Hydrogen storage on carbonized chicken feather fibers
外文翻译--储氢的风力涡轮机水塔

外文翻译Hydorgen storage in wind turbine towersInternational Journal of Hydrogen Energy 29 (2004) 1277–1288 Ryan Kottenstettea, Jason Cotrellb; aSummer intern from Santa Clara University, 1235 Monroe St, Santa Clara, CA 95050, USA National Wind Technology Centre, National Renewable Energy Laboratory, 1614 Cole Blvd, Golden, CO 80401, USA Received 18 November 2003; accepted 15 December 2003 Abstract: Modern utility-scale wind turbine towers are typically conical steel hydrogen in what we have termed a hydrogen tower. This paper examines potential technical barriers to this technology and identi4es a minimum cost design. We discovered that hydrogen towers have a “crossover pressure” at which the critical mode of failure crosses over from fatigue to bursting. The crossover pressure for many turbine towers is between 1.0 and 1:5 mPa (approximately 10–15 atm) The hydrogen tower design resulting in the least expensive hydrogen storage uses all of the available volume for storage and is designed at its crossover an additional $83,000 beyond the cost of the conventional tower) and would store 940 kg of hydrogen at1:1 mPa of pressure. The resulting incremental storage cost of $88/kg is approximately 30% of that for conventional pressure vessels. Published by Elsevier Ltd on behalf of the International Association for Hydrogen Energy.Keywords: Wind turbine; Tower; Hydrogen; Storage; Pressure vessel1. IntroductionLow-cost hydrogen storage is recognized as a cornerstone of a renewables-hydrogen economy. Modern utility-scale wind turbine towers are typically conical steel structures that, in addition to supporting the nacelle, could be used to store gaseous hydrogen. We have coined the phrase hydrogen tower to describe this technology. During hours, electrolyzers could use energy from the wind turbines or the grid to generate hydrogen and store it in turbine towers. There are many potential uses for this stored fuel. The stored hydrogen could later be used to generate electricity via a fuel cell during times of peak demand.This capacity for energy storage could signi4cantly mitigate the drawbacks to the Auctuating nature of the wind and provide a cost ective means of meeting peak demand. Alternatively, the hydrogen could be used for fuel cell vehicles or transmitted to gaseous hydrogen pipelines. Storing hydrogen in a wind turbine tower appears to have been 4rst suggested by Lee Jay Fingersh at the National Renewable Energy Laboratory An extension of the hydrogen tower idea is to store hydrogen in shore wind turbine towers and posibly even foundations. shore foundations are of ten monopiles which could potentially provide large amounts of storage without ecting the positioning ladder, and power electronics. A similar idea for generating and storing hydrogen in the base of a Aoating shore wind turbine was proposed by William Heronemus in the 1970s However, this study focuses on the economics and design of onshore hydrogen towers. The objectives of this paper are as follows:(1) Identify the paramount considerations associated with using a wind turbine tower for hydrogen storage.(2) Propose and analyze a cost ective design for a hydrogen tower.03603199/$ 30.00 Published by Elsevier Ltd on behalf of the International Association for Hydrogen Energy.(3) Compare the cost of storage in hydrogen towers to the cost of hydrogen dtorage storage in conwentional pressure vesselsThere are many competitive methods of storing hydrogen such as liquid hydrogen storage, underground geologic storage, and transmission pipeline storage. However, a comparison was made only to one storage technology to limit the scope of this study. Conventional pressure vessel tech- nology was chosen because it is the most widely available of the technologies and the method most likely to be used for the moderate amounts of hydrogen storage considered in this study. This study engages these objectives within the wider wind-hydrogen system,Various balance of station costs such as transportation, licensing, and piping are therefore outside the scope of this report. This paper outlines the assumptions made during this study, outlines primary considerations associated with a hydrogen tower, highlights design characteristics of a hydro- gentower, presents several conceptual designs, and assesses the feasibility of the concept based on comparisons to con- ventional towers and pressure vessels2. Benchmarks and assumptions2.1. Hydrogen generationThis study assumes electrolyzers generate the hydrogen to be stored in the hydrogen towers. As will later be demonstrated, the most economical pressures for storage in hydrogen towers are below 1:5 mPa. This study assumes that proton exchange membrane (PME) and high-pressure alkaline electrolyzers can produce htdrogen up to this pressure without the use of an additional compressor2.2. Conventional towersWe chose to use the 1.5-MW tower model speci4ed in the WindPACT Advanced Wind Turbine Designs Study as our baseline conventional tower This tower was modeled after a conventional tower built from four tapered, tubular, steel sections which are bolted together. Conventional towers are built by welding together cylingenerally decrease in steps as the tower tapers to smaller diameters at higher elevations. For simplicity, the Wind PACT tower model instead assumes the wall thickness tapers in a smooth linear fashion. The model assumes a constant tower diameter/wall thickness (d=t) ratio of 320. In order to save material costs, a highd tratio is desirable. However, forratios above 320, towers become subject to local wall buck- ling problems. Additional assumptions regarding the tower are that the diameter at the top is constrained to be at least 1=2 of the base diameter; the steel used for the tower walls has a yield strength of 350 mPa (about 50 ksi); and the cost of the tower is $1.50/kg [3]. For the purposes of this study, other costs were included, such as a personnel ladder ($10/ft), and a tower access door ($2000 4xed cost). The modeled tower is shown in Fig.1with a tabulation of critical values listed in Table1.2.3. Conventional pressure vesselsIndustrial pressure vessels for noncorrosive gases are of- ten built of carbon steel similar to that used in wind turbine tower construction. Although the most economical pressure vessel geometry is long and slender, vessels are often limited by shipping constraints to a practical length of about25m. This length limitation means that in order to better distribute the high 4xed costs associated with 4ttings and manways, pressure vessels are designed with relatively large diameters and high pressure ratings. Although higher pressures reduce the cost per kg of stored gas, higher pressures In this paper, storage devices are often compared based on a cost/mass ratio. This ratio is the cost (in dollars) of a storage device divided by the mass of deliverable hydrogen gas stored. The cost/mass ratio is used because it is more convenient than the common practice of citing a volumetric capacity and a pressure rating for each storage device. Use of the cost/mass ratio does, however, make the given values accurate only for hydrogen storage. Deliverable hydrogen is the amount of hydrogen in the storage reservoir that can be extracted during the normal operation of the storage facility. In pressure vessels, a certain amount of gas is required to pro- vide a cushion. This is the volume of gas that must remain in the storage facility to provide the required pressurization to extract the remaining gas. In some scenarios, such as underground storage, the volume of inaccessible gas can be sign cost to In this study, the ect of this cushion gas is neglected when computing the store gaseous hydrogen because it is small when compared to other storage- related costs. In addition, this study models hydrogen as an ideal gas. This approximation is sulciently accurate for the low temperatures and pressures considered in this study.3. Hydrogen tower considerationsHydrogen storage creates a number of additional considerations in wind turbine tower design. Accelerated at- mosphericcorrosion on the tower interior and hydrogen embrittlement may adversely aect the tower’s ductility, yield strength, and fatigue life. Additionally, storing hydrogen at pressure signi4cantly increases the stresses on the tower. Therefore, wall reinforcement will likely be required. A structural analysis is required to evaluate how internal pressure may the tower’s design life.3.1. CorrosionBoth atmosphericcorrosion and hydrogen embrittlement will ect the interior of a hydrogen tower. Conventional wind turbine towers are protected internally and externally from atmosphericcorrosion by paint. When a tower is used to store a pressurized gas, however, it becomes subject to the guidelines set forth in the American Society of Mechanical Engineers (ASME) Boiler and Pressure Vessel Code. The code states that paint is not an adequate form of protection for the interior of pressure vessels. Enough material must therefore be added to anticipate atmospheric corrosion . Fortunately, the interior of a hydrogen tower is a controlled environment. Hydrogen from a PEM electrolyzer does not contain contaminants that cause atmospheric corrosion (of primary concern are sulfur dioxide and chlorine).The product hydrogen (which would be fully saturated with water vapor) could be dried to below the critical humidity level (less than 80% relative humidity) at minimal cost. Under these conditions, atmospheric corrosion would penetrate the steel’s surface at the negligible rate of less than 0.01m per year3.2. Hydrogen attackOne of the two primary modes of corrosion failure when steel is exposed to a hydrogen environment is hydrogen attack Although some sources do not distinguish hydrogen attack from hydrogen embrittlement (HE), other sources distinguish them by their diering responses to temperature. It is important not to confuse hydrogen attack, a phenomenon that occurs only at high temperatures, with HE, a phenomenon that primarily damages materials at ambient temperatures. Hydrogen attack, also known as hydrogen-induced cr acking, is a process wherein hydrogen diuses through the steel’s lattice structure, coalescing at voids and inclusions where the hydrogen reacts with the carbon present in the steel. This results in decarburization, as well as the formation of methane gas. The methane gas exerts an internal pressure, causing 4ssures or internal cracking. Hydrogen attack does not occur below 200℃; for this reason it is commonly called high-temperature hydrogen at- tack. It is anticipated that hydrogen storage in turbine towers will be at or near ambient temperatures (25℃–30℃), which are far enough below the 200℃threshold to make hydrogen attack an unlikely phenomenon.3.3. Hydrogen embrittlementThe term hydrogen embrittlement is commonly used to describe hydrogen environment embrittlement (HEE) and internal hydrogen embrittlement. HEE is caused by subjecting metal to a hydrogen-rich environment. During internal hydrogen embrittlement, hydrogen is produced inside a metal’s structure, usually by a processing technique and is unlikely to be relevant to hydrogen towers. The term hydrogen embrittlement will refer to HEE for the remainder of this paper. HEE is a process in which atomic hydrogen (Has opposed to H2) adsorbs to a metal’s surface and cau ses brittle failure below the yield strength of an aected material. Many factors inAuence a compo- nent’s susceptibility to hydrogen embrittlement. Those factors relevant to turbine towers consist of environ- mental ects including temperature, pressure, and hydrogen purity, as well as material properties including grain size, hardness, and strength. This section explore how hydrogen embrittlement may ect a hydrogen tower. Evidence suggests that, unlike hydrogen attack, hydrogen environment embrittlement may be most severe at ambient temperatures Like hydrogen attack, however, HEE becomes more severe with increasing pressure. Test data suggests that the degree of embrittlement is proportional to the square root of hydrogen gas pressure This suggests that designing turbine towers for relatively low-pressure storage may help prevent hydrogen embrittlement. It is fortunate, therefore, that the storage pressures under consideration are only about 10% of hydrogen pipeline operating pressures. Hydrogen gas purity is another major environmental factor controlling HEE. Experimental evidence has shown that crack propagation in a stressed specimen could be controlled by the introduction of oxygen into the hydrogen environment. Investigators demonstrated that a crack propagating in a pure hydrogen environment could be stopped with the introduction of as little as 200 ppm oxygen at atmospheric pressure Because the method of H2production under consideration is via an electrolyzer, gas will be readily available. Al- though adding to H2can result in an explosive mixture, adding the necessary levels of is expected to have little ect on safety. This is because the required oxygen con- centration (approximately 200 ppm) is far above the upper combustible limit of hydrogen in oxygen (94% by volume). Two hundred ppm oxygen in hydrogen represents only0.02% (by volume) of the oxygen required to create an explosive environment. Steel composed of larger grains with precipitates heavily concentrated along grain boundaries can also expedite HEE because they allow for easier diusion of hydrogen through the metal’s lattice structure The Sourcebook for Hydrogen Applications lists proper control of grain size as a successful measure of HEE prevention Grain size is controlled in the steel forming and treatment process. For tunately, selection of steel plate with the appropriate grain size is not anticipated to be diLcult. Increased material hardness can also magnify the ects of hydrogen embrittlement. Typically, hardness is increased by causing residual tensile str esses in a material’s surface through treatments like forging, cold rolling, or welding. Theoretically, when hydrogen adsorbs to a material’s surface, it decreases the energy required to form a surface crack The combination of these two factors facilitates the for mation of surface cracks. Tower welds are therefore particularly susceptible to HEE because rapid cooling of the welds can cause “hard spots” where carbon and other impurities coalesce. However, as a general guideline, trouble-free welds can be obtained in low-alloy steels containing up to about 0.28% carbon and to a carbon equivalent (C +14Mn) of about0.55% Steels ering the strength assumed in this study (such as S355J0 as speci4ed by British Standard EN 10025 and Grade485 steel as speci4ed by ASTM Speci4cation A 516/A) have equivalent carbon contents of 0.65% and 0.60%, respectively. These steels require preheating of the joint and the use of low-hydrogen electrodes to protect their welds from HE. Alternatively, the tower’s structural requirements could be met with thicker walls made of steels having lower carbon and manganese contents or possibly by the use of steels which meet the American Petroleum Institute speci4- cation 5L such as X70—a 70 ksi steel which is resistant to hydrogen induced cracking. Another possibility which this study does not address is the use of composite reinforcement of the tower walls. Material strength, a property related to both grain size and hardness, is perhaps the most predominant material property inAuencing hydrogen embrittlement. It has been generally observed that higher-strength steels exhibit greater loss of ductility, lower ultimate strengths, and greater propensity for delayed failure than their lower-strength counterparts when subjected to a hydrogenenvironmentIt is for these rea- sons that many experts suggest use of lower-strength steels for hydrogen applications. Some experts have designated an ultimate strength of 700 MPa as a benchmark, below which steels are signi4cantly less susceptible to HEE Steels commonly used for tower construction fall within this bench- mark; towers are typically constructed of a low-strength, low-carbon structural steel with yield and ultimate strengths at or below 350 and 630 MPa, respectively.Based on the considerations outlined above, the risk of HEE does not exclude the use of wind turbine towers for hydrogen storage. It is, however, diLcult to compare the use of a wind turbine tower as a pressure vessel to more tra- ditional hydrogen applications because, unlike conventional pressure vessels, they are subjected to signi4cant dynamic loads inherent in wind turbine structures. The dynamic struc- tural loads applied to a turbine tower would serve to repeat- edly open micro4ssures, one mechanism by which HEE is theorized to propagate. Due to the potential for catastrophic failure, HEE requires more research and experimentation.3.4. Structural analysisPressurizing the interior of a wind turbine tower creates unique structural demands. A pressurized tower must not only withstand loads caused by normal operation of the wind turbine, but it must also ful4ll the requirements of a pres- sure vessel. Tubular towers for modern utility-scale wind turbines are typically limited by the fatigue strength of the horizontal welds. One primary concern, therefore, is the ef- fect of pressurizing the tower on the fatigue strength of these welds. In addition, the hydrogen pressure loads must not exceed allowable margins for pressure vessels.3.5. Loads and stressesWind turbines are subjected to widely varying aerodynamicloads. These loads induce large bending moments that, in turn, cause tensile and compressive stresses paral lel to the axis of the tower (axial stresses). At the base of the tower, these stresses signi4cantly exceed the compres- sive stresses caused by the weight of the turbine. Frequent, Auctuating aerodynamic loads seen during normal operation make fatigue the critical mode of failure for modern turbine towers. Subjecting a tower to internal pressure causes a very different loading scenario. Because the pressure is uniform, it causes loadsin the axial direction and in the tangential direction (hoop stresses). The hoop stresses are twice the magnitude of the axial stresses which makes the hoop stress the limiting design constraint for many cylindrical pressure vessels. These fatigue stresses di@er drastically from those caused by the Auctuating aerodynamic loads in that the pres- sure stresses occur at a much lower frequency (on the order of a few per day rather than hundreds or thousands per day). As a result, the fatigue damage from the pressure stresses is expected to be negligible compared to the fatigue damage from the aerodynamicloads.Based on the considerations outlined above, the risk of HEE does not exclude the use of wind turbine towers for hydrogen storage. It is, however, diLcult to compare the use of a wind turbine tower as a pressure vessel to more tra- ditional hydrogen applications because, unlike conventional pressure vessels, they are subjected to signi4cant dynamic loads inherent in wind turbine structures. The dynamic struc- tural loads applied to a turbine tower would serve to repeat- edly open micro4ssures, one mechanism by which HEE is theorized to propagate. Due to the potential for catastrophic failure, HEE requires more research and experimentation.3.6. Crossover pressureAs the pressure rating of a hydrogen tower is increased, the primary mode of failure for the tower walls crosses over from fatigue to bursting. Once this “crossover” pressure is reached, the required wall thickness is determined by the maximum allowable hoop stress, rather than axial fatigue Fig.2shows required thickness as a function of pressure for both the fatigue and burst conditions. The solid set of lines describes thickness required at the base of the tower, and the dashed set of lines describes thickness required at the top of the tower. The crossover pressure for a given tower cross section is de4ned as the point where the line describing hoop stress requirements (the line with the steeper slope) overtakes the line describing fatigue requirements (the line which is almost horizontal). Below the crossover pressure, the required tower wall thickness is determined by the fatigue line. Above the crossover pressure, the required thickness is determined by the hoop stress line. Equations of these lines can be solved at an arbitrary tower crosssection to 4nd the crossover pressure. From the ASME Pressure Vessel Code储氢的风力涡轮机水塔发表于《国际期刊的氢能》(29期)(2004卷:1277至1288);瑞安,贾森撰实习时于美国梦露圣大学, 1235年,在美国加州圣克拉拉国家可再生能源实验室,2003年11月18日本文收稿为2003年12月15日。
水产常用英文
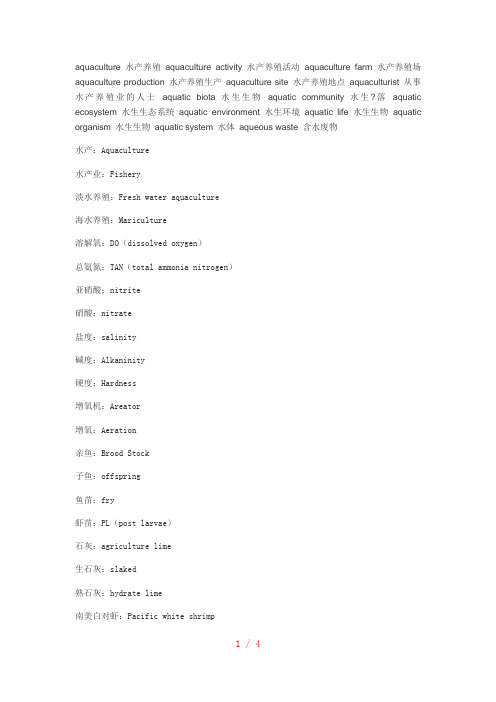
aquaculture 水产养殖aquaculture activity 水产养殖活动aquaculture farm 水产养殖场aquaculture production 水产养殖生产aquaculture site 水产养殖地点aquaculturist 从事水产养殖业的人士aquatic biota 水生生物aquatic community 水生?落aquatic ecosystem 水生生态系统aquatic environment 水生环境aquatic life 水生生物aquatic organism 水生生物aquatic system 水体aqueous waste 含水废物水产:Aquaculture水产业:Fishery淡水养殖:Fresh water aquaculture海水养殖:Mariculture溶解氧:DO(dissolved oxygen)总氨氮:TAN(total ammonia nitrogen)亚硝酸:nitrite硝酸:nitrate盐度:salinity碱度:Alkaninity硬度:Hardness增氧机:Areator增氧:Aeration亲鱼:Brood Stock子鱼:offspring鱼苗:fry虾苗:PL(post larvae)石灰:agriculture lime生石灰:slaked熟石灰:hydrate lime南美白对虾:Pacific white shrimp斑节对虾:tiger shrimp 拟穴青蟹:mud crab淡水小龙虾:cray fish 蛤:clam螺丝:snail牡蛎:oyster双壳类:bivalve腹足类:gastropod海星:sea star海胆:sea urchin海带:kelp鲈鱼:bass加州鲈:Large mouth bass 大菱鲆:founder石斑鱼:grouper鲍鱼:abalone鲤鱼:carp草鱼:grass carp青鱼:sapphire鳙鱼:bighead carp鲢鱼:chub鲶鱼:catfish罗非鱼:tilapia鲟鱼:sturgen淡水龟:tortoise海龟:turtle鳖:softshell turtle浮游生物:plankton浮游植物:phytoplankton浮游动物:zooplankton硅藻:diatom甲藻:Dinoflagellate轮虫:rotifer丰年虫:artemia桡足类:copepod枝角类:Cladoceran无节幼体:Nauplii细菌:bacterium弧菌:vibrosis真菌:fungi病毒:virus寄生虫:parasite食物转换率:FCR(feed conversion ratio)维生素:vitamin蛋白质:protein脂类:lipid食道:Esophagus胃:stomach肠:intestine肝:liver胆:Gallbladder胰:Pancreas肝胰腺:Hepatopancreas鳍:fin鳃:gill鳞:scale侧线:Lateral line鳔:Swim bladder生殖乳突:Genital papilla(注:专业文档是经验性极强的领域,无法思考和涵盖全面,素材和资料部分来自网络,供参考。
碳基储氢材料英语

Introduction:Hydrogen storage is a crucial technology for the development of clean energy systems, particularly in the context of hydrogen fuel cells and renewable energy storage. Among various hydrogen storage materials, carbon-based materials have emerged as a promising class due to their high hydrogen storage capacity, low cost, and ease of synthesis. This review aims to provide a comprehensive overview of carbon-based hydrogen storage materials, including their types, properties, challenges, and potential applications.1. Types of Carbon-Based Hydrogen Storage Materials1.1 Activated Carbon:Activated carbon is one of the most widely used carbon-based hydrogen storage materials. It has a high specific surface area, which canprovide a large number of active sites for hydrogen adsorption. The hydrogen storage capacity of activated carbon can reach up to 1.5 wt% at room temperature and 3 wt% at 77 K. However, the cycling stability and the rapid release of hydrogen are still challenges for practical applications.1.2 Carbon Nanotubes (CNTs):Carbon nanotubes (CNTs) are another class of carbon-based hydrogen storage materials. They have a unique structure with high surface area, excellent mechanical properties, and tunable hydrogen storage capacity. The hydrogen storage capacity of CNTs can reach up to 2 wt% at room temperature and 4 wt% at 77 K. However, the high cost of CNTs and the difficulty in mass production are obstacles for their application.1.3 Graphene:Graphene, a single layer of carbon atoms arranged in a hexagonal lattice, has attracted considerable attention as a hydrogen storage material. It possesses a large specific surface area, excellent electrical conductivity, and tunable hydrogen storage capacity. The hydrogenstorage capacity of graphene can reach up to 4 wt% at room temperatureand 6 wt% at 77 K. However, the practical application of graphene is hindered by its large-scale production and cost issues.1.4 Carbon Nanofibers (CNFs):Carbon nanofibers (CNFs) are another type of carbon-based hydrogen storage materials. They have a high specific surface area, goodelectrical conductivity, and tunable hydrogen storage capacity. The hydrogen storage capacity of CNFs can reach up to 2 wt% at room temperature and 3 wt% at 77 K. However, the difficulty in mass production and the high cost are challenges for their application.2. Properties of Carbon-Based Hydrogen Storage Materials2.1 Adsorption Energy:The adsorption energy is an important parameter for evaluating the hydrogen storage performance of carbon-based materials. It is defined as the energy required to adsorb one mole of hydrogen molecules onto the surface of the material. A higher adsorption energy indicates a stronger interaction between hydrogen molecules and the material, which is beneficial for hydrogen storage.2.2 Desorption Rate:The desorption rate is another critical parameter for hydrogen storage materials. It represents the rate at which hydrogen is released from the material under certain conditions. A high desorption rate is desirable for practical applications, as it ensures the rapid release of hydrogen for energy conversion or storage.2.3 Cycling Stability:Cycling stability refers to the ability of hydrogen storage materials to retain their hydrogen storage capacity after multiple adsorption-desorption cycles. A high cycling stability is essential for long-term and reliable hydrogen storage applications.3. Challenges and Solutions3.1 Low Hydrogen Storage Capacity:One of the main challenges for carbon-based hydrogen storage materials is their relatively low hydrogen storage capacity compared to other materials, such as metal hydrides. To improve the hydrogen storage capacity, researchers have focused on modifying the surface properties of carbon materials, such as introducing functional groups or constructing heteroatom-doped carbon materials.3.2 High Cost:The high cost of carbon-based hydrogen storage materials is another significant challenge. To reduce the cost, researchers have explored alternative synthesis methods, such as using low-cost carbon sources and developing scalable production processes.3.3 Low Cycling Stability:The low cycling stability of carbon-based hydrogen storage materials is a critical issue for practical applications. To enhance the cycling stability, researchers have investigated the use of composite materials, surface modification techniques, and the development of novel carbon materials with superior properties.4. Potential Applications4.1 Hydrogen Fuel Cells:Carbon-based hydrogen storage materials have great potential in hydrogen fuel cells, where they can be used as hydrogen storage systems. The high hydrogen storage capacity and rapid release of hydrogen make them suitable for this application.4.2 Renewable Energy Storage:Carbon-based hydrogen storage materials can be used to store hydrogen produced from renewable energy sources, such as wind and solar power. This can help to balance the intermittent nature of renewable energy and ensure a continuous supply of energy.4.3 Transportation:Hydrogen-powered vehicles can benefit from carbon-based hydrogen storage materials due to their high hydrogen storage capacity and low cost. These materials can be used to store hydrogen in vehicles, enablinglong-range transportation with minimal environmental impact. Conclusion:Carbon-based hydrogen storage materials have shown great promise as a clean energy technology. Their high hydrogen storage capacity, low cost, and ease of synthesis make them attractive candidates for various applications, including hydrogen fuel cells, renewable energy storage, and transportation. However, challenges such as low hydrogen storage capacity, high cost, and low cycling stability need to be addressed to fully realize the potential of these materials. Future research efforts should focus on improving the properties of carbon-based hydrogen storage materials and developing scalable production processes to make them more practical and cost-effective for wide-scale applications.。
关于海洋生态系统中的营养循环 英语作文
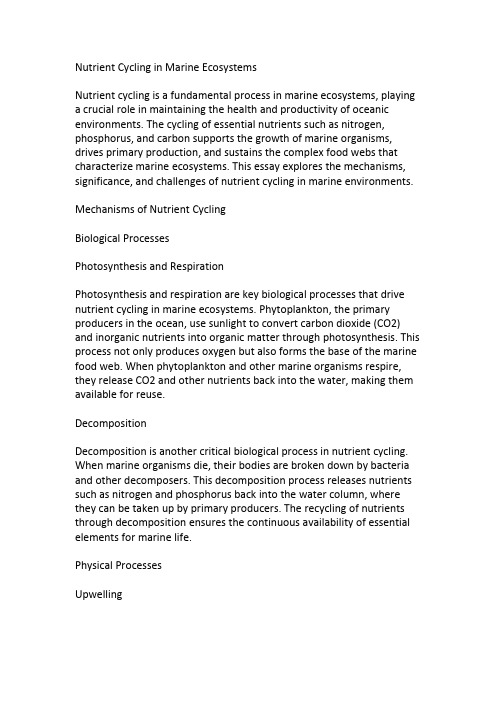
Nutrient Cycling in Marine EcosystemsNutrient cycling is a fundamental process in marine ecosystems,playing a crucial role in maintaining the health and productivity of oceanic environments.The cycling of essential nutrients such as nitrogen, phosphorus,and carbon supports the growth of marine organisms, drives primary production,and sustains the complex food webs that characterize marine ecosystems.This essay explores the mechanisms, significance,and challenges of nutrient cycling in marine environments.Mechanisms of Nutrient CyclingBiological ProcessesPhotosynthesis and RespirationPhotosynthesis and respiration are key biological processes that drive nutrient cycling in marine ecosystems.Phytoplankton,the primary producers in the ocean,use sunlight to convert carbon dioxide(CO2) and inorganic nutrients into organic matter through photosynthesis.This process not only produces oxygen but also forms the base of the marine food web.When phytoplankton and other marine organisms respire, they release CO2and other nutrients back into the water,making them available for reuse.DecompositionDecomposition is another critical biological process in nutrient cycling. When marine organisms die,their bodies are broken down by bacteria and other decomposers.This decomposition process releases nutrients such as nitrogen and phosphorus back into the water column,where they can be taken up by primary producers.The recycling of nutrients through decomposition ensures the continuous availability of essential elements for marine life.Physical ProcessesUpwellingUpwelling is a physical process that brings nutrient-rich deep water to the surface.This occurs when wind-driven currents push surface water away from the coast,allowing deeper water to rise and replace it. Upwelling zones are among the most productive areas in the ocean, supporting high levels of primary production and rich biodiversity.The influx of nutrients from upwelling fuels the growth of phytoplankton, which in turn supports higher trophic levels.Ocean CurrentsOcean currents play a significant role in the distribution and cycling of nutrients.These currents transport nutrients across vast distances, connecting different regions of the ocean.For example,the thermohaline circulation,also known as the global conveyor belt,moves nutrient-rich water from the deep ocean to the surface and from the poles to the equator.This circulation helps maintain nutrient balance and supports marine productivity on a global scale.Chemical ProcessesNitrogen FixationNitrogen fixation is a chemical process that converts atmospheric nitrogen(N2)into a form that can be used by marine organisms,such as ammonium(NH4+).This process is carried out by specialized bacteria and cyanobacteria,known as diazotrophs.Nitrogen fixation is essential for replenishing the nitrogen supply in marine ecosystems,as nitrogen is a critical nutrient for the growth of phytoplankton and other organisms.DenitrificationDenitrification is the process by which nitrate(NO3-)is converted back into nitrogen gas(N2),which is then released into the atmosphere.This process is carried out by anaerobic bacteria in low-oxygen environments, such as sediments and oxygen minimum zones.Denitrification helps regulate the nitrogen cycle by removing excess nitrogen from the ocean, preventing nutrient over-enrichment and maintaining ecological balance.Significance of Nutrient CyclingSupporting Primary ProductionNutrient cycling is essential for supporting primary production in marine ecosystems.The availability of nutrients such as nitrogen,phosphorus, and iron determines the growth and productivity of phytoplankton. These primary producers form the base of the marine food web, providing energy and nutrients for higher trophic levels,including zooplankton,fish,and marine mammals.Healthy nutrient cycling ensures a continuous supply of essential elements,sustaining the productivity and biodiversity of marine ecosystems.Maintaining Ecosystem BalanceNutrient cycling helps maintain the balance and stability of marine ecosystems.The recycling of nutrients through biological,physical,and chemical processes ensures that essential elements are available in the right amounts and forms for marine organisms.This balance prevents nutrient deficiencies and excesses,which can lead to ecological disruptions such as algal blooms,hypoxia,and loss of biodiversity. Effective nutrient cycling supports the resilience and health of marine ecosystems.Carbon SequestrationNutrient cycling plays a role in carbon sequestration,a process that removes CO2from the atmosphere and stores it in the ocean. Phytoplankton photosynthesis captures CO2,and a portion of the organic carbon produced is transported to the deep ocean through the biological pump.This sequestration of carbon in the deep ocean helps mitigate the impact of greenhouse gas emissions and contributes to climate regulation.Nutrient cycling is thus interconnected with the global carbon cycle and climate system.Challenges in Nutrient CyclingHuman ImpactsHuman activities have significantly altered nutrient cycling in marine ecosystems.Agricultural runoff,wastewater discharge,and industrial pollution introduce excessive nutrients,particularly nitrogen andphosphorus,into coastal waters.This nutrient over-enrichment,known as eutrophication,can lead to harmful algal blooms,hypoxia(low oxygen levels),and the degradation of marine habitats.Managing nutrient inputs and reducing pollution are critical for protecting nutrient cycling processes.Climate ChangeClimate change poses a major challenge to nutrient cycling in marine ecosystems.Rising sea temperatures,ocean acidification,and changes in ocean circulation patterns can disrupt the distribution and availability of nutrients.For example,warming waters can reduce the efficiency of upwelling,limiting the supply of nutrients to surface waters.Ocean acidification can affect the ability of certain organisms,such as shell-forming plankton,to utilize nutrients effectively.Understanding and mitigating the impacts of climate change on nutrient cycling is essential for sustaining marine ecosystems.OverfishingOverfishing can disrupt nutrient cycling by altering the structure and function of marine food webs.The removal of key species,such as top predators and herbivores,can have cascading effects on nutrient dynamics.For example,the decline of large predatory fish can lead to an increase in smaller fish and invertebrates,which may alter nutrient recycling rates and patterns.Sustainable fishing practices are necessary to maintain the integrity of nutrient cycling processes.ConclusionNutrient cycling is a vital process that sustains the health and productivity of marine ecosystems.Through biological,physical,and chemical mechanisms,essential nutrients are recycled and made available to marine organisms,supporting primary production, ecosystem balance,and carbon sequestration.However,human impacts, climate change,and overfishing pose significant challenges to nutrient cycling.Addressing these challenges requires effective management and conservation strategies to protect nutrient cycling processes and ensure the resilience and sustainability of marine ecosystems.By understandingand valuing the importance of nutrient cycling,we can work towards a healthier and more productive ocean.。
壳聚糖改性污泥水热炭活化过硫酸盐降解活性黑5_染料废水

DOI:10.7524/j.issn.0254-6108.2022092702于露滢, 陈红, 于鑫, 等. 壳聚糖改性污泥水热炭活化过硫酸盐降解活性黑5染料废水[J]. 环境化学, 2024, 43(4): 1211-1221.YU Luying, CHEN Hong, YU Xin, et al. Chitosan modified sludge hydrochar activated peroxydisulfate to degradate activated black 5 dyeing wastewater[J]. Environmental Chemistry, 2024, 43 (4): 1211-1221.壳聚糖改性污泥水热炭活化过硫酸盐降解活性黑5染料废水 *于露滢1 陈 红1,2 ** 于 鑫1 王 凯1 曾可佳1 叶沁辉1 郑凯远1(1. 东华大学环境科学与工程学院,上海,201600;2. 全国循环经济工程实验室,上海,210620)NO−3PO3−4HCO−3摘 要 印染废水可生化性低,生物处理难度大. 通过在剩余污泥中掺杂壳聚糖,经水热处理制备出壳聚糖改性生物炭(CBC),并用于活化过二硫酸盐(PDS),实现对活性黑5(RB5)染料废水的高效降解. 在水热温度为200 ℃,水热时间为6 h时制备的CBC对RB5的去除效果最优,反应60 min去除率可达到100 %. 此外,PDS投量为2 mmol·L−1,CBC投量为5 g·L−1,初始pH=5时反应效果最佳. 反应系统中的Cl−和对RB5去除几乎无影响,而、有明显抑制作用. 机理研究证实了单线态氧(1O2)对RB5的降解起主要贡献,而不是PDS氧化体系常见的硫酸根自由基.关键词 高级氧化,水热炭,染料废水,单线态氧.Chitosan modified sludge hydrochar activated peroxydisulfate to degradate activated black 5 dyeing wastewaterYU Luying1 CHEN Hong1,2 ** YU Xin1 WANG Kai1 ZENG Kejia1 YE Qinhui1 ZHENG Kaiyuan1(1. College of Environmental Science and Engineering, Donghua University, Shanghai, 201600, China;2. National Engineering Laboratory of Circular Economy, Shanghai, 210620, China)NO−3PO3−4HCO−3Abstract Printing and dyeing wastewater is difficult to treat biologically due to property of low biodegradability. By doping chitosan in the wasted sludge, modified biochar (CBC) was prepared by hydrothermal treatment and was used to activate peroxydisulfate (PDS) to achieve efficient degradation of activated black 5 (RB5) dyeing wastewater. The CBC prepared under the condition of hydrothermal temperature of 200 °C and hydrothermal time 6 h showed the best RB5 removal effect, achieving a removal rate of 100 % at 60 min. In addition, the best performance was obtained with a PDS dosage of 2 mmol·L−1, a CBC dosage of 5 g·L−1 and an initial pH of 5. The Cl− and in the reaction system had almost no effect on RB5 removal, while the and exhibited a significant inhibitory impact. The mechanism study confirmed that the singlet oxygen (1O2) played a major contribution to the degradation of RB5 rather than sulfate radical, which is common in PDS oxidation systems.Keywords advanced oxidation,hydrochar,dye wastewater,singlet oxygen.偶氮染料是印染工业中最常用且应用范围最广的一类染料,是印染废水的主要组成部分[1]. 染料2022 年 9 月 27 日 收稿(Received:September 27,2022).* 国家自然科学基金(52070040,51878136)资助.Supported by the National Natural Science Foundation of China (52070040 ,51878136).1212环 境 化 学43 卷废水具有色度高、毒性大、可生化性差等特点,如果处理不当排放到环境中,将会对周围生态环境和人体造成严重危害[2]. 目前常用的处理方法包括生物法[3]、膜分离法[4]、吸附法[5]、高级氧化法[6]等. 膜分离法虽分离效果好、出水水质高但存在膜材料的成本高,容易被污染等问题;吸附法所用的吸附剂容易达到饱和且再生费用较高,限制了该方法在染料废水中的应用;此外,采用生物法处理前期投资大,处理周期长. 高级氧化(AOPs)工艺作为一种功能强大且具有良好的发展前景的技术,因其应用广泛、反应速度快、氧化能力强等优点备受关注[7]. 由于硫酸盐自由基具有强的氧化性,以及更广泛的pH适用性[8 − 9],近年来基于过硫酸盐(PS)的AOPs技术受到关注.由于PS的稳定性,在不添加活化剂的情况下,PS很难与有机物发生反应. 目前对PS催化活化的手段包括紫外光活化[10]、过渡金属活化[11]以及碳材料活化[12]等. 紫外活化在实际应用中对污染物的去除率较低,过渡金属活化会引入金属离子,容易产生二次污染,因此碳材料催化活化技术开始受到广泛关注. 目前已经证实了包括氧化还原石墨烯、碳纳米管、纳米金刚石和生物炭等碳材料,可以用作过二硫酸盐(PDS)和过一硫酸盐(PMS)活化的催化剂,以增强污染物的降解[13 − 14]. 相比于碳纳米管、纳米金刚石等催化剂造价昂贵,以生物废弃物为原料制备的生物炭具有成本低,制作简单和良好的活化性能等优点,其催化应用潜力近年来备受关注[14].研究已证实,以剩余活性污泥[15]、竹子[16]等废弃生物质制成的生物炭,具有良好的活化PDS的效果. 生物炭的制备主要采用热处理法,包括热解法和水热法,其中热解法需要对原料进行干化预处理,且热解温度高,材料制备能耗大[17],而原料无需干化的水热处理具有反应温度低、能耗低的特点,成为低成本制备生物炭的更优选择,此外,为提高生物炭的催化效能,常对生物炭进行改性处理,如杂原子掺杂[18]、表面含氧官能化[19]、单原子掺杂[20]等. 生物炭表面的含氧官能团决定了生物炭催化剂的性质,如羧基决定了生物炭的表面电荷[21],酚基决定了生物炭表面的氧化还原性质[22]. 其中简单的酸碱改性可实现生物炭表面含氧官能化,使表面含氧官能团发生改变,从而实现生物炭催化活化效能的提升[23].除了使用化学性碱如NaOH进行改性,壳聚糖作为目前自然界中唯一发现的带正电荷的天然碱性多糖[24],具有良好的降解性、生物相容性和生物药理学活性[25],因此可作为生物炭改性的碱性物质.本研究以剩余活性污泥经水热法制备生物炭,经氢氧化钠(NaOH)碱改性、壳聚糖改性及联合改性后活化PDS,基于对RB5染料废水的降解效能确定最优改性方法. 考察水热处理条件、改性剂投加量、生物炭活化PDS反应条件、系统中的阴离子等对污染物降解效能的影响,并通过自由基淬灭和电子顺磁共振波谱仪(EPR)自由基捕获,探究参与污染物降解的主要活性物质,以确定反应机理.1 材料与方法(Materials and methods)1.1 实验材料(1)未改性生物炭的制备将从上海市某污水处理厂二沉池取回的污泥进行重力沉降,浓缩后在105 ℃下干燥4 h,用粉碎机破碎后过100目聚乙烯筛,将干燥污泥按照1.8 g挥发性悬浮固体(VSS)的量加入60 mL去离子水中,混合均匀后转移至密闭的水热反应釜内,在温度为220 ℃的条件下加热4 h. 将水热后的产物进行固液分离,固相物质即为制备所得的水热炭,命名为BC.(2)经NaOH碱改性生物炭的制备对于采用碱改性的生物炭,将从上海市某污水处理厂二沉池取回的污泥进行重力沉降,浓缩后在105 ℃下干燥4 h,用粉碎机破碎后过100目聚乙烯筛,将干燥污泥按照1.8 g VSS的量加入60 mL去离子水中,使用NaOH和H2SO4调节体系的pH至11,混合均匀后转移至密闭的水热反应釜内,在温度为220 ℃的条件下加热4 h,将水热后的产物进行固液分离,并将固体物质干燥后命名为BC-pH=11.水热反应前添加0.18 g壳聚糖,并用NaOH和H2SO4调节体系pH至11,相同水热条件下制备的生物炭命名为10CBC-pH=11.(3)壳聚糖改性生物炭的制备破碎后过100目聚乙烯筛,将干燥污泥按照1.8 g VSS 的量加入60 mL 去离子水中,将0.018 、0.072、0.144、0.18 g 的壳聚糖添加至1.8 g VSS 的干燥污泥中(壳聚糖质量占污泥VSS 质量的1%、4%、8%和10%),混合均匀后置于密闭的水热反应釜中,并在温度为220 ℃的条件下加热4 h. 将水热后的产物进行固液分离,固相物质即为制备所得的水热炭,分别命名为1CBC 、4 CBC 、8CBC 、10CBC.(4)实验试剂L-组氨酸(C 6H 9N 3O 2)和PDS (Na 2S 2O 8)购于阿拉丁试剂有限公司;重水(D 2O )、壳聚糖((C 6H 11NO 4)n ,脱乙酰度=80.0%—95.0%)、氯化钾(KCl )、磷酸二氢钾(KH 2PO 4)、硝酸钾(KNO 3)、氯仿(CHCl 3)购于国药化学试剂有限公司;5-二甲基-1-吡咯啉-N-氧化物(DMPO )、2,2,6,6-四甲基-4-哌啶酮(TEMP )、甲醇(CH 3OH )、叔丁醇(C 4H 10O )、碳酸氢钠(NaHCO 3)购于上海易恩化学技术有限公司;RB5购于Sigma-Aldrich 公司.1.2 实验方法1.2.1 各类生物炭对RB5染料废水的去除实验(1)对RB5染料废水的吸附去除实验取100 mL 浓度为40 mg·L −1的RB5溶液,向溶液中加入5 g·L −1的生物炭(BC ,BC-pH=11,10CBC ,10CBC-pH=11),置于恒温摇床(LYGZ-2102C , 金坛良友仪器(常州))内以160 r·min −1转速在((25±1)℃)下振荡. 在设定时间取样,样品经0.45 μm 滤膜过滤后采用紫外可见分光光度计(TU-1810,普析通用有限责任公司(北京))在597 nm 的波长下测定RB5浓度. 每次实验均进行3组平行实验,将所得结果的平均值进行数据分析.(2)改性和未改性生物炭活化PDS 对RB5染料废水的去除实验取100 mL 浓度为40 mg·L −1的RB5溶液. 向溶液中加入5 g·L −1的生物炭(BC 、BC-pH=11、10CBC 、10CBC-pH=11)和1 mmol·L −1的PDS ,置于恒温摇床内以160 r·min −1转速在((25±1)℃)下振荡. 在设定时间取样,样品经0.45 μm 滤膜过滤后采用紫外可见分光光度计在597 nm 的波长下测定RB5浓度. 每次实验均进行3组平行实验,将所得结果的平均值进行数据分析.(3)壳聚糖改性生物炭活化PDS 降解RB5染料废水的影响因素研究在探究不同壳聚糖添加量所制备的生物炭对活化PDS 降解RB5废水的实验中,取100 mL 浓度为40 mg·L −1的RB5溶液. 向溶液中加入5 g·L −1的生物炭(BC 、1CBC 、4CBC 、8CBC 、10CBC )和1 mmol·L −1的PDS ,置于恒温摇床内以160 r·min −1转速在((25±1)℃)下振荡. 在设定时间取样,样品经0.45 μm 滤膜过滤后采用紫外可见分光光度计在597 nm 的波长下测定RB5浓度. 每次实验均进行3组平行实验,将所得结果的平均值进行数据分析.在最佳壳聚糖添加量制备的生物炭(1CBC )基础上,探究1CBC 的制备条件(水热时间和水热温度)及活化PDS 的反应条件(PDS 的投量,1CBC 的投量,初始RB5的浓度,初始pH ,不同阴离子)的影响,采用控制变量法,除研究变量外,其它变量均保持不变,以选取最佳条件. 每次实验均进行3组平行实验,将所得结果的平均值进行数据分析.本实验反应速率采用伪一级动力学公式进行拟合. 通过得到不同反应条件下的ln (C 0/C t )与t 之间的关系,即可得到其反应速率.d C d t =−kC (1)ln (C t C 0)=−kC (2)式中,k 为反应速率常数,min −1;C t 为反应t 时刻对应的污染物浓度,mg·L −1;C 0为反应初始时刻污染物的浓度,mg·L −1.1.2.2 自由基淬灭实验将5 g·L −11CBC 和2 mmol·L −1PDS 置于100 mL 锥形瓶中,分别加入40 mg·L −1 RB5和50 mmol·L −14 期于露滢等:壳聚糖改性污泥水热炭活化过硫酸盐降解活性黑5染料废水1213膜过滤后采用紫外可见分光光度计在597 nm的波长下测定剩余RB5的浓度. 每次实验均进行3组平行实验,将所得结果的平均值进行数据分析.1.2.3 EPR自由基捕获实验SO−4O−2使用EPR(EMXnano Bench Top,德国布鲁克)检测反应体系的活性物质. DMPO用于捕获·OH和·;TEMP用于捕获1O2,·使用DMPO在纯甲醇体系中捕获. 在反应速率最快的时刻进行取样,经0.22 μm的膜过滤后,取2滴待测溶液,加入20 μL对应捕获剂(DMPO或TEMP),然后将溶液置于毛细管中进行EPR自由基检测分析.在D2O中捕获1O2时,使用TEMP在纯D2O体系中进行. 在反应速率最快的时刻取样,经0.22 μm 的膜过滤后,取2滴待测溶液并加入20 μL的TEMP,然后将溶液置于毛细管中进行EPR自由基检测分析.1.2.4 金属浸出实验浸出液中金属浓度的测定:将5 g·L−1的生物炭和2 mmol·L−1的PDS加入100 mL的去离子水中,置于恒温摇床内以160 r·min−1转速在((25±1)℃)下振荡. 分别在30、60、120、180 min取样,样品经0.45 μm滤膜过滤后采用原子发射光谱仪(Prodigy-ICP,美国)进行Fe、Cu、Al、Mn、Cr、As、Cd、Zn、Hg、Pb金属浓度的检测.浸出液活化PDS降解RB5实验:将5 g·L−1的生物炭加入100 mL的去离子水中,置于恒温摇床内以160 r·min−1转速在((25±1)℃)下震荡3 h后得到浸出液. 然后将浸出液过滤后加入40 mg·L−1的RB5和2 mmol·L−1的PDS进行反应,在设定时间取样,样品经0.45 μm滤膜过滤后采用紫外可见分光光度计在597 nm的波长下测定RB5浓度. 每次实验均进行3组平行实验,将所得结果的平均值进行数据分析.2 结果与讨论(Results and discussion)2.1 生物炭改性方式对PDS活化效果的影响研究污泥基生物炭经不同改性方式后,单独生物炭以及生物炭活化PDS系统对RB5的去除效果.生物炭本身对RB5的吸附效果如图1(a)所示,发现未进行改性的生物炭(BC)和只进行碱改性的生物炭(BC-pH=11)对RB5的吸附效果甚微,但经过壳聚糖改性后的生物炭(10CBC, 10 CBC-pH=11),表现出一定的吸附效果,RB5的去除效率在4 %—18 %,去除效果有限. 可知,污泥基生物炭及改性生物炭均难以通过吸附方式对RB5进行有效去除. 此外,在仅投加PDS时,RB5亦不能被氧化去除.图 1 RB5的吸附实验(a)和各类生物炭活化PDS降解RB5实验(b)([RB5]=40 mg·L−1;[PDS]=1 mmol·L−1 ;[ 生物炭 ]=5 g·L−1 )Fig.1 RB5 adsorption experiment (a) and RB5 degradation experiment by PDS activated by various biochar(b)([RB5]=40 mg·L−1;[PDS]=1 mmol·L−1;[biochar]=5 g·L−1)当生物炭投加PDS后,从图1(b)中可知,RB5的降解显著提升,说明生物炭可有效活化PDS降解RB5. 虽然经不同方式改性后的生物炭均在180 min达到了对RB5的完全降解,但降解速率有显著差1214环 境 化 学43 卷4 期于露滢等:壳聚糖改性污泥水热炭活化过硫酸盐降解活性黑5染料废水1215有效的活化PDS,且壳聚糖改性比碱改性有更好的活化效果,此外,碱和壳聚糖同时改性对于生物炭活化PDS无协同作用,甚至比单独壳聚糖改性的生物炭效果略差. 壳聚糖的良好改性效果可能得益于其表面丰富的官能团,有研究利用壳聚糖掺杂的生物炭微球催化剂实现对阿莫西林的有效降解[26]. 因此,本研究确定以壳聚糖改性的方式制备污泥基生物炭CBC,并进行条件优化.2.2 壳聚糖掺杂比例对RB5降解的影响壳聚糖改性生物炭制备时,壳聚糖的添加量决定着催化剂所能提供的活性位点数量. 图2(a)表明了壳聚糖在污泥中不同掺杂比例条件下制备的生物炭,对RB5降解的影响,图2(b)进一步表明了对RB5降解反应速率的影响. 在壳聚糖的掺杂比例从1%(1CBC)增加至10%(10CBC)的过程中,RB5的降解速率先加快后减慢,在投加量为4%时降解速率最快(降解速率为0.0677 min−1),在此基础上增加壳聚糖的投量,反应速率反而降低,在投加量为10%(10CBC)时,降解速率降低至0.0491 min−1. 造成该现象的原因可能是:过量的壳聚糖负载在生物炭上会堵塞相关的活性位点,导致降解速率有一定程度下降. 除此之外,壳聚糖的加入使反应时间从180 min缩短至60 min. 根据上述分析并考虑到经济适用性,本文选取1%(1CBC)作为最佳掺杂量进行后续的研究.图 2 壳聚糖掺杂比例对RB5降解效果的影响(a)及RB5降解速率的变化(b)([RB5]=40 mg·L−1;[PDS]=1 mmol·L−1 ;[ 生物炭 ]=5 g·L−1 )Fig.2 Effect of chitosan doping ratio on the degradation of RB5 (a) and the change of RB5 degradation rate (b)([RB5]=40 mg·L−1;[PDS]=1 mmol·L−1;[biochar]=5 g·L−1)2.3 水热炭制备条件对RB5降解的影响研究表明,水热条件对于生物炭的制备以及催化性能有显著的影响[27]. 因此,本研究探讨不同的水热温度和水热时间制备出的生物炭,对活化PDS降解RB5的影响,结果见图3.图 3 水热时间(a)和水热温度(b)对RB5降解的影响([RB5]=40 mg·L−1;[PDS]=1 mmol·L−1;[生物炭]=5 g·L−1)Fig.3 Effect of hydrothermal time (a) and hydrothermal temperature (b) on the degradation of RB5([RB5]=40 mg·L−1;[PDS]=1 mmol·L−1;[biochar]=5 g·L−1)图3(a)展示了水热时间对RB5降解的影响. 在水热时间为2 h和4 h ,反应温度为220 ℃时,体系1216环 境 化 学43 卷未完全碳化,导致没有显著的降解差异. 但随着水热时间的延长,反应体系对RB5的降解速率有了明显的改善,并在水热时间为8 h时达到最优,降解速率为0.084 min−1,且反应时间从120 min缩短至60 min.此外,在水热时间为6 h时,亦能在60 min实现RB5的完全去除,因此,确定最优反应时间为6 h.图3(b)显示了水热温度对RB5的降解影响. 设置水热反应时间为6 h,水热温度从180 ℃增至240 ℃时,体系对RB5的降解速率呈先增加后减小的趋势. 在反应时间为60 min时,180 ℃、200 ℃、220 ℃、240 ℃条件下制备的1CBC活化PDS,对RB5的去除率分别为86%、97%、100%和92%. 综合RB5降解效果与经济因素,本研究选取最佳水热温度为200 ℃,水热时间为6 h,采用此条件制备的1CBC进行后续研究.2.4 催化体系反应条件对RB5降解的影响2.4.1 催化剂和PDS投量对RB5降解的影响除生物炭的制备条件会对RB5的去除产生影响外,反应条件亦直接影响污染物的去除表现. PDS投量对RB5降解的影响如图4(a)所示,RB5的降解速率随PDS投量的增加(由0.5 mmol·L−1增至4.0 mmol·L−1)逐渐提高,降解速率由0.0313 min−1增至0.0706 min−1,可能由于PDS投量的增加使体系产生了更多的活性物质,从而加快反应速率,由于PDS投量为2 mmol·L−1和4 mmol·L−1时,均表现出RB5的快速高效去除,因此确定PDS的最优投量为2 mmol·L−1.图 4 PDS投量(a)生物炭的投量(b)对RB5降解的影响Fig.4 Effect of PDS dosage (a) and biochar dosage (b) on the degradation of RB5同样,催化剂1CBC的投量影响RB5的降解效果(图4(b)),随着1CBC投量从1.0 g·L−1增加至10.0 g·L−1,体系中催化活化PDS的活性位点增多,引起RB5的降解速率由0.0093 min−1逐步增加至0.0487 min−1. 由于1CBC投量为5.0 g·L−1和10.0 g·L−1时,反应均在120 min完成,因此选择生物炭的最佳投量为5.0 g·L−1.2.4.2 初始pH及污染物浓度对RB5降解的影响溶液pH变化会对体系中PDS的存在状态及材料的表面电荷产生影响[28],进而影响污染物去除表现. 图5展示了初始pH及反应中pH的变化对RB5降解的影响. 图5(a)为不同初始pH对RB5降解的影响,可知,在不同初始pH下,1CBC在180 min时对RB5的吸附效果相同,均为10%. 在1CBC/PDS 体系,RB5的降解效果显著提升,其中在初始pH=5时去除效率最高,为0.0113 min−1;随着初始pH的升高,反应速率逐渐降低. 当pH=9时,在120 min时RB5的去除率仅为49%,1CBC活化PDS的能力下降. 酸性条件利于RB5的降解,可能是由于壳聚糖具有去质子化的胺基,在酸性条件下与带负电荷的RB5染料之间强烈的静电相互作用导致;而在碱性条件下,静电相互作用受抑制,导致降解速率下降[29].为了进一步探究不同初始pH对BR5降解效果差异的原因,测定了反应过程中pH的变化(图5(b)).在1CBC吸附实验中,不同初始pH条件下,反应180 min后,pH均接近6—7,趋于中性. 这可能是由于生物炭成分复杂,具有一定的缓冲能力导致. 然而,在1CBC/PDS系统中,无论初始pH呈酸性还是碱性,体系在180 min时的pH均呈酸性. 可能原因如式(3)、式(4)和式(5)所示[30 − 31],在初始pH=5时,导致H +的产生,使反应过程中的pH 不断下降.图 5 初始pH 对RB5降解的影响(a ),反应过程中pH 的变化(b ),1CBC/PDS 反应过程中浸出的金属浓度(c )和浸出液对RB5降解的影响(d )Fig.5 Effect of initial pH on the degradation of RB5 (a ), the change of pH during the reaction (b ), leaching concentration of metal during 1CBC/PDS reaction (c ) and effect of leaching solution on RB5 degradation (d )S 2O 2−8+H +→HS 2O −8(3)HS 2O −8→SO 2−4+SO −.4+H+(4)S 2O 2−8+H 2O →SO 2−5+SO 2−4+2H +(5)此外,由于污泥中可能含有多种金属,目前许多金属已经证实具有活化PS 的效果[32]. 因此本研究为进一步探究污泥生物炭在反应中释放出的金属离子是否具有催化作用,在初始pH=5时,测定了1CBC/PDS 体系中多种金属(Fe 、Cu 、Al 、Mn 、Cr 、As 、Cd 、Zn 、Hg 、Pb )的浸出浓度,由于Cu 、Cr 、As 、Cd 、Hg 、Pb 的浓度低于检出限,图5(c )中只显示了浓度高于检出限的Fe 、Al 、Mn 、Zn 的浸出浓度,图5(d )为浸出液活化PDS 降解RB5的去除效果. 在图5(c )中金属浓度随着反应时间的延长不断增加,其中在180 min 时Al 、Mn 、Zn 浓度均在5 mg·L −1以下,而Fe 的浓度已达到了20 mg·L −1左右. 为进一步验证反应过程中浸出的金属是否会对RB5的降解产生影响,将1CBC 在去离子水中浸出180 min 后,在浸出液中加入2 mmol·L −1的PDS 对RB5进行降解,结果如图5(d )所示. 尽管浸出液中有较高的金属含量,但是浸出液中的金属离子未表现出PDS 的活化及对RB5的降解.在1CBC/PDS 反应系统中,不同初始RB5浓度下,污染物的浓度随反应时间的变化如图6所示.在反应时间为30 min 时,RB5初始浓度为40 mg·L −1、80 mg·L −1、160 mg·L −1和240 mg·L −1的情况下,降解效率分别为100%、100%、84%和70%;图6(b )表明了不同初始浓度下的RB5对反应速率的影响,发现随着RB5浓度的增加,体系的降解速率有所降低,但是在60 min 的反应时间内,不同浓度的RB5染料废水均能完全降解,说明1CBC/PDS 体系受到RB5浓度的影响较小,进一步体现该体系在处理高浓度RB5废水中的优势.4 期于露滢等:壳聚糖改性污泥水热炭活化过硫酸盐降解活性黑5染料废水1217图 6 初始RB5浓度对反应的影响(a )和体系中降解速率的变化(b )Fig.6 Effect of initial RB5 concentration on the reaction (a ) and the change of degradation rate in the system (b )2.4.3 不同阴离子对RB5降解的影响PO 3−4NO −3HCO −3NO −3PO 3−4HCO −3PO 3−4HCO −3CO −3HCO −3印染废水是一个复杂的水体,通常含有各种阴离子,这些离子的存在可能会对PDS 体系造成一定的影响[33]. 本研究探究了Cl -、、和对1CBC/PDS 体系降解RB5的影响. 结果如图7所示,20 mmol·L −1 的Cl − 和对RB5的降解速率几乎没有影响. 甚至还有研究表明在以过一硫酸盐(PMS )为氧化剂的AOPs 系统中,适量的Cl −可以与PMS 反应生成HClO 和Cl 2,进一步增强体系的氧化强度[34]. 然而,和对体系产生明显的抑制作用,结合2.4.2中pH 对反应的影响,可能是因为属于碱性阴离子,导致溶液的pH 升高,因此产生污染物降解抑制的现象[35]. 此外,有研究表明可以促进PMS 的分解,并且可以与·OH 和SO 4−·反应生成氧化能力较弱的HCO 3·和·自由基[36],在本体系中可能是由于消耗了体系中的PDS 导致抑制效果达到90%.图 7 阴离子对RB5去除效果的影响(离子浓度为20 mmol·L −1)Fig.7 Effect of anion on the removal of RB5 (ion concentration=20 mmol·L −1)2.5 反应机理探究基于硫酸根自由基的AOPs 技术,污染物的降解途径主要包括自由基途径和非自由基途径. 在自由基反应途径中起主要作用的是·OH 、SO 4−·、O 2−·等自由基,而非自由基途径起主导作用的是1O 2、电子转移和表面活性氧物种[37].SO −4O −2SO −4为确定参与RB5降解的活性物种,本研究对1CBC/PDS 体系进行自由基淬灭和EPR 自由基捕获,如图8所示. 使用4种常见的自由基淬灭剂,其中,甲醇通常用于·OH 和·的淬灭,叔丁醇通常用于淬灭·OH ;氯仿和L-组氨酸是·和1O 2的有效淬灭剂. 结果发现,甲醇和叔丁醇对反应速率有抑制作用,且降解速率与对照组相比分别降低了33.0%和54.7%,但最终仍可实现RB5的全部去除. 氯仿对反应体系几乎没有抑制作用,而L-组氨酸的加入对体系产生强烈的抑制作用,使降解速率由0.048 min −1降至0.0003 min −1. 从自由基淬灭的实验结果推测,反应中的活性物种可能是·OH 、·和1O 2.为进一步验证参与反应的活性物种,以 DMPO 和 TEMP 作为自旋捕获剂,采用EPR 进行活性物质捕获,通过测定反应体系中未成对电子的顺磁性来鉴定自由基的存在[38].1218环 境 化 学43 卷图 8 不同淬灭剂对反应体系降解RB5的影响(淬灭剂为50 mmol·L −1)Fig.8 Effect of different quenching agents on the degradation of RB5 in the reaction system (quenchers=50 mmol·L −1)SO −4SO −4SO −4SO −4SO −4SO −4图9(a )为1CBC/PDS 体系及其对照组的·OH 和·的自由基捕获图谱,在1CBC 系统中无明显的·OH 和·的自由基信号;单独PDS 体系中检测到了显著的·信号,而·OH 信号不明显. 在1CBC/PDS 体系,信号较杂乱,无明显的·OH 和·自由基信号. 实验结果表明,单独PDS 可以通过自身分解产生·自由基,但在1CBC/PDS 系统中,尽管有高效的RB5降解效能,但降解效果不是由·OH 和·引起.据文献报道,D 2O 可以大大延长1O 2的寿命[39],即体系中如果产生1O 2,在D 2O 中将检测到更强的信号. 图9(b )为1CBC/PDS 体系及其对照组的1O 2捕获图谱. 在单独的1CBC 系统和单独PDS 系统中无1O 2信号, 1CBC/PDS 中检测到微弱的1O 2信号. 为近一步确认1O 2的存在,用D 2O 替换H 2O 再次检测,如图9(b )所示,在D 2O 中检测到了高强度的1O 2信号,结合自由基淬灭实验,进一步确认1O 2为1CBC/PDS 体系的活性物种,即1CBC/PDS 体系是以为1O 2为主的非自由基氧化体系,RB5的降解主要通过1O 2氧化实现.图 9 1CBC/PDS 体系的EPR 谱图Fig.9 EPR spectrum of the 1CBC/PDS system3 结论(Conclusion)以剩余污泥为原料,通过水热反应制备生物炭,并采用不同的改性方式优化水热炭活化PDS 降解RB5染料废水的降解效能,得到以下主要结论.(1)相比于采用NaOH 改性,使用壳聚糖改性后的污泥水热炭对活化PDS 降解RB5染料废水具有更快的降解速率.(2)确定了1CBC/PDS 体系中水热炭制备的最佳水热温度为200 ℃,最佳水热时间为6 h ;最佳4 期于露滢等:壳聚糖改性污泥水热炭活化过硫酸盐降解活性黑5染料废水1219NO−3HCO−3PO3−4(3)反应体系中,Cl−和对RB5的去除效率影响很小;而和对RB5的去除产生显著的抑制作用.(4)自由基淬灭实验和EPR自由基捕获实验结果证明了1O2是1CBC/PDS体系降解RB5起主要贡献的活性物种.参考文献(References)PARMAR N D, SHUKLA S R. Decolourization of dye wastewater by microbial methods- A review [J]. Indian Journal of Chemical Technology, 2018, 25(4): 315-323.[ 1 ]ZENG Q Q, LIU Y, SHEN L G, et al. Facile preparation of recyclable magnetic Ni@filter paper composite materials for efficient photocatalytic degradation of methyl orange [J]. Journal of Colloid and Interface Science, 2021, 582(Pt A): 291-300.[ 2 ]BERKESSA Y W, YAN B H, LI T F, et al. Treatment of anthraquinone dye textile wastewater using anaerobic dynamic membrane bioreactor: Performance and microbial dynamics [J]. Chemosphere, 2020, 238: 124539.[ 3 ]AĞTAŞ M, YıLMAZ Ö, DILAVER M, et al. Hot water recovery and reuse in textile sector with pilot scale ceramic ultrafiltration/ nanofiltration membrane system [J]. Journal of Cleaner Production, 2020, 256: 120359.[ 4 ]袁思杰, 张芮铭. 染料废水处理技术研究进展[J]. 染料与染色, 2022, 59(4): 55-62.YUAN S J, ZHANG R M. Research progress of dye wastewater treatment technology[J]. Dyestuffs and Coloration, 2022, 59(4): 55-62(in Chinese).[ 5 ]dos SANTOS A J, BRILLAS E, CABOT P L, et al. Simultaneous persulfate activation by electrogenerated H2O2 and anodic oxidation at a boron-doped diamond anode for the treatment of dye solutions [J]. Science of the Total Environment, 2020, 747: 141541.[ 6 ]LUTZE H V, BIRCHER S, RAPP I, et al. Degradation of chlorotriazine pesticides by sulfate radicals and the influence of organic matter [J]. Environmental Science & Technology, 2015, 49(3): 1673-1680.[ 7 ]GIANNAKIS S, LIN K Y A, GHANBARI F. A review of the recent advances on the treatment of industrial wastewaters by Sulfate Radical-based Advanced Oxidation Processes (SR-AOPs) [J]. Chemical Engineering Journal, 2021, 406: 127083.[ 8 ]谷得明, 郭昌胜, 冯启言, 等. 基于硫酸根自由基的高级氧化技术及其在环境治理中的应用[J]. 环境化学, 2018, 37(11): 2489-2508.GU D M, GUO C S, FENG Q Y, et al. Sulfate radical-based advanced oxidation processes and its application in environmental remediation [J]. Environmental Chemistry, 2018, 37(11): 2489-2508 (in Chinese).[ 9 ]IKE I A, LINDEN K G, ORBELL6 J D, et al. Critical review of the science and sustainability of persulphate advanced oxidation processes [J]. Chemical Engineering Journal, 2018, 338: 651-669.[10]MIAO J, ZHU Y, LANG J Y, et al. Spin-state-dependent peroxymonosulfate activation of single-atom M-N moieties via a radical-free pathway [J]. ACS Catalysis, 2021, 11(15): 9569-9577.[11]TANG L, LIU Y N, WANG J J, et al. Enhanced activation process of persulfate by mesoporous carbon for degradation of aqueous organic pollutants: Electron transfer mechanism [J]. Applied Catalysis B: Environmental, 2018, 231: 1-10.[12]CHEN X, OH W D, LIM T T. Graphene- and CNTs-based carbocatalysts in persulfates activation: Material design and catalytic mechanisms [J]. Chemical Engineering Journal, 2018, 354: 941-976.[13]WANG J, WANG S. Preparation, modification and environmental application of biochar: A review [J]. Journal of Cleaner Production, 2019, 227: 1002-1022.[14]YIN R, GUO W, WANG H, et al. Singlet oxygen-dominated peroxydisulfate activation by sludge-derived biochar for sulfamethoxazole degradation through a nonradical oxidation pathway: Performance and mechanism [J]. Chemical Engineering Journal, 2019, 357: 589-599.[15]MA D, YANG Y, LIU B, et al. Zero-valent iron and biochar composite with high specific surface area via K2FeO4 fabrication enhances sulfadiazine removal by persulfate activation [J]. Chemical Engineering Journal, 2021, 408: 127992.[16]ZHU S, HUANG X, MA F, et al. Catalytic removal of aqueous contaminants on N-doped graphitic biochars: Inherent roles of adsorption and nonradical mechanisms [J]. Environmental Science & Technology, 2018, 52(15): 8649-8658.[17]HUANG Q, SONG S, CHEN Z, et al. Biochar-based materials and their applications in removal of organic contaminants from wastewater: State-of-the-art review [J]. Biochar, 2019, 1(1): 45-73.[18]ODINGA E S, WAIGI M G, GUDDA F O, et al. Occurrence, formation, environmental fate and risks of environmentally persistent free radicals in biochars [J]. Environment International, 2020, 134: 105172.[19]SHANG Y N, XU X, GAO B Y, et al. Single-atom catalysis in advanced oxidation processes for environmental remediation [J].Chemical Society Reviews, 2021, 50(8): 5281-5322.[20]WANG R Z, HUANG D L, LIU Y G, et al. Recent advances in biochar-based catalysts: Properties, applications and mechanisms for [21]1220环 境 化 学43 卷。
氢能电解槽英语术语
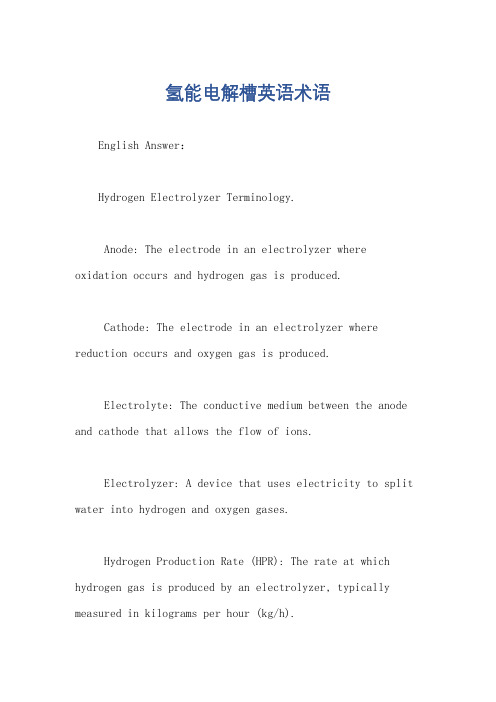
氢能电解槽英语术语English Answer:Hydrogen Electrolyzer Terminology.Anode: The electrode in an electrolyzer where oxidation occurs and hydrogen gas is produced.Cathode: The electrode in an electrolyzer where reduction occurs and oxygen gas is produced.Electrolyte: The conductive medium between the anode and cathode that allows the flow of ions.Electrolyzer: A device that uses electricity to split water into hydrogen and oxygen gases.Hydrogen Production Rate (HPR): The rate at which hydrogen gas is produced by an electrolyzer, typically measured in kilograms per hour (kg/h).Alkaline Electrolyzer: An electrolyzer that uses an alkaline electrolyte, such as potassium hydroxide (KOH).Anion Exchange Membrane (AEM) Electrolyzer: An electrolyzer that uses an anion exchange membrane as the electrolyte.Balance of Plant (BOP): The auxiliary equipment and systems that support the operation of an electrolyzer, such as water treatment, gas compressors, and power conditioning.Current Density: The amount of current passing through the electrolyzer per unit area of the electrode, typically measured in amperes per square centimeter (A/cm2).Depolarization: The reduction of the overpotential required for hydrogen evolution, which increases the efficiency of the electrolyzer.Efficiency: The ratio of the amount of energy required to produce hydrogen to the amount of energy stored in thehydrogen gas produced.Electrolysis: The process of using electricity to decompose water into hydrogen and oxygen gases.Faradaic Efficiency: The ratio of the actual amount of hydrogen produced to the theoretical amount that should be produced based on the amount of electricity used.Hydrogen Generation Unit (HGU): A system that combines an electrolyzer with auxiliary equipment, such as water treatment, gas compressors, and power conditioning.Ion Exchange Membrane (IEM) Electrolyzer: An electrolyzer that uses an ion exchange membrane as the electrolyte.Operating Voltage: The voltage required to drive the electrolysis reaction in an electrolyzer.Oxygen Production Rate (OPR): The rate at which oxygen gas is produced by an electrolyzer, typically measured inkilograms per hour (kg/h).Proton Exchange Membrane (PEM) Electrolyzer: An electrolyzer that uses a proton exchange membrane as the electrolyte.Stack: A series of electrolyzer cells connected electrically in series.Thermodynamic Efficiency: The ratio of the maximum possible amount of energy that can be stored in the hydrogen produced to the amount of electricity required to produce it.Water Splitting: The process of splitting water into hydrogen and oxygen gases using electrolysis.中文回答:氢能电解槽术语。
第10单元A课文翻译

参考译文:二氧化碳的海洋封存海洋封存二氧化碳,是控制化石燃料燃烧导致气候变化的有效手段。
人们可以通过多种方式利用天然碳储层降低人为二氧化碳排放对大气的影响。
在3个主要的天然碳储层中,海洋碳储层的储量到目前为止是最大的。
海洋碳储层的储量比陆地碳储层高出数倍,而陆地碳储层的储量大于大气碳储层的储量。
然而,目前仅大气碳储层承受化石燃料燃烧排放的二氧化碳的全部负荷,这就引起人们关注气候变化。
目前,人们已开发了增强陆地碳汇的方法,例如增加造林面积,而且,人们正在验证利用天然(地下)储层封存二氧化碳的方法。
由于海洋碳封存的过程非常复杂,因此,增强海洋碳封存能力的方法的效率并不显著。
然而,利用海洋碳储层储存(或封存)碳的潜力是巨大的。
当不考虑是否采取额外的人为干涉活动时,海洋确实是大气层中二氧化碳的主要吸收汇。
利用海洋碳储层封存二氧化碳的方法至少有两种:1)从大规模工业点源捕集二氧化碳并把二氧化碳直接注入深海;2)通过添加营养素使海洋肥化来增强大气二氧化碳的提取。
尽管上述两种方法的原理存在较大差异,但是,利用这两种方法均能提高海洋储层封存碳的速率,从而减少大气储层所承受的负荷。
由于上述两种方法仍存在不足之处,因此,利用该两种方法仍不能彻底解决减少大气储层负荷的问题。
如果二氧化碳排放量与气候变化之间的关系得到证实,则应在较长时期内减少二氧化碳的排放量。
然而,当减少二氧化碳的排放量时,利用该两种方法的确能够提供争取时间的途径。
上述两种方法在有关海洋肥化方面仍存在极大的不确定性。
把二氧化碳注入深海的相关科学研究虽然仍需进一步完善,但却易于理解。
在前工业时期,在燃烧的化石燃料向大气大量排放二氧化碳之前,全球碳储层基本上保持平衡。
尽管在大气和海洋、大气和陆地之间大量交换了碳通量,但从一种储层向另一种储层没有任何纯粹的得失。
自从工业革命以来,化石燃料已成为全世界的主要能源。
随着化石燃料的大量利用,大气中二氧化碳的排放量持续增加(目前每年向大气排放的二氧化碳为23英吨(Gt),相当于6英吨碳)。
氢能源的特点英文作文

氢能源的特点英文作文Title: Hydrogen Energy: A Clean and Versatile FutureIn the quest for sustainable and environmentally friendly energy sources,hydrogen energy has emerged as a promising contender. Hydrogen, the most abundant element in the universe, possesses an array of remarkable characteristics that make it an ideal alternative to traditional fossil fuels. This essay delves into the unique attributes of hydrogen energy, its potential applications, and thechallenges that lie ahead in its widespread adoption.Hydrogen Energy: An OverviewHydrogen energy is essentially the chemical energy released during the reaction between hydrogen and oxygen, producing only water vapor as a byproduct. This process is not only clean but also sustainable, offering a stark contrast to theharmful emissions associated with fossil fuel combustion. Hydrogen's versatility lies in its ability to be produced from various sources, including renewable ones like solar and wind power, and its ease of storage and transportation.Key Characteristics of Hydrogen Energy1.Cleanliness: Hydrogen combustion is inherently clean, releasing only watervapor. This eliminates greenhouse gas emissions and other pollutants, making it a viable solution to mitigate climate change and improve air quality.2.Renewability: Hydrogen can be produced using renewable energy sources,ensuring a sustainable and endless supply. This not only reduces reliance on finite fossil fuels but also promotes energy diversity and resilience.3.High Energy Density: Hydrogen boasts a remarkable energy density, allowing itto store and transport large amounts of energy efficiently. This feature is particularlyadvantageous for long-distance transportation and large-scale energy applications.4.Flexibility: Hydrogen can be utilized in diverse ways, including as a fuel forcombustion engines, as an energy source for fuel cells, and even as a raw material inindustrial processes. Its versatility enables it to meet a wide range of energy demands. 5.Ease of Storage and Transportation: Hydrogen can be compressed or liquefiedfor convenient storage and transportation, making it a practical energy carrier. However, specialized infrastructure is required to ensure safe handling.Applications of Hydrogen Energy1.Transportation: Hydrogen fuel cell vehicles (FCVs) are the most visibleapplication of hydrogen energy. These vehicles emit zero emissions and offer a driving range comparable to traditional combustion engines. With the development of acomprehensive hydrogen refueling network, FCVs could revolutionize the transportation sector.2.Power Generation: Hydrogen can be used in fuel cells to generate electricity,providing a clean and efficient alternative to fossil fuel-based power plants. Thisapproach not only reduces emissions but also enhances energy security and resilience.3.Industrial Applications: Hydrogen is essential in numerous industrial processes,such as steel production, refining, and chemical synthesis. By replacing fossil fuels with hydrogen, these industries can significantly reduce their carbon footprints.Challenges and OpportunitiesDespite its numerous advantages, the widespread adoption of hydrogen energy faces several challenges. The production of hydrogen, particularly throughelectrolysis, requires substantial amounts of electricity, which can be costly.Moreover, the infrastructure for hydrogen storage, transportation, and distribution is still in its infancy, requiring significant investments. Safety concerns associated with hydrogen's highly flammable nature also necessitate the development of robust and reliable systems.However, ongoing research and technological advancements offer hope forovercoming these challenges. The development of more efficient andcost-effective production methods, such as solar-powered electrolysis, cansignificantly reduce the cost of hydrogen. Additionally, internationalcollaborations and partnerships can accelerate the construction of the necessary infrastructure and foster innovation in the field.ConclusionHydrogen energy, with its cleanliness, renewability, high energy density, andversatility, holds immense potential as a sustainable and environmentally friendly energy source. Its widespread adoption will require overcoming challenges related to production costs, infrastructure development, and safety concerns.Nevertheless, with continued research, investment, and international cooperation, hydrogen energy can pave the way for a cleaner, greener, and more sustainable future.。
- 1、下载文档前请自行甄别文档内容的完整性,平台不提供额外的编辑、内容补充、找答案等附加服务。
- 2、"仅部分预览"的文档,不可在线预览部分如存在完整性等问题,可反馈申请退款(可完整预览的文档不适用该条件!)。
- 3、如文档侵犯您的权益,请联系客服反馈,我们会尽快为您处理(人工客服工作时间:9:00-18:30)。
Erman Şenöz, Richard P. Wool Department of Chemical Engineering University of Delaware
13th Annual Green Chemistry & Engineering Conference, June 23, 2009
1.0 1.5 2.0
0
1.0
0.5
0.5
0.0
0.0 1.0 1.5 2.0
0
1.6 1.4 1.2
H e a tin g tim e a t 4 0 0 C (h r)
1.6 1.4 1.2
He ating tim e a t 4 50 C (hr)
Hydrogen Uptake (wt%)
1.0 0.8 0.6 0.4 0.2 0.0 5 10 15 20 25 30 35 40 45 50
NO MELTING !
With isotherm at 215 0C
Endotherm
2 hrs isothermal heat treatment at 185 0C
MELTING PEAK !
40
60
80
100 120 140 160 180 200 220 240 260
With isotherm at 185 0C
for future H2 powered technologies.
Background
(∆Hads= ~4 kJ/mol) Graphite Carbon Nanofibers Carbon Nanotubes Metal Organic Frameworks (MOF) Activated Carbon
0 .0 1
Electron Current (nA)
0.01
66 65 51 91 106
1E -3
0
100
200
300
0
400
500
600
T e m p e r a tu r e ( C )
Electron Current (nA)
0 .0 1
1E-3
67 55
0
50 100 150 200 250 300 350 400 450 500 550 600
Hydrogen Uptake (wt%)
1.0 0.8 0.6 0.4 0.2 0.0 0 10 20 30 40 50
2 hr 1.5 hr 1 hr
1 hr 1.5 hr 2 hr
Pressure (bar)
Pressure (bar)
Hydrogen storage capacities of CCFF heated up to 400 0C for 1, 1.5 and 2 hrs performed at 77K
Temperature ( C)
300 250 200 150 100 50 0 0 2 4 6 8 10 12 14 16 18 20 22 24 26 28 30 32
0
215 0C
T im e (h )
Crosslinking
2 hrs isothermal heat treatment at 215 0C
0
-0 .6
400
450
500
550
600
T e m p e ra tu re ( C )
Thermal Analysis of CFF (TGA and DSC)
0
0 .6
Degradation Rate low (W/s)
-4 0 .0 -6 -0 .3 -8 -0 .6 -1 0 0 50 100 150 200 250 300 350
1 E -3
Temperature ( C)
0
0
100
200
300
0
400
500
600
T e m p e r a tu r e ( C )
Hydrogen Uptake Capacities
1.5 1.2
1.6 1.4
Hydrogen Uptake (wt%)
Hydrogen Storage Capacity (wt%)
~75 kg/vehicle is required $5.5 million/vehicle is required for SWCNT $22, 000/vehicle is required for MWCNT
1 Louis Schlapbach, MRS Bull., 2002 2 Jesse L. C. Rowsell and Omar M. Yaghi, Angew. Chem. Int. 2005,44, 4670-4679 3 UDaily Archive April 9, 2007
1 8 (H 2O )
---NH-C-------NH-C-------NH-C----=O =O
Electron Current (nA)
0 .1 5
3 4 (S H 2 ) 7 6 (C S 2 ) 6 4 (S O
+ 2 +
+
, S2 )
+ +
+
0 .1 0
4 8 (C H 3S H ,S O )
OBJECTIVES
To find the best process to obtain H2 storage material from waste materials, chicken feather fibers (CFF) To fulfill Department of Energy’s (DOE) 2010 H2 storage targets which are
Chicken Feather Fiber (CFF) Properties
Bio-renewable Agricultural waste Very cheap! 6 µm diameter1 Above 92% Keratin2 Hollow tubes1 Low density
α-helix Keratin Structure
Temperature ( C)
0
Thermal Analysis of CFF (TGA and DSC)
Melting transition is at ~230 0C
0 .6 100 90 80
Heat Flow (W/g)
70
Weight (%)
0 .0 60 50 40 30 20 10 0 50 100 150 200 250 300 350
Gravimetric Capacity= 6 wt% H2 (light) Volumetric Capacity= 45 g H2/l (compact) System Storage Cost= $4 /kWh (cheap to store) System Cost= $666 (cheap)
0
400
450
500
550
600
T e m p e ra tu re ( C )
Thermal Analysis (TGA+Mass Spec.)
10
Electron Current (nA)
1
0 .1
0 .0 1
1 E -3
0
50
100
150
200
250
300
350
0
400
450
500
550
600
34 22 18 89 76 67 66 65 64 60 58 55 51 50 48 44 106 103 94 91
T e m p e ra tu re ( C )
Thermal Analysis (TGA+Mass Spec.)
Methionine Cysteine -S-S-S-S0 .2 0
Physisorption
Chemisorption
(∆Hads = ~50-100 kJ/mol) Metal Hydrides Complex Hydrides
Status of hydrogen storage vs. system targets as of 20081
1 Annual Progress Report, DOE Hydrogen Program, 2008
0.9
1.2 1.0 0.8 0.6 0.4 0.2 0.0
0.6
0.3
350 400 420 450
5 10 15 20 25 30 35 40
0
C 0 C 0 C 0 C
50
0.0 45
350
400
420
0
450
M aximum Heating Temperature ( C)
Pressure (bar)
-S-S-S-S-
1 8 (H 2O )
+
-S-S-S-S-
Electron Current (nA)
0 .1 5
3 4 (S H 2 ) 7 6 (C S 2 ) 6 4 (S O
+ 2 +
+
, S2 )
+ +
+
0 .1 0
4 8 (C H 3S H ,S O )
0 .0 5
0 .0 0 0 50 100 150 200 250 300 350
OUTLINE
Introduction