有害元素对高炉炉缸侧壁碳砖的侵蚀
有害元素对宣钢高炉的影响
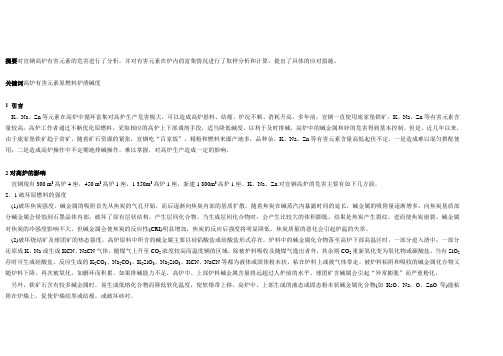
摘要对宣钢高炉有害元素的危害进行了分析,并对有害元素在炉内的富集情况进行了取样分析和计算,提出了具体的应对措施。
关键词高炉有害元素原燃料炉渣碱度1 引言K、Na、Zn等元素在高炉中循环富集对高炉生产危害极大,可以造成高炉悬料、结瘤、炉况不顺、消耗升高。
多年前,宣钢一直使用庞家堡铁矿,K、Na、Zn等有害元素含量较高,高炉工作者通过不断优化原燃料,采取相应的高炉上下部调剂手段,适当降低碱度,以利于及时排碱,高炉中的碱金属和锌的危害得到基本控制。
但是,近几年以来,由于庞家堡铁矿趋于贫矿,随着矿石资源的紧张,宣钢吃“百家饭”,精粉和燃料来源产地多,品种杂,K、Na、Zn等有害元素含量高低起伏不定,一是造成难以混匀搭配使用;二是造成高炉操作中不定期地排碱操作,难以掌握,对高炉生产造成一定的影响。
2对高炉的影响宣钢现有300 m3高炉4座,450 m3高炉1座,1 350m3高炉1座,新建1 800m3高炉1座。
K、Na、Zn对宣钢高炉的危害主要有如下几方面。
2.1破坏原燃料的强度(1)破坏焦炭强度。
碱金属的吸附首先从焦炭的气孔开始,而后逐渐向焦炭内部的基质扩散,随着焦炭在碱蒸汽内暴露时间的延长,碱金属的吸附量逐渐增多。
向焦炭基质部分碱金属会侵蚀到石墨晶体内部,破坏了原有层状结构,产生层间化合物。
当生成层间化合物时,会产生比较大的体积膨胀,结果是焦炭产生裂纹,进而使焦炭崩裂。
碱金属对焦炭的冷强度影响不大,但碱金属会使焦炭的反应性(CRI)明显增加,焦炭的反应后强度将明显降低。
焦炭质量的恶化会引起炉温的失常。
(2)破坏烧结矿及球团矿的热态强度。
高炉原料中所含的碱金属主要以硅铝酸盐或硅酸盐形式存在,炉料中的碱金属化合物落至高炉下部高温区时,一部分进入渣中;一部分还原成K、Na或生成KCN、NaCN气体,随煤气上升至CO2浓度较高而温度辆的区域,除被炉料吸收及随煤气逸出者外,其余则CO2重新氧化变为氧化物或碳酸盐,当有SiO2存时可生成硅酸盐。
有害元素对高炉冶炼的影响

有害元素对高炉冶炼的影响有害元素通常指硫(S)、磷(P)、钾(K)、钠(Na)、铅(Pb)、Zn (锌)、As(砷)、Cu。
通常高炉冶炼对铁矿石要求如下:Pb<0.1%、Zn<0.1%、As<0.07%、Cu<0.2%、K2O+Na2O≤0.25%。
硫(S):硫对钢材是最为有害的成份,它使钢材产生“热脆性”。
铁矿石中硫含量高,高炉脱硫成本增大,所以入炉铁矿石含硫愈少愈好。
λ磷(P):磷对钢材来说也是常见有害元素之一,它使钢材产生“冷脆性”。
铁矿石中的磷,在高炉冶炼时100%进入生铁,烧结也不能脱磷,控制生铁含磷量主要是靠控制铁矿石含磷量。
脱磷只能通过炼钢来进行,增加了炼钢的脱磷成本。
因此,铁矿石含磷越低越好。
λ碱金属:碱金属主要有钾和钠。
钾、钠对高炉的影响不是正比例性质,高炉本身有一定的排碱能力,碱金属在控制范围内对高炉影响不大。
但是入炉铁矿石碱金属含量太多,超过高炉排碱能力,就会形成碱金属富集,导致高炉中上部炉料碱金属含量大大超过入炉料原始水平。
铁矿石含有较多的碱金属极易造成软化温度降低,软熔带上移,不利于发展间接还原,造成焦比升高。
球团含有碱金属会造成球团异常膨胀引起严重粉化,恶化料柱透气性。
碱金属对焦炭性能破坏也很严重。
另外,高炉中上部碱金属化合物黏附在炉墙上,促使炉墙结厚、结瘤并破坏砖衬。
因此,铁矿石含碱金属越低越好。
λ铅(Pb):铅在高炉中几乎全部被还原,由于密度高达11.34t∕m³,故沉于死铁层之下,易破坏炉底砖缝,有可能会造成炉底烧穿。
λ锌(Zn):锌很容易气化,锌蒸汽容易进入砖缝,氧化成为ZnO后膨胀,破坏炉身上部耐火砖衬。
λ砷(As):砷对钢材来说也是有害元素之一,它使钢材产生冷脆性,使得钢材焊接性能变差。
铁矿石中砷基本还原进入生铁,影响生铁质量。
此外砷在烧结过程中挥发,对环境影响较大。
λ铜(Cu):铜会使钢材“热脆”,钢材不易轧制和焊接。
少量铜能改善钢的耐蚀性。
在高炉冶炼中,铜全部还原进入生铁中。
烧结矿中有害元素对高炉的危害和抑制

烧结矿中有害元素对高炉的危害和抑制
为适应当前严峻的钢铁形势,进一步降低铁水成本,各钢铁企业都采用低价的外矿粉进行烧结,并充分利用烧结、炼铁、炼钢工序所产生的各种除尘灰,利用其低价和含有大量的C、Fe、CaO、MgO等有利成分的优势,来降低烧结料消耗,从而达到降低成本的目的。
但由于各种外矿粉及除尘灰都含一定量的K、Na、Zn等有害元素,大量配加会造成高炉碱负荷、锌负荷超标,高炉炉墙结厚结瘤,加剧炉缸侵蚀,影响炉况稳定顺行。
防治K、Na、Zn元素侵蚀高炉炉缸炭砖的隔热夹层型炉缸内衬-.

2014年全国炼铁生产技术会议暨炼铁学术年会防治 K 、 Na 、 Zn 元素侵蚀高炉炉缸炭砖的隔热夹层型炉缸内衬徐瑞图张建来何汝生曹永国(北京瑞尔非金属材料有限公司北京 100086摘要:以气态形式存在于高炉炉缸中的 K 、 Na 、 Zn 元素,对炉缸炭砖有强烈的破坏作用,明显影响高炉寿命。
隔热夹层型炉缸内衬通过增加炭砖、陶瓷杯的界面热阻,使炉缸炭砖的热面温度远离 K 、 Na 、 Zn 的沸点温度,降低了炉缸炭砖的温差应力,抑制了 K 、 Na 、 Zn 元素对炭砖的接触和渗透破坏,降低了陶瓷杯的温差应力,延长了高炉炉缸炭砖、陶瓷杯的使用寿命。
关键词:高炉碱金属锌陶瓷杯炭砖侵蚀1. 前言原燃料带入高炉的 K 、 Na 和 Zn 有害于高炉冶炼过程,明显危害高炉内衬的使用寿命, 几乎所有的炼铁厂均根据自身情况确定了 K 、 Na 和 Zn 的入炉负荷标准。
高炉炼铁工艺设计规范明确提出入炉原料和燃料应控制有害杂质量,其中:K2O+Na2O 的控制值宜≤ 3.0kg/t、 Zn 的控制值宜≤ 0.15kg/t[1]。
然而,随着优质原燃料资源的逐渐减少、除尘灰泥的再处理入炉利用等,常见高炉冶炼生产中的实际 K 2O 、 Na 2O 和 Zn 负荷远超上述指标,有的高炉的碱金属、锌的实际负荷甚至成倍于上述指标。
毋容置疑,这种情况已经影响到我国高炉寿命实绩。
能够预计,高炉炼铁工艺不可避免地将面对越来越高的碱、锌负荷,它们对高炉寿命的影响将更加明显。
过去,对碱金属、锌对高炉内衬的影响研究、防治措施主要集中在影响机理、降低入炉量、炉渣排碱等方面,鲜见关于炉缸内衬结构形式对碱金属、 Zn 侵蚀炉缸炭砖影响的研究。
降低碱金属、锌化合物的入炉量能从源头上降低它们对炉缸炭砖的侵蚀,但在优质原燃料逐渐减少的资源压力下,始终将它们控制在前述指标下是困难的,碱金属、锌化合物的入炉量必然不断上升。
高炉冶炼生产中,可采用较低的炉渣碱度甚至酸性渣,较低的铁水温度、甚至较高的- 1 -生铁含 S 、加大渣量等操作手段通过炉渣排碱,减轻碱害。
[教育]有害元素对高炉的危害含量和有效预防措施
![[教育]有害元素对高炉的危害含量和有效预防措施](https://img.taocdn.com/s3/m/3a049b3bd0d233d4b04e6946.png)
莱芜高炉解剖研究:碱金属平衡计算
•入炉原料中碱金属分 布
•产物中碱金属分布
•莱钢3#120高炉碱负荷(碱负荷为M2O的入炉量)为:
• 与全国碱负荷平均在3~4kg/tFe相比,高出45%~60%,处于较高水平。
碱金属平衡小结
3)在石墨晶格上形成使碳的边界连接变弱的一种放电体,这是焦炭反应 性增加的另一个原因。综上所述,无论用哪一种方法增碱,焦炭增碱 后的结果都大致一样,即随着含碱量的增加,焦炭的反应性相应升高 ,焦炭的体积膨胀,强度明显降低,易粉化。
高炉碱金属对铁矿石冶金性能的影响
1. 1)碱金属能明显促进烧结矿的还原,对降低焦比有利。 2. 2)少量碱金属能够提高烧结矿的软熔温度,使得高炉软
氰化钾在622℃熔化,1625℃气化;氰化钠在562℃熔化, 1530℃气化。因此在风口区它们能以气态的形式存在,它 随煤气流向上运动,当温度降低后它们便转变为液态。所 以在炉身下部、炉腰、炉腹和炉缸碱金属氰化物完全可能 以液体的形式出现。
•碱化物在高炉里的行为,我们还应了解它们的相对稳定性。
•高炉中碱金属的循环富集
[教育]有害元素对高炉的危 害含量和有效预防措施
提纲
1. 有害元素在高炉中的影响 2. 碱金属在高炉中的分布-高炉解剖 3. 有害元素的来源-碱金属平衡计算 4. 排减措施
•1碱金属对高炉的危害主要表现
1)提前并加剧CO2对焦炭的气化反应,缩小了间接还原区,扩大了 直接还原区,进而引起焦比升高;降低焦炭的粒度和强度,从而降 低料柱特别是软熔带气窗的透气性,引起风口破损。
携带着碱蒸气,碱金属氰化物和碱金属碳酸盐的高炉煤气在 自下而上的运动过程中,所携带的上述碱化物会沉积在内衬 和炉料上,而来不及反应和沉积的碱金属则随煤气和炉尘从 炉顶排出,大部分未还原的碱金属硅酸盐随炉渣排出。
高炉炉缸烧穿原因及预防

高炉炉缸烧穿原因及预防一、国内外高炉炉缸烧穿原因各有不同,可以归纳为几个原因:1、炉缸冷却强度不够,与炭砖的导热能力和冶炼强度水平不匹配。
炉缸采用的炭砖导热系数与微孔结构要同时兼顾,冷却壁导热能力和冷却水量都要进一步提高,炭捣层的热导率应与炭病相近,避免其成为热阻层。
新建高炉的炉底结构,应采用微孔结构,抗铁水熔蚀性能好的炭砖,并做到从炭砖热面(与铁水接触面)至炉体水冷管,传热能力逐渐升高,不形成热阻层,使热量顺利传出去。
2、缺乏监测炉缸手段。
在新建高炉时为减少投资,炉缸温度监测点少,对冷却壁水温差、水流量、热流强度等参数检测手段少,不能及时发现炉缸的异常,导致烧穿事故突然发生。
3、炉缸耐材质量影响。
炭砖产品质量没达到要求,炭砖加入人工石墨过多,抗铁水熔蚀性能差。
造成这种现象的原因是追求炭病的高导热系数,但因为炉缸侧壁内存在高热阻的气隙,阻碍炭砖热量传递至冷却水中,反而使得炭砖表面温度升高,在铁水流冲刷和侵蚀下,造成事故。
4、冷却壁制造安装存在缺陷。
冷却壁若在安装、生产过程中开焊漏水,会造成炭砖加速氧化破损,易引发重大事故。
碳砖与冷却壁之间的炭素捣料应选择与碳砖的热导率相当的捣料,同时选择有足够冷却能力的冷却结构。
5、生产操作存在问题。
入炉钾、钠、铅、锌等有害元素对炉缸耐火材料的破坏。
高炉风口小套、冷却器漏水至炉缸,引起炭砖氧化、粉化。
有些钢铁厂为了抢占市场,不计后果的追求高炉冶炼强度,这对包括长寿系统在内的整个高炉及其附属系统都带来了极大负荷,对炉缸损害较大。
对于炉衬侵蚀严重的高炉,未进行钛矿护炉。
炉缸压浆不当,泥浆将砖衬压碎进入炉内,与铁水接触引发炉缸放炮,导致炉缸烧穿事故。
铁水深度不够,铁水从铁口通道进入砖缝,加速炭砖侵蚀。
高炉炉缸发生事故前会有先兆,应尽早发现炉缸危险的蛛丝马迹。
如果缺少监测手段、或者检测失灵,高炉炉缸烧穿事故突发。
对于监测系统完善的高炉,利用热电偶温度、热流强度信息可判断不同部位的侵蚀情况和残余砖衬厚度,预防炉缸烧穿。
有害元素对高炉操作的影响
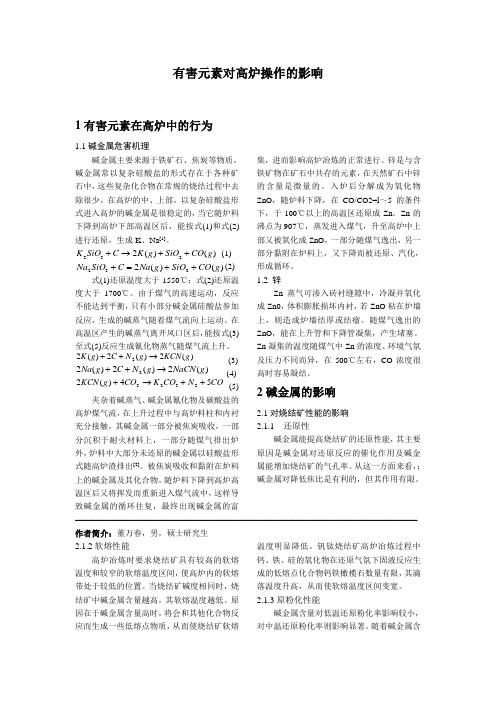
有害元素对高炉操作的影响1有害元素在高炉中的行为1.1碱金属危害机理碱金属主要来源于铁矿石、焦炭等物质,碱金属常以复杂硅酸盐的形式存在于各种矿石中,这些复杂化合物在常规的烧结过程中去除很少。
在高炉的中、上部,以复杂硅酸盐形式进入高炉的碱金属是很稳定的,当它随炉料下降到高炉下部高温区后,能按式(1)和式(2)进行还原,生成K 、Na [1]。
)()(2232g CO SiO g K C SiO K ++→+ (1))()(2232g CO SiO g Na C SiO Na ++=+(2)式(1)还原温度大于1550℃;式(2)还原温度大于1700℃。
由于煤气的高速运动,反应不能达到平衡,只有小部分碱金属硅酸盐参加反应,生成的碱蒸气随着煤气流向上运动。
在高温区产生的碱蒸气离开风口区后,能按式(3)至式(5)反应生成氰化物蒸气随煤气流上升。
)(2)(2)(22g KCN g N C g K →++ (3))(2)(2)(22g NaCN g N C g Na →++ (4) CON CO K COg KCN 54)(22322++→+ (5)夹杂着碱蒸气、碱金属氰化物及碳酸盐的高炉煤气流,在上升过程中与高炉料柱和内衬充分接触,其碱金属一部分被焦炭吸收,一部分沉积于耐火材料上,一部分随煤气排出炉外,炉料中大部分未还原的碱金属以硅酸盐形式随高炉渣排出[2]。
被焦炭吸收和黏附在炉料上的碱金属及其化合物,随炉料下降到高炉高温区后又将挥发而重新进入煤气流中,这样导致碱金属的循环往复,最终出现碱金属的富集,进而影响高炉冶炼的正常进行。
锌是与含铁矿物在矿石中共存的元素,在天然矿石中锌的含量是微量的。
入炉后分解成为氧化物ZnO ,随炉料下降,在CO/CO2=l ~5的条件下,于100℃以上的高温区还原成Zn 。
Zn 的沸点为907℃,蒸发进入煤气,升至高炉中上部又被氧化成ZnO ,一部分随煤气逸出,另一部分黏附在炉料上,又下降而被还原、汽化,形成循环。
烧结矿中有害元素对高炉的危害和抑制(新编版)

( 安全技术 )单位:_________________________姓名:_________________________日期:_________________________精品文档 / Word文档 / 文字可改烧结矿中有害元素对高炉的危害和抑制(新编版)Technical safety means that the pursuit of technology should also include ensuring that peoplemake mistakes烧结矿中有害元素对高炉的危害和抑制(新编版)为适应当前严峻的钢铁形势,进一步降低铁水成本,各钢铁企业都采用低价的外矿粉进行烧结,并充分利用烧结、炼铁、炼钢工序所产生的各种除尘灰,利用其低价和含有大量的C、Fe、CaO、MgO 等有利成分的优势,来降低烧结料消耗,从而达到降低成本的目的。
但由于各种外矿粉及除尘灰都含一定量的K、Na、Zn等有害元素,大量配加会造成高炉碱负荷、锌负荷超标,高炉炉墙结厚结瘤,加剧炉缸侵蚀,影响炉况稳定顺行。
1.烧结矿中有害元素的来源烧结所有外矿粉有害元素含量如下表所示:表1烧结外矿粉有害元素含量(%)试样名称ZnNaNa2OKK2O信昂澳粉0.015 0.047 0.064 0.022 0.027 雄鹰澳粉0.025 0.1190.14 0.076 0.092 巴姆澳粉0.0055 0.156 0.21 0.035 0.042 繁荣巴粗0.0091 0.031 0.042 0.216 0.26博斯巴粗0.140.0130.0180.070.085在高炉生产中,钾、钠、锌存在两个循环,第一个循环是高炉内部的小循环,第二个循环是烧结—高炉的大循环。
通过上表可看出,原料中的钾、钠、锌的量是相对稳定但不可控,要控制其富集减少对高炉的危害就是要打破第二个循环,减少高炉布袋灰、烧结机头灰等高碱、高锌灰的循环使用。
- 1、下载文档前请自行甄别文档内容的完整性,平台不提供额外的编辑、内容补充、找答案等附加服务。
- 2、"仅部分预览"的文档,不可在线预览部分如存在完整性等问题,可反馈申请退款(可完整预览的文档不适用该条件!)。
- 3、如文档侵犯您的权益,请联系客服反馈,我们会尽快为您处理(人工客服工作时间:9:00-18:30)。
炉缸侧壁 碳 砖 环 裂 已 经 被 国 内 外 研究 者 所 公 [7 ] 认, 对其形成机理 有 一 些 不 同 的 理 论 . 日 本 新 日 铁研究者池田順一 等 就 新 日 铁 Muroran 3 高 炉 的解体研究发现, 炉缸上部中间部位有约 100 mm 的 脆化层, 其给出的原因是碳砖气孔在 1 μm 以上易发 [11 ] 生渗铁, 从而使碳砖 发 生 脆 化. 黄 晓 煜 等 对 鞍 钢 高炉炉缸破损状况 进 行 了 详 细的 调查, 认为脆化层 是铁水与碳砖接触 处 的 侵蚀机理, 脆 化 层并不 是 产 生环裂的主要原因, 也 不 符 合 我国 综 合炉 底 破 损 的 [4 ] 实际情况. 张寿荣等 认为铁水的渗 透 是引起 高 炉 炉缸炉底破坏的主要原因. 降 低碳 砖 的 气 孔 率 是 最 好的解决办法. 综合炉缸侧壁 的 环 状裂 缝 是由 于碳 砖和 高铝 砖热 膨胀 不 同 而 造成 的. 碱 金 属 和 Zn、 ZnO 一起产生的侵蚀作用是高炉炉衬特别是 炉 身 内 衬破损的主要 原 因. 除 改 善 耐火材料质 量外, 还必 须设计一种较好的冷 却 方 式, 以保持炉衬热端的温 12] 度低于碱金属起侵蚀 作 用的 温度. 文献[ 表 明, 碱金属在碳砖侵蚀中 起 重 要 作 用, 其 碱 金 属在 碳 砖 表面的侵蚀机理为 K2 O( s) + 3C ( s) + N2 ( q) = 2KCN( q) + CO( q) ( 1) 通 过大 量 的 炉 底 炉缸 的 调查, 发现渗入碳砖气 孔的 碱 蒸 气 , 大大加速碳砖中 碳 素 熔 损. 同 时 认 为, 1 000 ℃ 左右 碳 砖 的 在碳砖表面碱金属的气化 侵蚀, 中间部位反应( 1 ) 最 激 烈, 从而使 碳 砖 的 密 度变 差, 强度降低, 更容易 破 坏. 从而 得 出 了 碳 砖 另一种 侵 — —渗铁侵蚀. 在高于 1 150 ℃ 时, 蚀机理— 砖中 碳 素 颗粒与渗入砖中的铁水进行渗碳过程, 使碳砖渗铁. 在低于 1 150 ℃ 时, 渗入砖中的铁水凝固并析出片状 石墨沉积, 其体积膨胀对砖起着碎裂破坏作用.
本文 研究 共 取 四类 有 代 表性的 五 个 试样: ① 第
表1 Table 1 位置 1 2 3 4 C 57. 23 83. 65 70. 37 4. 55 O 10. 58 6. 92 15. 61 35. 82 Na 1. 33 0. 43 0. 59 — 第一层碳砖上凝结物能谱分析结果( 质量分数) % Ca — — — 2. 71 Fe 21. 89 2. 16 — 46. 77 Zn — — 0. 46 —
第4 期
祁成林等: 有害元素对高炉炉缸侧壁碳砖的侵蚀
表2 Table 2 图 2 中各点能谱分析结果( 质量分数) EDS analysis results of three points in Fig. 2 Al — 0. 18 0. 19 Si 0. 52 0. 83 0. 88 S — 0. 16 0. 30 Cl 0. 22 — — K 1. 86 1. 28 3. 05 Ca 0. 26 — —
-10 [8 ]
图1 Fig. 1
第一层碳砖上凝结物全形貌
SEM image of coagulation on in the first layer carbon bricks
2
炉缸侧壁碳砖环裂微观分析
Fig. 2
图2
图 1 中点 1 的形貌
SEM image of Point 1 in Fig. 1
1 ) School of Metallurgical and Ecological Engineering,University of Science and Technology Beijing,Beijing 100083 ,China 2 ) Hunan Valin Xiangtan Iron and Steel Co. Ltd. ,Xiangtan 411100 ,China 3 ) Nanchang Changli Iron and Steel Co. Ltd. ,Nanchang 330001 ,China mail: qichenglin_ustb@ yahoo. cn Corresponding author,E-
元素对高炉炉缸侧壁碳砖的侵蚀以及粉化断裂机理. 结果表明, 高炉炉缸不同部位的碳砖侵蚀机理不 同. 第 一 层 以 有 害 元 素 在碳素熔损反应中的催化作用及生成白榴石为主; 上部碳砖侵蚀 以 K 渗 透 到 砖 缝 中, 改 变砖质为 主; 风 口 以 Zn 侵蚀为 主; 铁 口 K 含量较多, 另有 Pb 富集. 同种有害元素在不同部位侵蚀碳砖的机理有所不同. K 元素在最上部以催 化 作 用 为 主, 在下部 以渗透到碳砖内部使碳砖改性为主; Zn 在风口碳砖有明显的结晶, 在炉缸炉底上部含有大量的 Zn 并没有结晶, 而是附着在砖 表面上部. 关键词 分类号 高炉; 炉缸; 碱金属; 侵蚀 TF 573. 1
EDS analysis results of coagulation on the first layer carbon bricks Mg — — — 0. 58 Al 0. 41 1. 24 2. 61 3. 91 Si 1. 48 2. 49 5. 37 5. 25 S 1. 22 — 0. 42 — K 5. 86 2. 65 5. 04 0. 41
Erosion of carbon bricks at the hearth sidewall by harmful elements in a blast furnace
QI Chenglin1)
,ZHANG Jianliang1) ,LIN Chongchun1) ,YIN Jian2) ,CHANG Jian3) ,LU Weijia1)
第 33 卷 第 4 期 2011 年 4 月
北
京
科
技
大
学
学
报
Vol. 33 No. 4 Apr. 2011
Journal of University of Science and Technology Beijing
有 害 元素对高 炉炉 缸侧壁 碳 砖 的 侵 蚀
祁成林
1)
张建良
1)
林重春
1)
高炉炉缸侵蚀是影响高 炉 寿命 的 主要因 素. 炉 缸侧壁碳砖环裂是炉缸侵蚀的最主要原因之 -2 [1 ] . 新投产大型高 炉炉缸侧壁烧 穿事 故 屡 有发 一 生, 随着高炉冶炼 不 断 强 化 和 高 炉 用 料 有 害 元 素 的 -6 [3 ] . 逐渐增加, 对于高炉炉缸侧壁侵蚀 有 了 再 认 识
ABSTRACT
Seven samples of a blast furnace at representative positions were analyzed by scanning electron microscopy ( SEM) , en-
ergy dispersive spectrometry ( EDS) ,Xray diffraction ( XRD) and atomic absorption spectrometry to study the erosion of carbon bricks at the BF hearth sidewall by harmful elements and the mechanism of pulverizing fracture. The results show that the erosion mechanism of carbon bricks at different parts of the hearth is different. In the first layer the erosion is mainly caused by the catalytic effects of harmful elements in the carbon loss reaction and the generation of leucite; in the upper area,penetration of K into brick work joints leading to a quality change of carbon bricks plays the leading role; in the tuyere, Zn is the main cause of erosion; but in the taphole the content of K is larger,with enrichment of Pb. It is also found that a harmful element has different effects at different parts of the hearth. In the upper area, the erosion mechanism is mainly the catalytic effect of K in the erosion reaction, but in lower part is the penetration of K into carbon bricks leading to a quality change of carbon bricks; Zn significantly crystallizes on carbon bricks in the tuyere, however in the hearth bottom Zn attaches to carbon bricks without obvious crystallization. KEY WORDS blast furnaces; hearths; alkali metals; erosion
· 492·