提高Φm水泥磨台时产量的措施
水泥磨台时产量低原因分析及处理方法
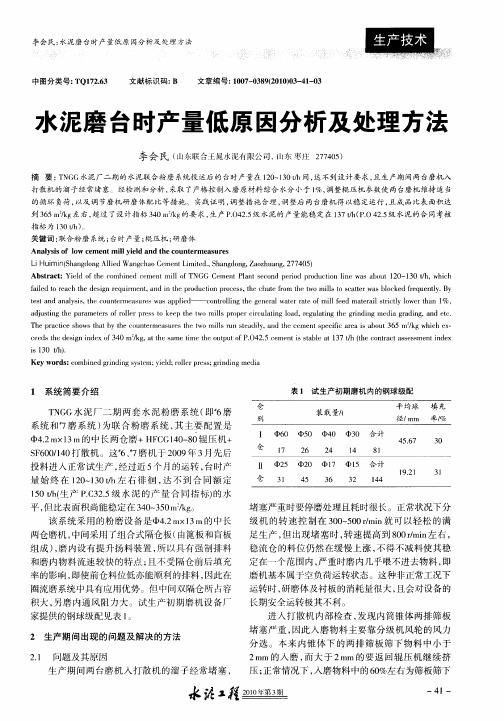
ce sh einidxo 0H /g a tesm me h up t f .4 . cm n t l a 17t tecnrc assm n idx ed e s e f 4 ik, th a et eotu 0 25 e e tss be t 3 h( ot t ses e tn e t d g n 3 i t oP i a / h a i l0 t ) s 3 / . h
42 1 i 中长 两仓 磨 +H C 4 — 0 压 机 + .m× 3n的 F G10 8 辊 S 6 0 10 F 0 /4 打散 机 。这 、 磨 机 于 2 0 年 3 6 7 09 月先 后
投料 进 入正 常试 生 产 , 经过 近 5 月 的运转 , 时产 个 台
ajsn eprme r o l r rs t k e etoml r e i u t gl d rg l igtegidn dagaig a de . dut gt aa t s fol es o ept ispo r r l i a ,eua n r igmei rdn, n t i h e r ep h w l p cc an o t h n c
李 会 民 : 泥 磨 台时 产 量 低 原 因分 析及 处理 方 法 水
中 图分 类 号 : Q126 T 7. 3
文 献标 识 码 : B
文章 编 号 :0 7 0 8 (0 00 — 1 0 10 — 392 1 )3 4 — 3
水泥磨 台时产 量低原 因分析及处理 方法
李 会 民 ( 联合王晁水泥 公司,I 山东 有限 I I 东枣庄 270) 745
A na y i f l ce e il el d hec l sso ow m ntm l yi d an t ount m e s e er a ur s
水泥磨台时产量突燃阶段性下降的原因分析

l : 一 为球 磨机 通风 量(lh ; 1 J I/ ) l
一
为球 磨 机产 量 ( h ; t) /
4 0一 为经验 系数 0 一 3 研 磨体 影 响
内的停 留[ , { I 以俅 水泥细 度 当有 火块 料 时 , 』 叮
使水 泥磨 台时 突然 F降 1% ~2% 0 0
杜恭 贵 , 永 华 ( 于鄙 邹 南方, } 有限公 u 汀 l 436 } ] 青水 ‘ , J 20) : 鄙3
产过 程 r , 会 出现 突 发性 或 阶段 性 台时 产 量下 降 {总 l 1
的情 况 , 时 苠全 难 以查 找 出 真 实原 有 根 据 笔者 从 事 l 多 粉磨 L 0 怍经 验 , 义 就此现 象 的原 【进 小 太 1
多 从事 粉 磨 l 者攻 关 的重 要 课 题 , 住 l 的生 , 潮湿 细粉 会粘 附堵 塞隔 仓板和 出料 篦缝 , 既降 低 l单位 时间 内物 料 的通 过 量 及 流速 , r 又影 响磨 机 通风 ; H由于静 电作用 , 湿细粉 还 会 衬 板工 作表 潮
通 风 , 时 产 量 由 7 h 降 至 6 l 下 降 幅 度 达 台 8/ t 2/, t1
l.%, 时 应停 机 开 仓清 理堵 塞 部 分 , 67 此 加大 筒体 表 面住 淋水 降温 , 消除静 电效 应 , 为此 才能 予 以解决 上
述 问题 , 复全 l常产 量 恢 r 经 验 旺明 , 流 磨 磨 内 风速 砬 控 制 在 1 开 . 0~1 . 2
l 0% ~ 2 % : 0
ms / 左白 , 固流 磨 应保 持在 08~1 m s . . / 左有 ; 0 另磨 内
通 风量 磨 机产量 的关 系可 参照 经验公 式调 整 , : 即
提高Φ4.2×14.5m水泥磨运行指标的几项技措

提高Φ4.2×14.5m水泥磨运行指标的几项技措2015-3-5摘要:安徽海螺(295.04元/吨,-0.14%)集团水泥股份公司2台Φ4.2m×14.5m水泥磨于2010年9月投产,生产初期,磨机工况不稳定,技经指标不理想。
经分析各方面的影响因素,采取了一系列针对性措施,磨机工况、技经指标有了明显改善和提高。
0 前言笔者公司2台Φ4.2m×14.5m水泥磨于2010年9月投产,生产初期,磨机工况不稳定,技经指标不理想。
为提高磨机运行质量,增强企业竞争力,经认真梳理各方面影响因素,结合实际情况,拟定调整措施,并实施了系列小改革,使磨机工况、技经指标有了明显改善和提高。
其中水泥生产工序电耗由39.2kWh/t下降到37.5kWh/t,综合台产由115t/h提高到138t/h,出磨水泥比表面积合格率由75.8%上升到99.8%。
现就这2台Φ4.2m×14.5m水泥磨机在运行管理方面的成功经验和系统技改方面的具体措施进行总结介绍,以与同行交流。
1 影响磨机产、质量的原因分析及调整措施1.1 熟料易磨性的影响及其调整水泥熟料的物理性质及成分波动对粉磨效果有很大影响。
高温熟料、过多粉状熟料会造成磨机台产下降,同时熟料的4种主要矿物C3S,C2S,C3A,C4AF易磨性相差很大。
在相同粉磨时间内,4种矿物的易磨性排列分别是C3S>C3A>C4AF>C2S。
即C3S是熟料矿物中最易磨的矿物,随着粉磨时间的延长,其比表面积近似呈直线增加,C3A的情况与之相类似,C2S则最难粉磨。
因此当熟料中C2S成分含量增大时,磨机台产下降。
为减少高温料、粉状料入磨,首先要保持熟料库具有适当料位,以保证熟料有一定的冷却时间,并有利于下料的均匀稳定;其次,往熟料磨头仓送料时,尽量使用熟料库边缘熟料,即同一个库只开启边缘两条皮带,同一条皮带开启前后的下料口,尽量避免使用熟料库中间的高温、粉状物料。
提高水泥磨能力的途径

提高水泥磨能力的途径水泥粉磨过程的高效率、低能耗运行,一直是生产企业追求的目标。
“提高磨机能力”,也是一个永恒的话题。
不断提高球磨机的粉磨效率,降低粉磨电耗和生产成本,最大幅度地达到高细、高产,是我们不懈追求的目标。
尤其是水泥新标准的实施,对水泥细度、比表面积和颗粒组成都提出了更高的要求,水泥企业往往以降低混合材掺加量或提高水泥比表面积来提高水泥强度,而要获得较高比表面积最简单的办法是降低磨机的产量和增加研磨时间,但带来的结果是出现“过粉磨现象”,使<3um的微粉增多且颗粒组成状况不佳,强度提高不多,而粉磨电耗却大幅度上升。
这种采用降低产量和增加研磨时间提高水泥成品细度或增加熟料含量来提高水泥强度的作法,势必会造成生产成本的上升。
因此,必须从磨机内部改造、物料预破碎、研磨体的合理级配等入手来提高水泥3-30um颗粒的含量,从而提高水泥的强度。
一、提高水泥磨能力的一般途径1、降低入磨物料粒度降低入磨物料(熟料)粒度,可降低单位产品电耗,提高水泥粉磨能力。
入磨物料粒度大小是影响磨机产量的主要因素,粒度小可减小钢球的平均球径,在装载量相同的情况下,钢球个数增加,钢球的总面积增加,可增加钢球与物料的接触面积,提高粉磨效率,因此采用“多碎少磨”即磨前预粉碎工艺可降低粉磨系统电耗和提高磨机能力。
2、调整磨机内部结构采取了磨前预破碎工艺,入磨物料粒度减小了,但粉磨能力并未提高,现象是出磨提升和O-Sepa选粉机电流高、负荷重,循环负荷率高、达到了240%,选粉效率很低、才25%左右,通过作筛析曲线也得到了印证,在第一仓曲线很陡,第二仓曲线接近水平线。
显然该磨机第一仓冲击力太强,第二仓研磨能力严重不足,针对这种状况,在第二仓加了3吨小钢球后,台时产量可提到70t/h左右,为进一步发挥该磨机能力,又对磨机内部结构作了适当调整,将一仓长度由原来的5.35m缩短为4.85m,即把隔仓板向前移动一块衬板长度,二仓长度由原来的7.25m增加到7.75m,增加细磨仓的研磨能力,提高粉磨效率。
水泥磨台时产量下降的原因及解决措施

1. 水泥磨台时产量突发性或阶段性下降的原因(1)物料变化引起台时产量大幅波动物料易磨性突然变差。
据资料显示,当熟料的相对易磨性系数从1.02降到0.92时,磨机台时产量下降1.5吨以上,熟料中含有黄心料和欠烧料。
黄心料和欠烧料很容易黏附于研磨体和衬板表面,形成缓冲垫层,大大影响粉磨效率。
这种熟料可使磨机台时产量下降10%~20%,物料中含有大块。
磨内研磨体数量最大值,是根据常规情况的最大入磨物料粒度而确定的,对非正常情况下的大块物料破碎能力明显不足,所以必须大幅度减少喂料量、延长物料在磨内的停留时间,这样才能保证水泥的细度。
这些物料可使水泥磨台时产量突然下降10%~20%。
(2)通风变差,由于袋式除尘器清灰不力、风机风叶磨损严重、风机和电机的传动皮带松动、风管积灰等原因引起磨内通风变差时,会使磨机台时产量突然下降。
当物料水分偏大而磨机通风不良时,磨内水蒸气排放困难,导致潮湿细粉堵塞隔仓板和出料篦缝,降低了单位时间内物料的通过量及流速。
这些研磨体在研磨物料时由于静电原因,还会在衬板工作表面附层形成缓冲垫层,导致研磨体对物料的冲击破碎能力大大减弱。
同时,物料水分变大,堵塞双层隔仓板和出料篦板,影响磨内通风,磨机台时产量可下降17%左右,粉磨电耗上升。
(3)入磨物料水分增大,物料水分多少直接影响配料的准确性和磨机产量及电耗,如果湿物料掺量比例较大,有可能导致“饱磨”或将内衬板粘上一层厚厚的料层,要被迫进行停磨处理。
一般来说,综合水分每增加1%,磨机台时产量下降8%~10%;当综合水分>5%时,磨机将无法进行粉磨作业。
(4)水泥细度指标降低,细度指标降低、细度平均值下降,立即会引起磨机台时产量下降。
在一定条件下,球磨机的产量与水泥细度成反比。
(5)包球和糊磨,当发生包球和糊磨现象时,磨机台时产量将大幅度下降。
尤其是糊磨时台时产量更低,而包球时还会出现细度值偏大问题。
(6)研磨体装载量过少,一般确定的装载量都允许有一定的波动范围,以适应研磨体补加周期内装载量从多到少的需要。
浅谈 3.2×13m 水泥磨的增产改造技术
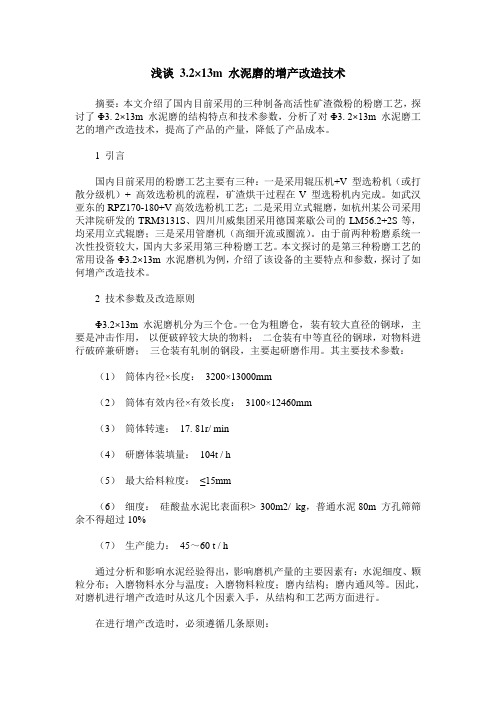
浅谈 3.2×13m 水泥磨的增产改造技术摘要:本文介绍了国内目前采用的三种制备高活性矿渣微粉的粉磨工艺,探讨了Φ3. 2×13m 水泥磨的结构特点和技术参数,分析了对Φ3. 2×13m 水泥磨工艺的增产改造技术,提高了产品的产量,降低了产品成本。
1 引言国内目前采用的粉磨工艺主要有三种:一是采用辊压机+V 型选粉机(或打散分级机)+ 高效选粉机的流程,矿渣烘干过程在V 型选粉机内完成。
如武汉亚东的RPZ170-180+V高效选粉机工艺;二是采用立式辊磨,如杭州某公司采用天津院研发的TRM3131S、四川川威集团采用德国莱歇公司的LM56.2+2S等,均采用立式辊磨;三是采用管磨机(高细开流或圈流)。
由于前两种粉磨系统一次性投资较大,国内大多采用第三种粉磨工艺。
本文探讨的是第三种粉磨工艺的常用设备Φ3.2×13m 水泥磨机为例,介绍了该设备的主要特点和参数,探讨了如何增产改造技术。
2 技术参数及改造原则Φ3.2×13m 水泥磨机分为三个仓。
一仓为粗磨仓,装有较大直径的钢球,主要是冲击作用,以便破碎较大块的物料;二仓装有中等直径的钢球,对物料进行破碎兼研磨;三仓装有轧制的钢段,主要起研磨作用。
其主要技术参数:(1)筒体内径×长度:3200×13000mm(2)筒体有效内径×有效长度:3100×12460mm(3)筒体转速:17. 81r/ min(4)研磨体装填量:104t / h(5)最大给料粒度:≤15mm(6)细度:硅酸盐水泥比表面积> 300m2/ kg,普通水泥80m 方孔筛筛余不得超过10%(7)生产能力:45~60 t / h通过分析和影响水泥经验得出,影响磨机产量的主要因素有:水泥细度、颗粒分布;入磨物料水分与温度;入磨物料粒度;磨内结构;磨内通风等。
因此,对磨机进行增产改造时从这几个因素入手,从结构和工艺两方面进行。
水泥磨提产改造方案
极低,有效地延长了其使用寿命。
⑹ 主轴下轴承密封采用新的设计方案,采用了干油站强制润滑轴承, 有效地解决了轴承进灰和漏油两项重大难题,切实有效地延长了轴承使用 寿命。 ⑺ 高效率的集尘系统可将30μm以下颗粒及时并大量地收集进入成品
,有效地提高了产品的比表面积。
四、高效涡流选粉机性能参数:
4.3 Sepax高效涡流选粉机特点
四、高效涡流选粉机性能参数:
85%以上,但其系统装机容量却要降低30%,且可在正压下工作,细粉 收集仅采用高效旋风筒即可,无需再配置庞大的气箱脉冲袋式除尘器, 这样不但降低了粉磨电耗,而且也降低了投资费用(省去了气箱脉冲袋 式除尘器)和维护保养费用。与转子式选粉机相比其分级效率高出15% ,而装机容量却差不多,因而产量要高出20~30%。
1.3.2产、质量指标
时间
辊压机 辊压机 出磨提 入磨提 80um 比 表 项目名 选粉机 磨机电 筛 余 m2/kg 台时t/h 动辊电 定辊电 升机电 升机电 称 电流 流 ≦1.2% >370 流 流 流 流
345 125 35 32 99 130 180 160
14:00 PO42.5 0.4
3 、布袋收尘器JMPL128-2X8D,处理风量150000m3/h,过滤风 速1.07m/min,系统阻力≦1500Pa,风机GY75T-VN021F,风 量180000m3/h,压力7500Pa,电机YJTGKK5003-6/560kw 4、球磨机Ǿ3.8X13m,二仓,其中一仓长2.75m,二仓9.75m。电
⑶ 与O-Sepa涡流选粉机相比, Sepax涡流选粉机增加了分散、预分
级装置。采用航空空气动力学分析方法对整个流场进行了优化设计;采用 悬浮分散技术使物料充分分散;采用预分级技术,有效地减小了大小颗粒 间的干扰,为精确分级创造了条件。 ⑷ Sepax涡流选粉机与尺寸相近的离心式、旋风式、单(双)转子
提高水泥磨产质量的一些措施
提高水泥磨产质量的一些措施1"多破少磨"前些年,水泥的入磨粒度一直未被水泥厂家所重视。
近年来,水泥粉磨工艺已把水泥的入磨粒度提升到了重要位置。
“多破少磨〃的观点己被行业人士所认同。
"多破少磨〃即把原来进入磨机的30mm的物料粒径改为3mm以下。
现阶段生产破碎机的厂家纷纷推出了高细锤式破碎机、筛分滚压破碎机、辑压机等。
本厂针对企业实际情况把原有鄂式破碎机改为超细锤式筛分破碎机,入磨粒度由原来的30mm降至5mm以下,从而提高了磨机产量。
现采用的辐压机使入磨粒度降至2mm以下。
产量提高50%以上。
2改善工艺流程水泥粉磨工艺流程主要分为开流和圈流系统。
我单位原为开流系统,水泥细度不易控制,波动较大。
针对以上情况出资几十万元,把开流粉磨改为圈流粉磨。
增设一台高效转子选粉机,更新了一台高效袋式收尘器。
起到了提高水泥比表面积,增加水泥强度的良好效果。
现在采用馄压机、打散分级机、准3.8mχ13m水泥磨联合粉磨系统,水泥磨产量由原来的60~70t提高到100-120t(>3控制入磨物料水分、温度和易磨性控制入磨物料综合水分<1.5%,这是保证磨机优质高产的基本要求。
水分过高,将造成辑压机挤压料饼过实,不易打散。
同时易造成磨内通风不良,堵塞隔仓板、篦板、糊球(段)、衬板,除尘器结露等。
我厂对混合材进厂水分、物料生产过程中烘干水分严格控制,认真考核,使入磨物料温度严格控制在工艺要求范围内。
确保磨机正常运转。
物料的粉磨难易程度来自于物料本身,熟料中C2S和C4AF高贝IJ难磨,我厂配料中力求保证生产C3A和C3S高的熟料。
改善入磨物料性能,我的经验是:把熟料和矿渣单独粉磨,利用冬季水泥停产期间单独粉磨制备了一定量的矿渣微粉。
在生产水泥期间按比例加入,提高了矿渣的易磨性;掺入与水泥细度基本接近的粉煤灰做混合材,提高了混合材的易磨性。
因此,必须从原、燃料进行优化,提高被粉磨物料易磨性,从而提高粉磨效率。
水泥粉磨系统技术措施及技术改造的优化
2 0 年 第3 02 期
No. 2 0 3 O2
《 } 纪 书芘旱 瓤》 |世 C me t ief rN w p c e n d e E o h Gu o 耪膏 拄_ 木
中 图分类号 : Q 7 ’ 文献标识码 :B 文章编号 :1 807( 0 ) - 1 0 T I2 3 6 0 - 3 02 30 3 0 4 2 0 01 -
低,辊压 机略 高于立磨 ,但是从 运转 的稳 定性和对
维普资讯
2 O 年 第3 o2 期
N . 20 o3 0 2
张超等:水泥粉磨系统技术措施及技术改造的优化
1 . 球 磨机 内部结构 的改进 .4 1
艏謦垃摹
表2 国内几个厂家辊压机和立磨的使用情况 Байду номын сангаас
水泥粉磨 系统技 术措施及技术改造 的优化
张超 张永谋 陕西秦岭水泥股 份有限公 司 (2 10 770)
摘 要 水泥粉磨系统的每一个环节,如粉磨工艺、选粉机.磨机结构、研磨体级配等都有潜力可挖 均可通 过技术 改造优化选择使粉磨系统的自 力得到充分发摊 实现优质 ,高产,低消耗 关键词 水泥粉磨 粉磨工艺 收尘器 助磨剂 技术改造
项目 立磨 辊压 机
粉磨原理 ( 利用率 ,压力等 ) 圆周速 度
属于料床粉磨 ,所 施粉磨力多 次 利用率高: 压力低 ( 不能超过 5 MP ) 0 a; 压力角不超 10 。 2 圆周速度 是变化 的 U= ( ×g2 CD , )。
大 于3 %效果差,不 宜用 物 料受 0 挤压作用,物料易结饼,故配套选 粉机须有打散功能或单 设打散机 。
l . 采用H tmi 卧式辊 简磨 )和 高效选粉机 组成 l5 1 o l o l(
QC成果--提高水泥粉磨台时产量
自我评价表
项目 质量意识 个人能力 QC知识 工作理念
表8
团队精神
自我评价 (平均值)
活动前 (评分) 活动后 (评分)
3
2.5
2.8
3
3.5
5.5
4
4
5
5
制表人:吕常海2009年6月
自我评价雷达图
质量意识 6 团队精神 4 2 0 个人能力
活动前 (评分) 活动后 (评分)
工作理念
QC知 识
制图人:吕常海2009年6月
十、巩固措施
为保证取得的成果, 我们从以下几个方面进行了巩固措施:
ห้องสมุดไป่ตู้
每天对台时产量进行关注,若低于110 T/H,必须及时查找原因, 每月对粉煤灰秤的下料器叶片进行检查,若叶片间隙大于2MM时 时刻对辊压机辊间压力进行监控,若辊间压力低于170Bar时必须
原因查不清楚要召开专题会。 必须处理密封。 及时更换比例阀。
影响因素统计表
表3 : 序号 1 影响因素 辊压机辊间压力(Bar) 10月 136 11月 141 12月 138 设计值 165~175
2
3
磨机回粉量(t/h)
比表面积≥360㎡/kg
298
378
325
382
310
375
180~220
S≥360㎡/kg
【现状一】
经小组讨论分析,辊压机压力偏低且存有失压现象, 导致辊压机效能发挥不足,需及时处理。
王学飞
2008.12
2
粉磨效率低
改变磨机 级配
倒出磨机一仓、二仓的研磨体, 杨国春 进行人工筛选后重新称重级配 王学飞 吕常海 因比例阀属进口元件,比例阀 芯不能单独订购,只能整体更 换
- 1、下载文档前请自行甄别文档内容的完整性,平台不提供额外的编辑、内容补充、找答案等附加服务。
- 2、"仅部分预览"的文档,不可在线预览部分如存在完整性等问题,可反馈申请退款(可完整预览的文档不适用该条件!)。
- 3、如文档侵犯您的权益,请联系客服反馈,我们会尽快为您处理(人工客服工作时间:9:00-18:30)。
提高Φ×13m水泥磨台时产量的措施
我公司是2009年投产的年产120万吨粉磨站,有两条HFCG1200×450辊压机+SF500/100打散分级机+Φ×13球磨机组成的联合粉磨生产线,设计能力为80t/d,主导产品为P·水泥和P·水泥。
投产之初,达不到产量设计指标,两年来,经过采取一系列措施,台时产量有较大提高,取得了较好的效果。
1 投产之初的情况
原磨内设计级配(见表1)
原配料方案(见表2)
控制指标
P·水泥:比表面积≥350m2/kg, SO3:±
P·水泥:80μm筛余≤%,SO3:±
台时产量
(1)生产P·水泥时,台时产量在75~77 t/h;
(2)生产P·水泥时,台时产量在78~80 t/h;
2 工艺配料方案的调整
我们于2009年3月份投产,投产之初,生产P·水泥磨机台时产量在80t/h左右,生产P·水泥磨机台时产量在77t/h左右。
在配料方案上也做过几次调整,但由于磨前掺有矿渣,易磨性差,磨机台时产量始终没有达到设计要求。
为此,我们于2010年初对配料方案进行了重大调整,P·水泥磨前配料取消了矿渣掺量,P·水泥磨前仅保留3%左右的矿渣掺量,改在磨尾掺入矿渣粉,即在P·出磨水泥中掺加%的矿粉(磨前配料为100%,矿粉属于100%以外掺入)。
同样,在P·出磨水泥中掺加%的矿粉,出磨水泥与矿粉经过混料机混合后入成品库。
通过磨后外掺矿粉后,水泥熟料料耗都有不同程度的下降,水泥的后期强度有了明显的增长,而且磨机台时产量有了提高。
调整后的磨前配料方案见表3所示。
掺入矿粉后换算成入库水泥的组分见表4。
3 配料方案调整前后水泥性能的比较(见表5)
通过上述配料方案调整后,P·和P·水泥平均台时产量达到83吨左右。
4 对打散机和磨机内部进行了部分改进
针对个别用户反映水泥中有细小(1~)颗粒的问题,我们于2010年底对打散机筛板篦缝和磨内双隔仓板之间的筛板篦缝做了调整。
(1)打散机筛板篦缝由缩小到;为防止大颗粒飞溅到外层,将内筒加高了250mm。
(2)将磨内双层隔仓板之间的筛板篦缝由缩小到。
通过对筛板篦缝的改进,经方孔筛多次检验,水泥中没再出现用户反映的细小颗粒。
5 磨机级配的调整(见表6)
6 改进过程控制和操作方法
(1)每条生产线上有四台熟料秤,正常情况下只使用其中两台秤,由于熟料在库内分级,每台秤上的熟料颗粒、粉料交替出现,每次持续时间一般在6~8小时。
如果粉状熟料达到70%以上,严重影响辊压机的挤压效果。
为此,我们通知库下岗位工,根据熟料秤物料状况,定期更换不同的熟料秤,确保所使用的两台熟料秤一台为粒状、另一台为粉状,从而使物料颗粒得到合理搭配,稳定了进入辊压机的物料粒度,提高了挤压效果。
(2)对于筛分磨,物料水分对磨机的产量影响非常大。
我们控制出烘干机的矿渣水分小于%;其它物料水分小于%,入磨综合水分小于%。
水分超过%小于%时,台时产量将降低5%~10%;水分超过%时将出现饱磨现象,达到%以上,基本无法生产。
为此,建立了严格的物料水分控制考核制度,确保入磨水分得到有效控制。
(3)科学进行操作,适时调整辊压机进料闸板,保证料流稳定;过去,为控制进入辊压机物料的多少,采取棒阀插入长短的办法进行调节,现在认为,这一方法是不科学的。
采取棒阀插入长短的办法进行控制进入辊压机物料的做法,容易使进入辊压机的料流不均衡,易产生偏辊和振动。
通过适当调整辊压机进料闸板,控制进入辊压机物料的多少,并且使料流均衡,两侧压力一致,提高了挤压效果。
(4)投产之初,由于对辊压机还不够十分了解和掌握,担心压力过大产生振动而影响辊压机使用寿命,导致压力偏小,辊缝偏大,出辊压机颗粒偏大。
投产之初平均压力在~,平均辊缝在28~32mm。
经过外出学习和实际摸索,现在平均压力控制在~,平均辊缝在20~25mm。
保证实际电流达到额定电流的75%~80%(额定电流为440A),最大限度地发挥辊压机的挤压作用。
(5)合理控制磨头打散机除尘器的风机转速,使进入打散机的细粉尽可能全部被风抽走带入磨内,确保打散机回粉里没有细粉,以提高辊压机的挤压效果。
可以在回粉下料管开一个门,定期取样进行粒度检测,以没有细粉为宜。
(6)加强中控操作,科学利用除尘风机变频器,根据磨尾负压、温度、磨音和出磨水泥细度合理用风。
在物料水分不超过%,磨内隔仓篦板缝没有堵塞的情况下,生产P·水泥时,
磨尾除尘风机转速一般控制在700~800r/min左右;生产P·水泥时,磨尾除尘风机转速一般控制在800~900r/min(满负荷转速为960r/min)左右;如果水分偏大或磨内隔仓篦板缝有堵塞时,应适当提高磨尾除尘风机转速。
(7)定期进入磨内检查衬板、隔仓板的磨损情况,防止和避免研磨体窜仓,及时清理隔仓板篦缝内的杂质,以保证磨内物料流速和磨内通风良好。
(8)经常观察磨机电流的变化情况,根据电流变化及时补充研磨体,一般每半个月补球一次,补球时按照设计的平均球径,按比例补充各种规格的钢球。
每一个月补段一次,根据实测仓位合理添加。
7 结束语
经过采取以上一些措施,磨机台时产量有了稳定的提高。
据统计,2011年全年生产水泥85万吨,磨前平均台时产量h,水泥综合电耗下降了t,仅电费一项可创效益万元。