复合肥造粒工艺比较
复合肥生产方法与主要生产工艺

复合肥生产方法1、团粒法:粉状的基础肥料借助于液相(水+蒸汽+肥料溶液)粘聚成粒,再借助于外力的挤压成型。
该法是我国目前复混肥料加工的主要方法。
2、料浆法:在这种工艺中,要造粒的物料是料浆形式,一般是由硫酸、硝酸、磷酸与氨、磷矿粉(或这两种物料以某种形式的结合)进行反应得到的。
3、掺全法:把颗粒度和强度接近的基础肥料(基本彼此间无化学反应)进行一定比例的掺拌混合。
4、流体法:分为液体(清液)肥料和悬浮流体肥料两种。
5、熔融法:氮素肥料尿素或硝氨和磷铵钾盐一起熔融后用塔式或油冷方式进行生产NP或NPK颗粒状复合肥。
6、浓液造粒法:该法是团粒法和料浆法的改进,尿素、硝氨以90%以上的浓溶液进入造粒系统,改善了造粒和性能和产品的质量。
本法可以直接利用尿素,硝铵系统的浓缩液时行联产NPK复混肥。
7、挤压法:利用机械外力的作用便粉体基础化肥成粒的一种方法。
热稳定性差的基础化肥,如碳酸氢铵和基础肥制NPK时,都采取此法。
复混肥的主要生产工艺技术1、掺混法生产工艺:对基础肥料的总的要求是粒度均匀,水份含量低,颗粒强度好,贮藏时不结块。
2、物理团粒法:是用物理的方法便非颗粒状的或粉末状的物料加工成为符合要求的粒径大小,并具有足够的机械稳定性的肥料技术。
我国常用的技术有团聚造粒(无机、有机-无机复混肥)、挤压造粒(有机-无机复混肥)、喷浆造粒(磷酸铵类产品)三种类型。
3、料浆法生产工艺:料浆是用硫酸、硝酸、磷酸或一些混合酸与氨反应的产物,有时也用酸与磷矿粉反应的产物。
在料浆中加入钾盐或直接把钾盐加至造粒机内,可制提NPK 三元复混肥。
料浆造粒的机理主要依靠料浆的涂布作用而使颗粒逐渐增大,并得到强度坚硬和流程性优良的颗粒肥料。
4、熔体造粒法:可分为造粒塔喷淋造粒工艺(高塔)、油冷造粒工艺、双轴造粒工艺、转鼓造粒工艺、喷浆造粒工艺、盘式造粒工艺、钢带造粒工艺。
5、挤压法生产工艺:是固体物料依靠外部压力进行团聚的干法造粒过程。
氨化造粒复合肥
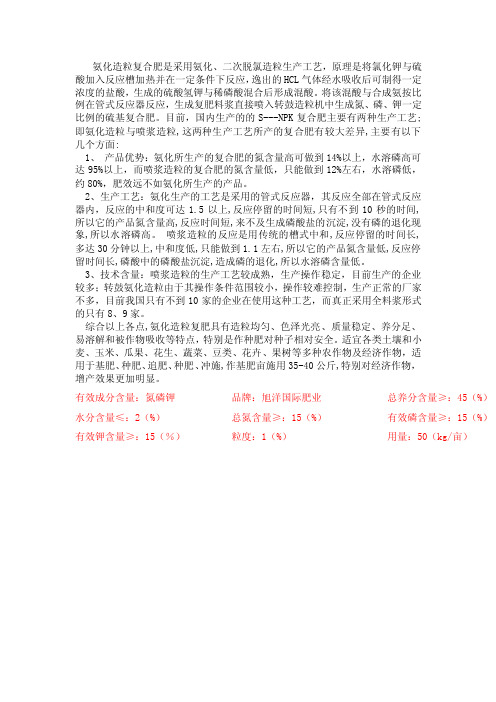
氨化造粒复合肥是采用氨化、二次脱氯造粒生产工艺,原理是将氯化钾与硫酸加入反应槽加热并在一定条件下反应,逸出的HCL气体经水吸收后可制得一定浓度的盐酸,生成的硫酸氢钾与稀磷酸混合后形成混酸。
将该混酸与合成氨按比例在管式反应器反应,生成复肥料浆直接喷入转鼓造粒机中生成氮、磷、钾一定比例的硫基复合肥。
目前,国内生产的的S---NPK复合肥主要有两种生产工艺;即氨化造粒与喷浆造粒,这两种生产工艺所产的复合肥有较大差异,主要有以下几个方面:1、产品优势:氨化所生产的复合肥的氮含量高可做到14%以上,水溶磷高可达95%以上,而喷浆造粒的复合肥的氮含量低,只能做到12%左右,水溶磷低,约80%,肥效远不如氨化所生产的产品。
2、生产工艺:氨化生产的工艺是采用的管式反应器,其反应全部在管式反应器内,反应的中和度可达1.5以上,反应停留的时间短,只有不到10秒的时间,所以它的产品氮含量高,反应时间短,来不及生成磷酸盐的沉淀,没有磷的退化现象,所以水溶磷高。
喷浆造粒的反应是用传统的槽式中和,反应停留的时间长,多达30分钟以上,中和度低,只能做到1.1左右,所以它的产品氮含量低,反应停留时间长,磷酸中的磷酸盐沉淀,造成磷的退化,所以水溶磷含量低。
3、技术含量:喷浆造粒的生产工艺较成熟,生产操作稳定,目前生产的企业较多;转鼓氨化造粒由于其操作条件范围较小,操作较难控制,生产正常的厂家不多,目前我国只有不到10家的企业在使用这种工艺,而真正采用全料浆形式的只有8、9家。
综合以上各点,氨化造粒复肥具有造粒均匀、色泽光亮、质量稳定、养分足、易溶解和被作物吸收等特点,特别是作种肥对种子相对安全。
适宜各类土壤和小麦、玉米、瓜果、花生、蔬菜、豆类、花卉、果树等多种农作物及经济作物,适用于基肥、种肥、追肥、种肥、冲施,作基肥亩施用35-40公斤,特别对经济作物,增产效果更加明显。
有效成分含量:氮磷钾品牌:旭洋国际肥业总养分含量≥:45(%)水分含量≤:2(%)总氮含量≥:15(%)有效磷含量≥:15(%)有效钾含量≥:15(%)粒度:1(%)用量:50(kg/亩)。
复合肥工艺及特点
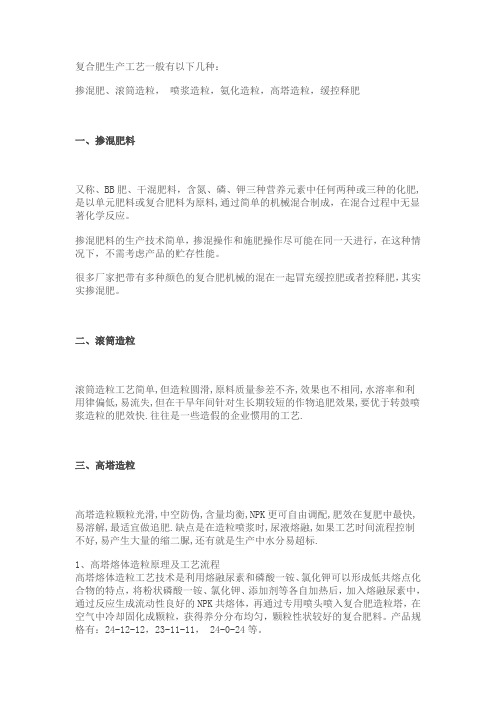
复合肥生产工艺一般有以下几种:掺混肥、滚筒造粒,喷浆造粒,氨化造粒,高塔造粒,缓控释肥一、掺混肥料又称、BB肥、干混肥料,含氮、磷、钾三种营养元素中任何两种或三种的化肥,是以单元肥料或复合肥料为原料,通过简单的机械混合制成,在混合过程中无显著化学反应。
掺混肥料的生产技术简单,掺混操作和施肥操作尽可能在同一天进行,在这种情况下,不需考虑产品的贮存性能。
很多厂家把带有多种颜色的复合肥机械的混在一起冒充缓控肥或者控释肥,其实实掺混肥。
二、滚筒造粒滚筒造粒工艺简单,但造粒圆滑,原料质量参差不齐,效果也不相同,水溶率和利用律偏低,易流失,但在干旱年间针对生长期较短的作物追肥效果,要优于转鼓喷浆造粒的肥效快.往往是一些造假的企业惯用的工艺.三、高塔造粒高塔造粒颗粒光滑,中空防伪,含量均衡,NPK更可自由调配,肥效在复肥中最快,易溶解,最适宜做追肥.缺点是在造粒喷浆时,尿液熔融,如果工艺时间流程控制不好,易产生大量的缩二脲,还有就是生产中水分易超标.1、高塔熔体造粒原理及工艺流程高塔熔体造粒工艺技术是利用熔融尿素和磷酸一铵、氯化钾可以形成低共熔点化合物的特点,将粉状磷酸一铵、氯化钾、添加剂等各自加热后,加入熔融尿素中,通过反应生成流动性良好的NPK共熔体,再通过专用喷头喷入复合肥造粒塔,在空气中冷却固化成颗粒,获得养分分布均匀,颗粒性状较好的复合肥料。
产品规格有:24-12-12,23-11-11, 24-0-24等。
2、生产流程主要分为三个部分:原料处理、造粒、冷却处理。
见下图示。
高塔造粒技术主要利用了熔体造粒法技术,造粒塔喷淋造粒工艺应用最早、最广泛的是单一氮肥(如尿素、硝酸铵等)的造粒,现已扩大到氮磷及氮磷钾复合肥料的造粒。
该工艺的一个特殊要求是,氯化钾必须磨得细,以防止造粒喷头的孔眼堵塞,并且需要将其预热到足够高的温度,以防止混合时熔融物冷却。
3、熔体造粒工艺优点与常用的复混肥制造工艺相比,熔体造粒工艺具有以下优点:a、简化了生产流程。
复合肥造粒工艺及优缺点
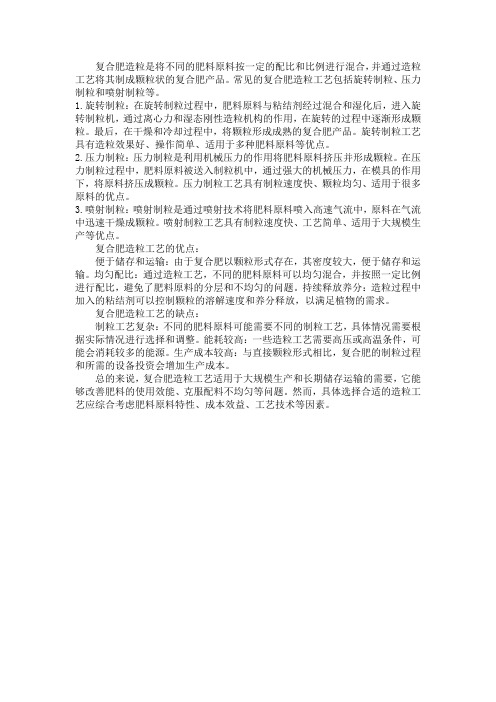
复合肥造粒是将不同的肥料原料按一定的配比和比例进行混合,并通过造粒工艺将其制成颗粒状的复合肥产品。
常见的复合肥造粒工艺包括旋转制粒、压力制粒和喷射制粒等。
1.旋转制粒:在旋转制粒过程中,肥料原料与粘结剂经过混合和湿化后,进入旋转制粒机,通过离心力和湿态刚性造粒机构的作用,在旋转的过程中逐渐形成颗粒。
最后,在干燥和冷却过程中,将颗粒形成成熟的复合肥产品。
旋转制粒工艺具有造粒效果好、操作简单、适用于多种肥料原料等优点。
2.压力制粒:压力制粒是利用机械压力的作用将肥料原料挤压并形成颗粒。
在压力制粒过程中,肥料原料被送入制粒机中,通过强大的机械压力,在模具的作用下,将原料挤压成颗粒。
压力制粒工艺具有制粒速度快、颗粒均匀、适用于很多原料的优点。
3.喷射制粒:喷射制粒是通过喷射技术将肥料原料喷入高速气流中,原料在气流中迅速干燥成颗粒。
喷射制粒工艺具有制粒速度快、工艺简单、适用于大规模生产等优点。
复合肥造粒工艺的优点:便于储存和运输:由于复合肥以颗粒形式存在,其密度较大,便于储存和运输。
均匀配比:通过造粒工艺,不同的肥料原料可以均匀混合,并按照一定比例进行配比,避免了肥料原料的分层和不均匀的问题。
持续释放养分:造粒过程中加入的粘结剂可以控制颗粒的溶解速度和养分释放,以满足植物的需求。
复合肥造粒工艺的缺点:制粒工艺复杂:不同的肥料原料可能需要不同的制粒工艺,具体情况需要根据实际情况进行选择和调整。
能耗较高:一些造粒工艺需要高压或高温条件,可能会消耗较多的能源。
生产成本较高:与直接颗粒形式相比,复合肥的制粒过程和所需的设备投资会增加生产成本。
总的来说,复合肥造粒工艺适用于大规模生产和长期储存运输的需要,它能够改善肥料的使用效能、克服配料不均匀等问题。
然而,具体选择合适的造粒工艺应综合考虑肥料原料特性、成本效益、工艺技术等因素。
复合肥生产工艺比较

熔融温度一般由可熔的原料熔点来决定,尿素熔点 132.7℃,硝铵熔点170.4℃,在配方中加入一定量的助 熔剂可在低于熔点下熔融,对尿素来说可减少缩二脲的产 生,硝铵则可降低熔融的危险性。 熔融体与其他固体原料在一定的搅拌强度下混合,根据物 料粘稠度来确定搅拌桨叶端线速度和搅拌桨叶型式以保证 物料的混合均匀,也可采用乳化机进行乳化,以达到改善 造粒性能。 混合前的固体原料一般采用加热器预热,来确保大量的固 体料在混合槽中不至于急冷固化。当然也有采用冷料混合, 但必须设计出合理的混合程序,以避免冷料所带来的负面 影响。
Company Logo
熔融混合温度及时间的控制原则
目前有三种制浆过程
1)熔融尿液(或硝铵)与经过磨细加热的其他原料搅拌混合。 )熔融尿液(或硝铵)与经过磨细加热的其他原料搅拌混合。 2)固体尿素(或硝铵)与其他原料搅拌混合后加热熔融。 )固体尿素(或硝铵)与其他原料搅拌混合后加热熔融。 3)熔融尿液(或硝铵)与其他原料搅拌混合并乳化。 )熔融尿液(或硝铵)与其他原料搅拌混合并乳化。
复合肥生产工 艺比较
LOGO
武汉中农国际贸易有限公司
几种不同的造粒工艺
滚筒造粒工艺简单,但造粒圆滑 原料质量参差不齐 滚筒造粒工艺简单 但造粒圆滑,原料质量参差不齐 效果也 但造粒圆滑 原料质量参差不齐,效果也 不相同,水溶率和利用率偏低 易流失,但在干旱年间针对生 不相同 水溶率和利用率偏低,易流失 但在干旱年间针对生 水溶率和利用率偏低 易流失 长期较短的作物追肥效果,要比转鼓喷浆造粒的肥效快 要比转鼓喷浆造粒的肥效快. 长期较短的作物追肥效果 要比转鼓喷浆造粒的肥效快 转鼓喷浆造粒粒度坚硬,肥效比高塔造粒长 不宜流失,易做 肥效比高塔造粒长,不宜流失 转鼓喷浆造粒粒度坚硬 肥效比高塔造粒长 不宜流失 易做 生长期长的作物基肥使用.缺点是化合时氮素易流失 缺点是化合时氮素易流失,故有 生长期长的作物基肥使用 缺点是化合时氮素易流失 故有 二次加氮的工艺. 二次加氮的工艺 氨化造粒是管道喷浆成粒,肥效期介于滚筒和转鼓喷浆之 氨化造粒是管道喷浆成粒 肥效期介于滚筒和转鼓喷浆之 利用率优于喷浆,而低于高塔造粒 水溶性不错,颗粒成 间,利用率优于喷浆 而低于高塔造粒 水溶性不错 颗粒成 利用率优于喷浆 而低于高塔造粒,水溶性不错 不规则状,高氮高钾等含量可自由调节 适合配方施肥. 高氮高钾等含量可自由调节,适合配方施肥 不规则状 高氮高钾等含量可自由调节 适合配方施肥 高塔造粒颗粒光滑,中空防伪 含量均衡,NPK更可自由调 中空防伪,含量均衡 高塔造粒颗粒光滑 中空防伪 含量均衡 更可自由调 肥效在复肥中最快,易溶解 最适宜做追肥.缺点是在造 配,肥效在复肥中最快 易溶解 最适宜做追肥 缺点是在造 肥效在复肥中最快 易溶解,最适宜做追肥 粒喷浆时,尿液熔融 如果工艺时间流程控制不好,易产生大 尿液熔融,如果工艺时间流程控制不好 粒喷浆时 尿液熔融 如果工艺时间流程控制不好 易产生大 量的缩二脲,还有就是生产中水分易超标 还有就是生产中水分易超标. 量的缩二脲 还有就是生产中水分易超标
复合肥几种主要工艺

复合肥生产工艺一般有以下几种:喷浆造粒,氨化造粒,高塔造粒,缓控释肥--------------------------------------------------------------------------------采用氨化、二次脱氯造粒生产工艺,原理是将氯化钾与硫酸加入反应槽加热并在一定条件下反应,逸出的HCL气体经水吸收后可制得一定浓度的盐酸,生成的硫酸氢钾与稀磷酸混合后形成混酸。
将该混酸与合成氨按比例在管式反应器反应,生成复肥料浆直接喷入转鼓造粒机中生成氮、磷、钾一定比例的硫基复合肥。
具有造粒均匀、色泽光亮、质量稳定、养分足、易溶解和被作物吸收等特点,非凡是作种肥对种子相对安全。
适宜各类土壤和小麦、玉米、瓜果、花生、蔬菜、豆类、花卉、果树等多种农作物及经济作物,适用于基肥、种肥、追肥、种肥、冲施。
这个是氨化造粒的解释,可我感觉这是喷浆造粒的解释--------------------------------------------------------------------------------氨酸法工艺流程:将多种基础肥料及添加剂按工艺配方要求分批计量,经混料机搅拌均匀后与返料一起,由电子计量皮带输送入造粒机内。
浓度98%或93%的硫酸经槽车外购入硫酸储槽存放,经泵打入硫酸稀释储槽并计量后供造粒所需。
液氨经蒸发为气氨由管道输送入造粒机内。
氨和硫酸在造粒机内的管道中连续反应直接进入造粒机料层进行造粒工作。
物料在70~80℃温度和蒸汽的调节下在造粒机内团聚成粒。
成粒的湿物料在皮带运输机上冷却硬化后,再进入烘干机干燥脱水。
烘干后的物料由提升机输送到筛分机,筛分后的大颗粒经破碎后与筛下细料一道返回造粒机再造粒。
合格的颗粒经防潮、防结块的包膜处理后经风冷进入成品再次筛分、计量包装。
包装好的成品由转运车运入库房存放。
造粒机所产生的废气由通风机抽出并送入尾气水洗装置系统洗涤。
干燥热风由热风炉经热风机提供。
复合肥氨酸法造粒工艺
复合肥氨酸法造粒工艺复合肥生产的工艺,主要是团粒法、料浆法二种工艺组成。
料浆法工艺因其生产规模、投资规模等多项因素制约,主要在少数大型国有企业应用;而团粒法因其工艺简单、投资少、操作便利等特点而被国内大多数厂家采用,其缺点是生产过程中经验因素比较强,产品对原料局限性比较大,特别是高氮高尿系列复合肥的生产,甚至很困难。
因此采用部分料浆法的氨酸法喷浆造粒工艺正在被广泛推广应用。
液氨与硫酸在工艺中,就是硫酸喷在物料的表面,这是化肥生产氨化造粒中多孔固体中酸的氨化问题。
这时过程的速率主要受氨分子趋近颗粒外表面,再从表面进入毛细孔的扩散速率的控制。
研究结果指出,对运动中的颗粒,气体扩散到表面的速率很快,在颗粒内部的扩散则较慢。
因为气体不仅要进入孔道,而且还要通过液膜和反应产物形成的屏蔽。
氨到达颗粒表面的速率与设备的类型和进气方式有关。
氨气通过颗粒床的流态可分为两种:一种是滤过式,这时氨气通过颗粒之间的缝隙连续流过,几乎不影响粒子的运动;一种是喷射式,这时氨气通过喷嘴流速较大,在颗粒床形成空间或喷舌,引起颗粒作剧烈的旋转运动,大大强化了传质和传热过程。
在喷舌流态条件下进行氨化的研究指出,为保持合适的气速,喷口直径应较颗粒直径大10倍以上。
调整气速使刚好形成喷舌。
固体颗粒上硫酸的氨化通常都在造粒机中进行,液氨通过埋在颗粒床中的分布器,沿造粒机轴向均匀喷出。
良好的设计可使氨的吸收率达到90%以上。
氨分布器是氨化造粒机的重要部件。
用在需连续氨化造粒过程的转鼓造粒机称为氨化转鼓造粒机,是磷复肥造粒中的一种常用设备,是美国TVA(田纳西流域管理局)在50年代初期开发的。
迄今在世界各国的磷复肥生产中广泛应用。
按照美国TVA氨化转鼓造粒机的设计准则,在造粒机靠筒体轴线的上方设有一管梁,以便安装氨分布器和酸管、蒸汽管,返料从造粒机头加入,在筒体的转动下形成一滚动的物料床,硫酸由酸泵压送,从硫酸喷洒管的喷嘴喷洒在物料床上进行造粒。
高塔造粒生产硝基复合肥的工艺研究
高塔造粒生产硝基复合肥的工艺争论高塔造粒工艺生产复合肥是我国近10 年进展起来的工艺。
其产品具有外观颗粒均匀、光润圆滑、均带小孔,养分稳定,水分低等特点,深受农民欢送,至今国内已建成装置的产量超过1000 万t。
高塔工艺生产的主要是尿基复合肥。
硝基复合肥是指以硝铵磷或者硝酸铵作为氮源生产的复合肥,而区分于使用尿素、氯化铵、硫酸铵等生产的传统复合肥。
硝基复合肥可以直接被作物充分吸取,具有速溶速效的特点,尤其适用于国内雨水较少、气温较低的北方旱地碱性土壤。
硝态氮肥可以促进作物快速生长,特别适合于蔬菜、果树、烟草等经济作物。
硝基复合肥在国际上特别是在欧美国家得到广泛应用,据统计,俄罗斯、波兰、法国、巴西、美国硝酸铵占氮肥总产量的比例分别为39.7%、30.9%、27.5%、16.1%和12.6%,而我国加上进口缺乏5%。
正是由于含硝态氮肥料的优点,很多厂家看准市场需求,大力进展硝基复合肥。
很多厂家都尝试利用原有高塔设备生产硝基复合肥,但都存在肯定问题。
1高塔造粒生产硝基复合肥存在的主要问题1)无法连续生产。
熔融后的硝酸铵在参加粉状物料后消灭料浆变黏稠,流淌陛太差,频繁堵塞喷头和管道。
2)存在安全隐患。
混合槽内硝铵简洁猛烈分解,进而有发生火灾的危急。
3)产量下降。
熔融设备生产尿基产品时力量可满足,但生产硝基产品时达不到生产尿基的产能。
2高塔造粒生产硝基复合肥存在问题的缘由分析国内高塔硝基复合肥生产企业多以硝铵〔硝酸磷肥、硝磷铵〕为生产原料,参加磷铵、氯化钾〔硫酸钾〕和其他添加剂进展生产,不同于国外的以磷矿和硝酸为原料进展生产。
但两种生产方法的原理一样。
下面以荷兰和俄罗斯的生产工艺为比照,分析国内高塔造粒生产硝基复合肥存在的问题。
2.1 荷兰和俄罗斯高塔造粒生产硝基复合肥的特点1〕荷兰斯塔米卡本法硝酸磷酸铵钾生产流程。
荷兰斯塔米卡本公司〔Stami Carbon〕造粒塔喷淋造粒生产硝酸磷酸铵钾的工艺流程见图1。
复合肥常见造粒生产工艺简介
复合肥常见造粒生产工艺简介复合肥造粒生产工艺简介氨化造粒采用氨化、二次脱氯造粒生产,原理是将氯化钾与硫酸加入反应槽加热并在一定条件下反应,逸出的HCL 气体经水吸收后可制得一定浓度的盐酸,生成的硫酸氢钾与稀磷酸混合后形成混酸。
将该混酸与合成氨按比例在管式反应器反应,生成复肥料浆直接喷入转鼓造粒机中生成氮、磷、钾一定比例的硫基复合肥。
Kcl+HSO4=HCL+KHSO4具有造粒均匀、色泽光亮、质量稳定、养分足、易溶解和被作物吸收等特点,特别是作种肥对种子相对安全。
适宜各类土壤和小麦、玉米、瓜果、花生、蔬菜、豆类、花卉、果树等多种农作物及经济作物,适用于基肥、种肥、追肥、种肥、冲施。
氨酸法工艺流程:将多种基础肥料及添加剂按工艺配方要求分批计量,经混料机搅拌均匀后与返料一起,由电子计量皮带输送入造粒机内。
浓度98%或93%的硫酸经槽车外购入硫酸储槽存放,经泵打入硫酸稀释储槽并计量后供造粒所需。
液氨经蒸发为气氨由管道输送入造粒机内。
氨和硫酸在造粒机内的管道中连续反应直接进入造粒机料层进行造粒工作。
物料在70-80℃温度和蒸汽的调节下在造粒机内团聚成粒。
成粒的湿物料在皮带运输机上冷却硬化后,再进入烘干机干燥脱水。
烘干后的物料由提升机输送到筛分机,筛分后的大颗粒经破碎后与筛下细料一道返回造粒机再造粒。
合格的颗粒经防潮、防结块的包膜处理后经风冷进入成品再次筛分、计量包装。
包装好的成品由转运车运入库房存放。
造粒机所产生的废气由通风机抽出并送入尾气水洗装置系统洗涤。
干燥热风由热风炉经热风机提供。
烘干后的尾气经高效旋风除尘器除尘后由尾气风机送洗涤塔洗涤并由烟囱排空。
出洗涤塔的洗涤水循环使用,部分泵入硫酸稀释储槽做稀释补充水用。
经洗涤后的尾气排入大气。
NH3+HSO4=NH3(HSO4)+热力高塔熔体造粒原理高塔熔体造粒工艺技术是利用熔融尿素和磷酸一铵、氯化钾可以形成低共熔点化合物的特点,将粉状磷酸一铵、氯化钾、添加剂等各自加热后,加入熔融尿素中,通过反应生成流动性良好的NPK共熔体,再通过专用喷头喷入复合肥造粒塔,在空气中冷却固化成颗粒,获得养分分布均匀,颗粒性状较好的复合肥料。
复合肥主要工艺技术和生产方法介绍
复合肥料的生产方法一、综合颗粒状复混肥料的生产方法主要有以下几种:1.料浆法以磷酸、氨为原料,利用中和器、管式反应器将中和料浆在氨化粒化器中进行涂布造粒,在生产过程中添加部分氮素和钾素以及其他物质,再经干燥、筛分、冷却而得到NPK复合肥产品,这是国内外各大化肥公司和工厂大规模生产常采用的生产方法。
磷酸可由硫酸分解磷矿制取,有条件时也可直接外购商品磷酸,以减少投资和简化生产环节。
该法的优点是既可生产磷酸铵也可生产NPK 肥料,同时也充分利用了酸、氨的中和热蒸发物料水份,降低造粒水含量和干燥负荷,减少能耗,此法的优点是:生产规模大,生产成本较低,产品质量好,产品强度较高。
由于通常需配套建设磷酸装置及硫酸装置,建设不仅投资大,周期长,而且涉及磷、硫资源的供应和众多的环境保护问题(如磷石膏、氟、酸沫、酸泥等),一般较适用于在磷矿加工基地和较大规模生产、产品品数不多的情况。
如以外购的商品磷酸为原料,则目前稳定的来源和运输问题及价格因素是不得不考虑的,近年来,由于我国磷酸工业技术和装备水平的提高,湿法磷酸作为商品进入市场有了良好的条件,在有资源和条件的地区建立磷酸基地,以商品磷酸满足其它地区发展高浓度磷复肥的需要,正在形成一种新的思路和途径,市场需求必将促进这一行业发展,也必将解决众多地区原料磷酸的需求问题。
拥有该种生产技术的外国公司主要有挪威的norsk hydro、西班牙incro、espindsea、法国的AZF、KT、美国的Davy/TV A等。
国内的主要生产厂家有:中阿化肥有限公司、江西贵溪化肥厂、云南云峰化工公司、南京南化磷肥厂、大连化工厂、金昌化工公司、广西鹿寨磷肥厂等。
拥有相近于该种生产技术的国内企业主要有山东的红日集团、四川成都科技大学、上海化工研究院等。
2.固体团粒法以单体基础肥料如:尿素、硝铵、氯化铵、硫铵、磷铵(磷酸一铵、磷酸二铵、重钙、普钙)、氯化钾(硫酸钾)等为原料,经粉碎至一定细度后,物料在转鼓造粒机(或园盘造粒机)的滚动床内通过增湿、加热进行团聚造粒,在成粒过程中,有条件的还可以在转鼓造粒机加入少量的磷酸和氨,以改善成粒条件。
- 1、下载文档前请自行甄别文档内容的完整性,平台不提供额外的编辑、内容补充、找答案等附加服务。
- 2、"仅部分预览"的文档,不可在线预览部分如存在完整性等问题,可反馈申请退款(可完整预览的文档不适用该条件!)。
- 3、如文档侵犯您的权益,请联系客服反馈,我们会尽快为您处理(人工客服工作时间:9:00-18:30)。
复合肥生产工艺一般有以下几种:喷浆造粒,氨化造粒,高塔造粒,缓控释肥--------------------------------------------------------------------------------采用氨化、二次脱氯造粒生产工艺,原理是将氯化钾与硫酸加入反应槽加热并在一定条件下反应,逸出的HCL气体经水吸收后可制得一定浓度的盐酸,生成的硫酸氢钾与稀磷酸混合后形成混酸。
将该混酸与合成氨按比例在管式反应器反应,生成复肥料浆直接喷入转鼓造粒机中生成氮、磷、钾一定比例的硫基复合肥。
具有造粒均匀、色泽光亮、质量稳定、养分足、易溶解和被作物吸收等特点,非凡是作种肥对种子相对安全。
适宜各类土壤和小麦、玉米、瓜果、花生、蔬菜、豆类、花卉、果树等多种农作物及经济作物,适用于基肥、种肥、追肥、种肥、冲施。
这个是氨化造粒的解释,可我感觉这是喷浆造粒的解释--------------------------------------------------------------------------------氨酸法工艺流程:将多种基础肥料及添加剂按工艺配方要求分批计量,经混料机搅拌均匀后与返料一起,由电子计量皮带输送入造粒机内。
浓度98%或93%的硫酸经槽车外购入硫酸储槽存放,经泵打入硫酸稀释储槽并计量后供造粒所需。
液氨经蒸发为气氨由管道输送入造粒机内。
氨和硫酸在造粒机内的管道中连续反应直接进入造粒机料层进行造粒工作。
物料在70~80℃温度和蒸汽的调节下在造粒机内团聚成粒。
成粒的湿物料在皮带运输机上冷却硬化后,再进入烘干机干燥脱水。
烘干后的物料由提升机输送到筛分机,筛分后的大颗粒经破碎后与筛下细料一道返回造粒机再造粒。
合格的颗粒经防潮、防结块的包膜处理后经风冷进入成品再次筛分、计量包装。
包装好的成品由转运车运入库房存放。
造粒机所产生的废气由通风机抽出并送入尾气水洗装置系统洗涤。
干燥热风由热风炉经热风机提供。
烘干后的尾气经高效旋风除尘器除尘后由尾气风机送洗涤塔洗涤并由烟囱排空。
出洗涤塔的洗涤水循环使用,部分泵入硫酸稀释储槽做稀释补充水用。
经洗涤后的尾气排入大气。
喷浆造粒工艺可以参考磷肥与复婚肥料书。
--------------------------------------------------------------------------------高塔熔体造粒原理及工艺流程高塔熔体造粒工艺技术是利用熔融尿素和磷酸一铵、氯化钾可以形成低共熔点化合物的特点,将粉状磷酸一铵、氯化钾、添加剂等各自加热后,加入熔融尿素中,通过反应生成流动性良好的NPK共熔体,再通过专用喷头喷入复合肥造粒塔,在空气中冷却固化成颗粒,获得养分分布均匀,颗粒性状较好的复合肥料。
产品规格有:24-12-12,23-11-11,24-0-24等。
生产流程主要分为三个部分:原料处理、造粒、冷却处理。
见下图示。
高塔造粒技术主要利用了熔体造粒法技术。
该技术最早应用于磷酸一铵(MAP)、硝酸磷酸铵(APN),尿素磷酸铵(UAP),在这些生产方法中,可以加入钾盐或其它固体物料生产颗粒状氮磷钾复合肥产品。
按造粒方式的不同,熔体造粒法制复合肥工艺主要可分为:造粒塔喷淋造粒工艺,油冷造粒工艺,双轴造粒工艺,转鼓造粒工艺,喷浆造粒工艺,盘式造粒工艺,钢带造粒工艺等。
造粒塔喷淋造粒工艺应用最早、最广泛的是单一氮肥(如尿素、硝酸铵等)的造粒,现已扩大到氮磷及氮磷钾复合肥料的造粒。
荷兰斯塔米卡本公司曾用造粒塔喷淋造粒工艺生产硝酸磷酸铵钾;挪威海德鲁用造粒塔喷淋造粒制尿素磷酸铵及尿素磷酸铵钾。
该工艺的一个非凡要求是,氯化钾必须磨得细,以防止造粒喷头的孔眼堵塞,并且需要将其预热到足够高的温度,以防止混合时熔融物冷却。
①熔体造粒工艺优点与常用的复混肥制造工艺相比,熔体造粒工艺具有以下优点:a、可直接利用尿素浓溶液,省去了尿素溶液的喷淋造粒过程(尿液的计量采用质量流量计),以及固体尿素制复混肥料时的破碎操作,简化了生产流程。
b、熔体造粒工艺充分利用原熔融尿素的热能,物料水分含量很低,无需干燥过程,大大节省了能耗。
c、可以生产高氮复合肥,最高氮含量产品为颗粒尿素的生产。
d、合格产品颗粒百分含量很高。
e、颗粒表面光滑、圆润,不结块,具有较高的市场竞争力。
f、操作环境好,无三废排放,属清洁生产工艺,粉尘浓度控制在100 mg/m3。
g、熔体造粒装置基建投资和操作费用通常比常规的固体配料蒸汽造粒装置要低,生产规模大的装置更是如此。
10万吨/年塔式造粒工程装置开车结果表明:a 工艺流程简单,设备少,易操作。
b 产品性能好,颗粒表面光滑、圆润,水分低,只要包装好,产品不结块。
②造粒塔喷淋造粒的主要缺点:a 产品规格受到一定的限制。
造粒所需混合物必须是能形成可流动的熔体,因此借助尿素和硝铵的优势,只能生产40%浓度以上的高氮产品,由于磷酸一铵与尿素的反应机理的存在,将对料浆性态造成较大的影响,因此磷的加入受到限制。
一般要求NPK的配比为N≥20%,P2O5≤10%,钾无非凡限制。
b 产品颗粒大小调节范围较窄,非凡是生产颗粒较大的产品有一定的难度。
由于高温熔体凝固点不高,遇冷即成粒;受颗粒物在塔内的停留时间限制,粒径大,不易冷却,到塔底后反而会被摔变形、不圆滑。
因此粒径多在1—2mm。
c 温度,混合时间,配比,颗粒大小的控制要求比较严格。
d 造粒塔必须有一定的高度,最低75米,普遍在90-95米,对小型生产装置来说,投资费用并不节省。
--------------------------------------------------------------------------------喷浆造粒与氨化造粒的主要区别是在造粒方式上,喷浆造粒是自成粒的粒子以返料的形式形成料幕,与喷出的料浆结合层层涂布,成粒。
而氨化造粒在转鼓中还要通入一定量的气氨,继续中和,并产生热量从而蒸发并带走一部分水分。
它的成粒方式主要是粘结成粒。
虽然工艺上很相似,但是这两者在进入造粒机的料浆水分是不一样的。
喷浆造粒一般30%左右,而氨化造粒一般在15%左右。
高塔造粒主要是物料的熔融造粒,物料的含水量很低,2%左右,成粒方式是自成粒,一般含氮量很高,一般都在20%以上,所以属于速溶速效。
至于,缓控释肥其种类和加工形式多种多样,目前流行的有内质的和外包的两种,内质加入内质剂如尿酶抑制剂和硝化抑制剂,或者是聚天冬氨酸等,外包的则有硫包膜,树酯包膜,以及一些无机包膜象一些磷酸盐类等,还有一些化学控释的如尿甲醛等,生产工艺各有不同。
--------------------------------------------------------------------------------氨化造粒和喷浆造粒的区别:氨化造粒和喷浆造粒相比,是不是说第一次在管式反应器中进行中和反应是一样的,然后喷浆造粒的就直接去造粒机了,而氨化的在转鼓造粒机中又加入气氨,进行第二次中和反应了?也就是说氨化造粒是两次加气氨中和反应,喷浆造粒只加一次气氨中和反应?--------------------------------------------------------------------------------可以这样理解,对于氨化造粒可以是一次中和也可以是两次中和,但是,喷浆造粒与氨化造粒它们的料浆与氨的中和度是不同的,氨化造粒的中和度更高一些,也就是酸碱反应的程度更深一些,因些喷浆造粒的料浆温度一般只有110~120度左右,而氨化造粒的料浆的温度一般在220~280度之间,较之喷浆造粒要高得多。
--------------------------------------------------------------------------------(氨化造粒的中和度更高一些,也就是酸碱反应的程度更深一些)意思是说氨化造粒比喷浆造粒的中和度要高,也就是说氨化造粒的工艺加入的气氨要多一些?也就是说p它们是一种工艺,只不过在中和这个工序,氨化造粒的加入的氨多罢了是这个意思吗?--------------------------------------------------------------------------------不能这么说,虽然表面上,是这样,但是,由于两种料浆的温度、含水量、组成上皆有很大的区别,所以料浆的成粒性也不同,因而造粒方式也不一样,你这样的理解有些以偏概全了,建议先看看一些相关资料和文章。
--------------------------------------------------------------------------------不要拘泥于定义根据自己的生产和设计情况来不要管什么是氨化什么是喷浆难道两个融合在一起生产就不行了吗?氨化一定要使气氨吗,液氨不行吗?敢于突破习惯性思维,根据实际情况来取相应的措施就说这些了,有些关于保密不好具体的多说--------------------------------------------------------------------------------喷浆造粒与氨化造粒的主要区别是在造粒方式上,喷浆造粒是自成粒的粒子以返料的形式形成料幕,与喷出的料浆结合层层涂布,成粒。
氨化造粒在转鼓中还要通入一定量的气氨,继续中和,并产生热量从而蒸发并带走一部分水分。
它的成粒方式主要是粘结成粒喷浆造粒,是把料浆用喷枪喷入造粒机,而氨化造粒是粘结成粒,那么是不是说氨化的就是把料浆慢慢的倒入造粒机内,然后随着造粒机的转动就粘结成粒了?假如是这样的话,那么氨化造粒,在把料浆倒入造粒机内的时候,是不是会结疤呢?来自原料工序的各种固体原料和系统内的返料进入转鼓造粒机由硫酸贮罐来的浓硫酸和来自循环泵的洗涤液,经计量后加入到管式反应器的混合段进行混合稀释,氨站来自的液氨经计量后分为两路,一路通过液氨蒸发器和混合器A与少量蒸汽混合气化,经过管式反应器的中心管进入管式反应器反应段,通过特制的分布器均匀与混合后的稀硫酸反应,生产的高温硫酸氢铵溶液经反应器雾化喷嘴均匀喷到造粒机料层上。
另一路液氨通过液氨蒸发器和混合器B与蒸汽混合气化后,经蒸汽气氨混合分布器进入料层内与经管式反应器来的硫酸氢铵和料层中的磷酸一铵等继续在造粒机内进行反应生产硫酸铵和磷酸二铵,同时放出化学反应热,干、湿物料在造粒机的转动作用下团聚成粒。
如有其它液体原料喷入(如尿液),则硫酸、洗涤液的用量应适当降低,以保证造粒的液相量与热量平衡。
管式反应器排出的水蒸汽以及料层中排出的水蒸汽随造粒尾气排出,造粒尾气与冷却尾气在冷却旋风除尘器出口汇合,经综合尾气沉降室进一步分离粉尘后,由综合尾气风机进入复喷管和洗涤塔进行洗涤吸收,经洗涤后的净化尾气由烟囱排空,洗涤液用泵送至洗涤塔和管式反应器,通过管式反应器后形成蒸汽及高温料浆予以回收。