生产线平衡性教育
生产线平衡案例分析培训

生产线平衡案例分析培训引言在现代制造业中,生产线平衡是一个至关重要的概念。
通过合理的生产线平衡,可以提高生产效率、降低成本、优化资源利用等。
本文将通过分析一个生产线平衡案例,介绍生产线平衡的原理和方法,并探讨如何进行生产线平衡培训。
案例分析假设一个玩具生产厂家拥有一个生产线,负责生产玩具汽车。
该生产线由多个工作站组成,每个工作站负责一道具体的工序。
现有数据如下:•工作站1:个体组装,每小时可完成200辆玩具汽车的组装。
•工作站2:上色,每小时可完成150辆玩具汽车的上色。
•工作站3:质检,每小时可完成180辆玩具汽车的质检。
根据以上数据,可以计算出每个工作站的产能利用率,如下:•工作站1:200/200 = 100%•工作站2:150/200 = 75%•工作站3:180/200 = 90%从上述数据可以看出,工作站2的产能利用率较低,成为生产线上的瓶颈工序。
如果不及时解决这个问题,将会影响整个生产线的效率和产能。
生产线平衡原理和方法生产线平衡是指合理地安排生产线上各个工作站的工作量,使得各个工作站之间的产能相对平衡,解决瓶颈问题,提高生产效率。
生产线平衡的原理和方法主要包括以下几个方面:1. 识别瓶颈工序首先,需要通过数据分析或实地观察,明确生产线上的瓶颈工序。
瓶颈工序指的是生产能力较低,成为整个生产线效率的制约因素的工序。
在上述案例中,工作站2就是瓶颈工序。
2. 改善瓶颈工序针对瓶颈工序,可以考虑以下几种改善方法:•提高工作站的产能:通过增加设备数量、改进工艺或技术等方式,提高工作站的生产能力。
•减少工作站的工作量:通过优化生产流程,简化工序或调整工作站之间的任务划分,减少瓶颈工序的工作量。
在上述案例中,可以考虑增加上色工作站的设备数量或改善工艺,以提高生产效率。
3. 平衡工作站的工作量在解决瓶颈工序的同时,还需要平衡其他工作站的工作量,使得各个工作站的产能相对平衡。
平衡工作站工作量的方法包括:•调整任务划分:根据不同工作站的产能和工作特点,合理划分任务,避免工作站之间的工作量差距过大。
生产线平衡培训

生产线平衡培训一、概述生产线平衡是一种重要的生产管理技术,通过对生产线的布局、工序时间、人员安排等进行优化,实现生产效率的最大化。
生产线平衡培训旨在帮助员工理解生产线平衡的重要性,掌握相关的方法和技巧,从而提高生产线的运作效率和质量。
二、培训内容1.生产线平衡的基本概念–生产线平衡的定义–生产线平衡与生产效率的关系2.生产线平衡的重要性–生产线平衡对企业的意义–生产线平衡对产品质量的影响3.生产线平衡的方法与工具–时间研究方法–工序分析技术–平衡分析工具的使用4.生产线平衡实践案例分析–成功案例分享–失败案例反思三、培训目的生产线平衡培训的目的在于帮助员工全面了解生产线平衡的概念和实践,掌握相关的技术和方法,提高生产线运作的效率和质量,确保企业能够在激烈的市场竞争中保持竞争力。
四、培训收益1.提高生产线运作效率2.提升产品质量3.减少生产成本4.提升员工技能和意识五、培训流程1.培训前的准备–制定培训计划–确定培训内容和形式2.培训内容介绍–生产线平衡的相关理论知识–生产线平衡的方法与工具介绍3.培训案例分析–基于真实案例的分析讨论4.结业考核–考核员工对于生产线平衡知识的掌握程度六、总结生产线平衡培训是企业提高生产效率、产品质量、降低成本的重要途径之一。
只有通过持续的培训和实践,企业才能在市场竞争中立于不败之地。
希望通过本次培训,员工能够深入理解生产线平衡的重要性,掌握相关技术和方法,为企业的发展贡献力量。
以上是关于生产线平衡培训的文档,希望对您有所帮助。
生产线平衡培训课程
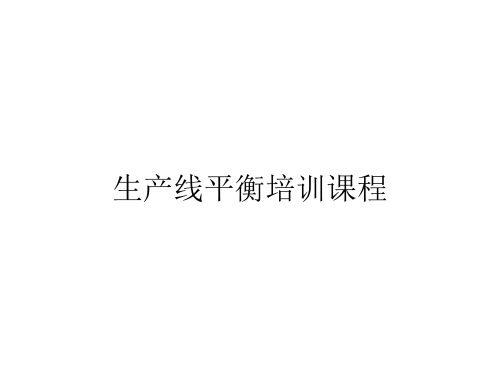
本文档后面有精心整理的常用PPT编辑图标,以提高工作效率
内容安排
一.线平衡定义 二.生产线平衡分析方法 三.B值、F值的定义与计算 四.线平衡案例分析
一. 线平衡定义
一. 线平衡定义
1. 什么是生产线平衡
– 生长线平衡是指构成生产线各道工序所需的时 间处于平衡状态,作业人员的作业时间尽可能
2. 改善前分析
四. 线平衡经典案例分享
3. 改善前后对比
四. 线平衡经典案例分享
3. 改善前后对比
四. 线平衡经典案例分享
3. 改善前后对比
全员参与的思想准备
• 给予和获取信息 • 接受非寻常的工作方法和解决方案 • 对目前的方法提升疑问 • 不允许找借口 • 马上纠正错误 • 问五个为什么,发掘出问题的真正原因 • 每个人意见都是有价值的 • 不追求无完美,一个60%的解决方案,比一
四. 线平衡经典案例分享
1. 案例说明:电子电装7人柔性线,改善前各 工位的工作时间如下所示:
四. 线平衡经典案例分享
2. 改善前分析
–生产线各工位分析如下:
改善前生产线平衡率=(18+16+24+37+45+16)/(37*7)*100%=60.2%
–改善前生产线各工位平衡图
四. 线平衡经典案例分享
个几乎无法实现的100%完美的解决方案好
后面附件PPT常用图标,方便大家提高工作效率
生活
图标元素
生活
图标元素
医疗
图标元素
二. 生产线平衡分析方法
– 例3:减少人手(2)
• 降低线体速度,减少生产产量
二. 生产线平衡分析方法
• 4种增Байду номын сангаас的工作
生产线平衡的培训资料
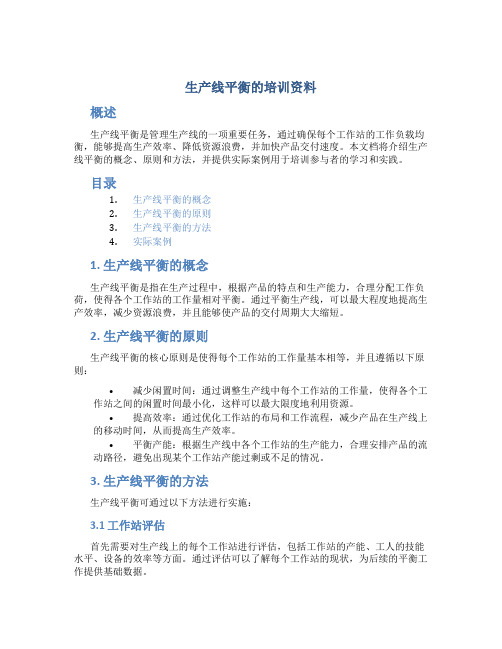
生产线平衡的培训资料概述生产线平衡是管理生产线的一项重要任务,通过确保每个工作站的工作负载均衡,能够提高生产效率、降低资源浪费,并加快产品交付速度。
本文档将介绍生产线平衡的概念、原则和方法,并提供实际案例用于培训参与者的学习和实践。
目录1.生产线平衡的概念2.生产线平衡的原则3.生产线平衡的方法4.实际案例1. 生产线平衡的概念生产线平衡是指在生产过程中,根据产品的特点和生产能力,合理分配工作负荷,使得各个工作站的工作量相对平衡。
通过平衡生产线,可以最大程度地提高生产效率,减少资源浪费,并且能够使产品的交付周期大大缩短。
2. 生产线平衡的原则生产线平衡的核心原则是使得每个工作站的工作量基本相等,并且遵循以下原则:•减少闲置时间:通过调整生产线中每个工作站的工作量,使得各个工作站之间的闲置时间最小化,这样可以最大限度地利用资源。
•提高效率:通过优化工作站的布局和工作流程,减少产品在生产线上的移动时间,从而提高生产效率。
•平衡产能:根据生产线中各个工作站的生产能力,合理安排产品的流动路径,避免出现某个工作站产能过剩或不足的情况。
3. 生产线平衡的方法生产线平衡可通过以下方法进行实施:3.1 工作站评估首先需要对生产线上的每个工作站进行评估,包括工作站的产能、工人的技能水平、设备的效率等方面。
通过评估可以了解每个工作站的现状,为后续的平衡工作提供基础数据。
3.2 平衡产能根据生产线上各个工作站的产能评估结果,进行产能平衡的规划。
可以通过调整工作站的工作时间、工人的数量或者生产设备的配置来实现产能的平衡。
3.3 优化工作流程通过分析工作站之间的依赖关系和产品流动路径,优化工作流程,减少产品在生产线上的移动时间。
可以通过重新布局工作站的位置、调整物料供应的方式等方法来优化工作流程。
3.4 周期时间分析对生产线上的每个工作站进行周期时间分析,找出生产线上的瓶颈点,并通过调整工作负载,降低瓶颈点的负荷,达到平衡生产线的目的。
生产线平衡的培训资料

生产线平衡的培训资料1. 概述本培训资料介绍了生产线平衡的基本概念、原则和方法,旨在帮助生产线工作人员提高生产效率和产能利用率。
通过培训,学员将了解到如何平衡生产线的各个工作站,以实现生产流程的优化和最大化生产效益。
2.生产线平衡的概念生产线平衡是指在生产过程中,合理安排每个工作站的工作内容和工作节奏,以达到最佳的生产效率和产能利用率。
生产线平衡的目标是使每个工作站的工作量相等,从而避免工作站之间的瓶颈和浪费。
2.1 为什么需要生产线平衡生产线平衡可以有效提高生产效率和产能利用率,减少资源浪费和生产成本。
通过平衡生产线,可以避免工作站之间的不匹配和拥堵,从而提高生产效率和产品质量。
2.2 生产线平衡的好处•提高生产效率和产能利用率•减少资源浪费和生产成本•改善工作站间的协调和合作•提高产品质量和降低次品率3. 生产线平衡的原则生产线平衡的实现需要遵循一定的原则,以确保生产线的工作流畅和高效。
3.1 流程和工作内容分析在进行生产线平衡之前,首先需要对生产流程和工作内容进行分析。
通过仔细分析每个工作站的工作内容和工作流程,可以找到工作站之间的依赖关系和瓶颈点,为后续的平衡工作提供依据。
3.2 任务分配和工作量平衡根据流程和工作内容的分析结果,合理分配任务和平衡工作量是实现生产线平衡的重要步骤。
通过根据工作站的工作内容和节奏,合理分配任务和平衡工作量,可以避免工作站之间的工作不匹配和拥堵。
3.3 周期性评估和调整生产线平衡需要周期性的评估和调整,以适应市场需求和生产环境的变化。
随着市场需求的变化,生产线平衡也需要相应的调整和优化,以确保生产线的高效运行。
4. 生产线平衡的方法生产线平衡的方法有很多,不同的方法适用于不同的生产线和生产环境。
以下介绍几种常用的生产线平衡方法。
4.1 工作站平衡工作站平衡是指根据生产线的工作内容和工作节奏,合理安排工作站的位置和工作内容,以达到最佳的工作效率和产能利用率。
4.2 任务分配平衡任务分配平衡是指根据生产线的任务需求和工作量预估,合理分配任务和平衡工作量,以确保工作站之间的工作量相等。
生产线平衡分析课程
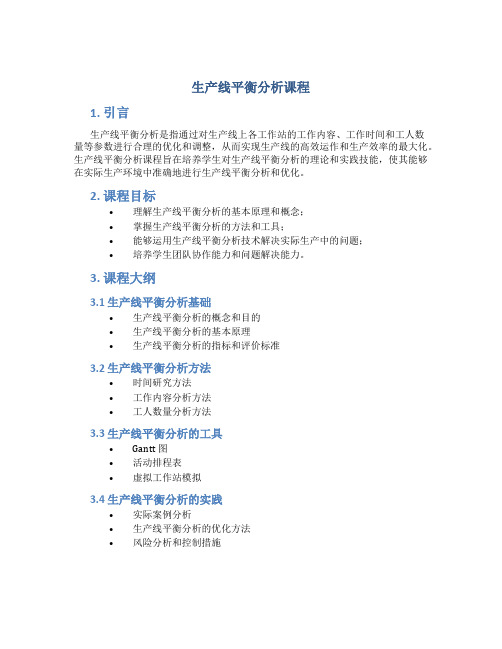
生产线平衡分析课程1. 引言生产线平衡分析是指通过对生产线上各工作站的工作内容、工作时间和工人数量等参数进行合理的优化和调整,从而实现生产线的高效运作和生产效率的最大化。
生产线平衡分析课程旨在培养学生对生产线平衡分析的理论和实践技能,使其能够在实际生产环境中准确地进行生产线平衡分析和优化。
2. 课程目标•理解生产线平衡分析的基本原理和概念;•掌握生产线平衡分析的方法和工具;•能够运用生产线平衡分析技术解决实际生产中的问题;•培养学生团队协作能力和问题解决能力。
3. 课程大纲3.1 生产线平衡分析基础•生产线平衡分析的概念和目的•生产线平衡分析的基本原理•生产线平衡分析的指标和评价标准3.2 生产线平衡分析方法•时间研究方法•工作内容分析方法•工人数量分析方法3.3 生产线平衡分析的工具•Gantt 图•活动排程表•虚拟工作站模拟3.4 生产线平衡分析的实践•实际案例分析•生产线平衡分析的优化方法•风险分析和控制措施4. 教学方法本课程采用理论教学与实践相结合的教学方法,包括课堂讲授、案例分析、小组讨论、实地考察等环节。
5. 评估方式本课程评估以期末考试和实际案例分析报告为主要依据。
期末考试包括理论题和实践题,以检验学生对生产线平衡分析的理论和实践能力。
实际案例分析报告要求学生运用所学方法和工具分析具体生产线平衡问题,并提出解决方案并进行评估。
6. 参考资料•Buffa, E. S., Sarin, R. K. (1989). Modern Production/Operations Management (6th ed.)。
Wiley Publishing.•Nahmias, S. (2015). Production and Operations Analysis (7th ed.)。
McGraw-Hill Education.7. 结语通过本课程的学习,学生将掌握生产线平衡分析的基本理论和实践技能,能够在实际生产中运用所学知识进行生产线平衡分析和优化。
生产线平衡培训讲义

生产线平衡培训讲义1. 培训目的本讲义旨在向生产线工作人员介绍生产线平衡的概念、原则和方法,以提高生产线的效率和稳定性。
2. 生产线平衡的定义生产线平衡是指通过合理的工作安排,使各个工作站之间的工作负荷相对均衡,以达到提高生产线效率、减少资源浪费和降低生产成本的目标。
3. 生产线平衡的原则生产线平衡的实施需要遵循以下原则:•平衡时间:确保每个工作站的工作时间相对均衡,避免出现工作站之间的长短板问题。
•平衡工序:使每个工作站之间的工序数量相对均衡,避免某个工作站的工序过多或过少。
•平衡人力:合理安排工作人员的数量和分配,避免出现人力不足或闲置的情况。
•平衡设备:合理配置设备和工具,以支持各个工作站的工作,避免出现设备过剩或不足的情况。
4. 生产线平衡的步骤4.1 收集数据在进行生产线平衡前,需要首先收集相关的数据,包括但不限于以下内容:•各个工作站的工作时间。
•各个工作站的工序数量。
•各个工作站的人员数量和技能水平。
•各个工作站的设备和工具情况。
4.2 分析数据在收集完数据后,需要对数据进行分析,找出工作站之间的不平衡情况和影响因素。
通过数据分析,可以确定具体的改进方向。
4.3 制定改进方案根据数据分析的结果,可以制定具体的改进方案。
改进方案可以包括以下内容:•调整工作站的工作时间,使其相对均衡。
•重新分配工作站的工序数量,使其相对均衡。
•调整工作站的人员数量和技能水平,使其相对均衡。
•调整工作站的设备和工具配置,以适应工作站的需求。
4.4 实施改进方案在制定改进方案后,需要进行实施。
实施改进方案时,需要注意以下事项:•确保改进方案的可行性和有效性。
•鼓励工作人员的参与和反馈,以提高方案的实施效果。
•监控改进方案的执行情况,及时进行调整和改进。
4.5 持续改进生产线平衡是一个持续不断的过程,需要不断进行改进和优化。
通过持续改进,可以进一步提高生产线的效率和稳定性。
5. 生产线平衡的效益生产线平衡的实施可以带来以下效益:•提高生产线的效率,减少生产周期。
生产线平衡培训课件
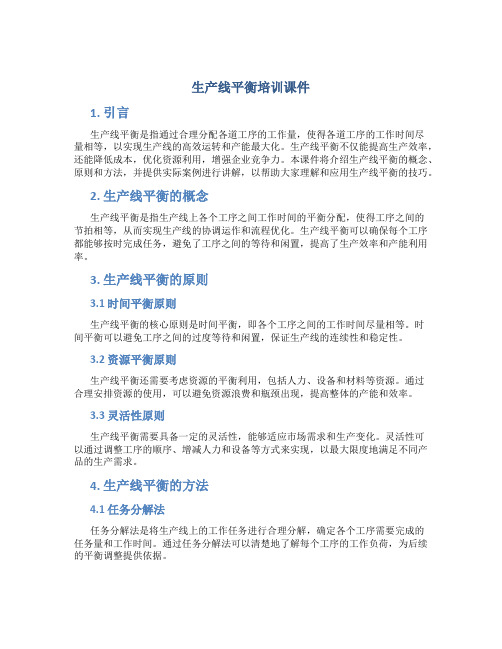
生产线平衡培训课件1. 引言生产线平衡是指通过合理分配各道工序的工作量,使得各道工序的工作时间尽量相等,以实现生产线的高效运转和产能最大化。
生产线平衡不仅能提高生产效率,还能降低成本,优化资源利用,增强企业竞争力。
本课件将介绍生产线平衡的概念、原则和方法,并提供实际案例进行讲解,以帮助大家理解和应用生产线平衡的技巧。
2. 生产线平衡的概念生产线平衡是指生产线上各个工序之间工作时间的平衡分配,使得工序之间的节拍相等,从而实现生产线的协调运作和流程优化。
生产线平衡可以确保每个工序都能够按时完成任务,避免了工序之间的等待和闲置,提高了生产效率和产能利用率。
3. 生产线平衡的原则3.1 时间平衡原则生产线平衡的核心原则是时间平衡,即各个工序之间的工作时间尽量相等。
时间平衡可以避免工序之间的过度等待和闲置,保证生产线的连续性和稳定性。
3.2 资源平衡原则生产线平衡还需要考虑资源的平衡利用,包括人力、设备和材料等资源。
通过合理安排资源的使用,可以避免资源浪费和瓶颈出现,提高整体的产能和效率。
3.3 灵活性原则生产线平衡需要具备一定的灵活性,能够适应市场需求和生产变化。
灵活性可以通过调整工序的顺序、增减人力和设备等方式来实现,以最大限度地满足不同产品的生产需求。
4. 生产线平衡的方法4.1 任务分解法任务分解法是将生产线上的工作任务进行合理分解,确定各个工序需要完成的任务量和工作时间。
通过任务分解法可以清楚地了解每个工序的工作负荷,为后续的平衡调整提供依据。
4.2 循环时间法循环时间法是确定整个生产线的节拍时间,即完成一个循环所需的时间。
通过循环时间法可以确定各个工序的工作时间和节拍,保证生产线上各个工序之间的协调运作。
4.3 平衡调整法平衡调整法是根据任务分解法和循环时间法的结果,对生产线进行平衡调整。
通过增加或减少工序的工作时间,调整工序的顺序和安排,以实现工序之间的平衡。
5. 生产线平衡的实例案例5.1 汽车装配线以汽车装配线为例,通过任务分解法、循环时间法和平衡调整法,可以实现不同工序之间的平衡。
- 1、下载文档前请自行甄别文档内容的完整性,平台不提供额外的编辑、内容补充、找答案等附加服务。
- 2、"仅部分预览"的文档,不可在线预览部分如存在完整性等问题,可反馈申请退款(可完整预览的文档不适用该条件!)。
- 3、如文档侵犯您的权益,请联系客服反馈,我们会尽快为您处理(人工客服工作时间:9:00-18:30)。
5
8.6
6
9.5
7
8.9
8
9.5
9
9.4
10
9.1
11
9.8
12
9.8
13
9.9
14
8.5
15
9.0
16
9.19 #REF! 8.9 #REF!
标准时间 8.8
作业时间 作 8.1 8.5 11.1 9.9 8.4 9.8 9.4 6.4 9.5 8.2 9.8 10.2 11.6 6.6 7.7 业 工程人数 1 1 1 1 1 1 1 1 2 1 1 1 1 1 1 时
LOB 分析技法
Dong guan Samsung Plant Innovation
1
LOB 测量分析技法
LOB 分析技法
一、理论课程
二、实践课程
Dong guan Samsung Plant Innovation
2
一、“LOB”概念:
LOB 分析技法
1、“LOB”定义: Line of Balance 顾名思义:生产线的平衡性。
LOB 分析技法
MAX MIN DIFFERENT
11.6 9.9 8.9 7.8 8.5 6.6 9.0 7.7 6.8 4.9 9.19 8.9
11.60 6.8 4.80 合计
标准分析表
11.1 8.8 8.1 9.38.9 9.2 8.5 9.1 9.8 9.5 9.9 8.9
机种名 LINE名
改 善 后
11
9.25
13.5
12.5 9.25
10
∑HT=66.5,N=6,Neck=13.5,LOB=82.1%
Dong guan Samsung Plant Innovation
分割型
20
再编程案例分析:
案例2
改 善 前
LOB 分析技法
8
7.5
7
6.5
9
7
∑HT=45,N=6,Neck=9,LOB=83.3%
Dong guan Samsung Plant Innovation
15
工程再编程:
3) 工程再编程的 Step :
Step1:现象确认 — 根据“3現主义”确认现场(现场, 现物,现实) — 分析工具:P/Q分析、生产路径分 析、流程线图、工程图 Step2:现象否定/浪费清除 — 7 大浪费、工程别浪费清除表
Side0 Alignment 40Track UV Bonding Grease DUB&Plate Cover lower Ass`y Setp Motor&Track Track 0& Sensor Head& Ass`y check Load Process PCB Screw组 立 Upper Ass`y UVW solder 投入工程 Side Plate Cover zuli
Dong guan Samsung Plant Innovation
17
工程再编程:
4) 工程改善关联:
LOB 分析技法
工程改善的目的
Cost 节减:
— 材料费节减、工数节减、其它制 造经费节减 生产性向上: — Bottle Neck 解除、稼动率向上、 最佳 LIEN构筑 材料损失减少: — 维持搬运/保管过程的品质、包装 方法/容器的改善、检查工程改善
7
三、 DATA 的收集方法
LOB 分析技法
、DATA收集的对象是什么?
“ Time” ,即:作业时间
、 Data收集目的 — 要解决问题的基本: 作为 LOB 评价的基础资料活用 — 确保使用于 LOB 评价的测定体系的信赖度 — 对每一个工程的正确理解
Dong guan Samsung Plant Innovation
Dong guan Samsung Plant Innovation
13
四、工程再编程:
1) 基本概念:
LOB 分析技法
何谓“工程”?
工程 = 作业 + 作业; 作业 = 动作 + 动作
● 否定现有的 LINE 状态,通过在白纸状态下的工程
流程、部品供应、作业者和设备的配置、浪费的清除等,构筑
(你认为)最佳的 LINE。
改 善 后
8
15.5
7.5
7
13.5
6.5
9
16
7
∑HT=45,N=3,Neck=16,LOB=93.8% 统合型
2、LOB 的计算公式:
∑HT LOB = ————— N × T-neck
∑HT:各作业者作业时间总和 N: 生产线的作业人员数
T-neck :Neck工程作业时间
Dong guan Samsung Plant Innovation
3
“LOB”概念:
LOB 分析技法
Dong guan Samsung Plant Innovation
12.0 9.0 6.0 3.0 0.0 1 2 3
8.6 8.4
8.8 8.9
9.59.8
9.4 8.9
9.5 6.4
9.5 9.4
9.1 8.2
9.2 9.1
9.8 9.8
10.2 9.8
标 准 时
4
5
6
7
8
9
10
11
12
13
14
15
16
17
18
19
20
21
22
23
工程NO
1
2
9.2
3
9.1
4
8.9
工程再编程类型:
1、工程分割型再编程
2、工程统合型再编程
Dong guan Samsung Plant Innovation
请大家给出你现在管辖的LINE形态!
19
再编程案例分析:
案例1
改 善 前
LOB 分析技法
11
13.5
18.5
12.5
10
∑HT=65.5,N=5,Neck=18.5,LOB=70.8%
— Modapt
Dong guan Samsung Plant Innovation
12
DATA 的收集方法 2、TIME 的测量方法:
LOB 分析技法
、Stop watch:秒表测量法 IE测量原则:一般测量次数是20次,去掉一个最 大值和一最小值,剩下18个测量值,求其平均就可以 算做测量对象的时间! 注意点:20次测量过程中MIN的出现是在4M配 合最恰当的时候测量出来的,也是我们管理者追求的 管理目标!
Dong guan Samsung Plant Innovation
14
工程再编程: 2) Line 工程再编成 的 Point :
LOB 分析技法 Tact Time 生产 有移动的立式作业实施 SPH达成 100% 标准作业遵守 实施有韵律的作业
Trouble 发生时Line Stop 手作业的简易自动化 Fool Proof 设置 Single 准备交替推进 Cell / U-Line 适用
P T — Pitch Time 投入间隔时间
Dong guan Samsung Plant Innovation
11
DATA 的收集方法 2、TIME 的 测 量 方 法:
LOB 分析技法
、PTS(Predetermined Time System )
预定时间系统
— WF(WORK FACTOR)
8
DATA 的收集方法
、 Data 计划收集时考虑事项
LOB 分析技法
— 单纯化收集:树立尽可能减少不必要Data量的收集取样计划 — 维持Data的一贯性:提供具体的Guideline和Data收集方法, 时间,场所 — 要使Data收集容易:预先准备Check Sheet 或表格 — Data收集的最小化变动:树立让不影响Data收集的妥当性的
-
LOB 分析技法
过剩生产的浪费 待期的浪费 搬运的浪费 加工的浪费 在库的浪费 动作的浪费 不良的浪费
Who When Where What Why How many How to
Step3:工程的目的追求
— 5 次为什么?( 5 ห้องสมุดไป่ตู้HY )
— “ 5 W 2 H” 法 Step4:发现改善对象 — 浪费对策 — SPD, Tact Time, LOB
人来收集Data的计划
— 对Data收集者的教育:为了让Data收集者不只是了解Data 收集方法,还要了解为什么收集而进行说明
Dong guan Samsung Plant Innovation
9
DATA 的处理 Check Sheet
制品名 分析月日 作成者 编程效率 #REF!
11.6 11.1
Dong guan Samsung Plant Innovation
5
生产模式的历史变化:
LOB 分析技法
Dong guan Samsung Plant Innovation
6
生产模式的历史变化:
◆ Cell Line 和 U-Line的特性对比
区 分
LOB 分析技法
特 性
1940年开始日本 TOYOTA在汽车业开始 “U”字行Line 动作的立式作业→纯作业 现象浪费的 ZERO化 有利于机械加工/大型制品 从投入到完成包装由一个人完成
4
二、生产模式的历史变化:
◆ Conveyor System 的出现
LOB 分析技法
1920年 美国 FordSystem (福特) 提出了 C/V System ◆ Toyota Production —“ TPS”生产模式 — 传送带生产方式,就是现在的流水线生产(C/V LINE )。 特点:适用于大批量生产 1930年日本的丰田汽车公司总裁 Toyota提出新 ◆ “Lean Production System” 的生产方式。40年代又出现“U”Line. “TPS”主要特点 有: 1、年,美国的 自动化 1980 MIT(Massachusetts Institute ◆ “Cell Line”生产模式 2、 JIT )麻省理工学院提出 — Just In Time (JIT是Toyota在超 of Technology 市购物过程中突发奇想而出的) 1995年,COMPAQ 公司提出“; Cell Line”生产模 式,相继之后 VOLVO 公司也导入 Cell Line 生产模 式,(U-Line 的变异出CELL)