热处理裂纹的修补方法【汇总】
加热炉耐火衬里裂缝修补方法
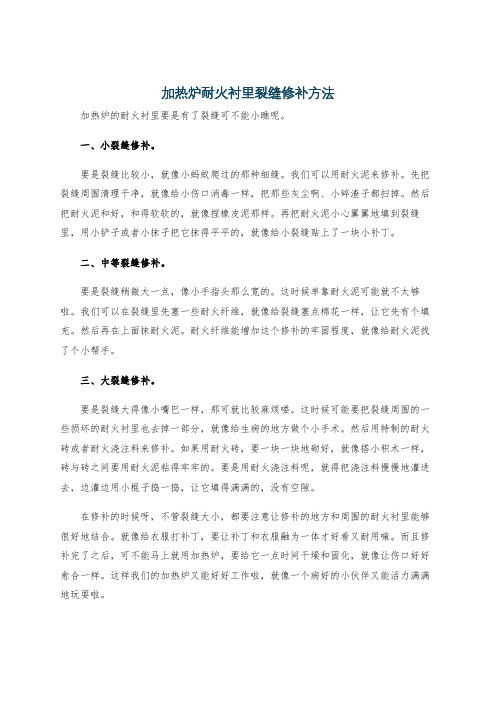
加热炉耐火衬里裂缝修补方法
加热炉的耐火衬里要是有了裂缝可不能小瞧呢。
一、小裂缝修补。
要是裂缝比较小,就像小蚂蚁爬过的那种细缝。
我们可以用耐火泥来修补。
先把裂缝周围清理干净,就像给小伤口消毒一样,把那些灰尘啊、小碎渣子都扫掉。
然后把耐火泥和好,和得软软的,就像捏橡皮泥那样。
再把耐火泥小心翼翼地填到裂缝里,用小铲子或者小抹子把它抹得平平的,就像给小裂缝贴上了一块小补丁。
二、中等裂缝修补。
要是裂缝稍微大一点,像小手指头那么宽的。
这时候单靠耐火泥可能就不太够啦。
我们可以在裂缝里先塞一些耐火纤维,就像给裂缝塞点棉花一样,让它先有个填充。
然后再在上面抹耐火泥。
耐火纤维能增加这个修补的牢固程度,就像给耐火泥找了个小帮手。
三、大裂缝修补。
要是裂缝大得像小嘴巴一样,那可就比较麻烦喽。
这时候可能要把裂缝周围的一些损坏的耐火衬里也去掉一部分,就像给生病的地方做个小手术。
然后用特制的耐火砖或者耐火浇注料来修补。
如果用耐火砖,要一块一块地砌好,就像搭小积木一样,砖与砖之间要用耐火泥粘得牢牢的。
要是用耐火浇注料呢,就得把浇注料慢慢地灌进去,边灌边用小棍子捣一捣,让它填得满满的,没有空隙。
在修补的时候呀,不管裂缝大小,都要注意让修补的地方和周围的耐火衬里能够很好地结合。
就像给衣服打补丁,要让补丁和衣服融为一体才好看又耐用嘛。
而且修补完了之后,可不能马上就用加热炉,要给它一点时间干燥和固化,就像让伤口好好愈合一样。
这样我们的加热炉又能好好工作啦,就像一个病好的小伙伴又能活力满满地玩耍啦。
焊接热裂纹产生的原因及解决方法

焊接热裂纹产生的原因及解决方法焊接裂纹是最危险的焊接缺陷,严重地影响着焊接结构的使用性能和安全可靠性,许多焊接结构的破坏事故,都是焊接裂纹引起的。
裂纹除了降低焊接接头的强度外,不因裂纹的末端有一个尖锐的缺口,将引起严重的应力集中,促使裂纹的发展和焊接结构破坏。
根据形成焊接裂纹的温度可分为热裂纹和冷裂纹,根据裂纹发生的位置可分为焊缝金属中的裂纹和热影响中的裂纹。
热裂纹在焊接过程中,焊缝和热影响区金属冷却到固相线附近的高温区产生的焊接裂纹。
1)热裂纹的形成在焊缝金属中的热裂纹也称为凝固裂纹。
由于被焊接的材料大多都是合金,而合金凝固自开始到最终结束,是在一定的温度区间内进行的,,这是热裂纹产生关系到的基本原因。
焊缝金属中的许多杂质的凝固温度都低于焊缝金属的凝固温度,这样首先凝固的焊缝金属把低熔点的杂质推挤到凝固结晶的晶粒边界,形成了一层液体薄膜,又因为焊接时熔池的冷却速度很大,焊缝金属在冷却的过程中发生收缩,使焊缝金属内产生拉应力,拉应力把凝固的焊缝金属沿晶粒边界拉开,又没有足够的液体金属补充时,就会形成微小的裂纹,随着温度的继续下降,拉应力增大,裂纹不断扩大,这就是凝固裂纹。
当焊缝金属中含有较多的低熔点杂质时,焊缝金属极易产生凝固裂纹,母材和焊接材料中含有害杂质,特别是硫。
硫在钢中与铁化合形成硫化亚铁(FeS),硫化亚铁义与铁发牛反应形成一种共晶物质,凝固温度为988°远低丁钢铁的凝固温度,所以硫足引起钢材焊缝金属中发生凝固裂纹的最主要的元素。
另外,钢材中含碳量较高时,有利于硫在晶界处富集,因而也是促进形成凝固裂纹的原因,所以采用含碳量低的焊接材料有利于防止凝固裂纹的产生。
在热影响区熔合线附近产生的热裂纹称为液化裂纹或称热撕裂。
多层焊时,前一焊层的一部分即为后一焊层的热影响区,所以液化裂纹也可能在焊缝层间的融化线附近产生。
液化裂纹产生的原因基本与凝固裂纹相似。
这种裂纹可以成为冷裂纹的裂纹源,所以危害也很大。
金属材料热处理变形及开裂问题的解决措施
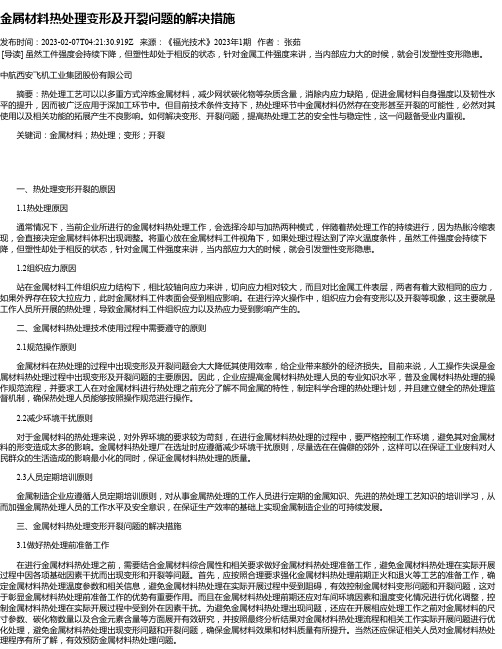
金属材料热处理变形及开裂问题的解决措施发布时间:2023-02-07T04:21:30.919Z 来源:《福光技术》2023年1期作者:张茹[导读] 虽然工件强度会持续下降,但塑性却处于相反的状态,针对金属工件强度来讲,当内部应力大的时候,就会引发塑性变形隐患。
中航西安飞机工业集团股份有限公司摘要:热处理工艺可以以多重方式淬炼金属材料,减少网状碳化物等杂质含量,消除内应力缺陷,促进金属材料自身强度以及韧性水平的提升,因而被广泛应用于深加工环节中。
但目前技术条件支持下,热处理环节中金属材料仍然存在变形甚至开裂的可能性,必然对其使用以及相关功能的拓展产生不良影响。
如何解决变形、开裂问题,提高热处理工艺的安全性与稳定性,这一问题备受业内重视。
关键词:金属材料;热处理;变形;开裂一、热处理变形开裂的原因1.1热处理原因通常情况下,当前企业所进行的金属材料热处理工作,会选择冷却与加热两种模式,伴随着热处理工作的持续进行,因为热胀冷缩表现,会直接决定金属材料体积出现调整。
将重心放在金属材料工件视角下,如果处理过程达到了淬火温度条件,虽然工件强度会持续下降,但塑性却处于相反的状态,针对金属工件强度来讲,当内部应力大的时候,就会引发塑性变形隐患。
1.2组织应力原因站在金属材料工件组织应力结构下,相比较轴向应力来讲,切向应力相对较大,而且对比金属工件表层,两者有着大致相同的应力,如果外界存在较大拉应力,此时金属材料工件表面会受到相应影响。
在进行淬火操作中,组织应力会有变形以及开裂等现象,这主要就是工作人员所开展的热处理,导致金属材料工件组织应力以及热应力受到影响产生的。
二、金属材料热处理技术使用过程中需要遵守的原则2.1规范操作原则金属材料在热处理的过程中出现变形及开裂问题会大大降低其使用效率,给企业带来额外的经济损失。
目前来说,人工操作失误是金属材料热处理过程中出现变形及开裂问题的主要原因。
因此,企业应提高金属材料热处理人员的专业知识水平,普及金属材料热处理的操作规范流程,并要求工人在对金属材料进行热处理之前充分了解不同金属的特性,制定科学合理的热处理计划,并且建立健全的热处理监督机制,确保热处理人员能够按照操作规范进行操作。
修复铸铁裂纹的所有方法

修复铸铁裂纹的所有方法铸铁裂纹的修复在许多工业应用中均为非常重要的一环,这也是一项非常复杂而技术性强的工作。
它不仅能够使铸件外观得到改善,而且还可以延长铸件的使用寿命,增加其强度和性能。
因此,修复铸铁裂纹的所有方法值得我们来探讨。
首先,让我们了解一下热修复。
通常情况下,热修复指在铸铁表面上进行焊接操作以彻底修复裂纹,并确保其表面平整、美观和无缺陷。
焊缝处可以使用铜粉、铝粉或者小晶粒铁等熔剂材料来对该部位进行填充,然后由起飞机等特殊设备将物料进行热熔态填充;最后,使用喷涂技术使其完成修复。
其次,我们可以尝试使用焊缝补强的方式来修复裂纹。
这种方法的基本原理就是在不改变铸铁表面外形的情况下,通过焊接弊航或者小晶粒铁来补强破裂处。
常见的焊接该等材料有:填充焊、钎焊、溅射焊、超声波焊等。
这种方法在处理小裂纹时尤其有效。
第三,可以扩大铸铁模具或者模板的孔径,来修复裂纹。
这种方法的基本思路是通过扩大模具的孔径,将裂纹部位的材料平均分布,从而彻底填平裂纹并使之不至于在运动时被撞击或拉伸损坏,以此达到修补裂纹的目的。
此外,如果裂纹太多或太深,也可以使用塑性变形的方式来将这些裂纹补平。
最后,也可以使用无损检测技术来检测铸铁表面是否存在裂纹,以便及时发现并进行修补。
无损检测技术主要有:磁粉检测、超声检测、核磁共振检测、X射线检测等。
通过这些检测技术,可以更准确地定位到不同表面的裂纹,并做出更加有效的修补方案。
总而言之,修复铸铁裂纹的所有方法有许多,包括热修复、焊缝补强、扩大模具孔径和无损检测等方法,它们都能够有效地修复铸铁表面上的裂纹。
对于每种方法,我们都需要更深入地去研究和未来使用,以更好地修复和保养铸铁件。
模具钢淬火中的裂纹分析及解决方案
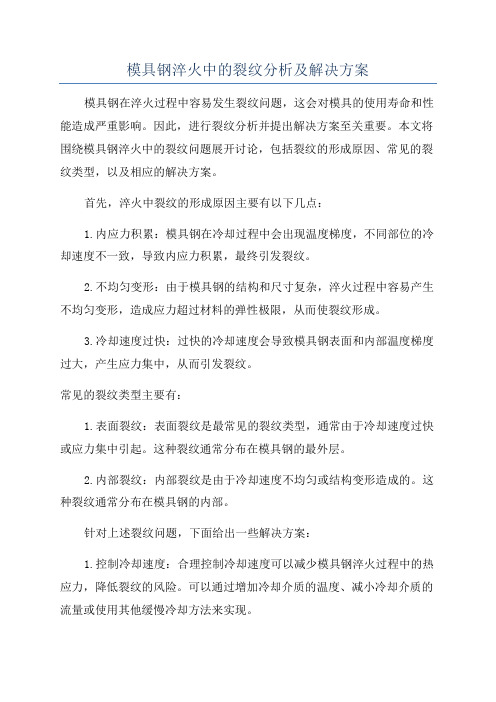
模具钢淬火中的裂纹分析及解决方案模具钢在淬火过程中容易发生裂纹问题,这会对模具的使用寿命和性能造成严重影响。
因此,进行裂纹分析并提出解决方案至关重要。
本文将围绕模具钢淬火中的裂纹问题展开讨论,包括裂纹的形成原因、常见的裂纹类型,以及相应的解决方案。
首先,淬火中裂纹的形成原因主要有以下几点:1.内应力积累:模具钢在冷却过程中会出现温度梯度,不同部位的冷却速度不一致,导致内应力积累,最终引发裂纹。
2.不均匀变形:由于模具钢的结构和尺寸复杂,淬火过程中容易产生不均匀变形,造成应力超过材料的弹性极限,从而使裂纹形成。
3.冷却速度过快:过快的冷却速度会导致模具钢表面和内部温度梯度过大,产生应力集中,从而引发裂纹。
常见的裂纹类型主要有:1.表面裂纹:表面裂纹是最常见的裂纹类型,通常由于冷却速度过快或应力集中引起。
这种裂纹通常分布在模具钢的最外层。
2.内部裂纹:内部裂纹是由于冷却速度不均匀或结构变形造成的。
这种裂纹通常分布在模具钢的内部。
针对上述裂纹问题,下面给出一些解决方案:1.控制冷却速度:合理控制冷却速度可以减少模具钢淬火过程中的热应力,降低裂纹的风险。
可以通过增加冷却介质的温度、减小冷却介质的流量或使用其他缓慢冷却方法来实现。
2.合理设计模具结构:模具的设计结构应该避免尖角和过于薄壁的部位,以减少应力集中导致的裂纹。
在可能的情况下,可以添加过渡圆角和半径,有助于减少裂纹的风险。
3.适当的预处理:通过适当的热处理工艺可以改善模具钢的力学性能和织构,减少应力集中和变形,降低裂纹的发生。
这包括应用回火、退火和正火等热处理方法。
4.使用有效的质量控制措施:在制造模具钢过程中,需要严格控制原材料的质量,以确保材料的均匀性和稳定性。
此外,必须严格控制加工中的工艺参数,以确保产品的质量。
总结起来,模具钢淬火中的裂纹问题对模具的使用寿命和性能都有很大的影响。
针对裂纹的形成原因和类型,我们可以通过控制冷却速度、合理设计模具结构、适当的预处理和使用有效的质量控制措施等方面来解决这一问题。
解决冲压模具热处理变形和开裂的有效方法

解决冲压模具热处理变形和开裂的有效方法预备热处理对于共析钢的冲压模具锻件,应先进展正火处理,然后进展球化退火,以消除锻件内网状二次渗碳体,细化晶粒,消除内应力,并为后续(或最终)热处理作好组织准备。
冲压凹模零件淬火前,应先进展低温回火(稳定化处理)。
对一些形状较为复杂、精度要求高的凹模,在粗加工后精加工前,应先进展调质处理,以减少淬火变形,尽量防止开裂倾向,并为最终热处理作好组织准备。
优化淬火、回火处理工艺加热温度确实定淬火加热温度过高,使得奥氏体晶粒粗大,且会造成氧化、脱碳现象,零件变形与开裂的倾向增大。
在规定的加热温度范围内,淬火加热温度偏低那么会造成零件内孔收缩,孔径尺寸变小。
故应选用加热温度标准的上限植;而对于合金钢,加热温度偏高,那么会引起内孔膨胀,孔径尺寸变大,因此应选用加热温度的下限值为宜。
加热方式的改良对于一些小型的'冲压凸凹模或细长的圆柱形零件(如小冲头),可事先预热至520--580℃,然后放入中温盐浴炉内加热至淬火温度,比直接使用电炉或反射炉加热淬火零件变形明显减小,且能控制开裂倾向。
尤其是高合金钢模具零件,正确的加热方式为:先预热(温度为530--560℃),然后升至淬火温度。
加热过程中应尽量缩短高温段时间,以减少淬火变形及防止小裂纹的消费。
回火处理的控制模具零件从冷却剂中取出后,不宜在空气中停留较长时间,应及时放入回火炉中进展回火处理。
回火处理时,应防止低温回火脆性和高温回火脆性。
对于一些精度要求的模具零件,淬火后采用屡次回火处理,以消除内应力,减小变形,防止开裂倾向。
线切割前的淬火处理对于一些线切割加工的冲压模零件,线切割加工之前应采用分级淬火和屡次回火(或高温回火)热处理工艺,以进步零件的淬透性,并使其内应力分布趋于均匀,且处于较小内应力状态。
内应力越小,线切割后的变形和开裂的倾向性就越小。
冷却方式的优化当零件从加热炉中取出放入冷却剂之前,应放置在空气中适当预冷,随后放入冷却剂中淬火,这是减小零件淬火变形及防止零件开裂倾向的有效方法之一。
几种热处理补救措施
几种热处理补救措施热处理是金属材料加工中的重要工艺之一,它能够通过改变材料的组织结构,提高其力学性能和使用寿命。
然而,在热处理过程中,有时会出现一些问题,例如材料变形、裂纹、变色等。
为了解决这些问题,我们可以采取以下几种热处理补救措施。
合理控制热处理温度是解决问题的关键。
热处理温度直接影响到材料的组织结构和性能。
如果温度过高或过低,都会导致材料的力学性能下降。
因此,在进行热处理之前,需要根据材料的种类和要求确定合适的处理温度,并严格控制在一个合理范围内。
热处理时间也是影响材料性能的重要因素。
过短的时间可能导致组织结构未完全转变,而过长的时间则可能导致材料过度退火,失去原有的力学性能。
因此,在进行热处理时,需要根据材料的特性和要求确定合适的处理时间,并严格控制在一个适当的范围内。
热处理过程中的冷却速率也需要注意。
不同的材料对应不同的冷却速率要求。
如果冷却速率过快,可能导致材料的组织结构不稳定,出现裂纹或变形等问题;而冷却速率过慢,则可能导致材料的硬度不够,性能不达标。
因此,在进行热处理时,需要根据材料的特性和要求选择合适的冷却方式和速率,并确保在整个过程中能够得到良好的控制。
热处理中的环境气氛也需要考虑。
不同的材料对应不同的气氛要求。
有些材料需要在氧化环境中进行热处理,以提高其表面硬度和耐腐蚀性;而有些材料则需要在惰性气氛中进行热处理,以减少氧化和变色。
因此,在进行热处理时,需要根据材料的特性和要求选择合适的环境气氛,并确保能够得到良好的控制和保护。
热处理后的材料还需要进行适当的后续处理。
例如,对于某些材料,可能需要进行退火、回火、淬火等附加热处理工艺,以进一步调整其组织结构和性能,达到最佳效果。
因此,在进行热处理后,需要根据材料的特性和要求进行适当的后续处理,以确保最终获得符合要求的产品。
热处理是一项复杂的工艺,需要综合考虑多个因素,并进行合理的控制。
通过合理控制热处理温度、时间和冷却速率,选择合适的环境气氛,以及进行适当的后续处理,可以有效解决热处理过程中出现的问题,提高材料的力学性能和使用寿命。
热处理淬火十种裂纹分析与措施
热处理淬火十种裂纹分析与方法-4-161、纵向裂纹裂纹呈轴向, 形状细而长。
当模具完全淬透即无心淬火时, 心部转变为比容最大淬火马氏体,产生切向拉应力, 模具钢含碳量愈高, 产生切向拉应力愈大, 当拉应力大于该钢强度极限时造成纵向裂纹形成。
以下原因又加剧了纵向裂纹产生: (1)钢中含有较多S、P、***、Bi、Pb、Sn、As等低熔点有害杂质, 钢锭轧制时沿轧制方向呈纵向严重偏析分布, 易产生应力集中形成纵向淬火裂纹, 或原材料轧制后快冷形成纵向裂纹未加工掉保留在产品中造成最终淬火裂纹扩大形成纵向裂纹; (2)模具尺寸在钢淬裂敏感尺寸范围内(碳工具钢淬裂危险尺寸为8-15mm, 中低合金钢危险尺寸为25-40mm)或选择淬火冷却介质大大超出该钢临界淬火冷却速度时均易形成纵向裂纹。
预防方法: (1)严格原材料入库检验, 对有害杂质含量超标钢材不投产; (2)尽可能选择真空冶炼, 炉外精炼或电渣重熔模具钢材; (3)改善热处理工艺, 采取真空加热、保护气氛加热和充足脱氧盐浴炉加热及分级淬火、等温淬火; (4)变无心淬火为有心淬火即不完全淬透, 取得强韧性高下贝氏体组织等方法, 大幅度降低拉应力, 能有效避免模具纵向开裂和淬火畸变。
2、横向裂纹裂纹特征是垂直于轴向。
未淬透模具, 在淬硬区与未淬硬区过渡部分存在大拉应力峰值, 大型模具快速冷却时易形成大拉应力峰值, 因形成轴向应力大于切向应力, 造成产生横向裂纹。
铸造模块中S、P.***, Bi, Pb, Sn, As等低熔点有害杂质横向偏析或模块存在横向显微裂纹, 淬火后经扩展形成横向裂纹。
预防方法: (1)模块应合理铸造, 原材料长度与直径之比即铸造比最好选在2—3之间, 铸造采取双十字形变向铸造, 经五镦五拔多火铸造, 使钢中碳化物和杂质呈细、小, 匀分布于钢基体, 铸造纤维组织围绕型腔无定向分布, 大幅度提升模块横向力学性能, 降低和消除应力源; (2)选择理想冷却速度和冷却介质: 在钢Ms点以上快冷, 大于该钢临界淬火冷却速度, 钢中过冷奥氏体产生应力为热应力, 表层为压应力, 内层为张应力, 相互抵消, 有效预防热应力裂纹形成, 在钢Ms—Mf之间缓冷, 大幅度降低形成淬火马氏体时组织应力。
金属合金结构裂纹的修复方法
金属合金结构裂纹的修复方法裂纹是金属合金结构中常见的缺陷,如果不及时修复,可能导致结构的破坏和功能的丧失。
本文将介绍一些常用的金属合金结构裂纹修复方法,以帮助解决这一问题。
1. 线焊修复线焊修复是一种常见的金属合金结构裂纹修复方法。
它包括以下步骤:- 清洁和准备:首先,清洁裂纹周围的金属表面,并对裂纹进行准确的标记和测量。
- 焊接准备:接下来,选择合适的焊条或焊丝,并进行预热和熔化金属表面。
- 焊接过程:将焊条或焊丝焊接到裂纹上,通过熔化金属,填充和覆盖裂纹。
- 后续处理:最后,冷却焊接部位,并对修复区域进行美化和检查。
线焊修复方法简单快捷,并且可以应用于各种金属合金结构的裂纹修复,但是需要技术人员具备一定的焊接技能和经验。
2. 电弧焊修复电弧焊修复是另一种常用的金属合金结构裂纹修复方法。
其步骤如下:- 清洁和准备:与线焊修复相似,首先需要清洁和标记裂纹,确保修复过程的准确性。
- 焊接准备:选择适当的电极和焊接工艺参数,并预热裂纹区域。
- 焊接过程:使用电弧焊机进行焊接,通过生成高温的电弧将焊剂融化填充到裂纹中。
- 后续处理:冷却焊接部位,并进行后续的检查和修整。
电弧焊修复方法可以适用于多种金属合金结构的裂纹修复,但需要技术人员具备良好的焊接技能和掌握焊接工艺知识。
3. 热处理修复热处理修复是一种利用金属的热膨胀性质修复裂纹的方法。
其步骤如下:- 清洁和准备:同样,首先需要清洁和标记裂纹,以确保修复过程的准确性。
- 热处理:将金属结构加热至一定温度,使其膨胀,从而关闭裂纹。
- 冷却和处理:将加热的金属结构冷却,并对修复区域进行后续的处理和检查。
热处理修复方法相对简单,但不能适用于所有类型的金属合金结构。
它需要掌握合适的热处理参数和技术。
总结起来,线焊修复、电弧焊修复和热处理修复是常见的金属合金结构裂纹修复方法,其中线焊修复和电弧焊修复需要一定的焊接技能和经验。
根据实际情况选择合适的修复方法,并严格按照操作规程进行操作,以保证修复的质量和可靠性。
分析金属材料热处理变形问题及开裂问题的解决措施
分析金属材料热处理变形问题及开裂问题的解决措施摘要:金属材料性能全面提升的最为有效途径就是热处理,但是在实际的热处理过程中,最不可避免的问题,就是热处理变形和开裂问题,其对工件的加工和后续的交付非常不利。
基于此,本篇文章对金属材料热处理变形问题及开裂问题的解决措施进行深入的分析和探讨。
关键词:金属材料热处理变形问题开裂问题前言:所谓金属材料的热处理,其主要就是以固态金属具体的工艺制造需求,将相应的加热和保温以及冷却处理实施进来,与此同时,还要将相应的机械作用和化学作用辅助配合进来,改变金属材料的内部结构,改变其性能,进而将符合工艺需求的金属产品制造出来。
1.热处理变形开裂的主要原因在金属材料的热处理中,主要存在两种类型的变形,首先就是尺寸变形,其次就是形状变形,而对于大部分的类型而言,其都是金属材料本身在接受热处理的过程中,工件内部的应力进一步导致。
而实际的内应力不同,则又分为两种应力类型,一种为组织应力,另一种为热应力。
而金属材料工件本身会出现变硬的问题,主要原因就是这两种应力因素结合到一起的成果,远远的超出了应力自身的变形极限,进而出现永久变形的问题。
1.1.热处理引起的开裂与变形因素在金属材料的热处理中,主要包含冷却和加热这两个过程中。
而且在实际的热处理过程中,相应的金属工件要经过热胀冷缩处理,而实际的体积变化非常明显。
对于金属材料工件而言,其在达到相应的淬火温度时,会明显的降低工件屈服强度,提高工件塑性,在热处理金属的过程中,金属屈服强度无法超越内应力,则实际的塑性变性进一步发生。
1.1.组织应力引起的变形和开裂因素对于金属材料工件而言,相应的组织应力具备两个非常明显的特点:首先,就是实际的切向应力要远远的大于轴向应力,而且与金属工件表层十分贴近;其次,就是对于金属工件表面而言,其本身主要会受到拉应力的影响,与此同时,内部则受到压应力。
对于组织应力而言,其本身在经历工件淬火的过程中,之所以会发生形变和开裂的问题,其根本原因就是在实际的热处理过程中,受到了组织应力和热应力的综合影响。
- 1、下载文档前请自行甄别文档内容的完整性,平台不提供额外的编辑、内容补充、找答案等附加服务。
- 2、"仅部分预览"的文档,不可在线预览部分如存在完整性等问题,可反馈申请退款(可完整预览的文档不适用该条件!)。
- 3、如文档侵犯您的权益,请联系客服反馈,我们会尽快为您处理(人工客服工作时间:9:00-18:30)。
热处理裂纹的修补方法
内容来源网络,由深圳机械展收集整理!
一渗碳
(1)浓度过高:可将工件在中性介质中加热到正火温度,是碳在中性介质气氛中向内部扩散,减低表面浓度。
(2)浓度不够:可重新升温再渗。
(3)渗层脱碳:可重新进行一次短时渗碳
(4)淬火后硬度过低出现大量残余奥氏体:将工件进行高温回火,保温可延长,使残余奥氏体及马氏体转变为珠光体,随后在750——780低温淬火,此时合金元素和碳均不能完全溶解于奥氏体,淬火就可减少残余奥氏体含量。
二氮化
1.硬度不够的主要原因:
(1)氮化温度过高或者一度过高
(2)第一阶段氮的分解率过高
(3)氮化时间过短,氮化层太薄
(4)炉罐新换,氮气没适度增加, 对于出现硬度低的不合格工件,可先给予退氮,然后重新氮化
2.深度浅,氮化层不足原因分析
(1)第二阶段氮化温度低,时间短
(2)工件氮化前未经调质处理
(3)氮分解率控制不当防止出现这一缺陷的主要措施是将工件的组织基体处理为索氏体,稳定分解率,足够保温时间。
对于氮化出现以上问题的补救方法是在正常温度下重新氮化。
3.表面氧化
(1)出炉时温度过高
(2)冷却过程中有空气进入
4.氮化层脆性大甚至有裂纹
(1)氮分解率过低
(2)氮化温度低
(3)退氮气处理不当
(4)冷却速度过慢
(5)预先热处理造成脱碳或组织粗大
措施:适当提高氮的分解率和氮化温度,退氮要充分,降温过程中加大氮的流量,以加快冷却速度可避免以上缺陷。
对于出现脆性的工件可将工件在500——520(保温3——5小时)进行退氮处理,或将在570——580(在氮的气氛中回火4——5小时),在630——650回火2小时左右均可。
5.工件变形大
(1)氮化前没有充分除应力
(2)冷却过快
(3)放置不当
6.氮化层深度不够硬度不均匀
(1炉温不均匀,氮流量不均
(2)工件表面有油污
三正火与退火
1.过热与过烧:
过热的工件机械性能差,冲击韧性低,而且还影响以后的热处理质量。
措施:将工件重新正火或完全退火,对于过共析钢,在正火后,还应用球化退火或高温退火来改善组织。
过共析钢一般不得采用完全退火的办法,否则会引起另一种缺欠——网状碳化物,如果晶粒过于粗大,一次正火或退火不能达到返修要求时,可用两次正火,第一次正火温度要高些(比正常正火温度高100度左右),但升温要快,保温要短。
第二次正火应比在正常的规范下进行,也可采用淬火和高温回火处理。
2.网状碳化物:
过共析钢加热到Acm以上以缓慢的速度进行冷却时,溶解于奥氏体的碳就会有一部分以碳化物的形式沿晶界析出呈网状分布。
措施:将工件进行正火,正火时对于大型工件应吹风冷却,以防止碳化物析出。
此外,亦可将工件加热到Acm以上30——50度,进行淬火,并进行650——700的回火。
3.硬度过高:
主要原因是冷却速度过快,一般碳钢以100——200度/h,合金钢以50—100度/h.对于合金工具钢来说,进行等温球化退火时,如果保温时间不足,没有来得级分解的一部分奥氏体在随后的冷却中转变为较硬的组织氏硬度偏高的主要原因。
措施:进行重新退火,另一种方法是将工件在Ac1以下20——30度给予保温5小时的回火。
渗碳常见问题与解决方法
氮化表面硬度或深度不够
(1)可能是钢料化学成分不适合作氮化处理
(2)可能是氮化处理前的组织不适合
(3)可能是氮化温度过高或太低
(4)炉中之温度或流气不均匀
(5)氨气的流量不足
(6)渗氮的时间不够长
氮化工件弯曲很厉害
(1)氮化前的弛力退火处理没有做好
(2)工件几何曲线设计不良,例如不对称、厚薄变化太大等因素
(3)氮化中被处理的工件放置方法不对
(4)被处理工件表面性质不均匀,例如清洗不均或表面温度不均等因素
氮化工件发生龟裂剥离现象
(1)氨的分解率超过85%,可能发生此现象
(2)渗氮处理前工件表面存在脱碳层
(3)工件设计有明显的锐角存在
(4)白层太厚时
氮化工件的白层过厚
(1)渗氮处理的温度太低
(2)氨的分解率低於15%时,可能发生此现象
(3)在冷却过程不恰当
氮化处理时之氨分解率不稳定
(1)分解率测定器管路漏气
(2)渗氮处理时装入炉内的工件太少
(3)炉中压力变化导致氨气流量改变
(4)触媒作用不当
工件需进行机械加工处如何防止渗碳?
(1)镀铜法,镀上厚度20mm以上的铜层
(2)涂敷涂敷剂后乾燥,可使用水玻璃溶液中悬浮铜粉(3)涂敷防碳涂敷剂后乾燥,主要使用硼砂和有机溶剂為主(4)氧化铁和黏土混合物涂敷法
(5)利用套筒或套螺丝
渗碳后工件硬度不足
(1)冷却速度不足,可利用喷水冷却或盐水冷却
(2)渗碳不足,可使用强力渗碳剂
(3)淬火温度不足
(4)淬火时加热发生之脱碳现象所导致,可使用盐浴炉直接淬火渗碳层剥离现象
(1)含碳量之浓度坡度太大,应施以扩散退火
(2)不存在中间层,应缓和渗碳的速率
(3)过渗碳现象,可考虑研磨前次之渗碳层
(4)反覆渗碳亦可能產生渗碳层剥离的现象
内容来源网络,由深圳机械展收集整理!
更多相关内容,就在深圳机械展!。