高线表面质量缺陷的产生原因及排除方法
高速线材产品表面“裂纹”成因及判定
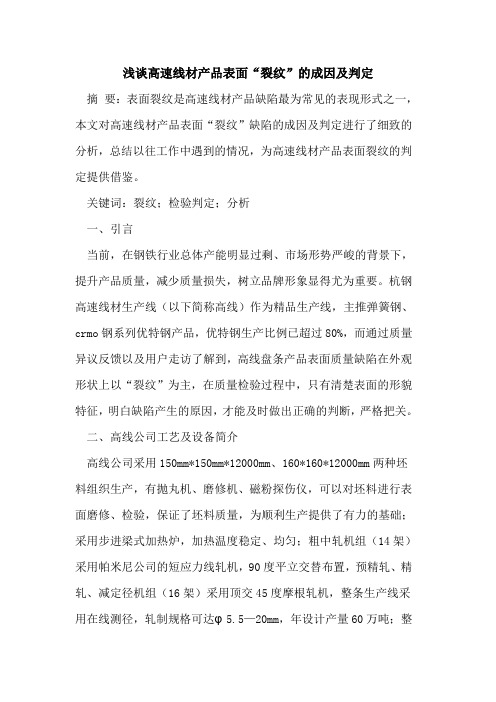
浅谈高速线材产品表面“裂纹”的成因及判定摘要:表面裂纹是高速线材产品缺陷最为常见的表现形式之一,本文对高速线材产品表面“裂纹”缺陷的成因及判定进行了细致的分析,总结以往工作中遇到的情况,为高速线材产品表面裂纹的判定提供借鉴。
关键词:裂纹;检验判定;分析一、引言当前,在钢铁行业总体产能明显过剩、市场形势严峻的背景下,提升产品质量,减少质量损失,树立品牌形象显得尤为重要。
杭钢高速线材生产线(以下简称高线)作为精品生产线,主推弹簧钢、crmo钢系列优特钢产品,优特钢生产比例已超过80%,而通过质量异议反馈以及用户走访了解到,高线盘条产品表面质量缺陷在外观形状上以“裂纹”为主,在质量检验过程中,只有清楚表面的形貌特征,明白缺陷产生的原因,才能及时做出正确的判断,严格把关。
二、高线公司工艺及设备简介高线公司采用150mm*150mm*12000mm、160*160*12000mm两种坯料组织生产,有抛丸机、磨修机、磁粉探伤仪,可以对坯料进行表面磨修、检验,保证了坯料质量,为顺利生产提供了有力的基础;采用步进梁式加热炉,加热温度稳定、均匀;粗中轧机组(14架)采用帕米尼公司的短应力线轧机,90度平立交替布置,预精轧、精轧、减定径机组(16架)采用顶交45度摩根轧机,整条生产线采用在线测径,轧制规格可达φ5.5—20mm,年设计产量60万吨;整条轧线设置有3把飞剪,起到剪切头尾及故障时的剪碎的作用,同时配备5段冷却水箱,控制轧件温度;散卷冷却采用斯泰尔摩控制冷却线,最后通过集卷机集卷后上p/f输送线,完成打包、称重、贴牌入库。
主要工艺流程如下:坯料准备→入炉、加热→出炉→高压水除鳞→粗轧→1#飞剪→中轧→2#飞剪→预精轧→1#水箱→3#飞剪→精轧→2、3#水箱→减定径→涡流探伤→4#水箱→测径仪→5#水箱→吐丝机→斯泰尔摩运输线→集卷→p/f输送线→检验、取样、切头尾→打捆→称重、挂牌→入库三、缺陷分布及检验情况高线盘条产品涉及16个规格,40多个钢种,以弹簧钢、crmo类钢等优特钢为主。
棒线材表面缺陷产生原因及消除方法

棒线材表⾯缺陷产⽣原因及消除⽅法线材⽿⼦产⽣原因及消除⽅法线材表⾯沿轧制⽅向的条状凸起称为⽿⼦,有单边⽿⼦也有双边⽿⼦。
⾼速线材轧机⽣产中由于张⼒原因,产品头尾两端很难避免⽿⼦的产⽣。
有下述情况时容易产⽣⽿⼦:(1)轧槽与导卫板安装不正;(2)轧制温度的波动较⼤或不均匀较严重,影响轧件的宽展量;(3)坯料的缺陷,如缩孔、偏析、分层及外来夹杂物,影响轧件的正常变形;(4)来料尺⼨过⼤。
预防及消除⽅法如下:(1)正确安装和调整⼊⼝导卫;(2)提⾼钢坯加热质量,控制好轧制温度;(3)合理调整张⼒;(4)控制来料尺⼨。
线材表⾯的凸起及压痕(轧疤)形成的原因线材表⾯连续出现周期性的凸起或凹下的印痕,缺陷形状、⼤⼩相似。
凸起及压痕主要是轧槽损坏(掉⾁或结瘤)造成的。
线材产品检验项⽬及影响尺⼨精度的主要因素线材产品检验包括六项内容:外形尺⼨,压扁实验,含碳量⽐较,快速碳分析,⼒学性能试验和⾼倍检验。
影响线材尺⼨精度有以下主要因素:有温度、张⼒,孔型设计、轧辊及⼯艺装备的加⼯精度、孔槽及导卫的磨损、导卫板安装和轧机的机座刚度、调整精度、轧辊轴承的可靠性和电传控制⽔平和精度等。
其中张⼒是影响线材产品尺⼨精度的最主要因数。
在轧制线材的过程中尽可能实现微张⼒或⽆张⼒轧制是⾼速线材轧制的宗旨。
孔型设计与轧件精度也有密切关系,⼀般讲椭圆—⽴椭圆孔型系列消差作⽤⽐较显著;⼩辊径可以减少宽展量,其消差作⽤⽐⼤辊径好。
孔型设计中应特别注意轧件尺⼨变化后的孔型适应性,即变形的稳定性、不扭转不倒钢不改变变形⽅位。
线材裂纹产⽣的原因及预防⽅法裂纹在线材中的分布是不连续的,垂直于线材表⾯或呈⼀⾓度陷⼊线材。
裂纹长短不⼀,通常呈直线形,偶尔也有横向裂纹或龟裂。
由钢坯上的缺陷经轧制后形成的裂纹常伴有氧化质点、脱碳现象,裂纹中间常存在氧化亚铁;由轧后控冷不当形成的裂纹⽆脱碳现象伴⽣,裂缝中⼀般⽆氧化亚铁,多呈横裂或龟裂。
从炼钢到轧钢都有可能产⽣裂纹。
高线表面质量缺陷的产生原因及排除方法

高速线材表面质量缺陷的产生原因及排除方法摘要:对高速线材常见表面质量缺陷裂纹、折叠、耳子、划痕等进行了原因分析,并提出了相应排除方法。
关键词:高速线材、表面质量缺陷、原因分析、排除方法。
概述:在高速线材的生产中,成品的表面缺陷是影响产品质量的一个重要因素,其大致有以下几种:裂纹、折叠、耳子、划痕、碳化钨辊环的破裂和掉肉、麻面、结疤(翘皮或鳞皮)。
2原因分析及排除方法2.1裂纹裂纹是指线材表面沿轧制方向有平直或弯曲、折曲,或以一定角度向线材内部渗透的缺陷。
裂纹长度和深度不同,在线材的长度方向上都能发现。
有的裂纹内有夹杂物,两侧也有脱碳现象。
2.1.1线材表面产生裂纹的主要原因在于钢坯上未消除的裂纹(无论纵向或横向)、皮下气泡及非金属夹杂物都会在线材表面造成裂纹。
连铸坯上的针孔如不消除,经轧制被延伸、氧化、溶解就会造成成品的线状发纹。
针孔是连铸坯的重要缺陷之一,不显露时很难检查出来,应特别予以注意。
高碳钢线材轧制后冷却速度过快,也可能造成成品裂纹,后者还能出现横向裂纹。
轧后控冷不当形成的裂纹无脱碳现象伴生,裂纹中一般无氧化铁皮。
另外坯料清理不好也会产生此类问题。
轧制过程中形成裂纹的原因主要有以下几点:(1)轧槽不合适,主要是尖角和轧槽尺寸有问题。
(2)轧槽表面太粗糙或损坏。
(3)粗轧前几道导卫的划伤。
(4)粗大的氧化铁皮轧进轧件表面及内部,而且这通常在粗轧前几道产生。
(5)导卫使用不当主要是尺寸太大。
2.1.2若产生裂纹,应从以下几方面进行检查,排除故障:(1)高压水除鳞是否正常工作,是否某架轧机轧辊的冷却水路被堵塞或偏离轧槽。
(2)导卫是否偏离轧制线,有无氧化铁皮堵塞在某个导卫中。
(3)轧槽是否过度磨损或因处理堆钢事故时损伤了轧槽。
(4)精轧机是否有错辊,导卫是否对中及尺寸是否对应于所轧的规格。
2.2折叠线材表面沿轧制方向平直或弯曲的细线,以任意角度渗入线材的表面内,在横断面上与表面呈小角度交角状的缺陷多为折叠,通常折叠较长,但亦有间断的不连续的,并在线材的长度方向上都有分布,折处的两侧伴有脱碳层或部分脱碳层,折叠中间常存在氧化铁夹杂。
线材表面缺陷发生原因分析及其减少措施
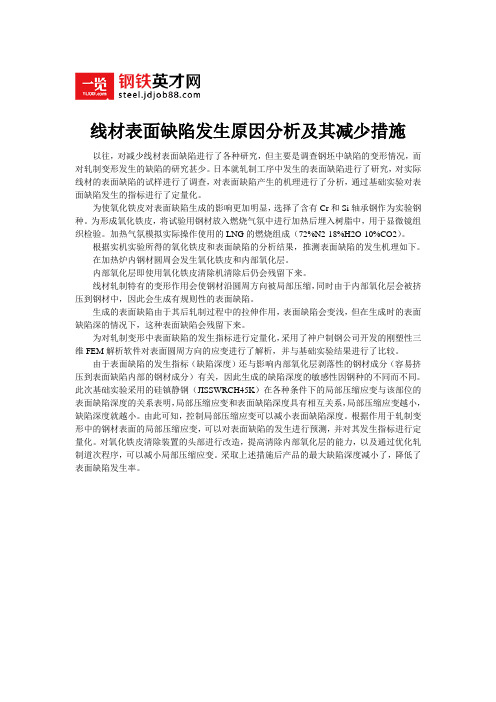
线材表面缺陷发生原因分析及其减少措施以往,对减少线材表面缺陷进行了各种研究,但主要是调查钢坯中缺陷的变形情况,而对轧制变形发生的缺陷的研究甚少。
日本就轧制工序中发生的表面缺陷进行了研究,对实际线材的表面缺陷的试样进行了调查,对表面缺陷产生的机理进行了分析,通过基础实验对表面缺陷发生的指标进行了定量化。
为使氧化铁皮对表面缺陷生成的影响更加明显,选择了含有Cr和Si轴承钢作为实验钢种。
为形成氧化铁皮,将试验用钢材放入燃烧气氛中进行加热后埋入树脂中,用于显微镜组织检验。
加热气氛模拟实际操作使用的LNG的燃烧组成(72%N2-18%H2O-10%CO2)。
根据实机实验所得的氧化铁皮和表面缺陷的分析结果,推测表面缺陷的发生机理如下。
在加热炉内钢材圆周会发生氧化铁皮和内部氧化层。
内部氧化层即使用氧化铁皮清除机清除后仍会残留下来。
线材轧制特有的变形作用会使钢材沿圆周方向被局部压缩,同时由于内部氧化层会被挤压到钢材中,因此会生成有规则性的表面缺陷。
生成的表面缺陷由于其后轧制过程中的拉伸作用,表面缺陷会变浅,但在生成时的表面缺陷深的情况下,这种表面缺陷会残留下来。
为对轧制变形中表面缺陷的发生指标进行定量化,采用了神户制钢公司开发的刚塑性三维FEM解析软件对表面圆周方向的应变进行了解析,并与基础实验结果进行了比较。
由于表面缺陷的发生指标(缺陷深度)还与影响内部氧化层剥落性的钢材成分(容易挤压到表面缺陷内部的钢材成分)有关,因此生成的缺陷深度的敏感性因钢种的不同而不同。
此次基础实验采用的硅镇静钢(JISSWRCH45K)在各种条件下的局部压缩应变与该部位的表面缺陷深度的关系表明,局部压缩应变和表面缺陷深度具有相互关系,局部压缩应变越小,缺陷深度就越小。
由此可知,控制局部压缩应变可以减小表面缺陷深度。
根据作用于轧制变形中的钢材表面的局部压缩应变,可以对表面缺陷的发生进行预测,并对其发生指标进行定量化。
对氧化铁皮清除装置的头部进行改造,提高清除内部氧化层的能力,以及通过优化轧制道次程序,可以减小局部压缩应变。
高速线材表面质量缺陷及控制措施
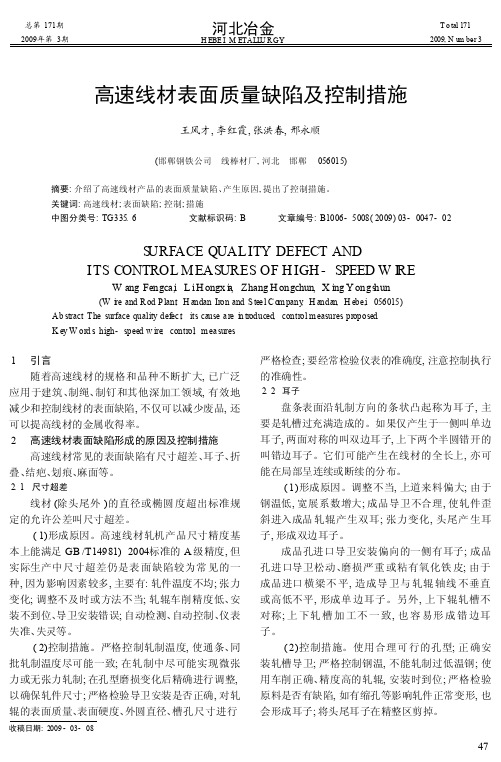
总第171期2009年第3期河北冶金H EBE I M ETALL U RGYT o tal1712009,N u m ber3收稿日期:2009-03-08高速线材表面质量缺陷及控制措施王风才,李红霞,张洪春,邢永顺(邯郸钢铁公司线棒材厂,河北邯郸056015)摘要:介绍了高速线材产品的表面质量缺陷、产生原因,提出了控制措施。
关键词:高速线材;表面缺陷;控制;措施中图分类号:TG335.6文献标识码:B文章编号:B1006-5008(2009)03-0047-02 S URF ACE QUALITY DEFECT ANDITS CONTROL MEAS URES OF H IGH-SPEED W I RE W ang Fengca,i L iH ongx i a,Zhang H ongchun,X ing Y ongs hun(W i re and R od P lan,t H andan Iron and S tee l C o m pany,H andan,H ebe,i056015)Ab strac:t The surface quality defec,t its cause a re i n troduced,control m easures proposed.K ey W ord s:high-speed w ire;contro;l m ea sures1引言随着高速线材的规格和品种不断扩大,已广泛应用于建筑、制绳、制钉和其他深加工领域,有效地减少和控制线材的表面缺陷,不仅可以减少废品,还可以提高线材的金属收得率。
2高速线材表面缺陷形成的原因及控制措施高速线材常见的表面缺陷有尺寸超差、耳子、折叠、结疤、划痕、麻面等。
2.1尺寸超差线材(除头尾外)的直径或椭圆度超出标准规定的允许公差叫尺寸超差。
(1)形成原因。
高速线材轧机产品尺寸精度基本上能满足GB/T14981)2004标准的A级精度,但实际生产中尺寸超差仍是表面缺陷较为常见的一种,因为影响因素较多,主要有:轧件温度不均;张力变化;调整不及时或方法不当;轧辊车削精度低、安装不到位、导卫安装错误;自动检测、自动控制、仪表失准、失灵等。
线材质量常见五大问题及措施.doc
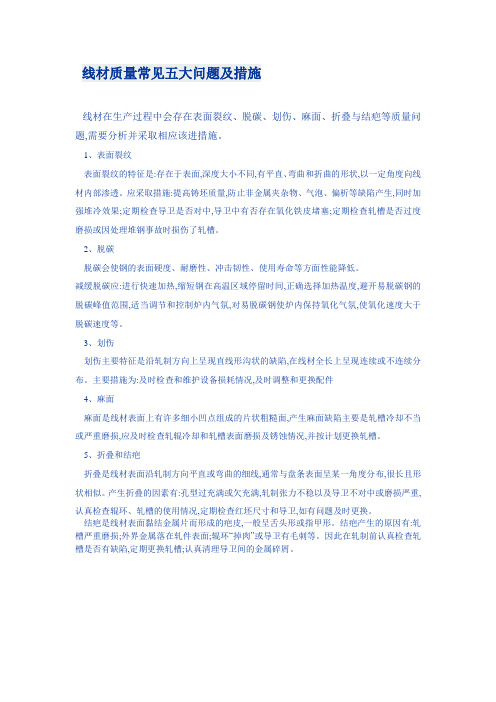
线材质量常见五大问题及措施线材在生产过程中会存在表面裂纹、脱碳、划伤、麻面、折叠与结疤等质量问题,需要分析并采取相应该进措施。
1、表面裂纹表面裂纹的特征是:存在于表面,深度大小不同,有平直、弯曲和折曲的形状,以一定角度向线材内部渗透。
应采取措施:提高铸坯质量,防止非金属夹杂物、气泡、偏析等缺陷产生,同时加强堆冷效果;定期检查导卫是否对中,导卫中有否存在氧化铁皮堵塞;定期检查轧槽是否过度磨损或因处理堆钢事故时损伤了轧槽。
2、脱碳脱碳会使钢的表面硬度、耐磨性、冲击韧性、使用寿命等方面性能降低。
减缓脱碳应:进行快速加热,缩短钢在高温区域停留时间,正确选择加热温度,避开易脱碳钢的脱碳峰值范围,适当调节和控制炉内气氛,对易脱碳钢使炉内保持氧化气氛,使氧化速度大于脱碳速度等。
3、划伤划伤主要特征是沿轧制方向上呈现直线形沟状的缺陷,在线材全长上呈现连续或不连续分布。
主要措施为:及时检查和维护设备损耗情况,及时调整和更换配件4、麻面麻面是线材表面上有许多细小凹点组成的片状粗糙面,产生麻面缺陷主要是轧槽冷却不当或严重磨损,应及时检查轧辊冷却和轧槽表面磨损及锈蚀情况,并按计划更换轧槽。
5、折叠和结疤折叠是线材表面沿轧制方向平直或弯曲的细线,通常与盘条表面呈某一角度分布,很长且形状相似。
产生折叠的因素有:孔型过充满或欠充满,轧制张力不稳以及导卫不对中或磨损严重,认真检查辊环、轧槽的使用情况,定期检查红坯尺寸和导卫,如有问题及时更换。
结疤是线材表面黏结金属片而形成的疤皮,一般呈舌头形或指甲形。
结疤产生的原因有:轧槽严重磨损;外界金属落在轧件表面;辊环“掉肉”或导卫有毛刺等。
因此在轧制前认真检查轧槽是否有缺陷,定期更换轧槽;认真清理导卫间的金属碎屑。
材料加工过程中常见缺陷形成原因和控制措施

材料加工过程中常见缺陷形成原因和控制措施在材料加工的过程中,常常会出现一些缺陷,这些缺陷可能会降低材料的性能和质量。
了解这些常见的缺陷形成原因以及相应的控制措施,对于提高材料加工的效率和质量至关重要。
一、表面缺陷1. 划痕和刮痕:这些缺陷通常是由于加工过程中使用的工具和设备表面不平整或硬度不足导致的。
此外,操作不当或过度力度也可能导致划痕和刮痕的形成。
控制措施包括使用平整且硬度适当的工具和设备,并合理控制力度和操作方式,避免划痕和刮痕的产生。
2. 锈斑和氧化:这些缺陷通常是由于材料受到氧气和水的侵蚀和反应导致的。
在加工过程中,应尽量避免材料长时间暴露在潮湿的环境中,同时使用防锈剂和表面处理技术可以有效地防止锈斑和氧化的形成。
3. 气泡和孔洞:这些缺陷通常是由于材料内部存在气体或液体,在加工过程中由于温度或压力的变化导致气体或液体无法逸出,从而形成气泡和孔洞。
控制措施包括材料预处理,如真空处理以去除内部气体,并且在加工过程中要合理控制温度和压力,防止气泡和孔洞的形成。
二、尺寸缺陷1. 偏差:加工过程中,由于工具磨损、设备不稳定或操作不准确等原因,会导致零件尺寸偏离设计要求。
控制措施包括定期检查和更换工具、维护设备的稳定性,并确保操作人员接受过专业的培训,提高操作的准确性。
2. 粗糙度:材料表面的粗糙度是加工过程中另一个常见的缺陷。
粗糙的表面可能会影响零件的质量和功能。
控制措施包括选择适当的加工方法和工艺参数,如切削速度、进给速度以及刀具和夹具的选择,以获得所需的表面质量。
三、组织缺陷1. 结晶缺陷:材料加工过程中,结晶缺陷的形成通常是由于材料的冷却速度过快或冷却不均匀导致的。
这些缺陷可能包括晶界偏大、晶界分布不均匀等问题。
为了减少结晶缺陷的形成,可以采取适当的冷却措施,如控制冷却速度和温度梯度,以及进行热处理等。
2. 晶粒长大不均匀:晶粒长大不均匀往往会导致材料的性能和力学性能降低。
控制措施包括合理选择和设计加工工艺,如适当的热处理和锻造工艺,以及控制加工温度、压力和时间等参数,以实现晶粒的均匀长大。
常见表面缺陷的预防与补救措施

常见表面缺陷的预防与补救措施常见表面缺陷的预防与补救措施涂覆膜层分三个类别:一.电镀膜层二.转化膜层(氧化、钝化、磷化)三.有机膜层(喷油、喷粉)一.电镀膜层一.电镀膜层6).脆性:镀层能受基体变形的能力,主要决定于材料应力.7).麻点:电镀层表面形成的小凹坑.8).海绵状:镀层与基体结合不牢固的疏松多孔的沉积物.9).斑点:镀层表面出现后斑点或污点.1 10).树枝状结晶:电镀时在阳极上(特别是边缘和其它高电流密度区)形成的粗糙/松散的树枝状或不规则突起的沉积物.二.转化膜层1). 1).烧损:在阳极氧化过程中,氧化膜层受到严重电击穿,铝局部损坏,或局部过热表面呈松软的粉状现象.2).封孔灰:表面封孔产生一层松软浮灰层.二.转化膜层3).起粉:膜层,疏松,附着不牢固.4).着色不均:颜色不均匀,发花.5).剥落:碎裂和附着力下降的现象.6).应力破裂:机械加工受热影响产生的内应变,膜层裂开.三.有机涂层缺陷1).起泡:涂层局部粘附不良引起涂膜浮起.2).针孔:涂层表面上以看见类似针刺成的微小孔.3).开裂:涂层出现不连续的外观开裂变化,通常由于涂层老化而引起的.4).剥落:一道或多道涂层脱离下涂层,或涂层完全脱离基材的现象7).厚边:靠基体的边缘或折弯角处的涂料堆积现象.三.有机涂层缺陷6).粉化:涂层表面由于一种或多种漆基的降解及颜料的分解而呈现出疏松附着细粉的现象.5).流挂:喷涂时涂层流动产生的堆积8).收缩:涂层干燥后仍滞留的若干大小不等,分布各异的圆形小坑现象.9).露底(漏涂区):局部无涂层或涂料覆盖不严等现象(常见于内折弯角处,孔的连缘截面,基材切口边缘截面等部位)二.常见缺陷产生原因.预防措施和补救措施起泡原因:1.电镀工艺配方有缺陷2.电镀溶液有污梁3.电镀前除油不彻底(前处理不干净)4.工序不完整.起泡预防:1.选择证明良好的配方2.严格管理维护镀液3.加强控制前处理4.完善工序.其中基材原因:选用不合适的材料,氢气量增加,氢脆造成.补救措施:无法补救,必须重镀 .二. 基材花斑原因:电镀前基材料产生严重锈蚀而出现,电镀后形成花斑.预防:对基材采取良好有效的工序间进行防腐蚀性措施.补救措施:基材粗糙而易镀层中产生微小缺陷.镀后无法补救,镀前可用机械方法消除(拉丝,打磨)三. 挂印原因:表面处理生产的必然的印迹现象.预防:补救是必然进行的,在挂印位置在工件内表面和B面必曾时增加工艺孔.补救措施:1.手工涂漆2.镀彩锌采用金色漆修补3.相同颜色漆作修补(其它金属)四. 黑点原因:有多种,各环节都有可能导致.1.基材中有不允许的杂质,有裂纹或小针孔.2. 钝化膜质量不良.3. 表面处理后因素:1).环境恶劣. 2).污染(汗液,胶水,气体腐蚀).4.搬运过程中划碰伤.四. 黑点预防:1. 选用合格的基体材料2. 机械加工过程中有保护措施.3. 处理后避免污染,选择良好的环境.4.加强电镀工艺,使钝化良好.五.基材晶粒粗大原因:金属材料(铝板)在轧制过程中出现问题 .预防:加强材料来料质量控制 .补救措施:无法补救,由于材料轧制时的工艺参数控制不良而产生的此种现象,导致性能发生变化.六.裂纹原因:多是因为材料本身的性能较差所决定或者折弯前材料表面有微小裂纹.预防:1.严格按照设计要求,采用性能延伸良好材料.2.避免微小深划痕迹(拉丝) .3.尽量避免拉丝、拉丝纹路与拆弯直线方向一致.补救措施:无法补救,表面处理前进行补救,封严或扩大开口.七.露白原因:1.溶液截留而滞后腐蚀导致,如缝隙,微孔,裂纹,压铆缝隙,盲孔.2.因磨擦磨损导致.预防:1.控制焊缝质量及夹缝大/小。
- 1、下载文档前请自行甄别文档内容的完整性,平台不提供额外的编辑、内容补充、找答案等附加服务。
- 2、"仅部分预览"的文档,不可在线预览部分如存在完整性等问题,可反馈申请退款(可完整预览的文档不适用该条件!)。
- 3、如文档侵犯您的权益,请联系客服反馈,我们会尽快为您处理(人工客服工作时间:9:00-18:30)。
高速线材表面质量缺陷的产生原因及排除方法
摘要:对高速线材常见表面质量缺陷裂纹、折叠、耳子、划痕等进行了原因分析,并提出了相应排除方法。
关键词:高速线材、表面质量缺陷、原因分析、排除方法。
概述:在高速线材的生产中,成品的表面缺陷是影响产品质量的一个重要因素,其大致有以下几种:裂纹、折叠、耳子、划痕、碳化钨辊环的破裂和掉肉、麻面、结疤(翘皮或鳞皮)。
2原因分析及排除方法
2.1裂纹
裂纹是指线材表面沿轧制方向有平直或弯曲、折曲,或以一定角度向线材内部渗透的缺陷。
裂纹长度和深度不同,在线材的长度方向上都能发现。
有的裂纹内有夹杂物,两侧也有脱碳现象。
2.1.1线材表面产生裂纹的主要原因在于钢坯上未消除的裂纹(无论纵向或横向)、皮下气泡及非金属夹杂物都会在线材表面造成裂纹。
连铸坯上的针孔如不消除,经轧制被延伸、氧化、溶解就会造成成品的线状发纹。
针孔是连铸坯的重要缺陷之一,不显露时很难检查出来,应特别予以注意。
高碳钢线材轧制后冷却速度过快,也可能造成成品裂纹,后者还能出现横向裂纹。
轧后控冷不当形成的裂纹无脱碳现象伴生,裂纹中一般无氧化铁皮。
另外坯料清理不好也会产生此类问题。
轧制过程中形成裂纹的原因主要有以下几点:
(1)轧槽不合适,主要是尖角和轧槽尺寸有问题。
(2)轧槽表面太粗糙或损坏。
(3)粗轧前几道导卫的划伤。
(4)粗大的氧化铁皮轧进轧件表面及内部,而且这通常在粗轧前几道产生。
(5)导卫使用不当主要是尺寸太大。
2.1.2若产生裂纹,应从以下几方面进行检查,排除故障:
(1)高压水除鳞是否正常工作,是否某架轧机轧辊的冷却水路被堵塞或偏离轧槽。
(2)导卫是否偏离轧制线,有无氧化铁皮堵塞在某个导卫中。
(3)轧槽是否过度磨损或因处理堆钢事故时损伤了轧槽。
(4)精轧机是否有错辊,导卫是否对中及尺寸是否对应于所轧的规格。
2.2折叠
线材表面沿轧制方向平直或弯曲的细线,以任意角度渗入线材的表面内,在横断面上与表面呈小角度交角状的缺陷多为折叠,通常折叠较长,但亦有间断的不连续的,并在线材的长度方向上都有分布,折处的两侧伴有脱碳层或部分脱碳层,折叠中间常存在氧化铁夹杂。
2.2.1坯料中如存在缩孔、偏析、夹杂等缺陷,或者坯料修整不好都有可能产生类似折叠的缺陷。
轧制中可能产生折叠的原因有:
(1)孔型中过充满是折叠产生的主要原因。
(2)机架间张力太大也是产生折叠的原因之一。
(3)导卫对中不好可出现单侧充满从而造成折叠。
(4)轧机调整不当,轧件尺寸不对或导卫磨损严重也可能产生间断折叠。
(5)坯料加热温度不均匀。
2.2.2若产生折叠,应从以下几方面进行检查,排除故障:
(1)检查轧辊冷却,粗轧机中氧化铁皮堆积过多也可能是产生间断折叠的原因。
(2)是否有某个导卫偏离了轧制中心线引起过充满。
(3)导卫不正常,检查滑动导卫中是否有异物堆积,滚动导卫中导辊是否正常。
(4)通过轧机的轧件尺寸是否正确,是否过充满。
(5)检查张力情况。
检查坯料出炉温度,沿坯料长度上温度不均也可导致间断性过充满。
2.3耳子
线材表面沿轧制方向的凸起称为耳子,主要是轧槽过充满造成的。
坏料中如存在缩孔,偏析和夹杂等缺陷,会在轧制时导致轧件过充满。
2.3.1轧制中可能产生耳子的原因有:
(1)轧件尺寸不正确或辊缝调节不当。
(2)张力过大,导致线材头尾出现耳子。
(3)成品轧机上导卫对中不好或调整不当。
(4)坯料温度不均匀,高温段成品尺寸合适,而低温段则出现耳子。
(5)轧件抖动会产生断续耳子,一段在线材的一侧,另一段在线材的另一侧。
2.3.2若产生成品出耳子,应从以下几方面进行检查,排除故障:
(1)精轧机组入口轧件尺寸必须正确。
(2)工作辊径搭配,辊缝设定正确也很重要。
(3)检查轧机中的张力条件,如果速度适当,入口轧件和工作辊径正确,则精轧机中的张力应当是很小的。
(4)如果只是在线材一侧有耳子,则检查成品轧机入口导卫对中、对正是否良好。
(5)如果要消除轧件抖动现象,需进行检查并做到以下几点:精轧机组的辊环工作直径正确,入口轧件尺寸正确;辊缝调节正确;导卫调节正确;使用减震导卫;若钢种变化,轧件的宽展量也会变化,应做相应调整。
2.4划痕
划痕是线材表面沿长度方向上像沟的缺陷,其形状和大小各不相同,有的划痕沟侧有翻起的重叠边,也有很小的尖裂纹像划痕,划痕主要是成品通过有缺陷的设备,如导卫、活套、水冷箱、夹送辊、吐丝机、散卷输送线、集卷器及打捆机造成的。
2.4.1在轧制过程中产生划痕的原因有以下几方面:
(1)导卫中有堆积物。
(2)导卫安装不当或导辊断裂。
(3)导卫有毛刺。
(4)轧机的对中性不好,或导卫对中性不好。
(5)导卫开口度较大。
2.4.2轧件若产生划痕,应从以下几方面进行检查,排除故障:
(1)每次轧机停机以后要进行检查,通常要检查每个机架上的导卫,在
检查时有必要用手电筒照明以便观察清楚。
(2)孔型或导卫对中性不好是产生划痕的最常见的原因,要定期检查。
2.5碳化钨辊环的破裂和“掉肉”
碳化钨辊环裂纹通常会在线材表面形成周期性缺陷,有时会在线材表面形成发纹,辊环“掉肉”有时会在线材的表面形成凸块或结疤。
2.5.1碳化钨辊环的破裂和“掉肉”形成原因有:
(1)由于碳化钨辊环的自身特性,冷却不当很容易断裂。
(2)辊环轧槽中的“掉肉”可能是由于冷却不当、辊环磨槽技术不当等造成。
(3)冷却水的酸碱度不合适。
2.5.2若产生碳化钨辊环的破裂和“掉肉”,应从以下几方面进行检查,排除故障:
(1)每次停机时都应检查辊环的使用情况,如果轧槽表面过早的剥落,应立即分析调查其原因。
(2)在运输与搬运时要小心轻放,要有适当的运输和存放工具。
(3)线材表面如存在凸块或结疤,则要测量从一个凸块或结疤到下一凸块或结疤的间距,以确定出现故障的架次。
(4)如果工作辊环或导卫中有剥落,则会相当的明显。
(5)辊环修磨不当会使辊环的表面过熟,辊环表面会呈“紫蓝”色,这样的辊环不应当再安装到轧机上去。
(6)定期检查轧机的冷却水的水质,必须控制好悬浮物的含量,单纯由钴组成粘结相的牌号PH值应保持在7.5-8.5之间,由钴镍铬组成粘结相的牌号PH值应小于7.5。
2.6麻面
在放大镜下能明显地看出在线材表面连续分布着不规则的凸凹缺陷,此即麻面。
2.6.1轧制过程中产生麻面缺陷的主要原因有:
(1)轧槽冷却不当或严重磨损。
(2)冷却水的PH值不合适,WC辊环中的粘结剂被腐蚀,从而使WC颗粒
在轧制过程中脱落出来。
2.6.2若产生麻面,应从以下几方面进行检查,排除故障:
(1)严格按计划更换轧槽。
(2)交接班时要全面检查轧辊冷却和轧槽表面的情况。
(3)定期检查水质情况。
(4)检查轧辊的冷却水管是否堵塞。
2.7结疤(翘皮)
线材表面与线材基体部分结合或完全未结合的金属片层称为结疤。
前者是由成品以前几道次轧件上的凸起物件轧入基体形成的,后者是已脱离轧件的金属碎屑轧在轧件表面上形成的。
2.7.1坯料表面质量不好,漏检坯料上原有的结疤,或连铸坯表面未清除干净的翘皮、飞翅等均可形成结疤。
在轧制中产生结疤的原因有:
(1)坯料过热。
(2)坯料修磨不好。
(3)轧槽过度磨损。
(4)辊环“掉肉”。
(5)轧机导卫有毛刺。
2.7.2若产生结疤(翘皮或鳞层),应从以下几方面进行检查,排除故障:
(1)料过热会产生偏析,并且产生过量的氧化铁皮。
(2)轧制过程中较大块的氧化铁皮轧入轧件的表面形成结疤缺陷,因此要使用高压水除鳞消除氧化铁皮。
(3)偏析使坯料表面不平整,破裂碎片被轧入轧件内,在轧制后期破裂形成结疤,因此要控制好加热温度;
(4)轧机停稳以后,要仔细检查轧辊及导卫表面是否有毛刺、磨损、掉肉等问题。
3结语
高速线材表面质量缺陷的形成原因及故障排除方法并不复杂,现场操作人员要遵循以上原因进行分析,对排除方法要点要认真思考,经常不断地、定时的对导卫、轧辊、钢坯及加热、冷却水等进行检查,以减少高速线材表面质量缺
陷的发生次数,排除时应力求分析准确解决迅速。