氮化铝粉末的制备方法与机理
氮化铝制备方法

氮化铝制备方法
一、背景介绍
氮化铝是一种重要的陶瓷材料,具有优异的物理、化学性质,广泛应用于电子、光电、航空等领域。
氮化铝制备方法的研究已经成为材料科学领域的热点之一。
二、传统制备方法
1. 热压法:将氮化铝粉末放入模具中,在高温高压下进行热压,使其致密化。
2. 真空烧结法:将氮化铝粉末在真空条件下进行烧结,使其致密化。
3. 气相沉积法:将金属铝和氨气反应,生成氮化铝薄膜。
三、新型制备方法
1. 溶胶-凝胶法:将金属铝与硝酸反应生成硝酸铝溶液,加入尿素后进行水解和聚合反应,在高温下得到氮化铝凝胶,再进行热处理得到氮化铝陶瓷。
2. 气相转移法:将金属铝和氨在高温下反应生成AlN蒸汽,然后通过惰性气体输送到基板上,在基板上沉积出氮化铝薄膜。
3. 气相热解法:将金属铝和氨在高温下反应生成AlN蒸汽,然后通过惰性气体输送到高温反应室中,在高温下进行热解反应,得到氮化铝粉末。
四、制备方法的优缺点比较
1. 传统制备方法:
优点:制备工艺简单,成本低。
缺点:制备出来的氮化铝材料致密度不高,力学性能较差。
2. 新型制备方法:
优点:制备出来的氮化铝材料致密度高,力学性能好。
缺点:制备工艺复杂,成本较高。
五、结论
随着科技的发展和人们对材料性能要求的提高,新型氮化铝制备方法逐渐替代传统方法成为主流。
但是,在实际应用中需要根据具体情况选择合适的制备方法。
氮化铝陶瓷粉体制备方法研究进展

氮化铝陶瓷粉体制备方法研究进展
随着科学技术的不断发展,高性能氮化铝陶瓷材料的研究备受关注。
而氮化铝陶瓷粉体的制备方法则是氮化铝陶瓷材料研究的重要基础。
本文主要介绍了氮化铝陶瓷粉体制备方法的研究进展。
一、热反应法
热反应法是最早用于制备氮化铝粉体的方法,其原理是利用反应热将铝和氮化物转化为氮化铝。
热反应法具有制备工艺简单、反应速度较快等优点,但也存在着反应条件难以控制、产物结晶度低等缺点。
氮气反应法是利用氮气和铝在高温下进行反应,得到氮化铝粉末的一种方法。
该方法主要优点为可获得高纯度且晶粒细小的氮化铝粉末,但需要高温高压条件,能耗较高。
三、溶胶凝胶法
溶胶凝胶法是采用溶胶化学原理,将金属的氧化物转化为高分子物质,并通过热处理方法转化为金属氧化物、金属化合物、金属、无机和有机骨架,从而获得氮化铝粉末。
溶胶凝胶法具有借助化学反应实现制备、反应速度高、制备出的产品具有较高精度控制等优点。
四、氧化还原法
氧化还原法是指先将铝与氮化物加入反应器中,再加热至高温,经氮气氛围下还原,得到氮化铝粉末。
氧化还原法制备氮化铝粉末优点是制备出的粉末具有较高的晶粒度以及良好的流动性,但需要高温高压条件,对反应器的材料要求较高,同时还存在着反应难度较大且产物中存在少量杂质的问题。
综上所述,氮化铝陶瓷粉体的制备方法具有各自的优缺点,应根据不同的应用需求选择合适的制备方法。
未来应进一步探索制备高性能氮化铝陶瓷粉体的新方法,并提高制备粉体的纯度、成分均匀性和产品性能。
氮化铝陶瓷粉体制备方法研究进展
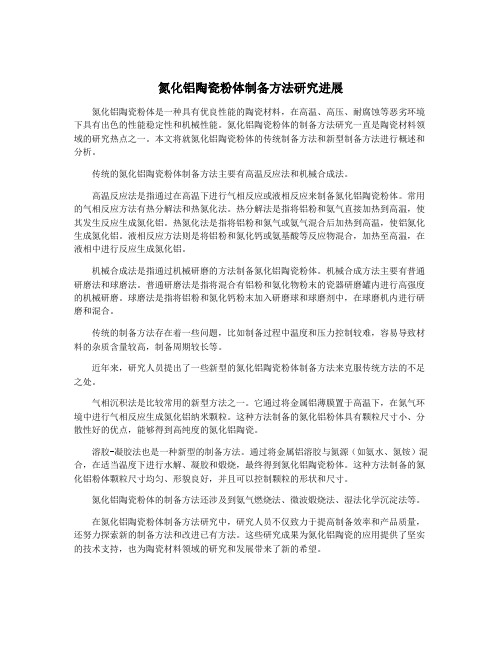
氮化铝陶瓷粉体制备方法研究进展氮化铝陶瓷粉体是一种具有优良性能的陶瓷材料,在高温、高压、耐腐蚀等恶劣环境下具有出色的性能稳定性和机械性能。
氮化铝陶瓷粉体的制备方法研究一直是陶瓷材料领域的研究热点之一。
本文将就氮化铝陶瓷粉体的传统制备方法和新型制备方法进行概述和分析。
传统的氮化铝陶瓷粉体制备方法主要有高温反应法和机械合成法。
高温反应法是指通过在高温下进行气相反应或液相反应来制备氮化铝陶瓷粉体。
常用的气相反应方法有热分解法和热氮化法。
热分解法是指将铝粉和氨气直接加热到高温,使其发生反应生成氮化铝。
热氮化法是指将铝粉和氮气或氨气混合后加热到高温,使铝氮化生成氮化铝。
液相反应方法则是将铝粉和氮化钙或氨基酸等反应物混合,加热至高温,在液相中进行反应生成氮化铝。
机械合成法是指通过机械研磨的方法制备氮化铝陶瓷粉体。
机械合成方法主要有普通研磨法和球磨法。
普通研磨法是指将混合有铝粉和氨化物粉末的瓷器研磨罐内进行高强度的机械研磨。
球磨法是指将铝粉和氮化钙粉末加入研磨球和球磨剂中,在球磨机内进行研磨和混合。
传统的制备方法存在着一些问题,比如制备过程中温度和压力控制较难,容易导致材料的杂质含量较高,制备周期较长等。
近年来,研究人员提出了一些新型的氮化铝陶瓷粉体制备方法来克服传统方法的不足之处。
气相沉积法是比较常用的新型方法之一。
它通过将金属铝薄膜置于高温下,在氮气环境中进行气相反应生成氮化铝纳米颗粒。
这种方法制备的氮化铝粉体具有颗粒尺寸小、分散性好的优点,能够得到高纯度的氮化铝陶瓷。
溶胶-凝胶法也是一种新型的制备方法。
通过将金属铝溶胶与氮源(如氨水、氮铵)混合,在适当温度下进行水解、凝胶和煅烧,最终得到氮化铝陶瓷粉体。
这种方法制备的氮化铝粉体颗粒尺寸均匀、形貌良好,并且可以控制颗粒的形状和尺寸。
氮化铝陶瓷粉体的制备方法还涉及到氨气燃烧法、微波煅烧法、湿法化学沉淀法等。
在氮化铝陶瓷粉体制备方法研究中,研究人员不仅致力于提高制备效率和产品质量,还努力探索新的制备方法和改进已有方法。
氮化铝粉末的生产工艺

氮化铝粉末的生产工艺氮化铝是一种具有高熔点、高硬度和优异导热性能的陶瓷材料,广泛应用于电子、光电子和航空航天等领域。
氮化铝粉末的生产工艺是通过化学气相沉积(CVD)或热反应法制备。
在化学气相沉积法中,氨气(NH3)和氮气(N2)作为反应气体在反应室中与铝源(通常为三乙酰丙酮铝等有机铝化合物)反应,生成氮化铝。
具体工艺如下:1. 反应装置:通常为石英管炉或Kiln炉。
反应装置分为加热区、反应区和冷却区。
加热区通过电加热将反应装置加热到适宜温度。
2. 反应气体:将氨气和氮气按一定比例混合,供给到反应装置中。
氨气作为还原剂与铝源反应生成氮化铝。
3. 金属铝源:一般使用有机铝化合物作为金属铝源,例如三乙酰丙酮铝等。
4. 反应温度:根据实际工艺要求,通常在1500℃-2000℃之间选择合适的反应温度。
5. 沉积反应:反应开始后,铝源和氨气在高温下通过化学反应生成氮化铝。
反应过程中需要保持合适的气氛,并严格控制氨气和氮气的流量和比例。
6. 冷却处理:反应结束后,需要将产物冷却至室温。
冷却过程需要缓慢进行,以避免氮化铝产物受到机械应力的破坏。
在热反应法中,常用的工艺为高温固相反应。
具体工艺如下:1. 原料准备:准备高纯度的氮化铝原料,一般为高纯度的氨气和氧化铝。
2. 原料混合:将氨气和氧化铝按一定比例混合均匀,制成混合料。
3. 热反应:将混合料放入高温炉中,在高温下进行热反应。
反应过程中,氨气与氧化铝发生反应生成氮化铝。
反应温度通常在1400℃-1800℃之间。
4. 冷却处理:反应结束后,将产物冷却至室温。
冷却过程需要缓慢进行,以避免氮化铝产物受到机械应力的破坏。
无论是化学气相沉积法还是热反应法,生产氮化铝粉末主要受反应温度、反应气氛和反应时间等因素的影响。
工艺参数的优化可以提高产率、改善产品性能,并控制产物的粒径和形貌。
此外,生产过程中需要注意安全措施,防止有害气体泄漏和环境污染。
氮化铝陶瓷粉体制备方法研究进展
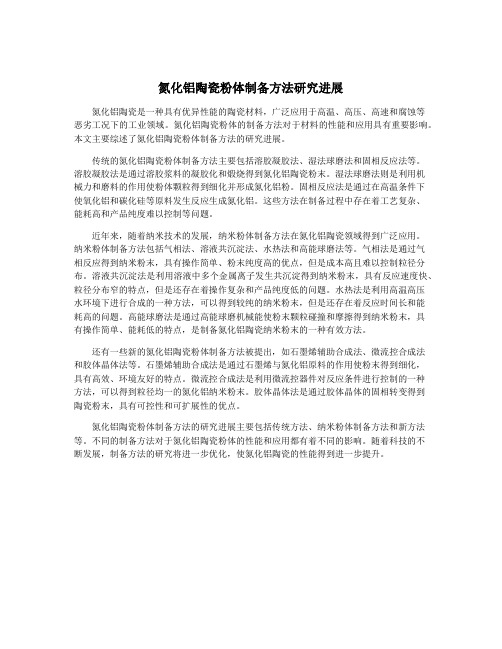
氮化铝陶瓷粉体制备方法研究进展氮化铝陶瓷是一种具有优异性能的陶瓷材料,广泛应用于高温、高压、高速和腐蚀等恶劣工况下的工业领域。
氮化铝陶瓷粉体的制备方法对于材料的性能和应用具有重要影响。
本文主要综述了氮化铝陶瓷粉体制备方法的研究进展。
传统的氮化铝陶瓷粉体制备方法主要包括溶胶凝胶法、湿法球磨法和固相反应法等。
溶胶凝胶法是通过溶胶浆料的凝胶化和煅烧得到氮化铝陶瓷粉末。
湿法球磨法则是利用机械力和磨料的作用使粉体颗粒得到细化并形成氮化铝粉。
固相反应法是通过在高温条件下使氧化铝和碳化硅等原料发生反应生成氮化铝。
这些方法在制备过程中存在着工艺复杂、能耗高和产品纯度难以控制等问题。
近年来,随着纳米技术的发展,纳米粉体制备方法在氮化铝陶瓷领域得到广泛应用。
纳米粉体制备方法包括气相法、溶液共沉淀法、水热法和高能球磨法等。
气相法是通过气相反应得到纳米粉末,具有操作简单、粉末纯度高的优点,但是成本高且难以控制粒径分布。
溶液共沉淀法是利用溶液中多个金属离子发生共沉淀得到纳米粉末,具有反应速度快、粒径分布窄的特点,但是还存在着操作复杂和产品纯度低的问题。
水热法是利用高温高压水环境下进行合成的一种方法,可以得到较纯的纳米粉末,但是还存在着反应时间长和能耗高的问题。
高能球磨法是通过高能球磨机械能使粉末颗粒碰撞和摩擦得到纳米粉末,具有操作简单、能耗低的特点,是制备氮化铝陶瓷纳米粉末的一种有效方法。
还有一些新的氮化铝陶瓷粉体制备方法被提出,如石墨烯辅助合成法、微流控合成法和胶体晶体法等。
石墨烯辅助合成法是通过石墨烯与氮化铝原料的作用使粉末得到细化,具有高效、环境友好的特点。
微流控合成法是利用微流控器件对反应条件进行控制的一种方法,可以得到粒径均一的氮化铝纳米粉末。
胶体晶体法是通过胶体晶体的固相转变得到陶瓷粉末,具有可控性和可扩展性的优点。
氮化铝陶瓷粉体制备方法的研究进展主要包括传统方法、纳米粉体制备方法和新方法等。
不同的制备方法对于氮化铝陶瓷粉体的性能和应用都有着不同的影响。
【精品文章】氮化铝粉体制备及氮化铝陶瓷烧结方法简介
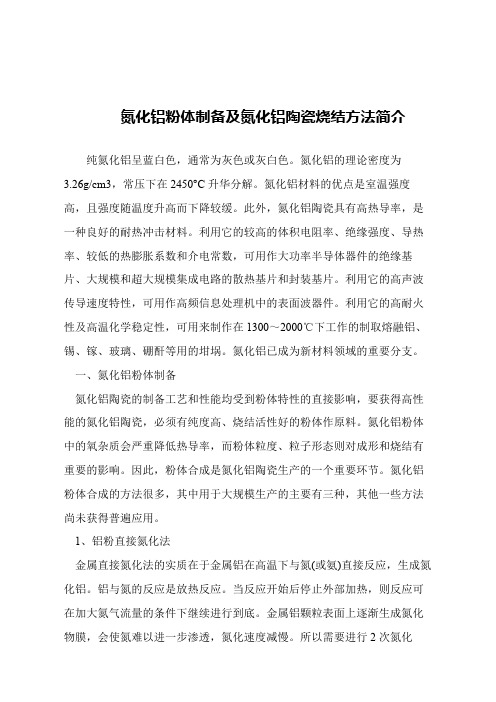
氮化铝粉体制备及氮化铝陶瓷烧结方法简介
纯氮化铝呈蓝白色,通常为灰色或灰白色。
氮化铝的理论密度为
3.26g/cm3,常压下在2450°C升华分解。
氮化铝材料的优点是室温强度高,且强度随温度升高而下降较缓。
此外,氮化铝陶瓷具有高热导率,是一种良好的耐热冲击材料。
利用它的较高的体积电阻率、绝缘强度、导热率、较低的热膨胀系数和介电常数,可用作大功率半导体器件的绝缘基片、大规模和超大规模集成电路的散热基片和封装基片。
利用它的高声波传导速度特性,可用作高频信息处理机中的表面波器件。
利用它的高耐火性及高温化学稳定性,可用来制作在1300~2000℃下工作的制取熔融铝、锡、镓、玻璃、硼酐等用的坩埚。
氮化铝已成为新材料领域的重要分支。
一、氮化铝粉体制备
氮化铝陶瓷的制备工艺和性能均受到粉体特性的直接影响,要获得高性能的氮化铝陶瓷,必须有纯度高、烧结活性好的粉体作原料。
氮化铝粉体中的氧杂质会严重降低热导率,而粉体粒度、粒子形态则对成形和烧结有重要的影响。
因此,粉体合成是氮化铝陶瓷生产的一个重要环节。
氮化铝粉体合成的方法很多,其中用于大规模生产的主要有三种,其他一些方法尚未获得普遍应用。
1、铝粉直接氮化法
金属直接氮化法的实质在于金属铝在高温下与氮(或氨)直接反应,生成氮化铝。
铝与氮的反应是放热反应。
当反应开始后停止外部加热,则反应可在加大氮气流量的条件下继续进行到底。
金属铝颗粒表面上逐渐生成氮化物膜,会使氮难以进一步渗透,氮化速度减慢。
所以需要进行2次氮化。
氮化铝粉末的制备方法与机理
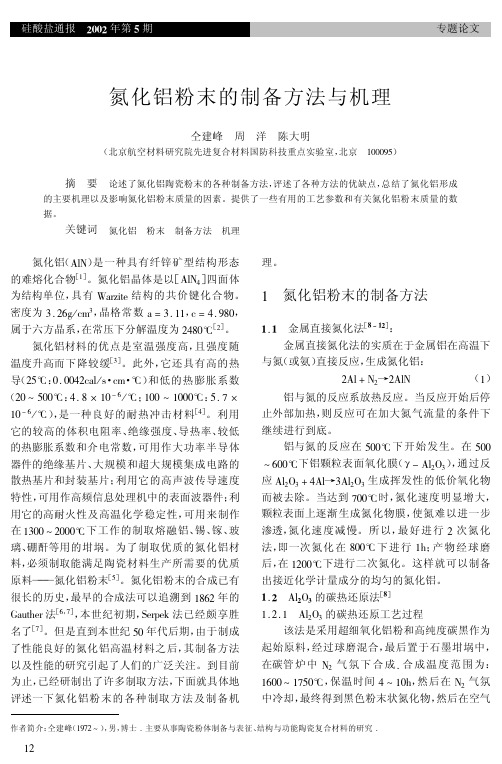
氮化铝粉末的制备方法与机理仝建峰周洋陈大明(北京航空材料研究院先进复合材料国防科技重点实验室,北京100095)摘要论述了氮化铝陶瓷粉末的各种制备方法,评述了各种方法的优缺点,总结了氮化铝形成的主要机理以及影响氮化铝粉末质量的因素。
提供了一些有用的工艺参数和有关氮化铝粉末质量的数据。
关键词氮化铝粉末制备方法机理作者简介:仝建峰(1972~),男,博士.主要从事陶瓷粉体制备与表征、结构与功能陶瓷复合材料的研究.氮化铝(AIN )是一种具有纤锌矿型结构形态的难熔化合物[1]。
氮化铝晶体是以[AIN 4]四面体为结构单位,具有Warzite 结构的共价键化合物。
密度为3.26g /cm 3,晶格常数a =3.11,c =4.980,属于六方晶系,在常压下分解温度为2480C [2]。
氮化铝材料的优点是室温强度高,且强度随温度升高而下降较缓[3]。
此外,它还具有高的热导(25C :0.0042caI /S ·cm ·C )和低的热膨胀系数(20~500C :4.8X 10-6/C ;100~1000C :5.7X10-6/C ),是一种良好的耐热冲击材料[4]。
利用它的较高的体积电阻率、绝缘强度、导热率、较低的热膨胀系数和介电常数,可用作大功率半导体器件的绝缘基片、大规模和超大规模集成电路的散热基片和封装基片;利用它的高声波传导速度特性,可用作高频信息处理机中的表面波器件;利用它的高耐火性及高温化学稳定性,可用来制作在1300~2000C 下工作的制取熔融铝、锡、镓、玻璃、硼酐等用的坩埚。
为了制取优质的氮化铝材料,必须制取能满足陶瓷材料生产所需要的优质原料———氮化铝粉末[5]。
氮化铝粉末的合成已有很长的历史,最早的合成法可以追溯到1862年的Gauther 法[6,7],本世纪初期,Serpek 法已经颇享胜名了[7]。
但是直到本世纪50年代后期,由于制成了性能良好的氮化铝高温材料之后,其制备方法以及性能的研究引起了人们的广泛关注。
氮化铝粉末生产工艺

氮化铝粉末生产工艺氮化铝是一种耐热、硬度和强度都很高的陶瓷材料,被广泛应用于电子、军工、航空航天等领域。
氮化铝粉末作为其原材料之一,在氮化铝制备过程中起着关键作用。
因此,研究氮化铝粉末生产工艺具有重要意义。
氮化铝粉末的制备方法有多种,其中常用的有溶胶凝胶法、氨解法、高能球磨法等。
以下是一种常用的氨解法制备氮化铝粉末的工艺流程:一、原料准备制备氮化铝粉末的主要原料是氨气(NH3)和氢气(H2),氮气(N2)作为惰性气体使用。
此外,还需要称量铝粉(Al)和碳粉(C)。
二、氨解反应氨解反应在封闭式反应器中进行,反应温度通常在800℃至1000℃之间。
反应过程中,铝一般处于液态,而碳粉则是在高温下热分解为碳(C)和二次燃料甲烷(CH4),并与铝发生反应生成氮化铝。
氢气是还原剂,避免了氮化物形成异质链接。
氮气在反应中起到稀释作用,维持反应气氛。
氨气是反应的主体,且参与反应生成氮气。
三、热处理经过氨解反应得到的产物需要进行热处理,将其放入高温炉中,在氢气氛中进行600℃~800℃高温热处理。
热处理过程中,产物会发生损失和烧结。
热处理时间和温度的选择对粉末的质量和性能影响较大。
四、制粒热处理后的产物需要破碎并且进行粗、细选,然后进行制粒,获得均匀的颗粒形态的粉末。
通常采用润湿法或柔性致密聚合法进行制粒。
五、筛分制粒后的氮化铝粉末需要进行筛分,以去除粗颗粒、杂质等。
粒径的选择应根据具体需要的应用条件而定。
通过不同的筛孔直径,可以得到不同粒径分布的氮化铝粉末。
六、包装筛分后的粉末放入铝箔袋或聚乙烯袋中,密封存储,以提高其稳定性和耐潮性。
综上所述,氨解法制备氮化铝粉末的过程包括原料准备、氨解反应、热处理、制粒、筛分和包装等环节。
该方法制备的氮化铝粉末具有粒径分布均匀、颗粒形态优良、生产效率高等优点,被广泛应用于氮化铝复合材料及高温结构材料等领域。
- 1、下载文档前请自行甄别文档内容的完整性,平台不提供额外的编辑、内容补充、找答案等附加服务。
- 2、"仅部分预览"的文档,不可在线预览部分如存在完整性等问题,可反馈申请退款(可完整预览的文档不适用该条件!)。
- 3、如文档侵犯您的权益,请联系客服反馈,我们会尽快为您处理(人工客服工作时间:9:00-18:30)。
氮化铝粉末的制备方法与机理仝建峰周洋陈大明(北京航空材料研究院先进复合材料国防科技重点实验室,北京100095)摘要论述了氮化铝陶瓷粉末的各种制备方法,评述了各种方法的优缺点,总结了氮化铝形成的主要机理以及影响氮化铝粉末质量的因素。
提供了一些有用的工艺参数和有关氮化铝粉末质量的数据。
关键词氮化铝粉末制备方法机理作者简介:仝建峰(1972~),男,博士.主要从事陶瓷粉体制备与表征、结构与功能陶瓷复合材料的研究.氮化铝(AIN )是一种具有纤锌矿型结构形态的难熔化合物[1]。
氮化铝晶体是以[AIN 4]四面体为结构单位,具有Warzite 结构的共价键化合物。
密度为3.26g /cm 3,晶格常数a =3.11,c =4.980,属于六方晶系,在常压下分解温度为2480C [2]。
氮化铝材料的优点是室温强度高,且强度随温度升高而下降较缓[3]。
此外,它还具有高的热导(25C :0.0042caI /S ·cm ·C )和低的热膨胀系数(20~500C :4.8X 10-6/C ;100~1000C :5.7X10-6/C ),是一种良好的耐热冲击材料[4]。
利用它的较高的体积电阻率、绝缘强度、导热率、较低的热膨胀系数和介电常数,可用作大功率半导体器件的绝缘基片、大规模和超大规模集成电路的散热基片和封装基片;利用它的高声波传导速度特性,可用作高频信息处理机中的表面波器件;利用它的高耐火性及高温化学稳定性,可用来制作在1300~2000C 下工作的制取熔融铝、锡、镓、玻璃、硼酐等用的坩埚。
为了制取优质的氮化铝材料,必须制取能满足陶瓷材料生产所需要的优质原料———氮化铝粉末[5]。
氮化铝粉末的合成已有很长的历史,最早的合成法可以追溯到1862年的Gauther 法[6,7],本世纪初期,Serpek 法已经颇享胜名了[7]。
但是直到本世纪50年代后期,由于制成了性能良好的氮化铝高温材料之后,其制备方法以及性能的研究引起了人们的广泛关注。
到目前为止,已经研制出了许多制取方法,下面就具体地评述一下氮化铝粉末的各种制取方法及制备机理。
1氮化铝粉末的制备方法1.1金属直接氮化法[8~12]:金属直接氮化法的实质在于金属铝在高温下与氮(或氨)直接反应,生成氮化铝:2AI +N 2!2AIN(1)铝与氮的反应系放热反应。
当反应开始后停止外部加热,则反应可在加大氮气流量的条件下继续进行到底。
铝与氮的反应在500C 下开始发生。
在500~600C 下铝颗粒表面氧化膜(!-AI 203),通过反应AI 203+4AI !3AI 203生成挥发性的低价氧化物而被去除。
当达到700C 时,氮化速度明显增大,颗粒表面上逐渐生成氮化物膜,使氮难以进一步渗透,氮化速度减慢。
所以,最好进行2次氮化法,即一次氮化在800C 下进行1h ;产物经球磨后,在1200C 下进行二次氮化。
这样就可以制备出接近化学计量成分的均匀的氮化铝。
1.2AI 203的碳热还原法[8]1.2.1AI 203的碳热还原工艺过程该法是采用超细氧化铝粉和高纯度碳黑作为起始原料,经过球磨混合,最后置于石墨坩埚中,在碳管炉中N 2气氛下合成.合成温度范围为:1600~1750C ,保温时间4~10h ,然后在N 2气氛中冷却,最终得到黑色粉末状氮化物,然后在空气中,600~700C下保温10~161,进行脱碳处理,即得到灰白色、流动性良好的AIN粉末。
碳热还原法制备AIN的反应式为:AI2O3+3C+N2!2AIN+3CO(2)这是一个总的反应式,可分为二步,一步是氧化铝的还原,另一步是氮化。
长期以来,碳热还原法制备AIN的反应机理已经提出了很多种,总的来讲,可分为气-固反应,固-固反应2大类。
气体还原固体氧化物的机理,现在普遍接受的观点是吸附-自动催化理论[10],这种理论认为,气体还原剂还原金属氧化物,分为以下几个步骤:第一步是气体还原剂,如CO被氧化物吸附;第二步是被吸附的还原剂分子与固体氧化物中的氧相互作用并产生新相;第三步是反应的气体产物从固体表面上解吸;在反应速度与时间的关系曲线上具有自动催化的特点,具体方程式如下:吸附:MeO(S)+X(g)!MeO·X(吸附)(3)反应:MeO·X(吸附)!Me·XO(吸附)(4)解吸:Me·XO(吸附)!Me+XO(!)(5)气体还原金属氧化物总起来有以下过程[13]:(1)气体还原剂分子由气流中心扩散到固体外表面按吸附机理发生化学还原反应;(2)气体通过金属扩散到氧化物-金属界面上发生还原反应;(3)氧化物的氧原子通过金属扩散到金属-气体界面上可能发生反应;(4)气体反应产物通过金属转移到金属外表面;(5)气体反应产物从金属外表面扩散到气流中心而出去。
这一反应机理已得到承认,能解释许多金属氧化物还原的实验事实。
碳热还原氮化法的主要工序如图1所示[14]。
图1AlN粉末制造工艺流程图1.2.2碳热还原氮化法制备AIN粉的机理研究关于AIN粉的碳热还原氮化法制造原理已有很多人作过研究,由于实验的条件和实验的重点不同,各人得出的结论也有很大的差异[15]。
在AI-O-N-C体系中,碳热还原氮化法的主要固相产物为氮化铝。
体系的相图如图2所示[16]。
图2C-Al-0-N体系相图体系中可能发生的反应有[17]:2AI2O3(S)+3C(S)+2N2(g)=4AIN(S)+3CO2(g)(6)AI2O3(S)+3C(S)+N2(g)=2AIN(S)+3CO(g)(7)2AI2O3(S)+9C(S)=2AI4C3(S)+6CO(g)(8)AI4C3(S)+2N2(g)=4AIN(S)+3C(S)(9)AI2O3(S)+12C(S)=2AIN(S)+AI4C3(S)+9CO(g)(10)应用公式:"G =#"G 生成物—#"G 反应物"G =-RTIDK可计算这些反应的标准自由能变化"G 及其平衡常数K和产物的平衡蒸气压。
计算结果表明在此体系中最易发生的反应是反应(7),反应(9)是自发进行的。
对反应(7)而言:"G="G +RTID(P CO3/P N2)="H -T"S +RTID(P CO3/P N2)(11)当反应处于封闭体系的平衡态时,"G=0,即"H -T"S =689940-353.09T eg=0(12)由此算得Teg=1852K,即在封闭体系中,反应(7)发生的温度必须是T>1852K。
进一步的研究表明[18],反应(7)分二步进行。
第一步是AI2O3的碳热还原固相反应,生成铝蒸气和铝的低价气体氧化物,其反应式为:AI2O3(S)+3C(S)=2AI(g)+3CO(g)(13)AI2O3(S)+2C(S)=AI2O(g)+2CO(g)(14)AI2O3(S)+C(S)=AI2O2(g)+CO(g)(15)在高温时,反应(14)占优势,为主要反应。
反应的第二步是铝蒸气和铝的低价氧化物的气相氮化:2al(g)+N2(g)=2alN(S)(16)al2O(g)+N2(g)+C(S)=2alN(S)+CO(g)(17)al2O(g)+N2(g)+CO(g)=2alN(S)+CO2(g)(18)CO2(g)+C(S)=2CO(g)(19)在碳热还原氮化过程中,当温度较高时反应中会生成中间相alON,随着反应温度的升高和反应时间的延长,alON逐渐向alN转化,当反应进行完全时,alON会完全消失,最终得到纯的alN 粉[19]。
由此可见,alN的生成过程主要由气相反应所控制[20,21],反应过程伴随的alN晶须生长现象[22]证明了这一点。
原料中应有足够的碳来生成CO(g),以促使al2O3(S)的蒸气化和alON(S)向alN(S)的转化[19]。
反应转化率可用下式进行计算[23]:alN(%)=R·C·2M alN·(M al2O3)-1·(1-F)-1(20)式中R—反应率(%),C—反应前al2O3的含量,M—各成分的分子量,F—反应的质量减少率。
表1列举了使用碳热还原法合成氮化铝粉末特性的典型的例子。
可以看出,合成工艺参数大致相同,起始原料al2O3/C的重量比的理论值为2.83,但是,实验表明:过量的碳能保证al2O3充分的还原,所以每个作者都选择了过量的碳。
表1碳热还原法合成AlN粉末特性[24~26]序号al/C(%)温度(C)时间(h)粒度(H m)主要元素(%)al N O C1216507 2.00~4.0065.5132.520.930.46 2216006 1.3164.8033.40 1.100.11 3 2.4155050.30~0.70--0.070.18在al2O3碳热还原法制备alN粉体的工艺中,常加入CaO,CaF2,Y2O3等作为催化剂,其中,CaF2可以更为有效地降低活化能,提高反应速率,有人使用了O,Y,T,G-al2O3及al(OH)3等不同的铝源,发现还有助于控制粉末团聚,获得理想的粒径分布,粉末里残余的碳也可以在空气中837K 左右烧除[27]。
碳热还原法合成的alN粉体纯度较高,成型和烧结性能都比较好,但合成温度较高,反应时间较长,粉末粒度较大。
1.3等离子化学合成alN粉末采用等离子化学合成法来制备alN粉末,能有效地缩短反应时间,合成超细的粉末产品。
从70年代后期,人们纷纷关心使用等离子化学合成法来合成alN粉末,而且在这方面做了大量的研究工作[28,29]。
在等离子体合成时,一般采用无电极的高频或超高频放电的等离子体发生器。
合成过程在含有氨的等离子体中加入铝粉的情况下进行。
等离子流径向温度梯度比较大,而且沿中心线的温度比较高,因此,铝粉颗粒的加热取决于颗粒流落入等离子流中心高温区的速度。
用各种规模的设备在高频放电低温等离子体合成的氮化铝粉的化学成分和比表面积见表2[5]。
表中alN-a 是用实验室设备制取的;alN-B是用半规模化设备制取的;alN-C是用大规模化设备生产的。
等离子化学合成的alN由于粒度细、比表面积大而具有很高的活性和良好的工艺性能。
这种粉末用烧结法制取制品时,烧结温度可降低300 C,并可制得几乎完全致密的氮化铝陶瓷。
表2等离子体合成的氮化铝粉的化学成分和比表面积粉末化学成分(%)al总N2al游离O2C总Fe Si比表面积(m2/g)alN-a63.4032.000.20 2.00未发现0.200.1026.20 alN-B64.0033.200.15 2.00未发现0.130.1037.00 alN-C64.1032.500.16 2.150.550.800.3046.001.4化学气相沉积法化学气相沉积法或热解法是基于铝的挥发性化合物与氨的化学反应从气相中沉积氮化铝的方法。