最新PCB各工序知识介绍
PCB部分工序详解及注意事项

PCB部分工序详解及注意事项PCB(Printed Circuit Board)即印刷电路板,是电子产品中常见的一个组件。
它起到电路连接、电源分配、信号传输等作用。
PCB的制作过程是一个较为复杂的流程,需注意一些关键环节以保证质量和性能。
下面将介绍PCB部分工序的详解及注意事项。
PCB的制作主要包括设计、打样、制版、清洗、印刷、成型、组装等多个工序。
首先是设计工序,设计工程师根据产品功能需求和电路图纸,使用电子设计自动化工具(EDA)进行电路布局设计,确定PCB的层数、外形尺寸、焊盘位置等。
在设计时,需要注意布局合理、信号良好、热量分布均匀等因素。
打样工序是制作试样以进行测试和验证的过程。
根据设计图纸,制作一到数个样板,打样时需注意避免过量的焊盘和不必要的线路,以减少制作成本。
制版工序是将设计图纸转化为制板所需的文件。
制版人员将设计文件导入到制版软件中,生成制板图形,然后通过暗室曝光、显影、腐蚀等步骤制作出铜箔层和钻孔层,并进行钻孔、外形切割等加工。
清洗工序是将制作好的PCB进行清洗以去除残留物和污染物。
清洗时需注意使用合适的溶剂和工艺,避免对PCB产生损伤。
印刷工序是将电路板上的组件和标记印刷上去。
通常使用丝网印刷或喷墨印刷技术进行印刷。
成型工序是将电路板进行成型以适应产品的外形尺寸和连接要求。
成型可以通过机械加工、模具压制等方式进行。
组装工序是将电路板上的元器件进行焊接和连接。
组装通常分为手工焊接和自动化焊接两种方式,需要注意焊接温度、时间和方法,避免焊接不良或损坏元器件。
在PCB制作过程中,还有一些常见的注意事项需要注意。
首先是对PCB生产环境的要求,应保持室温、湿度和尘埃等环境因素的控制。
其次是对于材料的选择,应选择适合的基板材料、铜箔厚度和绝缘层材料。
此外,焊接时需注意焊接温度、时间、焊盘布局等参数,以确保焊接质量。
还需对PCB进行严格的控制和测试,确保产品的性能和质量。
总之,PCB制作过程是一项复杂且关键的工序,需要细心和耐心地处理每个环节。
PCB外层后工序简介

即将已调稀的非水溶性绿油油墨,以水帘方 式连续流下,在水平输送前进的板面上均匀涂满 一层绿油,待其溶剂挥发半硬化之后,再翻转做 另一面涂布的施工方式。
喷涂印刷(Spray Coating) 利用压缩空气将调稀绿油以雾化粒子的方式
化学反应: Ni2+ +2H2PO2- +2H2O
Ni+2HPO32+4H++H2
副反应: 4H2PO2-
2HPO32-+2P+2H2O+H2
反应机理:
H2PO2- +H2O +H++2H
HPO32-
Ni2++2H Ni+2H+
H2PO2-+H OH-+P+H2O H2PO2- + H2O HPO32+H++H2
(1)板面前处理(Suface preparation) —— 去除板面氧化物及杂质,粗化铜面 以增强绿油的附着力。
(2) 绿油的印制(Screen print) —— 通过丝印方式按客户要求,绿油均 匀涂覆于板面。
(3)低温锔板(Predrying) ——将湿绿油内的溶剂蒸发掉,板面绿油 初步硬化准备曝光。
(6) 沉金
作用:是指在活性镍表面通过化学换 反应沉积薄金。
化学反应: 2Au++Ni
2Au+Ni2+
特性:
由于金和镍的标准电极电位相差较 大,所以在合适的溶液中会发生置换反 应。镍将金从溶液中置换出来,但随着 置换出的金层厚度的增加,镍被完全覆 盖后,浸金反应就终止了。一般浸金层 的厚度较薄,通常为0.1μm左右,这既可 达到降低成本的要求,也可提高后续钎 焊的合格率。
PCB制造各工艺流程详解

PCB制造各工艺流程详解1.电路设计电路设计是PCB制造的第一步,主要包括电路原理图设计和PCB版图设计。
初步确定电路的整体结构和连接方式,并将其转化为电路原理图。
然后,根据原理图设计PCB版图,确定各个元件的位置、布局、连接线路等。
2.元件采购与预处理在制造之前,需要采购元件并进行预处理。
元件的选择应根据电路设计的要求和元件的性能特点进行,可以通过下单、议价等方式采购。
预处理包括清洗、修整等,确保元件的质量和可用性。
3.PCB制版PCB制版是将PCB电路设计转化为实体的过程。
首先,将设计好的PCB版图按照比例放大到实际大小,并在光板上通过紫外线曝光将图形转移到光敏胶上。
然后,通过化学反应,将光敏胶上的图形转移到铜层上。
最后,通过蚀刻和清洗等步骤去除不需要的铜层,形成电路板的导电部分。
4.元件贴装元件贴装是将预处理过的元件按照设计好的位置进行安装的过程。
首先将PCB放置在贴装机上,然后自动或手动将元件精确定位到指定的位置。
贴装完成后,通过焊接技术将元件固定在PCB上。
5.焊接焊接是将元件与PCB电路板连接的过程,常用的焊接方法有插针焊接、表面焊接和波峰焊接等。
插针焊接是将元件引脚插入PCB的插孔中,并通过加热使焊点形成连接。
表面焊接是将元件的焊脚与PCB表面的焊盘直接连接,通过加热和焊料实现焊接。
波峰焊接是将PCB放置在流动的焊料波中,通过焊料的表面张力使焊点形成连接。
6.表面处理表面处理是对PCB表面进行处理,以增加PCB的耐腐蚀性和导电性。
常用的表面处理方法有镀金、镀锡和喷涂等。
镀金是在PCB表面覆盖一层金属,提高导电性。
镀锡是在PCB表面覆盖一层锡,增加耐腐蚀性。
喷涂是在PCB表面喷涂一层保护层,防止腐蚀和污染。
7.调试与测试8.包装与出货最后,将经过调试和测试的PCB进行包装和出货。
包装可根据客户要求进行,常用的包装方式有盒装、袋装和盘装等。
出货时要确保包装的完好性,以防止在运输过程中受到损坏。
PCB部分工序详解及注意事项
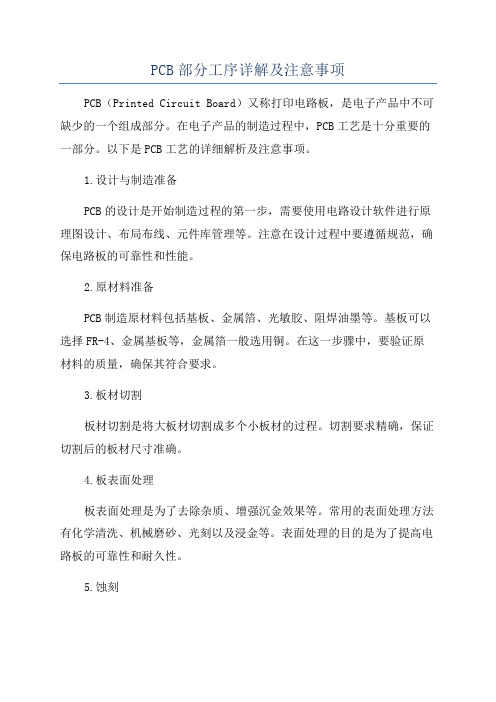
PCB部分工序详解及注意事项PCB(Printed Circuit Board)又称打印电路板,是电子产品中不可缺少的一个组成部分。
在电子产品的制造过程中,PCB工艺是十分重要的一部分。
以下是PCB工艺的详细解析及注意事项。
1.设计与制造准备PCB的设计是开始制造过程的第一步,需要使用电路设计软件进行原理图设计、布局布线、元件库管理等。
注意在设计过程中要遵循规范,确保电路板的可靠性和性能。
2.原材料准备PCB制造原材料包括基板、金属箔、光敏胶、阻焊油墨等。
基板可以选择FR-4、金属基板等,金属箔一般选用铜。
在这一步骤中,要验证原材料的质量,确保其符合要求。
3.板材切割板材切割是将大板材切割成多个小板材的过程。
切割要求精确,保证切割后的板材尺寸准确。
4.板表面处理板表面处理是为了去除杂质、增强沉金效果等。
常用的表面处理方法有化学清洗、机械磨砂、光刻以及浸金等。
表面处理的目的是为了提高电路板的可靠性和耐久性。
5.蚀刻蚀刻是将铜箔蚀刻成制定的线路形状的过程。
常用的蚀刻方法有湿法蚀刻和干法蚀刻。
在蚀刻过程中,要控制好蚀刻剂的浓度和时间,避免过蚀或欠蚀。
6.镀铜镀铜是为了增加线路的导电性能和保护线路不被氧化。
通过电化学方法,在铜箔表面镀一层铜。
在镀铜过程中需要控制好电流密度和镀铜时间,确保铜层的均匀性和厚度。
7.冲孔冲孔是为了在电路板上形成元件引脚的孔洞。
常用的冲孔方法有机械冲孔和激光冲孔。
在冲孔过程中要确保孔径准确,不得损坏板材。
8.焊接焊接是将元件连接到电路板上的过程。
焊接方法有手工焊接和机器焊接。
在焊接过程中,要控制好焊锡的温度和时间,避免焊接不良或短路等问题。
9.包覆胶包覆胶是为了保护电路板上的元件和线路,增强电路板的可靠性和稳定性。
常用的包覆胶有环氧树脂、硅胶等。
包覆胶需要控制好涂胶的厚度和均匀性。
10.后焊接处理后焊接处理包括焊盘复查、割锡、清洁、阻焊油墨涂覆等步骤。
焊盘复查是为了检查焊盘是否连接良好,割锡是为了去除多余的焊锡,清洁是为了去除焊接过程中产生的污垢,阻焊油墨涂覆是为了防止短路和氧化。
PCB各工序知识介绍

PCB各工序知识介绍PCB(Printed Circuit Board)是电子产品中不可或缺的一个组成部分,它承载着电子元器件,并提供了连接和支持这些元器件所需的电路。
在PCB制造的过程中,有多个关键的工序需要进行,以确保PCB的质量和可靠性。
接下来将详细介绍各个PCB工序的知识。
1.原材料准备:PCB的主要原材料是铜箔和基板。
铜箔作为PCB的导电层,负责连接电子元器件。
而基板则提供了支持和固定元器件的平台。
在原材料准备阶段,需要对铜箔进行切割和整平,以及对基板进行加工和预处理。
2.印制制作:在印制制作工序中,需要使用特殊的设备将电路图案打印到基板上。
这通常通过使用光刻技术和蚀刻技术来实现。
首先,将电路图案通过光阻材料覆盖在基板上,然后通过光刻曝光将电路图案暴露出来。
最后,使用蚀刻液将未覆盖的铜箔部分蚀刻掉,从而形成电路。
3.钻孔和插件:在钻孔和插件阶段,需要在PCB上钻孔来安装连接器和其他组件。
首先,根据设计要求在特定位置进行钻孔。
然后,使用钢钻头将孔径扩大,并进行外层导电层的拍孔。
最后,通过钻孔加工进行多孔插件,以容纳各种组件。
4.金属化和保护:金属化和保护工序是为了提高PCB的导电性能和保护电路。
首先,将电路表面进行金属化处理,通常是通过镀金或镀锡来实现。
这样可以增强电路的导电性能,并提供耐腐蚀的保护层。
然后,通过打印或喷涂方式施加保护层,如防焊膜、阻焊膜和丝印标识,以保护电路免受外界环境的侵害和损坏。
5.焊接和装配:在焊接和装配阶段,将电子元器件与PCB进行连接。
这个过程通常是通过使用焊锡来实现的。
首先,在PCB上涂上焊膏,并将元器件放置在正确的位置上。
然后,通过加热焊接区域,使焊膏熔化并形成连接。
最后,通过质量检测,确保焊接的质量和可靠性。
6.电测试和品质检验:在PCB制造的最后阶段,需要进行电测试和品质检验,以确保PCB的功能和质量。
电测试包括测试电路的连通性、导通和绝缘性能。
品质检验则包括外观检查、尺寸测量、绝缘电阻测试等。
PCB工艺介绍
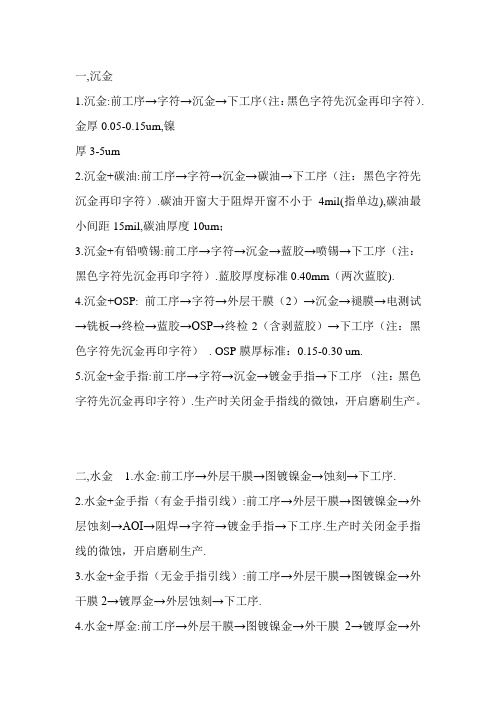
一,沉金1.沉金:前工序→字符→沉金→下工序(注:黑色字符先沉金再印字符).金厚0.05-0.15um,镍厚3-5um2.沉金+碳油:前工序→字符→沉金→碳油→下工序(注:黑色字符先沉金再印字符).碳油开窗大于阻焊开窗不小于4mil(指单边),碳油最小间距15mil,碳油厚度10um;3.沉金+有铅喷锡:前工序→字符→沉金→蓝胶→喷锡→下工序(注:黑色字符先沉金再印字符).蓝胶厚度标准0.40mm(两次蓝胶).4.沉金+OSP: 前工序→字符→外层干膜(2)→沉金→褪膜→电测试→铣板→终检→蓝胶→OSP→终检2(含剥蓝胶)→下工序(注:黑色字符先沉金再印字符). OSP膜厚标准:0.15-0.30 um.5.沉金+金手指:前工序→字符→沉金→镀金手指→下工序(注:黑色字符先沉金再印字符).生产时关闭金手指线的微蚀,开启磨刷生产。
二,水金 1.水金:前工序→外层干膜→图镀镍金→蚀刻→下工序.2.水金+金手指(有金手指引线):前工序→外层干膜→图镀镍金→外层蚀刻→AOI→阻焊→字符→镀金手指→下工序.生产时关闭金手指线的微蚀,开启磨刷生产.3.水金+金手指(无金手指引线):前工序→外层干膜→图镀镍金→外干膜2→镀厚金→外层蚀刻→下工序.4.水金+厚金:前工序→外层干膜→图镀镍金→外干膜2→镀厚金→外层蚀刻→下工序.水金标准:金厚0.25-0.75um,镍厚3-5um .增加干膜2厚金菲林.5.水金+有铅喷锡:前工序→图镀镍金→外层蚀刻→外层AOI→阻焊→字符→印兰胶→喷锡→下工序.增加印蓝胶的菲林,蓝胶制作相邻位置连片制作,以便于后续剥蓝胶.蓝胶厚度标准0.40mm(两次蓝胶).三,沉锡. 1.沉锡:锡厚度标准:0.8-1.2um.1)成品尺寸≥50X100mm (长边必须≥100mm,短边必须≥50mm): 前工序→字符→外形→电测→ 沉锡→电测试2→终检(2)成品尺寸<50X100mm(长边<100mm 或短边<50mm):前工序→字符→电测→ 沉锡→外形→电测试2→终检.2.沉锡+碳油:碳油厚度10um.前工序→字符→碳油→电测→印兰胶→沉锡→电测试(2)→终检.增加印碳油的菲林;印炭油前需在火山灰磨板线清洗板面,关闭磨刷.四,沉银. 1.沉银:银厚度标准:0.10-0.30um;前工序→字符→外形→电测→半检→ 沉银→半检→电测试2→终检.2.沉银+碳油:碳油厚度10um.前工序→字符→碳油→电测→印兰胶→半检→沉银→半检→电测试2→终检.增加印碳油的菲林.印炭油前需在火山灰磨板线清洗板面,关闭磨刷.3.沉银+金手指:金手指标准:镍厚:3-5um;常规金厚0.25-0.75um;厚金0.8~1.5um .前工序→字符→镀金手指→外形→电测→(贴红胶带)→半检→ 沉银→半检→电测试(2)→终检.(所有沉银板必须先字符再沉银.)五.OSP 1.OSP:OSP膜厚标准:0.15-0.30um.前工序→铣板→终检→OSP→终检2→后工序.2.OSP+碳油:碳油厚度10um.前工序→字符→ 碳油→电测试→铣板→终检→OSP →终检2→ 后工序.增加印碳油的菲林.印炭油前需在火山灰磨板线清洗板面,关闭磨刷.3.OSP+镀金手指:金手指标准:镍厚:3-5um,常规金厚0.25-0.75um;厚金0.8~1.5um .前工序→字符→镀金手指→铣板→电测试→终检→OSP→终检2→后工序.生产时关闭金手指线的微蚀,开启磨刷生产.六,喷锡 1.喷锡(有铅):锡厚标准:2-40um.前工序→字符→喷锡→下工序.2.喷锡(无铅):前工序→字符→喷锡→下工序.3.喷锡(有铅)+金手指:金手指标准:镍厚:3-5um,金厚0.25-0.75um前工序→字符→镀金手指→喷锡→下工序.4.喷锡(无铅)+金手指:前工序→字符→镀金手指→喷锡→下工序.5.碳油+喷锡(有铅):碳油厚度10um.阻焊→字符→碳油→喷锡→下工序.增加印碳油的菲林.印炭油前需在火山灰磨板线清洗板面,关闭磨刷;6.碳油+喷锡(无铅):(同上).七,全板镀厚金:硬金厚度标准:镍厚控制3-5um;常规厚金0.25-0.75um;超厚金0.8~2.0um.钻孔→沉铜→板镀→外光成像→图镀镍金(Cu/Ni/Au)→镀厚金→外层蚀刻→下工序.优缺点:.沉金:A.沉积层平整,有较强的硬度,表层不易擦花.2.有很好的导电性和多次焊接性能3.储存期长(1年以上).1.生产成本高;2.流程控制比较困难;3.有潜在的黑垫缺陷;4.修理及返工困难;B.沉银:1.沉积层平整;2.有很好的导电性和焊接性;3.流程控制简单;4.返工和修理简单;1.储存期短(6~12个月);2.不能多次焊接;3.银面易变黄;4.对储存环境和运输要求很高;C.OSP:1.生产成本低;2.流程控制简单;3.返工简单;1.储存期短;2.不能多次焊接;膜太薄,耐热冲击能力差.D.喷锡:1.生产成本低;2.有很好的导电性和焊接性;3.可多次焊接;4.储存期长(1年以上)1.喷锡表面平整性差;2.细间距加工困难;3.高温处理板易变形;4.含铅,严重污染环境;E.沉锡:1.流程控制简单;2.沉积层平整;3.有很好的导电性及焊接性;4.可多次焊接;5.储存期为一年;1.易擦花;2.有潜在的锡须生产的可能;。
PCB排板工序基本知识培训
PCB排板工序基本知识培训一、排板的定义在压板之前,将铜箔(Copper foil)、半固化片(Prepreg)和经过氧化的芯板,按照MI 设计的层次进行组合。
二、排板的流程三、序号 注 意 事 项3 设备维护保养时,应先确认电源开关、空气开关是否关闭,才能进行保养工作4 输送机运转中,请勿靠近或触摸运转部分,以免发生危险5 输送设备运转当中,如遇故障,应立即切断电源通知维修部维修 6员工必须按照公司相关规定佩戴相应防护用具四、设备最大尺寸最小尺寸最大板厚最小板厚 自动排板线逢开/2007.1120”X24“18"X20"-0.05mm设备名称制造商设备型号设备设计能力安装年月五、物料名称英文名化学分子式包装形式性质保存期限备注RCC RCC /纸箱/<5℃,5个月P片Prepreg /纸箱/(20±1℃,55±5%)3个月49.5"宽幅铜箔copper foil /纸箱/(20±1℃,55±5%)22"/26"宽幅岗位名称生产设备参数制板层压厚度控制范围panels/book检查方式管理方法板厚≤0.8mm 11~120.8mm <板厚≤1.0mm 9~101.0mm <板厚≤1.2mm 7~81.2mm <板厚≤1.8mm 5~61.8mm <板厚4~5排板目视、设备自动计数排板岗位生产及品质检查记录层数排板机注:洁净房环境控制——温度:20℃±1℃;湿度:55%±5%。
七、保养八、过程产品品质控制8.1过程产品品质控制项目8.2.1所有接触板面、PP和RCC等材料的员工必须戴手套。
8.2.2操作员工双手拿P片,防止折伤。
8.2.3取core时,需要双手拿板,防止擦伤棕化膜。
8.2.4推车时,要求平稳,禁止突然快速启动或者停止,防止板移动而擦伤棕化膜。
8.2.5在牛皮纸上放置1张2oz的铜箔,防止牛皮纸纤维掉落在钢板或板面上形成板凹。
PCB生产工艺流程
PCB生产工艺流程PCB(Printed Circuit Board),即印刷电路板,是一种用于连接和支持电子元件的电路板。
在电子制造业中,PCB生产工艺流程是非常重要的,决定了PCB的质量和可靠性。
下面将详细介绍PCB生产工艺流程。
1.原材料准备:2.毛胚制备:毛胚制备是PCB生产的核心步骤,包括蚀刻、覆铜、打孔等工艺。
(1)蚀刻:将覆铜层保护膜部分剥离,然后将空白部分蚀刻掉,形成电路板的形状和线路。
(2)覆铜:将覆铜液均匀涂布在基板表面,使得基板表面形成一层铜箔,用于导电。
(3)打孔:根据设计要求,在基板上打孔,以便进行电子元件的连接。
3.图案制作:图案制作是指将电路设计图案转移到PCB板上,包括图案制作光阻、曝光、显影等步骤。
(1)图案制作光阻:将光敏涂料(光阻剂)涂覆在PCB板上,然后通过加热或暴露于紫外线下,使涂层固化。
(2)曝光:将电路设计图案通过连续曝光到光阻层上,形成与电路板设计图案相同的光刻图案。
(3)显影:用显影剂去除未固化的光刻图案。
4.蚀刻:蚀刻是将未被光刻图案遮蔽的铜箔部分蚀刻掉,形成电路板的导线和连接孔。
5.镀金:镀金是为了提高PCB板的导电性和耐腐蚀性,使得PCB板更加稳定和可靠。
常用的镀金方法有化学镀金、电镀镀金和电镀锡等。
6.排钻:排钻是用机器将电路板上的孔进行排列和钻孔,以便电子元件的安装和焊接。
7.焊盘沉镀:焊盘沉镀是为了提高焊接连接性能,保证电子元件的焊接质量。
通常采用热浸镀锡或喷锡等方法。
8.控制板外层:将两块PCB板层叠在一起,通过压力和温度将其压合在一起。
9.修边:通过机器将PCB板修边成所需的形状和尺寸。
10.印刷标识:11.成品检验:对PCB板进行检验,包括外观检查、尺寸检查、电气性能测试等。
12.包装和出货:将通过检验的PCB板进行包装,并按照要求进行分拣和出货。
以上是PCB生产工艺的主要流程,每个步骤都需要严格控制和操作,以保证PCB板的质量和可靠性。
PCB部分工序详解及注意事项
PCB部分工序详解及注意事项PCB(Printed Circuit Board,印刷电路板)是现代电子产品中不可或缺的一部分,它被广泛应用于电子设备、通信设备、计算机硬件等领域。
PCB的工序主要包括设计、制作、组装等,下面将详细介绍PCB的部分工序及注意事项。
一、PCB设计PCB设计是将电路原理图转化为具体的PCB板的布局和线路连接,设计出符合产品要求的PCB板。
在PCB设计中,需要注意以下几点:1.电路布局:合理的电路布局可以减少线路互相干扰的可能性。
尽量使各功能模块分布均匀,避免高频信号线和低频信号线相互交叉;2.确定适当的板材:根据产品的特性和要求选择合适的板材。
常见的板材有FR-4、FR-2、金属基板等;3.阻抗控制:对于高速信号传输线路,需要控制阻抗,以确保信号传输的质量;4.保证良好的散热性能:尤其对于功耗较大的电路板,需要进行散热设计,避免严重温度升高导致电路故障。
二、PCB制作PCB制作是将设计好的电路板进行实际制作的过程,主要包括以下工序:1.印制底图印制底图是将PCB设计图纸按照比例放大后在铜板上印制出来,通常使用光感材料进行印制,然后通过化学腐蚀去除不需要的铜涂层,形成待焊盘和导线线路。
2.电路制作电路制作是在印制底图的基础上,将元器件焊接到PCB板上,并连接各个元件之间的线路。
主要包括以下几个工序:a.黏贴:将电路板上的元器件和焊盘上的焊膏进行粘贴。
b.焊接:通过加热将焊膏熔化,并将焊盘和元器件焊接在一起。
c.点胶:对于需要固定元件的地方,如BGA封装,需要进行点胶固定。
d.贴片:将小型元器件使用贴片机粘贴到焊盘上。
e.焊接检测:焊接完毕后,需要进行焊点质量的检测,保证焊点质量。
三、PCB组装PCB组装是将制作好的PCB板安装到电子产品中的过程,主要包括以下几个工序:1.技术文件准备:准备PCB设计文件、元器件清单以及制程与质量控制文件等。
2.物料采购:根据元器件清单进行物料的采购,保证元器件的质量和数量的准确性。
PCB生产流程介绍
PCB生产流程介绍PCB是印刷电路板的英文缩写,是一种用于电子元器件安装和电路连接的基板。
PCB的生产流程主要包括设计、制版、印刷、贴装和测试等几个阶段。
1.设计阶段:PCB的设计是整个生产流程的第一步。
设计师根据电路原理图和布局要求,在计算机辅助设计软件中完成电路板的布局和布线。
2.制版阶段:制版是将电路板的布局图转换为实际可用的制作光刻版。
这个阶段的主要工作是使用光刻设备将电路板的图案印制在覆铜板上,并用化学物质将不需要的铜材料蚀刻掉。
3.印刷阶段:在印刷阶段,印刷电路板上的图案将通过将特殊的导电油墨印刷到覆铜板上来形成印刷电路。
这个阶段的主要工作是使用印刷设备将导电油墨印刷到覆铜板上,并通过热风或紫外线照射使导电油墨固化。
4.贴装阶段:在贴装阶段,通过自动贴装机将电子元器件粘贴到已制成的印刷电路板上。
贴装的元器件包括芯片、电阻、电容等。
在贴装之前,需要进一步检查印刷电路板是否有缺陷,例如短路、断路等。
5.焊接阶段:在焊接阶段,通过波峰焊接机将贴装完成的电子元器件与印刷电路板焊接在一起。
焊接的方法通常有浸锡法和无铅焊接法两种。
焊接完成后,需要进行视觉检测和电气性能测试,以确保焊接的质量和可靠性。
6.测试阶段:在测试阶段,对已制成的印刷电路板进行电气性能测试,以确保其功能正常。
测试方法包括功能测试、电气测试和可靠性测试等。
7.包装阶段:以上是PCB的主要生产流程介绍。
每个阶段都需要严格的操作和控制,以确保PCB的质量和性能。
同时,随着科技的进步,PCB的生产流程也在不断发展和改进,以满足日益复杂的电子产品需求。
- 1、下载文档前请自行甄别文档内容的完整性,平台不提供额外的编辑、内容补充、找答案等附加服务。
- 2、"仅部分预览"的文档,不可在线预览部分如存在完整性等问题,可反馈申请退款(可完整预览的文档不适用该条件!)。
- 3、如文档侵犯您的权益,请联系客服反馈,我们会尽快为您处理(人工客服工作时间:9:00-18:30)。
干膜的性质
Dry Film 干菲林
曝光后干膜的分子结构为立体网状结构,不溶于1% Na2CO3溶液。
Dry Film 干菲林
显影的原理
感光膜中未曝光部分的活性基团与稀碱 溶液反应生成可溶性物质而溶解下来, 从而把未曝光的部分溶解下来,而曝光 部分的干膜不被溶解。
未曝光的感光膜 已曝光的感光膜
可溶解 不可溶解
Pre-preg
Layer 1 Layer 2
Press Process
Copper Foil
Laminate
Layer 3 Layer 4
Take 4 layer for Example
Press Process
上热压模板
牛皮纸缓冲层
上定位模板
叠层 定位销钉
下定位模板
下热压模板
PIN LAM 多层板压合的全过程包括预压、全压和保压冷却三个阶段
今日之print-etch(photoimage transfer) 的技术,就是沿袭其发明而来的。
PCB 制作方法
制造方法介绍
A、减除法 通过选择性地去除无用导电箔而形成导电图形的工艺。 其流程见图1.9
PCB 制作方法
B、半加成法和全加成法的定义 ▪ 半加成法
在未覆铜箔基材或薄箔基材上,用化学沉积金属,结 合电镀或蚀刻,或者三者并用形成导电图形的一种加
成法工艺。
▪ 全加成法
相对半加成法而言,完全采用化学沉积在绝缘基板上
形成导电图形的工艺。
PCB 制作方法
加成法,
又可分半加成与全加成法,见下图。
半加成
PCB 制作方法
Inner Board
Cutting 内层开料
内层制作
Inner Dry Film 内层干菲林
Inner Etching
(DES) 内层蚀刻
(2)
内层洗板 Clean
去毛边 debur
焗板 Bake Boards
内层制作
原始大料寸:41“×49”、43“×49”、40”×48”等
内层开料
▪
16.33“ 10.25 “
41“
49“
1张大料
12块板料
内层开料
去毛边
去除切料后留下的毛屑及锋利的铜边,从而减 少后工序板与板相撞擦花铜面的机率,板厚大于 0.4mm的板可在专用的磨边机上自动磨边
Prepreg
Chemical Clean 化学清洗
内层
Resists Lamination 辘干膜
Exposure 曝光
DES 显影/蚀板
Black Oxide 黑氧化
Oxide Replacement
棕化
AOI 自动光学检测
Laying- Up 排板
PE Punching 啤孔
Pressing 压板
Middle Inspection 中检
Solder Mask 湿绿油
Component
Mark 白字
外层制作(续)
Hot Air
Levelling 喷锡
Profiling 外形加工
FQC 最后品质控制
FA 最后稽查
Packing 包装
内内层层开开料料
内层切料
⑴
Inner Board
Cutting
PCB的发展史
1903年Mr. Albert Hanson首创利用“线 路”(Circuit)观念应 用于电话交换机系统。
它是用金属箔予以切割 成线路导体,将之粘着 于石蜡纸上,上面同样 贴上一层石蜡纸,成了 现今PCB的机构雏型。 见右图。
PCB的发展史 PCB的发展史 1936年,Dr Paul Eisner真正发明了PCB的 制作技术,也发表多项专利。
AOI 自动光学检测
Black Oxide
(Oxide Replacement) 黑氧化(棕化)
Laying- up/
Pressing 排板/压板
Drilling 钻孔
外层制作
PTH/Panel Plating
沉铜/板电
Dry Film 干菲林
Pattern Plating
/Etching 图电/蚀刻
和抗蚀剂中粘结剂的作用完成贴膜。
辘干膜三要素:压力、温度、传送速度。
干膜
聚酯薄膜
聚乙烯保护膜 干膜
内层
干膜曝光原理 在紫外光照射下,光引发剂吸收了光能 分解成游离基,游离基再引发光聚合单 体进行聚合交联反应,反应后形成不溶 于稀碱溶液的立体型大分子结构。
干膜的性质
Dry Film 干菲林
曝光前干膜的分子结构为链状结构,可溶于1%的Na2CO3 溶液。
Drilling –钻孔
啤圆角:除去生产板上四角上的尖角,以免擦花、插穿菲林及伤人。 磨板边:除去生产板周围的纤维丝,防止擦花。 打字唛:在生产板边线用字模啤出生产型号(距板边4-5mm)。 钉板: 将生产板与底板用管位钉固定在一起,以避免钻孔时板间滑
PCB各工序知识介绍
PCB 扮演的角色
PCB的功能 提供完成第一层级构装的组件与其它必须的电子 电路零件接合的基地,以组成一个具特定功能的 模块或成品。
PCB的角色 在整个电子产品中,扮演了整合连结总其成所有 功能的角色。
因此当电子产品功能故障时,最先被质疑往往就 是PCB。
PCB 扮演的角色 电子构装层级区分示意。
内层
化学清洗
用碱溶液去除铜表面的油污、指印及其它有机 污物。然后用酸性溶液去除氧化层和原铜基材 上为防止铜被氧化的保护涂层,最后再进行微 蚀处理以得到与干膜具有优良粘附性能的充分 粗化的表面。
优点:除去的铜箔较少(1~1.5um),基材本身 不受机械应力的影响,较适宜薄板。
内层
辘干膜(贴膜)
先从干膜上剥下聚乙烯保护膜,然后在加热加压的条 件下将干膜抗蚀剂粘贴在覆铜箔板上。干膜中的抗蚀 剂层受热后变软,流动性增加,借助于热压辊的压力
内层开料
洗板
去除切料和去毛刺时产生的板屑和PP粉, 可减少或避免PP粉在烤板后固化于铜面上的 机率
内层开料
焗板 去除板内的水份,降低板的内应力
内层
Copper Foil
铜箔类型:1/4OZ;1/3OZ;1/2OZ;1OZ;2OZ;3OZ P片类型:106、2116、1080、7628、2113等
Dry Film 干菲林
停放15分钟
辘干膜
曝光
停放15分钟
显影
正片菲林
负片菲林
Press Process
定位系统 ▪ PIN LAM 有销钉定位
▪ MASS LAM 无销钉定位 1. X射线打靶定位法 2. 熔合定位法
Press Process
黑化/棕化原理
对铜表面进行化学氧化或黑化,使其表 面生成一层氧化物(黑色的氧化铜或棕 色的氧化亚铜或两者的混合物),以进一 步增加表面积,提高粘结力。