失效模式分析
fmea失效模式分析案例
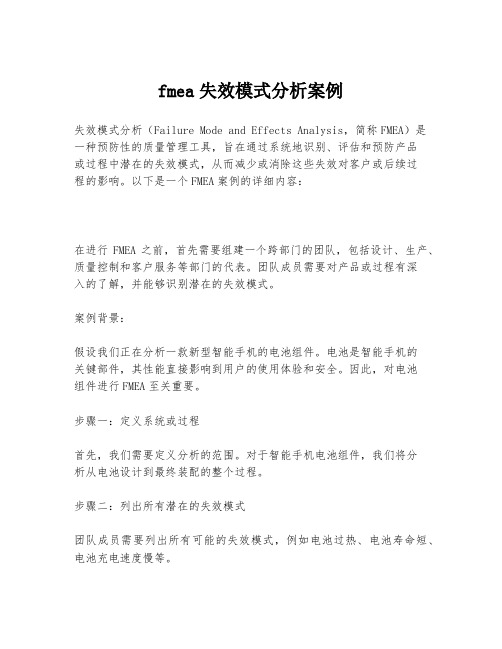
fmea失效模式分析案例失效模式分析(Failure Mode and Effects Analysis,简称FMEA)是一种预防性的质量管理工具,旨在通过系统地识别、评估和预防产品或过程中潜在的失效模式,从而减少或消除这些失效对客户或后续过程的影响。
以下是一个FMEA案例的详细内容:在进行FMEA之前,首先需要组建一个跨部门的团队,包括设计、生产、质量控制和客户服务等部门的代表。
团队成员需要对产品或过程有深入的了解,并能够识别潜在的失效模式。
案例背景:假设我们正在分析一款新型智能手机的电池组件。
电池是智能手机的关键部件,其性能直接影响到用户的使用体验和安全。
因此,对电池组件进行FMEA至关重要。
步骤一:定义系统或过程首先,我们需要定义分析的范围。
对于智能手机电池组件,我们将分析从电池设计到最终装配的整个过程。
步骤二:列出所有潜在的失效模式团队成员需要列出所有可能的失效模式,例如电池过热、电池寿命短、电池充电速度慢等。
步骤三:确定失效模式的潜在原因对于每个失效模式,团队需要确定可能导致该失效的原因。
例如,电池过热可能是由于电池设计不当、材料选择错误或制造过程中的缺陷。
步骤四:评估失效模式的严重性使用1到10的评分系统,团队需要评估每个失效模式的严重性。
评分越高,表示失效对客户或后续过程的影响越大。
步骤五:确定失效模式的潜在后果团队需要确定每个失效模式可能导致的后果。
例如,电池过热可能导致设备损坏或用户受伤。
步骤六:评估当前控制措施的有效性团队需要评估现有的控制措施是否能够有效预防或检测到潜在的失效模式。
例如,是否有严格的质量控制流程来检测电池的过热问题。
步骤七:计算风险优先数(RPN)风险优先数是通过将严重性(S)、发生概率(O)和检测难度(D)的评分相乘得到的。
RPN越高,表示该失效模式的风险越大。
步骤八:制定改进措施对于高RPN值的失效模式,团队需要制定改进措施。
这些措施可能包括重新设计电池、改进制造工艺或加强质量控制。
PCB行业之失效模式影响分析(FMEA)
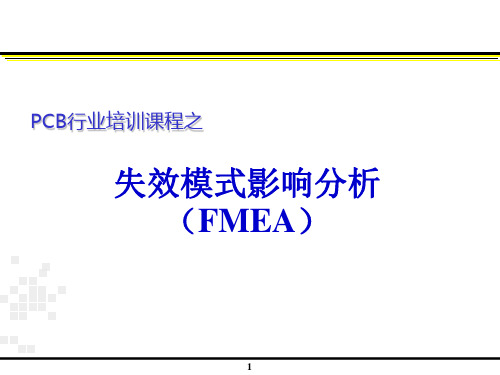
Finished Thickness (mils after
plating)
25.0 35.0 13.0
47.0
53.00% 53.50%
15.0 25.0 15.0
47.0
33.40%
Finished (S/M to S/M)
Custome r
requirem ent
13.0 35.0 25.0 295.0
80 - 199 26 - 80 1-25
Immediate Action Immediate Investigation Immediate Monitoring No Action
5/1000件(5000PPM) 2/1000件(2000PPM) 1/1000件(1000PPM) 0.5/1000件(500PPM) 0.1/1000件(100PPM) ≤0.05/1000件(50PPM)
Cpk / Ppk
<0.55 ≥0.55 ≥0.78 ≥0.86 ≥0.94 ≥1.00 ≥1.10 ≥1.20 ≥1.30 ≥1.67
7
何时结束
开始
设计FMEA
当产品功能及设计开始 时在整个设计未完成时
结束
当产品设计及图纸全部 得到确认可以实施时
当产品初期设计及有图
过程FMEA 纸时而生产辅助工具设
计未完成时
当产品彻底退出生产线 时
8
The DFMEA Form
Failure Mode and Effect Analysis (FMEA)
< 1 in 20,000
2
Low(发生几率低)
(< 50)
Occasional failures associated with similar designs
DFMEA失效模式分析报告-案例

DFMEA失效模式分析报告-案例1. 引言本文档旨在提供针对某一特定产品的DFMEA(设计失效模式及影响分析)报告。
该报告基于针对该产品的失效模式分析的结果,旨在识别和评估潜在的设计失效模式及其潜在影响。
2. 背景信息产品名称:(产品名称)产品型号:(产品型号)报告日期:(报告日期)3. 方法论在分析失效模式之前,我们采用以下方法进行了系统的DFMEA分析:1. 收集产品设计文档和相关技术资料;2. 召开团队会议,对产品进行全面的功能分析;3. 根据功能分析,确定可能存在的失效模式;4. 对每个失效模式进行评估,包括严重程度、频率和发现难度的评估;5. 提出各种可能的故障根本原因;6. 提出相应的纠正措施和预防措施,以减轻潜在的失效模式对产品造成的影响。
4. 失效模式分析及评估在DFMEA分析中,我们发现以下潜在的失效模式及其评估结果:4.1 失效模式1- 描述:(失效模式1的详细描述)- 严重程度:(对产品的影响程度评估,如高、中、低)- 频率:(失效模式发生的频率评估,如高、中、低)- 发现难度:(失效模式的可发现程度评估,如高、中、低)- 根本原因:(该失效模式发生的可能原因)4.1.1 纠正措施- 描述:(纠正该失效模式的措施)4.1.2 预防措施- 描述:(预防该失效模式的措施)4.2 失效模式2- 描述:(失效模式2的详细描述)- 严重程度:(对产品的影响程度评估,如高、中、低)- 频率:(失效模式发生的频率评估,如高、中、低)- 发现难度:(失效模式的可发现程度评估,如高、中、低)- 根本原因:(该失效模式发生的可能原因)4.2.1 纠正措施- 描述:(纠正该失效模式的措施)4.2.2 预防措施- 描述:(预防该失效模式的措施)......5. 结论本报告中,我们对产品的失效模式进行了深入的分析和评估。
通过识别各个失效模式并提出相应的纠正和预防措施,我们能够最大程度地减少潜在的设计失效,并提升产品的质量和可靠性。
过程失效模式与后果分析PFMEA

过程失效模式与后果分析PFMEA一、PFMEA的定义和目标PFMEA是一种系统性的过程分析方法,用于评估潜在的失效模式、错误或缺陷,以及这些失效模式或错误对产品质量和工作过程的潜在影响。
它的主要目标是提前识别和减轻过程中可能导致质量问题的潜在风险,以便采取适当的预防和纠正措施,提高产品质量和客户满意度。
二、PFMEA的基本概念和步骤1.风险识别:通过审核过程文档、历史数据、专家经验等方式,识别可能存在的失效模式。
2.评估失效的严重程度:对每个失效模式进行定量或定性评估,确定其对产品质量和安全性的潜在影响,此项评估需要专业知识和经验的支持。
3.识别可能的失效原因:找出导致失效发生的根本原因,可以通过使用逻辑树、鱼骨图、5W1H等工具进行分析。
4.评估失效的频度:对每个失效模式进行评估,确定其在过程中发生的概率或频次。
5.识别已有的控制措施和预防措施:列举已有的预防和控制措施,以评估其对失效模式的控制效果。
6.评估失效的检测度:确定失效模式是否可以在目前的检测过程中被发现。
7.进行风险评估:通过对失效模式的严重程度、频度和检测度进行组合评估,计算出风险优先级数(RPN)。
8.制定预防和纠正措施:根据风险优先级,确定应采取的预防和纠正措施,并将其确定为优先处理的问题。
9.追踪改进:追踪和记录已实施的预防和纠正措施,并评估其有效性。
三、PFMEA的优势和应用1.优势:PFMEA有助于企业识别和应对过程中的风险,提前预防可能导致质量问题的问题,并减少相关成本。
通过完善的PFMEA过程,可以提高产品质量、可靠性和客户满意度。
2.应用:PFMEA广泛应用于制造业,尤其在汽车、医疗器械和航空航天等高风险行业中。
它通常在新产品开发过程中进行,也可以应用于现有产品或过程的改进。
四、PFMEA存在的挑战和解决方法1.数据收集的困难:获取过程相关数据和知识的困难是PFMEA面临的主要挑战之一、解决方法包括培训和指导工作人员,建立数据收集和共享机制等。
PFMEA过程失效模式及后果分析

PFMEA过程失效模式及后果分析PFMEA(Process Failure Mode and Effects Analysis)过程失效模式及后果分析是一种常用的质量管理工具,用于评估和改进产品制造过程中的潜在问题和风险。
它旨在预测和预防可能导致产品失效的过程步骤。
1.确定过程步骤:首先,识别和定义产品制造过程中的每个关键步骤,包括原材料采购、加工、装配、测试等。
2.确定失效模式:对于每个过程步骤,识别可能导致失效的模式。
失效模式可以是设备故障、人为错误、材料质量问题等。
3.评估失效后果:对于每个失效模式,评估其可能导致的后果和影响。
后果可以涉及到产品质量问题、安全风险、客户满意度等。
4.定义风险优先级:根据失效模式的严重性、发生频率和检测能力,为每个失效模式分配一个风险优先级。
这可以帮助制定合理的风险控制策略。
5.制定改进计划:对于评估出的高优先级失效模式,制定相应的改进计划和控制措施。
这可能包括优化生产工艺、提供培训和教育、改进设备维护等。
6.实施和监控措施:执行改进计划,并监控其有效性。
定期对PFMEA进行更新,以反映过程改进和新的风险评估。
通过实施PFMEA,可以有效地识别和消除潜在的制造过程问题,并降低产品质量问题的风险。
下面以汽车制造业为例,具体分析PFMEA的应用。
在汽车制造过程中,每个制造步骤都可能存在潜在的失效模式。
例如,原材料采购环节可能存在材料质量问题的风险,加工环节可能存在操作错误或设备故障的风险,装配环节可能存在组装错误或安装不良的风险,测试环节可能存在测试不准确或设备故障的风险。
针对这些潜在问题,可以使用PFMEA来识别并评估其风险。
例如,在加工环节,识别可能的失效模式可能包括不正确的参数设置、设备故障、操作错误等。
然后,评估这些失效模式可能导致的后果和影响,如产品偏差、生产延误、设备故障等。
根据评估结果,确定失效模式的风险优先级,以便制定相应的改进计划和控制措施。
例如,对于评估为高风险的加工失效模式,可以采取以下改进措施:加强对操作员的培训和教育,确保他们正确操作设备和设置参数;增加设备维护和保养频率,以减少设备故障的风险;实施过程监控和自动化控制,以确保稳定的生产环境。
质量管理中的失效模式与影响分析
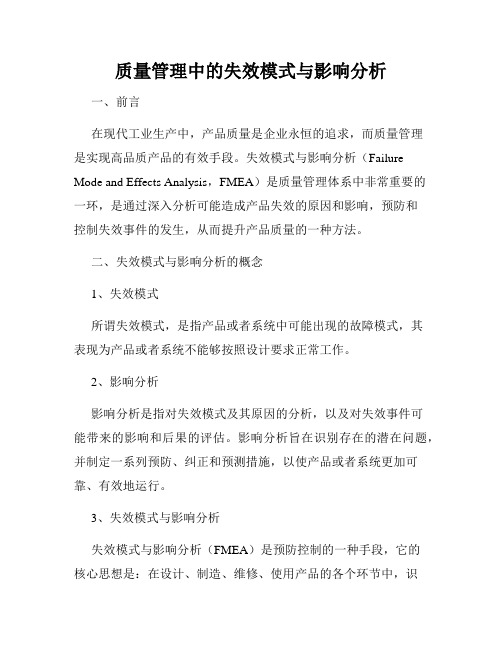
质量管理中的失效模式与影响分析一、前言在现代工业生产中,产品质量是企业永恒的追求,而质量管理是实现高品质产品的有效手段。
失效模式与影响分析(Failure Mode and Effects Analysis,FMEA)是质量管理体系中非常重要的一环,是通过深入分析可能造成产品失效的原因和影响,预防和控制失效事件的发生,从而提升产品质量的一种方法。
二、失效模式与影响分析的概念1、失效模式所谓失效模式,是指产品或者系统中可能出现的故障模式,其表现为产品或者系统不能够按照设计要求正常工作。
2、影响分析影响分析是指对失效模式及其原因的分析,以及对失效事件可能带来的影响和后果的评估。
影响分析旨在识别存在的潜在问题,并制定一系列预防、纠正和预测措施,以使产品或者系统更加可靠、有效地运行。
3、失效模式与影响分析失效模式与影响分析(FMEA)是预防控制的一种手段,它的核心思想是:在设计、制造、维修、使用产品的各个环节中,识别潜在失效模式、评估其可能影响和后果,并随后采取预防措施,从而提高产品的质量和可靠性。
三、失效模式与影响分析的步骤FMEA是一个基于团队合作的、有序的分析过程,主要分为以下步骤:1、确定需要分析的产品或者系统首先需要确定需要进行FMEA分析的产品或者系统,以及所涉及的物理和功能性方面。
2、制定失效模式制定失效模式是指对所选产品或者系统进行分析,并确定可能存在的失效模式。
在此过程中,需要考虑影响失效模式的所有因素,包括物理变形、设备磨损、操作不当、环境因素等。
3、评估失效模式的严重性在确定了失效模式后,需要评估失效模式的严重性,包括对生产和用户产生的影响等方面进行评估。
4、确定可能的原因在确定失效模式和严重性后,需要确定可能的原因,以及导致失败模式和严重性的根本原因。
5、确定纠正措施在确定了原因后,需要制定出一些纠正措施,以减少或消除可能造成失效事件的原因。
6、制定预防性措施最后,需要制定一系列预防性措施,以防止不良失效模式或原因继续存在。
SMT过程失效模式分析范例(PFMEA)
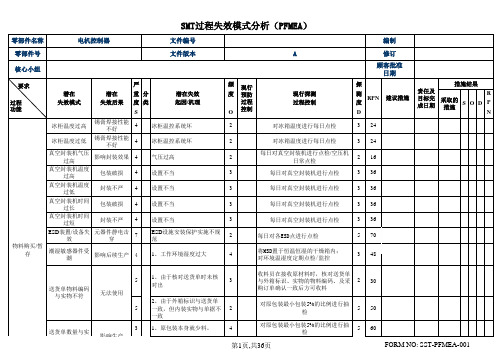
严频探潜在潜在重分潜在失效度现行探测测R 失效模式失效后果度类起因/机理过程控制度PSO DN冰柜温度过高锡膏焊接性能不好4冰柜温控系统坏2对冰箱温度进行每日点检324冰柜温度过低锡膏焊接性能不好4冰柜温控系统坏2对冰箱温度进行每日点检324真空封装机气压过高影响封装效果4气压过高2每日对真空封装机进行点检/空压机日常点检216真空封装机温度过高包装破损4设置不当3每日对真空封装机进行点检336真空封装机温度过低封装不严4设置不当3每日对真空封装机进行点检336真空封装机时间过长包装破损4设置不当3每日对真空封装机进行点检336真空封装机时间过短封装不严4设置不当3每日对真空封装机进行点检336ESD 装置/设备失效元器件静电击穿7ESD 设施安装保护实施不规范2每日对各ESD点进行点检570潮湿敏感器件受潮影响后续生产41、工作环境湿度过大4将MSD置于恒温恒湿的干燥箱内;对环境温湿度定期点检/监控34851、由于核对送货单时未核对出3收料员在接收原材料时,核对送货单与外箱标识、实物的物料编码、及采购订单确认一致后方可收料23052、由于外箱标识与送货单一致,但内装实物与单据不一致2对原包装最小包装5%的比例进行抽检55031、原包装本身就少料。
4对原包装最小包装5%的比例进行抽检560责任及目标完成日期建议措施措施结果DS O 现行预防过程控制无法使用影响生产送货单数量与实物不符物料购买/暂存送货单物料编码与实物不符文件版本A修订SMT过程失效模式分析(PFMEA)零部件名称电机控制器文件编号编制RPN 采取的措施核心小组顾客批准日期零部件号过程功能要求第1页,共36页FORM NO: SST-PFMEA-001等文件出错用错料第3页,共36页FORM NO: SST-PFMEA-00131、烘烤人员不清楚温度标准4培训《MSD管制办法》33632、MSD的标识不清晰2将《SMT MSD干燥记录表》记录清楚21233、未生产而长时间放置3长时间放置的MSD实行真空包装21831、烘烤人员不清楚厚度/间距标准4培训《PCB、IC烘烤作业指导书》33632、烘烤人员因“烤箱空间”不够而随意加厚、加密4严格执行《PCB、IC烘烤作业指导书》33631、烘烤人员不清楚裸露时间标准4培训《PCB、IC烘烤作业指导书》33632、烘烤人员未执行“先出先消耗”的原则3执行“先出先消耗”原则21841、空调性能下降5及时反馈空调维修员48042、空调性能下降,该区管理员未及时点检5将裸露MSD置于恒温恒湿的干燥箱内;对环境温湿度定期点检/监控24041、冰箱冷藏性能下降3及时反馈冰箱维修员33642、锡膏管理员不清楚标准3培训标准:锡膏存储温度在0~10℃22443、锡膏管理员未及时监控4点检(1次/2小时)控制在0~10℃23241、锡膏管理员不清楚标准3培训标准:锡膏存储温度在0~10℃22442、锡膏管理员未及时监控4点检(1次/2小时)控制在0~10℃23241、锡膏进料后的有效期短4检验出厂的瓶身标签:有效期≥6月34842、未执行“先进先出”3标识清晰,执行“先进先出”,严格控制锡膏存储期在6个月内22441、锡膏管理员不清楚标准4培训标准:室温下锡膏回温时间≥4H 23242、管理员控制的起止回温时间不清晰4利用《锡膏使用标识卡》严格记录/管控34843、因"急"而超前使用4“急”则须提前解冻34841、锡膏管理员不清楚标准4培训标准:室温下锡膏回温时间≥4H 23242、回温的起止时间标识不清楚4利用《锡膏使用标识卡》严格记录/管控34843、停产时,未将已解冻品及时回冻4《锡膏使用标识卡》标识清晰,工作环境中未开封放置不能超过24小时232烧录器电压不稳定程序拷贝时出错,影响功能5220V输入电压不稳定2每日对其进行点检44051、硬件、软件运行有误2每日对其画面显示状况进行确认33052、作业员违规操作3按照“PI-150”作业,禁止多余操作345拷贝电脑运行不正常程序拷贝时出错,影响功能锡膏活性下降,导致印刷性能下降锡膏回温解冻时间过长锡膏存储期限过长PCB、IC等返潮,影响焊接品质开封/烘烤后裸露时间过长PCB、IC等返潮,影响焊接品质该区环境湿度过大锡膏活性下降锡膏存储温度过低PCB、IC等湿度仍过大,影响焊接品质锡膏存储温度过高缩短锡膏存储周期,影响焊接品质摆放厚度过厚、间距过小PCB、IC等反潮,影响焊接品质MSD于干燥箱内的时间过长备/领出锡膏变质,影响焊接品质锡膏吸水引起锡珠\气泡\炸锡锡膏回温解冻时间过短第5页,共36页FORM NO: SST-PFMEA-00131、拷贝槽的拷贝脚弹性不够3每日对拷贝脚的完好性进行点检32732、IC的放置不到位3保证作业员将IC脚充分接触到拷贝槽的底部32733、IC脚氧化2发现时,及时反馈IQC63651、软件确认书或效验和或备录忘或ECN/BOM等文件出3对每个工单的首次软件拷贝的IC要求物料房拉长进行首件确认46052、用错软件5对每个工单的首次软件拷贝的IC要求物料房拉长进行首件确认37553、用错IC5对每个工单的首次软件拷贝的IC要求物料房拉长进行首件确认,并使用BOM/ECN核对所拷贝IC实物的正确性37551、作业员不能识别辅料型号/用途3对作业员培训《辅料型号、使用对照表》34552、作业员疏忽3领辅料时,实行两人确认345ESD设施失效静电敏感器件被击穿,功能丢失7ESD设施的安装或保护或实施不规范2每日对各ESD点进行点检57031、作业指导书未制作4及时制作33632、丢失/未悬挂4每日对各工位作业指导书进行点检33631、作业员不能识别Feeder类型2对作业员培训各类机器、Feeder类型的识别方法31832、作业员未掌握物料类型与Feeder类型的匹配方法2对作业员培训各Feeder类型与物料类型匹配的方法31833、作业员疏忽3上料/换料后,对所上Feeder与物料的匹配情况进行两人核对、确认32751、站位表的制作出错31、站位表制作后,实行两人确认2、站位表在上线使用之前,技术员必须用BOM核对站位表是否正确,交助工签名后方可使用34552、拿错站位表4拉长依据客户、机型、程序名领取站位表,与技术员实行两人确认36051、站位表出错3拉长依据客户、机型、程序名领取站位表,与技术员实行两人确认345拷贝槽与IC 的接触不良作业指导书不全不按标准/流程作业,流出不良程序不能拷入,影响功能生产辅料发错用错辅料拷错程序,影响功能/换错物料软件确认书,效验和,备录忘ECN,BOM未核对物料上线物料抛损、影响贴片质量Feeder(类型)使用出错错料站 位 表出错第6页,共36页FORM NO: SST-PFMEA-001清晰第8页,共36页FORM NO: SST-PFMEA-001出。
失效模式及影响分析

失效模式及影响分析失效模式及影响分析(Failure mode and effects analysis,简称FMEA)是一种用于系统故障预防和可靠性改进的方法。
通过对系统的各个组成部分及其可能的失效模式和影响进行分析,能够帮助识别和消除潜在的故障点,提高系统的可靠性和安全性。
失效模式(Failure mode)是指系统、产品或组件在正常条件下未能按预期执行其功能或要求的方式,即失效的特定表现形式。
常见的失效模式包括:停止工作、性能下降、产生误差、漏水/泄露、短路、断裂等。
影响(Effects)是指失效模式对系统、用户、环境或企业造成的潜在危害或负面影响。
影响的级别可以从事故、严重故障、中度故障、轻微故障、降低可靠性等方面来评估。
FMEA通过对失效模式和其影响进行分析,可以进行以下几个方面的评估:1. 严重性评估(Severity Evaluation):根据失效模式对系统、用户或环境的影响程度,评估其严重性级别。
将影响分为高、中、低等级,并确定具体的损失程度。
2. 发生频率评估(Occurrence Evaluation):根据失效模式发生的概率或频率,评估其出现的可能性。
通过对设备或系统历史数据的统计分析,可确定每年失效次数或概率。
3. 检测能力评估(Detection Evaluation):根据可用的检测手段和方法,评估对失效模式的检测能力。
检测能力可以通过验证和验证手段的准确性和可靠性来评估。
通过对这三个因素进行综合评价,可以计算出风险优先数(Risk Priority Number, RPN)。
RPN是一个综合评估指标,用于确定优先改进的失效模式。
FMEA的主要目的是帮助预防失效,减少系统故障,并且在设计或改进产品或过程时识别并降低风险。
通过FMEA分析,可以及早发现和解决潜在问题,提高系统可靠性,减少维修和停机时间,降低成本和提高用户满意度。
FMEA可以应用于各个领域,如制造业、软件开发、航空航天等。
- 1、下载文档前请自行甄别文档内容的完整性,平台不提供额外的编辑、内容补充、找答案等附加服务。
- 2、"仅部分预览"的文档,不可在线预览部分如存在完整性等问题,可反馈申请退款(可完整预览的文档不适用该条件!)。
- 3、如文档侵犯您的权益,请联系客服反馈,我们会尽快为您处理(人工客服工作时间:9:00-18:30)。
失效模式分析(FMEA)控制程序
1.0 [目的]
通过对产品在设计及生产过程所采取的分析评估,消除存在或潜在的异常原因.
2.0 [适用范围]
适用于产品设计阶段及制造过程阶段使用.
3.0 [定义]
3.1 严重度(S):潜在失效模式发生时对下一工序或产品影响后果的严重程度的评
鉴指标.
3.2 发生机率(O):实际上发生和造成失效模式之原因的机率.
3.3 风险优先数:是指严重度(S),发生机率(O),难检度(D)的乘积, 是用来评定事项
处理的优先级.
3.4 顾客:在本程序中,一般是指"最终使用者",但也可以是后续的或下一制造或装
配工序,以及服务工作.
4.0 [职责]
4.1 FMEA小组:由研发中心.工程部等相关人员组成
4.2 品管部FMEA成员:选定产品和工序、成效追踪评估及整理
4.3 工程部FMEA成员:失效模式效应分析、技术改善对策之提出
4.4 制造部FMEA成员:管理改善对策之提出、改善措施之执行
4.5 研发中心FMEA成员: 产品失效模式效应分析,产品特性改善对策之提出
注:上述仅为部分事项之主办人员权责划分,但仍需其它部门成员共同商讨定案
5.0 [程序内容]
5.1 FMEA作业过程
5.1.1 成立FMEA小组
1). 由跨功能小组组成FMEA小组,成员以5-9人组成最佳.
2). 成员必需具备下述条件:
a. 有确定措施或对策之权力;
b. 有执行任务之能力;
c. 有6个月以上之实际工作经验.
5.1.2 FMEA的主题选定
1).在《产品质量先期策划和控制计划程序》的《控制计划 (QC工程表)》中, 跨
功能小组需确定需要做PFMEA的机种.
5.1.3 FMEA编号:记录PFMEA文件的编号,以便查询,
5.1.4 确定项目名称:确定所分析的系统、子系统或零件的过程特性、名称、编号.
5.1.5 责任部门确定:确定失效模式产生的部门和小组.
5.1.6 确定权责人:填入负责准备FMEA工作的负责人.
5.1.7 确定项目:填入产品编号.
5.1.8 记录制作日期:填入编制FMEA原始稿的整理日期及最新修定的日期.
5.1.9 填入FMEA小组成员:将参加FMEA小组的成员名单予以记录.
5.1.10 确定工序和产品特性与功能
1).简单描述被分析的过程或工序产品特性,并尽可能简单地说明该工艺过程或工
序的目的和该该产品特性和功能的目的.
2).如果工序过程产品特性和功能包括许多具有不同失效模式,那么可以把这些工
序和产品特性及功能作为独立的过程列出.
5.1.11 确定失效模式:根据特定的工序和产品特性和功能,列出每一个不良现象.
5.1.12 分析失效后果:应依据顾客或下一工序和产品特性及功能可能注意到的或
经历的情况来描述失效的后果.
5.1.13 评定严重度:依失效的后果评定严重度 ,评定方式请参见《潜在的失效模式
及后果分析配分表》(附件一).
5.1.14 失效起因分析:针对每一个潜在的失效模式在尽可能广的范围内根《统计
技术程序》分析据需要依并列出每个可以想到的失效起因.
5.1.15 评定发生机率:依失效起因评定发生机率, 评定方式请参见《潜在的失效模
式及后果分配分表》(附件一).
5.1.16 控制方法描述:对尽可能阻止失效模式的发生或者探测将发生的失效模式
的控制的描述
5.1.17 评定难检度:评定在下一个或后续工艺前或零部件离开制造或装配工位和
产品特性实现之前,利用控制方法找出缺陷存在的可能性, 评定方式请参见《潜在
的失效模式及后果分析配分表》(附件一).
5.1.18 计算风险优先数:
1). 风险优先数(RPN)=严重度(S)*发生机率(O)*难检度(D).
2). 通过风险优先数以体现及选择其需优先改善的失效模式.
5.1.19 优先改善项目选定
1). 当失效模式按RPN值排出先后顺序后,应首先对排列在最前面的事和最关键
的项目采取纠正措施,在一般实践中, 不管RPN值大小如何,当严重度高(S≧3)时,
就应予以特别注意.
2). 需要改善时提出建议措施:
A. 针对失效模式提出相应的纠正措施
B. 若失效的根本起因不详,则建议采用的措施应通过《统计技术程序》的相应手
法展开确定
注. 当不需要改善时处理结果如下:如对某一特定原因无建议措施,那么就在措施
栏填“无”予以明确
5.1.20 建议措施责任确定:确定负责建议措施的组员和个人,以及预计完成的日期.
5.1.21 效果确认:当明确了采取的措施后,计算并记录纠正后的发生机率、严重度
和难检度,计算并记录纠正后的RPN值.
A.PRN值减少了,由跨功能小组负责人核准.
B.PRN值没有减少,分析原因如属改善措施无效需重新分析,返回5.2.0重新操作;
如属意外的机遇则立即纠正通过,同样转入由跨功能小组负责人核准.
5.1.22 纳入标准化:由责任单位将有效的措施纳入工程图、作业指导书或其他标
准文件;
5.2 对FMEA的一般认识.
5.2.1 在最初的潜在过程FMEA(PFMEA)中,希望负责过程的主管能够直接地、主
动地联系所有相关部门,这些部门包括但不限于工程、生产、品管等部门,FMEA
应成为促进不同部门之间充分交换意见的催化剂,从而提高整全集体的工作水平;
5.2.2 PFMEA是一份动态文件, 应在生产或过程可行性分析阶段开始,而且要考
虑以单个零件到总成的所有制造工序.
5.2.3 DFMEA假定所设计的产品会满足设计要求,因设计缺限所产生失效模式不
包含在PFMEA中
5.2.4 PFMEA并不一定是依靠改变产品设计来克服过程缺陷的,但它要考虑与计
划的制造厂装配过程有关的产品设计特性参数,以便最大限度地保证产品能够满
足顾客的要求和期望;
5.2.5 PFMEA也有助于新机器设备的开发,其方法是一样的,只是应将所设计的机
器设备当作一种产品来考虑.在确定了潜在的失效模式之后,就可以着手采取纠正
措施消除潜在失效模式或不断减少它们发生的可能性;
6.0 [流程图]
无
7.0 [记录]
《PFMEA潜在的失效模式及后果分析》《DFMEA潜在的失效模式及后果分析》
8.0 [相关文件]
《潜在的失效模式及后果分析配分表》(附件一)
《潜在的失效模式及后果分析记录作业说明书》
《产品质量先期策划和控制计划程序》《统计技术作业指导书》