齿轮箱润滑流量计算
5齿轮箱油润滑与冷却部分培训教材

第五章齿轮箱油润滑与冷却系统5.1 润滑与冷却系统的作用齿轮箱的润滑十分重要,良好的润滑能够对齿轮和轴承起到足够的保护作用。
此外还具有如下性能:1) 减小摩擦和磨损,具有高的承载能力,防止胶合。
2)吸收冲击和振动。
3)防止疲劳点蚀。
4)冷却、防锈、抗腐蚀。
本齿轮箱采用飞溅润滑+加压(强制)润滑方式,此种方式可以起到更好的润滑作用。
系统采用Mobilgear SHC XMP 320合成润滑油,它在极低温度状况下具有较好的流动性;在高温时的化学稳定性好并可抑制黏度较低。
5.2 润滑与冷却系统的组成(1)泵单元:这部分主要由电机泵和过滤器两部分组成。
过滤器内部有精滤和粗滤两级滤网。
在滤网的两侧设有压差继电器。
可以对滤网的状态进行监控。
(2)冷却单元:冷却单元主要是热交换器,当系统油温过高时,压力油被送到热交换器进行热量交换。
(3)连接管路及单向阀。
5.3 原理图5.4工作过程系统要求在每次开机工作前,必须先启动润滑与冷却系统,待各润滑点充分得到润滑后在启动齿轮箱工作。
齿轮箱要求其内部的齿轮油工作时不得低于-15°C。
即当温度低于-15°C时,先通过齿轮箱中的加热系统,将齿轮油加热到-15°C在启动机器。
当温度在-15°C--+45°C 时,油泵装置要求保证40 [l/min]油流量,用于齿轮箱润滑。
此时齿轮油不经过空气换热器。
其回路如图a所示(图中红色线代表回路):但由于刚开机时齿轮油温度较低,所以齿轮油的粘度大,造成系统内压力升高。
如果此时系统内压力高于10bar,那么齿轮油通过安全阀直接与电机构成回路,加速齿轮油的循环,使油温迅速升高,降低系统的压力。
此时回路如图b所示(红色线代表回路,其他参数如图a所示)随着齿轮油的循环,齿轮油温度不断升高,管路中的压力逐渐降低。
当压力在3bar—10bar范围时。
10bar安全阀自动关闭,3bar安全阀自动打开。
齿轮泵计算公式
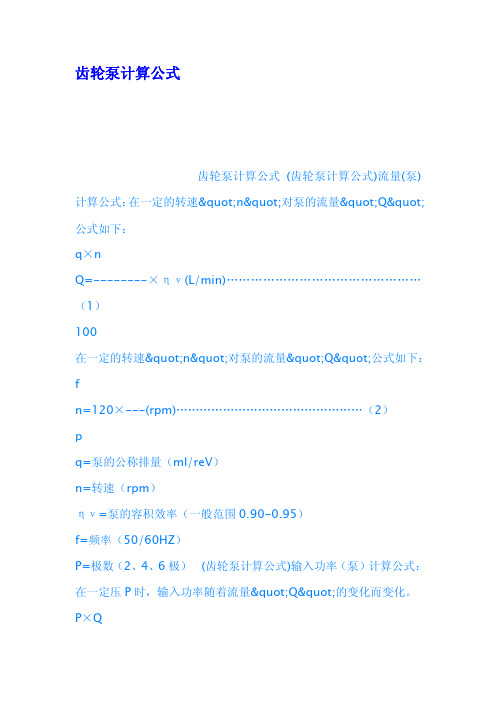
齿轮泵计算公式齿轮泵计算公式(齿轮泵计算公式)流量(泵)计算公式:在一定的转速"n"对泵的流量"Q"公式如下:q×nQ=--------×ην(L/min) (1)100在一定的转速"n"对泵的流量"Q"公式如下:fn=120×---(rpm) (2)pq=泵的公称排量(ml/reV)n=转速(rpm)ην=泵的容积效率(一般范围0.90-0.95)f=频率(50/60HZ)P=极数(2、4、6极)(齿轮泵计算公式)输入功率(泵)计算公式:在一定压P时,输入功率随着流量"Q"的变化而变化。
P×QW=--------------(KW) (3)612×0.089×ηP=输出口工作压力(Mpa)Q=流量(L/min)ην=泵机械效率(一般范围0.8-0.9)(齿轮泵计算公式)例题:有液压系统,泵的公称排量Q=10ml/rev,马达频率为50HZ4极,泵的输出压力为20Mpa,容积效率为时不晚0%,机械效率为85%.求泵的流量和输出功率?50n=120×---=1500(rpm)410×1500Q=--------×0.9=13.5(L/min)10020×13.5W=--------------=5.296(KW)612×0.089×0.85(齿轮泵计算公式)流量(马达)计算公式:在一定的转速"n"对泵的流量"Q"公式如下:V×nQ=--------(L/min)1000ηνV=马达排量(cc/reV)n=转速(rpm)ην=马达的容积效率(一般范围0.93-0.97,在1000-3000rpm)(齿轮泵计算公式)功率-效率(马达)计算公式:A)液压功率在一定的压力ΔP时,功率WH随流量"Q"的变化而变化公式如下:Q×ΔPWh=--------(KW)612ΔP=出入油口的压差(bar)B)机械功率传递到马达轴上的机械功率Wm计算如下:2π×n×MtWm=--------(KW)60×1000设定公式:WmWh=-----ηt=ην×ηm(KW)ηt(齿轮泵计算公式)扭矩(马达)计算公式:在不同的压力ΔP下马达轴的扭矩"Mt"为:V×ΔPMt=--------×ηm(N.m)(L/min)20×4πΔP=出入油口的压差(bar)ηm=马达的机械效率(在工作初始时约为.085,在工作转速时约为.90)注意:容积,机械和总效率依据压力,转速和油液特性以及相关温度和粘度因素。
强制润滑轴承用油量计算

强制润滑轴承用油量计算
强制润滑是指在机械设备的运行过程中,通过润滑油泵将润滑油以一定的压力和流量输送到轴承上,以保证轴承得到充分的润滑。
在使用强制润滑系统时,需要根据轴承的尺寸、转速、工作温度等因素,计算出所需的润滑油量。
首先,需要确定轴承的尺寸,包括内径、外径、宽度等参数。
在确定轴承尺寸的基础上,需要了解轴承的转速,通常以每分钟转速(RPM)来表示。
同时,还需要考虑轴承的工作温度范围,以确定所需的润滑油的黏度。
根据轴承的尺寸、转速和工作温度范围,可以通过相关公式计算出所需的润滑油量。
一般情况下,润滑油量的计算公式为:
Q =(0.001~0.005)×D×L×n
其中,Q为润滑油量,单位为升/分钟;D为轴承内径,单位为毫米;L为轴承长度,单位为毫米;n为每分钟转速,单位为转/分钟。
根据实际情况,可以将0.001~0.005的系数进行调整。
除了润滑油量的计算,还需要确定润滑油的供油方式、压力和流量等参数。
这些参数需要结合实际情况进行选择和设计,以确保轴承得到充分的润滑,同时避免润滑油过多或过少的情况发生。
总之,强制润滑轴承的油量计算需要考虑轴承的尺寸、转速、工作温度等因素,并通过相关公式进行计算。
在确定润滑油量的同时,还需要结合实际情况,选择合适的润滑油供油方式、压力和流量等参数,以确保轴承得到充分的润滑。
齿轮泵排量计算公式单位

齿轮泵排量计算公式单位
1.概述
齿轮泵是一种常见的液压泵,用于输送液压油或其它液体。
在液压系
统中,了解齿轮泵的排量是非常重要的。
本文将介绍齿轮泵排量计算公式
及其单位,并提供实际应用示例。
2.什么是齿轮泵排量
齿轮泵排量是指齿轮泵每分钟输送液体的体积。
常用的单位有立方厘
米/分钟(c m³/m in)、立方米/小时(m³/h)等。
3.齿轮泵排量计算公式
齿轮泵排量的计算公式如下:
排量=齿轮宽度×齿轮转速×齿轮槽数
其中,
-齿轮宽度是指齿轮的宽度或高度,单位为毫米(mm);
-齿轮转速是指齿轮的旋转速度,单位为转每分钟(r pm);
-齿轮槽数是指齿轮上齿的数量,无单位。
4.实际应用示例
假设某液压系统中的齿轮泵的齿轮宽度为40m m,齿轮转速为1200r pm,齿轮槽数为6。
我们可以使用上述计算公式来计算齿轮泵的排量:
排量=40m m×1200rp m×6=288000m m³/m in
通过进一步转换单位,我们可以将排量表示为立方厘米/分钟:
排量=288000m m³/m i n=288c m³/m in
因此,该液压系统中的齿轮泵的排量为288立方厘米/分钟。
5.总结
本文介绍了齿轮泵排量的计算公式及其单位。
了解齿轮泵的排量对于液压系统的设计和运行非常重要,可以帮助工程师选择合适的泵和计算系统的工作效率。
希望本文能对读者有所帮助。
各种齿轮参数计算公式大全
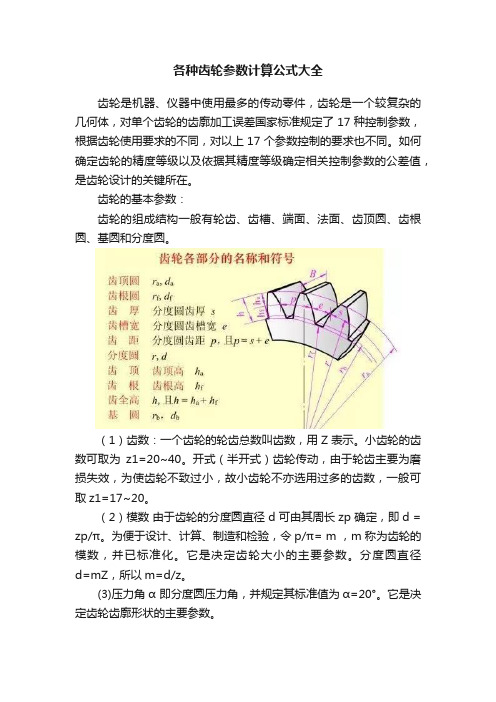
各种齿轮参数计算公式大全齿轮是机器、仪器中使用最多的传动零件,齿轮是一个较复杂的几何体,对单个齿轮的齿廓加工误差国家标准规定了17种控制参数,根据齿轮使用要求的不同,对以上17个参数控制的要求也不同。
如何确定齿轮的精度等级以及依据其精度等级确定相关控制参数的公差值,是齿轮设计的关键所在。
齿轮的基本参数:齿轮的组成结构一般有轮齿、齿槽、端面、法面、齿顶圆、齿根圆、基圆和分度圆。
(1)齿数:一个齿轮的轮齿总数叫齿数,用Z表示。
小齿轮的齿数可取为z1=20~40。
开式(半开式)齿轮传动,由于轮齿主要为磨损失效,为使齿轮不致过小,故小齿轮不亦选用过多的齿数,一般可取z1=17~20。
(2)模数由于齿轮的分度圆直径 d 可由其周长 zp 确定,即d = zp/π。
为便于设计、计算、制造和检验,令p/π= m ,m 称为齿轮的模数,并已标准化。
它是决定齿轮大小的主要参数。
分度圆直径d=mZ,所以m=d/z。
(3)压力角α 即分度圆压力角,并规定其标准值为α=20°。
它是决定齿轮齿廓形状的主要参数。
分度圆直径d=mZ/cosβ压力角rb=rcosα=1/2mzcosα在两齿轮节圆相切点P处,两齿廓曲线的公法线(即齿廓的受力方向)与两节圆的公切线(即P点处的瞬时运动方向)所夹的锐角称为压力角,也称啮合角。
对单个齿轮即为齿形角。
标准齿轮的压力角一般为20”。
在某些场合也有采用α=14.5° 、15° 、22.50°及25°等情况。
(4)齿顶高系数和顶隙系数:h*a 、C*两齿轮啮合时,总是一个齿轮的齿顶进入另一个齿轮的齿根,为了防止热膨胀顶死和具有储成润滑油的空间,要求齿根高大于齿顶高。
为次引入了齿顶高系数和顶隙系数。
正常齿:h*a =1; C*=0.25 短齿:h*a =0.8; C*=0.3一对相互啮合的齿轮,模数、压力角必须相等。
标准齿轮的压力角(对单个齿轮而言即为齿形角)为20°齿轮参数计算公式大全:1. 内齿模数齿轮2. 直齿模数齿轮3. 斜齿模数齿轮4. 伞齿模数齿轮5. 变位模数齿轮6. 直齿径节齿轮7. 斜齿径节齿轮8. 齿条。
齿轮箱润滑回路相关知识讲解
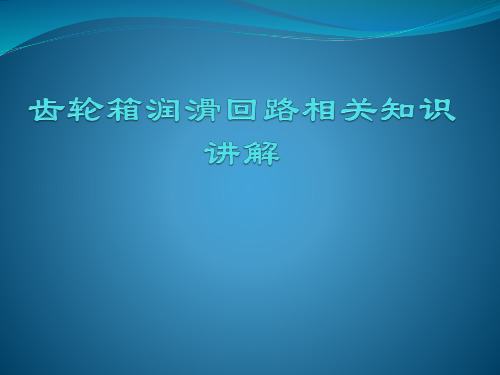
⑷温控阀在油温达到45℃开启,50℃时全开,在此切换过程中,油将同时在直 通齿轮箱的管路和通往散热器的管路中过流,并随着切换过程2路流量大小有 变化,但总流量不变。
三、润滑系统的日常维护
1.润滑电机泵的控制 (单速泵)
启动温度:油池温度≥5℃方可运 行电机泵 关闭温度:油池温度≤ 0℃方可运 行电机泵
2.检查箱体内油位是 否合格
3.检查机械泵进油阀是否打开
关 闭 状 态
4.检查电机泵进油阀是否 打开
5.检查外部油管接头 是否漏油
6.检查润滑软管接 头有无松动、漏 油现象
4.温控阀结构和工作原理
弹簧
温控阀盖 去齿轮箱油口
阀体 活塞体
活塞杆
去散热器油口
⑴ 依靠密封在活塞内的空气,受热膨胀推动活塞的反作用力,以及弹簧的弹 力,共同作用于阀体,使之移动,达到切换油路的目的。
⑵ 当油温过高,密封的空气受热膨胀时,推动活塞上移,由于活塞顶在温控 阀盖上无法移动,迫使阀体在活塞的反作用力下,克服弹簧的阻力,推动阀 体下移,从而断开直通油路,接通油冷却通道,高温润滑油进入散热器进行 冷却后,再进入齿轮箱。
一、齿轮箱润滑系统
(一)润滑系统的基本原理
润滑系统一般采用齿轮泵(有的齿轮箱会配有机械泵)从齿轮箱内 部吸油,齿轮泵由电动机驱动,齿轮泵泵出的润滑油经过滤器过滤后分 两路,一路(当油温≤40℃时)直接进入分配器,一路经过风冷油换热 器(有的齿轮箱装有水冷换热器)后再进入分配器,当油温至55℃时, 润滑油完全经过风冷换热器换热后进入分配器。 这样润滑油不停地循 环、冷却,不断地带走齿轮箱发出的热量,维持油温不超过80℃。润滑 系统和齿轮箱上装有温度传感器、压力传感器、压力开关、压力表等, 用来监测齿轮箱的运行,如果系统不能稳定运行,上述元件中的某个会 输出不正常的信号,提示系统有异常。
润滑点需要油量的计算
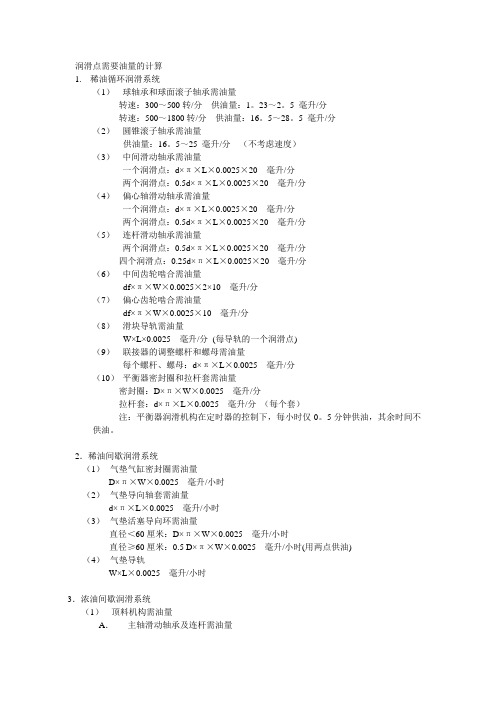
润滑点需要油量的计算1.稀油循环润滑系统(1)球轴承和球面滚子轴承需油量转速:300~500转/分供油量:1。
23~2。
5 毫升/分转速:500~1800转/分供油量:16。
5~28。
5 毫升/分(2)圆锥滚子轴承需油量供油量:16。
5~25 毫升/分(不考虑速度)(3)中间滑动轴承需油量一个润滑点:d×π×L×0.0025×20 毫升/分两个润滑点:0.5d×π×L×0.0025×20 毫升/分(4)偏心轴滑动轴承需油量一个润滑点:d×π×L×0.0025×20 毫升/分两个润滑点:0.5d×π×L×0.0025×20 毫升/分(5)连杆滑动轴承需油量两个润滑点:0.5d×π×L×0.0025×20 毫升/分四个润滑点:0.25d×π×L×0.0025×20 毫升/分(6)中间齿轮啮合需油量df×π×W×0.0025×2×10 毫升/分(7)偏心齿轮啮合需油量df×π×W×0.0025×10 毫升/分(8)滑块导轨需油量W×L×0.0025 毫升/分(每导轨的一个润滑点)(9)联接器的调整螺杆和螺母需油量每个螺杆、螺母:d×π×L×0.0025 毫升/分(10)平衡器密封圈和拉杆套需油量密封圈:D×π×W×0.0025 毫升/分拉杆套:d×π×L×0.0025 毫升/分(每个套)注:平衡器润滑机构在定时器的控制下,每小时仅0。
5分钟供油,其余时间不供油。
2.稀油间歇润滑系统(1)气垫气缸密封圈需油量D×π×W×0.0025 毫升/小时(2)气垫导向轴套需油量d×π×L×0.0025 毫升/小时(3)气垫活塞导向环需油量直径<60厘米:D×π×W×0.0025 毫升/小时直径≥60厘米:0.5 D×π×W×0.0025 毫升/小时(用两点供油) (4)气垫导轨W×L×0.0025 毫升/小时3.浓油间歇润滑系统(1)顶料机构需油量A.主轴滑动轴承及连杆需油量轴承处:d×π×L×0.008 毫升/2小时连杆轴承:0.5 d×π×L×0.008 毫升/2小时(每点)B.滑块导轨需油量W×L×0.008 毫升/2小时(每个导轨)C.凸轮机构需油量D×π×W×0.008 毫升/2小时D.轴套需油量d×π×L×0.008 毫升/2小时(每个套)E.拉杆套或销轴需油量d×π×L×0.008 毫升/2小时(每个润滑点)F.气缸活塞密封处不能用浓油润滑,必须用稀油润滑,油量计算公式同气垫气缸密封圈公式。
液压常用计算公式-液压泵
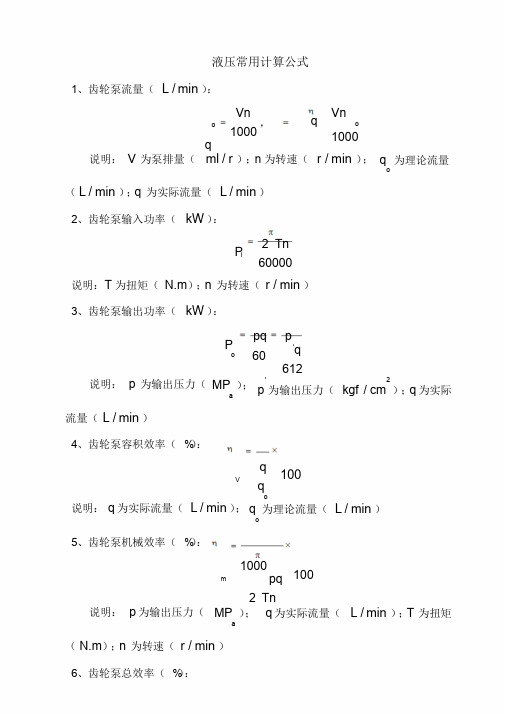
液压常用计算公式1、齿轮泵流量(L/min):Vn o,1000q qV no1000说明:V为泵排量(ml/r);n为转速(r/min);q为理论流量o(L/min);q为实际流量(L/min)2、齿轮泵输入功率(kW):P i 2Tn 60000说明:T为扭矩(N.m);n为转速(r/min)3、齿轮泵输出功率(kW):P o pq60p'q612说明:p为输出压力(MP);a'p为输出压力(2kgf/cm);q为实际流量(L/min)4、齿轮泵容积效率(%):V qqo100说明:q为实际流量(L/min);q为理论流量(L/min)o5、齿轮泵机械效率(%):m 1000pq2Tn100说明:p为输出压力(M P);q为实际流量(L/min);T为扭矩a(N.m);n为转速(r/min)6、齿轮泵总效率(%):V m说明:V为齿轮泵容积效率(%);m为齿轮泵机械效率(%)7、齿轮马达扭矩(N.m):P qT2t,T T t m说明:P为马达的输入压力与输出压力差(M P);q为马达排量a(ml/r);T为马达的理论扭矩(N.m);T为马达的实际输出扭矩(N.m);tm为马达的机械效率(%)8、齿轮马达的转速(r/min):n QqV说明:Q为马达的输入流量(ml/min);q为马达排量(ml/r);V 为马达的容积效率(%)9、齿轮马达的输出功率(kW):P2nT 60310说明:n为马达的实际转速(r/min);T为马达的实际输出扭矩(N.m)10、液压缸面积(2cm):2 DA4说明:D为液压缸有效活塞直径(cm)11、液压缸速度(m min):VQ 10A说明:Q为流量(L min);A为液压缸面积(2cm)12、液压缸需要的流量(L min):Q V A10A10St说明:V为速度(m min);A为液压缸面积(2cm);S为液压缸行程(m);t为时间(min)13、液压缸的流速(m/s):V1Q4QV,V2A D1Q4QV VV2D d2A(22) 3);说明:Q为供油量(m/s V为油缸的容积效率(%);D为无杆腔活塞直径(m);d为活塞杆直径(m)14、液压缸的推力(N):22F1(A P A P o)D(P P)d P12m o o4m22F o D P P d P2(P A P()A)21m o4m说明:F为无杆端产生的推力(N);F2为有杆端产生的推力(N);1P为油缸的进油压力(P a);P o为油缸的回油背压(P a);D为无杆腔活塞直径(m);d为活塞杆直径(m);m为油缸的机械效率(%)15、油管管径(mm):d 4.63Q v说明:Q为通过油管的流量(L/min);v为油在管内允许的流速(m/s)16、管内压力降(2kgf/cm):P 0.6984dU SLQ说明:U为油的黏度(cst);S为油的比重;L为管的长度(m);Q 为流量(l/min);D为无杆腔活塞直径(m);d为管的内径(cm)17、推荐各种情况管道中油液的流速:流速吸油管压力管回油管短管及局部收缩处v(m/ s) 0.5-1.5 2-6 1.5-2.5 10说明:对于压力管,当压力高、流量大、管路短时取大值,反之取小值。
- 1、下载文档前请自行甄别文档内容的完整性,平台不提供额外的编辑、内容补充、找答案等附加服务。
- 2、"仅部分预览"的文档,不可在线预览部分如存在完整性等问题,可反馈申请退款(可完整预览的文档不适用该条件!)。
- 3、如文档侵犯您的权益,请联系客服反馈,我们会尽快为您处理(人工客服工作时间:9:00-18:30)。
齿轮箱润滑流量计算
摘要:本文通过一个工程实例介绍齿轮箱循环式稀油润滑系统的设计原理及计算方法。
关键词:齿轮箱稀油循环润滑系统设计原理计算方法
齿轮箱的制造质量是保证齿轮长期正常工作的必要条件,但齿轮润滑油的循环系统对齿轮寿命的影响也是很大的,如果齿轮的润滑流量不足,会造成齿轮齿面的粘着破坏,缩短齿轮的寿命,如润滑流量设计过大则会造成投资的增加、运行成本的增加。
所以选择一个合理的润滑流量对齿轮箱的设计是十分重要的。
齿轮的润滑方式是采用油浴润滑方式还是采用喷淋润滑,取决于齿轮外沿的圆周切线速度。
当圆周切线速度大于15m/s时,采用喷淋润滑方式;如圆周切线速度小于15m/s ,原则上可采用油浴润滑方式,但要进行热平衡校验,如果齿轮箱外形很紧凑,散热面积小,要采用喷淋润滑方式。
所以齿轮箱润滑方式的确定,要视润滑油液是否达到热平衡。
齿轮箱喷淋润滑方式的流量计算是十分重要的,本文介绍一种大型齿轮箱的工程计算方法,供工程设计人员参考:
根据比热容的计算公式,经过单位变换可得出下式:
K ×P F
Q = ——————l/min
C ×ΔT
式中:Q——润滑流量
K——系数;
C——润滑油的比热容;
ΔT——温差;
P F——功率损失;kW
例:某冶金企业减速机,电机额定功率为5000KW,电机的过载系数为2.5倍,负载曲线见附图,齿轮为单级齿轮硬齿面人字形齿,加工精度为6级,机械效率0.99(不含轴承的机械效率),润滑油的密度取值0.85, 润滑油的比热容为1.88,并假设润滑油的流量为均匀连续介质。
试计算齿轮齿面的润滑流量。
1、计算发热功率:
根据减速箱的负载功率曲线,可按算术平均功率计算公式计算该减速箱的平均功
率。
P1×T1+P2×T2
P平均= ——————
∑T
9200×16+800×40
代入数值得P平均= ————————= 3200 kW
56
考虑齿轮箱的效率为0.99,齿轮箱输入轴的实际功率为P=P平均/ 0.99 = 3232 kW 假设齿轮的功率损失全部转化为热量,则发热功率为P F =32 kW
2、计算润滑流量:
K ×P
根据Q = ——————l/min
C×ΔT
式中:润滑油的比热容C= 1.88
润滑油的密度0.85
设允许的润滑油温差ΔT= 10℃
可将上式简化为Q=3.75×P F = 3.75×32= 120 l/min
润滑油流量的最终确定与润滑油的喷射方式有着密切的关系,润滑油的喷射方式有两种;低压(采用钢管头打扁)喷射和高压(加阻尼和喷嘴)喷射,一般说来,采用低压喷射方式时流量取大值,采用高压喷射方式时流量取小值。
喷嘴的安装位置应放在齿轮啮合区的分离面上,有利于热量的带出。
润滑流量的最终确定还与润滑油箱体和冷却强度有着密切关系,所以在做系统设计时要中和考虑包含当地的环境温度等各方面的因素,才能设计出最优的润滑系统。
双级或多级齿轮的减速箱的流量确定,其第二级的流量按单级齿轮计算流量的90%计取较为合理,其余各级按上述原则递减。
参考文献:
中国机械工程学会摩擦学会《润滑工程》北京:机械工业出版社,1986
《国内外最新润滑油及润滑实用手册》广东科技出版社,1997。