(2015)3155–3166Fig.1.Schematic representation of crack velocity (v )dependence on the stressintensity factor (K )in SCG (dashed curve).Below the threshold K 0,crack growth rates are negligible.In Region I,the crack growth follows a power law,v =AK n .Region II begins at K =K T and is characterized by a weak dependence of v on K .In Region III,K ∼=K c and sample failure is catastrophic.Simplification brought here to this behavior is shown by solid (red)lines.affect the measurement of fracture toughness.This question has been addressed by several authors,starting with seminal papers by Evans and Johnson addressing the effect in samples con-taining through-thickness cracks [7],and later by a few other authors in the context of samples containing straight-through cracks [8]and chevron notches [9–12].In these analyses it was shown that SCG can cause what appears to be a valid measure-ment of the critical intensity factor for fast fracture,K c ,to be significantly underestimated because the actual crack length at instability exceeds by an unknown amount what it would be in the absence of SCG.Strategies exist to minimize or eliminate the problem in some cases,such as testing in artificial environments,e.g.,silicone oil [13,14]or inert gas [15].Such methods are,however,not fail-proof;for example,slow crack growth has been observed with samples immersed in oil [16].Also,testing in inert or liquid envi-ronments can be impractical,notably when conducting micro-or nano-tests [17]using nano-indentation instruments or within an electron microscope [18].In such tests,enclosing the sam-ples in inert gas is difficult,while immersion in a wetting liquid such as oil is not an option,as this might cause contamination and possible damage to the testing apparatus.There are,thus,many situations (especially for microscopic sample sizes)where fracture toughness testing must be conducted in the presence of SCG.The main objective of this study is to systematically outline how and when SCG will,or will not,corrupt results of a fracture toughness test conducted under load-control.We cast solution of the problem into a simple adimensional graphical form that gives a visualization of the course of testing under different conditions of imposed loading rates,material properties and simplified v –K characteristics encompassing most ceramics.This is achieved by recognizing that,under steady increasing load,time and load are in essence the same variable.One can then formulate the course of crack advance in two different scenarios,namely:(i)the load is the sole driving force for crack advance (i.e.cracking progresses at fixed K =K c )and (ii)the crack can also be driven by slow crack growth processes.On this basis,we then tackle the influence of SCG for samples with a straight-through crack,or a chevron-notch.As an outcome of the analysis we derive criteria for which a toughness test should,in practice,give a reasonably accurate measure of K c .Provided basic v –K characteristics of the material in the relevant environment (e.g.,ambient air,silicone oil or inert gas)have been either determined experimentally or can be esti-mated or bounded,and provided testing is conducted under load control,the approach is quite general and can be transposed to other sample geometries,or can be extended to deal with added features such as R -curve behavior (see Appendix A ).Comparing a few (standard)sample geometries,the analysis finally leads to conclude that,when SCG is present,chevron-notched samples present advantages in testing for K c under load control,which make it attractive for miniaturized toughness tests conducted with microscopic specimens.2.Problem formulation:short straight-through cracksWe simplify the usual SCG functional phenomenology,namely the v (K )behavior depicted in Fig.1,by making the following assumptions,summarized with the red curve in the figure:(i)we neglect the sub-threshold region,and thus take K 0=0because crack growth rates are negligible in this regime of low stress intensity factors [5];(ii)we take the crack growth rate in Region II to be a constant,v T ;(iii)we simplify the steeply rising dependence of v on K inRegion III by considering the crack propagation transition between Region II and Region III to be sharp.We do so because this transition is,generally,quite steep.Region I of the SCG regime is described by the usual power law,Eq.(1).Region II,in which the crack tip velocity plateausat da/dt =v T ,is reached at K =K T and thus v T =AK n T.Consider now a test specimen spanning length W along the crack path,having width B in the crack front direction,and con-taining a crack of initial length a i .We assume that the material is,for all practical purposes (meaning everywhere except at the very tip of the crack),linear elastic and isotropic.We assume no R -curve behavior:the resistance to sudden failure of the material is then independent of crack length and is measured by a simple scalar,namely its critical crack intensity factor,K c .This simpli-fies the derivation and its presentation;however,when dealing with the situation where the material exhibits R -curve behavior,meaning when K c is a function of (a −a i )where a is the instan-taneous crack length [19],the present analysis can be adapted;see Appendix A .Likewise,K T could also be taken to depend on crack length but for simplicity it will be taken to be constant.G.ˇZagar et al./Journal of the European Ceramic Society 35(2015)3155–31663157The instantaneous crack tip stress-intensity factor K (a )islinked to the sample compliance C by the well-known relation,K =P2b da ≡PB √WF (˜a)(2)where ˜a=a/W is the dimensionless crack length,E =E /(1−ν2)with E being the Young’s modulus and v the Poisson’s ratio of the material (we thus assume that the crack front is predominantly in plane strain),b is the instanta-neous width of the crack front and C is the sample compliance as a function of the crack length.The dimensionless function F (˜a )is a characteristic of the test sample configuration,and is directly given for common test samples in general references;e.g.[20].If we now consider a graph having as coordinates˜P≡PK c B √W(3)on the horizontal axis,and ˜a on the vertical axis,then the “fast fracture”curve traced by˜P=1F (˜a )(4)defines,for the sample in question,the locus where fast frac-ture is governed by purely stress-driven processes,as it occurs in a chemically inert environment at K =K c .Note that the fast fracture curve given by Eq.(4)depends only on the sample geometry.We assume,in all that follows,that monotonic loading is applied with a constant loading rate α(in Newtons per second)under load control,i.e.that P =αt .On a graph like this,any test conducted under monotonic loading with a fixed loading rate αis characterized by a crack trajectory that runs from left to right,along a horizontal line if there is no SCG,or along an ascending curve if slow crack growth occurs.When a particular crack trajectory intersects the curve traced by Eq.(4),say atPoint (˜P f ,˜a f ),then fast fracture processes drive crack growth.Depending on the slope of the fast fracture curve at Point (˜P f ,˜a f ),subsequent crack advancement occurs in one of the two manners.The first is stable crack growth,made possible when the fast fracture curve has a positive slope at the point of intersection:the crack then moves in a controlled way under the sole action of stress-driven crack tip processes along the fast fracture curve,at a rate that is equal to the slope of that curve times the rate at which the load increases with time,i.e .d ˜a/d ˜t =d ˜a/d ˜P·d ˜P/d ˜t .This can happen if the material exhibits R -curve behavior (see Appendix A ).Conversely,if the slope of the curvedescribed by Eq.(4)is infinite or negative at Point (˜Pf ,˜a f ),then unstable crack growth sets in and the sample breaks suddenly.We do not describe dynamic fracture here;hence,the entire region to the right of the curve described by Eq.(4)is out of consideration.On the same graph,the curve defined by˜P =˜K T F (˜a),(5)Fig.2.Dimensionless crack length ˜a in a straight-through,constant Y sample,versus dimensionless load ˜Paccording to Eqs.(10)and (11)for SCG kinet-ics characterized by n =10(solid),40(dashed)and 80(dash-dotted),and fordimensionless loading rates ˜α:10−2(red,square),10−1(blue,triangle),1(green,circle)and 10(magenta,diamond).Condition for fast fracture,given by Eq.(4),is shown by the thick black curve.The critical load in the absence of SCG is reached along a horizontal trajectory,at the point indicated with a star symbol (to the far right).The boundary between Regions I and II,given by Eq.(5),is shown as a thick gray curve.Parameters used in drawing this plot are:initialcrack size ˜ai =0.05,crack geometric factor Y =1.12√πand stress intensity factor ratio K T /K c =0.5.with ˜KT =K T /K c ,defines the locus where SCG transits from Region I to Region II.Since the SCG rate in Region II is a constant (v T ),all crack trajectories on the graph within Region II,and hence in the area situated between the two homothetic curves described by Eqs.(4)and (5),are straight lines of identical sloped ˜a d ˜P=1˜α(6)where ˜αis a normalized loading rate defined as ˜α=α√W/(v T BK c ).To the left of the curve described by Eq.(5),SCG occurs in Region I.Here,as shown by several authors [7,10–12],the crack length history must be derived by integrating Eq.(1).If expressed in dimensionless form,Eq.(1)can be written as,d ˜a d ˜P =1˜α˜K n T [F (˜a )˜P ]n (7)and can be solved by separation of variables and integration,i.e.˜a ˜a idx [F (x )]n =1˜α˜K n T ˜Pn +1n +1(8)For illustration,Fig.2describes the case of an advancingcrack such thatF (˜a)=Y √˜a,(9)where the geometrical factor Y is constant;such is the case fora short straight-through crack with Y =1.12√π.This simpli-fies calculations;however,qualitatively all the results obtained in what follows for this simple configuration represent the trends of a wide group of specimens whose F (˜a )is a monotonically3158G.ˇZagar et al./Journal of the European Ceramic Society 35(2015)3155–3166increasing function of ˜a :single edge notched tension (SENT),single edge notched beam (SENB),double cantilever beam (DCB),center cracked tension (CCT),double edge notched tension (DENT)or compact specimen (CS)geometries [20].With simple straight-through cracks,rapid fracture occurs where ˜P=1/(Y √˜a )(black curve in Fig.2).The boundary between SCG Regions I and II is given by the curve ˜P =˜K T /(Y √˜a )(gray curve in Fig.2).To the left of this boundary,i.e.in Region I,with Y constant,crack trajectories obey:˜a =(˜a i )2−n 2+2−n 2(n +1)Y n ˜α˜K n T˜P (n +1) 22−n,(10)where ˜ai =a i /W is the normalized initial (short)crack length.Eq.(10)corresponds to Eq.(5)of Evans and Johnson [7],which was derived with the same assumptions as here including constant Y ,but with the slight difference that equations were expressed in terms of applied stress rather than load.In Region II the crack trajectories run along straight lines,described in normalized coordinates by:˜a =˜a T +(˜P−˜P T )˜α(11)where ˜P T and ˜a T are respectively the load and the crack lengthat the boundary between Regions I and II;their values can be determined by combining Eqs.(5)and (10)at ˜a =˜a T .A few examples of complete SCG trajectories,for several values of thedimensionless loading rate ˜αand SCG exponent n ,are shown in Fig.2.The slope of the fast fracture curve for this simple straight-through crack case is always negative;thus,instability in such samples will always take place at the intersection of the crack growth trajectory with the fast fracture curve.This,of course,is a well-known characteristic of all straight-through crack samples.If,however,the material displays R -curve behavior,then the thick black curve in Fig.2may show a region of positive slope.As is well known,this makes stable crack growth a possibility even in the absence of a reactive species in the environment (see Appendix A ).As seen in Fig.2,for high enough ˜αthe crack remains sta-tionary until final fracture occurs at ˜P c =1/F (˜a i ).Alternatively,when the loading rate ˜αis small,the crack can suddenly accel-erate after lingering for a while,causing what appears as suddenfracture to occur at a value of ˜Pf that is well below ˜P c .There-fore,for small enough ˜α,SCG can bias results of a toughness test to give values that seem sound,yet are significantly lower than K c .For practical purposes,thus,it is instructive to have acriterion for the minimum loading rate ˜αthat will ensure that SCG effects are not significant.To arrive at such a criterion,we quantify the influence of SCG in terms of a confidence parameter ηP .Let us take the effect of SCG on a measurement of K c to be acceptably small if the loadat which sudden fracture of the sample occurs is ˜Pf =ηP ˜P c ,where ηP is a confidence parameter near unity,e.g.ηP =0.95.For the simplified SCG behavior adopted above (solid red curvein Fig.1),the minimum loading rate ˜αthat satisfies ηP =0.95is solved numerically using Eqs.(10)and (11)in terms oftheFig.3.Minimum dimensionless loading rate required for measurement of thefracture toughness with load confidence ηP =0.95for samples such that F (˜a )=Y √˜awith Y constant,given as a function of the SCG exponent n .Solid curves give the “exact”minimum loading rates obtained via numerical calculations by considering SCG kinetics in both Regions I and II.The corresponding minimum loading rates according to Eq.(12)are plotted with dashed lines.Minimum loading rate from Eq.(13)is plotted as the dash-dotted curve.The parameters˜a i and Y are the same as in Fig.2(˜ai =0.05,Y =1.12√π).SCG exponent n and for several values of the parameter ˜KT ;results are given as solid curves in Fig.3.The calculation is not very complicated;however,simpler criteria would be more convenient.We thus lay out two simple,analytically tractable albeit more conservative criteria that give a rapid prediction of aminimum loading rate ˜αfor valid toughness measurement with this sample configuration.The first criterion can be obtained by ignoring Region II and under the simplification that slow crack growth is governed only by the power law in Eq.(1)[10,12].In this case,Eq.(10)yields the condition˜αI ≥ηn +1P[ηn −2P−1]Y ˜a 3/2i˜K n T2−n2(n +1)(12)which is conservative,since by replacing the constant v T orRegion II by the power law dependence of Region I,the crackvelocities for ˜K>˜K T are (at times grossly)overestimated.The criterion obviously becomes gradually less conservative as ˜KT →1.As seen,due to the power law nature of the crack growth law and the generally high exponents,the overestima-tion can be quite large (dashed ˜KT =0.5and ˜K T =0.7curves in Fig.3).This limits interest in the practical application of Eq.(12)to cases where ˜KT values are very near the upper limit,i.e .,to ˜KT ≈1.Another,often more interesting,conservative estimate is obtained if we conversely consider that slow crack growth occurs only according to kinetics of Region II,i.e .at constant speed v T over the full range of K values.Then,the crack trajectory sim-ply follows ˜a =˜a i +˜P/˜αover its entire slow growth history.For given ηP we then find the general condition:˜αII ≥˜P f ˜a f −˜a i =ηP ˜Pc F −1[1/(ηP ˜P c )]−˜a i,(13)G.ˇZagar et al./Journal of the European Ceramic Society 35(2015)3155–31663159Fig.4.Dimensionless crack length ˜a in a straight-through SENB sample (threepoint bending setup with the span S /W =4)according to Eq.(14)vs .the dimen-sionless load for SCG kinetics characterized by n =10(solid),40(dashed)and80(dash-dotted),and for dimensionless loading rates ˜α:10−2(red,square),10−1(blue,triangle),1(green,circle)and 10(magenta,diamond).Condition for fast fracture,given by Eq.(4),is shown by the thick black curve.The critical load in the absence of SCG is reached along a horizontal trajectory,at the point indicated with a star symbol (to the far right).The boundary between Regions I and II,given by Eq.(5),is shown as a thick gray curve.Parameters used in drawing this plot are:initial crack size ˜a i =0.45and stress intensity factor ratio K T /K c =0.75.where F −1is the inverse function of F (˜a ).Because now the crackspeed is overestimated for ˜K <˜K T ,the condition given in Eq.(13)becomes less conservative when ˜KT is low,as indicated in Fig.3by the convergence,as ˜KT decreases,of solid curves (exact solutions for the minimum ˜α)toward the dash-dotted (black)curve.If ˜K T ≤∼0.75,Eq.(13)gives a much more relevant (i.e .,significantly lower)estimate of the minimum loading rate ˜αthan does Eq.(12),over the full range of considered SCG exponent n values.3.Standard fracture test specimensThe analysis is easily extended to other straight-through sample geometries:the only change is a somewhat more compli-cated function F (˜a ).Note also that,while Eq.(12)was derived specifically for samples such that F (˜a)=Y √˜a with constant Y =1.12√π,Eq.(13)is a general expression that is easily applied to any sample geometry.To illustrate this,in Figs.4and 5we show results that are similar to those in Figs.2and 3,respectively,but for a more realistic SENB specimen in a three point bending setup witha span ˜S=S/W =4.This is characterized by the geometrical function [20,21],F SENB (˜a )=3˜S√˜a 2(1+2˜a )(1−˜a )3/2{1.99−˜a (1−˜a )×[2.15−3.93˜a+2.7˜a 2]},(14)where the initial crack length ˜ai =0.45and for the material with ˜K T =0.75(resembling in this regard fused silica at relative humidity of ∼70%[22]).General steps of the analysis,for this or other sample geometries,are asfollowsFig.5.Minimum dimensionless loading rate required for measurement of the fracture toughness with load confidence ηP =0.95for the same SENB sample as in Fig.4,given as a function of the SCG exponent n .Solid curves give the “exact”minimum loading rates obtained via numerical calculations by considering SCG kinetics in both Regions I and II.Minimum loading rate from Eq.(13)is plotted as the dash-dotted curve.Parameter ˜a i is the same as in Fig.4.(i)Given F (˜a ),the fast fracture curve and the boundarybetween Regions I and II (Eqs.(4)and (5)respectively),are drawn on a plot of ˜aversus ˜P .(ii)Then,from Eq.(8),crack trajectories are computed anddrawn starting from (0,˜a i )up to the end of Region I,i.e.where the trajectory hits the curve described by Eq.(5),for several values of the loading rate ˜α.In Region II,those curves are continued with a fixed slope 1/˜α(equal to the tangent of the line from Region I at that point)all the way up to the fast fracture curve (given by Eq.(4)).These crack trajectories through Regions I and II simply give,in dimen-sionless coordinates,the crack tip history for the sample geometry in question according to the adopted simplified kinetics of SCG.The intersection point of the SCG trajec-tory with the fast fracture curve determines the measuredload ˜P f and crack length ˜a f at final fracture.(iii)The apparent fracture toughness,K f ,and the relativeerror,˜K f ,can then be directly computed:˜K f =K f /K c =˜P f F (˜a i ).We next apply this line of reasoning to the interesting case of chevron-notched samples.4.Chevron-notched samplesThe typical chevron-notched specimen is subjected to Mode I loading normal to a narrow slot that is selectively machined to ensure that the crack surface remains triangular (or has a shape close thereto;what follows is easily adapted to other near-triangular chevron configurations).Standard parameters that describe the geometry of a chevron-notched sample,namely Configuration B prescribed by ASTM Standard C1421-10[21],are shown in Fig.6.Besides driving the crack to travel under conditions close to plane strain,the thin chevron notch also promotes the sponta-neous initiation of a sharp crack under small to moderate loading,3160G.ˇZagar et al./Journal of the European Ceramic Society35(2015)3155–3166Fig.6.(a)A chevron-notched beam specimen(Configuration B)as recom-mended for fracture toughness evaluation of ceramic materials in a three-pointbending setup according to ASTM C1421-10[21].B is the width of the specimen,W is its length along the crack trajectory and S=6.3W is the span of a three-pointbending setup.The relative crack length˜a=a/W at any time is measured fromthe specimen notched face,while˜a0=a0/W=0.40and˜a1=a1/W=0.95 are the relative distances from the specimen notched face to the apex and thebottom of the triangle,respectively.The crack front width is,for a straight sym-metric crack front across a triangular notch,b/B=(˜a−˜a0)/(˜a1−˜a0).(b)The dimensionless compliance function C v(˜a)(red squares)leading to the charac-teristic function F v(˜a)(blue solid curve)for this chevron-notched specimen was obtained via a series offinite element calculations assuming linear elasticity and a straight crack front of width b[26,38].The minimum of F v(˜a)at˜a=˜a M indicated by the blue star,is the value used to compute the fracture toughness of a brittle linear elastic material in the absence of SCG.at the apex of the triangle,where the level of stress concentration is high.Thus,chevron-notched specimens do not,in principle, require any precracking(this said,in practice crack initiation can be an issue;also,as will be seen below,crack initiation has interesting consequences on the potential influence of SCG in a chevron notched specimen test).Provided the crack initiation load is sufficiently low,further crack advance is ensured under increasing load with an expand-ing crack front b(Fig.6).This leads to a characteristic function F≡F v of the form:F v(˜a)=B2bdC vd˜a=12˜a1−˜a0˜a−˜a0dC vd˜a.(15)Here C v is the dimensionless compliance,a function of the crack length˜a that is related to the(dimensional)sample com-pliance C by C v=EBC/(1−ν2).The dimensionlesscompliance Fig.7.Plot of the SCG trajectories calculated according to Eqs.(7)and(11)for a chevron-notched sample(Configuration B in ASTM C1421-10[21],Fig.6), and for SCG kinetics characterized by exponents n=10(solid),40(dashed)and 80(dash-dotted)and dimensionless loading rates˜α:10−2(red,square),10−1 (blue,triangle),1(green,circle)and10(magenta,diamond).The fast fracture border corresponding to Eq.(4)is shown as a thick black curve,while the point of instability in the absence of SCG is indicated with a star symbol(and corresponds to the minimum in Fig.6b).The boundary between Regions I and II,given by Eq.(5),is shown with a thick gray curve.Parameters used in drawing this plot are:initial crack size˜a i=0.45and stress intensity factor ratio K T/K c=0.5. C v and its derivative,dC v/d˜a,are both monotonically increasingfunctions of˜a.Because the crack front b also increases as the crack advances, the characteristic function F v(˜a)of an appropriately designed chevron-notched sample exhibits a minimum at a certain inter-mediate crack length˜a0<˜a M<1.To give an example,curves of C v and F v valid for the standard ASTM sample,together with values for˜a M and minima F v(˜a M),are plotted in Fig.6. In the˜P−˜a graph introduced previously,curves traced by Eqs.(4)and(5)for a chevron-notched specimen(thick black and gray curves in Fig.7,respectively),start with a positive slope, before turning around and then showing a negative slope for crack lengths˜a>˜a M.With a steadily increasing load and in the absence of SCG,the minimum of Eq.(15),F v(˜a M)corresponds to the critical(max-imal)force˜P c and signals a transition from stable to unstable crack propagation[23].When SCG is absent,therefore,any crack in the chevron notch of initial length˜a i<˜a Mfirst traces a horizontal trajectory up to the fast fracture border defined by Eq.(4).Then it continues to travel,in stable fashion,along the positive slope portion of the(thick black)fast fracture curve up to Point(˜P c,˜a M),whereupon it becomes unstable and suddenly cuts the sample in two.Measuring the fracture toughness K c of a brittle material in the absence of SCG requires a compliance–calibration curve for the relevant chevron-notched specimen geometry,so that one can calculate F v(˜a M).With this information at hand,and provided that a crack during the test is nucleated at sufficiently low load,i.e.that the nucleated crack length˜a i is below˜a M, and that the crack front b remains straight,then the material’s fracture toughness K c can be computed via Eq.(2)by measuring only the maximum load at fracture,˜P f[21,23–28].。