轴承套圈的磨削烧伤及其检测方式的研究
减缓轴承套圈沟道磨削烧伤的探讨

a d h a- r ame t u r q e t ee mi e y t e g i d n r c s . h y e e mi e ea e n e t te t n ,b tfe u n l d t r n d b h r i g p o e s T e h p  ̄h r a g n r td y n
b rn i g c n c u e l c lt mp r t r ie y g i d n a a s o a e e au e rs ,wh c l ma e t u a e d v lp ih mo e e u i h wil k he s r c e e o n o g n o s f
5月
文章 编号 :1 0 ・3 2( 0 )0 -0 20 0 67 0 2 1 I 20 5 -4
减 缓 轴承套 圈沟道磨 削烧伤 的探讨
肖容美 ,李辛沫
( 邑 大 学 机 电 工程 学 院 ,广 东 江 门 5 9 2 五 2 0 0)
摘要 : 轴承套 圈沟道磨 削加 工 时产生的高温会 造成磨 削工件表 面局 部升 温而形成不均一的组织
根 据 以上 试验 结 果 可 以发 现 :在 轴 承磨 削加 工 的过程 中 ,在 进 给量 厂保 持不 变 的条件 下 ,如果 速 度 比 a过低 或者 过 高 均 容易 导 致轴 承套 圈沟道 表 面烧伤 ,而且 表 面质 量较 差 .特别 是 当速度 比 口 的数值 很小 时 。沟道 表 面烧 伤 最 为严 重 ,只有 当速 度 比 口在 4 —5 5 5时 , 可 以减少 烧 伤并 能获得较 才 好 的表 面质 量 .另外 , 当 件在 4 0—5 mi ,工 件表 面质 量 几乎 无 变化 ,但 件继续加 大后 , 5 m/ n时 工 件的磨 削表 面粗 糙 度 变 化加 剧 且其 数 值 总体 增加 ,温度 升高 ,烧伤 加 深 .需要 说 明 的是 ,判断烧 伤程 度 主要依 赖 观察 法 ,一般 常 见 的烧 伤颜 色最 初是 浅 黄色 ,随着烧 伤 程 度 的加剧 ,颜 色会 逐渐加
基于轴承套圈磨削工艺试验的理论方法研究

43
基于轴承套圈磨削工艺试验的理论方法研究
关佳亮,杨洋,刘书君,张龙月
北京工业大学
摘要:分析了正交试验、二次回归通用旋转组合方法和灰色系统理论的基本原理,应用以上三种据各因素的影响规律优化工艺参数,并基于磨削试验对以上三种方法进行
3 基于 GCr15轴承钢磨削试验的常用 理论方法对比试验
试验及检测设备 应用正交试验设计、二次回归通用旋转组合设 计以及灰色系统理论进行工艺参数优化试验研究, 均采用 ELID精密超精密高效磨削技术对 GCr15轴 承外圆进行精磨试验,试验及检测设备包括:M1412 型外圆磨床(改装有 ELID模块)、60mm的 W10粒 度铸铁基 金 刚 石 砂 轮 (自 主 研 发 )、ELID专 用 直 流 脉冲电源(自主研发)、用于磨削轴承钢的 ELID专 用磨削液(自主研发)、TR300粗糙度形状检测仪。 轴承滚道的表面粗糙度在很大程度上决定了轴 承的使用性能,故滚道表面粗糙度是衡量轴承质量 的重要指标。本文的三个试验均为精加工阶段,均 选择表面粗糙度作为评价指标。ELID精密高效镜 面磨削技术不仅与磨削参数有关,与各种电参数也 有关系。三个磨削试验均选择磨削深度、砂轮线速 度、电解电压和占空比作为评价指标的影响因素。 32 基于正交试验的 GCr15轴承钢磨削试验 设计及参数优化 (1)GCr15轴承钢 ELID磨削的正交试验设计 将磨削深度、砂轮线速度、电解电压和占空比作 为试验 因 素,每 个 因 素 取 三 水 平,对 轴 承 套 圈 进 行 ELID磨削加工,探究上述四因素对表面粗糙度的影 响规律,采用四因素三水平正交试验,用 W10粒度的
使用正交设计,为达到最终目标,首先应选择评 价指标;其次是选择因素和水平;再次是根据实际需 要选择正交表;然后依照正交表所确定的参数组合 进行试验,记录相应数据;最后对试验数据及结果进 行计算处理,研究每个因素对试验指标的影响规律。
关于轴承酸洗的目的、烧伤产生原因和检测方法

关于轴承酸洗的目的、烧伤产生原因、酸洗槽配比成份和检测方法酸洗主要是检测轴承内外圈在磨削时有无烧伤和裂纹,因烧伤是一种热损伤,它使工件表面在高温下产生氧化形成极薄的氧化层,降低了表面硬度,严重的烧伤还会产生龟裂(即与磨削方向垂直的微细裂纹),所以检测烧伤是磨加工的关键检查项目,决不可缺失。
一般磨削烧伤与采用的磨削速比不当、砂轮过硬,使砂轮磨削表面堵塞,冷却润滑不良、砂轮修正不当有关。
GCr15 /440C 酸洗的工艺路线如下:脱脂槽→流动冷水槽→酸洗槽→流动冷水槽→第一明化槽→流动冷水槽→第二明化槽→流动冷水槽→中和槽→流动冷水槽→防锈槽。
1.脱脂槽体积为 0.6×0.6×0.45=0.162m3用料:体积按0.14m3计算(需加热至75℃~85℃)无水碳酸钠 Na2C03 0.14×1.5%=2.1kg磷酸三钠 Na3P04 0.14×1.5%=2.1kg氢氧化钠 NaOH 0.14×10%=1.4kg2.酸洗槽体积为 0.57×0.39×0.35=0.078m3 用料HNO3(硝酸)(室温)溶液体积按0.57×0.39×0.3=0.067m3 0.067×4%=2.68L=3.752kg3.第一明化槽体积为0.57×0.39×0.35=0.078m3(室温)溶液体积按0.57×0.39×0.3=0.067m3 计算:高锰酸钾 KMnO4 0.067×3.5%=2.345kg磷酸三钠 Na3P04 0.067×6.5%=4.355kg氢氧化钠 NaOH 0.067×3.5%=2.345kg4.第二明化槽体积为0.57×0.39×0.35=0.078m3(室温)溶液体积按0.57×0.39×0.3=0.067m3 计算:盐酸 HCL 0.067×12.5%=8.375L=9.88kg二氯化锡SnCl2·2H2O0.067×0.35%=0.2345kg金属颗粒 Sn 0.067×0.1%=0.067kg5.中和槽体积为 0.6×0.6×0.6=0.216m3(室温)溶液体积按 0.6×0.6×0.5=0.18m3无水碳酸钠 Na2C03 0.18×3%=5.4kg6.防锈槽体积同中和槽亚硝酸钠 NaNO2: 0.18×7%=12.6kg无水碳酸钠 Na2C03 0.18×0.4%=0.72kg以上材料可编入轴承零件酸洗规程内,酸洗槽材料陶瓷缸或搪瓷缸,下面有出水口,可按上述尺寸制作,磨削工件时一般每两小时抽查一次,如发现不合格,加大抽查的频率,酸洗后,工件表面呈灰白色,如果在沟道内有轻微烧伤,是呈断续黑色条纹,严重时,呈片状,团状黑斑,按P4级要求,轴承工作表面不允许有烧伤痕迹。
轴承磨削烧伤的产生原因及解决方法浅析

支点 角 度直 接 影 响套 圈 的受力 ,而受 力 又影 响套 圈参 与磨 削 的质 量 。 目前 ,使 用 的 电磁 夹 盘 无心 支 承方 式 是靠 轴 承套 圈与机 床 主轴 回转 中
2 套 圈 的温 升 分 析
从 热 力 学 公 式Q= c・ M ・ A t 中 ,可 以 看 出轴 承 套 圈 的 磨 削 热 与 材 料 的 比热 、参 与磨 削 的
质 量 和套 圈温 升 △f 成 正 比 ,而 套 圈材料 是 事 先
心之间的偏心量所产生的偏心力矩使轴承套圈靠 紧支点 来 实 现某 径 向定 位 ,轴 向定 位 是靠 电磁 力 和轴 向定 位 环来 实 现 的 ,而且 定位 环 与轴 承套 圈 之 间在 工 作 时 有 相对 运 动 。 图 1 为 工 件 自重 的 受 力 分 析 ,图 2 具 体 分 析 工 件 中心 与 回转 中心 偏 心量 所 产生 的偏 心力 。
De p a t r me n t , Ha r b i n Be a r i n g Gr o u p Co r p o r a t i o n , Ha r b i n 1 5 0 0 3 6 , C h i n a)
Ab s t r a c t : Th r o u g h t h e t h e r mo d y n a mi c f o m u r l a , t h i s a r t i c l e a n a l y z e s t h e ma i n r e a s o n f o r t h e b e a r i n g g r i n d i n g b u m, a n d i f n d s a r e a s o n a b l e wa y t o a v o i d b e a r i n g b u m. Ke y wo r d s : g r i n d i n g b u ms o f b e a r i n g ; r i n g t e mp e r a t u r e r i s e ; s u p p o r t i n g p o i n t ; g r i n d i n g wh e e l
轴承圈烧伤和裂纹产生原因初探

在计算中: D — —工件 曲率半径; R— — 砂 轮 半 径 ; a p ——磨削深度 。 据 以上公式可 以看 出, 减小砂轮直径可 以减少传递到工件上 的磨削热 量, 随着砂轮直径的减小, 烧伤情况大有好转; 提 高工件线速度 v对 降低烧 伤率具有显著的作用。 根据公式 ( 3 ) ( 4 ) 、 ( 5 ) 不同磨削形式与传递给工件热量之 间的比例关 系, 充 分表明了 内圆磨削 比平面磨削容 易产生磨削烧伤 , 平面磨削 比外 圆 磨 削容易产生磨削烧伤 。 在上述 公式 运算和数据 分析的基础上 , 采 用如下磨 削工艺规程 , 则工 件基本上不会产生烧伤现象: 砂轮 : P 4 0 0  ̄ 1 0 0 x1 2 7 WA 4 6 K5 V3 5 冷却液 : 乳化液 磨削参数 :
砂轮线速度 V s 2 1 m/ s
、
中具有 明显的优越性 , 例如 强度大 、 硬度 高、 耐磨性 好、 疲劳强度高 、 弹性 极 限高等优 点, 因此受到 了人们 的广泛关注 但是在 对产品进行磨削加 工的 过程 中, 如果操作者 的操作方法不 正确或者 出现 失误, 那么必 然会导致轴
途径 。
三、 磨削裂纹 Βιβλιοθήκη 磨 削过程 中,磨削裂纹是各种应力叠加后超过材料 的极 限强度 , 从
而使工件表 面产 生细微 的裂纹 。为防止磨削裂纹 的产 生, 就必 须从降低 表 面应力上采取措施 。 本文仅对轴承钢 组织对 磨削应力和磨削裂纹的影响进 行探 索, 有以下几个方 面。
1 、 热 阻 的影 响
轴承钢具有较 高的热 阻, 高热阻必然要形成很高 的温度梯度 。在磨 削 加工层的残 余应 力中,由磨削温度和温度梯度形成 的热应 力是主要的, 而 由磨削阻力而产 生的机械应力则非常小 。 r 2 、 热膨胀系数 的影 响 在马氏体轴承钢 中, 碳化物 的热膨胀系数 比基本金属要 小。因此 随着 磨削温度 的周期性变化 , 碳化物和基体金属之 间的形变差 也将 在晶界处形 成和积累相应的热应力 。 3 、 碳化物 的影 响 当碳 化物均匀分布 的点状碳化 时, 对磨削应 力的分散是有利 的, 因而 不容易产 生磨削裂纹 。 当存在着带状 碳化物 时, 则容易引起应力集中, 也容 易产 生磨削裂纹 。在存在 网状碳化物时 , 特别是 当网状碳化物完 全地包 围 晶界启0 断了基体组织 的连续性时 , 在 晶界处应力集中就非常严 重的。 这 时 即使采用合理的磨 削规 范, 磨削裂 纹也难 以避免 , 严重时会产 生表 面材料 剥落现象。 4 、 残余奥 氏体 的影 响 在马 氏体轴承钢 ( GC r 1 5或 G Cr 1 5 S i Mn ) 中, 存在着 一定 的残余奥 氏
磨削烧伤的检测方法

磨削烧伤的检测方法可能形成网状裂纹,它会导致齿面剥落.这当然是绝对不允许的。
用硬度测试法鉴别磨削烧伤的方法,并用超声波硬度计进行了实验,证明该方法简单易行,可以广泛应用于磨削加工中。
磨削烧伤及其常用检查方法在机械类产品中,很多重要零部件如轴承、齿轮、曲轴、凸轮轴、活塞销和万向节等,在热处理之后均需经过磨削加工。
相比之下,磨削时单位切削面积上的功率消耗远远超过其它加工方法,所转化热量的大部分会进入工件表面,因此容易引起加工面金相组织的变化。
在工艺参数、冷却方法和磨料状态选择不当的情况下,工件在磨削过程中极易出现相当深的金相组织变化层(即回火层),并伴随出现很大的表面残余应力,甚至导致出现裂纹,这就是所谓的磨削烧伤问题。
零部件的表面层烧伤将使产品性能和寿命大幅度地下降,甚至根本不能使用,造成严重的质量问题。
为此,生产企业一方面通过执行正确、科学的工艺规范,减轻和避免出现磨削烧伤现象;另一方面,加强对零部件的检验,及时发现不合格工件,并判断正在进行的磨削工艺状况。
但长期以来,对工件表面磨削烧伤的检验,除了最简单的目测法外,就是采用已延续多年的传统方法——酸洗法,即在被检零部件表面涂上酸液或将其浸入盛有按规定配制的酸液槽中。
之后(或在把工件取出后)根据表面呈现的不同颜色,对磨削烧伤的程度作出相应的判断。
一般地说,若色泽没有变化,就表明情况正常;而当颜色变成灰色,则说明已有烧伤情况存在,随着色泽变得越来越深,表示工件表面因温度更高,引起的磨削烧伤更为严重。
酸洗法具体如下:This is only a suggestion from my collegue ( Dino Calvanelli ) to find theburns on the gears此为有关过烧检测的建议:Clean each sample (part) to be inspected (free ofdirt,oil,grease,fingermarks,protective coatings,etc.).清洗产品,确保无灰尘、油污、手印、表面覆盖物等。
浅谈轴承套圈检测方法研究及设计

浅谈轴承套圈检测方法研究及设计【摘要】轴承套圈的加工过程中会出现一些不合格品,如何实现不合格品的自动分拣一直是一个值得研究的课题,论文从设计的角度提出机器视觉检测轴承套圈的过程及方法,为进一步实现机器视觉下的轴承套圈检测提供了技术方法的依据。
【Abstract】Some unqualified products will appear during the processing of bearing rings. How to realize the automatic sorting of unqualified products has always been a subject worth studying. From the point of view of design,this paper puts forward the process and method of machine vision inspection of bearing ring,which provides a technical basis for further realization of bearing ring detection under the machine vision.【?P键词】轴承;套圈;检测;机器视觉;图像采集【Keywords】bearing;ring;detection;machine vision;image acquisition【中图分类号】TH133.3 【文献标志码】A 【文章编号】1673-1069(2018)03-0185-021 引言轴承是机械工业中的重要零件之一,广泛应用于机床、航空、汽车等机械设备中。
轴承的精度和质量直接影响机械产品的性能和寿命,因此轴承的精度和质量一直是企业最关心的问题之一。
在轴承套圈加工中,车削加工是一个重要环节。
车辆的质量直接影响后续的加工。
轴承磨加工技术及痕迹或烧伤的原因分析
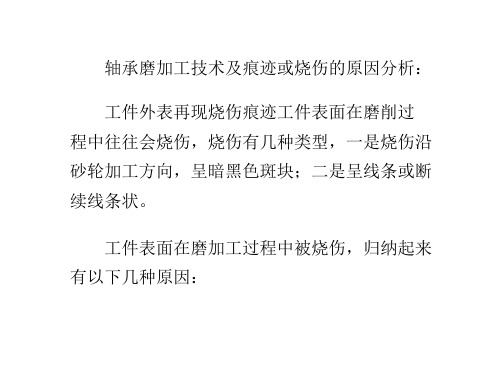
出现种种缺陷,以致影响轴承的整体质量。
轴承在精密磨削时,由于粗糙要求很高,外 表呈现的磨削痕迹往往能用肉眼观察到其外表 磨削痕迹主要有以下几种。 外表出现交叉螺旋线痕迹出现这种痕迹的
酒性温婉。水酒含糖,不耐久放,因此大多在冬天制作
原因主要是由于砂轮的母线平直性差,存在凹凸 现象,磨削时,砂轮与工件仅是局部接触,当工
酒性温婉。水酒含糖,不耐久放,因此大多在冬天制作
4.砂轮修整速度过快或修整机构间隙过大; 5.修整砂轮的金刚石不锐利或质量不好; 6.超精用油石质量不好,装置位置不正确; 7.超精用煤油质量达不到要求; 8.超精时间过短等。 轴承在磨加工过程中,其表面是通过高速旋
转的砂轮进行磨削的因此在磨削时如果不按作 业指导书进行操作和调整设备,就会在轴承外表
施加以解决,杜绝批量烧伤。
外表粗糙度达不到要求轴承零件的外表粗 糙度均有规范和工艺要求,但在磨加工和超精过 程中因种种原因,往往达不到规定的要求。 造成工件外表粗糙度达不到要求的主要原
因是 1.磨削速度过低,进给速度过快,进刀量过 大,无进给磨削时间过短; 2.工件转速过高或工件轴和砂轮轴振动过 大; 3.砂轮粒度太粗或过软;
点,就呈现云彩状暗黑色斑点,且周界不定整;
{HotTag}如果脱碳,则呈现灰白或暗黑色花斑; 如果磨加工裂纹,则裂纹呈龟裂状,如是烧伤, 一是外表沿砂轮加工方向呈现暗黑色斑块,二是
酒性温婉。水酒含糖,不耐久放,因此大多在冬天制作
呈现线条或断续线条状。如在磨加工过程中出现 上述烧伤现象,必需及时分析原因,采取有效措
5.砂轮修整不好,有局部凸起等。 外表出现鱼鳞状外表再现鱼鳞状痕迹的主 要原因是由于砂轮的切削刃不够锋利,磨削时发 生啃住现象,此时振动较大。 造成工件外表出现鱼鳞状痕迹的具体原因 是 1.砂轮外表有垃圾和油污物;