金属塑性成型原理-知识点
塑性成形原理知识点总结
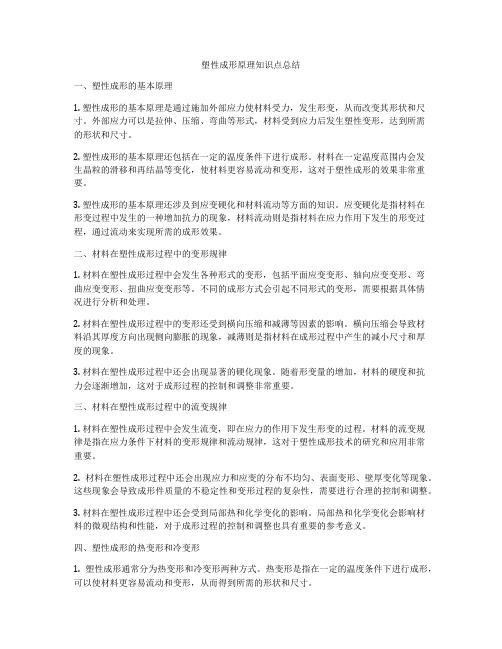
塑性成形原理知识点总结一、塑性成形的基本原理1. 塑性成形的基本原理是通过施加外部应力使材料受力,发生形变,从而改变其形状和尺寸。
外部应力可以是拉伸、压缩、弯曲等形式,材料受到应力后发生塑性变形,达到所需的形状和尺寸。
2. 塑性成形的基本原理还包括在一定的温度条件下进行成形。
材料在一定温度范围内会发生晶粒的滑移和再结晶等变化,使材料更容易流动和变形,这对于塑性成形的效果非常重要。
3. 塑性成形的基本原理还涉及到应变硬化和材料流动等方面的知识。
应变硬化是指材料在形变过程中发生的一种增加抗力的现象,材料流动则是指材料在应力作用下发生的形变过程,通过流动来实现所需的成形效果。
二、材料在塑性成形过程中的变形规律1. 材料在塑性成形过程中会发生各种形式的变形,包括平面应变变形、轴向应变变形、弯曲应变变形、扭曲应变变形等。
不同的成形方式会引起不同形式的变形,需要根据具体情况进行分析和处理。
2. 材料在塑性成形过程中的变形还受到横向压缩和减薄等因素的影响。
横向压缩会导致材料沿其厚度方向出现侧向膨胀的现象,减薄则是指材料在成形过程中产生的减小尺寸和厚度的现象。
3. 材料在塑性成形过程中还会出现显著的硬化现象。
随着形变量的增加,材料的硬度和抗力会逐渐增加,这对于成形过程的控制和调整非常重要。
三、材料在塑性成形过程中的流变规律1. 材料在塑性成形过程中会发生流变,即在应力的作用下发生形变的过程。
材料的流变规律是指在应力条件下材料的变形规律和流动规律,这对于塑性成形技术的研究和应用非常重要。
2. 材料在塑性成形过程中还会出现应力和应变的分布不均匀、表面变形、壁厚变化等现象。
这些现象会导致成形件质量的不稳定性和变形过程的复杂性,需要进行合理的控制和调整。
3. 材料在塑性成形过程中还会受到局部热和化学变化的影响。
局部热和化学变化会影响材料的微观结构和性能,对于成形过程的控制和调整也具有重要的参考意义。
四、塑性成形的热变形和冷变形1. 塑性成形通常分为热变形和冷变形两种方式。
金属塑性成型原理-知识点
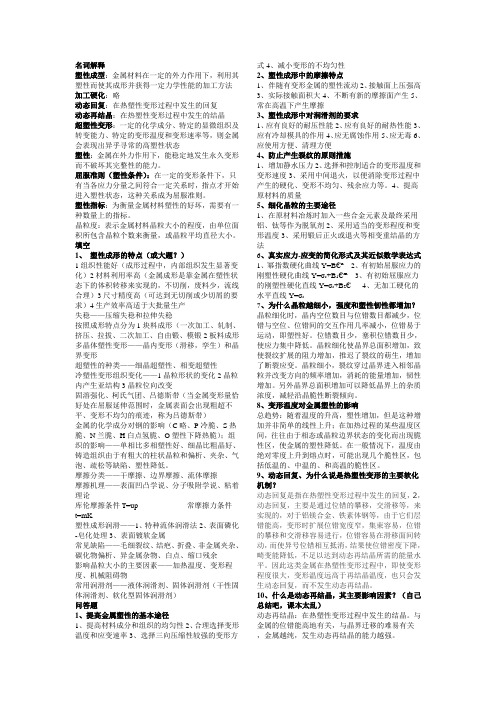
名词解释塑性成型:金属材料在一定的外力作用下,利用其塑性而使其成形并获得一定力学性能的加工方法加工硬化:略动态回复:在热塑性变形过程中发生的回复动态再结晶:在热塑性变形过程中发生的结晶超塑性变形:一定的化学成分、特定的显微组织及转变能力、特定的变形温度和变形速率等,则金属会表现出异乎寻常的高塑性状态塑性:金属在外力作用下,能稳定地发生永久变形而不破坏其完整性的能力。
屈服准则(塑性条件):在一定的变形条件下,只有当各应力分量之间符合一定关系时,指点才开始进入塑性状态,这种关系成为屈服准则。
塑性指标:为衡量金属材料塑性的好坏,需要有一种数量上的指标。
晶粒度:表示金属材料晶粒大小的程度,由单位面积所包含晶粒个数来衡量,或晶粒平均直径大小。
填空1、塑性成形的特点(或大题?)1组织性能好(成形过程中,内部组织发生显著变化)2材料利用率高(金属成形是靠金属在塑性状态下的体积转移来实现的,不切削,废料少,流线合理)3尺寸精度高(可达到无切削或少切屑的要求)4生产效率高适于大批量生产失稳——压缩失稳和拉伸失稳按照成形特点分为1块料成形(一次加工、轧制、挤压、拉拔、二次加工、自由锻、模锻2板料成形多晶体塑性变形——晶内变形(滑移,孪生)和晶界变形超塑性的种类——细晶超塑性、相变超塑性冷塑性变形组织变化——1晶粒形状的变化2晶粒内产生亚结构3晶粒位向改变固溶强化、柯氏气团、吕德斯带(当金属变形量恰好处在屈服延伸范围时,金属表面会出现粗超不平、变形不均匀的痕迹,称为吕德斯带)金属的化学成分对钢的影响(C略、P冷脆、S热脆、N兰脆、H白点氢脆、O塑性下降热脆);组织的影响——单相比多相塑性好、细晶比粗晶好、铸造组织由于有粗大的柱状晶粒和偏析、夹杂、气泡、疏松等缺陷、塑性降低。
摩擦分类——干摩擦、边界摩擦、流体摩擦摩擦机理——表面凹凸学说、分子吸附学说、粘着理论库伦摩擦条件T=up 常摩擦力条件t=mK塑性成形润滑——1、特种流体润滑法2、表面磷化-皂化处理3、表面镀软金属常见缺陷——毛细裂纹、结疤、折叠、非金属夹杂、碳化物偏析、异金属杂物、白点、缩口残余影响晶粒大小的主要因素——加热温度、变形程度、机械阻碍物常用润滑剂——液体润滑剂、固体润滑剂(干性固体润滑剂、软化型固体润滑剂)问答题1、提高金属塑性的基本途径1、提高材料成分和组织的均匀性2、合理选择变形温度和应变速率3、选择三向压缩性较强的变形方式4、减小变形的不均匀性2、塑性成形中的摩擦特点1、伴随有变形金属的塑性流动2、接触面上压强高3、实际接触面积大4、不断有新的摩擦面产生5、常在高温下产生摩擦3、塑性成形中对润滑剂的要求1、应有良好的耐压性能2、应有良好的耐热性能3、应有冷却模具的作用4、应无腐蚀作用5、应无毒6、应使用方便、清理方便4、防止产生裂纹的原则措施1、增加静水压力2、选择和控制适合的变形温度和变形速度3、采用中间退火,以便消除变形过程中产生的硬化、变形不均匀、残余应力等。
塑性成形原理知识点
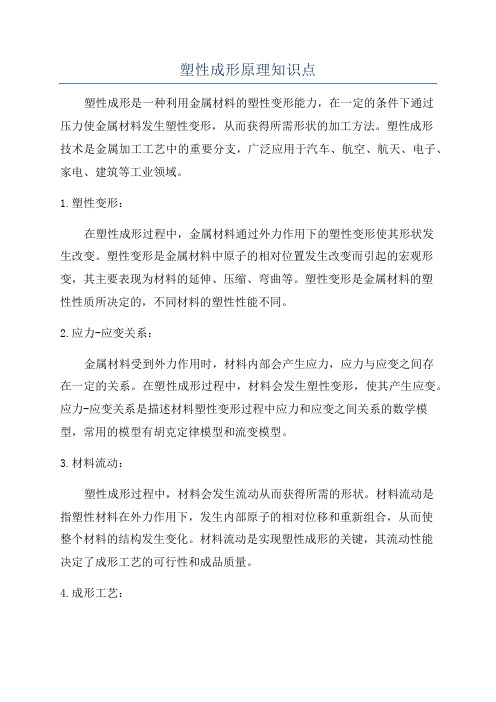
塑性成形原理知识点塑性成形是一种利用金属材料的塑性变形能力,在一定的条件下通过压力使金属材料发生塑性变形,从而获得所需形状的加工方法。
塑性成形技术是金属加工工艺中的重要分支,广泛应用于汽车、航空、航天、电子、家电、建筑等工业领域。
1.塑性变形:在塑性成形过程中,金属材料通过外力作用下的塑性变形使其形状发生改变。
塑性变形是金属材料中原子的相对位置发生改变而引起的宏观形变,其主要表现为材料的延伸、压缩、弯曲等。
塑性变形是金属材料的塑性性质所决定的,不同材料的塑性性能不同。
2.应力-应变关系:金属材料受到外力作用时,材料内部会产生应力,应力与应变之间存在一定的关系。
在塑性成形过程中,材料会发生塑性变形,使其产生应变。
应力-应变关系是描述材料塑性变形过程中应力和应变之间关系的数学模型,常用的模型有胡克定律模型和流变模型。
3.材料流动:塑性成形过程中,材料会发生流动从而获得所需的形状。
材料流动是指塑性材料在外力作用下,发生内部原子的相对位移和重新组合,从而使整个材料的结构发生变化。
材料流动是实现塑性成形的关键,其流动性能决定了成形工艺的可行性和成品质量。
4.成形工艺:塑性成形工艺是金属材料经过一系列工艺操作,通过压力使其发生塑性变形,最终获得所需形状的过程。
常见的塑性成形工艺包括冲压、拉伸、挤压、压铸、滚压等。
不同工艺适用于不同形状的零件,根据材料的性质和零件的要求选择合适的成形工艺。
5.工艺过程控制:塑性成形过程中,需要对各个环节进行控制以确保成品质量。
工艺过程控制包括工艺参数的选择、设备的调整、模具结构的设计等。
在塑性成形过程中,要控制好温度、应力、应变速率等因素,以避免过大的变形应力引起材料的断裂或变形过大导致零件尺寸偏差。
塑性成形技术不仅可以实现复杂形状的制造,而且可以提高材料的强度和刚度,降低材料的质量,节省原材料和能源。
因此,塑性成形技术在现代工业生产中具有重要的地位和应用价值。
金属塑性成形原理
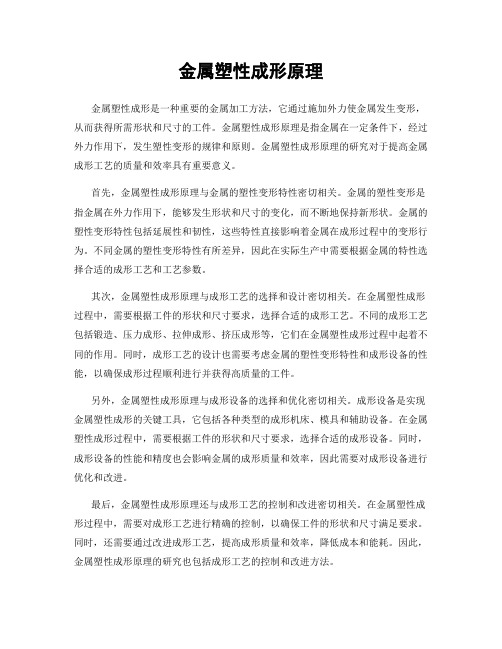
金属塑性成形原理金属塑性成形是一种重要的金属加工方法,它通过施加外力使金属发生变形,从而获得所需形状和尺寸的工件。
金属塑性成形原理是指金属在一定条件下,经过外力作用下,发生塑性变形的规律和原则。
金属塑性成形原理的研究对于提高金属成形工艺的质量和效率具有重要意义。
首先,金属塑性成形原理与金属的塑性变形特性密切相关。
金属的塑性变形是指金属在外力作用下,能够发生形状和尺寸的变化,而不断地保持新形状。
金属的塑性变形特性包括延展性和韧性,这些特性直接影响着金属在成形过程中的变形行为。
不同金属的塑性变形特性有所差异,因此在实际生产中需要根据金属的特性选择合适的成形工艺和工艺参数。
其次,金属塑性成形原理与成形工艺的选择和设计密切相关。
在金属塑性成形过程中,需要根据工件的形状和尺寸要求,选择合适的成形工艺。
不同的成形工艺包括锻造、压力成形、拉伸成形、挤压成形等,它们在金属塑性成形过程中起着不同的作用。
同时,成形工艺的设计也需要考虑金属的塑性变形特性和成形设备的性能,以确保成形过程顺利进行并获得高质量的工件。
另外,金属塑性成形原理与成形设备的选择和优化密切相关。
成形设备是实现金属塑性成形的关键工具,它包括各种类型的成形机床、模具和辅助设备。
在金属塑性成形过程中,需要根据工件的形状和尺寸要求,选择合适的成形设备。
同时,成形设备的性能和精度也会影响金属的成形质量和效率,因此需要对成形设备进行优化和改进。
最后,金属塑性成形原理还与成形工艺的控制和改进密切相关。
在金属塑性成形过程中,需要对成形工艺进行精确的控制,以确保工件的形状和尺寸满足要求。
同时,还需要通过改进成形工艺,提高成形质量和效率,降低成本和能耗。
因此,金属塑性成形原理的研究也包括成形工艺的控制和改进方法。
综上所述,金属塑性成形原理是金属塑性成形过程中的基本规律和原则,它涉及金属的塑性变形特性、成形工艺的选择和设计、成形设备的选择和优化、成形工艺的控制和改进等方面。
金属塑性成形知识点

1、塑性:塑性成形的定义?答.塑性是指在外力作用下,材料能稳定地发生永久变形而不破坏其完整性的能力。
形指利用外力使金属材料产生塑性变形,改变形状、尺寸和改善性能,品的加工方法。
2、塑性成形的特点,规律?答:特点①能改善金属的组织,率较高,适用于大批量生产规律:①最小阻力定律②加工硬化规律,总是向最小阻力方向移动3、影响塑性的主要因素?答:变形温度,变形速度,变形程度,分,组织结构,应力状态,周围介质4、如何提高塑性?答:强的变形方式④减小变形的不均匀性5、三个摩擦条件?答;变条件6、平面应力与平面应变的区别。
平面应力:只在平面内有应力,向的应力可忽略,例如薄板拉压问题。
平面应变:只在平面内有应变,7、平面应力状态。
答:在研究受力构件一点应力状态中,间状态下可有3个方向的x轴,y轴,z在空间状态下可在3如果点在空间中仅在2即所有应力分量均处于同一个平面内,种状态为平面应力状态。
8、金属的超塑性答:是指金属材料在一定的内部条件组织形态)和外部条件(变形温度、等)下所显示的极高塑性。
10 尺寸和改善性能,,规律?规律:变形速度,变形程度,只在平面内有应力,只在平面内有应变,3个方向轴,z32和外部条件(变形温度、.塑性是指在外力作用下,材料能稳定地发尺寸和改善性能,,规律?答:特点①能改善金属的组织,率较高,适用于大批量生产规律:①最小阻力变形温度,变形速度,变形程度,只在平面内有应力,只在平面内有应变,在研究受力构件一点应力状态中,3个方向轴,y轴,z32是指金属材料在一定的内部条件和外部条件(变形温度、塑性成使其尺寸和改善性能,从而获得各种产,规律?金属质点在塑性x轴,y轴,z轴)应3个平面上存在应2个方向存在应力分量,即。
金属塑性成形原理
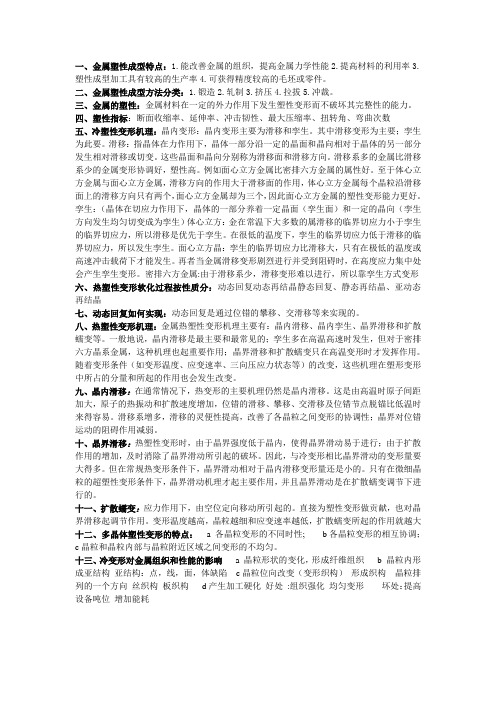
一、金属塑性成型特点:1.能改善金属的组织,提高金属力学性能2.提高材料的利用率3.塑性成型加工具有较高的生产率4.可获得精度较高的毛坯或零件。
二、金属塑性成型方法分类:1.锻造2.轧制3.挤压4.拉拔5.冲裁。
三、金属的塑性:金属材料在一定的外力作用下发生塑性变形而不破坏其完整性的能力。
四、塑性指标:断面收缩率、延伸率、冲击韧性、最大压缩率、扭转角、弯曲次数五、冷塑性变形机理:晶内变形:晶内变形主要为滑移和孪生。
其中滑移变形为主要;孪生为此要。
滑移:指晶体在力作用下,晶体一部分沿一定的晶面和晶向相对于晶体的另一部分发生相对滑移或切变。
这些晶面和晶向分别称为滑移面和滑移方向。
滑移系多的金属比滑移系少的金属变形协调好,塑性高。
例如面心立方金属比密排六方金属的属性好。
至于体心立方金属与面心立方金属,滑移方向的作用大于滑移面的作用,体心立方金属每个晶粒沿滑移面上的滑移方向只有两个,面心立方金属却为三个,因此面心立方金属的塑性变形能力更好。
孪生:(晶体在切应力作用下,晶体的一部分养着一定晶面(孪生面)和一定的晶向(孪生方向发生均匀切变成为孪生)体心立方:金在常温下大多数的属滑移的临界切应力小于孪生的临界切应力,所以滑移是优先于孪生。
在很低的温度下,孪生的临界切应力低于滑移的临界切应力,所以发生孪生。
面心立方晶:孪生的临界切应力比滑移大,只有在极低的温度或高速冲击载荷下才能发生。
再者当金属滑移变形剧烈进行并受到阻碍时,在高度应力集中处会产生孪生变形。
密排六方金属:由于滑移系少,滑移变形难以进行,所以靠孪生方式变形六、热塑性变形软化过程按性质分:动态回复动态再结晶静态回复、静态再结晶、亚动态再结晶七、动态回复如何实现:动态回复是通过位错的攀移、交滑移等来实现的。
八、热塑性变形机理:金属热塑性变形机理主要有:晶内滑移、晶内孪生、晶界滑移和扩散蠕变等。
一般地说,晶内滑移是最主要和最常见的;孪生多在高温高速时发生,但对于密排六方晶系金属,这种机理也起重要作用;晶界滑移和扩散蠕变只在高温变形时才发挥作用。
金属塑性成形原理
第一章在外力作用下使金属材料发生塑性变形而不破坏其完整性的能力称为塑性。
金属材料在一定的外力作用下,利用其塑性而使其成形并获得一定力学性能的加工方法称为塑性成形,也称塑性加工或压力加工。
金属塑性成形的特点:(1)组织、性能好(2)材料利用率高。
(3)尺寸精度高。
(4)生产效率高,适于大批量的生产。
第二章P7)当晶体受力时,由于各个滑移系相对于外力的空间位向不同,其上所作用的切应力分量的大小也必然不同。
现设某一晶体作用有由拉力P引起的拉伸应力σ,其滑移面的法线方向与拉伸轴的夹角为φ,面上的滑移方向与拉伸轴的夹角为λ(见图),通过简单的静力学分析可知,在此滑移方向上的切应力分量为τ=σcosφcosλ。
令μ=cosφcosλ,称为取向因子。
若φ=λ=45,则μ=μmax=0.5,τ=τmax=σ/2。
此意味着该滑移系处于最佳取向,其上的切应力分量最有利于优先达到临界值而发生滑移,而当φ=90,λ=0或φ=0,λ=90时,μ=τ=0此时无论σ多大,滑移的驱动力恒等于零,处于此取向的滑移系不能发生滑移。
晶体滑移时的应力分析由于塑性变形使金属内部组织发生变化,因而金属的性能也发生相应的改变。
其中变化最显著的是金属的力学性能,即随着变形程度的增加,金属的强度、硬度增加,而塑性韧性降低,这种现象称为加工硬化。
例子:P18~19P28将不同变形温度和在此温度下的不同变形程度、以及发生再结晶后空冷所得的晶粒大小,画成立体图,称为第二类再结晶图或动态再结晶图。
GH4037镍基高温合金的动态再结晶图P31所谓超塑性,可以理解为金属和合金具有超常的均匀变形能力,其伸长率达到百分之几百、甚至百分之几千。
P40塑性是指金属在外力作用下,能稳定地发生永久变形而不破坏其完整性的能力,它是金属的一种重要的加工性能。
为了衡量金属材料塑性的好坏,需要有一种数量上的指标,称为塑性指标。
塑性指标是以材料开始破坏时的塑性变形量来表示,它可以借助于各种实验方法来测定。
金属塑性成形原理知识点
金属塑性成形原理知识点弹性:材料的可恢复变形的能力。
塑性:在外力作用下使金属材料发生塑性变形而不破坏其完整性的能力。
塑性变形:材料在一定外力作用下,利用其塑性而使其成型并获得一定力学性能的加工方法。
塑性成形:金属材料在一定的外力作用下,利用其塑性而使其成形并获得一定力学性能的加工方法。
塑性成形的特点:组织性能好、材料利用率高、生产效率高、尺寸精度高、设备相对复杂。
冷态塑性变形的机理:晶内变形(滑移和孪生)和晶间变形(滑动和转动)滑移:晶体在力的作用下,晶体的一部分沿一定的晶面(滑移面)和晶向(滑移向)相对于晶体的另一部分发生相对移动或切变。
孪生:晶体在力的作用下,晶体的一部分沿一定的晶面(孪生面)和晶向(孪生向)发生均匀切边滑移面:滑移中,晶体沿着相对滑动的晶面。
滑移方向:滑移中,晶体沿着相对滑动的晶向。
塑性变形的特点:不同时性、不均匀性、相互协调性。
合金:合金是由两种或者两种以上的金属元素或者金属元素与非金属元素组成具有金属特性的物质。
合金分为固溶体(间隙固溶体、置换固溶体)和化合物(正常价、电子价、间隙化合物)固溶强化:以间隙或者置换的方式融入基体的金属所产生的强化。
弥散强化:若第二项是通过粉末冶金的方法加入而引起的强化。
时效强化:若第二项为力是通过对过饱和固溶体的时效处理而沉淀析出并产生强化。
冷态下的塑性变形对组织性能的影响:组织:晶粒形状发生变化,产生纤维组织晶粒内部产生亚晶结构第 1 页晶粒位向改变:产生丝织构和板织构性能:产生加工硬化(随着塑性变形的程度的增加,金属的塑性韧性降低,强度硬度提高的现象)加工硬化的优点:变形均匀,减小局部变薄,增大成形极限缺点:塑性降低、变形抗力提高、变形困难。
热塑性变形的软化过程:动态回复、动态再结晶、静态回复、静态再结晶、亚动态再结晶金泰回复:从热力学角度,变形引起金属内能增加,而处于稳定的高自用能状态具有向变形前低自由能状态自发恢复的趋势静态再结晶:冷变形金属加热到更高温度后,在原来版型体中金属会重新形成无畸变的等轴晶直至完全取代金属的冷组织的过程。
金属塑性成形原理
金属塑性成形原理金属塑性成形是指通过外力作用下,金属材料在一定温度范围内发生塑性变形的过程。
金属塑性成形是制造工业中常用的一种加工方法,它能够制造出各种形状和尺寸的零部件,广泛应用于汽车、航空航天、机械制造等领域。
金属塑性成形的原理是基于金属材料的内部结构和性能特点,通过外力使其发生形变,从而得到所需的形状和尺寸。
金属材料的塑性成形主要依靠金属的塑性变形特性,其原理主要包括以下几个方面:一、应力和应变。
金属材料在受到外力作用时,会产生应力和应变。
应力是单位面积上的力,而应变是单位长度上的变形量。
金属材料在受到外力作用时,会发生应力和应变的变化,从而产生塑性变形。
二、晶粒滑移。
金属材料的内部结构是由大量的晶粒组成的,晶粒之间存在着晶界。
当金属受到外力作用时,晶粒会沿着晶界发生滑移,从而使得金属材料发生塑性变形。
晶粒滑移是金属塑性成形的重要原理之一。
三、冷加工和热加工。
金属材料在不同温度下的塑性变形特性是不同的。
在常温下进行的金属塑性成形称为冷加工,而在一定温度范围内进行的金属塑性成形称为热加工。
冷加工和热加工对金属材料的塑性成形有着不同的影响,需要根据具体的工艺要求来选择合适的加工方法。
四、金属材料的变形机制。
金属材料的塑性变形主要有拉伸、压缩、弯曲、挤压等形式。
这些变形机制是通过外力作用下,金属材料内部晶粒的滑移和变形来实现的。
不同的变形机制对应着不同的加工工艺和设备,需要根据具体的要求来选择合适的成形方式。
综上所述,金属塑性成形的原理是基于金属材料的内部结构和性能特点,通过外力使其发生形变,从而得到所需的形状和尺寸。
金属塑性成形是制造工业中常用的一种加工方法,它能够制造出各种形状和尺寸的零部件,广泛应用于汽车、航空航天、机械制造等领域。
深入理解金属塑性成形的原理,对于提高加工工艺的效率和质量具有重要意义。
金属塑性成形原理
1.金属塑性成形是金属加工的方法之一,它是在外力作用下使金属产生塑性变形,从而将工件加工成所需形状和尺寸的加工方法。
2.金属塑性成形的特点:1.组织,性能得到改善和提高2.材料利用率高3.生产效率高4.尺寸精度高3.金属塑性成形分类:按照成形的特点不同将塑性加工分为轧制,拉拔,挤压,锻造和冲压。
按成形时工件温度不同分为热成形,冷成形和温成形。
4.塑性理论采用的假设:1.变形体是连续的,即整个变形体内不存在任何空隙。
2.变形体是均质的和各向同性的。
3.在变形的任意瞬间,力的作用是平衡的。
4.在一般情况下,忽略体积力的影响。
5.在变形的任意瞬间,体积不变。
5.塑性变形是利用金属的塑性,在外力作用下使金属成形的一种加工方法。
作用于金属的外力分为两类:一类是作用在金属表面上的力,称为面力,它可以是集中力,但更一般的是分布力,面力可以分为作用力,反作用力和摩擦力。
第二类是作用在金属每个质点上的力,称为体积力。
6.主应力的概念:切应力为零的平面叫做主平面,主平面上的正应力叫做主应力,7.应力张量不变量:对于一个确定的应力状态,只能有一组主应力。
因此应力状态特征方程的系数都应该是单值,不随坐标而变,分别称为应力张量的第一,二,三变量。
8.主切应力:切应力随斜面上的方位而变化,当斜面上的切应力为极大值时,该切应力称为主切应力。
三个切应力中绝对值最大的一个叫做最大切应力。
9.应力张量的分解:按照应力叠加原理,表示受力物体内任一点应力状态的应力张量可以分解为应力球张量和应力偏张量。
10.应力球张量和应力偏张量的物理意义:由于球应力状态在任何斜面上都没有切应力,所以应力球张量不能使物体产生形状变化,只能产生体积变化。
被分解出的应力球张量没有切应力,任意方向都是主方向且主应力相等。
因而应力偏张量使物体产生形状变化,而不能产生体积变化,材料的塑性变形就是由应力偏张量引起的。
11.平面应力状态的特点:①.变形体内各质点在与某一方向(如z 向)垂直的平面没有应力作用,即0===zy zx z ττσ,z 轴为主方向,只有xy y x τσσ、、三个应力分量:②.xy y x τσσ、、沿z 轴方向均匀分布,即应力分量与z 轴无关,对z 的偏导数为零。
- 1、下载文档前请自行甄别文档内容的完整性,平台不提供额外的编辑、内容补充、找答案等附加服务。
- 2、"仅部分预览"的文档,不可在线预览部分如存在完整性等问题,可反馈申请退款(可完整预览的文档不适用该条件!)。
- 3、如文档侵犯您的权益,请联系客服反馈,我们会尽快为您处理(人工客服工作时间:9:00-18:30)。
名师整理精华知识点
名词解释
塑性成型:金属材料在一定的外力作用下,利用其塑性而使其成形并获得一定力学性能的加工方法
加工硬化:略
动态回复:在热塑性变形过程中发生的回复
动态再结晶:在热塑性变形过程中发生的结晶
超塑性变形:一定的化学成分、特定的显微组织及转变能力、特定的变形温度和变形速率等,则金属会表现出异乎寻常的高塑性状态
塑性:金属在外力作用下,能稳定地发生永久变形而不破坏其完整性的能力。
屈服准则(塑性条件):在一定的变形条件下,只有当各应力分量之间符合一定关系时,指点才开始进入塑性状态,这种关系成为屈服准则。
塑性指标:为衡量金属材料塑性的好坏,需要有一种数量上的指标。
晶粒度:表示金属材料晶粒大小的程度,由单位面积所包含晶粒个数来衡量,或晶粒平均直径大小。
填空
1、塑性成形的特点(或大题?)
1组织性能好(成形过程中,内部组织发生显著变化)2材料利用率高(金属成形是靠金属在塑性状态下的体积转移来实现的,不切削,废料少,流线合理)3尺寸精度高(可达到无切削或少切屑的要求)4生产效率高适于大批量生产
失稳——压缩失稳和拉伸失稳
按照成形特点分为1块料成形(一次加工、轧制、挤压、拉拔、二次加工、自由锻、模锻2板料成形多晶体塑性变形——晶内变形(滑移,孪生)和晶界变形
超塑性的种类——细晶超塑性、相变超塑性
冷塑性变形组织变化——1晶粒形状的变化2晶粒内产生亚结构3晶粒位向改变
固溶强化、柯氏气团、吕德斯带(当金属变形量恰好处在屈服延伸范围时,金属表面会出现粗超不平、变形不均匀的痕迹,称为吕德斯带)
金属的化学成分对钢的影响(C略、P冷脆、S热脆、N兰脆、H白点氢脆、O塑性下降热脆);组织的影响——单相比多相塑性好、细晶比粗晶好、铸造组织由于有粗大的柱状晶粒和偏析、夹杂、气泡、疏松等缺陷、塑性降低。
摩擦分类——干摩擦、边界摩擦、流体摩擦
摩擦机理——表面凹凸学说、分子吸附学说、粘着理论
库伦摩擦条件T=up 常摩擦力条件
t=mK
塑性成形润滑——1、特种流体润滑法2、表面磷化-皂化处理3、表面镀软金属
常见缺陷——毛细裂纹、结疤、折叠、非金属夹杂、碳化物偏析、异金属杂物、白点、缩口残余
影响晶粒大小的主要因素——加热温度、变形程度、机械阻碍物
常用润滑剂——液体润滑剂、固体润滑剂(干性固体润滑剂、软化型固体润滑剂)
问答题
1、提高金属塑性的基本途径
1、提高材料成分和组织的均匀性
2、合理选择变形温度和应变速率
3、选择三向压缩性较强的变形方式
4、减小变形的不均匀性
2、塑性成形中的摩擦特点
1、伴随有变形金属的塑性流动
2、接触面上压强高
3、实际接触面积大
4、不断有新的摩擦面产生
5、常在高温下产生摩擦
3、塑性成形中对润滑剂的要求
1、应有良好的耐压性能
2、应有良好的耐热性能
3、应有冷却模具的作用
4、应无腐蚀作用
5、应无毒
6、应使用方便、清理方便
4、防止产生裂纹的原则措施
1、增加静水压力
2、选择和控制适合的变形温度和变形速度
3、采用中间退火,以便消除变形过程中产生的硬化、变形不均匀、残余应力等。
4、提高原材料的质量
5、细化晶粒的主要途径
1、在原材料冶炼时加入一些合金元素及最终采用铝、钛等作为脱氧剂
2、采用适当的变形程度和变形温度
3、采用锻后正火或退火等相变重结晶的方法
6、真实应力-应变的简化形式及其近似数学表达式1、幂指数硬化曲线Y=BЄn 2、有初始屈服应力的刚塑性硬化曲线Y=σs+B1Єm 3、有初始屈服应力的刚塑性硬化直线Y=σs+B2Є4、无加工硬化的水平直线Y=σs
7、为什么晶粒越细小,强度和塑性韧性都增加?晶粒细化时,晶内空位数目与位错数目都减少,位错与空位、位错间的交互作用几率减小,位错易于运动,即塑性好。
位错数目少,塞积位错数目少,使应力集中降低。
晶粒细化使晶界总面积增加,致使裂纹扩展的阻力增加,推迟了裂纹的萌生,增加了断裂应变。
晶粒细小,裂纹穿过晶界进入相邻晶粒并改变方向的频率增加,消耗的能量增加,韧性增加。
另外晶界总面积增加可以降低晶界上的杂质浓度,减轻沿晶脆性断裂倾向。
8、变形温度对金属塑性的影响
总趋势:随着温度的升高,塑性增加,但是这种增加并非简单的线性上升;在加热过程的某些温度区间,往往由于相态或晶粒边界状态的变化而出现脆性区,使金属的塑性降低。
在一般情况下,温度由绝对零度上升到熔点时,可能出现几个脆性区,包括低温的、中温的、和高温的脆性区。
9、动态回复、为什么说是热塑性变形的主要软化机制?
动态回复是指在热塑性变形过程中发生的回复,2,动态回复,主要是通过位错的攀移,交滑移等,来实现的,对于铝镁合金、铁素体钢等,由于它们层错能高,变形时扩展位错宽度窄,集束容易,位错的攀移和交滑移容易进行,位错容易在滑移面间转动,而使异号位错相互抵消,结果使位错密度下降,畸变能降低,不足以达到动态再结晶所需的能量水平。
因此这类金属在热塑性变形过程中,即使变形程度很大,变形温度远高于再结晶温度,也只会发生动态回复,而不发生动态再结晶。
10、什么是动态再结晶,其主要影响因素?(自己总结吧,课本太乱)
动态再结晶:在热塑性变形过程中发生的结晶。
与金属的位错能高地有关,与晶界迁移的难易有关
,金属越纯,发生动态再结晶的能力越强。