[冶金行业管理]烧结矿中有害元素对高炉的危害和抑制
有害元素对宣钢高炉的影响
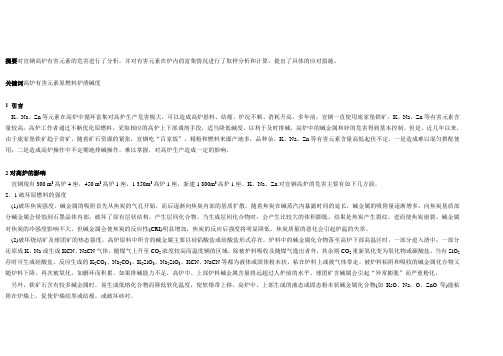
摘要对宣钢高炉有害元素的危害进行了分析,并对有害元素在炉内的富集情况进行了取样分析和计算,提出了具体的应对措施。
关键词高炉有害元素原燃料炉渣碱度1 引言K、Na、Zn等元素在高炉中循环富集对高炉生产危害极大,可以造成高炉悬料、结瘤、炉况不顺、消耗升高。
多年前,宣钢一直使用庞家堡铁矿,K、Na、Zn等有害元素含量较高,高炉工作者通过不断优化原燃料,采取相应的高炉上下部调剂手段,适当降低碱度,以利于及时排碱,高炉中的碱金属和锌的危害得到基本控制。
但是,近几年以来,由于庞家堡铁矿趋于贫矿,随着矿石资源的紧张,宣钢吃“百家饭”,精粉和燃料来源产地多,品种杂,K、Na、Zn等有害元素含量高低起伏不定,一是造成难以混匀搭配使用;二是造成高炉操作中不定期地排碱操作,难以掌握,对高炉生产造成一定的影响。
2对高炉的影响宣钢现有300 m3高炉4座,450 m3高炉1座,1 350m3高炉1座,新建1 800m3高炉1座。
K、Na、Zn对宣钢高炉的危害主要有如下几方面。
2.1破坏原燃料的强度(1)破坏焦炭强度。
碱金属的吸附首先从焦炭的气孔开始,而后逐渐向焦炭内部的基质扩散,随着焦炭在碱蒸汽内暴露时间的延长,碱金属的吸附量逐渐增多。
向焦炭基质部分碱金属会侵蚀到石墨晶体内部,破坏了原有层状结构,产生层间化合物。
当生成层间化合物时,会产生比较大的体积膨胀,结果是焦炭产生裂纹,进而使焦炭崩裂。
碱金属对焦炭的冷强度影响不大,但碱金属会使焦炭的反应性(CRI)明显增加,焦炭的反应后强度将明显降低。
焦炭质量的恶化会引起炉温的失常。
(2)破坏烧结矿及球团矿的热态强度。
高炉原料中所含的碱金属主要以硅铝酸盐或硅酸盐形式存在,炉料中的碱金属化合物落至高炉下部高温区时,一部分进入渣中;一部分还原成K、Na或生成KCN、NaCN气体,随煤气上升至CO2浓度较高而温度辆的区域,除被炉料吸收及随煤气逸出者外,其余则CO2重新氧化变为氧化物或碳酸盐,当有SiO2存时可生成硅酸盐。
杜绝有害焦 高炉不“生病”

(壹佰钢铁网推荐)近年来,国内外原燃料价格不断上涨,而质量水平却逐年下降,保持供应稳定都变得困难。
为了降低生产成本,原燃料中大量配加尘泥固废料,致使有害元素在高炉内循环富集。
这样会大幅减弱焦炭热态性能,加剧其在高温区的粉化,致使炉况顺行不好,难以降低焦比、提高煤比,对高炉正常生产带来了不利影响。
因此,有必要开展细致全面的研究,深入了解有害元素对焦炭热态性能的影响规律和特点,进而明确对高炉冶炼的危害程度,确立合理的有害元素入炉负荷标准,并探寻更加科学有效的控制手段。
这对保证高炉的长期平稳生产具有重要意义。
焦炭热态性能影响高炉稳定焦炭是高炉炼铁工艺不可缺少的燃料。
特别是在现代大型高炉冶炼条件下,随着焦比的降低、冶炼强度的提高,焦炭负荷增加,在高炉内的滞留时间延长,其作为料柱骨架保持炉内透气透液性的作用更加突出。
因此,高炉冶炼中焦炭的热态性能非常重要。
焦炭的热态性能指标包括反应性(CRI)和反应后强度(CSR)。
反应性是焦炭在高温状态下与氧化性气氛发生碳溶反应的能力。
反应后强度是焦炭在经受氧化性气氛溶蚀状态下保持高温强度的能力。
焦炭热态性能不好,则在高温区域更易粉化,骨架作用能力减小,恶化料柱透气透液性,影响煤气流稳定和高炉顺行。
降低CRI、提高CSR一直是炼铁界的共识。
在加剧焦炭粉化的众多因素中,循环富集的碱金属等有害元素能够催化碳溶反应,对焦炭的破坏非常严重。
因此,研究有害元素对焦炭热态性能的影响,进而明确对高炉冶炼的危害以便采取相应控制措施,对保证高炉长期平稳生产具有重要意义。
有害元素影响焦炭热态性能碱金属(K、Na)的影响。
进入高炉的碱金属主要以复杂的硅酸盐和硅铝酸盐形式存在。
这些含碱矿物在高温区熔融后大部分进入炉渣,与焦炭充分接触时部分以硅酸盐形式被C 还原出K、Na单质。
因为高炉炉腹和炉缸部位的环境温度远远超过了金属K、Na的沸点(分别为759℃、883℃),生成的单质碱金属立即气化以蒸汽形式随煤气流上升,在不同温度条件下又与其他物质反应生成碳酸盐、硅酸盐、氰化物等。
有害元素对高炉冶炼的影响

有害元素对高炉冶炼的影响有害元素通常指硫(S)、磷(P)、钾(K)、钠(Na)、铅(Pb)、Zn (锌)、As(砷)、Cu。
通常高炉冶炼对铁矿石要求如下:Pb<0.1%、Zn<0.1%、As<0.07%、Cu<0.2%、K2O+Na2O≤0.25%。
硫(S):硫对钢材是最为有害的成份,它使钢材产生“热脆性”。
铁矿石中硫含量高,高炉脱硫成本增大,所以入炉铁矿石含硫愈少愈好。
λ磷(P):磷对钢材来说也是常见有害元素之一,它使钢材产生“冷脆性”。
铁矿石中的磷,在高炉冶炼时100%进入生铁,烧结也不能脱磷,控制生铁含磷量主要是靠控制铁矿石含磷量。
脱磷只能通过炼钢来进行,增加了炼钢的脱磷成本。
因此,铁矿石含磷越低越好。
λ碱金属:碱金属主要有钾和钠。
钾、钠对高炉的影响不是正比例性质,高炉本身有一定的排碱能力,碱金属在控制范围内对高炉影响不大。
但是入炉铁矿石碱金属含量太多,超过高炉排碱能力,就会形成碱金属富集,导致高炉中上部炉料碱金属含量大大超过入炉料原始水平。
铁矿石含有较多的碱金属极易造成软化温度降低,软熔带上移,不利于发展间接还原,造成焦比升高。
球团含有碱金属会造成球团异常膨胀引起严重粉化,恶化料柱透气性。
碱金属对焦炭性能破坏也很严重。
另外,高炉中上部碱金属化合物黏附在炉墙上,促使炉墙结厚、结瘤并破坏砖衬。
因此,铁矿石含碱金属越低越好。
λ铅(Pb):铅在高炉中几乎全部被还原,由于密度高达11.34t∕m³,故沉于死铁层之下,易破坏炉底砖缝,有可能会造成炉底烧穿。
λ锌(Zn):锌很容易气化,锌蒸汽容易进入砖缝,氧化成为ZnO后膨胀,破坏炉身上部耐火砖衬。
λ砷(As):砷对钢材来说也是有害元素之一,它使钢材产生冷脆性,使得钢材焊接性能变差。
铁矿石中砷基本还原进入生铁,影响生铁质量。
此外砷在烧结过程中挥发,对环境影响较大。
λ铜(Cu):铜会使钢材“热脆”,钢材不易轧制和焊接。
少量铜能改善钢的耐蚀性。
在高炉冶炼中,铜全部还原进入生铁中。
烧结矿中有害元素对高炉的危害和抑制

烧结矿中有害元素对高炉的危害和抑制
为适应当前严峻的钢铁形势,进一步降低铁水成本,各钢铁企业都采用低价的外矿粉进行烧结,并充分利用烧结、炼铁、炼钢工序所产生的各种除尘灰,利用其低价和含有大量的C、Fe、CaO、MgO等有利成分的优势,来降低烧结料消耗,从而达到降低成本的目的。
但由于各种外矿粉及除尘灰都含一定量的K、Na、Zn等有害元素,大量配加会造成高炉碱负荷、锌负荷超标,高炉炉墙结厚结瘤,加剧炉缸侵蚀,影响炉况稳定顺行。
碱金属、铅、锌等有害金属元素对高炉影响的生产认知和调研

碱金属、铅、锌等有害金属元素对高炉影响的生产认知和调研高炉炼铁技术人员越来越重视生铁成本控制,低成本冶炼、经济炉料结构冶炼不断得到认可,但有害金属元素入炉负荷不断升高,不仅未能达到低成本冶炼的目标,还一度造成生产被动……高炉生产对铁矿石原料的要求是:含铁量高、脉石少、有害杂质少、化学成分稳定、粒度均匀、良好的还原性以及一定的机械强度等等。
我国国内铁矿石资源呈现两大特点:一是贫矿多,富矿少。
贫矿资源占矿石总量的80%左右。
二是单一矿种少,复合矿石多。
随着钢铁工业的迅猛发展,资源消耗殆尽,铁矿石富矿不断减少,或者为降低生铁原料成本的需要,大量富含其它元素的复合铁矿石逐渐大量使用。
入炉有害杂质元素的负荷加大,对高炉生产和高炉寿命造成的影响日益突出。
我们说高炉入炉有害元素主要由钾、钠、铅、锌、砷、硫等,当其入炉负荷显著提高到一定数值后,逐渐影响高炉正常生产,破坏炉况顺行,非计划休风率升高、铁水质量降低和技术经济指标下降明显,增加生铁成本,同时,大大威胁高炉安全生产。
高炉炼铁前辈对碱金属、铅、锌等的认识早期,高炉炼铁技术人员对于碱金属的认知是在实践生产中,摸索着进行的,然后再加大分析、评估其利弊。
碱金属:1)20世纪中期,美国基尼瓦厂高炉每次停炉检修和更换炉衬时发现高炉内有炉瘤,初步分析认为是由于原料中的碱金属负荷过高引起的。
2)1970年6月,加拿大钢铁公司高炉炉况恶化,导致三个月炉况失常,通过化验分析,所使用球团中的碱金属含量是其他球团的3-4倍。
当去掉这种高碱金属球团时,炉况顺行好转,焦炭负荷提高,焦比降低。
铅:20世纪中期,高炉炉底砖衬不同程度的出现了膨胀、增重现象,且发现炉底、炉基耐火衬体中均有大量的铅存在,进一步的分析研究后,逐步形成了铅在高炉内渗透机理。
锌:20世纪40年代,苏联炼铁技术人员已经认识到锌对高炉的主要危害是形成锌瘤,影响高炉生产、炉顶设备和炉衬。
60年代,在苏联科茨捏茨和乌拉尔钢铁厂高炉的炉喉和上升管道中均发现了锌瘤,这些锌瘤呈灰色或灰绿色,表面可以看到细的红锌矿结晶颗粒。
烧结矿对高炉的影响
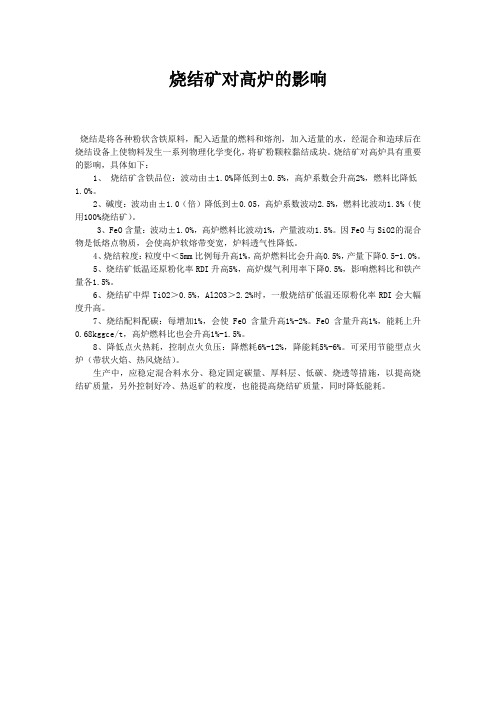
烧结矿对高炉的影响
烧结是将各种粉状含铁原料,配入适量的燃料和熔剂,加入适量的水,经混合和造球后在烧结设备上使物料发生一系列物理化学变化,将矿粉颗粒黏结成块。
烧结矿对高炉具有重要的影响,具体如下:
1、烧结矿含铁品位:波动由±1.0%降低到±0.5%,高炉系数会升高2%,燃料比降低
1.0%。
2、碱度:波动由±1.0(倍)降低到±0.05,高炉系数波动2.5%,燃料比波动1.3%(使用100%烧结矿)。
3、FeO含量:波动±1.0%,高炉燃料比波动1%,产量波动1.5%。
因FeO与SiO2的混合物是低熔点物质,会使高炉软熔带变宽,炉料透气性降低。
4、烧结粒度:粒度中<5mm比例每升高1%,高炉燃料比会升高0.5%,产量下降0.5-1.0%。
5、烧结矿低温还原粉化率RDI升高5%,高炉煤气利用率下降0.5%,影响燃料比和铁产量各1.5%。
6、烧结矿中焊TiO2>0.5%,Al2O3>2.2%时,一般烧结矿低温还原粉化率RDI会大幅度升高。
7、烧结配料配碳:每增加1%,会使FeO含量升高1%-2%。
FeO含量升高1%,能耗上升0.68kggce/t,高炉燃料比也会升高1%-1.5%。
8、降低点火热耗,控制点火负压:降燃耗6%-12%,降能耗5%-6%。
可采用节能型点火炉(带状火焰、热风烧结)。
生产中,应稳定混合料水分、稳定固定碳量、厚料层、低碳、烧透等措施,以提高烧结矿质量,另外控制好冷、热返矿的粒度,也能提高烧结矿质量,同时降低能耗。
转发:锌对高炉的危害

(1)跟踪监控入炉锌负荷。
由于料场堆积大量的高锌矿粉,通过进购低锌矿,增加低锌矿比例,降低高锌矿用量,使烧结矿中的锌含量由0。
095%降到0.070%以下。
(2)自产球团矿中的锌含量由0.060%降到0。
040%以下。
(3)烧结停止配加重力灰,防止高锌灰再次循环.(4)调整块矿比例,减少高锌块矿用量。
4。
2 建立合理的操作制度.4.2.1 选择合理的装料制度(1)上部布料明确“两股气流”的操作思想,各炉布矿角度内缩一个档位,布矿环带减少一圈,做到了边缘、中心两道气流兼顾.(2)各炉缩小矿批8~10%,通过上部调剂,改善料柱透气性,减少了崩料、炉顶料面“吹翻"现象,稳定了矿焦平台,炉况明显好转。
4.2。
2 选择适宜的送风制度(1)调整风口布局,1280m3高炉减小风口面积1%,1800 m3高炉减小面积4。
7%,各炉风速均有所提高,为活跃炉缸中心创造了条件。
(2)各炉降低煤比,由正常150—155kg/t降到130—140kg/t,改善了料柱透气性。
(3)当炉况初步稳定后,高炉选择高风温,风口前理论燃烧温度控制由原来的2260℃提高到2300℃,努力提高炉缸温度,增加高炉抗干扰能力。
4。
2。
3 热制度的确定(1)降低焦炭负荷,提高焦比10-15kg/t,综合负荷由2。
95倍左右降到2.8-2.85倍,改善了料柱透气性.(2)提高炉温,铁水物理热控制必须1480℃以上;铁水[Si]控制0.35—0。
55%,严禁[Si]低于0.30%,保证炉温充沛稳定。
(3)适当减少富氧率,富氧量1280m3高炉由4500 -5000 m3/h降到3500-4000m3/h,1800m3高炉由8000—8500m3/h降到7000-7500m3/h,平衡风口前理论燃烧温度,确保炉况顺行.4.2。
4 改进高炉休风及恢复操作由于休风后的恢复过程中,多次发生了烧坏风口情况,因此调整恢复思路.通过降低负荷,全焦冶炼改善料柱透气性;当炉缸温度,渣铁流动性正常后,炉缸透气性、透液性改善,逐步恢复风量和开风口,再恢复喷煤负荷;最后恢复富氧逐步强化,有效避免了高锌状况下恢复过程烧风口的问题。
朝阳钢铁高炉有害元素的分析及控制
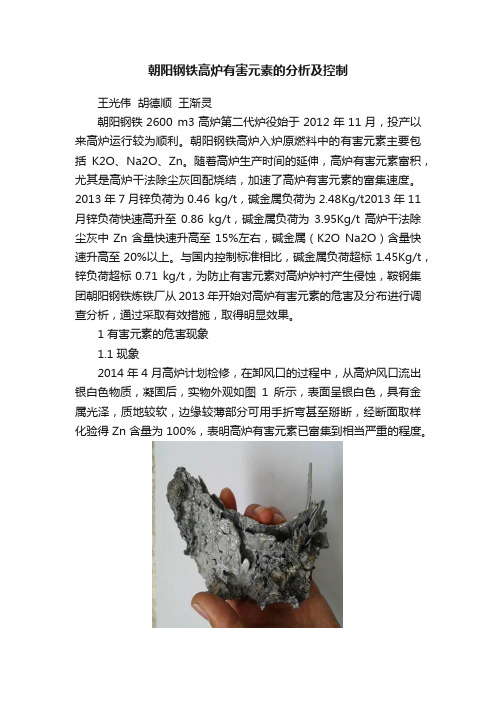
朝阳钢铁高炉有害元素的分析及控制王光伟胡德顺王渐灵朝阳钢铁2600 m3高炉第二代炉役始于2012年11月,投产以来高炉运行较为顺利。
朝阳钢铁高炉入炉原燃料中的有害元素主要包括K2O、Na2O、Zn。
随着高炉生产时间的延伸,高炉有害元素富积,尤其是高炉干法除尘灰回配烧结,加速了高炉有害元素的富集速度。
2013年7月锌负荷为0.46 kg/t,碱金属负荷为2.48Kg/t2013年11月锌负荷快速高升至0.86 kg/t,碱金属负荷为3.95Kg/t高炉干法除尘灰中Zn含量快速升高至15%左右,碱金属(K2O Na2O)含量快速升高至20%以上。
与国内控制标准相比,碱金属负荷超标1.45Kg/t,锌负荷超标0.71 kg/t,为防止有害元素对高炉炉衬产生侵蚀,鞍钢集团朝阳钢铁炼铁厂从2013年开始对高炉有害元素的危害及分布进行调查分析,通过采取有效措施,取得明显效果。
1 有害元素的危害现象1.1 现象2014年4月高炉计划检修,在卸风口的过程中,从高炉风口流出银白色物质,凝固后,实物外观如图1所示,表面呈银白色,具有金属光泽,质地较软,边缘较薄部分可用手折弯甚至掰断,经断面取样化验得Zn含量为100%,表明高炉有害元素已富集到相当严重的程度。
图1 风口流出白色物质1.2 危害1.2.1 炉体上涨有害元素富集造成高炉炉体上涨,主要表现在以下几个方面:高炉炉底板开焊,上涨约100 mm,如图2(a)所示;高炉炉体9 层平台标尺上涨约50 mm,如图2(b)所示;高炉冷却水管与平台联接处开焊,水管上移出现弯曲,如图2(c)所示;高炉上升管膨胀节发生位移,如图2(d)所示。
1.2.2 炉墙结厚2015 年9 月~2016 年2 月,由于高炉干法除尘灰无地存放及降成本需要,烧结开始回配干法除尘灰,烧结矿中Zn 含量和碱金属含量快速增加,高炉锌负荷升高至0.9 kg/t。
同时由于原料库存较低,导致入炉原燃料质量波动较大,入炉粉末增多,炉况波动大,造成2016 年3~5 月高炉炉墙结厚。
- 1、下载文档前请自行甄别文档内容的完整性,平台不提供额外的编辑、内容补充、找答案等附加服务。
- 2、"仅部分预览"的文档,不可在线预览部分如存在完整性等问题,可反馈申请退款(可完整预览的文档不适用该条件!)。
- 3、如文档侵犯您的权益,请联系客服反馈,我们会尽快为您处理(人工客服工作时间:9:00-18:30)。
(冶金行业)烧结矿中有害元素对高炉的危害和抑制烧结矿中有害元素对高炉的危害和抑制黄克存、班友合、孟德礼(国丰钢铁有限X公司技术部)摘要随着我X公司的高炉逐步进入炉役后期,延长高炉寿命不仅能够直接减少昂贵的大中修费用,仍能够避免由于停产造成的经济损失。
造成高炉损坏的原因和机理错综复杂,但烧结矿带入的碱金属和锌的破坏作用应引起我们的高度重视。
关键词高炉碱负荷锌负荷危害为适应当前严峻的钢铁形势,进壹步降低铁水成本,各钢铁企业都采用低价的外矿粉进行烧结,且充分利用烧结、炼铁、炼钢工序所产生的各种除尘灰,利用其低价和含有大量的C、Fe、CaO、MgO 等有利成分的优势,来降低烧结料消耗,从而达到降低成本的目的。
但由于各种外矿粉及除尘灰都含壹定量的K、Na、Zn等有害元素,大量配加会造成高炉碱负荷、锌负荷超标,高炉炉墙结厚结瘤,加剧炉缸侵蚀,影响炉况稳定顺行。
1.烧结矿中有害元素的来源烧结所有外矿粉有害元素含量如下表所示:表1烧结外矿粉有害元素含量(%)试样名称Zn Na Na2O K K2O 信昂澳粉0.015 0.047 0.064 0.022 0.027 雄鹰澳粉0.025 0.119 0.14 0.076 0.092巴姆澳粉0.0055 0.156 0.21 0.035 0.042 繁荣巴粗0.0091 0.031 0.042 0.216 0.26 博斯巴粗0.14 0.013 0.018 0.07 0.085 在高炉生产中,钾、钠、锌存在俩个循环,第壹个循环是高炉内部的小循环,第二个循环是烧结—高炉的大循环。
通过上表可见出,原料中的钾、钠、锌的量是相对稳定但不可控,要控制其富集减少对高炉的危害就是要打破第二个循环,减少高炉布袋灰、烧结机头灰等高碱、高锌灰的循环使用。
以下是我X公司布袋灰、烧结机头灰的有害元素成分分析:表2北区试样灰中有害元素含量(%)试样名称Zn Na Na2O K K2O红泥除尘灰0.290 0.0816 0.110 0.1743 0.210 36m2机头灰 2.000 5.1342 6.920 48.7915 58.800 36m2机尾灰0.120 0.0965 0.130 0.2987 0.360 北区450m2高炉重力1.120 0.1855 0.250 0.2157 0.260灰北区450m2高炉布袋0.240 0.3710 0.500 1.2032 1.450灰表3南区450m3高炉系统试样灰中有害元素含量(%)试样名称Zn Na Na2O K K2O 南区450m3布袋除5.000 0.4823 0.650 1.3774 1.660尘灰南区三号450m3重0.300 0.0890 0.120 0.1494 0.180力灰南区三号450m3布3.620 0.2968 0.400 0.8713 1.050袋灰1#72m2机头灰0.056 0.3190 0.430 2.0413 2.460 2#72m2机头灰0.057 0.3413 0.460 2.0911 2.520 72m2机尾灰0.024 0.0683 0.092 0.2323 0.280 2#132m2机头灰0.170 1.0684 1.440 7.4681 9.000 132m2机尾灰0.340 0.0460 0.062 0.1494 0.180表4南区1780m3高炉系统试样灰中有害元素含量(%)试样名称Zn Na Na2O K K2O 230m2烧结机尾灰0.084 0.0683 0.092 0.2987 0.360 120t转炉除尘灰0.090 0.2077 0.280 0.9626 1.1601780m3高炉重力0.560 0.1335 0.180 0.5726 0.690灰1780m3高炉布袋3.620 0.2226 0.300 1.1285 1.360灰2.高炉所用原燃料中有害元素含量及负荷计算1780m3高炉入炉原燃料有害元素含量及负荷计算如下表所示:表51780m3高炉碱负荷及锌负荷计算表名称消耗量(kg/t铁)K2O(%)K2O(kg)Na2O(%)Na2O(kg)K2O+Na2O(kg)Zn(%)Zn(kg)烧结矿 1386.4 0.38 5.268 0.13 1.802 7.071 0.07 0.970 球团矿34.66 0.16 0.055 0.16 0.055 0.111 0.029 0.010 块矿311.94 0.25 0.780 0.04 0.125 0.905 0.0004 0.001焦炭360 0.1150.414 0.0635 0.2286 0.6426 0.0247 0.089煤粉160 0.1 0.16 0.085 0.1360 0.2960 0.16 0.256 总计 6.677 2.3466 9.0236 1.326表6其它高炉碱负荷及锌负荷计算结果K2O+Na2O(kg) Zn(kg)北区4#450m3高炉 4.078 1.648南区4#450m3高炉7.359 0.898南区5#450m3高炉 5.730 2.7322 从之上计算的结果见,3月份高炉碱负荷最高达到9.0公斤/吨,锌负荷达到2.73公斤/吨,都处于严重超标状态,直接影响到高炉的顺行和长寿,进而影响X公司的经济效益。
以1780m3高炉为例,入炉原燃料带入的碱金属及锌含量分别占碱负荷、锌负荷的比例如下图所示:从炉料结构见,78.4%的碱金属来自烧结矿,来自其它的仅占21.6%,73.2%的锌来自于烧结矿,其它占26.8%。
从上图表能够见出,烧结矿是碱金属和锌的主要来源。
根据我X公司物料状况,结合俩个铁厂意见,拟定了碱负荷及锌负荷标准:高炉碱负荷≤5㎏/t,锌负荷≤1㎏/t。
3.有害元素对高炉的危害3.1危害1)钾、钠等碱金属能降低矿石的软化温度,引起球团矿异常膨胀而严重粉化,使烧结矿的仍原粉化加剧。
2)钾、钠等碱金属是焦炭溶损反应的催化剂,增加焦炭的反应性。
3)钾、钠等碱金属会造成炉缸堆积,高炉结瘤,透气性恶化,炉墙损坏及炉况失常。
4)锌常以闪锌矿的形式存在,在炉内,先转化为氧化物,然后在1000℃的高温区被CO仍原为气态锌,沉积在炉墙上,形成炉瘤,使透气性变坏和炉墙结厚,高炉难行、悬料次数急剧增加。
3.2K、Na的富集规律K、Na主要是以硅酸盐(K2SiO3、Na2SiO3)的形态存在于炉料中,当炉料下到高温区或炉缸时,硅酸钾将进行以下反应:2K2SiO3+2C=4K+2SiO2+2CO(1)2K↑+2(SiO2)+2(FeO)=2(K2SiO3)+2Fe(2)由式(1)可知,产生的K蒸汽随煤气上升,到中温区,和渣中FeO和SiO2反应又生成K2SiO3,反应式(2)的产物是K2SiO3和铁(Fe)被下降的炉料所吸收,因而使下降炉料中K2O含量增高,且且又随同炉料下降到高温区,钾含量高的炉料中的K2SiO3,下到高温区后,又被仍原成钾蒸气,又再次随煤气流上升到中温区,又和下降过程含有大量FeO和SiO2的炉料相遇,钾蒸气和SiO2将生成更多的硅酸钾的硅酸钾又再次随炉料下降到高温区,这样不断下降上升和气化吸收,不断循环之后,炉料中K2O含量在炉内不断增加,这就是所谓的碱金属“循环富集”过程,最终导致炉料和煤气中K2O含量增加,恶化料柱透气性,容易导致高炉崩塌料,或悬料,严重时导致高炉结厚和结瘤,对炉况产生严重影响。
3.3Zn的循环富集规律Zn常以闪锌矿(Zns)的形式存在,高炉冶炼时,先转化为氧化物,在高于1000℃高温区被仍原为气态锌,大量锌蒸汽随着煤气上升到温度较低的块状带时冷凝,然后再被CO2氧化为ZnO。
这些ZnO 仅少量随着炉尘逸出炉外,大量积存在块状带,块状带的高锌炉料在下降过程中,部分ZnO被氧化仍原部分进入软熔带。
软熔带内ZnO 绝大部分气化随煤气上升,从而造成锌在1200℃以下区域内的循环,因锌不被渣铁吸收,锌蒸汽在炉内循环,沉积在炉墙上,可和炉衬和炉料反应,形成低熔点化合物粘附在炉墙上,形成炉瘤,阻塞煤气通道,影响高炉顺行。
4.降低碱负荷、锌负荷的措施4.1降低碱负荷的措施1)对所使用的外粉进行批量检测,合理配加,以控制烧结矿碱金属含量。
2)对焦炭和煤粉灰分中的钾、钠含量,分品种每旬进行检验分析。
3)对烧结自循环的机头灰,因钾、钠含量极高,建议送综合料场处理后使用或停用。
4)在保证生铁含硫不出格的原则下,适当降低炉渣碱度。
自由碱度±0.1%,影响渣中碱金属氧化物0.3%。
5)炉渣碱度不变,生铁含硅±0.1%,影响渣中碱金属氧化物0.045%。
6)烧结机头电厂除尘灰由吸排车吸走外销,减轻碱金属循环富集,可使烧结矿碱金属含量降低20%。
4.2排碱制度1)大高炉每月排碱壹次,炉渣二元碱度控制在1.0~1.05,炉温控制0.5~0.6,时间3~4个班。
2)提高炉渣中的MgO含量,提高炉渣的流动性。
我厂在日常冶炼时,高炉炉渣二元碱度控制在1.1~1.16,MgO:450m3高炉11~12,1780m3高炉10~11。
3)减少入炉粉末,每周做3次筛分检测,<5mm不大于3%。
同时控制顶温到140℃之上,增加壹部分炉尘的吹出。
5.措施的实施为检验降低碱、锌负荷措施的效果,11月份对壹铁1780m3高炉碱负荷、锌负荷又进行了计算,结果如下表所示:表711月份碱负荷及锌负荷计算表名称消耗量(kg/t铁)K2O%K2O(kg)Na2O%Na2O(kg)K2O+Na2O(kg)Zn%Zn(kg)烧结矿1263.60.0861.090.10 1.26 2.35 0.14 1.77球团矿64.80.0940.060.13 0.08 0.150.0140.01南非块矿291.6 0.100.290.0580.17 0.460.00280.01焦炭360 0.0650.230.1670.60 0.840.2410.87煤粉140 0.42 0.590.46 0.64 1.230.0120.02合计2.262.76 5.02 2.67和3月份数据比较:表811月份和3月份的碱负荷及锌负荷对比名称K2O(kg) Na2O(kg K2O+Na2O(kg) Zn(kg))11月份合计 2.26 2.76 5.02 2.673月份合计 6.68 2.35 9.02 1.33合计比较-4.42 +0.42 -4.00 +1.34通过上表可见出,230烧结通过停用布袋灰,减少了其在烧结、高炉间的循环,11月份高炉碱负荷为5.02kg/t,比3月份的9.02kg/t 降低了4kg/t,基本达到制定的5kg/t标准。
11月份锌负荷为2.67kg/t,比3月份的1.33kg/t上升了1.34kg/t,较1kg/t的标准超1.67kg/t。