大型复合材料筒形结构自动铺带技术
基于自动铺带技术的复合材料结构件强度评估研究

基于自动铺带技术的复合材料结构件强度评估研究引言:复合材料是一种由两种或两种以上材料组成的复合体,具有优异的力学性能和工程应用潜力。
在航空航天、汽车工业、能源等领域中,复合材料的应用广泛,其中复合材料结构件的强度评估是一个关键问题。
本文旨在研究基于自动铺带技术的复合材料结构件强度评估方法与技术。
一、自动铺带技术的原理与应用自动铺带技术是一种将预浸复合材料纤维排列在设计规定位置的技术。
其主要原理是通过控制复合材料纤维与树脂的比例、面积密度和纤维层次,实现复合材料结构件的定向排列和强度提升。
自动铺带技术具有高效、高精度和低浪费等优点,因此在航空航天和汽车工业等领域广泛应用。
二、复合材料结构件强度评估的重要性复合材料结构件的强度评估是确保结构件在实际工况下能够承受预期载荷的关键。
在设计和制造复合材料结构件之前,强度评估能够提前预测结构件的破坏行为,指导结构优化和性能改进。
因此,开展复合材料结构件强度评估研究具有重要的理论和实践意义。
三、基于自动铺带技术的复合材料结构件强度评估方法1. 宏观力学模型基于自动铺带技术的复合材料结构件强度评估可以采用宏观力学模型进行。
通过建立合适的力学模型,将复合材料结构件视为多层板,进行强度评估和应力分析。
该方法能够较为准确地预测结构件的破坏行为和强度性能。
2. 细观力学模型细观力学模型是一种更加精细的强度评估方法,通过考虑复合材料纤维和树脂的微观结构与相互作用,建立复杂的力学模型。
该方法考虑了材料的非线性和破坏行为,可以提供更为精确的强度评估结果。
然而,由于模型的复杂性,该方法对计算资源和计算时间的要求较高。
3. 数值模拟与有限元分析数值模拟与有限元分析是一种较为常用的强度评估方法。
通过将复合材料结构件离散化为多个小单元,利用有限元方法对结构件进行力学分析和强度评估。
该方法能够较为准确地模拟复合材料结构件在复杂载荷下的响应,定量地评估结构件的强度。
四、复合材料结构件强度评估的关键因素1. 材料性能复合材料的性能对结构件的强度评估具有重要影响。
基于自动铺带技术的复合材料结构件热导性能研究

基于自动铺带技术的复合材料结构件热导性能研究随着科技的发展,复合材料在航空、汽车、船舶等领域中得到了广泛应用。
复合材料具有密度低、强度高、刚度高等优点,但其热导性能较差,这限制了其在高温环境下的应用。
因此,研究如何提高复合材料的热导性能,对于推动复合材料的应用具有重要意义。
自动铺带技术是一种常用于制造复合材料结构件的高效工艺。
它利用自动机械将多种纤维预浸料沿给定轮廓进行铺放,然后经过热固化等工艺步骤形成复合材料。
在进行复合材料结构件的热导性能研究时,我们可以从以下几个方面进行探索。
首先,我们可以研究复合材料中不同纤维材料对热导性能的影响。
复合材料通常由纤维和基体组成,其中纤维起到增强作用,而基体起到传导热量的作用。
通过选择合适的纤维材料,可以提高复合材料的热导率。
例如,石墨纤维具有较高的热导率,可以在复合材料中引入石墨纤维来提高整体的热导性能。
其次,我们可以研究复合材料中不同纤维体积含量对热导性能的影响。
纤维体积含量越高,纤维之间的接触面积越大,热量传导的通道也就越多,从而提高了复合材料的热导性能。
通过对不同纤维体积含量的复合材料进行热导率测试,可以确定最佳的纤维体积含量范围,以达到最优的热导性能。
此外,我们还可以研究复合材料中添加导热填料对热导性能的影响。
导热填料具有较好的导热性能,可以在复合材料中起到导热桥梁的作用,提高整体的热导率。
例如,铝粉、碳纳米管等导热填料可以添加到复合材料中,通过与纤维和基体的相互作用,引导热量的传递,提高复合材料的热导性能。
另外,研究复合材料的热导性能还可以从结构设计角度进行。
通过优化复合材料的结构,如纤维的排列方式、基体的厚度等,可以改变复合材料的热导性能。
例如,可以采用交错层压结构,使纤维沿不同方向排列,增加热传导路径,提高复合材料的热导性能。
除了上述几个方面的研究,我们还可以通过改变复合材料制备工艺来提高其热导性能。
例如,可以采用高温热固化工艺,提高复合材料的热固化度,减少热固化剂的残留,从而提高复合材料的热导率。
自动铺带技术在复合材料结构件热阻性能研究中的应用

自动铺带技术在复合材料结构件热阻性能研究中的应用引言热阻性能是复合材料结构件设计和制造中的一个重要指标。
在实际应用过程中,结构件的导热性能直接影响其热传导效率和稳定性。
因此,研究如何提高热阻性能,提高复合材料结构件的导热能力是一个热点和挑战。
近年来,自动铺带技术作为一种先进的制造方法,逐渐受到广泛关注和应用。
本文将探讨自动铺带技术在复合材料结构件热阻性能研究中的应用。
1. 自动铺带技术简介自动铺带技术是一种通过自动化设备将复合材料纤维连续铺放在模具上的制造方法。
通过控制铺带的角度、弯曲半径以及各层之间的纤维走向,可以实现复合材料结构件的复杂几何形状和优化力学性能。
自动铺带技术具有高效、精准和可重复性等优点,适用于大尺寸、高强度和复杂形状的结构件制造。
2. 复合材料结构件的热阻性能复合材料结构件的热阻性能是指材料在传导热传递过程中阻碍热流传递的能力。
熟知的热阻性能评估方法包括热传导率、热导率和热扩散系数等指标。
改善复合材料结构件的热阻性能对于提高其导热能力和应用范围具有重要意义。
3. 自动铺带技术在提高复合材料热阻性能中的应用自动铺带技术在提高复合材料结构件的热阻性能方面具有潜力。
首先,自动铺带技术可以实现纤维方向的优化设计,使得复合材料结构件的纤维走向和热传导方向一致,从而提高导热能力。
其次,自动铺带技术可以控制纤维之间的间隙和纤维层间的连续性,减少热阻损失。
此外,自动铺带技术还可以实现复合材料结构件的精细设计,通过合理布局纤维层的厚度和密度,进一步优化热传导路径,提高热传导效率。
4. 自动铺带技术在复合材料结构件热阻性能研究中的案例分析许多研究人员已经开始探索自动铺带技术在复合材料结构件热阻性能研究中的应用。
例如,一项研究使用自动铺带技术制备复合材料热管,通过控制不同铺带角度形成热流通道,并优化纤维层的布局,成功提高了热管的热传导性能。
另外,另一项研究使用自动铺带技术制备导热复合材料片,通过控制纤维层的厚度,优化了热传导路径,提高了导热性能。
自动铺带技术在复合材料加工中的误差分析与校正

自动铺带技术在复合材料加工中的误差分析与校正自动铺带技术是一种广泛应用于复合材料加工中的先进制造技术。
利用机器人系统,该技术能够实现快速、精确地将预浸料纤维带自动铺设在模具上,形成复合材料结构件。
然而,由于制造过程中存在各种误差,如机器人姿态误差、纤维带张力变化等,导致最终产品中可能存在不可忽视的误差。
因此,对自动铺带技术中的误差进行分析和校正是提高加工精度和质量的重要步骤。
首先,自动铺带技术中的误差可以分为几个方面。
机器人姿态误差是指由于控制系统不稳定或机械结构刚度不足等原因导致的机器人末端工具姿态与期望姿态之间的偏差。
纤维带张力误差则是由于张力传感器精度不高、张力控制系统不稳定等造成的纤维带张力变化不均匀。
此外,还存在其他误差源,如纤维带宽度和厚度的不均匀性、模具表面的几何变形等。
针对机器人姿态误差,可以通过提高控制系统的稳定性和增强机械结构的刚度来减小误差。
采用先进的机器视觉系统,能够实时获取铺带工具的位置和姿态信息,并与期望姿态进行比较,通过调整机器人控制指令来实现姿态误差的校正。
此外,引入自适应控制算法和传感器反馈控制系统,能够进一步提高铺带过程中的精度和稳定性。
对于纤维带张力误差,可以采用多传感器监测系统来实时监测纤维带的张力变化情况,并通过自适应控制算法来调整张力控制系统,使张力变化更加均匀稳定。
此外,对张力传感器进行校准和精度提高也是减小纤维带张力误差的关键措施。
除了机器人姿态误差和纤维带张力误差,纤维带宽度和厚度的不均匀性以及模具表面的几何变形也对最终产品的精度产生影响。
为了减小这些误差,可以在铺带前对纤维带进行预处理,通过切割和裁剪等方式将其调整为均匀宽度和厚度。
同时,在模具制造过程中,需要采用高精度的数控加工设备,并进行严格的质量控制,以减小模具表面的几何变形。
此外,误差分析与校正还需要借助先进的测量设备和方法。
利用三维扫描仪、光学显微镜等设备,能够实现对复合材料件的形状、尺寸和表面质量等的精确测量和分析。
自动铺带技术在复合材料制造中的应用探索
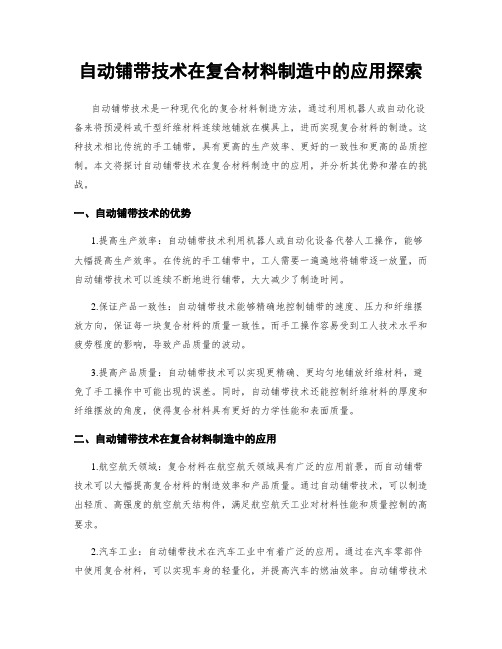
自动铺带技术在复合材料制造中的应用探索自动铺带技术是一种现代化的复合材料制造方法,通过利用机器人或自动化设备来将预浸料或干型纤维材料连续地铺放在模具上,进而实现复合材料的制造。
这种技术相比传统的手工铺带,具有更高的生产效率、更好的一致性和更高的品质控制。
本文将探讨自动铺带技术在复合材料制造中的应用,并分析其优势和潜在的挑战。
一、自动铺带技术的优势1.提高生产效率:自动铺带技术利用机器人或自动化设备代替人工操作,能够大幅提高生产效率。
在传统的手工铺带中,工人需要一遍遍地将铺带逐一放置,而自动铺带技术可以连续不断地进行铺带,大大减少了制造时间。
2.保证产品一致性:自动铺带技术能够精确地控制铺带的速度、压力和纤维摆放方向,保证每一块复合材料的质量一致性。
而手工操作容易受到工人技术水平和疲劳程度的影响,导致产品质量的波动。
3.提高产品质量:自动铺带技术可以实现更精确、更均匀地铺放纤维材料,避免了手工操作中可能出现的误差。
同时,自动铺带技术还能控制纤维材料的厚度和纤维摆放的角度,使得复合材料具有更好的力学性能和表面质量。
二、自动铺带技术在复合材料制造中的应用1.航空航天领域:复合材料在航空航天领域具有广泛的应用前景,而自动铺带技术可以大幅提高复合材料的制造效率和产品质量。
通过自动铺带技术,可以制造出轻质、高强度的航空航天结构件,满足航空航天工业对材料性能和质量控制的高要求。
2.汽车工业:自动铺带技术在汽车工业中有着广泛的应用。
通过在汽车零部件中使用复合材料,可以实现车身的轻量化,并提高汽车的燃油效率。
自动铺带技术可以大幅提高复合材料零部件的制造效率,满足汽车工业对大规模生产和高品质产品的需求。
3.建筑领域:自动铺带技术也可以应用于建筑领域的复合材料制造。
复合材料在建筑领域有着广泛的应用前景,可以用于制造建筑结构件、装饰材料等。
自动铺带技术可以提高建筑材料的生产效率,同时保证产品的一致性和质量,满足建筑行业对快速和高质量产品的需求。
自动铺带技术对复合材料构件性能的影响研究
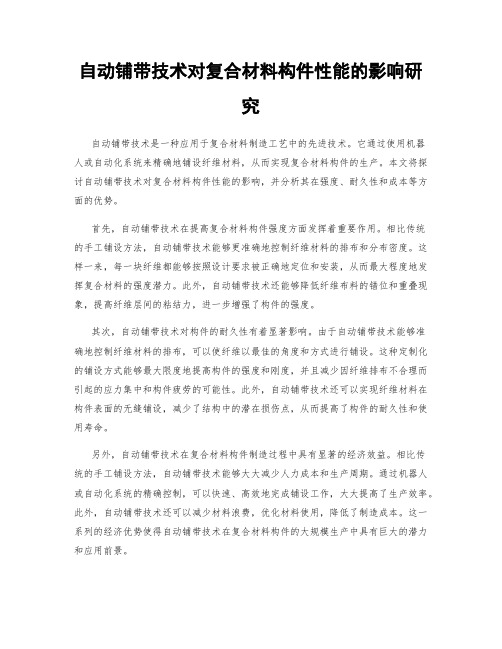
自动铺带技术对复合材料构件性能的影响研究自动铺带技术是一种应用于复合材料制造工艺中的先进技术。
它通过使用机器人或自动化系统来精确地铺设纤维材料,从而实现复合材料构件的生产。
本文将探讨自动铺带技术对复合材料构件性能的影响,并分析其在强度、耐久性和成本等方面的优势。
首先,自动铺带技术在提高复合材料构件强度方面发挥着重要作用。
相比传统的手工铺设方法,自动铺带技术能够更准确地控制纤维材料的排布和分布密度。
这样一来,每一块纤维都能够按照设计要求被正确地定位和安装,从而最大程度地发挥复合材料的强度潜力。
此外,自动铺带技术还能够降低纤维布料的错位和重叠现象,提高纤维层间的粘结力,进一步增强了构件的强度。
其次,自动铺带技术对构件的耐久性有着显著影响。
由于自动铺带技术能够准确地控制纤维材料的排布,可以使纤维以最佳的角度和方式进行铺设。
这种定制化的铺设方式能够最大限度地提高构件的强度和刚度,并且减少因纤维排布不合理而引起的应力集中和构件疲劳的可能性。
此外,自动铺带技术还可以实现纤维材料在构件表面的无缝铺设,减少了结构中的潜在损伤点,从而提高了构件的耐久性和使用寿命。
另外,自动铺带技术在复合材料构件制造过程中具有显著的经济效益。
相比传统的手工铺设方法,自动铺带技术能够大大减少人力成本和生产周期。
通过机器人或自动化系统的精确控制,可以快速、高效地完成铺设工作,大大提高了生产效率。
此外,自动铺带技术还可以减少材料浪费,优化材料使用,降低了制造成本。
这一系列的经济优势使得自动铺带技术在复合材料构件的大规模生产中具有巨大的潜力和应用前景。
除了上述优势,自动铺带技术还具有一些辅助性的影响。
例如,自动铺带技术能够实现对纤维材料的自动切割和粘接,减少了人工操作的繁琐程度,提高了生产效率。
同时,自动铺带技术还能够在铺设过程中实时监测和调节纤维材料的张力和排布,避免了因人为因素引起的误差,提高了构件的一致性和准确性。
这些辅助性的特点进一步加强了自动铺带技术在复合材料构件制造领域的竞争力和应用优势。
复合材料自动铺带技术应用及方案示例

度和铺叠位置、方向、角度的准确性, 发自动铺带设备,完成了小型铺带机
(2)该 设 备 在 铺 层 时 能 够 对 铺
从而避免了人为铺放产生的偏差,如 的研制,并应用于复合材料结构件 层路径进行手动和自动设置,自动功
产品出现缺陷的几率大、零件制造质 的研制;北京航空制造工程研究所 能具有最佳的铺层路径,每层带可在
虽 然 备采用龙门式结构,主要包括带装夹
国 内 自 动 和释放 ( 开卷 ) 系统、衬纸带回卷系
铺 带 技 术 统、带缺陷检测传感系统、带对中和
研 究 起 步 导向系统、切带系统、铺带和压实系
较 晚,但 在 统、工作区域安全系统、铺带监控系
技术研究和 统、带卷装卸系统、工装定位及自动
空客西班牙Illescas用铺带工艺制造的平尾、方向舵
自动铺带作为典型的增料加工 成型技术,其成型设备的制造技术涉 及机电装备技术、C A D / C A M 软件 技术和材料工艺技术等多个研究领
大飞机复合材料制造技术 Composite Manufacturing Technology for Large Commercial Jet
域,可实现:
许多型号飞机上。
量重复性差、质量分散性大,以及尺 与 Forest-Line 公司合作研制的大 ±90°之间采取任意角度和任意方
寸精度和铺放位置准确度不能满足 型复合材料自动铺带机的调试工作 向的铺放。
大尺寸、高精度零件制造的要求等问
题。采用复合材料自动铺带技术可
在提高质量的同时,大幅度地节省原
材料,降低制造成本。同时,由于可
MTM44-1/HTS(12K)-134-35%RW MTM44-1/E-IMS65-24K 194-32%RW
自动铺带技术研究现状
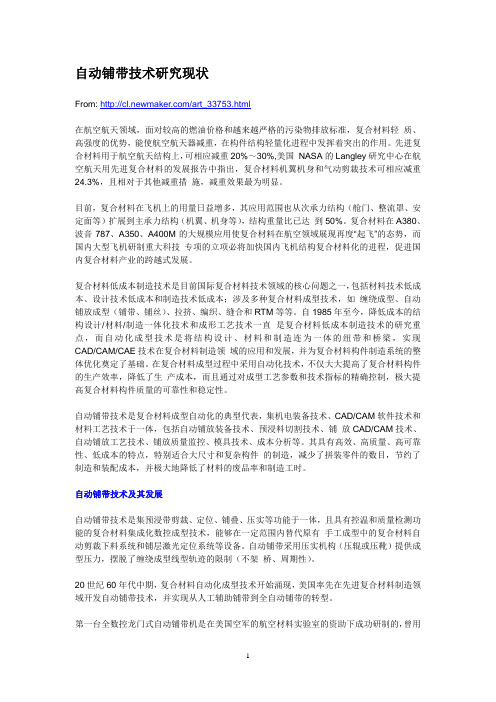
自动铺带技术研究现状From: /art_33753.html在航空航天领域,面对较高的燃油价格和越来越严格的污染物排放标准,复合材料轻质、高强度的优势,能使航空航天器减重,在构件结构轻量化进程中发挥着突出的作用。
先进复合材料用于航空航天结构上,可相应减重20%~30%,美国 NASA的Langley研究中心在航空航天用先进复合材料的发展报告中指出,复合材料机翼机身和气动剪裁技术可相应减重24.3%,且相对于其他减重措施,减重效果最为明显。
目前,复合材料在飞机上的用量日益增多,其应用范围也从次承力结构(舱门、整流罩、安定面等)扩展到主承力结构(机翼、机身等),结构重量比已达到50%。
复合材料在A380、波音787、A350、A400M的大规模应用使复合材料在航空领域展现再度“起飞”的态势,而国内大型飞机研制重大科技专项的立项必将加快国内飞机结构复合材料化的进程,促进国内复合材料产业的跨越式发展。
复合材料低成本制造技术是目前国际复合材料技术领域的核心问题之一,包括材料技术低成本、设计技术低成本和制造技术低成本;涉及多种复合材料成型技术,如缠绕成型、自动铺放成型(铺带、铺丝)、拉挤、编织、缝合和RTM等等。
自1985年至今,降低成本的结构设计/材料/制造一体化技术和成形工艺技术一直是复合材料低成本制造技术的研究重点,而自动化成型技术是将结构设计、材料和制造连为一体的纽带和桥梁,实现CAD/CAM/CAE技术在复合材料制造领域的应用和发展,并为复合材料构件制造系统的整体优化奠定了基础。
在复合材料成型过程中采用自动化技术,不仅大大提高了复合材料构件的生产效率,降低了生产成本,而且通过对成型工艺参数和技术指标的精确控制,极大提高复合材料构件质量的可靠性和稳定性。
自动铺带技术是复合材料成型自动化的典型代表,集机电装备技术、CAD/CAM软件技术和材料工艺技术于一体,包括自动铺放装备技术、预浸料切割技术、铺放CAD/CAM技术、自动铺放工艺技术、铺放质量监控、模具技术、成本分析等。
- 1、下载文档前请自行甄别文档内容的完整性,平台不提供额外的编辑、内容补充、找答案等附加服务。
- 2、"仅部分预览"的文档,不可在线预览部分如存在完整性等问题,可反馈申请退款(可完整预览的文档不适用该条件!)。
- 3、如文档侵犯您的权益,请联系客服反馈,我们会尽快为您处理(人工客服工作时间:9:00-18:30)。
·新材料新工艺·收稿日期:2010-09-06作者简介:张蕾,1982年出生,硕士,主要从事复合材料成型技术研究。
E -mail :vanbud@eyou.com大型复合材料筒形结构自动铺带技术张蕾王俊锋刘伟熊艳丽范佳(航天材料及工艺研究所,北京100076)文摘采用国产T300/605热熔法预浸料,对大型复合材料筒形结构自动铺带技术进行了研究。
通过对自动铺带角度的工艺优化,铺带角度进行微调,实现了复合材料筒形结构的满覆盖铺放。
在此基础上进行了大型复合材料筒形结构的自动铺带工艺试验,对自动铺带工艺试验件进行无损检测及取样性能测试。
结果表明:预浸料铺覆性良好,自动铺带成型的预浸带间隙或重叠≤1mm ,铺带角度与理论铺带角度偏差≤0.2ʎ。
试验件成型质量良好,自动铺带技术可以满足大型复合材料结构高质量成型需求。
关键词自动铺带,筒形结构,复合材料Automated Tape Placement in Large Composite Cylinder StructureZhang LeiWang JunfengLiu WeiXiong YanliFan Jia(Aerospace Research Institute of Materials &Processing Technology ,Beijing 100076)Abstract Automated tape placement in large cylinder structure was studied with domestic T300/605melting preparedprepreg.The ply angle was optimized to achieve the full-scale laying in large cylinder structure ,which would avoid the gap or overlaps.On the basis of the optimization ,the process experiment of large cylinder structure with automated tape placement was carried out and the result indicated that the adhesion of the prepreg tape was fit for automated tape placement.The gap or over-lap between the tapes were less than 1mm and the error of ply angle was less than 0.2ʎ.Nondestructive testing of the composite cylinder and test of mechanical and physical performance was carried out.The result showed that the property of the compositecylinder was eligible ,which indicated that automated tape placement satisfied the moulding of the large cylinder structure.Key words Automated tape placement ,Cylinder structure ,Composite 0引言自动铺带技术起源于20世纪60年代,第一台计算机全自动控制铺带机由General Dynamics 公司和Conrac 公司合作完成,用于铺放飞机的复合材料机翼部件[1]。
随着复合材料用量的增加,专业设备制造商开始研制自动铺带设备,专业化后形成自己的知识产权,如自适应压靴技术、辅助压辊技术、自适应跟踪技术、铺放质量在线检测与控制技术等,尤其在Natu-ral path 轨迹规划等软件技术方面有了长足进步。
自动铺带技术的应用,大大提高了复合材料结构件的成型效率和质量稳定性,减少了原材料的浪费[2],已经用于航空复合材料结构件制造,如机翼蒙皮、壁板等小曲率大型构件[3-5]。
近年来,自动铺带技术在飞机制造中所占比例越来越高,特别是B787,其复合材料结构质量约占50%,有将近80%采用自动铺带技术制造。
国内自动铺带技术的研究已开展数年,研究主要集中在设备技术方面,尚未见到在大型筒形结构件上应用的报道。
本文采用自行研制的热熔法预浸带和5坐标轴自动铺带设备,对大型复合材料筒形结构的自动铺放技术进行了研究。
1原材料与自动铺带系统1.1材料采用自行研制的国产T300/605热熔法预浸料厚度0.15mm ,可以根据需要分切为30 200mm 宽的预浸带。
1.2试验方法及设备1.2.1预浸料铺覆性试验借鉴GB /T2791—1995胶黏剂T 型剥离强度试验方法(挠性材料对挠性材料),使用电子万能试验机WD40025,测试预浸料的剥离强度。
试样制备:两块预浸料相同方向铺层,一侧预留5cm 用隔离材料隔开。
裁切尺寸为20cm ˑ2.5cm (试样长度沿纤维方向)。
1.2.2性能测试大型复合材料筒形结构取样按DqES279—97、DqES339—2001和GB3365—82进行挤压和层间剪切和孔隙率测试,用莱卡金相显微镜观察显微结构。
1.3自动铺带系统自动铺带系统由自动铺带机和CAD /CAM 软件两大部分构成(图1)。
自动铺带机运动轨迹控制部分包括5个自由度:芯模转动(C 轴)、铺带头小车移动(Z 轴)、铺带头伸臂(X 轴)、铺带头转动(A 轴)、铺带头升降(Y 轴)。
图1自动铺带系统构成Fig.1System of automated tape placement自动铺带头(图2)主要由预浸带切割系统、质量检测系统、预浸带输送系统、加热系统、压实系统等组成。
其中,预浸带切割系统采用精密超声切割装置,具有切割横向进给轴、切刀转动轴与送带进给轴三轴切割轨迹控制功能。
图2自动铺带头Fig.2Head of automated tape placement equipment2自动铺带工艺试验2.1预浸料的铺覆性预浸料的铺覆性对自动铺带工艺影响很大,良好的铺覆性可以有效提高铺带效率及质量。
国产T300/605热熔法预浸料的性能见表1。
表1国产T300/605热熔法预浸料性能Tab.1Quality of prepreg tape纤维面密度/g·m -2树脂含量/wt%挥发份含量/wt%165ʃ534ʃ3≤0.2目前国内还没有较为优异的预浸料铺覆性表征方法,通常采用定性的粘贴分离法和定量的T 型剥离强度法等来表征预浸料的铺覆性。
本文采用预浸料的剥离强度,并结合自动铺带试验来评价预浸带的铺覆性。
预浸料剥离强度试验结果见表2。
对国产T300/605预浸料进行自动铺带试验,预浸料贴合良好,铺带平整,衬纸衬膜完全揭除,没有粘辊现象发生,表明适合自动铺带工艺。
表2国产T300/605预浸料的剥离强度Tab.2Racking strength of T300/605试样号剥离强度/N·cm -11#2.92#2.13#3.24#3.15#3.16#3.07#2.88#3.29#3.110#2.5平均值2.92.2铺带角度优化自动铺带理论上能够实现任何角度铺层,但预浸带切割角β与铺带的可操作性有关,铺层角度α越大,β越小(图3)。
一般α为0ʎ 60ʎ。
图3铺层角度与预浸带切割角度Fig.3Tape angle and cutting angle in placement自动铺带时,为了实现筒体结构每层铺放整数条预浸带,避免铺放时预浸带出现间隙或搭接现象,需要对α进行微调。
随铺层厚度的增加,筒体结构自动铺带的α适当减小。
当铺层壁厚增加到一定程度,铺带角度与设计要求偏差较大时,在适当增加铺带条数的基础上对α进行微调,以实现α与设计角度接近。
α的求取过程如下。
α=arccosW ˑn2π[R +h ˑ(i -1)]式中,W 为预浸带的宽度,n 为每个铺层预浸带的条数,R 为筒段模具半径,h 为预浸带铺叠后的实际厚度,i 为铺带层数。
据此,可得到铺带机小车移动和芯模旋转的速度比值,并求得铺带头转角。
根据铺层角度和铺放轨迹的往复特性,可将铺层铺放角度分为:α,180ʎ+α或180ʎ-α。
假定筒段模具直径2m ,壁厚20mm ,预浸带单层厚度0.15mm ,计算优化后的角度见表3。
表3铺带条数、角度优化结果Tab.3Optimization of tape number and angle预浸带宽/mm 理论每层铺带数设计铺带角度/(ʎ)优化后铺带条数首层末层优化后铺带角度/(ʎ)首层末层10029.645303044.2545.3915044.445444545.5445.3910041.9042430.140.3515062.863640.14-0.102.3筒型结构自动铺带试验采用直径为1和2m 的两种筒形模具,进行0ʎ、45ʎ自动铺带试验。
预浸带宽度分别为75、100和150mm 。
自动铺带工艺流程见图4。
图4自动铺带流程Fig.4Flow chart of automated tape placement自动铺带头对刀是指铺带头由原点或轨迹上一点运动到铺带起始点;送料盘动作送料是指铺带头保持原有位置不变,送带并使预浸带移动一定距离之后,铺带头在铺带起始位置主压辊下压,随后铺带头由铺带起点移动到铺带终点;当铺带头运动到切割位置处时,保持铺带头位置不变,切刀转动预定角度切割预浸带,切割完毕后切刀回复到起始状态,在整个切割过程中,切刀需要将预浸带有效切断而保持背衬纸的连续。
自动铺带的试验见图5,结果见表4。
图5自动铺带试验Fig.5Experimentation of automated tape placement表4自动铺带试验结果Tab.4Results of automated tape placement模具直径/m 带宽/mm 弦高/mm 铺带质量预浸带间隙/mm 铺层角度误差/(ʎ)铺带效率/kg ·h -11755.6平整≤1≤0.2≤10.0110010平整≤1≤0.2≤13.5115023不可铺---2752.8平整≤1≤0.2≤5.5021005.0平整≤1≤0.2≤13.5215011平整≤1≤0.2≤20.0由表4看出,相同的带宽下,筒形模具直径越小,则预浸带在模具圆周方向上形成的弧线弦高越大。