作业条件危险性评价
作业条件危险性分析评价法

附录A作业条件危险性分析评价法(LEC)
作业条件危险性分析评价法(简称LEC)。
L(likelihood,事故发生的可能性)、E(exposure,人员暴露于危险环境中的频繁程度)和C(consequence,一旦发生事故可能造成的后果)。
给三种因素的不同等级分别确定不同的分值,再以三个分值的乘积D(danger,危险性)来评价作业条件危险性的大小,即:D=L×E×C。
D值越大,说明该作业活动危险性大、风险大。
表A.1 事故事件发生的可能性(L)判断准则
表A.2 暴露于危险环境的频繁程度(E)判断准则
表A.3 发生事故事件偏差产生的后果严重性(C)判别准则
表A.4 风险等级判定准则及控制措施(D)。
作业条件危险性评价(LEC法)及举例
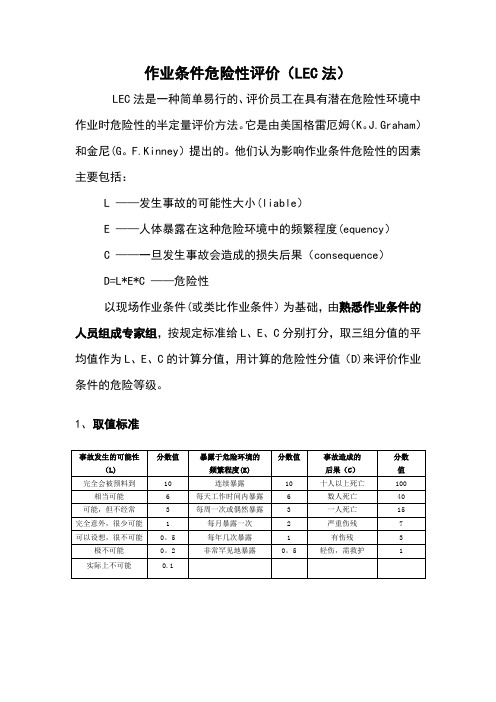
作业条件危险性评价(LEC法)
LEC法是一种简单易行的、评价员工在具有潜在危险性环境中作业时危险性的半定量评价方法。
它是由美国格雷厄姆(K。
J.Graham)和金尼(G。
F.Kinney)提出的。
他们认为影响作业条件危险性的因素主要包括:
L ——发生事故的可能性大小(liable)
E ——人体暴露在这种危险环境中的频繁程度(equency)
C ——一旦发生事故会造成的损失后果(consequence)
D=L*E*C ——危险性
以现场作业条件(或类比作业条件)为基础,由熟悉作业条件的人员组成专家组,按规定标准给L、E、C分别打分,取三组分值的平均值作为L、E、C的计算分值,用计算的危险性分值(D)来评价作业条件的危险等级。
1、取值标准
2、危险等级划分标准
举例说明
高处焊接作业辨识结果。
作业条件危险性评价

第五节主要危险、有害因素评价1、作业条件危险性评价(1)作业条件危险性评价法简介作业条件危险性评价法,即格雷厄姆——金尼法,LEC法。
对于一个具有潜在危险性的作业条件,影响危险性的主要因素有3个:1) 发生事故或危险事件的可能性(L):与实际发生的概率有关,从完全出乎意料之外到完全会被预料到。
发生事故或危险事件的可能性(L):2) 暴露于这种危险环境的频率(E):作业人员暴露于危险作业环境的次数越多、时间越长,则受到伤害的可能性也就越大。
暴露于这种危险环境的频率(E):3) 事故一旦发生可能产生的后果(C):造成事故或危险事故的人身伤害或物质损失可在很大范围内变化,从“引人注目,需要救护”到“大灾难”。
事故一旦发生可能产生的后果(C):4) 确定了上述3个具有潜在危险性的作业条件的分值,即可得危险性分值(D)。
计算公式:D=L×E×C。
危险性程度从“稍有危险,或许可以接受”到“显着危险,需要整改”到“极其危险,不能继续作业”。
危险性程度等级划分标准(D)(2)作业条件危险性评价分析1)作业单元及其存在的危险、危害因素选取整个生产、储存场所作为评价作业单元。
根据格雷厄姆-金尼法采用的评价方法和原则,针对东莞市大山气体有限公司氧气、乙炔生产项目具体情况及生产过程中具有潜在危险性的作业综合评估、评价。
2)作业条件危险性评价汇总表作业条件危险性评价结果汇总表3)作业条件危险性评价对策①严格执行《安全生产法》、《危险化学品安全管理条例》、《建筑设计防火规范》等国家、地方、行业的法律、法规、制度和标准规范的要求。
②完善并正常运作安全组织机构,明确专职安全管理人员及其职责。
③完善并认真执行各项安全生产责任制和各项安全管理制度。
④完善并正常运作事故应急救援抢救组织,做好事故预防与处理工作,定期组织事故应急救援抢救演练。
⑤完善各种安全台帐和动火作业票证等管理。
⑥完善安全操作规程。
⑦加强企业管理人员和从业人员的安全培训工作,持证上岗。
作业条件危险性分析LEC评价法

作业条件危险性分析LEC评价法概述作业条件危险性分析(LEC)评价法是指对危险物质或危险作业场所中可能发生的事故事件进行综合评价和分析,以确定其引发事故的频率和后果的程度,并通过评价结果来加强危险物质或危险作业场所的安全措施。
LEC评价法具有简单、快速和高效的特点,广泛应用于工业、交通、建筑等领域。
LEC评价法的原理LEC评价法是基于对危险作业条件的分析,综合考虑以下三个因素来评价其危险性:1.损失事件的可能性(L)2.损失事件发生时造成的影响(E)3.损失事件的后果的严重性(C)L、E、C三个因素都是可以用数值表示的。
其中,L代表概率,常以年度频次为衡量标准。
E和C通常采用财产和人命威胁的标准来定义。
LEC评价法能够综合考虑这些因素,其原理类似于风险矩阵方法,将它们与预设的标准相比较,并将危险性分为五个级别。
LEC评价法具体步骤LEC评价法的具体步骤如下:步骤1:确定损失事件(LOA)该步骤是为了明确评估的对象而进行的。
首先要将待评估的作业条件(LOA)明确规定为一个确定的损失事件,并给出其发生的时间与空间范围。
步骤2:确定发生的频率和影响损失事件的因素该步骤主要是为了确定评估损失事件(L, E, C)的因素、影响和发生的频率,并进行概率分析,确定各因素和影响对损失事件发生的贡献值。
步骤3:进行LEC分析该步骤主要是根据步骤2中确定的各因素和影响的贡献值,计算出评估结果,并根据预先设定的标准将危险性分为五个级别。
步骤4:确定减轻或消除危险的措施根据LEC评价结果,确定减轻或消除危险的措施,使评价结果进一步优化。
LEC评价法在实际中的应用LEC评价法广泛应用于各种危险作业条件的分析和评价,如化工、石油、建筑等行业。
在实际应用中,可以设置多种不同的评估方法和标准,以适应不同的行业或特定任务的需求。
例如,对于一个化工企业的储罐区,可采用LEC评价法来评估其危险性,按照以下步骤展开:步骤一:确定损失事件(LOA)•储罐区泄漏步骤二:确定发生的频率和影响损失事件的因素•液体储存量•损坏储罐数量•容器维护历史•消防设施配置情况•作业规程步骤三:进行LEC分析•发生概率–1年一次 1–1年以上 2•影响程度–经济受损低于8000美元 1–经济受损8万美元以上 5•严重程度–伤亡人数0人 1–伤亡人数超过5人 5根据上述分析结果,可将危险性分为五个级别,以评估储罐区的安全等级。
作业条件危险性评价法(LECD)
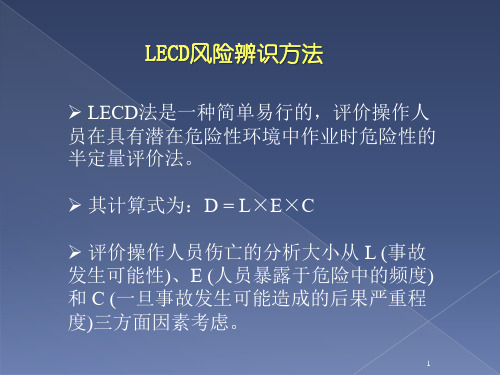
分值 10 6 3 1 0.5 0.2 0.1
事故或事件发生的可能性 完全可以预料 相当可能
可能,但不经常 可能性小
很不可能,完全意外 极不可能 实际不可能
9
10
11
12
设备设施风险辨识:
13
3
完整的LECD表:
4
作业内容:
作业内容: 通氯、高压釜维修、离心机维修、高压釜更换填料、循环水池清理 、电 气焊施工。。。。
5
可能产生的危害:
可能产生危害: 蒸汽烫伤、触电、机械伤害、淹溺、化学灼伤、蒸汽烫伤。。。
6
事故类别:
事故类别:参照 GB6441-86《企业伤亡事故分类》 1、物体打击;2、
LECD风险辨识方法
➢ LECD法是一种简单易行的,评价操作人 员在具有潜在危险性环境中作业时危险性的 半定量评价法。
➢ 其计算式为:D = L×E×C
➢ 评价操作人员伤亡的分析大小从 L (事故 发生可能性)、E (人员暴露于危险中的频度) 和 C (一旦事故发生可能造成的后果严重程 度)三方面因素考虑。
车辆伤害;3、机械伤害;4、起重伤害;5、触电;6、淹溺;7、灼烫;
8、火灾;9、高处坠落;10、坍塌;11、冒顶片帮;12、透水;13放炮
;14、瓦斯爆炸;15、火药爆炸;16、锅炉爆炸;17、容器爆炸;18、
其它爆炸;19、中毒和窒息;20其他伤害。
7
现有控制措施:
现有控制措施: 穿戴好劳保用品、遵守安全规程、专人监护、备好应急防护器材、 加强培训提高技能、贴警示牌。。。。
1
优点:
➢ 无需深奥的理论,便于在较短时间内使广大的危害因
素识别评价人员掌握;
➢ 通过半定量计算,可分析出各危害因素的风险等级,
8-作业条件危险性评价法
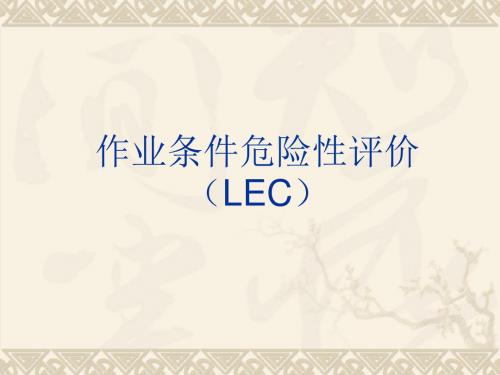
四、安全措施。根据工序评价出的危险度等级,在技术、设 备和管理上采取相应的措施。
(1)按评级等级采取安全措施。 (2)管理措施主要包括: ①人员配备。 ②教育培训。 ③维修。 五、用事故案例进行再评价。按照第四步讨论了安全措施之 后,再参照同类装置以往的事故案例评价其安全性,反过来 再讨论安全措施。 六、用其他评价方法进行再评价。通过安全性的再评价,发
二、定性评价。对建厂条件物质理化特性、工程系统图、各 种设备、操作要领、人员配备、安全教育计划等进行检查和 定性分析,确定各评分标准。 三、定量评价。把装置分成几个工序,再把工序各个单元的 危险度定量,以其中最大的危险度作为本工序的危险度。
危险度的定量评价,是将装置分为几个单元,对各单 元的物料、容量、温度、压力和操作等进行评定,最后按照 这些项的分数之和来评定该单元的危险度等级。
优缺点及适用范围
作业条件危险性评价法评价人们在某种具有潜在危 险的作业环境中进行作业的危险程度,该法简单易 行,危险程度的级别划分比较清楚、醒目。但是, 由于它主要是根据经验来确定3个因素的分数值及 划定危险程度等级,因此具有一定的局限性。而且 它是一种作业的局部评价,故不能普遍适用。此外, 在具体应用时,还可根据自己的经验、具体情况对 该评价方法作适当修正。
暴露于危险环境的频繁程度(E):清洗人员每天在此环 境中工作,取E=6。
第11页
发生事故产生的后果(C):如果发生燃烧爆炸事故,后果将是 非常严重的,可能造成人员的伤亡,取C=15。
D=LEC =3×6×15 =270
270处于160-320之间,危险等级属“高度危险、需立即整改” 的范畴。 整改措施: 1)车间加强通风,对通风设备定时维修; 2)操作人员穿戴防护用品; 3)及时编写事故应急预案并落实预案内容;
作业条件危险性评价法

作业条件危险性评价法一、作业条件危险性评价法概述作业条件危险性评价法是基于危险识别的原理,通过对工作环境中存在的潜在危险源进行全面识别和评估,从而达到保障员工安全和健康的目的。
它主要包括以下几个步骤:确定评价目标、收集信息、危险源识别和分析、评估危险性、风险等级划分和控制建议。
二、作业条件危险性评价法的评估流程1.确定评价目标:明确评价的工作环境和受众,确定对哪些危险源进行评估。
2.收集信息:收集与评估目标相关的信息,包括工作环境的布局、设备和工具的使用情况,职工的工作经验和技能等。
3.危险源识别和分析:通过观察和记录,确定工作环境中存在的潜在危险源,例如有害物质、高温、噪音等。
4.评估危险性:对危险源进行量化评估,包括对危险源的频率、暴露时间、暴露容量等进行分析,计算潜在的损害程度。
5.风险等级划分:根据危险性评估的结果,划分风险等级,确定危险性的程度。
6.控制建议:根据评估结果,提出相应的控制措施,包括工程控制、行政控制和个体防护等方面的建议。
三、作业条件危险性评价法的应用范围1.制造业:评估制造业中的设备操作、物料运输和工艺流程等环节中存在的危险源,提出相应的改进措施,减少事故风险。
2.石油化工:对于石油化工行业中的危险源进行评估,包括高温、高压和易燃易爆物质的处理等,确保工作环境的安全和稳定。
3.建筑施工:评估建筑施工现场的潜在危险源,如高处坠落、坍塌、电击等风险,提出相应的控制措施,确保施工过程的安全性。
4.机械制造:评估机械制造过程中存在的各类危险源,如机器设备操作、切削加工、电气设备等,提出相应的安全措施,减少工伤事故的发生。
作业条件危险性评价法具有指导实践、科学性和针对性的特点,对于组织保障员工安全和健康具有重要意义。
只有通过全面、科学地评估工作环境的危险性,才能提供有力的决策依据,采取相应的控制措施,保证员工的身体健康和工作安全。
作业条件危险性评价法
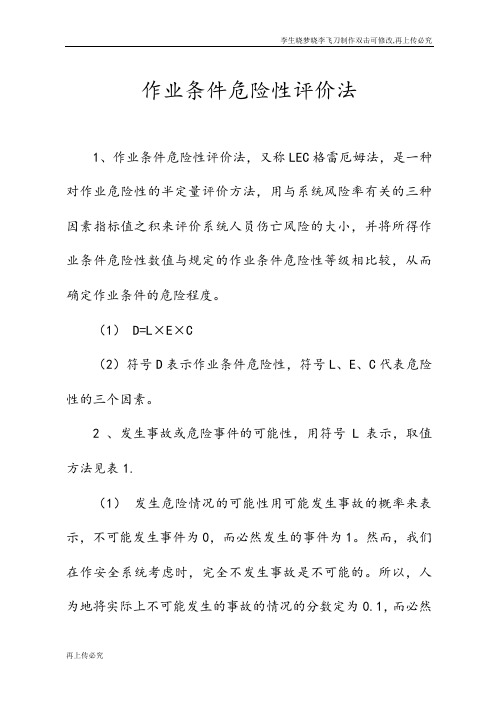
李生晓梦晓李飞刀制作双击可修改,再上传必究
再上传必究作业条件危险性评价法
1、作业条件危险性评价法,又称LEC格雷厄姆法,是一种对作业危险性的半定量评价方法,用与系统风险率有关的三种因素指标值之积来评价系统人员伤亡风险的大小,并将所得作业条件危险性数值与规定的作业条件危险性等级相比较,从而确定作业条件的危险程度。
(1) D=L×E×C
(2)符号D表示作业条件危险性,符号L、E、C代表危险性的三个因素。
2 、发生事故或危险事件的可能性,用符号L表示,取值方法见表1.
(1)发生危险情况的可能性用可能发生事故的概率来表示,不可能发生事件为0,而必然发生的事件为1。
然而,我们在作安全系统考虑时,完全不发生事故是不可能的。
所以,人为地将实际上不可能发生的事故的情况的分数定为0.1,而必然。
- 1、下载文档前请自行甄别文档内容的完整性,平台不提供额外的编辑、内容补充、找答案等附加服务。
- 2、"仅部分预览"的文档,不可在线预览部分如存在完整性等问题,可反馈申请退款(可完整预览的文档不适用该条件!)。
- 3、如文档侵犯您的权益,请联系客服反馈,我们会尽快为您处理(人工客服工作时间:9:00-18:30)。
作业条件危险性评价(LEC)
作业条件危险性评价是一种半定量危险性评价法。
它是以与系统风险率有关的三种因素指标值之积来评价系统人员伤亡风险的大小。
其简化公式是:D=LEC。
L—事故或危险事件的可能性大小。
当用概率来表示时,绝对不可能的事件发生的概率为0;而可能性小、完全意外发生的事件的分数值为1,在系统安全考虑时,绝对不发生事故是不可能的,所以认为地将事故实际不可能性的分数值定位0.1,而完全可能预料要发生的事件的可能性分数值定位10。
介于两者之间发生事故的可能性制定了若干个中间值,如下表所示。
E—暴露于危险环境的频繁程度。
人员出现在危险环境中的时间越频繁,则危险性越大。
规定连续暴露在此环境的情况为10,而非常罕见地暴露在危险环境中的分数值为0.4。
同样,将介于两者之间的各种为项规定若干个中间值,如下表所示。
C—发生事故可能造成的后果。
事故造成的人身伤害变化范围很大,对伤亡事故来说,可能从极小的轻伤直到多人死亡的严重结果。
由于发生事故可能产生的范围较广,所以规定分数值为1—100,轻伤规定分数为1,把发生事故造成10人以上死亡的可能性分数规定为100,其他情况的分数值均在1与100之间,如下表所示。
D—危险性分值。
根据公式就可以计算作业的危险程度,但关键是如何确定各个分值之积总分的评价。
依据经验,总分数值小于20被认为少有危险为1级,是低危险;如果危险分数值等于或大于70—160之间,那就是显著危险性,需要及时整改;如果危险分值等于或大于160时,其危险等级达到3-3级以上,那就表示有显著危险或高度危险性,应立即停止生产直到环境得到改善为止。
危险等级的划分是凭经验判断,难免带有局限性,不能认为是普遍适用的。
应用时需要结合实际情况予以修正。
危险性分值等级划分如下表所示。