60钢锻件
CL60钢碳与夹杂物的控制

Abta t Re adn o t e dfiu tc n r lis e fCab n a d icu in o sr c : g r ig t h i c l o to s u s o r o n n l s s f rCL6 se l sd f r t e f o 0 te u e o h
工艺流程见图 1 。 31 熔毕碳的控制 .
求[ ] C 的内控范围不大于 00 %,Mn 的内控范 .4 [ ]
围不 大 于 00 , . 6 才能 满足 组 批 的需 要 。如 C与
在普通 电弧炉冶炼时 , 一般对 要求探伤 的钢 种规 定 0 4 以 上 的 脱 碳 量 , ( . O ~ . 0/ 9 6 在 0 5 12 %) h . O / 的速度下 , 通过[ ] o] c 与[ 反应产 生的 C O气泡造成熔池沸 腾 , 去除钢水中的气体 、 夹杂 物, 并促进钢水 中成分 与温度的均匀 。在具备精
3 工 艺分 析
的铸锻件 , 习惯 了多品种、 单炉或小批 量生产 , 组
织生产 的方式和工人 的操作 等不太适应 于持 续、 稳 定 的批 量 生 产 , 成 产 品 的 质量 时 好 时 坏 。如 造 火车轮用 C 0 的探 伤要求类似转 子钢 , I 钢 6 在相 同工艺条件下 , 要求批量产品的化学成分、 力学性 能的离散性小 , 且能长期稳定生产 。技术 条件要
维普资讯
《 大型铸 锻件 》
H EAVY CAS NG TI AND ORGI F NG
No 3 .
Au u t 0 6 g s 0 2
C 6 L 0钢 碳 与 夹 杂 物 的控 制
王晓 东
金属材料取样规定-钢板、锻件
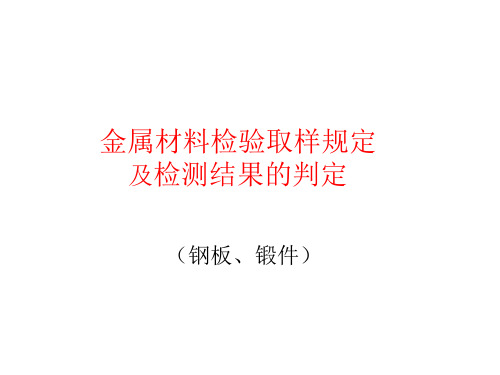
符号
• W——产品的宽度 • t ——产品的厚度(型钢为腿部厚度, 钢管为管壁厚度) • d ——产品的直径(多边形条钢为内切圆直径) • L ——纵向试样(试样纵向轴线与主加工方向 平行) • T ——横向试样(试样纵向轴线与主加工方向 垂直)
型钢取样位置
• 按图1在型钢腿部切取拉伸、弯曲和冲击样坯。 如型钢尺寸不能满足要求,可将取样位置向 中部位移。 • 对于腿部有斜度的型钢,可在腰部1/4处取样 (见图1b和d),经协商也可从腿部取样进行 机加工。 • 对于腿部长度不相等的角钢,可从任一腿部 取样。
试样的制备
• 制备试样时应避免由于机加工使钢表面产 生硬化及过热而影响其力学性能。机加工 最终工序应使试样的表面质量、形状和尺 寸满足相应试验方法标准的要求。 • 当要求标准状态热处理时,应保证试样的 热处理制度与样坯相同。
取样位置
一般要求: • 该标准给出了型钢、条钢、钢板、及钢管的 拉伸、冲击和弯曲试验取样位置 • 应在钢产品表面切取弯曲样坯,弯曲试样应 至少保留一个表面,当机加工和试验机能力 允许时,应制备全截面或全厚度弯曲试样。 • 当要求取一个以上试样时,可在规定位置相 邻处取样。
冷剪样坯所留加工余量按下表选取:
厚度或直径 ( mm) ≤4 >4~10 >10~20 >20~35 >35 加工余量 ( mm) 4 厚度或直径 10 15 20
试料的状态
• 按产品标准规定,取样的状态分为交货状态和标 准状态。 • 在交货状态下取样时,可从以下二种条件中选择: a、产品成型或热处理完成之后取样。 b、如在热处理之前取样,试料应在与产品交货 状态相同的条件下进行热处理。当需要矫直试料 时,应在冷状态下进行,除非产品标准另有规定。 • 在标准状态下取样时,应按产品标准或订货单规 定的生产阶段取样。如必须对试料矫直,可在热 处理之前进行热加工或冷加工,热加工的温度应 低于最终热处理的温度。 • 热处理之前的机加工:当热处理要求试样尺寸较 小时,产品标准应规定样坯的尺寸及加工方法。 • 样坯的热处理应按产品标准或订货单要求进行。
常用锻件牌号及化学成分

化
C
0.23 0.15~ 0.40 1.20~ 1.50
学
≤0.30
成
≤0.25 ≤0.25 ≤0.25 0.50~ ≤0.050 ≤0.020
份
V Nb
0.025~ 0.05
%
Ti Al N B
≤0.025 ≤0.025 ≤0.020
Si
0.40
Mn
1.40 1.30~ 1.60
≤0.30 ≤0.30 ≤0.25 ≤0.30 0.80~ 1.10
备注
低合金钢 低合金钢 低合金钢 低合金钢 低合金钢 低合金钢 低合金钢 低合金钢 低合金钢 低合金钢 低合金钢 低合金钢 低合金钢 低合金钢 低合金钢 低合金钢 低合金钢 低合金钢 低合金钢 低合金钢 低合金钢
≤0.30 0.40~ 1.00~
0.015~ 0.045
≤0.050
≤0.020
≤0.025 ≤0.035
常用锻件材料化学成份一览表
钢 号
20 A105 SA266 1级 SA266 2级 SA266 3级 SA266 4级 SA350 LF1级 SA350 LF2级1类 SA350 LF2级2类 Q245R 35 45 45(远洋) 16Mn Q345B Q345D S355J2G3 Q345R SA516Gr65 SA516Gr70 20MnMo
Cr
Mo
0.35 0.45~ 0.65 0.45~ 0.6 0.25~ 0.5 0.15~ 0.25 0.15~ 0.25
Ni
CU
P
≤0.015 ≤0.015 ≤0.012 ≤0.015 ≤0.040 ≤0.015 ≤0.035
S
锻件标准
NB/T47008-2010 NB/T47008-2010 NB/T47008-2010 NB/T47008-2010 SECTION Ⅱ 2010 SA-29 NB/T47008-2010 GB/T3077
热处理工艺复习题

2017热处理工艺复习题填空题1. 钢的热处理工艺由、、三个阶段所组成。
2. 热处理工艺基本参数:。
3. 钢完全退火的正常温度范围是,它只适应于钢。
4. 球化退火的主要目的是,它主要适用于钢。
5. 钢的正常淬火温度范围,对亚共析钢是,对过共析钢6. 当钢中发生奥氏体向马氏体的转变时,原奥氏体中碳含量越高,则M S点越,转变后的残余奥氏体量就越。
7. 改变钢整体组织的热处理工艺有、、、四种。
8. 淬火钢进行回火的目的是,回火温度越高,钢的强度与硬度越。
9. 化学热处理的基本过程包括、、等三个阶段。
10. 欲消除过共析钢中大量的网状渗碳体应采用,欲消除铸件中枝晶偏析应采用。
11. 低碳钢为了便于切削,常预先进行处理;高碳钢为了便于切削,常预先进行处理;12. 感应加热表面淬火,按电流频率的不同,可分为、、和三种。
而且感应加热电流频率越高,淬硬层越。
13. 钢的淬透性主要取决于————————————,马氏体的硬度主要取决于————————————,钢的表层淬火,只能改变表层的————————————,而化学热处理既能改变表层的————————————,又能改变表层的————————————。
14. 钢在一定条件下淬火后,获得一定深度的淬透层的能力,称为钢的淬透性。
淬透层通常以的深度来表示。
15. 中温回火主要用于处理__ ___ 零件,回火后得到组织。
16.45 钢正火后渗碳体呈呈状。
状,调质处理后渗碳体17. 形变热处理是将塑性变形的强化与热处理时的强化结合,使成型工艺与获得最终性能统一起来的一种综合工艺。
二、单选题1. 电阻炉空载功率小,说明炉子热损失:A)小;B)大;C)厉害;D)可忽略不计。
2. 检测氮碳共渗零件的硬度时应选用:A)洛式硬度计;B)维氏硬度计;C)布氏硬度计;D)肖氏硬度计。
3. 可控气氛炉渗碳时排出的废气:A)必须燃烧后排放;B)不燃烧直接排放;C)通入水中排放; D )通入碱水中排放。
自由锻工艺
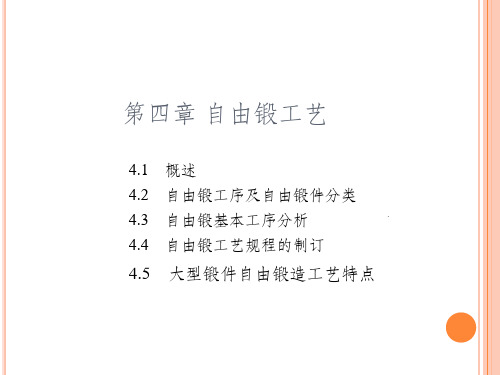
2.确定锻造比
锻造比:表示锻件在锻造成形时变形程度,锻造 比以金属变形前后的横断面积的比值或高度的比 值来表示锻比大小。
KLA 0/AD 02/D 2
KL H0 /H
.
锻造比反映了锻造对锻件组织和力学性能的影响, 是保证锻件品质的一个重要指标。 锻造比大:力学性能好;太大会造成力学性能各 向异性
表4-8 典型锻件的锻造比
.
表4-7 锻造工序锻造比和变形过程总锻造比的计算方法
.
.
➢ 重要锻件:采用镦粗拔长联合工艺,锻比要求 高达6~8。
4.4.4选择锻造设备
常用设备:锻锤和水压机
.
1.理论计算法
根据塑性成形原理建立的公式算出锻件成形所需的最大变 形力(或变形功),选取设备吨位。
(1)在水压机上锻造 (2)在锻锤上锻造 在锻锤上自由锻时,由于其打击力是不定的, 所以应根据锻件成形所需变形功来计算设备的打击能量或吨位。
.
α
单垫环镦粗
3.局部镦粗
坯料只在局部长度上产生鐓粗变形。
.
刚端
图4-19 局部镦粗
1、坯料局部鐓粗时, 按杆部选择坯料直径 2、H头/D0≤3
对于头部大杆部细小的杆件,选大于杆部直径的坯料
.
图4-20 头大杆细类锻件的局部镦粗
4.3.3 冲孔
在坯料上用冲子冲出通孔或不通孔(盲孔)的锻造工序。
.
图4-53 在垫环上冲孔 1—冲子 2—坯料 3—垫环 4—芯料
4.3.4 扩孔
扩孔:减小空心坯料壁厚而增加其内外径的锻造工序, 用以锻造各种圆环锻件。
分类:
1.冲子扩孔(胀形扩孔)
2.芯轴扩孔(拔长扩孔)
3.辗压扩孔(拔长扩孔)
锻造工艺规范
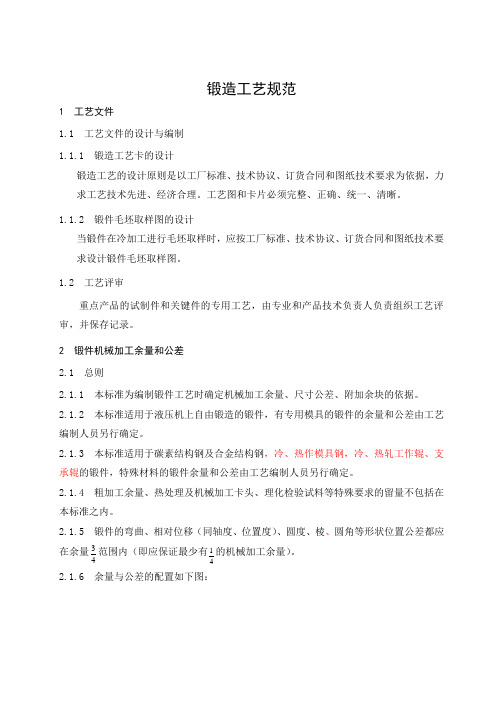
锻造工艺规范1 工艺文件1.1 工艺文件的设计与编制 1.1.1 锻造工艺卡的设计锻造工艺的设计原则是以工厂标准、技术协议、订货合同和图纸技术要求为依据,力求工艺技术先进、经济合理。
工艺图和卡片必须完整、正确、统一、清晰。
1.1.2 锻件毛坯取样图的设计当锻件在冷加工进行毛坯取样时,应按工厂标准、技术协议、订货合同和图纸技术要求设计锻件毛坯取样图。
1.2 工艺评审重点产品的试制件和关键件的专用工艺,由专业和产品技术负责人负责组织工艺评审,并保存记录。
2 锻件机械加工余量和公差 2.1 总则2.1.1 本标准为编制锻件工艺时确定机械加工余量、尺寸公差、附加余块的依据。
2.1.2 本标准适用于液压机上自由锻造的锻件,有专用模具的锻件的余量和公差由工艺编制人员另行确定。
2.1.3 本标准适用于碳素结构钢及合金结构钢,冷、热作模具钢,冷、热轧工作辊、支承辊的锻件,特殊材料的锻件余量和公差由工艺编制人员另行确定。
2.1.4 粗加工余量、热处理及机械加工卡头、理化检验试料等特殊要求的留量不包括在本标准之内。
2.1.5 锻件的弯曲、相对位移(同轴度、位置度)、圆度、棱、圆角等形状位置公差都应在余量43范围内(即应保证最少有41的机械加工余量)。
2.1.6 余量与公差的配置如下图:D :零件尺寸 C :锻件公称尺寸(基本尺寸) C ′:锻件最大尺寸 C ″:锻件最小尺寸 а:锻件名义机械加工余量δ′:下偏差(负公差) δ″:上偏差(正公差)2.1.7 本规范未包括的特殊形状的锻件及尺寸超出本规范的锻件,其余量和公差由工艺编制人员参照本规范确定。
2.1.8 在确定锻件余量时,必须兼顾零件的局部尺寸与整体尺寸的关系,局部应照顾整体,以减少加工余量。
2.1.9 易焊钢种和留有粗加工余量在粗加工后允许存在可以加工掉的局部黑皮的锻件,其锻造余量应比本标准表中规定值减少10~20%(按复杂程度)。
对易产生裂纹又不易焊补钢种(如9Cr2Mo 、32Cr2MnMo 、60CrMnMo )等锻件的余量不应比表中规定值减少。
压力容器用钢锻件标准简介(201101)-28页精选文档

中国通用机械工程总公司 秦晓钟
2019年1月
一、NB/T47008-2019
《承压设备用碳素钢和合金钢锻件》
1. 钢 号
标 准 JB4726-2000
NB/T47008-2019
钢号
11个钢号
16个钢号 增加20MnNiMo、15NiCuMoNb、
12Cr2Mo1V、12Cr3Mo1V、 10Cr9Mo1VNb
ASME(2019) SA336 F22 0.05~0.15 2.00~2.50 0.90~1.10 ≤0.025 ≤0.025
——
5. 20MnNiMo钢锻件
标准
NB/T47008-2019
钢号
20MnNiMo
Ni %
0.40~1.00
Mo %
0.45~0.60
P%
≤0.020
S%
≤0.012
KV2 (KV8) J -20℃,≥41
NB/T47009-2019
钢号
5个钢号
6个钢号 增加08Ni3D
2. 16MnD钢锻件
标准
P% S% 公称厚度 mm
JB4727-2000 ≤0.025 ≤0.015
≤300
NB/T47009-2019 ≤0.025 ≤0.012
≤100 >200~300
Rm MPa 450~600 480~630 450~600
0.06~0.12 1.20~1.60 0.45~0.85
≤0.020 ≤0.010 -70℃,≥60
ASME(2019) SA3.035 ≤0.040 -59℃,≥20
6. 08Ni3D钢锻件
标准 钢号 C% Ni % P% S% KV2 (KV8) J
长安大学机械工程材料复习资料
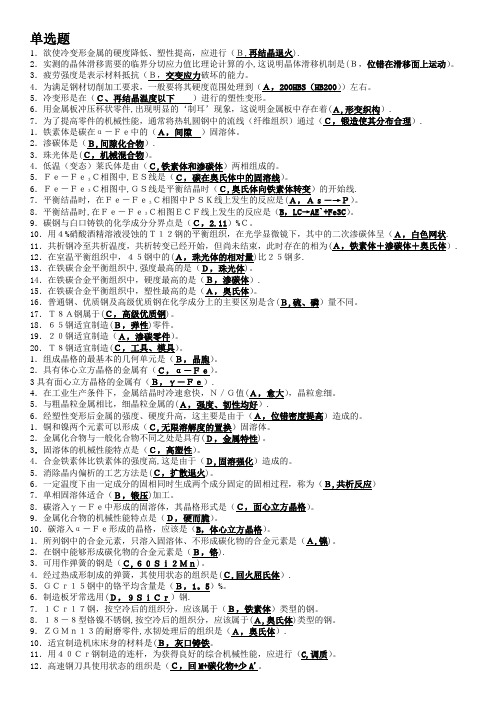
单选题1.欲使冷变形金属的硬度降低、塑性提高,应进行(B,再结晶退火).2.实测的晶体滑移需要的临界分切应力值比理论计算的小,这说明晶体滑移机制是(B,位错在滑移面上运动)。
3.疲劳强度是表示材料抵抗(B,交变应力破坏的能力。
4.为满足钢材切削加工要求,一般要将其硬度范围处理到(A,200HBS(HB200))左右。
5.冷变形是在(C、再结晶温度以下)进行的塑性变形。
6.用金属板冲压杯状零件,出现明显的‘制耳’现象,这说明金属板中存在着(A,形变织构).7.为了提高零件的机械性能,通常将热轧圆钢中的流线(纤维组织)通过(C,锻造使其分布合理).1.铁素体是碳在α-Fe中的(A,间隙)固溶体。
2.渗碳体是(B,间隙化合物).3.珠光体是(C,机械混合物)。
4.低温(变态)莱氏体是由(C,铁素体和渗碳体)两相组成的。
5.Fe-Fe3C相图中,ES线是(C,碳在奥氏体中的固溶线)。
6.Fe-Fe3C相图中,GS线是平衡结晶时(C,奥氏体向铁素体转变)的开始线.7.平衡结晶时,在Fe-Fe3C相图中PSK线上发生的反应是(A,As-→P)。
8.平衡结晶时,在Fe-Fe3C相图ECF线上发生的反应是(B,LC→AE`+Fe3C)。
9.碳钢与白口铸铁的化学成分分界点是(C,2.11)%C。
10.用4%硝酸酒精溶液浸蚀的T12钢的平衡组织,在光学显微镜下,其中的二次渗碳体呈(A,白色网状. 11.共析钢冷至共析温度,共析转变已经开始,但尚未结束,此时存在的相为(A,铁素体+渗碳体+奥氏体). 12.在室温平衡组织中,45钢中的(A,珠光体的相对量)比25钢多.13.在铁碳合金平衡组织中,强度最高的是(D,珠光体)。
14.在铁碳合金平衡组织中,硬度最高的是(B,渗碳体).15.在铁碳合金平衡组织中,塑性最高的是(A,奥氏体)。
16.普通钢、优质钢及高级优质钢在化学成分上的主要区别是含(B,硫、磷)量不同。
17.T8A钢属于(C,高级优质钢)。
- 1、下载文档前请自行甄别文档内容的完整性,平台不提供额外的编辑、内容补充、找答案等附加服务。
- 2、"仅部分预览"的文档,不可在线预览部分如存在完整性等问题,可反馈申请退款(可完整预览的文档不适用该条件!)。
- 3、如文档侵犯您的权益,请联系客服反馈,我们会尽快为您处理(人工客服工作时间:9:00-18:30)。
60钢锻件
材料名称:优质碳素结构钢
牌号:60
标准:GB/T 699-1999
对应日本牌号:S58C
对应德国牌号:C60(1.0601),CK60(1.1221),Cm60(1.1223)
对应美国牌号:1060
供应:山西永鑫生锻造
●特性及适用范围:
60号钢为亚共析钢,强度、硬度和弹性都很高,冷变形时塑性较低,切削性较差,焊接和淬透性差,水淬有产生裂纹倾向,大型制件多采用正火。
60号钢用于制造轴、弹簧圈、轮轴、各种垫圈、凸轮、钢绳等受力较大、在摩擦条件下工作,要求较高强度、耐磨性和一定弹性的零件。
2模具修补领域
它是唯一接合性较好之中硬度钢焊条,适用于空冷钢、铸钢:如ICD5、
7CrSiMnMoV…等等。
汽车板金覆盖件模具及大型五金板金冲压模具之拉延、拉伸部位修补,也可用于硬面制作。
另外在使用时也有一些需要注意的:
1. 于潮湿场地施工前,焊条先以150-200°C烘干30-50分钟。
2. 通常施以200°C以上预热,焊接后空冷,可能的话最好实施应力消除。
3. 需多层堆焊处,以CMC-E30N打底,可得到较好的焊接效果。
硬度 HRC 48-52
主要成份 Cr Si Mn C
适用电流范围:
直径及长度m/m 3.2*350mm 4.0*350mm
电流范围(Amp) 70-100 130-150
360号钢化学成分
●化学成份:
碳 C :0.57~0.65
硅 Si:0.17~0.37
锰 Mn:0.50~0.80
硫 S :≤0.035
磷 P :≤0.035
铬 Cr:≤0.25
镍 Ni:≤0.25铜 Cu:≤0.25
4力学性能
●力学性能:
抗拉强度σb (MPa):≥675(69)
屈服强度σs (MPa):≥400(41)
伸长率δ5 (%):≥12
断面收缩率ψ (%):≥35
硬度:未热处理≤255HB;退火钢≤229HB
试样尺寸:试样尺寸为25mm
●热处理规范及金相组织:
热处理规范:正火,810℃。
●交货状态:以不热处理或热处理(退火、正火或高温回火)状态交货。
要求热处理状态交货的应在合同中注明,未注明者按不热处理交货。