潜在失效模式及后果分析
设计潜在失效模式及后果分析
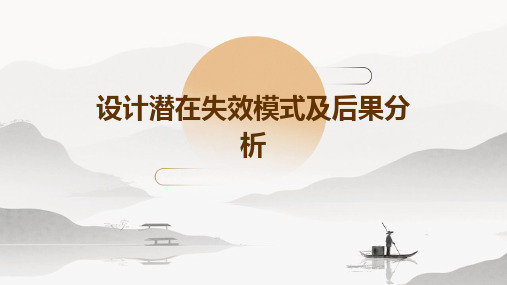
下一步行动计划
针对识别出的潜在失效模式, 制定相应的预防和缓解措施, 降低风险。
定期进行设计潜在失效模式 及后果分析复盘,不断完善 和优化产品设计。
持续监测和跟踪潜在失效模 式的改进情况,确保措施的 有效性。
FTA(故障树分析)
总结词
FTA是一种自上而下的逻辑分析方法,用于识别系统故障的原因,并确定导致 故障的最小割集。
详细描述
FTA通过构建故障树来分析系统故障的原因。故障树从顶事件(系统故障)开始, 逐级向下分析导致顶事件发生的所有可能原因。通过FTA,可以识别出导致系统 故障的关键因素,并确定预防措施和改进方案。
05
04
3. 热伤害
过热的产品可能烫伤使用者。
性能后果
总结词
产品的性能是用户最直接关注 的方面,潜在失效模式可能导
致产品性能下降或失效。
1. 功能丧失
产品部分或全部功能无法正常 工作,如电子预期标准,如 电池续航时间缩短、设备运行 速度变慢等。
3. 疲劳失效
产品因长时间使用或频繁使用而导致 的性能下降或损坏。
05
风险优先级评估
风险矩阵
风险矩阵是一种评估风险优先级的方 法,通过将风险发生的可能性和后果 的严重程度进行量化,将风险划分为 不同的等级。
在风险矩阵中,横轴表示风险发生的 可能性,纵轴表示后果的严重程度, 根据这两个维度的值,可以将风险划 分为高、中、低三个优先级。
软件可能存在安全漏洞,如未授权访问、恶意攻击等,威胁用户隐 私和系统安全。
人因设计潜在失效模式
操作失误
人为操作可能导致系统误动作或错误输入,影响系统 正常运行。
潜在失效模式及后果分析
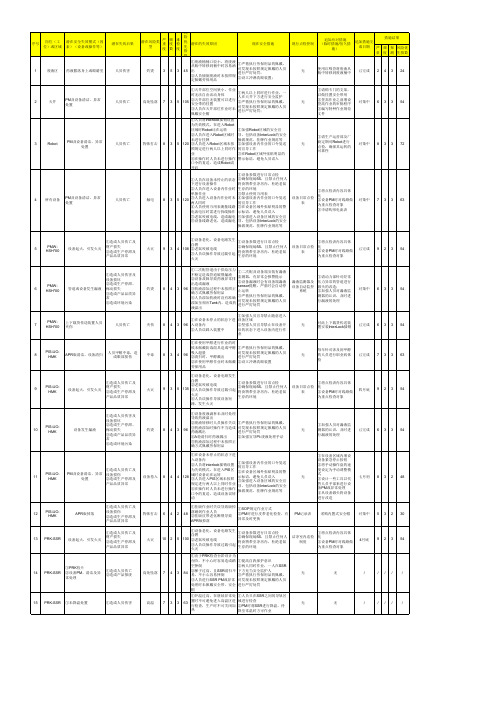
无
使用红吸管将废液从 瓶中转移到废液桶中
已完成
243
24
人员伤亡 人员伤亡 人员伤亡
高处坠落
7
3
5
105
①天井部位空间狭小,作业 时无法自由活动身体 ②天井部位无装置可以进行 安全带的挂置 ③人员在天井部位作业时未 佩戴安全帽
①两人以上同时进行作业,一 人在天井下方进行安全监护 ②严格执行劳保用品的佩戴, 对发现未按照规定佩戴的人员 进行严厉处罚;
帽
无
/
15 PRK-SSR ①未降温处置
①炉温过高,在继续异常处 ①人员只在SSR之间的导轨区
①造成人员伤害
高温
7
3
3
63
置时不可避免进入高温区进 域进行检查 行检查,生产时不可关闭加 ②PM时将SSR进行降温,待
无
热
降至常温时方可作业
无
/
9 2 3 54 /// / /// /
导,包括设备InterLock的安全 操做规范、挂牌作业规范等
动
①在设备区域内增设
设备紧急停止按钮
②将手动操作盘的速
度设定为手动调整模
无
式 ③设计一些工具以代
七月初
832
48
替人员手部来进行设
备PM或异常处理
④从设备源头将设备
进行改造
12
PIS-IJOHMK
APR版掉落
①造成人员伤亡及 设备损伤 ②造成生产停滞及 产品品质异常
药液溅出
进行严厉处罚
④A轮清扫时药液溅出
②加强宣导PI-废液处理手法
⑤药液添加过程中未按照正
确方式佩戴劳保用品
①加强人员对漏液监
无
测器的认识,及时进 已完成 6 3 3 54
潜在的失效模式与后果分析(FMEA)精选全文
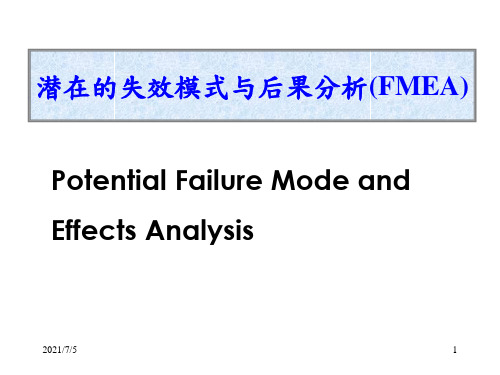
太短功能 :支撑架总成生产方法 (焊接)潜在失效模式 :
设计目标骑乘至少3000小时
不需保养, 及10000
小时的骑乘寿命适应99.5%男性成人
舒适的骑乘其它功能 :容易骑用潜在失效模式驾驶困难踩踏困难功能 :提供可靠的交通潜在失效模式链条经常损坏轮胎经常需要保养功能:提供舒适的交通潜在失效模式座椅位置令骑乘者
2021/7/5
19
FMEA的实施
FMA(失效模式分析)
FMEA(潜在失效模式及后果分析)
失效已经产生
失效还未产生,可能发生,但不是一定要发生
核心:纠正
核心:预防
诊断已知的失效
评估风险和潜在失效模式的影响开始于产品设计和工艺开发活动之前
指引开发和生产
指引贯穿整个产品周期
FMA:Failure Mode Analysis
2021/7/5
18
FMEA的实施
●及时性●它是一个事前的行为,而不是一个事后的行为。●事先花时间很好地进行综合的FMEA分析,能够容易、低成本地对产品或过程进行修改,从而减轻事后修改的危机。●FMEA能够减少或消除因修改而带来更大的机会。适当地应用FMEA是一个相互作用的过程,永无止境。● FMEA是一个动态的文件。● FMA是一种事后行为,是对产品/过程已经发生的失效 模式分析其产生的原因,评估其后果采取纠正措施的一种活动。●类似项目的FMA是FMEA的重要的输入参考资料。
2021/7/5
22
良好FMEA之具备事项
FMEA是早期预防失效及错误发生的最重要且最有效的方法之一。一个良好的FMEA必须具备: 1. 确认已知及潜在失效模式 2. 确认每一失效模式的后果和原因 3. 依据风险顺序(严重度、频度及探测度)采取措施 4. 提供问题改正行动及跟催
潜在失效模式和后果分析FMEA
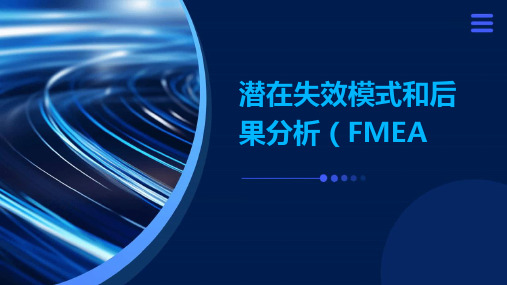
制定优先改进措施
01
根据RPN值评估结果,确定需要优先改进的潜在失效模式。
02
制定针对性的改进措施,包括设计优化、工艺改进、检验加强
等。
制定改进措施的实施计划和时间表,确保改进措施的有效执行
03 。
跟踪改进措施的实施情况
要点二
详细描述
在汽车行业中,FMEA被广泛应用于产品设计、生产和质 量控制过程中。例如,在发动机设计阶段,FMEA分析可 能识别出发动机气缸密封圈的潜在失效模式,如密封圈材 料疲劳或安装不当。这种失效可能导致发动机性能下降或 漏油,影响车辆的安全性和可靠性。通过FMEA分析,设 计团队可以采取措施优化密封圈材料和安装工艺,降低失 效风险。
服务流程改进
在服务流程中应用FMEA,有助于发 现和改进可能导致服务失败的潜在问
题。
生产过程控制
在生产过程中应用FMEA,有助于识 别和解决可能导致生产不合格品的潜 在问题。
维修和维护
在产品维修和维护过程中应用FMEA ,有助于预防和解决可能导致产品失 效的潜在问题。
02
CATALOGUE
FMEA分析过程
详细描述
潜在失效模式是指产品或过程中可能发生的故障或性能下降。通过分析历史数据、类似产品的失效模式以及专家 意见等途径,可以识别出潜在的失效模式。
确定失效影响
总结词
评估潜在失效模式对系统、产品或过程 的影响,有助于了解失效的严重程度。
VS
详细描述
失效影响是指潜在失效模式发生时,对系 统、产品或过程性能的影响程度。通过评 估失效影响,可以了解失效的严重程度, 为后续的风险评估提供依据。
潜在的失效模式及后果分析
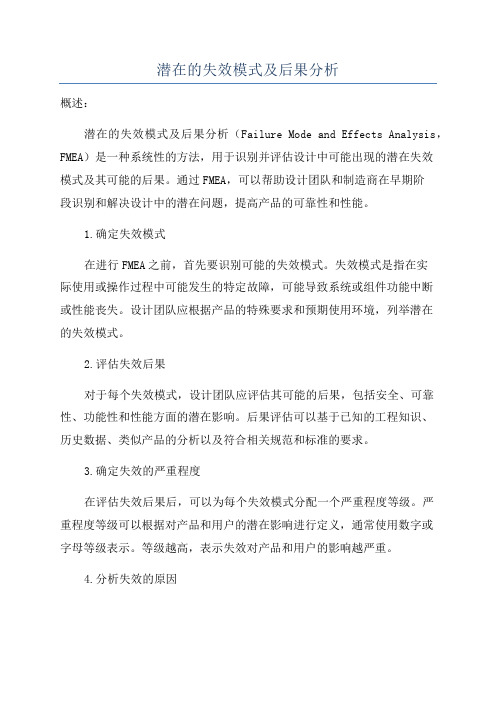
潜在的失效模式及后果分析概述:潜在的失效模式及后果分析(Failure Mode and Effects Analysis,FMEA)是一种系统性的方法,用于识别并评估设计中可能出现的潜在失效模式及其可能的后果。
通过FMEA,可以帮助设计团队和制造商在早期阶段识别和解决设计中的潜在问题,提高产品的可靠性和性能。
1.确定失效模式在进行FMEA之前,首先要识别可能的失效模式。
失效模式是指在实际使用或操作过程中可能发生的特定故障,可能导致系统或组件功能中断或性能丧失。
设计团队应根据产品的特殊要求和预期使用环境,列举潜在的失效模式。
2.评估失效后果对于每个失效模式,设计团队应评估其可能的后果,包括安全、可靠性、功能性和性能方面的潜在影响。
后果评估可以基于已知的工程知识、历史数据、类似产品的分析以及符合相关规范和标准的要求。
3.确定失效的严重程度在评估失效后果后,可以为每个失效模式分配一个严重程度等级。
严重程度等级可以根据对产品和用户的潜在影响进行定义,通常使用数字或字母等级表示。
等级越高,表示失效对产品和用户的影响越严重。
4.分析失效的原因在确定了可能的失效模式和其严重程度后,设计团队应分析失效的原因和潜在根本原因。
通过这一步骤,可以识别导致失效模式的设计、制造或其他因素,并采取相应的措施来预防失效的发生。
5.确定控制措施对于确定的失效模式和其原因,设计团队应确定适用的控制措施,以减少或消除失效的可能性。
控制措施可以包括设计变更、工艺改进、材料选择、测试和验证等。
6.重新评估风险在采取控制措施后,设计团队应重新评估失效模式的严重程度和发生概率。
这可以帮助团队确认控制措施的有效性,并通过进一步的优化来减少潜在的风险。
通过以上步骤,设计团队可以系统地识别并评估设计中的潜在失效模式及其可能的后果。
这种方法有助于提早发现和解决设计问题,减少不必要的成本和时间浪费,改善产品的质量和性能。
FMEA是一个灵活的工具,可以根据不同的应用领域和需求进行定制和适应。
潜在的失效模式及后果分析(FMEA)
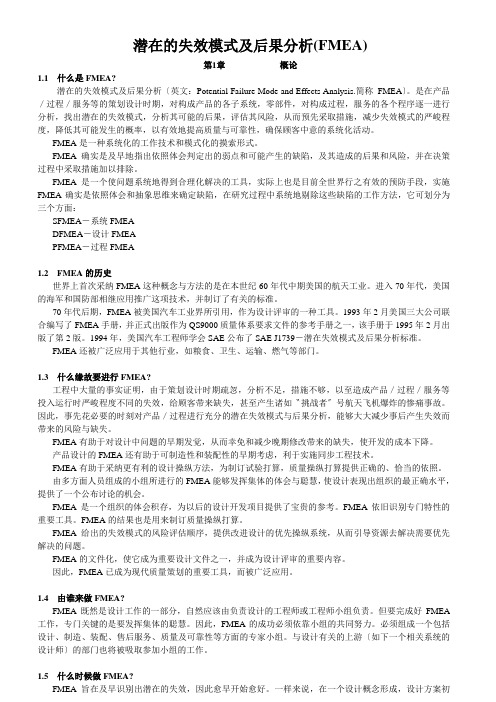
潜在的失效模式及后果分析(FMEA)第1章概论1.1 什么是FMEA?潜在的失效模式及后果分析〔英文:Potential Failure Mode and Effects Analysis.简称FMEA〕。
是在产品/过程/服务等的策划设计时期,对构成产品的各子系统,零部件,对构成过程,服务的各个程序逐一进行分析,找出潜在的失效模式,分析其可能的后果,评估其风险,从而预先采取措施,减少失效模式的严峻程度,降低其可能发生的概率,以有效地提高质量与可靠性,确保顾客中意的系统化活动。
FMEA是一种系统化的工作技术和模式化的摸索形式。
FMEA确实是及早地指出依照体会判定出的弱点和可能产生的缺陷,及其造成的后果和风险,并在决策过程中采取措施加以排除。
FMEA是一个使问题系统地得到合理化解决的工具,实际上也是目前全世界行之有效的预防手段,实施FMEA确实是依照体会和抽象思维来确定缺陷,在研究过程中系统地剔除这些缺陷的工作方法,它可划分为三个方面:SFMEA-系统FMEADFMEA-设计FMEAPFMEA-过程FMEA1.2 FMEA的历史世界上首次采纳FMEA这种概念与方法的是在本世纪60年代中期美国的航天工业。
进入70年代,美国的海军和国防部相继应用推广这项技术,并制订了有关的标准。
70年代后期,FMEA被美国汽车工业界所引用,作为设计评审的一种工具。
1993年2月美国三大公司联合编写了FMEA手册,并正式出版作为QS9000质量体系要求文件的参考手册之一,该手册于1995年2月出版了第2版。
1994年,美国汽车工程师学会SAE公布了SAE J1739-潜在失效模式及后果分析标准。
FMEA还被广泛应用于其他行业,如粮食、卫生、运输、燃气等部门。
1.3 什么缘故要进行FMEA?工程中大量的事实证明,由于策划设计时期疏忽,分析不足,措施不够,以至造成产品/过程/服务等投入运行时严峻程度不同的失效,给顾客带来缺失,甚至产生诸如〝挑战者〞号航天飞机爆炸的惨痛事故。
潜在失效模式与后果分析
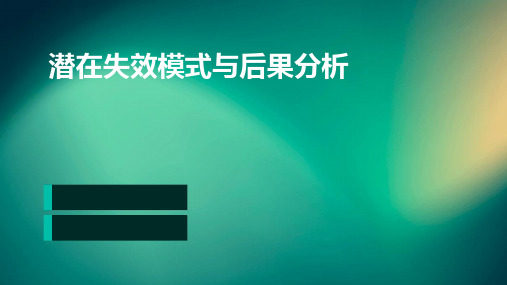
后果分析
交通事故、人员伤亡、品牌声誉受损等。
预防措施
严格把控零部件质量、定期进行车辆检查和 维护、提高生产工艺和流程的可靠性。
案例三:医疗器械潜在失效模式与后果分析
潜在失效模式
设备故障、软件错误、电池寿命过短等。
后果分析
诊断错误、治疗延误、患者生命安全受到威胁等。
预防措施
加强设备维护和校准、提高软件的安全性和稳定性、 采用高可靠性的电源和电池。
06 案例研究
案例一:电子产品潜在失效模式与后果分析
01
潜在失效模式
电子元件老化、过热、电磁干扰 等。
后果分析
02
03
预防措施
产品性能下降、突然失效、安全 问题等。
加强品质控制、定期维护和检查、 采用耐久性和可靠性更高的材料。
案例二:汽车行业潜在失效模式与后果分析
潜在失效模式
发动机故障、刹车系统失灵、气囊不起作用 等。
产品或过程出现故障,导致性能下降或维修成本增加。
后果评估
后果严重度评估
评估后果的严重程度,包括人员伤亡、财产 损失、环境影响等。
后果可能性评估
评估后果发生的可能性,包括概率和频率。
后果可检测性评估
评估后果在发生前被检测到的可能性。
后果严重性分级
高
01
严重后果,可能导致人员伤亡、重大财产损失或严重影响安全
头脑风暴法
通过绘制流程图,将产品或过程的各个阶 段进行详细描述,以便找出可能存在的失 效模式。
集合团队成员,通过集思广益的方式,提 出各种可能的失效模式。
历史数据分析法
通过分析历史数据,找出产品或过程中经 常出现的问题,从而识别潜在的失效模式 。
FMEA(失效模式与影响分析) 法
潜在失效模式及后果分析
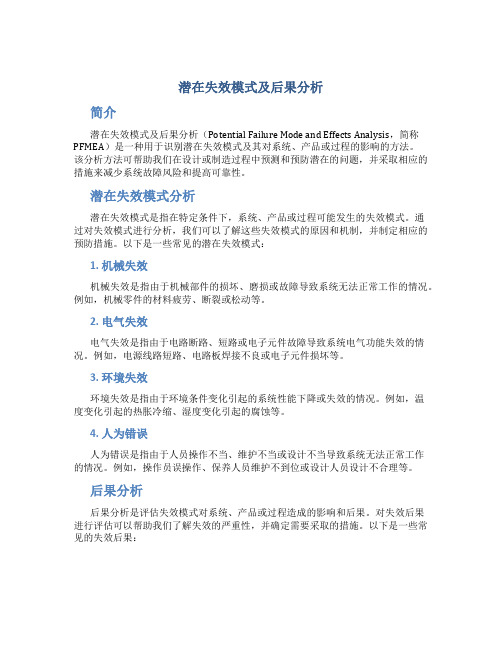
潜在失效模式及后果分析简介潜在失效模式及后果分析(Potential Failure Mode and Effects Analysis,简称PFMEA)是一种用于识别潜在失效模式及其对系统、产品或过程的影响的方法。
该分析方法可帮助我们在设计或制造过程中预测和预防潜在的问题,并采取相应的措施来减少系统故障风险和提高可靠性。
潜在失效模式分析潜在失效模式是指在特定条件下,系统、产品或过程可能发生的失效模式。
通过对失效模式进行分析,我们可以了解这些失效模式的原因和机制,并制定相应的预防措施。
以下是一些常见的潜在失效模式:1. 机械失效机械失效是指由于机械部件的损坏、磨损或故障导致系统无法正常工作的情况。
例如,机械零件的材料疲劳、断裂或松动等。
2. 电气失效电气失效是指由于电路断路、短路或电子元件故障导致系统电气功能失效的情况。
例如,电源线路短路、电路板焊接不良或电子元件损坏等。
3. 环境失效环境失效是指由于环境条件变化引起的系统性能下降或失效的情况。
例如,温度变化引起的热胀冷缩、湿度变化引起的腐蚀等。
4. 人为错误人为错误是指由于人员操作不当、维护不当或设计不当导致系统无法正常工作的情况。
例如,操作员误操作、保养人员维护不到位或设计人员设计不合理等。
后果分析后果分析是评估失效模式对系统、产品或过程造成的影响和后果。
对失效后果进行评估可以帮助我们了解失效的严重性,并确定需要采取的措施。
以下是一些常见的失效后果:1. 安全风险失效后果可能导致人员受伤、工作环境不安全或设备损坏,从而造成安全风险。
例如,机械失效可能导致意外伤害,电气失效可能引发火灾或触电事故。
2. 生产效率下降失效后果可能导致生产过程中断、产品质量下降或生产效率低下,从而影响企业的运营和利润。
例如,机械失效可能导致生产线停工,电气失效可能导致产品质量问题。
3. 用户体验不良失效后果可能导致产品性能下降,用户无法正常使用或满足需求,从而影响用户体验和满意度。
- 1、下载文档前请自行甄别文档内容的完整性,平台不提供额外的编辑、内容补充、找答案等附加服务。
- 2、"仅部分预览"的文档,不可在线预览部分如存在完整性等问题,可反馈申请退款(可完整预览的文档不适用该条件!)。
- 3、如文档侵犯您的权益,请联系客服反馈,我们会尽快为您处理(人工客服工作时间:9:00-18:30)。
潜在失效模式及后果分析
1. 简介
在工程设计和生产过程中,产品的失效模式及其潜在后果分析是非常重要的一环。
通过对产品失效模式和后果的分析,可以及早发现和解决潜在的问题,从而提高产品的可靠性和安全性。
2. 什么是潜在失效模式?
潜在失效模式是指在特定工作条件下可能导致产品失效的方式或方式组合。
每
个产品都可能存在多个潜在失效模式,而这些失效可能会对产品的性能、可靠性和安全性产生不利影响。
3. 为什么进行潜在失效模式及后果分析?
潜在失效模式及后果分析有以下几个重要的目的: - 识别并理解产品的潜在失
效模式,以便进行针对性的改进和优化; - 预测产品在特定工作条件下的失效后果,以便制定相应的应对措施; - 分析和评估潜在失效对产品性能、可靠性和安全性的
影响,以指导产品设计和工艺改进; - 为后续的可靠性测试和故障分析提供基础和
参考。
4. 潜在失效模式及后果分析的方法
潜在失效模式及后果分析可以采用多种方法,常见的方法包括以下几种: ### 4.1 故障模式与影响分析(FMEA) 故障模式与影响分析(Failure Mode and Effects Analysis, FMEA)是一种常见的潜在失效模式及后果分析方法。
通过对产品的各个部件和子系统进行系统性的分析,识别出各种潜在失效模式及其后果,并根据其严重性、发生概率和检测能力等指标进行评估和排序。
4.2 故障树分析(FTA)
故障树分析(Fault Tree Analysis, FTA)是另一种常用的潜在失效模式及后果分析
方法。
通过建立一个由事件和逻辑门构成的故障状态树,分析和推导出导致系统失效的各种可能性和后果。
4.3 事件树分析(ETA)
事件树分析(Event Tree Analysis, ETA)是一种与故障树分析类似的潜在失效模
式及后果分析方法。
与故障树分析不同的是,事件树分析是从系统的某个事件开始进行推导,分析该事件的多种可能性和后果,从而得出整个系统的失效模式和后果。
5. 实施潜在失效模式及后果分析的步骤
实施潜在失效模式及后果分析一般需要以下几个步骤:
•确定分析的范围和目标,明确需要分析的产品、系统或过程,并明确分析的目的和要求;
•收集和整理相关的信息数据,包括产品的设计文档、工艺流程表、可靠性数据等;
•识别潜在失效模式,通过对产品的各个组成部分进行逐一分析,识别可能的潜在失效模式;
•分析和评估潜在失效对产品性能、可靠性和安全性的影响,包括失效的后果、严重性、发生概率等指标;
•制定并实施相应的改进措施,根据分析结果,制定并实施相应的改进措施,从而减少潜在失效的发生和影响;
•追踪和监控改进效果,跟踪和监控产品的性能和可靠性指标,以验证改进措施的有效性和可行性。
6. 实例分析:汽车发动机失效模式及后果分析
以汽车发动机为例,进行潜在失效模式及后果分析:
失效模式后果
缺乏润滑引擎磨损、损坏
高温过载引擎过热、漏水
冷却液泄漏引擎过热、冷却系统失效
燃油泄漏引擎熄火、起火
电子控制故障引擎无法启动、性能下降
根据以上分析结果,我们可以采取以下措施:
•定期更换发动机油和过滤器,确保发动机的充分润滑;
•定期检查和更换冷却液,保证冷却系统的正常工作;
•定期检查和更换燃油系统的相关部件,避免燃油泄漏;
•加强对发动机电子控制系统的维护和检修,确保其可靠性和性能。
通过以上措施的实施,可以提高发动机的可靠性和安全性,减少潜在失效带来的不利影响。
7. 结论
潜在失效模式及后果分析是提高产品可靠性和安全性的重要手段之一。
通过对产品的潜在失效模式进行分析和评估,可以及早发现和解决潜在的问题,从而提高
产品的性能和可靠性。
因此,在产品设计和生产过程中,进行潜在失效模式及后果分析是非常必要和重要的。