高炉废渣处理工作危险有害因素分析
高炉渣处理爆炸原因分析及对策措施

高炉渣处理爆炸原因分析及对策措施原虎军,杜福来,罗亚中,杨利娟(云南安益安全评价有限公司,云南 昆明 650200)摘 要:近年来,高炉伴随着钢铁行业的快速发展朝向大型化发展,高炉渣处理伴随高炉生产重要性日渐突出。
然而在实践中,高炉渣处理工艺要求极高,一旦处理不当,将会有较大几率产生爆炸问题,一方面威胁生产工作人员生命安全;另一方面不利于保证生产工作的安全进行,影响到生产效益的增长。
本文围绕高炉渣处理展开分析,在深入分析高炉渣处理爆炸具体原因的基础上,立足于保证高炉安全生产目标,探讨了行之有效的应对措施。
关键词:高炉渣处理;爆炸原因;应对措施中图分类号:X757 文献标识码:A 文章编号:1002-5065(2019)12-0222-2Cause Analysis and Countermeasures of explosion in blast Furnace Slag treatmentYUAN Hu-jun, DU Fu-lai, LUO Ya-zhong, YANG Li-juan(Yunnan Anyi Safety Evaluation Co., Ltd.,Kunming 650200,China)Abstract: In recent years, with the rapid development of iron and steel industry, blast furnace slag treatment is becoming more and more important. However, in practice, blast furnace slag treatment process requirements are very high, once handled improperly, there will be a greater probability of explosion problems, on the one hand, threaten the lives of production staff; on the other hand, it is not conducive to ensuring the safety of production work, affecting the growth of production benefits. This paper focuses on the analysis of blast furnace slag treatment, on the basis of in-depth analysis of the specific causes of blast furnace slag treatment explosion, based on the goal of ensuring the safety of blast furnace production, discusses the effective countermeasures.Keywords: Blast furnace slag treatment; explosion cause; response measures1高炉渣处理爆炸具体原因分析1.1 高炉生产异常爆炸事故原因高炉渣处理过程中,一旦出现生产异常,其直接导致的结果就是高炉渣与铁无法有效分离,意味着高炉渣中含铁量将会有效提高,势必会影响到后续的处理,一旦处理不当,就会产生高炉渣处理爆炸事故。
高炉系统的危险有害因素辨识
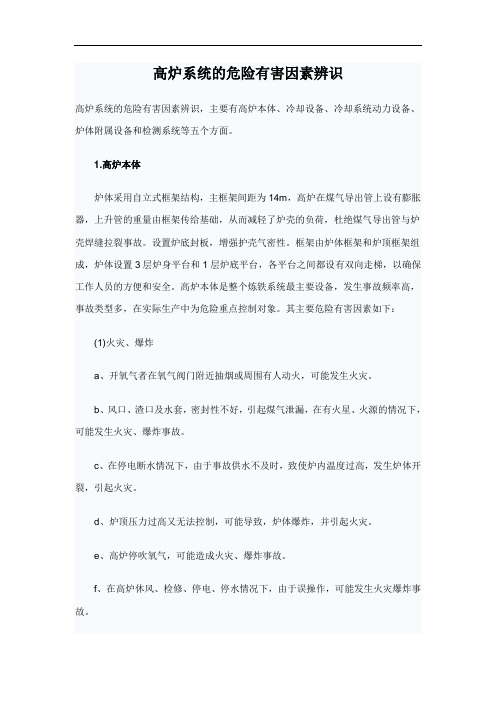
高炉系统的危险有害因素辨识高炉系统的危险有害因素辨识,主要有高炉本体、冷却设备、冷却系统动力设备、炉体附属设备和检测系统等五个方面。
1.高炉本体炉体采用自立式框架结构,主框架间距为14m,高炉在煤气导出管上设有膨胀器,上升管的重量由框架传给基础,从而减轻了炉壳的负荷,杜绝煤气导出管与炉壳焊缝拉裂事故。
设置炉底封板,增强护壳气密性。
框架由炉体框架和炉顶框架组成,炉体设置3层炉身平台和1层炉底平台,各平台之间都设有双向走梯,以确保工作人员的方便和安全。
高炉本体是整个炼铁系统最主要设备,发生事故频率高,事故类型多,在实际生产中为危险重点控制对象。
其主要危险有害因素如下:(1)火灾、爆炸a、开氧气者在氧气阀门附近抽烟或周围有人动火,可能发生火灾。
b、风口、渣口及水套,密封性不好,引起煤气泄漏,在有火星、火源的情况下,可能发生火灾、爆炸事故。
c、在停电断水情况下,由于事故供水不及时,致使炉内温度过高,发生炉体开裂,引起火灾。
d、炉顶压力过高又无法控制,可能导致,炉体爆炸,并引起火灾。
e、高炉停吹氧气,可能造成火灾、爆炸事故。
f、在高炉休风、检修、停电、停水情况下,由于误操作,可能发生火灾爆炸事故。
(2)中毒a、挖炉缸作业时,如通风不良,炉缸内煤气浓度过高,可能造成煤气中毒事故。
b、换风口及二套时,由于煤气泄漏,如不加强防护,可能造成煤气中毒事故。
c、在炉体清理作业中,由于残留煤气,如通风不良,无恰当防护措施,可能发生煤气中毒事故。
d、在高炉休风、检修、停电、停水情况下,由于误操作,可能发生火灾爆炸事故。
(3)烧伤a、在休风倒流阶段,炉前工离风口过近,可能被喷火烧伤。
b、在进行换风口操作时,由于风口内渣铁没有完全淌出,可能烧伤工人。
c、风管烧穿打水时,可能对工人造成伤害。
d、在风口区域、铁口旁取暖,工人可能被烧伤。
e、烧氧时,吹氧管顶的太死,氧气回火,可能造成工人烧伤。
(4)高空坠落a、平台四周栏杆走桥损坏、送脱,操作人员可能从高空坠落。
高炉渣处理爆炸原因及攻克措施探析

高炉渣处理爆炸原因及攻克措施探析高炉大型化发展趋势促使高炉渣处理逐渐受到人们的重视,但在处理过程中,受其自身的因素影响,容易出现爆炸情况,造成严重的影响,本文从高炉渣处理环节入手,深入进行分析,结合实际情况,从整体上进行分析,明确其爆炸原理,做好针对性预防措施,以降低爆炸事故发生几率。
标签:高炉;渣处理;爆炸原因;解决措施引言随着时代不断发展,高炉冶炼逐渐成为钢铁行业中主要的炼铁生产方式,可以生产出高质量的高炉生铁,并衍生出副产物,如高炉煤气、高炉渣以及炉尘。
高炉渣具有较多的用途,通过合理的急速水淬冷后可以作为高质量的建筑材料,实现资源的最大化利用,以满足当前的需求。
一、高炉渣处理爆炸原因分析(一)高炉渣水淬分析现阶段,我国在进行高炉渣处理过程中,主要是应用水淬工艺进行处理,通过水力冲渣进行处理,以满足生产的需求。
水淬工艺主要包括三个过程,为粒化、脱水、储运三个工艺,不同的过程其处理的目的不同,粒化的主要目的是利用高压水将高温液态渣击碎,通过水淬冷却为水渣。
脱水的目的是灵活利用过滤或者分离等方法进行水渣分离,将水渣进行集中处理,并保证其水可以进入循环使用。
储运是将当前经过处理的水渣进行集中的存储,并采用现有的技术进行二次脱水,灵活应用当前的辅助技术进行优化,满足当前的需求[1]。
(二)高炉炉渣爆炸通常情况下,高炉炉渣出炉后温度高达约为1450℃-1550℃,在进行水淬过程中,需要进行能量转化,高炉渣的温度瞬间下降,在释放大量的热同时,产生水汽,通过水蒸气进行能量转化。
高炉渣爆炸的形式较多,通常主要在高炉生产异常时容易出现爆炸,分离过程中由于热能量传递,造成水接收较大的能量,铁的含量较多,铁的导热系数又高,造成能量的聚集,并且铁容易产生凝固,形成受限空间,增大发生爆炸的几率,因此需要有效的控制铁含量。
渣中含铁是高炉冶炼的常见情况,但通常情况下其含量较少,对正常的冶炼影响较小,但如果存在悬料次数多、炉缸堆积、炉温较低等情况,将导致炉渣整体流动性降低,容易出现分离不佳情况,出现整体的异常,最终引发爆炸。
高炉本体危险性分析

高炉本体危险性分析高炉本体危险性分析高炉是钢铁工业中重要的生产设备,其操作过程中存在多种危险因素。
本文将重点分析高炉本体的危险性,主要包括爆炸与火灾危险、高温与热辐射、电气伤害、机械伤害、中毒与窒息以及其他危险等方面。
1.爆炸与火灾危险高炉在操作过程中,由于炉内燃料燃烧和原料反应,可能产生大量可燃气体,如一氧化碳和氢气。
这些气体在高温下可能与空气混合,遇到火源时可能引发爆炸或火灾事故。
此外,高炉内的焦炭和矿石等原料也可能因高温燃烧而引发火灾。
为了降低爆炸与火灾危险,应采取有效的防火措施,防止可燃气体泄漏和火源进入高炉内。
2.高温与热辐射高炉内温度极高,可达1000℃以上。
高温可能导致高炉结构受损,引发设备故障,同时也会对现场作业人员造成热辐射伤害。
为了降低高温与热辐射的危害,应采取有效的降温措施,如安装冷却装置和定期检查高炉设备。
3.电气伤害高炉操作过程中涉及到大量的电气设备,如鼓风机、除尘器等。
电气设备故障可能导致触电、电弧灼伤等电气伤害。
为了降低电气伤害的风险,应定期检查电气设备的安全性,确保接地良好,防止漏电和短路现象的发生。
4.机械伤害高炉操作过程中涉及到大量的机械运动部件,如皮带、链条等。
机械部件的破损或故障可能导致卷入、夹压等机械伤害事故。
为了降低机械伤害的风险,应定期检查机械部件的完好性和安全性,确保设备维护良好,防止机械故障的发生。
5.中毒与窒息高炉操作过程中产生的气体和粉尘中可能含有有害物质,如一氧化碳、二氧化硫等。
长期接触这些有害物质可能导致中毒和窒息事故的发生。
为了降低中毒与窒息的风险,应采取有效的通风措施,保证工作场所空气流通;同时应佩戴个人防护用品,如防毒面具、口罩等。
6.其他危险除了上述危险因素外,高炉操作过程中还可能存在其他危险因素,如高空作业风险、噪声危害等。
为了降低这些危险因素的影响,应采取有效的防护措施,如佩戴安全带、使用防噪耳塞等。
同时应加强现场安全管理,确保作业规范和安全规程的有效执行。
有害元素对高炉炼铁的影响及控制措施
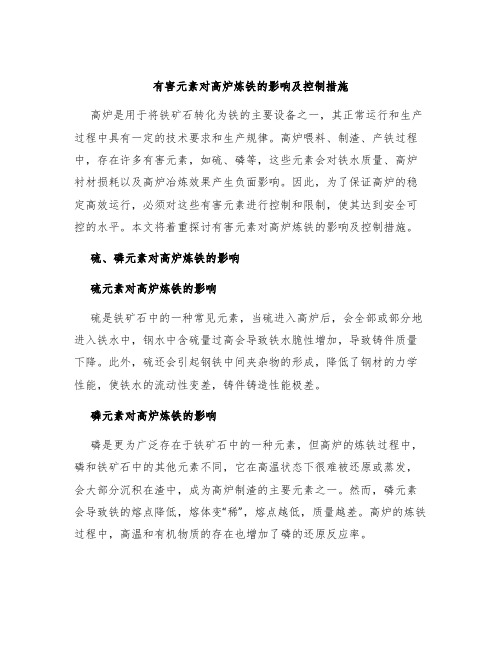
有害元素对高炉炼铁的影响及控制措施高炉是用于将铁矿石转化为铁的主要设备之一,其正常运行和生产过程中具有一定的技术要求和生产规律。
高炉喂料、制渣、产铁过程中,存在许多有害元素,如硫、磷等,这些元素会对铁水质量、高炉衬材损耗以及高炉冶炼效果产生负面影响。
因此,为了保证高炉的稳定高效运行,必须对这些有害元素进行控制和限制,使其达到安全可控的水平。
本文将着重探讨有害元素对高炉炼铁的影响及控制措施。
硫、磷元素对高炉炼铁的影响硫元素对高炉炼铁的影响硫是铁矿石中的一种常见元素,当硫进入高炉后,会全部或部分地进入铁水中,钢水中含硫量过高会导致铁水脆性增加,导致铸件质量下降。
此外,硫还会引起钢铁中间夹杂物的形成,降低了钢材的力学性能,使铁水的流动性变差,铸件铸造性能极差。
磷元素对高炉炼铁的影响磷是更为广泛存在于铁矿石中的一种元素,但高炉的炼铁过程中,磷和铁矿石中的其他元素不同,它在高温状态下很难被还原或蒸发,会大部分沉积在渣中,成为高炉制渣的主要元素之一。
然而,磷元素会导致铁的熔点降低,熔体变“稀”,熔点越低,质量越差。
高炉的炼铁过程中,高温和有机物质的存在也增加了磷的还原反应率。
控制措施在高炉炼铁的生产过程中,有害元素的控制是必不可少的一环。
下面将介绍一些常用的控制措施。
调整原料成分高炉熟料中的有害元素主要来源于铁矿石中,而铁矿石的含硫、含磷量的高低对高炉冶炼过程有很大的影响。
因此,一个有效的控制措施就是调整原料成分。
可以根据熟料化验分析结果预先掌握熟料成分,对成分含有过高有害元素的铁矿石进行挑选和筛选,或者采用掺混矿的方法控制高炉熟料的含硫、含磷量。
清洗高炉和加入流化剂在高炉生产过程中,很多有害元素都会在炉壁上结合和析出。
为了保证高炉正常运行和生产,必须定期对高炉进行清洗。
此外,加入流化剂,可以起到一定的促进还原反应和控制有害元素的效果。
在加入流化剂的过程中,可以调整流化剂的配比和添加时间,以达到较好的控制效果。
高炉有害元素利用分析

高炉有害元素的分析一、有害元素的来源通过对原燃料检测成份分析可以看出:1、碱金属来源主要来焦炭,其次是烧结矿和球团矿;2、Pb、Zn的来源,主要是球团矿和烧结矿。
Pb、Zn的主要来源是生产烧结矿、球团矿的精矿粉。
二、对高炉的影响1、有害元素破坏砖衬及炉体。
原料中的Zn如果长期超标,就会使高炉中Zn富集大量,随着生产的持续进行,Pb、Zn等在高温下就会渗透进入炉缸耐材砖缝,严重时会使风口中套变形,甚至会出现大套法兰上翘开裂冒煤气现象,并伴随煤气泄漏明显发展最终造成炉缸炉皮开裂。
2、造成炉皮开裂,冷却板损坏。
由于有害元素在炉内富集,在炉身中下部软融带附近,有害元素吸附或渗透进入砖缝,造成砖衬被侵蚀和异常膨胀,使冷却板暴露在高温气流中易受冲击而损坏。
随着原燃质量下降,有害元素入炉增加,在内的富集增加,对砖衬的破坏力度加大。
造成炉皮开裂的主要原因是使用含Zn高的原料的结果,从风口粘结物取样分析可知,zn在炉知富集是造成炉缸炉皮开裂的主要原因。
3、造成炉缸,炉底侵蚀速度加快。
碱金属,Zn等有害元素易在炉内循环富集,K、Na以液态或固态粉状化合物粘附在炉衬上破坏砖衬,Zn则以蒸汽形式渗入砖衬缝隙中,冷凝氧化成ZnO后体积膨胀损坏内衬,使高温铁水能够顺利渗入砖缝,造成水温差上升。
4、破坏焦炭强度,炉况顺行度下降。
碱金属的吸附首先从焦炭的气孔开始,而后逐步向焦炭内部扩散随着焦炭在碱金属蒸汽内暴露的时间延长,碱金属的吸附量逐渐增多,焦炭基质部分扩散的碱金属会侵蚀到石墨晶体内部,破坏原有的结构,使焦炭产生较大的体积膨胀,导致焦炭破碎,焦炭反应性增加,反应后强度降低。
5、致使高炉结瘤,严重影响高炉的生产。
大量研究表明,碱金属是高炉炉瘤形成的主要原因。
碱金属氧化物在高炉下部被还原为K、Na蒸气或生成K(Na)CN,随煤气上升到高炉上部,同炉衬发生反应,使砖衬软化和熔融,黏结粉料。
不断进行,就会逐渐形成炉瘤或结厚。
原料中含有较多碱金属,加上操作制度不合适,原料粉末多,炉渣排碱能力差,高炉便会出现频繁结瘤现象。
高炉项目毒性危害分析

高炉项目毒性危害分析高炉项目毒性危害分析高炉项目在生产过程中涉及大量的原料、燃料和工艺流程,同时伴随排放与治理、操作人员防护和环境监测等问题。
本文将围绕这些问题展开分析,以明确高炉项目的毒性危害。
1.原料与燃料高炉项目的主要原料包括铁矿石、焦炭和石灰石等。
其中,铁矿石是主要的含铁元素来源,焦炭则用于提供热量和还原剂,石灰石则用于降低炉渣的熔点。
这些原料和燃料的质量、数量和粒度等指标都会影响到高炉的运行效果和排放。
2.工艺流程高炉工艺流程包括原料准备、燃料添加、高炉操作、炉渣处理和煤气净化等环节。
在原料准备过程中,铁矿石、焦炭和石灰石等原料需要经过破碎、筛分和混合等处理;燃料添加环节则是在高炉内加入焦炭等燃料;高炉操作环节是通过控制温度、压力和气氛等因素来达到生产目的;炉渣处理环节是将炉渣进行分离和回收;煤气净化环节则是去除煤气中的有害成分并回收利用。
3.排放与治理高炉项目在生产过程中会产生大量的废气、废水和固体废弃物等污染物。
废气中主要包括二氧化碳、一氧化碳、二氧化硫和氮氧化物等有害气体,废水中则含有大量的悬浮物、酚类和氰化物等有害物质,固体废弃物则主要是炉渣和粉尘等。
针对这些污染物,目前主要的治理技术包括燃烧控制技术、废弃物处理技术和回收利用技术等。
然而,这些技术也存在一定的优缺点,例如燃烧控制技术可以减少二氧化碳排放,但会增加氮氧化物排放;废弃物处理技术可以有效去除有害物质,但处理成本较高;回收利用技术可以降低资源浪费,但回收率有待提高。
4.操作人员防护高炉项目的操作人员在生产过程中面临着多种有毒物质的风险,包括粉尘、有害气体和高温等。
为了减轻这些有毒物质对操作人员的影响,应采取一系列防护措施,例如提供个人防护装备、加强生产设施的维护保养、建立安全操作规程等。
此外,还应定期对操作人员进行健康检查和培训,以提高他们的自我保护意识和能力。
5.环境监测环境监测是高炉项目毒性危害管理的重要环节之一。
高炉本体系统危险有害因素分析(喷煤系统)

高炉本体系统危险有害因素分析(喷煤系统)高炉本体系统危险有害因素分析(喷煤系统)高炉喷煤系统是高炉本体系统的重要组成部分,其主要功能是将煤粉喷入高炉内,为高炉提供燃料和还原剂。
本文将从湿度、噪音和有害气体等方面对高炉喷煤系统存在的危险有害因素进行分析。
一、湿度1.湿度对设备的影响:高炉喷煤系统中的设备,如喷枪、输送管道等,在潮湿的环境中容易生锈、腐蚀,导致设备损坏,影响高炉的正常运行。
2.湿度对人员的影响:高炉喷煤系统在喷吹过程中会产生大量的水蒸气和粉尘,湿度过高可能导致操作人员呼吸困难、引发职业病等。
措施和建议:1.加强设备维护和保养,定期检查设备的锈蚀情况,及时采取防锈措施。
2.在操作室内安装除湿设备,保持适宜的湿度环境。
3.为操作人员提供相应的防护用品,如防尘口罩、防护眼镜等。
二、噪音1.噪音对人员健康的影响:高炉喷煤系统运行过程中产生的噪音较大,长期接触可能导致听力下降、头晕、失眠等健康问题。
2.噪音对工作的影响:噪音过大可能会干扰操作人员的注意力,导致操作失误或不当,从而引发事故。
措施和建议:1.采用低噪音设备,降低系统运行噪音。
2.对产生噪音较大的区域进行隔音处理,如安装隔音板、隔音罩等。
3.为操作人员提供耳塞等个人防护用品。
三、有害气体1.有害气体对人员健康的影响:高炉喷煤系统中产生的有害气体主要包括一氧化碳、二氧化硫、氮氧化物等,长期接触这些气体可能导致职业病,如中毒、呼吸道疾病等。
2.有害气体对工作的影响:有害气体会影响操作人员的视线和判断力,导致操作不当或失误,从而引发事故。
措施和建议:1.在操作室内安装气体检测仪,实时监测有害气体的浓度。
2.为操作人员提供呼吸防护用品,如空气呼吸器、防毒面具等。
3.对有害气体的排放进行处理和净化,以减少对环境和人员的影响。
4.加强操作人员的安全培训和教育,提高其对有害气体的认知和处理能力。
5.定期对高炉喷煤系统进行检修和维护,确保设备正常运行,减少有害气体的产生和排放。
- 1、下载文档前请自行甄别文档内容的完整性,平台不提供额外的编辑、内容补充、找答案等附加服务。
- 2、"仅部分预览"的文档,不可在线预览部分如存在完整性等问题,可反馈申请退款(可完整预览的文档不适用该条件!)。
- 3、如文档侵犯您的权益,请联系客服反馈,我们会尽快为您处理(人工客服工作时间:9:00-18:30)。
高炉废渣处理工作危险有害因素分析
渣处理系统包括粒化器、脱水器、溶渣流嘴及传动、水渣运输皮带系统、电动单梁起重机等主要设备。
其主要危险有害因素如下:
(1)机械伤害
a、在检查粒化头、转鼓、筛网、接受棚、格棚时,而没有到电磁站停电,可能造成人员误伤。
b、在清扫托轮、尾轮作业时,没有停电,可能造成人员误伤。
c、在更换托轮皮带时,没有停电,可能造成人员误伤。
(2)物体打击
水冲渣时,水渣飞溅,可能击伤附近工人。
(3)粉尘、噪声
在冲渣过程中,会产生一定噪声,如无正确防护措施,可能对工
人听力造成伤害;水渣在冷却过程中会产生大量的渣粒扬尘,如防护不当,可能对工人的健康造成危害。
(4)烫伤
由于水渣温度较高,工人不小心接触,可能导致工人烫伤。
(5)其它
由于水压较高,可能导致管道破裂,发生高压水伤人事故。
此外在高炉渣处理管网设备更换及处理过程中,事故水阀门因失电而自动开启,事故水迅速给上、下冲沟内作业极易发生工人被冲伤事故。