原材料异常处理
原材料入厂检验流程中的异常报告与处理流程

原材料入厂检验流程中的异常报告与处理流程一、异常报告的概念和重要性原材料的入厂检验是生产过程中非常重要的环节,可以确保产品质量符合标准要求。
然而,在检验过程中难免会遇到一些异常情况,例如原材料超出规定的质量标准、数量不符等问题。
这时就需要及时发出异常报告,以便进行处理和解决。
二、异常报告的内容和要求1. 异常报告应包括以下内容:- 异常情况的描述和分类- 异常原因的分析和说明- 异常影响的评估和预警- 异常处理的建议和方案2. 异常报告应具备以下要求:- 准确全面地反映异常情况- 逻辑清晰地说明异常原因- 提出合理可行的处理建议- 尽快上报相关部门进行处理三、异常报告的处理流程1. 接收异常报告- 检验员在发现异常情况后,应立即填写异常报告,并上报质量管理部门。
- 质量管理部门收到异常报告后,要及时处理并分配相关人员进行跟踪处理。
2. 分析异常原因- 质量管理部门应对异常报告进行认真分析,找出异常原因并进行归类。
- 如果需要进一步调查,可组织相关部门成立专门调查小组进行深入调查。
3. 制定处理方案- 根据异常报告中提出的建议,制定相应的处理方案。
- 确定责任人,明确处理流程和时间节点,落实措施并进行跟踪检查。
4. 处理异常情况- 负责人按照处理方案和流程进行处理,并通知相关部门协作配合。
- 在处理过程中,要及时上报进展情况,并对结果进行评估和总结。
四、异常报告的监督和评估1. 监督处理过程- 质量管理部门应对异常处理过程进行监督和督促,确保处理工作按照规定程序和时间节点进行。
- 如发现处理不当或拖延现象,应及时采取措施进行整改。
2. 评估处理结果- 处理完毕后,需要对异常处理结果进行评估和总结,分析处理效果和存在问题。
- 提出改进建议,完善异常处理流程,并进行经验总结和分享。
五、结论原材料入厂检验中的异常报告与处理流程,是企业质量管理体系中一个重要的环节。
通过规范处理流程和及时报告异常情况,可以有效防范和解决各类质量问题,提升企业生产效率和产品质量,确保企业可持续发展。
原材料异常处理流程
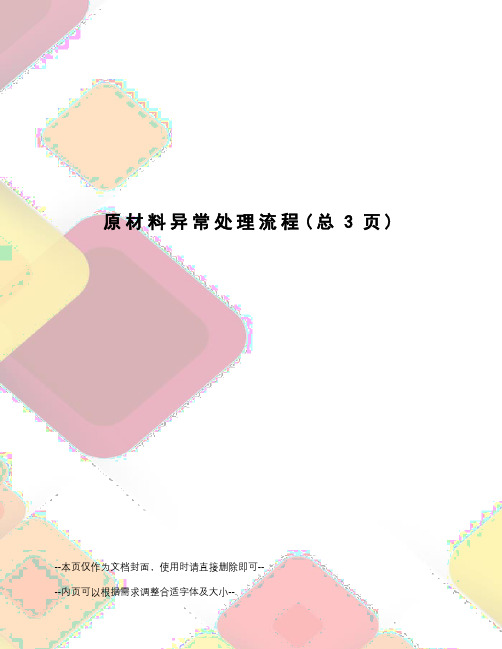
原材料异常处理流程(总3页)--本页仅作为文档封面,使用时请直接删除即可----内页可以根据需求调整合适字体及大小--江苏久诺建材科技有限公司发布日期15年8月5日原材料异常处理流程编号JN-JY-16实施日期15年8月10日页数 1 / 1 1:目的为了更好的控制原材料质量,对异常原材料快速处理,降低材料不良带来的影响,以及明确相关部门的职责和流程2 :范围适用于公司来料所发生的异常。
3 职责品保部:负责对原材料异常情况的确认;仓储部:负责对材料的存放,以及区域的划分;技术部:负责协助品保部确认异常情况对材料的影响、以及对材料的处理方法;生产部:负责确认异常材料对生产的影响;采购部:负责跟供应商沟通,监督供应商落实异常处理的决议;生管部:负责生产异常而导致的交期延后同销售部的沟通和确认。
4 :作业流程原材料检验员在发现材料异常时,要及时下达《异常处理报告》(必要时可以先电话通知,再开《异常处理报告》),并通知仓储部,对不良材料进行隔离;仓管员在接到检验员通知后要及时隔离原材料,防止在没有明确处理办法前使用材料;相关人员在接到《异常处理报告》时要在10分钟内赶到现场,若不能到达,必须安排人员到达现场协助处理。
A)技术部与品保部共同确认异常情况对产品的生产以及对质量的影响(必要时,生产部协助确认);B)检验员负责对异常产品的标识、以及后期处理情况的跟踪;处理结束后相关负责人对《异常处理报告》进行完善,确定异常产品的处理办法;采购部向供应商放映异常情况以及确认处理结果,并要求供应商进行整改。
品保部对后期整改工作进行跟踪确认。
对于过期原材料的复检,按照相关产品的检验标准执行。
版本拟制人拟制日期审核人审核日期批准人批准日期01。
食材加工中的质量异常处理与纠正措施

食材加工中的质量异常处理与纠正措施在食材加工过程中,质量异常可能时有发生。
这些异常可能会影响产品的品质和安全,进而对企业声誉和利润产生负面影响。
因此,采取及时有效的处理和纠正措施是至关重要的。
本文将探讨食材加工中常见的质量异常及其处理与纠正措施。
1. **原材料异常**原材料的质量异常是导致最终产品质量问题的主要原因之一。
当供应商提供的原材料存在质量问题时,加工企业应立即采取措施。
首先,需要立即停止使用受影响的原材料,并立即与供应商联系。
其次,对已接收的原材料进行追溯和检验,确定是否有其他受影响的批次。
最后,与供应商协商处理方案,包括更换受影响的原材料或要求赔偿。
2. **加工环境异常**加工环境的异常可能包括温度过高或过低、湿度异常、空气质量问题等。
这些异常可能导致产品受污染或加工过程受干扰。
因此,加工企业应建立严格的环境监控系统,并定期检查环境参数。
一旦发现异常,应立即采取措施,如调整环境参数、清洁环境、更换设备等,以确保加工环境符合要求。
3. **人为操作失误**人为操作失误是另一个常见的质量异常来源。
为了减少这种情况的发生,加工企业应该加强员工培训,并建立严格的操作规程。
如果发生人为操作失误导致的质量问题,应立即停止相关操作,并对责任人进行培训和纠正措施。
同时,对受影响的产品进行追溯和检查,确保不合格产品不流入市场。
4. **设备故障**设备故障可能导致生产线停止或产品质量下降。
因此,加工企业应定期检查和维护设备,确保其正常运行。
一旦发生设备故障,应立即停止生产,并派遣维修人员进行检修。
在设备恢复正常运行之前,不应恢复生产,以防止不合格产品的生产。
5. **产品质量异常处理**当发现产品质量异常时,加工企业应立即停止生产,并对受影响的产品进行隔离和追溯。
对于已经流入市场的产品,应立即采取召回措施,并对相关信息进行公告。
同时,对生产过程进行全面检查,确定质量异常的原因,并采取纠正措施,以防止类似问题再次发生。
原材料不合格品处理流程

原材料不合格品处理流程:发现原材料不良,开立进料不合格品处理单主管判定3.不良品判定结果:代用、选别、退货4.代用产品按代用方式入库5.选别:确定选别方式、选别后的合格品入库6.退货:由采购安排退回供应商7.以上三种判定,结果均需通知到采购部、生管部和仓库部同意按<不合格控制程序>入手展开顺藤摸瓜,-记录控制程序, 文件控制程序, 来料检验指导书, 预防纠正措施等逐步引用,具体措施参照楼上各DX高论!不合格品处理流程:发现原材料不良,开立进料不合格品处理单主管/工程师SQE/IQC判定3.不良品判定结果:代用、选别、退货,返工,返修,让步接收等4.代用产品按代用方式入库5.选别:确定选别方式、选别后的合格品入库6.退货:由采购安排退回供应商7 返工: 不合理地方返工处理8 返修: 即时解决处理不合格品,区别返工.9.标示,隔离,追溯,及时跟进等以上种种判定,结果均需通知到相关部门等!1) 来料Lot Out的处理:检查员判定Lot Out的部材,担当QE要及时确认不良品,并作出最终的判定,对最终判定NG,需要立即与供应商或客户进行反馈处理,并在规定时间内给出处理意见。
对于难以处理或处理不动的Case,请市场或采购联络处理,以满足生产的需求。
2)CA物料的处理:对于Lot Out的部材,在与供应商或客户交涉未果并生产紧急的部材,需要CA的部材,需要召开MRB会议,形成MRB决议,并安排好在部材投入前将不良品选出(如制定选别的方法、选别的流程、选别要点等)。
必须保证生产线投入的部材为良品。
3)生产线来料品质异常处理:对于生产线来料的品质异常,需要及时处理,对于异常频发的部材,需要及时确认在库品是否有同样的异常,如果有异常,则对部材进行及时的隔离并做相应的处置,以保证生产的顺畅。
我们公司是这样处理的了,1.有仓管员收到原材料通知IQC,IQC检验并记录在《来料检查日报》中,经判定不合格的有IQC加盖“不合格”印章,并填写《来料检验拒收报告》上报部门负责人;2.仓管员将不合格品原料放置到“不合格”区存放,3.品质部负责人收到拒收报告后组织相关人员对不合格原材料进行再次确认,经确认不合格后通知与之相关联的生产部,品质部,营业部。
来料检验及异常处理流程

来料检验及异常处理流程一、来料检验流程:1.接收原材料:当供应商将原材料送到公司时,接收人员负责接收原材料。
他们会核对送货单和实际接收数量,确保一致性。
如果发现数量不一致,则会与供应商协商解决。
2.样品收集:接收人员从接收的原材料中抽取一定数量的样品,确保样品能够全面代表整批原材料。
3.检验依据:根据公司的检验标准和规定,制定检验计划和检验依据,明确要求的检验项目和标准。
4.检验方法选择:根据检验项目的不同性质和要求,选择合适的检验方法,如外观检查、物理性质测试、化学成分分析等。
5.执行检验:根据检验计划和检验依据,实施相应的检验活动。
检验员按照检验方法和标准,对原材料进行检验,并记录检验结果。
6.检验结果评定:根据检验结果和标准,评定原材料是否合格。
如果原材料符合要求,则通过;如果不符合要求,则判定为不合格。
7.合格原材料处理:对于合格的原材料,将其进行封存,并进行标识。
符合要求的原材料可以进入下一道工序使用。
8.不合格原材料处理:对于不合格的原材料,根据具体情况,采取以下措施:返回供应商、报废、返工等。
同时,需要记录不合格原材料的情况并进行归档,以便后续处理。
二、异常处理流程:1.异常检测和发现:在来料检验过程中,如果发现原材料存在异常情况,如外观缺陷、超出标准范围的物理性质、化学成分分析结果与标准不符等,应立即停止检验过程,将异常情况进行记录和报告。
2.异常情况分类:根据异常情况的性质和严重程度,将异常情况进行分类。
如严重影响生产的异常、有风险的异常、可修复的异常等。
3.处理方案制定:根据异常情况的分类和具体情况,制定相应的处理方案。
对于严重影响生产的异常,需要立即停止生产并与供应商协商解决;对于有风险的异常,需要进行风险评估并采取合适的措施进行处理;对于可修复的异常,需要返工或者重新采购原材料。
4.异常情况解决:根据制定的处理方案,采取相应的措施解决异常情况。
如与供应商协商解决问题、制定修复方案并进行返工、重新采购原材料等。
原材料入厂检验流程中的异常处理与问题解决方法

原材料入厂检验流程中的异常处理与问题解决方法在原材料入厂检验流程中,异常处理和问题解决方法一直是生产过程中重要的环节。
无论是从供应商处运送过程中出现的质量问题,还是在仓储过程中出现的异常情况,都需要及时处理和解决,以确保产品质量和生产进度。
本文将从异常处理和问题解决方法两个方面进行探讨。
首先,原材料入厂检验流程中的异常处理至关重要。
当原材料经过运输到达生产厂家时,有可能会出现以下情况:一是货物破损,二是货物数量不符,三是货物质量不合格。
在这些异常情况下,厂家需要立即采取相应的措施来处理。
首先要及时通知供应商,协商解决方案。
如果货物破损或数量不符,可以要求供应商进行补发或退款;如果货物质量不合格,可以要求供应商进行重新提供合格的原材料。
同时,厂家还需要及时调整生产计划,以避免影响生产进度。
总之,及时沟通和妥善处理异常情况对于原材料入厂检验流程至关重要。
其次,问题解决方法在原材料入厂检验流程中也是必不可少的环节。
在日常检验中,有可能出现原材料不符合质量标准的情况,这时候就需要对问题进行分析和解决。
首先要明确问题的原因,可能是供应商生产过程中出现问题,也可能是在运输过程中引起的质量损坏。
针对不同的问题原因,制定相应的解决方案。
例如,如果是供应商生产问题,可以协商改进生产工艺;如果是运输损坏,可以要求加强包装防护措施。
同时,还要对问题进行记录和分析,以便今后避免同类问题的发生。
通过不断总结经验和改进方法,最终将原材料入厂检验流程中的问题解决到位,确保产品质量和生产顺利进行。
综上所述,原材料入厂检验流程中的异常处理和问题解决方法是保证产品质量和生产进度的关键环节。
只有在面对异常情况时及时处理,对问题进行深入分析和解决,才能确保生产过程的顺利进行。
厂家需要不断完善管理措施,加强与供应商的沟通合作,以确保原材料入厂检验流程的顺利进行。
希望通过不懈努力,实现生产流程的高效运行和产品质量的持续提升。
原材料质量异常处理的方法与技巧
原材料质量异常处理的方法与技巧原材料质量异常处理是生产过程中不可避免的问题之一,其处理方
法与技巧的掌握对于保证产品质量和生产效率至关重要。
以下将介绍
几种常见的原材料质量异常处理方法与技巧。
一、原材料质量异常的分类
原材料质量异常主要包括以下几种情况:外观异常、尺寸异常、成
分异常以及性能异常等。
针对不同类型的异常,需要采取不同的处理
方法与技巧。
二、外观异常处理方法
外观异常通常是由于原材料在运输或存储过程中受到了损坏或污染,可以采取以下处理方法:
1. 对受损部分进行剔除,只使用正常部分;
2. 进行表面清洁处理,如擦拭或清洗。
三、尺寸异常处理技巧
尺寸异常可能导致产品的装配或使用困难,可通过以下方法加以处理:
1. 对尺寸较大或较小的原材料进行削减或填补;
2. 调整生产工艺参数,使产品能够适应尺寸异常。
四、成分异常处理方法
成分异常可能导致产品性能不稳定或不达标,应该采取以下措施:
1. 检验原材料成分,查明异常原因;
2. 调整生产配方或采购新的原材料。
五、性能异常处理技巧
性能异常往往是由于原材料制备工艺不当或受到外部环境影响,可以通过以下方法处理:
1. 调整生产工艺,提高产品性能;
2. 对受污染或受损的原材料进行处理,保证产品性能符合要求。
六、结语
以上是几种常见的原材料质量异常处理方法与技巧,希望能够对生产过程中的异常情况处理提供参考。
在生产实践中,应该根据具体情况采取相应的处理措施,及时解决问题,确保产品质量和生产效率。
原材料异常处理流程
流程
校准 序号
内容
关联人员
时间 要求
操
作
步 1 骤
1、当生产车间在生产过 程中发现原材料不良比例 超过2%时,生产车间向质 保部及供销部进行反馈
第一时间
车间主管 检验员
一、问题反馈
流程
校准 序号
内容
质保部接收到车间的投诉 问题后,来料检验员首先 向供销部询问处理措施, 并开出《铝片异常处理单》 (如图1)
关联人员
时间 要求
图1
操
1
质保部主管
第一时间
作
步 骤
1、供销部将《工作联络 单》转交到供应商,并要 求供应商按照规定时间进 行回复
2
供销部主管
第一时间
一、问题反馈
流程
校准 序号
内容
1、根据供应商回复的内 容,由供销部将供应商回 复的内容填写到“供销部 意见”栏中 2、此单由生产车间进行 保管
关联人员
时间 要求
图1
第一时间 供销部主管
操
1
作
步 骤 2
1、供应商回传后,供销 部将表单传给财务,由财 务转交而给总经理进行批 复。 第一时间 供销部主管 财务人员 总经理
图2
1、此批物料生产结束后, 各车间对不良数进行汇总, 并填写到《铝片异常跟踪 单》中, 第一时间 冲压车间 组装车间
三、费用结算
流程
校准 序号
内容
1、此批物料生产结束后, 供销部根据车间填写的信 息进行汇总,并将供应商 所赔付的价格或数量,以 扣款单的形式传递给供应 商,让供应商进行回签。
关联人员
时间 要求
图1
操
1
供销部主管 第一时间
原材料不合格品处理流程
原材料不合格品处理流程:1.IQC发现原材料不良,开立进料不合格品处理单2.IQC主管判定3.不良品判定结果:代用、选别、退货4.代用产品按代用方式入库5.选别:确定选别方式、选别后的合格品入库6.退货:由采购安排退回供应商7.以上三种判定,结果均需通知到采购部、生管部和仓库部同意按<不合格控制程序>入手展开顺藤摸瓜,-记录控制程序, 文件控制程序, 来料检验指导书, 预防纠正措施等逐步引用,具体措施参照楼上各DX高论!不合格品处理流程:1.IQC发现原材料不良,开立进料不合格品处理单2.IQC主管/工程师SQE/IQC判定3.不良品判定结果:代用、选别、退货,返工,返修,让步接收等4.代用产品按代用方式入库5.选别:确定选别方式、选别后的合格品入库6.退货:由采购安排退回供应商7 返工: 不合理地方返工处理8 返修: 即时解决处理不合格品,区别返工.9.标示,隔离,追溯,及时跟进等以上种种判定,结果均需通知到相关部门等!1) 来料Lot Out的处理:检查员判定Lot Out的部材,担当QE要及时确认不良品,并作出最终的判定,对最终判定NG,需要立即与供应商或客户进行反馈处理,并在规定时间内给出处理意见。
对于难以处理或处理不动的Case,请市场或采购联络处理,以满足生产的需求。
2)CA物料的处理:对于Lot Out的部材,在与供应商或客户交涉未果并生产紧急的部材,需要CA的部材,需要召开MRB会议,形成MRB决议,并安排好在部材投入前将不良品选出(如制定选别的方法、选别的流程、选别要点等)。
必须保证生产线投入的部材为良品。
3)生产线来料品质异常处理:对于生产线来料的品质异常,需要及时处理,对于异常频发的部材,需要及时确认在库品是否有同样的异常,如果有异常,则对部材进行及时的隔离并做相应的处置,以保证生产的顺畅。
我们公司是这样处理的了,1.有仓管员收到原材料通知IQC,IQC检验并记录在《来料检查日报》中,经判定不合格的有IQC加盖“不合格”印章,并填写《来料检验拒收报告》上报部门负责人;2.仓管员将不合格品原料放置到“不合格”区存放,3.品质部负责人收到拒收报告后组织相关人员对不合格原材料进行再次确认,经确认不合格后通知与之相关联的生产部,品质部,营业部。
原材料异常问题处理方案
以退回公司与供应商交换处理;
问题三 材料异常处理缓慢
1、原因分析: 1)驻外人员提报不及时,提报信息不全多次来回询问,异常真实性有待考证; 2)不良样品验证大车来回送货周期长; 3)给出处理方式后,其他部门不配合,导致问题拖延; 2、解决方案: 1)异常提报严格按照流程进行,提报信息准确全面,否则不予受理; 2)驻外品管针对异常问题进行初步分析确认,判断材料异常问题点 3)库存验证与异常不符,又提供不出真实性证据,按照验证结果处理;
步处理;
问题二 材料短装问题
1、原因分析: 1)供应商来料短装; 2)材料无损耗,原材料存在破损,生产地保存丢失,制程中造成的不良,累计后以短装形式
提报不良,以期补货填补不足,避免超领; 2、解决方案: 1)避免因短装批次不同,厂内确认库存品与异常批次为不同批次,确认出现存在差异,由驻
外品管对异常批次进行再次检验确认; 2)生产地提供不出整箱或整袋未拆封产品给驻外品管确认情况下,厂内确认库存无短装,生
问题一 磁芯易较薄易破损; 2)IQC无检测磁芯强度设备,且检测为180 °拉力,实际生产为一侧台钳夹住另一侧承受
90°拉力,监区拉线力度过猛过大,拉力不统一; 3)磁芯搅拌凡立水,一次性搅拌太多力度太大,磁芯碰撞导致; 2、不良发生工序: 1)原材料来料个别磁芯暗裂或破损,IQC抽检难以抽到 2)运输途中造成 3)制程中凡立水搅拌磁芯、跌落、拉线都容易造成磁芯破损、暗裂 3、解决方案: 1)针对易破损磁芯型号,例如:T16*12*8,建议公司领导层裁决是否可以给予一定比例损耗; 2)驻外品管召回公司培训,后续原材料异常由驻外品管对异常问题做初步确定后再提报进一
- 1、下载文档前请自行甄别文档内容的完整性,平台不提供额外的编辑、内容补充、找答案等附加服务。
- 2、"仅部分预览"的文档,不可在线预览部分如存在完整性等问题,可反馈申请退款(可完整预览的文档不适用该条件!)。
- 3、如文档侵犯您的权益,请联系客服反馈,我们会尽快为您处理(人工客服工作时间:9:00-18:30)。
19
The End
20
4
描 述 问题
description_3: Problem description_3:
问题描述的准则 基于数据 无需原因 无需纠正措施/解决方案 无需纠正措施/ 不要太笼统
5
Containment action_1 暂时对策: 暂时对策: :
物的处理(涵盖库存清查) 1. 物的处理(涵盖库存清查) 已生产成品之疑虑品拦截与处理(查找影响批) 1.1 已生产成品之疑虑品拦截与处理(查找影响批); WIP部分之处理 部分之处理; 1.2 WIP部分之处理; 疑虑材料之处理; 1.3 疑虑材料之处理; 紧急处理对策: 2. 紧急处理对策: 2.1 Re-screen/Rework(厂商库存/ADATA库存/客户端). Re-screen/Rework(厂商库存/ADATA库存 客户端). 厂商库存/ADATA库存/ 2.2 紧急对策验证 补货/ 2.3 补货/空运安排等 通知业务, 2.4 通知业务,知会客户等 2.5落实不良品的产品追溯 2.5落实不良品的产品追溯 2.6清理仓库,工场, 2.6清理仓库,工场,生产线中的不良品或怀疑不良品 , 清理仓库 甚至在途产品。 甚至在途产品。
怎样进行问题描述? 怎样进行问题描述? 将某项问题依此七个方向去追问思考, 将某项问题依此七个方向去追问思考,找出任何有缺点或不满之 继而思考其改善方案。 处,继而思考其改善方案。
What: 了什么问题问题发生在何地? 了什么问题问题发生在何地? When: 时谁发现的? 时谁发现的? Why: How Many: How Much Cost: How: 的? Safety: 项 哪项工作发生 问题发生在何 为何这是问题? 为何这是问题? 同类问题有多少? 同类问题有多少? 造成多大的损失? 造成多大的损失? 问题是如何发现 有无安全注意事
15
WHY 中间原因
WHY 中间原因
WHY 中间原因
WHY 根本原因
Root cause Analysis _7: _7:
识别并确认根本原因和问题流出环节: 识别并确认根本原因和问题流出环节:
Input Process
•咨询专家 咨询专家: 咨询专家 工艺工程师, 供应商, 技术人士, 作业员. 工艺工程师 供应商 技术人士 作业员 •参考 “Is/Is Not”, 找到变化和区别 参考 •考虑尽可能多的可能性因素, 考虑尽可能多的可能性因素, 考虑尽可能多的可能性因素 不要仅限于一个或几个 •识别可能的根本原因 识别可能的根本原因 • 使用 whys 使用5 •使用 “Drill Deep” 的方法进行分析 使用 •通过测试或观察以验证根本原因 通过测试或观察以验证根本原因
17
Effective confirm _1: _1:
审核数据以确保纠正措施的效用 检查资料数据及催势 以确保问题已有效解决 如有关行动未能有效, 须回车根源问题分析
18
Preventive action _1: _1:
改善对策水平展开 1.1 类似机种水平展开, 类似机种水平展开, 1.2类似供应商水平展开, 1.2类似供应商水平展开, 类似供应商水平展开 1.3所交货客户水平展开 1.3所交货客户水平展开 文件标准化: 文件标准化: 2.1 SOP 修改; 修改; 2.2 SIP 修改; 修改; 2.3 BOM 修改; 修改; 2.4 图面修改; 图面修改; 2.5 QC 工程图(PMP)/FMEA修改; 工程图(PMP)/FMEA修改; (PMP)/FMEA修改 2.6采用防错法工具、标准化、长远方案制定后的培训 2.6采用防错法工具、标准化、 采用防错法工具
8
_1: Root cause Analysis _1:
会同RD、MQA、PE分析原物料异常Root 会同RD、MQA、PE分析原物料异常Root Cause RD 分析原物料异常
找问题真正原因时,最好不要盲目地动手改变目前的生产状态, 找问题真正原因时,最好不要盲目地动手改变目前的生产状态, 先动动脑。 先动动脑。 您第一件事是要先观察、分析、比较。 您第一件事是要先观察、分析、比较。列出您所知道的所有生产条件 即鱼骨图) 逐一观察,看看是否有些条件走样, (即鱼骨图),逐一观察,看看是否有些条件走样,还是最近有些什么 异动?换了夹具吗?换了操作人员?换了供应商?换了货运行? 异动?换了夹具吗?换了操作人员?换了供应商?换了货运行?修过电源 供 应器?流程改过? 或比较良品与不良品的检查结果, 应器?流程改过? 或比较良品与不良品的检查结果,看看那个数据有 很 大的差别,尺寸?重量?插拔力?CPK?耐电压? 不良的发生,总是有因, ?CPK?耐电压 大的差别,尺寸?重量?插拔力?CPK?耐电压? 不良的发生,总是有因, 资料分析常常可以看出蛛丝马迹。
13
Root cause Analysis _6: _6:
确定选择最有可能的原因---2 确定选择最有可能的原因---2: ---
1.选出三项最有可能的根深原因 2.列出原因发生率-60%,30%,10%
14
Root cause Analysis _3: _3:
识别根本原因的典型方法:5WHY
WHY 问题 5 WHY case:
10
Root cause Analysis _4: _4:
识别并验证根本原因: 识别可能原因(因果图) 选择最有可能的原因(矩阵表) 3.确定根本原因(柏拉图)
11
Root cause Analysis _5: _5:
因果分析: 因果分析:
环 库房湿度大 法 速度设定太快
包装方式不合理 端 面 受 伤
原材料异常处理
1
handle: Flow chart for abnormality handle:
识别潜在 因素 选择并验证纠正措施
选择可能性 因素 潜在因素 是 根本原因 吗? Y 识别问题 流出环节 识别可能性 解决方案
效果确认
N 问题陈述
实施长期 纠正措施
围堵措施 问题预防
2
description_1: Problem description_1:
9
_2: Root cause Analysis _2:
首先考虑一下出现目前情况的可能原因。集中 精力考虑手头现有的资料,同时注意倾听别人 的意见。 尽力做到客观地去看待问题会使你将那些表面 上看来错综复杂的问题简单化。 原因及效应分析图(鱼骨图) 锁定最少3个主要原因及估计各项发生比率 5 `Why?' # 5个'为什么?' 如有需要,可使用过程失效及效应分析图复检
产品堆放高度过高
对操作工艺不熟
操作粗心 人
贮存架间隙小 机
拉伸强度不稳定
料
12
Root cause Analysis _5: _5:
确定选择最有可能的原因: 确定选择最有可能的原因:
项目 A。产品堆放高度过高 B。包装方式不合理 C。操作粗心 D。库房湿度大 E。速度设定太快 F。贮存架间隙小 G。拉伸强度不稳定 H。对操作工艺不熟 总计 端口破损数(卷) 12 4 2 1 1 1 1 1 23 频率(%) 52.17 17.39 8.69 4.34 4.34 4.34 4.34 4.34 100 累计频率(%) 52.17 69.56 78.25 82.59 86.93 91.27 95.61 100
Output
•问题描述 问题描述 •设计细节 设计细节 •过程细节 过程细节
•根本原因的验证 根本原因的验证 •问题流出环节 问题流出环节 的验证 •找出的系统性 找出的系统性 原因
16
Corrective action _1: _1:
提出纠正措施并评估其有效性 验证(小批量) 验证(小批量)纠正措施 确定可行的纠正措施 1.要找出解决问题的最好方法, 1.要找出解决问题的最好方法,就要对所有的可择方案进行评 要找出解决问题的最好方法 验证。 估/验证。 2.可以把一些或所有的主要制约条件加到可择方案上, 2.可以把一些或所有的主要制约条件加到可择方案上,以便对 可以把一些或所有的主要制约条件加到可择方案上 各种可择方案进行筛选, 各种可择方案进行筛选,这些制约条件往往会左右对解决方案的 评估,它们是: 评估,它们是: 成本(实际上付多少钱收回到利益) a. 成本(实际上付多少钱收回到利益) b.可获性(可以达到目标?成效) b.可获性(可以达到目标?成效) 可获性 c.时间(花多长时间?) c.时间(花多长时间?) 时间
Input Process Output
•对象 对象 •缺陷 缺陷 •数需要的数据 识别任何需要的数据 •收集数据 收集数据 •分析数据 分析数据 •细化地描述问题 细化地描述问题
•细化的问题 细化的问题 描述
3
description_2: Problem description_2:
6
Containment action_2: :
应急措施注意事项: 应急措施注意事项: 为防止问题恶化并波汲其他产品及客户 尽快恢复客户信心 预先部置应变方案 采用产品追溯到生产批及评估损失范围 安全产品可能要回收 最后须验证行动有效性。 最后须验证行动有效性。
7
Containment action_3: 实施并验证临时措施 : 关键要点评价紧急响应措施 找出和选择最佳“临时抑制措施" 找出和选择最佳“临时抑制措施" 决策 实施,并作好记录验证(DOE、PPM分析 分析、 实施,并作好记录验证(DOE、PPM分析、控 制图等) 制图等)
有一台汽车故障不能行走 为什么汽车不能行走 因为引擎故障 为什么引擎故障 因为火星塞不点火 为什么火星塞不点火 因为火星塞潮湿沾水 为什么火星塞潮湿沾水 因为引擎盖的密封漏水, 因为引擎盖的密封漏水,以致水进入 所以如果只是把火星塞换了,汽车是可以走了, 所以如果只是把火星塞换了,汽车是可以走了,但是不用多久火星塞又要潮 汽车又要不动了,但如果把密封也换了, 湿,汽车又要不动了,但如果把密封也换了,那么火星塞就可以使用寿命比 较长了。 较长了。