高炉中有害元素的平衡分析及其脱除
炼铁原理剖析高炉内铁水中杂质的生成和去除机制
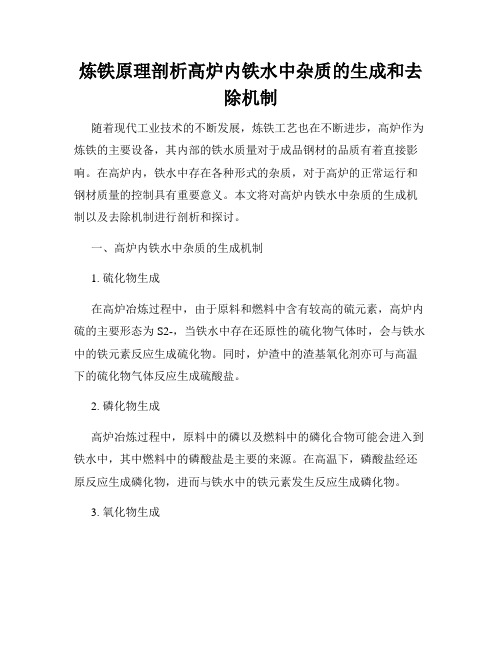
炼铁原理剖析高炉内铁水中杂质的生成和去除机制随着现代工业技术的不断发展,炼铁工艺也在不断进步,高炉作为炼铁的主要设备,其内部的铁水质量对于成品钢材的品质有着直接影响。
在高炉内,铁水中存在各种形式的杂质,对于高炉的正常运行和钢材质量的控制具有重要意义。
本文将对高炉内铁水中杂质的生成机制以及去除机制进行剖析和探讨。
一、高炉内铁水中杂质的生成机制1. 硫化物生成在高炉冶炼过程中,由于原料和燃料中含有较高的硫元素,高炉内硫的主要形态为S2-,当铁水中存在还原性的硫化物气体时,会与铁水中的铁元素反应生成硫化物。
同时,炉渣中的渣基氧化剂亦可与高温下的硫化物气体反应生成硫酸盐。
2. 磷化物生成高炉冶炼过程中,原料中的磷以及燃料中的磷化合物可能会进入到铁水中,其中燃料中的磷酸盐是主要的来源。
在高温下,磷酸盐经还原反应生成磷化物,进而与铁水中的铁元素发生反应生成磷化物。
3. 氧化物生成高炉内的氧气和含氧化物的原料在高温下会与铁水中的铁元素反应生成氧化物。
氧化物中常见的有氧化铁、二氧化硅等,它们的生成会对铁水的质量产生一定的影响。
4. 氨气生成高炉内铁水中的氨气主要来自于焦炭燃烧过程中的氨基化合物。
在高温下,氨基化合物释放出氨气,进而通过反应生成铁水中的氨气。
二、高炉内铁水中杂质的去除机制1. 物理去除对于某些密度较大的杂质,可以采用物理方法进行去除。
例如,采用沉淀、过滤等方式将密度较大的杂质从铁水中分离出来,提高铁水的纯度。
2. 矿物质添加剂在高炉冶炼过程中,可以添加一些矿物质来吸附和脱除铁水中的杂质。
例如,通过添加含氧化钠、氧化镁等矿物质来吸附和捕捉铁水中的氧化物、硫化物等杂质。
3. 化学反应去除通过化学反应使铁水中的杂质发生转化,然后以其他形式被捕获和去除。
例如,通过向铁水中加入一定量的石灰或石灰石,使铁水中的硫酸盐反应生成硫化钙沉淀,从而将硫酸盐去除。
4. 渣化作用高炉内的炉渣可以起到吸附和分离杂质的作用。
高炉有害元素调查分析

高炉有害元素调查分析摘要:鉴于1#高炉(580m3)高炉生产出现放铁期间白烟大、铁水物理热严重不足、炉况不顺、悬料、结瘤等问题,调研了高炉有害金属的分布情况。
通过现场取样,测定试样中有害金属含量,计算分析了高炉有害金属的分布与平衡。
结果表明:烧结矿及球团矿中有害金属含量是影响高炉有害金属负荷的主要因素,排有害金属主要由高炉渣、除尘灰完成。
结合实际生产情况,提出了防治高炉有害金属的途径。
关键词:有害金属;分布;有害金属负荷;平衡由于受到铁矿石资源的限制,加上矿源复杂,新疆金特钢铁公司炼铁高炉原燃料中有害金属含量较高。
在不断寻求新资源的过程中,忽略了对有害金属元素的控制,使得有害金属对高炉冶炼的危害逐渐暴露出来。
Zn、Pb、Na2O等元素入炉以后一方面破坏原燃料的冶炼性能,影响高炉技术经济指标的提升,高炉出现悬料、结瘤、炉况不顺、消耗升高,其危害随着生产进行而日益严重。
另一方面则对高炉砖衬进行侵蚀,给高炉长寿和组织安全稳定经济生产造成极大危害。
因此非常有必要对高炉Zn、Pb、Na2O等有害元素的入炉及排出情况进行长期监控,以便为高炉长寿、正常生产组织提供参考。
在本文中“碱负荷”是指每吨铁由炉料带入高炉的碱金属总量;“碱平衡”是指高炉冶炼过程中碱金属的收支明细表,反应了高炉在冶炼过程中碱金属的去留情况。
锌危害:(1)影响铁矿石和焦炭的冶金性能。
渗入铁矿石和焦炭孔隙中的锌蒸气沉积氧化成氧化锌后,一方面由于体积的膨胀会增加铁矿石和焦炭的热应力,破坏铁矿石和焦炭的热态强度,并导致烧结矿和球团矿的低温还原粉化指数有所提高,焦炭的反应性增加,反应后强度降低;另一方面,锌蒸气也会堵塞铁矿石和焦炭的孔隙,恶化高炉料柱的透气性,给高炉冶炼带来不利的影响。
(2)影响高炉的操作。
锌蒸气在上升过程中被氧化,氧化锌会冷凝黏结在上升管、下降管、炉喉及炉身上部砖衬上或大钟内表面,并形成高锌尘垢,并逐渐转变为高锌炉瘤。
炉喉及炉身上部砖衬上的锌瘤破坏炉料的下降和煤气流的上升,破坏炉料和煤气的正常分布,导致炉况失常。
衡钢1号高炉锌平衡研究及减轻锌负荷的措施

衡钢1号高炉锌平衡研究及减轻锌负荷的措施收藏本文分享锌在高炉炼铁过程中是一种微量的有害元素,不仅影响高炉的冶炼,对高炉长寿也至关重要。
衡钢1号高炉自2009年5月开炉以来,生产顺行稳定,但一直未对锌负荷作仔细研究。
为了详细了解衡钢高炉锌的分布情况,避免过重的锌负荷对高炉操作及生产带来不利影响,有必要对锌负荷和锌平衡进行分析,弄清锌的来源、去向,同时也为布袋灰、瓦斯灰等的再回收利用提供有效数据。
1锌对高炉的影响锌是与铁矿石共存的一种元素,它在铁矿石中常以闪锌矿(ZnS)的形式存在,有时也以碳酸盐或硅酸盐状态存在。
在天然铁矿中锌的质量分数是微量的,但由于其还原温度低、液态锌的沸点低,几乎不能被渣铁吸收。
锌对高炉的影响主要体现在以下2方面。
1)对高炉冶炼的影响。
锌在高炉炉内的循环会使热量发生转移,热量从高温区转移到了低温区,导致渣铁温度降低,渣的黏度升高,从而不利于高炉顺行和脱硫;另外,锌蒸气在高炉中上部冷凝后,黏附在炉墙和炉料上,易形成炉瘤,堵塞炉料气孔,恶化料柱透气性;除此以外,锌蒸气还会在料块表面冷凝,形成锌的金属或氧化物的薄膜,会弱化焦炭和矿石的冶金性能,降低料块的强度和还原性。
锌负荷的升高,还会引起焦比的上升。
还原1 kg锌需11 (本文共计3页)......[继续阅读本文]高炉内锌平衡与结瘤的分析锌是高炉有害元素之一,其在高炉内的循环富集会对高炉生产带来极大的危害,富集过剩严重影响高炉的热制度、煤气流的分布、高炉消耗等,在一定条件下还会造成炉内结瘤,严重影响正常生产。
为明确湘钢高炉的高炉内锌负荷及其平衡状况对内部结瘤的影响,本文通过现场取样检测,并计算分析了湘钢3、4号高炉的锌负荷和锌平衡状况,同时对结瘤瘤体进行了取样分析。
一、试验方法与数据采集分别对湘钢3BF、4BF原燃料进行取样,每座高炉取6组样,第1天取入炉的原、燃料样,包括烧结矿、球团矿、澳矿(3BF)、南非矿(4BF)、焦炭和煤粉,第2天取对应的高炉产物试样,包括铁水、高炉渣、瓦斯灰和除尘灰等。
高炉铁水有害元素分析与控制
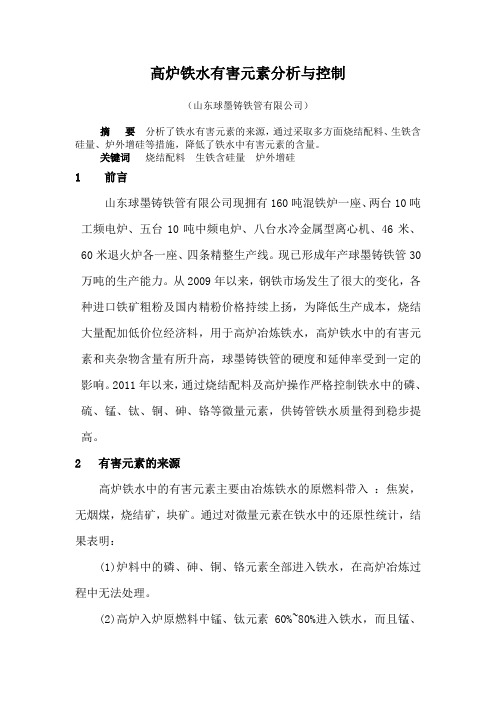
高炉铁水有害元素分析与控制(山东球墨铸铁管有限公司)摘要分析了铁水有害元素的来源,通过采取多方面烧结配料、生铁含硅量、炉外增硅等措施,降低了铁水中有害元素的含量。
关键词烧结配料生铁含硅量炉外增硅1 前言山东球墨铸铁管有限公司现拥有160吨混铁炉一座、两台10吨工频电炉、五台10吨中频电炉、八台水冷金属型离心机、46米、60米退火炉各一座、四条精整生产线。
现已形成年产球墨铸铁管30万吨的生产能力。
从2009年以来,钢铁市场发生了很大的变化,各种进口铁矿粗粉及国内精粉价格持续上扬,为降低生产成本,烧结大量配加低价位经济料,用于高炉冶炼铁水,高炉铁水中的有害元素和夹杂物含量有所升高,球墨铸铁管的硬度和延伸率受到一定的影响。
2011年以来,通过烧结配料及高炉操作严格控制铁水中的磷、硫、锰、钛、铜、砷、铬等微量元素,供铸管铁水质量得到稳步提高。
2 有害元素的来源高炉铁水中的有害元素主要由冶炼铁水的原燃料带入:焦炭,无烟煤,烧结矿,块矿。
通过对微量元素在铁水中的还原性统计,结果表明:(1)炉料中的磷、砷、铜、铬元素全部进入铁水,在高炉冶炼过程中无法处理。
(2)高炉入炉原燃料中锰、钛元素60%~80%进入铁水,而且锰、钛元素在铁水中含量与高炉铁水含硅量呈正相关性关系。
原始生铁含硅量的提高有助于有害元素含量的升高。
3 不同元素对铸铁管的危害供铸管铁水中一些元素达到一定值会对铸铁管的退火产生一定的影响,进而降低对铸铁管的产品质量:磷是铸铁中的常存元素,它对球墨铸铁的机械性能,尤其是冲击韧性和塑性有明显的不良影响,因此总是作为有害元素对待。
其主要原因是共晶团晶界产生的磷共晶脆相,磷共晶呈多角状分布于共晶团边界,急剧恶化球墨铸铁的力学性能,使球墨铸铁韧性下降;其次是磷阻碍珠光体的分解,又能固溶于铁素体中,这些都能降低韧性。
磷的质量分数每增加0.01%时,脆性转变温度升高4.0~4.5℃。
当磷的质量分数超过0.16%时,脆性转变温度已在室温以上,冲击断口出现脆性断裂。
有害元素对高炉冶炼的影响

立志当早,存高远有害元素对高炉冶炼的影响有害元素通常指硫(S)、磷(P)、钾(K)、钠(Na)、铅(Pb)、Zn(锌)、As(砷)、Cu。
通常高炉冶炼对铁矿石要求如下:Pb 小于0.1%、Zn 小于0.1%、As 小于0.07%、Cu 小于0.2%、K2O+Na2O≤0.25%。
硫(S):硫对钢材是最为有害的成份,它使钢材产生热脆性。
铁矿石中硫含量高,高炉脱硫成本增大,所以入炉铁矿石含硫愈少愈好。
磷(P):磷对钢材来说也是常见有害元素之一,它使钢材产生冷脆性。
铁矿石中的磷,在高炉冶炼时100%进入生铁,烧结也不能脱磷,控制生铁含磷量主要是靠控制铁矿石含磷量。
脱磷只能通过炼钢来进行,增加了炼钢的脱磷成本。
因此,铁矿石含磷越低越好。
碱金属:碱金属主要有钾和钠。
钾、钠对高炉的影响不是正比例性质,高炉本身有一定的排碱能力,碱金属在控制范围内对高炉影响不大。
但是入炉铁矿石碱金属含量太多,超过高炉排碱能力,就会形成碱金属富集,导致高炉中上部炉料碱金属含量大大超过入炉料原始水平。
铁矿石含有较多的碱金属极易造成软化温度降低,软熔带上移,不利于发展间接还原,造成焦比升高。
球团含有碱金属会造成球团异常膨胀引起严重粉化,恶化料柱透气性。
碱金属对焦炭性能破坏也很严重。
另外,高炉中上部碱金属化合物黏附在炉墙上,促使炉墙结厚、结瘤并破坏砖衬。
因此,铁矿石含碱金属越低越好。
铅(Pb):铅在高炉中几乎全部被还原,由于密度高达11.34t∕m³,故沉于死铁层之下,易破坏炉底砖缝,有可能会造成炉底烧穿。
锌(Zn):锌很容易气化,锌蒸汽容易进入砖缝,氧化成为ZnO 后膨胀,破坏炉身上部耐火砖衬。
有害元素对高炉操作的影响
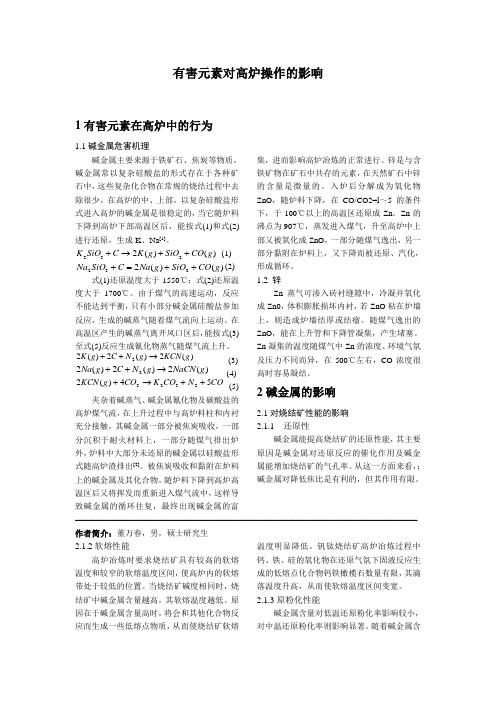
有害元素对高炉操作的影响1有害元素在高炉中的行为1.1碱金属危害机理碱金属主要来源于铁矿石、焦炭等物质,碱金属常以复杂硅酸盐的形式存在于各种矿石中,这些复杂化合物在常规的烧结过程中去除很少。
在高炉的中、上部,以复杂硅酸盐形式进入高炉的碱金属是很稳定的,当它随炉料下降到高炉下部高温区后,能按式(1)和式(2)进行还原,生成K 、Na [1]。
)()(2232g CO SiO g K C SiO K ++→+ (1))()(2232g CO SiO g Na C SiO Na ++=+(2)式(1)还原温度大于1550℃;式(2)还原温度大于1700℃。
由于煤气的高速运动,反应不能达到平衡,只有小部分碱金属硅酸盐参加反应,生成的碱蒸气随着煤气流向上运动。
在高温区产生的碱蒸气离开风口区后,能按式(3)至式(5)反应生成氰化物蒸气随煤气流上升。
)(2)(2)(22g KCN g N C g K →++ (3))(2)(2)(22g NaCN g N C g Na →++ (4) CON CO K COg KCN 54)(22322++→+ (5)夹杂着碱蒸气、碱金属氰化物及碳酸盐的高炉煤气流,在上升过程中与高炉料柱和内衬充分接触,其碱金属一部分被焦炭吸收,一部分沉积于耐火材料上,一部分随煤气排出炉外,炉料中大部分未还原的碱金属以硅酸盐形式随高炉渣排出[2]。
被焦炭吸收和黏附在炉料上的碱金属及其化合物,随炉料下降到高炉高温区后又将挥发而重新进入煤气流中,这样导致碱金属的循环往复,最终出现碱金属的富集,进而影响高炉冶炼的正常进行。
锌是与含铁矿物在矿石中共存的元素,在天然矿石中锌的含量是微量的。
入炉后分解成为氧化物ZnO ,随炉料下降,在CO/CO2=l ~5的条件下,于100℃以上的高温区还原成Zn 。
Zn 的沸点为907℃,蒸发进入煤气,升至高炉中上部又被氧化成ZnO ,一部分随煤气逸出,另一部分黏附在炉料上,又下降而被还原、汽化,形成循环。
炼铁高炉入炉原料中有害微量元素分析解决方案工作报告
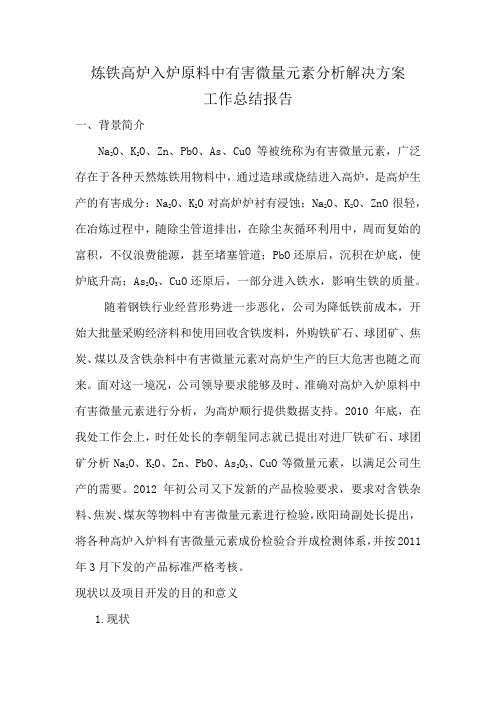
炼铁高炉入炉原料中有害微量元素分析解决方案工作总结报告一、背景简介Na2O、K2O、Zn、PbO、As、CuO等被统称为有害微量元素,广泛存在于各种天然炼铁用物料中,通过造球或烧结进入高炉,是高炉生产的有害成分:Na2O、K2O对高炉炉衬有浸蚀;Na2O、K2O、ZnO很轻,在冶炼过程中,随除尘管道排出,在除尘灰循环利用中,周而复始的富积,不仅浪费能源,甚至堵塞管道;PbO还原后,沉积在炉底,使炉底升高;As2O3、CuO还原后,一部分进入铁水,影响生铁的质量。
随着钢铁行业经营形势进一步恶化,公司为降低铁前成本,开始大批量采购经济料和使用回收含铁废料,外购铁矿石、球团矿、焦炭、煤以及含铁杂料中有害微量元素对高炉生产的巨大危害也随之而来。
面对这一境况,公司领导要求能够及时、准确对高炉入炉原料中有害微量元素进行分析,为高炉顺行提供数据支持。
2010年底,在我处工作会上,时任处长的李朝玺同志就已提出对进厂铁矿石、球团矿分析Na2O、K2O、Zn、PbO、As2O3、CuO等微量元素,以满足公司生产的需要。
2012年初公司又下发新的产品检验要求,要求对含铁杂料、焦炭、煤灰等物料中有害微量元素进行检验,欧阳琦副处长提出,将各种高炉入炉料有害微量元素成份检验合并成检测体系,并按2011年3月下发的产品标准严格考核。
现状以及项目开发的目的和意义1.现状(1)Na2O、K2O、Zn、PbO、As、CuO等检验项目在各种物料中的含量都很微少,想要准确测定微量或痕量的元素,一般都采用ICP分析或原子吸收分析方法。
这两种方法首先都需对待分析样品进行溶解,溶解的过程比较漫长,分析过程稍有差池就会造成分析失败,检验周期长、操作复杂也是这两种方法不可避免的缺点,对于大批量的进厂铁矿石、球团矿、焦炭、煤灰、含铁废料检验,已很难适应快速生产节奏的需要。
(2)X荧光仪分析速度快、对样品要求相对简单,在2011年已成功开发出铁矿石、球团矿微量元素快速分析方法,但该方法只适用于物质成份含量简单且相对稳定的铁矿石品种,焦炭、煤灰、含铁杂料等新品种因物相组成不同、成份结构复杂,不能简单用一种方法分析检验,需要一整套的系列分析解决方案,有针对性的对各种物料使用最为合适的分析方法。
高炉有害元素分析及控制

高炉有害元素分析及控制摘要:由于成矿原因和炼铁原料来源复杂,炼铁原料中含有锌杂质,因锌有害于高炉炼铁,要求入炉原料中锌含量应分别小于0.15 kg/t,而我国很多钢厂入炉原料中锌含量高于此标准。
近年来,国内钢铁产能过剩,钢铁价格持续低迷,钢企为节省成本少用国外铁矿石,多用周边品质差、价格低廉的国产矿石替代,使得有些高炉锌危害更加突出。
基于此,本文主要分析高炉内锌的主要来源以及对高炉的危害,提出了控制有害元素的措施和建议。
关键词:高炉炼铁;有害元素;锌元素;分析控制1锌在高炉中的行为机理1.1高炉内的循环铁矿石中的锌少量主要以铁酸盐(ZnO•Fe2O3)硅酸盐(2ZnO•SiO2)及硫化物(ZnS)的形式存在。
其锌硫化物先转化为复杂的氧化物,然后再在大于1000℃的高温区被CO还原为气态。
沸点为907℃时,加热为蒸汽,随煤气上升,到达温度较低的区域(580℃)时冷凝而再氧化。
再氧化形成的锌氧化细粒附着于上升煤气的粉尘时就被带出炉外,附着于下降的炉料时就再次进入高温区。
如此周而复始,就形成了在高炉内的富集现象。
1.2高炉内部的富集含矿物进入高炉后生成,固态ZnO,随炉料下降过程中被C、CO和Fe还原。
在高炉下部1000℃以上的高温区,ZnO还原出来的Zn全部被汽化为蒸汽分散于煤气中并随之上升,蒸汽到达高炉上部低温区时冷凝而再被氧化形成ZnO细粒,一部分随煤气从炉顶逸出炉外,一部分附着于下降的炉料再次进入高温区重新被还原和汽化,周而复始,形成了在高炉内的锌循环富集现象。
在高炉内的循环富集量可达到入炉料含量的10~30倍。
1.3在烧结、高炉系统间的循环富含锌元素的高炉煤气除尘灰被回收,用于烧结配料,含锌的烧结作为炼铁主原料重新进入高炉,形成了锌在烧结、高炉系统间的循环。
2锌对高炉危害2.1锌对高炉耐材及风口的破坏Zn被还原后,在>907℃时成为锌蒸汽,进入煤气中,渗入高炉上部耐材的缝隙,氧化后使其体积膨胀,破坏高炉上部的炉墙结构,严重时甚至可以导致炉壳胀裂,使煤气泄漏,造成一系列恶性事故。
- 1、下载文档前请自行甄别文档内容的完整性,平台不提供额外的编辑、内容补充、找答案等附加服务。
- 2、"仅部分预览"的文档,不可在线预览部分如存在完整性等问题,可反馈申请退款(可完整预览的文档不适用该条件!)。
- 3、如文档侵犯您的权益,请联系客服反馈,我们会尽快为您处理(人工客服工作时间:9:00-18:30)。
1 750 m3 高炉 w ( K2O) / % w (Na2O) / % 物料数量/ ( kg ·t - 1) w ( K2O) / ( kg ·t - 1) w ( Na2O) / ( kg ·t - 1) 碱金属/ ( kg ·t - 1)
表 1 1 750 m3 高炉碱金属投入产出计算 Table 1 Input and output calculating of alkali metals in 1 750 m3 BF
后即气化上升 ,在不同的温度条件下又与其它物 质反应转化为氰化物 、氟化物或硅酸盐等 。当其 随炉料下降到不同温度时又被重新还原 ,从而进 行循环和富集 。 碱金属在炉内的危害表现为 : ①降低了矿石的 软化温度 ,使矿石尚未充分还原就已熔化滴落 ,增加 了高炉下部的直接还原热量消耗 ; ②引起了球团矿 的异常膨胀而严重粉化 ; ③强化了焦炭的气化反应 , 使其反应后强度急剧降低且粉化 ; ④严重恶化了料 柱透气性 ,危及生产冶炼过程的进行 ; ⑤液态或固态 碱金属粘附于炉衬上 ,既导致炉墙严重结瘤 ,又能直 接破坏砖衬 。 1. 2 铅的行为与危害 铅在炉料中主要以 PbSO4 、PbS 等形态存在 ,在 高炉中很易被碳 、铁和一氧化碳还原 。由于金属铅 质量密度 (111 34 g/ cm3 ) 比铁水 (7. 87 g/ cm3 ) 的大 得多 ,而熔点 (327 ℃) 却低 ,因此 ,铅大部分沉积在 炉底砖衬缝隙中而破坏炉底 。铅的沸点为 1 540 ℃, 在高温区部分气化进入煤气中 ,上升到低温区时又 被氧化为氧化铅再随炉料下降 ,因而在高炉中形成
(1. 济南钢铁集团总公司技术中心 ,山东 济南 250101 ;2. 济南钢铁集团总公司国贸公司 ,山东 济南 250101)
摘 要 :通过对钾 、钠 、铅 、锌等高炉中微量有害元素进行投入支出平衡计算 ,分析研究了高炉各种投入产出物中 有害元素所占比例 ,探讨了减少高炉内有害元素富集的方法和措施 ,以降低其对高炉稳定顺行的危害程度 。 关键词 :高炉 ;有害元素 ;平衡 ;富集 中图分类号 : TF5 文献标识码 :A 文章编号 :100629356 (2007) 1120035206
Abstract :Based o n t he balance calculation of inp ut and o utp ut fo r microelement imp urities such as kalium , sodium , plumbum and zinc in B F , t he ratio of t he volume of harmf ul element s in inp ut and outp ut of t he B F was st udied , and t he met hod and measure to reduce t he volume of harmf ul element s accumulatio n in B F were discussed , resul2 ting in reduce t he harm to stability of B F. Key words :B F ; harmf ul element s ;balance ;accumulation
0. 001 0 0. 502 5 0. 102 0 0. 130 0
880
566
162
408
149
1 000
270
24
10
0. 387 0. 318 0. 028 0. 257 0. 077 1. 068 0. 090 1. 341 0. 042 0. 019 1. 492
0. 800 80 0. 469 78 0. 093 96 0. 359 04 0. 146 02 1. 870 00 0. 005 00 1. 357 00 0. 024 00 0. 013 00 1. 399 00
2 有害元素平衡计算与分析
多次对 1 750 m3 、350 m3 高炉的投入产出物进 行了取样化验 。高炉用原燃料 (烧结矿 、球团矿 、块
矿 、焦炭) 在槽下振动筛下料口取样 ,喷吹煤粉从取 样点取样 ,除尘灰从各自卸灰阀下取样 ,污泥从污泥 脱水机室脱水机皮带上取样 ,生铁和炉渣分别从炉 前铁渣沟中取样 。测定期间 ,根据高炉月报表所提 供的数据计算生铁产量 、炉渣量以及各种原燃料用 量 。除尘灰量采用原料厂月除尘灰进厂量的平均 值 ,污泥量采用动力厂每月污泥产出量的平均值 。 2. 1 试样的碱金属量及平衡计算 350 m3 、1 750 m3 高炉碱金属投入产出计算分 别见表 1 和表 2 ,投入产出分布见图 1 和图 2 。1 750 m3 高炉 碱 金 属 负 荷 2. 937 kg/ t , 其 绝 对 误 差 = 21 937 - 2. 891 = - 0. 046 kg/ t ,相对误差 = 0. 046/ 2. 937 = 1. 566 % ; 350 m3 高炉 碱金 属负荷 2. 615 kg/ t ,其绝对误差 = 2. 615 - 2. 748 = - 0. 133 kg/ t , 相对误差 = 0. 133/ 2. 615 = 5. 086 %。
0. 573 0. 489 0. 011 0. 359 0. 114 1. 545 0. 005 1. 374
0. 963 0. 820 0. 036 0. 621 0. 175 2. 615 0. 075 2. 516
(36. 81) (31. 36) (1. 38) (23. 76) (6. 68) (100) (2. 73) (91. 57)
1 有害元素在高炉中的行为与危害
1. 1 碱金属的行为与危害 碱 金 属 矿 物 一 般 以 铝 硅 酸 盐 和 硅 酸 盐 形 态 存 在 ,熔点较低 ,在 800~1 100 ℃即溶化 ,到高温区 时部分进 入 炉 渣 、部 分 被 碳 还 原 成 钾 和 钠 元 素 。 钾和钠的沸点只有 799 ℃和 882 ℃,故还原出来
注 :括号内数值为百分数 。
350 m3 高炉 w ( K2O) / % w (Na2O) / % 物料数量/ ( kg ·t - 1) w ( K2O) / ( kg ·t - 1) w ( Na2O) / ( kg ·t - 1) 合计/ ( kg ·t - 1)
表 2 350 m3 高炉碱金属投入产出计算 Table 2 Input and output calculating of alkali metals in 350 m3 BF
作者简介 :杨金福 (19692) ,男 ,大学本科 ,高级工程师 ; E2mail :qihuameimei @163. com ; 修订日期 :2007208210
36
中国冶金 第 17 卷
循环富集 ,使炉底沉积的铅越来越多 。在高炉内无 法控制铅的还原 ,只能控制其入炉量和定期排出沉 积的铅 。 1. 3 锌的行为与危害 锌常以硫化锌 ( ZnS) 状态存在 ,在大于 1 000 ℃ 的高温区还原成锌 。其沸点 (907 ℃) 很低 ,还原出 来的锌立即气化进入煤气 ,上升过程中部分随煤气 逸出炉外 ;但其易在管道和上部凝聚 ,大部分又被氧 化成氧化锌并被炉料吸收再度下降还原 ,形成循环 。 锌蒸气沉积在炉子上部砖衬缝隙或墙面上 ,其 氧化后的体积膨胀会损坏炉衬或造成结瘤 。
注 :括号内数值为百分数 。
除尘灰 0. 161 0. 150
16 0. 026 0. 024 0. 050 (1. 81)
污泥 0. 321 0. 239
19 0. 061 0. 045 0. 106 (3. 87)
产出
1. 299 1. 449 2. 748 (99. 98)
图 1 1 750 m3 高炉碱金属投入产出分布 Fig. 1 Input and output distributing of alkali metals in 1 750 m3 BF
烧结矿 球团 巴块 焦炭 煤粉 投入 生铁 炉渣
0. 046 0. 056 0. 017 0. 063 0. 058
0. 007 0. 423
0. 068 0. 083 0. 007 0. 086 0. 110
0. 001 0. 509
842
589
150
417
104
1 000
270
0. 390 0. 331 0. 026 0. 263 0. 060 1. 070 0. 070 1. 142
第 11 期 杨金福等 :高炉中有害元素的平衡分析及其脱除
37
图 2 350 m3 高炉碱金属投入产出分布 Fig. 2 Input and output distributing of alkali metals in 350 m3 BF
从以上图表看出 : ①碱金属投入支出的相对误 差 ,1 750 m3 、350 m3 高炉分别是 11 566 %、51 086 % , 均较低 ,这说明高炉中碱金属投入产出基本平衡 ;入 炉碱金属负荷分别为 21 937 、21 615 kg/ t , 1 750 m3 高炉比 350 m3 高炉多 01 322 kg/ t ,这主要与济钢高 炉入炉料结构有关 。350 m3 高炉进口球团比例高 , 其带入量略低一些 ,另外支出略高于带入 ; 而 1 750 m3 高炉支出略低于带入 ,主要是新高炉 ,有部分富 积在炉内 。通常认为碱负荷不超过 5 kg/ t ,而目前 济钢高炉均不超过 3 kg/ t ,总体处中等偏低水平 。 ②烧结矿带入碱金属最高 ,分别占 1 750 m3 、350 m3 高炉全部碱负荷的 401 45 %、361 81 % ,其次是球团 矿 261 84 %、311 36 % , 再 次 是 焦 炭 占 201 98 %、 231 76 % ,煤粉和进口块带入分别占 71 61 %、61 68 %