作业条件危险性分析评价法
作业条件危险性分析评价法

暴露于危险ห้องสมุดไป่ตู้境的频繁程度(E)判断准则
分值
频繁程度
分值
频繁程度
10
连续暴露(8小时不离工作岗位,或连班作业,算“连续暴露”)
2
每月一次暴露
6
每天工作时间内暴露
1
每年几次暴露
3
每周一次或偶然暴露
非常罕见地暴露
发生事故事件偏差产生的后果严重性(C)判别准则
分值
法律法规
及其他要求
人员伤亡
直接经济损失
风险值
风险等级
应采取的行动/控制措施
实施期限
A/1级
重大风险
在采取措施降低危害前,不能继续作业,对改进措施进行评估
立刻
160~320
B/2级
较大危险
采取紧急措施降低风险,建立运行控制程序,定期检查、测量及评估
立即或近期整改
70~160
C/3级
一般风险
可考虑建立目标、建立操作规程,加强培训及沟通
2年内治理
D=L×E×C。D值越大,说明该作业活动危险性大、风险大。
事故事件发生的可能性(L)判断准则
分值
事故、事件或偏差发生的可能性
10
完全可以预料。
6
相当可能;或危害的发生不能被发现(没有监测系统);或在现场没有采取防范、监测、保护、控制措施;或在正常情况下经常发生此类事故、事件或偏差
3
可能,但不经常;或危害的发生不容易被发现;现场没有检测系统或保护措施(如没有保护装置、没有个人防护用品等),也未作过任何监测;或未严格按操作规程执行;或在现场有控制措施,但未有效执行或控制措施不当;或危害在预期情况下发生
(万元)
停工
作业条件危险性分析LEC评价法

作业条件危险性分析LEC评价法概述作业条件危险性分析(LEC)评价法是指对危险物质或危险作业场所中可能发生的事故事件进行综合评价和分析,以确定其引发事故的频率和后果的程度,并通过评价结果来加强危险物质或危险作业场所的安全措施。
LEC评价法具有简单、快速和高效的特点,广泛应用于工业、交通、建筑等领域。
LEC评价法的原理LEC评价法是基于对危险作业条件的分析,综合考虑以下三个因素来评价其危险性:1.损失事件的可能性(L)2.损失事件发生时造成的影响(E)3.损失事件的后果的严重性(C)L、E、C三个因素都是可以用数值表示的。
其中,L代表概率,常以年度频次为衡量标准。
E和C通常采用财产和人命威胁的标准来定义。
LEC评价法能够综合考虑这些因素,其原理类似于风险矩阵方法,将它们与预设的标准相比较,并将危险性分为五个级别。
LEC评价法具体步骤LEC评价法的具体步骤如下:步骤1:确定损失事件(LOA)该步骤是为了明确评估的对象而进行的。
首先要将待评估的作业条件(LOA)明确规定为一个确定的损失事件,并给出其发生的时间与空间范围。
步骤2:确定发生的频率和影响损失事件的因素该步骤主要是为了确定评估损失事件(L, E, C)的因素、影响和发生的频率,并进行概率分析,确定各因素和影响对损失事件发生的贡献值。
步骤3:进行LEC分析该步骤主要是根据步骤2中确定的各因素和影响的贡献值,计算出评估结果,并根据预先设定的标准将危险性分为五个级别。
步骤4:确定减轻或消除危险的措施根据LEC评价结果,确定减轻或消除危险的措施,使评价结果进一步优化。
LEC评价法在实际中的应用LEC评价法广泛应用于各种危险作业条件的分析和评价,如化工、石油、建筑等行业。
在实际应用中,可以设置多种不同的评估方法和标准,以适应不同的行业或特定任务的需求。
例如,对于一个化工企业的储罐区,可采用LEC评价法来评估其危险性,按照以下步骤展开:步骤一:确定损失事件(LOA)•储罐区泄漏步骤二:确定发生的频率和影响损失事件的因素•液体储存量•损坏储罐数量•容器维护历史•消防设施配置情况•作业规程步骤三:进行LEC分析•发生概率–1年一次 1–1年以上 2•影响程度–经济受损低于8000美元 1–经济受损8万美元以上 5•严重程度–伤亡人数0人 1–伤亡人数超过5人 5根据上述分析结果,可将危险性分为五个级别,以评估储罐区的安全等级。
作业条件危险性分析评价法(LEC)
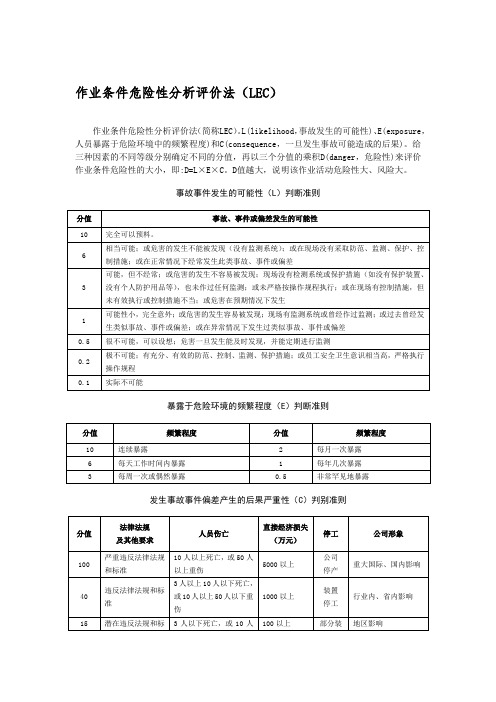
作业条件危险性分析评价法(LEC)
作业条件危险性分析评价法(简称LEC)。
L(likelihood,事故发生的可能性)、E(exposure,人员暴露于危险环境中的频繁程度)和C(consequence,一旦发生事故可能造成的后果)。
给三种因素的不同等级分别确定不同的分值,再以三个分值的乘积D(danger,危险性)来评价作业条件危险性的大小,即:D=L×E×C。
D值越大,说明该作业活动危险性大、风险大。
事故事件发生的可能性(L)判断准则
暴露于危险环境的频繁程度(E)判断准则
发生事故事件偏差产生的后果严重性(C)判别准则
风险等级判定准则及控制措施(D)。
作业条件危险性分析法(LEC)评价准则

作业条件风险程度评价(LEC)评价准则
基本原理是根据风险点辨识确定的危害及影响程度与危害及影响事件发生的可能性乘积确定风险的大小。
定量计算每一种危险源所带来的风险可采用如下方法:
D=LEC。
式中:D—风险值;
L—发生事故的可能性大小;
E—暴露于危险环境的频繁程度;
C—发生事故产生的后果。
当用概率来表示事故发生的可能性大小(L)时,绝对不可能发生的事故概率为0;而必然发生的事故概率为1。
从系统安全角度考虑,绝对不发生事故是不可能的,所以人为地将发生事故可能性极小的分数定为0.1,而必然要发生的事故的分数定为10,介于这两种情况之间的情况指定为若干中间值。
当确定暴露于危险环境的频繁程度(E)时,人员出现在危险
环境中的时间越多,则危险性越大,规定连续出现在危险环境的情况定为10,而非常罕见地出现在危险环境中定为0.5,介于两者之间的各种情况规定若干个中间值。
关于发生事故产生的后果(C),由于事故造成的人身伤害与财产损失变化范围很大,规定其分数值为1-100,把需要救护的轻微损伤或较小财产损失的分数规定为1,把造成多人死亡或重大财产损失的可能性分数规定为100,其他情况的数值均为1与100之间。
风险值(D)求出之后,企业应根据实际情况确定风险级别的界限值,以符合持续改进的思想。
下表可作为确定风险级别界限值的参考。
重大风险、较大风险、一般风险和低风险,分别用红、橙、黄、蓝四种颜色标示,按照全省统一的色谱技术要求使用颜色。
安全风险等级四色标识RGB色谱标准。
作业条件危险性分析法(LEC)评价准则

作业条件风险程度评价(LEC)评价准则
基本原理是根据风险点辨识确定的危害及影响程度与危害及影响事件发生的可能性乘积确定风险的大小。
定量计算每一种危险源所带来的风险可采用如下方法:
D=LEC。
式中:D—风险值;
L—发生事故的可能性大小;
E—暴露于危险环境的频繁程度;
C—发生事故产生的后果。
当用概率来表示事故发生的可能性大小(L)时,绝对不可能发生的事故概率为0;而必然发生的事故概率为1。
从系统安全角度考虑,绝对不发生事故是不可能的,所以人为地将发生事故可能性极小的分数定为0.1,而必然要发生的事故的分数定为10,介于这两种情况之间的情况指定为若干中间值。
当确定暴露于危险环境的频繁程度(E)时,人员出现在危险
环境中的时间越多,则危险性越大,规定连续出现在危险环境的情况定为10,而非常罕见地出现在危险环境中定为0.5,介于两者之间的各种情况规定若干个中间值。
关于发生事故产生的后果(C),由于事故造成的人身伤害与财产损失变化范围很大,规定其分数值为1-100,把需要救护的轻微损伤或较小财产损失的分数规定为1,把造成多人死亡或重大财产损失的可能性分数规定为100,其他情况的数值均为1与100之间。
风险值(D)求出之后,企业应根据实际情况确定风险级别的界限值,以符合持续改进的思想。
下表可作为确定风险级别界限值的参考。
重大风险、较大风险、一般风险和低风险,分别用红、橙、黄、蓝四种颜色标示,按照全省统一的色谱技术要求使用颜色。
安全风险等级四色标识RGB色谱标准。
作业条件危险性分析法
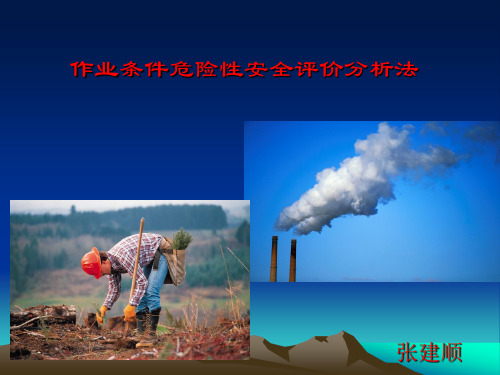
危险程度
极其危险,不能继续作业 高度危险,需要立即整改 显著危险,需要整改
分值
危险程度
20-70 可能危险,需要注意 <20 稍有危险,或许可能接受
由经验可知,危险性分值在20以下的环境属低 危险性,一般可以被人们接受,这样的危险性比 骑自行车通过拥挤的马路去上班之类的日常生活 活动的危险性还要低。当危险性分值在20~70时, 则需要加以注意;危险性分值70~160的情况时, 则有明显的危险,需要采取措施进行整改;同样, 根据经验,当危险性分值在160~320的作业条件 属高度危险的作业条件,必须立即采取措施进行 整改。危险性分值在320分以上时,则表示该作 业条件极其危险,应该立即停止作业直到作业条 件得到改善为止,详见表4。
2 优缺点及适用范围 作业条件危险性评价法评价人们在某种 作业条件危险性评价 具有潜在危险的作业环境中进行作业的危 险程度,该法简单易行,危险程度的级别 划分比较清楚、醒目。但是,由于它主要 是根据经验来确定3个因素的分数值及划定 危险程度等级,因此具有一定的局限性。 而且它是一种作业的局部评价,故不能普 遍适用。此外,在具体应用时,还可根据 自己的经验、具体情况对该评价方法作适 当修正。
表2 人体暴露在这种危险环境中的频繁程度E 分数值 暴露于危险环境的频繁程度 10 连续暴露(包括四班三运转) 6 每天工作时间内暴露 3 每周一次,或偶然暴露 2 每月一次暴露 1 每年几次暴露 5 非常罕见地暴露 表3 发生事故产生的后果C 分数值 发生事故产生的后果 100 大灾难,许多人死亡 40 灾 难,数人死亡 15 非常严重,一人死亡 7 严重,重伤 3 重大,致残 1 引人注目,需要救护
针对被评价的具体的作业条件,由有关人员 (车间主任、安全人员、技术人员、工人代表等) 组成小组,依据过去的经历、有关的知识,经充 分讨论,固定L、E、C的分数植;然后计算三个 指标的乘积,得出危险性分值D;最后依D值大小 确定风险等级。 表4 危险性分值D D值 危险程度 风险等级 >320 极其危险,不能继续作业 5 160~320 高度危险,要立即整改 4 70~160 显著危险,需要整改 3 20~70 一般危险,需要注意 2 <20 稍有危险,可以接受 1
作业条件分析法

作业条件危险性评价
表1-9 发生事故产生的后果(C)
分数 值
发生事故产生的后果
100
10人以上死亡
30
2—9人死亡
15
1人死亡
7
伤残
3
重伤
1
轻伤
作业条件危险性评价
D—危险性分值 根据公式就可以计算作业的危险程度,但关键是如何确定 各个分值之积总分的评价。依据经验,总分数值小于20被 认为少有危险为1级,是低危险;如果危险分数值等于或 大于70—160之间,那就是显著危险性,需要及时整改; 如果危险分值等于或大于160时,其危险等级达到3-3级 以上,那就表示有显著危险或高度危险性,应立即停止生 产直到环境得到改善为止。危险等级的划分是凭经验判断, 难免带有局限性,不能认为是普遍适用的。应用时需要结 合实际情况予以修正。危险性分值等级划分如表4所示。
作业条件危险性评价
表1 发生事故的可能性(L)
分数值
10 6 3 1 0.5 0.2 0.1
事故发生的可能性
完全可能预料 相当可能
可能但不经常 可能性小,实际不可能
作业条件危险性评价
E—暴露于危险环境的频繁程度 人员出现在危险环境中的时间越频繁,则危险性越 大。规定连续暴露在此环境的情况为10,而非常 罕见地暴露在危险环境中的分数值为0.4。同样, 将介于两者之间的各种为项规定若干个中间值,如 表2所示。
作业条件危险性评价
表1-10 危险等级划分
分数值
>320 160— 320 70—160 20—70 <20
危险程度 极其危险 高度危险 显著危险 一般危险 稍有危险
危险等级 5 4 3 2 1
作业条件危险性评价
作业条件危险性评价法( LEC法)
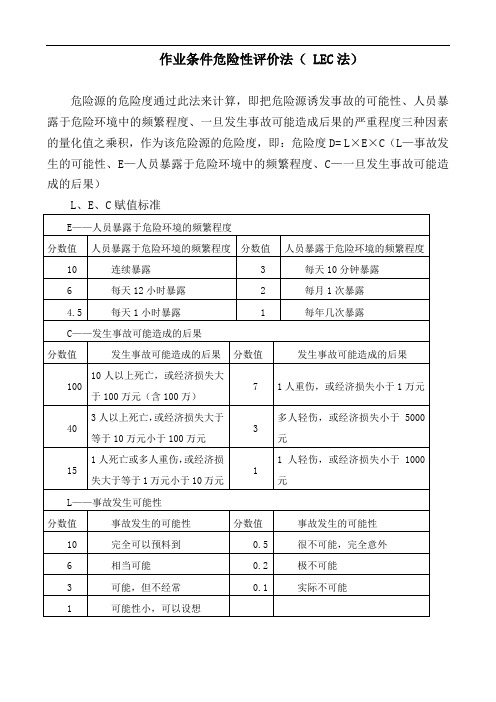
作业条件危险性评价法( LEC法)
危险源的危险度通过此法来计算,即把危险源诱发事故的可能性、人员暴露于危险环境中的频繁程度、一旦发生事故可能造成后果的严重程度三种因素的量化值之乘积,作为该危险源的危险度,即:危险度D= L×E×C(L—事故发生的可能性、E—人员暴露于危险环境中的频繁程度、C—一旦发生事故可能造成的后果)
L、E、C赋值标准
危险性等级划分标准
例子:
某工厂冲床无红外光电等保护装置,而未设计使用安全模,也无钩、夹等辅助工具,因此操作时可能发生冲手事故,发生事故的危险度计算方法:
1、确定分值:
L值:属于相当可能,6
E值:属于每天作业,6
C值:致残、严重伤害,3,7
D值:108,252。
- 1、下载文档前请自行甄别文档内容的完整性,平台不提供额外的编辑、内容补充、找答案等附加服务。
- 2、"仅部分预览"的文档,不可在线预览部分如存在完整性等问题,可反馈申请退款(可完整预览的文档不适用该条件!)。
- 3、如文档侵犯您的权益,请联系客服反馈,我们会尽快为您处理(人工客服工作时间:9:00-18:30)。
附录A作业条件危险性分析评价法(LEC)
作业条件危险性分析评价法(简称LEC)。
L(likelihood,事故发生的可能性)、E(exposure,人员暴露于危险环境中的频繁程度)和C(consequence,一旦发生事故可能造成的后果)。
给三种因素的不同等级分别确定不同的分值,再以三个分值的乘积D(danger,危险性)来评价作业条件危险性的大小,即:D=L×E×C。
D值越大,说明该作业活动危险性大、风险大。
表A.1 事故事件发生的可能性(L)判断准则
表A.2 暴露于危险环境的频繁程度(E)判断准则
表A.3 发生事故事件偏差产生的后果严重性(C)判别准则
表A.4 风险等级判定准则及控制措施(D)。