压圈冲压模具设计说明书终极版样本
压圈-冲压课程设计说明书
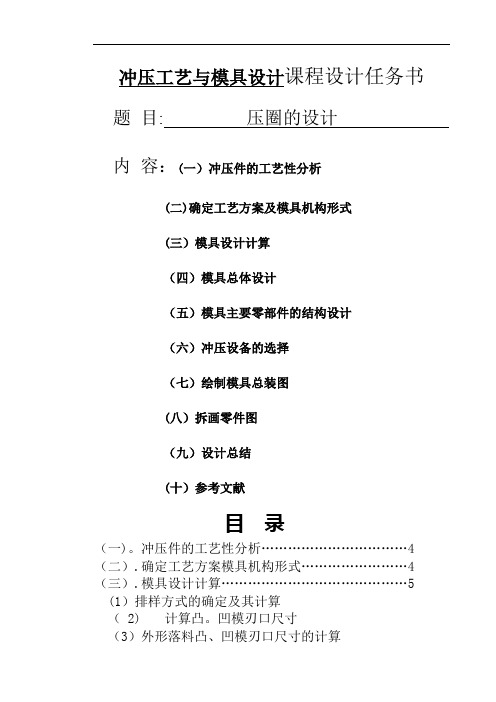
冲压工艺与模具设计课程设计任务书题目: 压圈的设计内容:(一)冲压件的工艺性分析(二)确定工艺方案及模具机构形式(三)模具设计计算(四)模具总体设计(五)模具主要零部件的结构设计(六)冲压设备的选择(七)绘制模具总装图(八)拆画零件图(九)设计总结(十)参考文献目录(一)。
冲压件的工艺性分析 (4)(二).确定工艺方案模具机构形式 (4)(三).模具设计计算 (5)(1)排样方式的确定及其计算( 2) 计算凸。
凹模刃口尺寸(3)外形落料凸、凹模刃口尺寸的计算(4)冲压力的计算(5)压力中心的计算(四)。
模具总体设计 (8)(五).模具主要零部件的结构设计 (9)(1)落料凸、凹模的结构设计(2)弹性元件的设计计算(3)模架的设计(六)。
冲压设备的选择 (12)(七)。
绘制模具总装图 (13)(八)。
拆画零件图 (13)(九)。
参考文献 (14)河南机专冲压课程设计说明书- 3 -11冲裁模具设计工件名称:压圈 生产批量:大批量材 料:Q235 厚 度:2mm 工件简图:如右图所示(一).冲压件的工艺性分析该零件形状简单、对称,是由圆弧和直线组成的.冲裁件内外形所能达到的经济精度为IT11~IT14。
凡产品图样上没有标注公差等级或者公差的尺寸,其极限偏差数值通常按IT14级处理.将以上精度与零件的精度要求相比较,可以为该零件的精度要求能够在冲裁加工中得到保证,其他尺寸标注、生产批量等情况,也均符合冲裁的工艺要求,故决定采用冲压方式进行加工。
经查公差表,各尺寸公差为: φ42-00。
62mm φ20+00.52mm 22+00.52mm 4+00。
3mm(二).确定工艺方案及模具结构形式该工件所需的冲压工序包括落料、冲孔两个基本工序,可以拟定出以下三种工艺方案:方案一:先落料,后冲孔,采用单工序模分两次加工。
方案二:落料-冲孔复合冲压,采用复合模加工. 方案三:落料—冲孔级进冲压,采用级进模加工.方案一模具结构简单,但需两道工序两副模具,成本高而生产效率低,难以满足顾客的要求,而且工件的累积误差大,操作不方便。
压圈冲压模具设计说明书(终极版)2
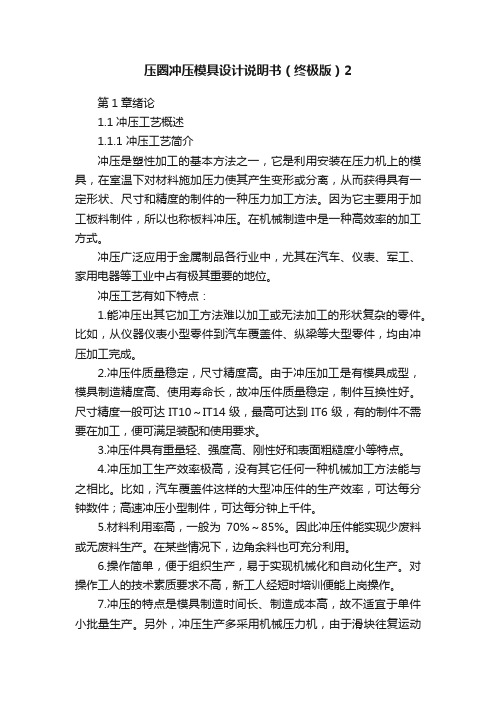
压圈冲压模具设计说明书(终极版)2第1章绪论1.1冲压工艺概述1.1.1 冲压工艺简介冲压是塑性加工的基本方法之一,它是利用安装在压力机上的模具,在室温下对材料施加压力使其产生变形或分离,从而获得具有一定形状、尺寸和精度的制件的一种压力加工方法。
因为它主要用于加工板料制件,所以也称板料冲压。
在机械制造中是一种高效率的加工方式。
冲压广泛应用于金属制品各行业中,尤其在汽车、仪表、军工、家用电器等工业中占有极其重要的地位。
冲压工艺有如下特点:1.能冲压出其它加工方法难以加工或无法加工的形状复杂的零件。
比如,从仪器仪表小型零件到汽车覆盖件、纵梁等大型零件,均由冲压加工完成。
2.冲压件质量稳定,尺寸精度高。
由于冲压加工是有模具成型,模具制造精度高、使用寿命长,故冲压件质量稳定,制件互换性好。
尺寸精度一般可达IT10~IT14级,最高可达到IT6级,有的制件不需要在加工,便可满足装配和使用要求。
3.冲压件具有重量轻、强度高、刚性好和表面粗糙度小等特点。
4.冲压加工生产效率极高,没有其它任何一种机械加工方法能与之相比。
比如,汽车覆盖件这样的大型冲压件的生产效率,可达每分钟数件;高速冲压小型制件,可达每分钟上千件。
5.材料利用率高,一般为70%~85%。
因此冲压件能实现少废料或无废料生产。
在某些情况下,边角余料也可充分利用。
6.操作简单,便于组织生产,易于实现机械化和自动化生产。
对操作工人的技术素质要求不高,新工人经短时培训便能上岗操作。
7.冲压的特点是模具制造时间长、制造成本高,故不适宜于单件小批量生产。
另外,冲压生产多采用机械压力机,由于滑块往复运动快,手工操作时,劳动强度大,易发生事故,故必须特别重视安全生产、安全管理以及采取必要的安全技术措施。
8.冲压模设计需要有很强的想象力与创造力,对于模具的设计者和制造者无论在理论、经验、创造力方面都要有很高的要求。
1.1.2 冲压模具的发展近年来,我国冲压模具水平已有很大提高。
压圈冲压模具设计说明书终极版word资料21页

第1章绪论1.1冲压工艺概述1.1.1 冲压工艺简介冲压是塑性加工的基本方法之一,它是利用安装在压力机上的模具,在室温下对材料施加压力使其产生变形或分离,从而获得具有一定形状、尺寸和精度的制件的一种压力加工方法。
因为它主要用于加工板料制件,所以也称板料冲压。
在机械制造中是一种高效率的加工方式。
冲压广泛应用于金属制品各行业中,尤其在汽车、仪表、军工、家用电器等工业中占有极其重要的地位。
冲压工艺有如下特点:1.能冲压出其它加工方法难以加工或无法加工的形状复杂的零件。
比如,从仪器仪表小型零件到汽车覆盖件、纵梁等大型零件,均由冲压加工完成。
2.冲压件质量稳定,尺寸精度高。
由于冲压加工是有模具成型,模具制造精度高、使用寿命长,故冲压件质量稳定,制件互换性好。
尺寸精度一般可达IT10~IT14级,最高可达到IT6级,有的制件不需要在加工,便可满足装配和使用要求。
3.冲压件具有重量轻、强度高、刚性好和表面粗糙度小等特点。
4.冲压加工生产效率极高,没有其它任何一种机械加工方法能与之相比。
比如,汽车覆盖件这样的大型冲压件的生产效率,可达每分钟数件;高速冲压小型制件,可达每分钟上千件。
5.材料利用率高,一般为70%~85%。
因此冲压件能实现少废料或无废料生产。
在某些情况下,边角余料也可充分利用。
6.操作简单,便于组织生产,易于实现机械化和自动化生产。
对操作工人的技术素质要求不高,新工人经短时培训便能上岗操作。
7.冲压的特点是模具制造时间长、制造成本高,故不适宜于单件小批量生产。
另外,冲压生产多采用机械压力机,由于滑块往复运动快,手工操作时,劳动强度大,易发生事故,故必须特别重视安全生产、安全管理以及采取必要的安全技术措施。
8.冲压模设计需要有很强的想象力与创造力,对于模具的设计者和制造者无论在理论、经验、创造力方面都要有很高的要求。
1.1.2 冲压模具的发展近年来,我国冲压模具水平已有很大提高。
大型冲压模具已能生产单套重量达50多吨的模具。
压圈冲压模具说明(终极版)2
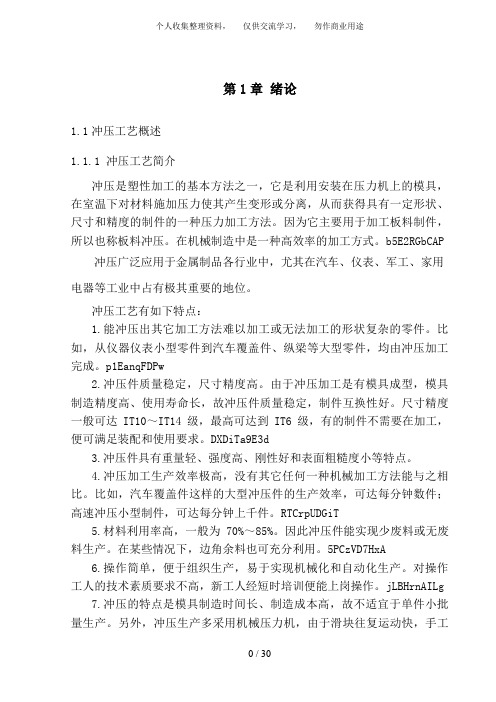
第1章绪论1.1冲压工艺概述1.1.1 冲压工艺简介冲压是塑性加工的基本方法之一,它是利用安装在压力机上的模具,在室温下对材料施加压力使其产生变形或分离,从而获得具有一定形状、尺寸和精度的制件的一种压力加工方法。
因为它主要用于加工板料制件,所以也称板料冲压。
在机械制造中是一种高效率的加工方式。
b5E2RGbCAP 冲压广泛应用于金属制品各行业中,尤其在汽车、仪表、军工、家用电器等工业中占有极其重要的地位。
冲压工艺有如下特点:1.能冲压出其它加工方法难以加工或无法加工的形状复杂的零件。
比如,从仪器仪表小型零件到汽车覆盖件、纵梁等大型零件,均由冲压加工完成。
p1EanqFDPw2.冲压件质量稳定,尺寸精度高。
由于冲压加工是有模具成型,模具制造精度高、使用寿命长,故冲压件质量稳定,制件互换性好。
尺寸精度一般可达IT10~IT14级,最高可达到IT6级,有的制件不需要在加工,便可满足装配和使用要求。
DXDiTa9E3d3.冲压件具有重量轻、强度高、刚性好和表面粗糙度小等特点。
4.冲压加工生产效率极高,没有其它任何一种机械加工方法能与之相比。
比如,汽车覆盖件这样的大型冲压件的生产效率,可达每分钟数件;高速冲压小型制件,可达每分钟上千件。
RTCrpUDGiT5.材料利用率高,一般为70%~85%。
因此冲压件能实现少废料或无废料生产。
在某些情况下,边角余料也可充分利用。
5PCzVD7HxA6.操作简单,便于组织生产,易于实现机械化和自动化生产。
对操作工人的技术素质要求不高,新工人经短时培训便能上岗操作。
jLBHrnAILg7.冲压的特点是模具制造时间长、制造成本高,故不适宜于单件小批量生产。
另外,冲压生产多采用机械压力机,由于滑块往复运动快,手工操作时,劳动强度大,易发生事故,故必须特别重视安全生产、安全管理以及采取必要的安全技术措施。
xHAQX74J0X8.冲压模设计需要有很强的想象力与创造力,对于模具的设计者和制造者无论在理论、经验、创造力方面都要有很高的要求。
冲压模具设计说明书
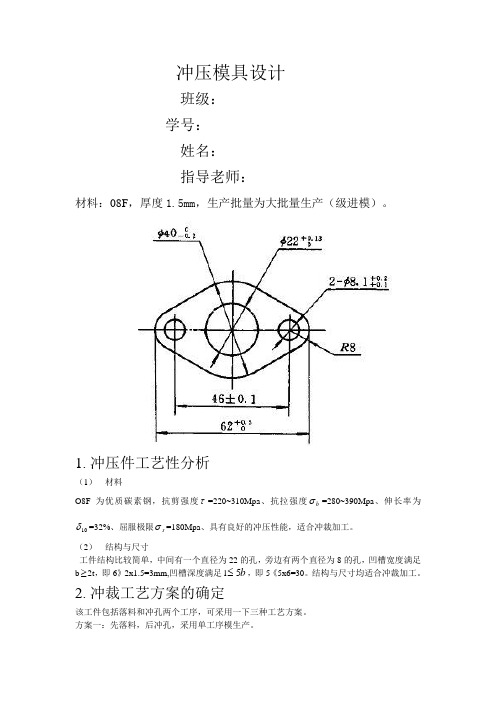
冲压模具设计班级: 学号: 姓名: 指导老师:材料:08F ,厚度1.5mm ,生产批量为大批量生产(级进模)。
1. 冲压件工艺性分析(1) 材料O8F 为优质碳素钢,抗剪强度τ=220~310Mpa 、抗拉强度b σ=280~390Mpa 、伸长率为10δ=32%、屈服极限s σ=180Mpa 、具有良好的冲压性能,适合冲裁加工。
(2) 结构与尺寸工件结构比较简单,中间有一个直径为22的孔,旁边有两个直径为8的孔,凹槽宽度满足b ≥2t ,即6》2x1.5=3mm,凹槽深度满足l b 5≤,即5《5x6=30。
结构与尺寸均适合冲裁加工。
2. 冲裁工艺方案的确定该工件包括落料和冲孔两个工序,可采用一下三种工艺方案。
方案一:先落料,后冲孔,采用单工序模生产。
方案二:落料——冲孔复合冲压,采用复合模生产。
方案三:冲孔——落料级进冲压,采用级进模生产。
综合考虑后,应该选择方案三。
因为方案三只需要一副模具,生产效率高,操作方便,工件精度也能满足要求,所以应该选用方案三比较合算。
3.选择模具总体结构形式由于冲压工艺分析可知,采用级进冲压,所以模具类型为级进模。
(1)确定模架及导向方式采用对角导柱模架,这种模架的导柱在模具对角位置,冲压时可防止由于偏心力矩而引起模具歪斜。
导柱导向可以提高模具寿命和工件质量,方便安装调整。
(2)定位方式的选择该冲件采用的柸料是条料,控制条料的送进方向采用导料板,无侧压装置;控制条料的送进步距采用侧刃粗定距;用导正销精定位保证内外形相对位置的精度。
(3)卸料、出件方式的选择因为该工件料厚1.5mm,尺寸较小,所以卸料力也较小,故选择弹性卸料,下出件方式。
4.必要的工艺计算(1)排样设计与计算该冲件外形大致为圆形,搭边值为a1=1.5mm,条料宽度为43.57mm,步距为A=88.4mm,一个步距的利用率为63.98%。
见下图S=1668.7-11x11x3.14-2x4x4x3.14=1188.28项目分类计算方法和结果排样冲裁件面积面积为1188.28mm条料宽度B=39.97+1.8+1.8=43.57mm 步距A=86.9+1.5=88.4mm材料利用率η冲压力的相关计算F 冲=KLt b τ=1.3*275*1.5*300=160875N F 卸=K 1F=0.04*160875=64350N F 推=nK 2F=4*0.055*160875=35392.5N F= F 冲+ F 卸+ F 推=260617.5N (3)计算模具压力中心代入公式X0=132.25115.69132.25396.14874.61132.2519.44115.6993.26132.250396.148++++++X X X X =19.73Y0=132.25115.69132.25396.14827.13132.250115.69)27.13(132.250396.148+++++-+X X X X =0(4) 计算凸、凹模工作部分尺寸并确定其制造公差 由于凸凹模的形状相对简单且材料较厚,冲裁间隙较大,可采用分开加工法确定凸凹模的刃口尺寸及公差。
压圈冲压模具设计说明书

江门职业技术学院毕业设计--压圈冲压模具设计说明书2011届专业学号学生姓名指导教师完成日期 2014年12月24日目录绪论 (4)第1章冲压工艺概述 (4)1.1.1冲压工艺的简介 (4)1.1.2冲压模具的发展 (5)1.2 工艺方案的确定 (6)1.2.1 锡青铜QSn4-4-2.5的性能 (6)1.2.2 方案确定 (6)1.2.3有关设计 (7)第2章复合冲压模具设计与计算 (7)2.1 冲裁件的工艺设计 (7)2.1.1冲裁件的工艺性分析 (7)2.1.2 确定工艺方案及模具形式 (7)2.2凹凸模间隙的选择 (7)2.2.1冲裁间隙的分类 (8)2.2.2 冲裁间隙对冲裁件的影响 (8)2.2.3 间隙对尺寸精度的影响 (8)2.2.4 间隙对冲裁力的影响 (8)2.2.5 间隙对模具寿命的影响 (9)2.2.6 确定合理间隙的理论依据 (9)2.2.7合理间隙的选择 (9)2.3凹凸模制造方法及刃口尺寸的计算 (10)2.3.1 凹凸模的制造方法 (10)2.3.2凹凸模刃口尺寸的计算 (10)2.4排样 (12)2.4.1排样的意义 (12)2.4.2排样的方法 (12)2.4.3搭边、进距计算 (13)2.5冲裁力的计算及选择压力机 (15)2.5.1冲裁力的计算 (15)2.5.2选择压力机 (19)2.6冲裁模主要零件的设计 (20)2.6.1凹模设计 (20)2.6.2 凹凸模设计 (22)2.6.3冲孔凸模的设计 (22)2.6.4定位零件的确定 (23)2.6.5卸料与推料装置 (23)2.6.6模座、导向零件 (24)2.6.7连接与固定零件 (24)致谢 (25)绪论冲压成形作为现代工业中一种十分重要的加工方法,用以生产各种板料零件,具有很多独特的优势,其成形件具有自重轻、刚度大、强度高、互换性好、成本低、生产过程便于实现机械自动化及生产效率高等优点,是一种其它加工方法所不能相比和不可替代的先进制造技术,在制造业中具有很强的竞争力,被广泛应用于汽车、能源、机械、信息、航空航天、国防工业和日常生活的生产之中。
精选-冲压模具设计说明书模板-1

(2014-2015学年第二学期)
姓名:陈晔彬徐松姜旭
提交日期:年月日
学号
学院
材料学院
课程编号
0822254426
课程名称
冲压工艺及模具设计
专业
材料成型
任课教师
夏春艳
教师评语:
成绩评定:分任课教师签名:年月日
说明
1、设计说明书要求自己动手撰写,如发现是从网上下载的,或者是抄袭剽窃别人设计的,按作弊处理,本门课程考核成绩计0分。
查标准JB/T -6743.1-94:凹模板宽B=125mm
取标准凹模尺寸为:125×125×14(mm)。
固定方法:用螺钉和销钉直接固定在模板上。
3.凸模的强度、刚度校核
根据该冲裁件的凸模不是特别细长,且该冲裁件厚度较小,所以可对凸模不进行强度,
刚度校核。
五、参考文献
[1]陈淑华,付青,等.基于神经网络自适应预测算法的谐波检测[J].电工技术学报,2011,26( 1) : 200-206.
凹模边壁厚:c≥(1.5~2)H
=(1.5~2)×17.64
=(26.46~35.28)mm实取c=30mm
凹模板宽度:B=S+(2.5~4.0)H
=62+(44.1~70.56)=(106.1~132.56)mm实取B=120mm
凹模板边长:L=b+2c
=62+2×30
=122mm
故凹模板外形尺寸为:120×122×17.64(mm)。
四、结构设计
(一)1.选择模具总体结构形式
根据以上分析,采用导料板加固定挡料销定位的弹性卸料及上出件的单工序模。
2.排样设计
(二)凹模的设计
1.凹模材料的选定
冲压模设计手册(珍藏版)

开计算原理 板料在弯曲过程中外层受到拉应力,内层受到压应力,从拉到
压之间有一既不受拉力又不受压力的过渡层--中性层,中性层在弯曲过程中的
长度和弯曲前一样,保持不变,所以中性层是计算弯曲件展开长度的基准,
中性层与板料厚度的中间层是不同的概念。中性层位置与变形程度有关,当
弯曲半径较大,折弯角度较小时,变形程度较小,中性层位置靠近板料厚度的
三:模具设计
1.模具设计流程 (1) 模具设计流程图
技术文件
未经允许不得翻印
2008 年 5 月第 1 版
-2-
文件:模具设计标准
客户产品图 样品
工艺分析要点
工艺评估
疑问 OK 产品加工图
反馈 提议/建议 技术讨论
产品图展开标准
L=A-T+C+B+K (3)当 C ≦3T 时<一 次 成 型 > :
L=A-T+C+B+K/2
Z 折 2. C≦3T 时<一次成型> :
L = A -T + C + B + D+ K
抽芽 抽芽孔尺寸计算原理为体积不变原理 ,即抽孔
前后材料体积不变;ABCD 四边形面积=GFEA 所 围成的面积.
a
l
T
B A
l
中性層 中性層
技术文件
未经允许不得翻印
2008 年 5 月第 1 版
-7-
文件:模具设计标准
(1)当 C ≧5 时, 一 般 分 两 次 成 型 , 按 两 个 90°折 弯 计 算. L=A-T+C+B+2K
(2)当 3T<C<5 时<一 次 成 型 > :
- 1、下载文档前请自行甄别文档内容的完整性,平台不提供额外的编辑、内容补充、找答案等附加服务。
- 2、"仅部分预览"的文档,不可在线预览部分如存在完整性等问题,可反馈申请退款(可完整预览的文档不适用该条件!)。
- 3、如文档侵犯您的权益,请联系客服反馈,我们会尽快为您处理(人工客服工作时间:9:00-18:30)。
第1章绪论1.1冲压工艺概述1.1.1 冲压工艺简介冲压是塑性加工的基本方法之一, 它是利用安装在压力机上的模具, 在室温下对材料施加压力使其产生变形或分离, 从而获得具有一定形状、尺寸和精度的制件的一种压力加工方法。
因为它主要用于加工板料制件, 因此也称板料冲压。
在机械制造中是一种高效率的加工方式。
冲压广泛应用于金属制品各行业中, 特别在汽车、仪表、军工、家用电器等工业中占有极其重要的地位。
冲压工艺有如下特点:1.能冲压出其它加工方法难以加工或无法加工的形状复杂的零件。
比如, 从仪器仪表小型零件到汽车覆盖件、纵梁等大型零件, 均由冲压加工完成。
2.冲压件质量稳定, 尺寸精度高。
由于冲压加工是有模具成型, 模具制造精度高、使用寿命长, 故冲压件质量稳定, 制件互换性好。
尺寸精度一般可达IT10~IT14级, 最高可达到IT6级, 有的制件不需要在加工, 便可满足装配和使用要求。
3.冲压件具有重量轻、强度高、刚性好和表面粗糙度小等特点。
4.冲压加工生产效率极高, 没有其它任何一种机械加工方法能与之相比。
比如, 汽车覆盖件这样的大型冲压件的生产效率, 可达每分钟数件; 高速冲压小型制件, 可达每分钟上千件。
5.材料利用率高, 一般为70%~85%。
因此冲压件能实现少废料或无废料生产。
在某些情况下, 边角余料也可充分利用。
6.操作简单, 便于组织生产, 易于实现机械化和自动化生产。
对操作工人的技术素质要求不高, 新工人经短时培训便能上岗操作。
7.冲压的特点是模具制造时间长、制造成本高, 故不适宜于单件小批量生产。
另外, 冲压生产多采用机械压力机, 由于滑块往复运动快, 手工操作时, 劳动强度大,易发生事故, 故必须特别重视安全生产、安全管理以及采取必要的安全技术措施。
8.冲压模设计需要有很强的想象力与创造力, 对于模具的设计者和制造者无论在理论、经验、创造力方面都要有很高的要求。
1.1.2 冲压模具的发展近年来, 中国冲压模具水平已有很大提高。
大型冲压模具已能生产单套重量达50多吨的模具。
为中档轿车配套的覆盖件模具内也能生产了。
精度达到1~2μm, 寿命2亿次左右的多工位级进模国内已有多家企业能够生产。
表面粗糙度达到Ra≤1.5μm的精冲模, 大尺寸( φ≥300mm) 精冲模及中厚板精冲模国内也已达到相当高的水平。
1. 模具CAD/CAM技术状况中国模具CAD/CAM技术的发展已有20多年历史。
由原华中工学院和武汉733厂于1984年共同完成的精冲模CAD/CAM系统是中国第一个自行开发的模具CAD/CAM系统。
由华中工学院和北京模具厂等于1986年共同完成的冷冲模CAD/CAM系统是中国自行开发的第一个冲裁模CAD/CAM系统。
20世纪90年代以来, 国内汽车行业的模具设计制造中开始采用CAD/CAM技术。
国家科委863计划将东风汽车公司作为CIMS应用示范工厂, 由华中理工大学作为技术依托单位, 开发的汽车车身与覆盖模具CAD/CAPP/CAM集成系统于1996年初经过鉴定。
2.模具设计与制造能力状况在国家产业政策的正确引导下, 经过几十年努力, 现在中国冲压模具的设计与制造能力已达到较高水平, 包括信息工程和虚拟技术等许多现代设计制造技术已在很多模具企业得到应用。
虽然如此, 中国的冲压模具设计制造能力与市场需要和国际先进水平相比仍有较大差距。
这一些主要表现在高档轿车和大中型汽车覆盖件模具及高精度冲模方面, 无论在设计还是加工工艺和能力方面, 都有较大差距。
轿车覆盖件模具, 具有设计和制造难度大, 质量和精度要求高的特点, 可代表覆盖件模具的水平。
虽然在设计制造方法和手段方面基本达到了国际水平, 模具结构周期等方面, 与国外相比还存在一定的差距。
汽车覆盖件模具制造技术正在不断地提高和完美, 高精度、高效益加工设备的使用越来越广泛。
高性能的五轴高速铣床和三轴的高速铣床的应用已越来越多。
NC、 DNC 技术的应用越来越成熟, 能够进行倾角加工超精加工。
这些都提高了模具面加工精度, 提高了模具的质量, 缩短了模具的制造周期。
1.2工艺方案的确定1.2.1 锡青铜QSn4-4-2.5的性能QSn4-4-2.5经退火处理后, 其抗剪强度为125~550MPa, 其抗拉强度为294~490 MPa, 其伸长率为5%~35%, 适合于做冲压材料。
××图1—1—1 压圈( 二维图)图1—1—2 压圈( 三维图)1.2.2 方案确定方案一: 冲孔—落料方案二: 落料, 冲孔(复合)方案三: 落料, 冲孔(连续)方案一: 单工序模, 先冲孔再落料保证一定的精度, 但主要适用于生产量较小或单件生产, 生产率较低, 且多了一模具, 生产周期长。
方案二: 避免了多次定位的结构, 并在冲裁过程中能够压料, 工件较平整, 较单工序模缩短生产周期。
方案三: 根据生产量, 模具能够采用连续模, 可是连续模的结构复杂, 对制造精度的要求高, 连续模比复合模比较生产周期长, 成本高, 维护也困难。
经过比较分析压圈的冲压模具设计采用方案二。
1.2.3 有关设计压圈由落料冲孔单工步成型, 只需设计落料冲孔复合模。
压圈生产过程由于结构废料较多, 原材料的利用率较低, 而模具费用的份额比例较大, 这样要求模具的结构简单, 生产率高, 落料冲孔复合模设计成一模一腔。
复合模采用倒装结构, 冲孔废料直接由冲孔凸模从凸凹模内孔推下, 卸件可靠, 操作安全方便, 生产效率高, 并为机械化出件提供有利条件, 应用十分广泛。
第2章复合冲压模具设计与计算2.1 冲裁件的工艺设计2.1.1冲裁件的工艺性分析冲裁件的工艺性分析是指冲裁件对冲裁的适应性, 即冲裁件的形状结构、尺寸的大小及偏差等是否符合加工的工艺要求。
冲裁件的工艺性是否合理对冲裁件的质量、模具的寿命和生产率有很大影响。
压圈形状简单、对称, 是由圆弧和直线组成的, 冲裁件内外所能达到的经济精度为IT11, 该零件的精度要求能够在冲裁加工中得到保证.其生产批量等情况, 也均符合冲裁的工艺要求, 故经压圈符合冲裁工艺要求。
2.1.2 确定工艺方案及模具形式综上分析, 冲裁件精度要求不高, 尺寸不大, 形状不复杂生产量为大批量生产, 材料厚度, t=0.2mm,且孔位精度无要求, 采用手工送料、刚性卸料、自动漏料、导料销导料的冲孔落料复合冲裁模具结构形式。
2.2凹凸模间隙的选择冲裁间隙指凸、凹模刃口间隙的距离。
冲裁间隙是冲压工艺和模具设计中的重要参数, 它直接影响冲裁件的质量、模具寿命和力能的消耗, 应根据实际情况和需要合理的选用。
冲裁间隙有单面间隙和双面间隙之分。
2.2.1冲裁间隙的分类根据冲裁件尺寸精度、剪切质量、模具寿命和力能消耗等主要因素, 将金属材料冲裁间隙分成三种类型: Ⅰ类( 小间隙) , Ⅱ类( 中等间隙) , Ⅲ类( 大间隙) 。
2.2.2 冲裁间隙对冲裁件的影响1、间隙过小时, 由凹模刃口处产生的裂纹在继续加压的情况下将产生二次剪切, 继而被挤入凹模。
这样, 制件端面中部留下撕裂面, 而两头出现光亮带, 在端面出现挤长的毛刺。
毛刺虽长单易去除, 只要中间撕裂不是很深, 仍可用。
2、间隙过大时, 材料的弯曲与拉伸增大, 拉伸应力增大, 材料容易被撕裂, 使制件的光亮代减小, 圆角与断裂都增大, 毛刺大而厚, 难去除。
因此随着间隙的增大, 制件的断裂面的倾斜度的增大, 毛刺增高。
2.2.3 间隙对尺寸精度的影响当凸、凹模的间隙较大时, 材料所受拉伸作用增大。
冲裁完后, 材料的弹性恢复使落料尺寸小于凹模尺寸, 冲孔孔径大于凸模直径。
此时穹弯的弹性恢复方向与其相反, 鼓薄板冲裁时制件尺寸偏差减小。
在间隙较小时, 由于材料受凸、凹模挤压力大, 故冲裁完后, 材料的弹性恢复使落料件尺寸增大, 冲孔孔径减小。
2.2.4 间隙对冲裁力的影响随着间隙的增大, 材料所受的拉力增大, 材料容易断裂分离, 因此冲裁力减小。
可是继续增大间隙时, 会因从凸、 凹模刃口处产生的裂纹不重合, 冲裁力减小。
由于间隙的增大, 使冲裁件的光亮面变小, 落料尺寸小于凹模尺寸, 冲孔尺寸大于凸模尺寸, 因而使卸料力、 推件力或顶件力也随之减小。
可是, 间隙继续增大时, 因为毛刺增大, 引起卸料力、 顶件力也迅速增大。
2.2.5 间隙对模具寿命的影响冲裁模具的寿命一般以保证获得合格产品时的冲裁次数来表示。
冲裁过程中模具的失效形式一般有: 磨损、 变形、 崩刃和凹模刃口涨裂四种。
间隙增大时可使冲裁力、 卸料力等减小, 因而模具的磨损也减小; 但当间隙继续增大时, 卸料力增加, 又影响模具磨损, 一般间隙为( 10%--15%t) 时磨损最小模具寿命较高。
间隙小时, 落料件梗塞在凹模洞口的涨裂力也大。
2.2.6 确定合理间隙的理论依据由以上分析可见, 凸、 凹模对冲裁件质量、 冲裁力、 模具寿命等都有很大的影响。
因此, 在设计和制造模具时有一个合理的间隙值, 以保证冲裁件的断面质量好, 尺寸精度高, 所需冲裁力小, 模具寿命高。
生产中常选用一个适当的范围作为合理间隙。
这个范围的最小值称为最小合理间隙Z min ,最大值称为最大合理间隙Z max 。
设计与制造新模具时采用最小合理间隙值。
确定合理间隙的理论根据是以凸、 凹模刃口处产生的裂纹相重合为依据。
能够计算得到合理间隙值, 计算公式如下: Z=2t(1-th 0 )tan β 由上式可看出, 间隙z 与材料厚度t 、 相对切入深度h 0/t 及破裂角β有关。
对硬而脆的材料, h 0/t 有较小值时, 则合理间隙值较大。
对软而韧的材料, h 0/t 有较大值, 则合理间隙值较小。
板厚越大, 合理间隙越大。
由于理论计算在生产中不便使用, 故当前广泛使用的是经验数据。
2.2.7合理间隙的选择表2-1常见金属材料的冲裁初始间隙( 双面)zmax=zmin+△z, 由表可知, 此复合模的最小双面间隙为zmin=0.010mm, 最大双面间隙为zmax=0.020mm。
2.3凹凸模制造方法及刃口尺寸的计算2.3.1 凹凸模的制造方法凸、凹模的加工方法有两种: 凸、凹模分开加工法和凸、凹模配合加工方法。
当凸、凹模分开加工时, 模具具有互换性, 便于模具成批量生产, 但精度要求很高, 制造困难, 相应的会增加加工成本。
凸、凹模配合加工适合于较复杂的、非圆形的模具, 制造简单, 成本低。
鉴于上述分析, 就零件图所需的凸、凹模宜采用凸、凹模配合加工。
2.3.2凹凸模刃口尺寸的计算模具刃口尺寸精度等级是影响冲裁件尺寸精度等级的主要因素, 模具的合理间隙值也是靠模具刃口尺寸及其精度来保证的。
因此, 在确定凹、凸模工作部分尺寸及其。