石灰回转窑技术规格书
4.2X60m回转窑

日产700吨活性石灰项目工艺技术方案Φ4.2×60m回转窑技术文本一、技术参数设备名称:回转窑数量:1台生产能力:石灰700t/d规格:Φ4.2×60m型式:单传动、单液压挡轮窑墩数:3个(2个)斜度:3.5%(正弦)转速:主传动时0.198~1.98r/min辅助传动时1.42r/h总重:553t。
(包括辅助传动、制动器、液压站、减速机和油站、窑头罩、窑头、窑尾密封装置、冷风装置等)。
二、主要零部件规格1-主传动装置1)主电机数量:1台型号:ZSN4-315-12功率:250kW电压:440调速范围:100-1000防护等级:IP44绝缘等级:F级冷却方式:起动转矩:2.5倍生产厂家:西门子2)主减速器数量:1台型号:ZSY630-71-1速比:713)入轴联轴器数量:l台4)出轴联轴器型式:胶块联轴器数量:l套2.开式齿轮传动装置数量:l套型式:单传动速比:7.21)大齿圈数量:1件(两半组合)规格:模数×齿数×齿宽28×180×450 材质:ZG35SiMn2)小齿轮数量:1个规格:模数×齿数×齿宽28×25×500 材质:3)小齿轮轴数量:1个材质:45#4.筒体部分:其中包括:1)筒体材质:Q235-C2)窑头护板材质:ZG3Cr25Ni20Si23)窑头护板联接螺栓、螺母材质:l Cr25Ni20Si24)窑尾护板材质:ZG3Cr25Ni20Si25)窑尾护板联接螺栓、螺母材质:.A2-50,A2-706)挡砖圈材质:Q2357)轮带,数量:轮带I、II各1件。
材质::ZG35SiMn型式:浮动式结构:实心矩形尺寸:直径×宽度I、ⅡΦ5000×520 ⅢΦ5000X520 (一侧带锥面)5.支承装置(I、II档)数量:其中包括:1)托轮数量:4个材质:ZG42CrMo尺寸:Φ1650×6502)托轮轴数量:2件材质:45#6.带挡轮的支承装置(Ⅲ档)数量:1套其中包括:1)托轮数量:2个材质:ZG42CrMo尺寸:Φ1650×6502)托轮轴数量:2个材质:45#3)挡轮数量:2个材质:ZG35CrMo 4)挡轮轴数量:2件材质:45#7.测温装置名称:装配式热电阻数量:8件8.挡轮液压站数量:l套9.安装工具数量:l组其中包括:(1)大齿轮安装工具数量:4件(2)筒体支撑(Φ4200) 数量:11件(3)大段节连接工具数量:24件10.窑头罩数量:l套11.窑头密封装置数量:l套型式:弹簧片叠压型12.窑尾密封装置数量:1套型式:弹簧片叠压型13.冷风套装置数量:2套四、制造标准和主要的技术要求1.按设计单位提供的Φ4.2×60m回转窑的总图、分总图及相关的配套部件图制造。
石灰回转窑工艺操作规程
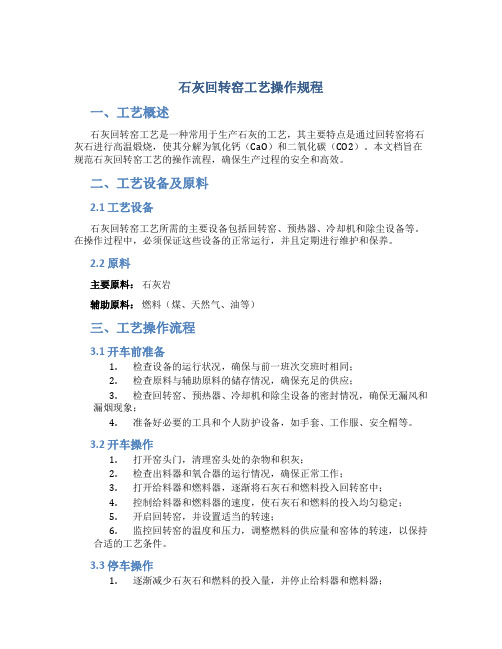
石灰回转窑工艺操作规程一、工艺概述石灰回转窑工艺是一种常用于生产石灰的工艺,其主要特点是通过回转窑将石灰石进行高温煅烧,使其分解为氧化钙(CaO)和二氧化碳(CO2)。
本文档旨在规范石灰回转窑工艺的操作流程,确保生产过程的安全和高效。
二、工艺设备及原料2.1 工艺设备石灰回转窑工艺所需的主要设备包括回转窑、预热器、冷却机和除尘设备等。
在操作过程中,必须保证这些设备的正常运行,并且定期进行维护和保养。
2.2 原料主要原料:石灰岩辅助原料:燃料(煤、天然气、油等)三、工艺操作流程3.1 开车前准备1.检查设备的运行状况,确保与前一班次交班时相同;2.检查原料与辅助原料的储存情况,确保充足的供应;3.检查回转窑、预热器、冷却机和除尘设备的密封情况,确保无漏风和漏烟现象;4.准备好必要的工具和个人防护设备,如手套、工作服、安全帽等。
3.2 开车操作1.打开窑头门,清理窑头处的杂物和积灰;2.检查出料器和氧合器的运行情况,确保正常工作;3.打开给料器和燃料器,逐渐将石灰石和燃料投入回转窑中;4.控制给料器和燃料器的速度,使石灰石和燃料的投入均匀稳定;5.开启回转窑,并设置适当的转速;6.监控回转窑的温度和压力,调整燃料的供应量和窑体的转速,以保持合适的工艺条件。
3.3 停车操作1.逐渐减少石灰石和燃料的投入量,并停止给料器和燃料器;2.降低回转窑的转速,逐渐停止回转窑的运转;3.关闭窑头门,确保密封;4.关闭除尘设备,并清理除尘器。
3.4 检修维护1.停车后,定期对设备进行检修和维护,确保设备的正常运行;2.清理设备内部和周围的积灰和杂物;3.定期检查设备的耐火材料和密封件,如果损坏,及时更换;4.对燃料器和给料器进行清洗和保养;5.定期检查烟囱和烟气排放口,确保排放符合环保要求。
四、安全注意事项1.工作人员必须熟悉工艺操作规程,并严格按照操作流程进行操作;2.在操作过程中,严禁站在窑体下方和窑头、窑尾处;3.严禁操作人员将手或其他物品伸入回转窑内部;4.使用燃料时,必须遵守安全用火规定,并确保燃料的质量符合要求;5.在操作中遇到异常情况(如烟气异常、温度过高等),应立即停车处理,并及时向上级报告。
直经3.5x54米石灰回转窑参数
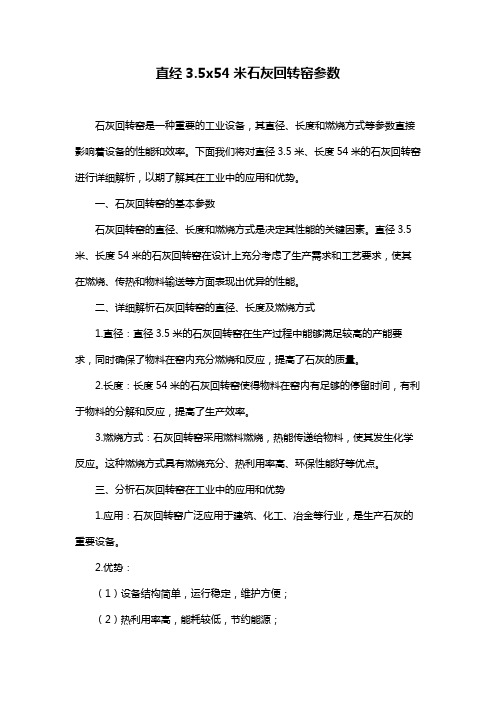
直经3.5x54米石灰回转窑参数石灰回转窑是一种重要的工业设备,其直径、长度和燃烧方式等参数直接影响着设备的性能和效率。
下面我们将对直径3.5米、长度54米的石灰回转窑进行详细解析,以期了解其在工业中的应用和优势。
一、石灰回转窑的基本参数石灰回转窑的直径、长度和燃烧方式是决定其性能的关键因素。
直径3.5米、长度54米的石灰回转窑在设计上充分考虑了生产需求和工艺要求,使其在燃烧、传热和物料输送等方面表现出优异的性能。
二、详细解析石灰回转窑的直径、长度及燃烧方式1.直径:直径3.5米的石灰回转窑在生产过程中能够满足较高的产能要求,同时确保了物料在窑内充分燃烧和反应,提高了石灰的质量。
2.长度:长度54米的石灰回转窑使得物料在窑内有足够的停留时间,有利于物料的分解和反应,提高了生产效率。
3.燃烧方式:石灰回转窑采用燃料燃烧,热能传递给物料,使其发生化学反应。
这种燃烧方式具有燃烧充分、热利用率高、环保性能好等优点。
三、分析石灰回转窑在工业中的应用和优势1.应用:石灰回转窑广泛应用于建筑、化工、冶金等行业,是生产石灰的重要设备。
2.优势:(1)设备结构简单,运行稳定,维护方便;(2)热利用率高,能耗较低,节约能源;(3)环保性能好,减少污染物排放;(4)生产效率高,满足大规模生产需求。
四、展望石灰回转窑的发展前景随着科技的不断进步和环保要求的提高,石灰回转窑将不断优化和改进,以满足更高性能、更低能耗和更环保的生产需求。
未来的石灰回转窑将具备以下特点:1.智能化:采用先进的控制系统,实现设备自动化运行,提高生产效率;2.环保化:采用新型燃烧技术和废气处理设备,降低污染物排放;3.大型化:扩大生产规模,满足日益增长的市场需求。
综上所述,直径3.5米、长度54米的石灰回转窑在工业领域具有广泛的应用和优势。
直经35x54米石灰回转窑参数

直经35x54米石灰回转窑参数
石灰回转窑的参数通常包括以下几个方面:
1. 尺寸:35x54米,这意味着石灰回转窑的长度为35米,直径为54米。
2. 倾角:石灰回转窑的倾角通常为3-4度,用于促进物料在窑内的流动和碰撞。
3. 转速:石灰回转窑的转速一般在0.3-3转/分钟之间,可以根据不同工艺要求进行调整。
4. 生产能力:石灰回转窑的生产能力取决于窑的尺寸和转速等因素,通常可以达到50-1000吨/天。
5. 燃料类型:石灰回转窑通常使用燃煤、燃油或天然气等作为燃料,以提供所需的热量。
6. 冷却方式:石灰回转窑的冷却方式通常采用下排风冷却或逆流冷却,以降低物料的温度并增加其稳定性。
这些参数可能会因具体的生产工艺和技术要求而有所不同,上述参数仅供参考。
石灰回转窑
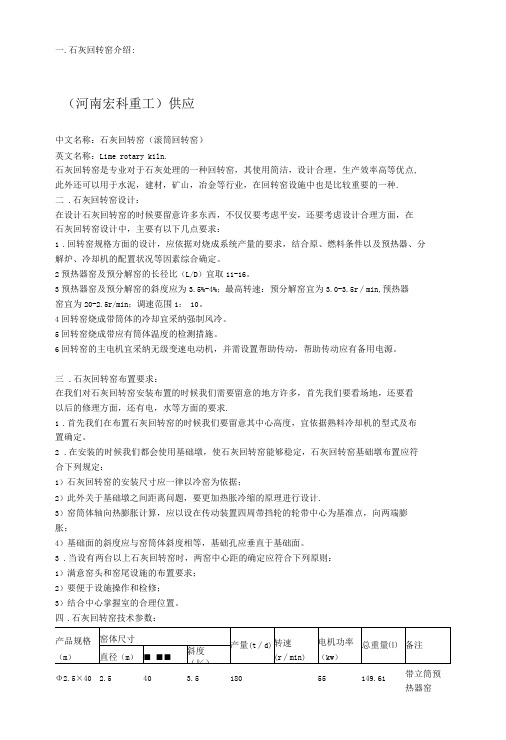
一.石灰回转窑介绍:(河南宏科重工)供应中文名称:石灰回转窑(滚筒回转窑)英文名称:Lime rotary kiln.石灰回转窑是专业对于石灰处理的一种回转窑,其使用简洁,设计合理,生产效率高等优点,此外还可以用于水泥,建材,矿山,冶金等行业,在回转窑设施中也是比较重要的一种.二 .石灰回转窑设计:在设计石灰回转窑的时候要留意许多东西,不仅仅要考虑平安,还要考虑设计合理方面,在石灰回转窑设计中,主要有以下几点要求:1.回转窑规格方面的设计,应依据对烧成系统产量的要求,结合原、燃料条件以及预热器、分解炉、冷却机的配置状况等因素综合确定。
2预热器窑及预分解窑的长径比(L/D)宜取11-16。
3预热器窑及预分解窑的斜度应为3.5%-4%;最高转速:预分解窑宜为3.0-3.5r∕min,预热器窑宜为20-2.5r/min;调速范围1: 10。
4回转窑烧成带筒体的冷却宜采纳强制风冷。
5回转窑烧成带应有筒体温度的检测措施。
6回转窑的主电机宜采纳无级变速电动机,并需设置帮助传动,帮助传动应有备用电源。
三 .石灰回转窑布置要求:在我们对石灰回转窑安装布置的时候我们需要留意的地方许多,首先我们要看场地,还要看以后的修理方面,还有电,水等方面的要求.1.首先我们在布置石灰回转窑的时候我们要留意其中心高度,宜依据熟料冷却机的型式及布置确定。
2.在安装的时候我们都会使用基础墩,使石灰回转窑能够稳定,石灰回转窑基础墩布置应符合下列规定:1)石灰回转窑的安装尺寸应一律以冷窑为依据;2)此外关于基础墩之间距离问题,要更加热胀冷缩的原理进行设计.3)窑筒体轴向热膨胀计算,应以设在传动装置四周带挡轮的轮带中心为基准点,向两端膨胀;4)基础面的斜度应与窑筒体斜度相等,基础孔应垂直于基础面。
3.当设有两台以上石灰回转窑时,两窑中心距的确定应符合下列原则:1)满意窑头和窑尾设施的布置要求;2)要便于设施操作和检修;3)结合中心掌握室的合理位置。
石灰化工回转窑相关标准

石灰化工回转窑相关标准1、HG-T 20566-1994化工回转窑设计规定2、HG 21546.1-93 回转圆筒用托轮、挡轮类型与技术条件3、HG 21546.2-93 回转圆筒用托轮4、HG 21546.3-93 回转圆筒用挡轮5、HG 21546.4-93 回转圆筒进出料箱密封装置类型与技术条件6、HG 21546.5-93 回转圆筒进出料箱密封装置(MG型)与技术条件7、HG 21546.6-93 回转圆筒进出料箱密封装置(JC型)与技术条件8、JC333-91水泥工业用回转窑9、JC/T 669-1997水泥工业用旋流式立筒预热器10、JC/T 842-1999 水泥工业用单筒冷却机11、JC 336-91(代替JC 336-83)水泥工业用推动篦式冷却机12、JCJ 03-90 水泥机械设备安装工程施工及验收规范13、JC 465-92水泥工业用预热器分解炉系统装备技术条件14、GB/T17912-1999回转窑用耐火砖形状尺寸15、JC/T730-2007水泥回转窖热平衡、热效率、综合能耗计算方法16、JC/T733-2007水泥回转窖热平衡测定方法17、(JG/T203-2007)钢结构超声波探伤及质量分级法18、机械安全基本概念与设计通则第1部分:基本术语和方法(GB/T 15706.1-2007)19、机械安全基本概念与设计通则第2部分:技术原则(GB/T 15706.2-2007)20、机械安全控制系统有关安全部件第2部分:确认(GB/T 16855.2-2007)21、工业自动化系统与集成开放系统应用集成框架第2部分:基于ISO 11898的控制系统的参考描述(GB/T19659.2-2006)22、工业自动化系统与集成开放系统应用集成框架第3部分:基于IEC 61158的控制系统的参考描述(GB/T19659.3-2006)23、回转窑用耐火砖热面标记(GB/T18257-2000)24、JB/T 9054-2000离心式除尘器行业标准25、【JB/T 8916-1999】回转窑/forum/detail144666_77.html。
回转窑石灰生产工艺参数
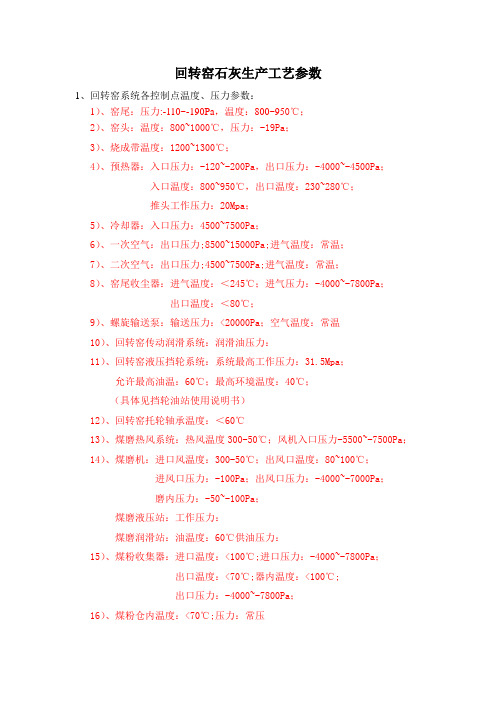
回转窑石灰生产工艺参数1、回转窑系统各控制点温度、压力参数:1)、窑尾:压力:-110~-190Pa,温度:800~950℃;2)、窑头:温度:800~1000℃,压力:-19Pa;3)、烧成带温度:1200~1300℃;4)、预热器:入口压力:-120~-200Pa,出口压力:-4000~-4500Pa;入口温度:800~950℃,出口温度:230~280℃;推头工作压力:20Mpa;5)、冷却器:入口压力:4500~7500Pa;6)、一次空气:出口压力;8500~15000Pa;进气温度:常温;7)、二次空气:出口压力;4500~7500Pa;进气温度:常温;8)、窑尾收尘器:进气温度:<245℃;进气压力:-4000~-7800Pa;出口温度:<80℃;9)、螺旋输送泵:输送压力:<20000Pa;空气温度:常温10)、回转窑传动润滑系统:润滑油压力:11)、回转窑液压挡轮系统:系统最高工作压力:31.5Mpa;允许最高油温:60℃;最高环境温度:40℃;(具体见挡轮油站使用说明书)12)、回转窑托轮轴承温度:<60℃13)、煤磨热风系统:热风温度300-50℃;风机入口压力-5500~-7500Pa;14)、煤磨机:进口风温度:300-50℃;出风口温度:80~100℃;进风口压力:-100Pa;出风口压力:-4000~-7000Pa;磨内压力:-50~-100Pa;煤磨液压站:工作压力:煤磨润滑站:油温度:60℃供油压力:15)、煤粉收集器:进口温度:<100℃;进口压力:-4000~-7800Pa;出口温度:<70℃;器内温度:<100℃;出口压力:-4000~-7800Pa;16)、煤粉仓内温度:<70℃;压力:常压17)氮气站:氮气瓶压力≮18)、窑尾CO分析仪:控制浓度<2000PPM;显示控制参数(详见工艺控制图),超出控制值进行闪烁,并音响报警;正常、上、下限分绿、黄、红颜色显示;2、石灰石供料显示供料量,并可以调整供料量;显示小时产量、班产量,累计日、月产量;3、成品显示小时产量、班产量,累计日、月产量;4、预热器储仓4台、冷却机2台、成品储仓6台、原煤储仓2台、煤粉储仓2台,共选用音叉料位计20台显示料位上下限进行自动及手动控制两种;5、煤粉计量自动跟踪给定量,显示瞬间供给量,并可以手动调整给定量;显示小时产量、班产量,累计日、月产量;6、一、二次风显示风机控制阀开启程度、出口温度、风压、风量,并可以调整供风量;7、窑头冷却风显示风机控制阀开启程度、并可以调整供风量;8、废气风机显示控制阀开启程度、进出口风压、风量、温度,并可以调整排风量;9、废气收尘器进口温度显示在控制范围内,超出上限可以自动调整冷风阀的开启量;10、煤磨热风风机温度显示在控制范围内,超出上、下限可以自动调整冷却机热风阀的混合量稳定热风温度在250±50℃范围以内;11、显示回转窑系统各设备的开启及运行状况;显示回转窑系统各设备电机运行电流。
石灰回转窑技术参数

石灰回转窑技术参数
石灰回转窑的技术参数包括以下方面:
1. 窑筒直径:一般在
2.5-6米之间,直径越大,生产能力越高。
2. 窑筒长度:一般在30-200米之间,长度越长,烧结时间越长,烧成的产品质量越好。
3. 倾角:一般在1%-5%之间,倾角越大,物料在窑筒中的停留时间越长,适合于生产精细产品。
4. 旋转速度:一般在0.5-3转/分钟之间,旋转速度越快,物料在窑筒中的停留时间越短,适合于生产大批量产品。
5. 石灰回转窑的主电机宜采用无级变速电动机,并需设置辅助传动,辅助传动应有备用电源。
6. 回转窑的烧成带筒体的冷却宜采用强制风冷,回转窑烧成带应有筒体温度的检测措施。
7. 窑体直径:400t石灰回转窑的直径一般为4-6米,根据生产需求和设备布局进行选择。
8. 窑体长度:窑体长度一般为30-60米,根据生产工艺和石灰石原料的特性来确定。
9. 倾角:一般为3-5度,它的选择与石灰石原料的性质有关。
这些参数的选择需要根据具体生产需求和设备布局等因素进行综合考虑。
- 1、下载文档前请自行甄别文档内容的完整性,平台不提供额外的编辑、内容补充、找答案等附加服务。
- 2、"仅部分预览"的文档,不可在线预览部分如存在完整性等问题,可反馈申请退款(可完整预览的文档不适用该条件!)。
- 3、如文档侵犯您的权益,请联系客服反馈,我们会尽快为您处理(人工客服工作时间:9:00-18:30)。
第六章活性石灰回转窑技术规格书第一节概述1.1规模公司钒资源综合利用项目新建80万t/a活性石灰窑工程,包括一条800t/d的回转窑活性石灰生产线和三条600t/d的竖窑活性石灰生产线。
1.2原、燃料资源和成品石灰用途1.2.1石灰石所需石灰石原料均由业主自有的石灰石矿山提供,石灰石原料在矿山上破碎筛分并经过水洗后,其中:粒度在18~50mm的石灰石由汽车运输进厂后直接储存在石灰回转窑原料堆场内,以供1条800t/d活性石灰回转窑生产线使用;粒度在40~80mm的石灰石由汽车运输进厂,储存在石灰竖窑原料堆场内,以供3条600t/d活性石灰竖窑生产线使用。
石灰石性能指标表(%)注:石灰石粒度:18~50mm,其中大于50mm和小于18mm的总量不大于5%;水分含量:≤4%;1.2.2燃料采用高炉煤气、转炉煤气和焦炉煤气混合后的煤气作为热源物质,采用热值为3500kcal/Nm3煤气,压力为10Kpa,温度为常温。
典型煤气成份如下:1.2.3产品运输和用途①回转窑石灰经筛分后20~80mm的石灰由皮带运输至新区炼钢车间供炼钢转炉、精炼炉使用,年需要量约10万吨;供老区的石灰采用汽车运输,年需求量约10万吨。
小于20mm的石灰送入破碎线破碎成0~3mm石灰粉。
②0~3mm石灰粉一部分采用气力输送至烧结石灰料仓,供烧结用,年需求量约55.4万吨;一部分采用气力(或罐车)输送,供KR脱硫用,年需要量2.3万吨;供老区的石灰粉约2.3万吨,采用罐车运输。
1.3总图运输1.3.1地理位置项目所在地属亚热带湿润季风气候区,具有四季分明、气候温和、雨量充沛、云雾多、日照少、无霜期长等气候特点。
区内年平均气温17.8℃,极端最高气温38℃,极端最低气温-4℃;年平均无霜期297天。
年平均日照1010.1小时。
年平均降雨量994.7mm,降雨量按季节分布严重不均,70%以上降于夏、秋二季。
且夏季降水强度大,多大雨和暴雨。
该地区常年主导风向为NNE风,频率9%;静风频率22%。
多年平均风速1.5m/s。
本工程所在场地的抗震设防烈度为6度,设计基本地震加速度值为0.05g。
1.3.2总平面布置的原则回转窑生产线与厂区主道路平行,自东北向西南方向平行布置,依次是窑尾废气处理系统、预热器、烧成系统、竖式冷却器;石灰石卸料储存系统、石灰石上料系统垂直于主生产线;成品储运系统平行于主生产线,利于节约用地。
3座竖窑在回转窑与石灰库之间,与回转窑平行主要包括:3座日产600吨活性石灰竖窑全钢结构窑本体及附属结构、石灰石原料堆场、原料地下式受料坑、原料除尘室及灰斗、综合风机房楼、综合控制室、煤气加压站、成品转运皮带及通廊、成品贮运等。
总平面布置符合物料流程,用辅助设施布置在负荷中心同时考虑充分利用已有的公辅设施。
除尘器、配电站、水处理、加压站尽量布置在主要用户附近。
各建(构)筑物的位置参见附图1.3.3车间组成窑区由回转窑生产区和竖窑生产区组成,操作控制室设置在一起。
1.3.4公辅设施公辅设施包括石灰贮运破碎输送及除尘系统、煤气加压站及煤气管网、循环水泵站及管网、总图道路及石灰石堆场等。
1.3.5竖向布置及场地排雨水本工程地势平坦,建设场地高程636.00米。
拟建场地与新区总平面规划标高一致。
要求新建生产线布置紧凑,流畅合理,完全能够满足工艺要求。
厂区内排水为明沟排水,排水沟的砌筑材料就地取材。
1.3.6运输石灰石年运输量约为160万吨,采用汽车运输;成品采用皮带或气力输送到各用灰点,除尘灰采用密闭罐车运输。
1.3.7道路围绕厂区新建主要道路设计宽度为7.0米,次要道路设计宽度为4.0米,结合生产工艺流程形成环线道路,同时满足生产运输、消防及管理需要,并避免运输路线的交叉干扰。
主要道路设计荷载按重型汽车荷载考虑,采用水泥混凝土路面。
1.4气象条件(1)气温:全年平均气温:17.8℃年极端最高气温:38℃年极端最低气温:-4℃(2)湿度:全年平均相对湿度:85%(3)降水量:年平均降水量:994.7mm24小时连续最大降水量:小时最大降水量:(4)风速、风向:年平均风速:1.5m/s年平均风向:NNE(5)最大冻结深度:一般无冻土1.5建筑及结构1.5.1建筑设计建筑设计要根据现行规范,既要考虑功能合理,技术先进美观实用,又要考虑当地及现场环境与各种技术条件和新材料的适用性。
1.5.2建筑构造1.5.2.1屋面厂区生产车间及辅助建筑均为无组织排水。
除尘器控制室、风机房、高压配电室、泵房所需设保温层,保温材料采用水泥膨胀珍珠岩,按规范施工,满足使用要求。
屋面防水采用4厚SBS改性沥青防水卷材和基层处理剂各一道。
窑头厂房起脊屋面,采用单层彩色涂料板,板厚大于0.6mm。
1.5.2.2墙体砖混结构砌体采用240蒸压粉煤灰砖,外墙面抹灰刷涂料;框架填充墙用240空心砖,或其它轻质保温填充砌体(根据当地情况另定)。
1.5.2.3地面一般均采用素混凝土地面;控制室采用防静电塑料地面;高压配电室采用环氧树脂漆地面。
1.5.2.4楼面一般均采用混凝土随捣随抹光楼面;控制室采用防静电塑料楼面。
1.5.2.5地坑防水地下水水面以下地坑应做防水混凝土地坑,并做好变形缝防水设计,浅坑只做防潮抗渗处理。
1.5.2.6门窗一般采用塑钢门窗;生产车间和其它生产辅助车间根据有关规范要求采用卷帘门、木门、隔声门等;生产车间高处采用通风钢百页窗或较宜开启的悬窗;钢皮带廊部分窗户采用立转窗。
1.5.2.7楼梯、栏杆厂区生产车间一般采用钢梯,钢管扶手,钢栏杆。
1.5.2.8外墙粉刷砖墙采用抹灰墙面外刷有色外墙涂料。
混凝土壁板外墙面刷涂料。
1.5.2.9内墙粉刷生产车间内墙做150高水泥踢脚线,以上采用抹灰墙面外刷白色墙涂。
控制室内墙做150高水泥踢脚线,以上采用抹灰墙面外刷高级乳胶漆。
一般钢筋混凝土库壁内不作粉刷,要求内壁平整光洁,拆横后用水泥腻子将刷部不整之处刮平即可。
1.5.2.10天棚一般生产车间如为现浇钢筋砼顶板,拆模后用水泥腻子刮后刷白色涂料两遍,如为预制板面应勾缝刮腻刷涂料;控制室设轻钢龙骨铝塑板天棚。
1.5.3结构设计1.5.3.1基础工程窑头及其他多层厂房基础采用钢筋混凝土独立基础或桩基。
窑尾预热器塔架基础采用钢筋混凝土整体基础或桩基。
成品粉灰库、成品块灰库基础采用钢筋混凝土环形基础或桩基。
大型设备基础:如窑中基础一般采用钢筋混凝土墙式基础一般采用大块式钢筋混凝土基础,。
输送天桥:架空的天桥,采用较大跨度的钢桁架承重,基础采用钢筋混凝土独立基础或桩基,所有钢支架的柱脚用C15素砼保护。
一般砌体结构基础为墙下条形基础。
地坑及地沟采用防水钢筋混凝土结构,抗渗等级S8。
1.5.3.2结构方案窑头采用钢筋混凝土结构,其他多层厂房采用现浇钢筋混凝土框架结构。
窑尾预热器塔架:窑尾采用框架结构。
成品粉灰库、成品块灰库采用混凝土结构,侧壁及顶部采用混凝土结构。
输送天桥:架空的天桥,采用较大跨度的钢桁架承重,支柱采用钢支架承重结构。
一般砌体结构:采用空心砌块承重结构,屋面为现浇钢筋混凝土结构。
1.6技术要求1.6.1成品质量GB/T3286.1-1998说明:活性度是指取活性石灰50g,用4NHCl滴定,5min滴定值。
1.6.2废气排放浓度粉尘有组织排放,排放标准按2007年下发的《钢铁工业大气污染物排放标准》-炼钢标准执行,经除尘后的废气粉尘含量低于30mg/Nm3。
1.7总设计原则1.7.1选择生产工艺方案时,在认真调查研究的基础上做好方案对比,尽可能地采用成熟、可靠的新工艺、新技术,做到既技术先进,又经济合理、切实可靠;1.7.2在保证生产工艺合理流畅的基础上,充分考虑地形地貌对建设场地的影响,以及原料、燃料、水、电、压缩氮气等的需求情况,尽量减少工程总投资;原料、成品系统以及工程范围内的公辅设施,在满足生产的前提下,力求从简设计,严格控制基建投资;3×600t/d竖窑生产线与1×800t/d回转窑生产线共用一套成品石灰筛分破碎储运系统。
要求4个窑皆能从两台主皮带输送成品灰。
1.7.3工艺技术装备水平本着先进、使用、可靠、经济的原则进行;1.7.4所有工艺设备的设计及设备制造以国产设备为主,只引进部分关键技术和关键设备;1.7.5电气和自动化控制,要考虑到技术先进,设备和仪器成熟可靠实用;1.7.6选用节能设备,充分贯彻节能降耗的原则;1.7.7贯彻国家环保政策,注意环境保护。
1.7.8选用先进、可靠的传感器、计量秤对物料(包括原料入炉、成品产量、皮带输送到各用户的成品)进行计量,提高计量精度及自动化水平;1.7.9布置力求紧凑,减少中间物料的倒运环节,减少扬尘点,减少物料的转运破碎和扬尘;1.7.10所有扬尘点粉尘处理选用新型、高效收尘设备,使工程中的粉尘达标排放;1.7.11设计符合国家、行业和地方有关法律、法规、标准和有关规定。
1.8投标方供货总要求1.8.1所有设备应正确设计和制造,为了安全和持续运行,满足要求工况下的功能而不致有过度的应力、振动、腐蚀、老化等其它运行和维修问题。
1.8.2设备必须是全新的并有可靠的设计。
所组成的部件如认为带有试制性质的将不予接受。
设备部件的制造过程应是高技术的,加工精确并有良好工艺、光洁、合适的公差配合及互换性。
易于磨损、腐蚀或老化、或需要调正、检查、或更换的部件应提供备用品,并能比较方便地拆卸、更换和修理。
应有安装或维修时便于起吊或搬运的设施。
1.8.3所有的材料应符合有关规范的要求,并应是全新的和优质的。
铸件和锻件应符合相应的材料规范,无有害的缺陷。
1.8.4在设备制造过程中必须实施严格质量管理,包括必要的处理、检验和试验、监造,出厂前需由招标方检查验收。
1.8.5对于转动机械、转子或叶轮等部件必须有安全的运转频率,并进行必要的静态和动态平衡。
1.8.6机械设备和电气设备应能在额定频率±5%的变化下安全和持续地运行。
1.8.7投标方应为烟道、管道(包括附件)和地下管沟提供防腐保护并严格执行;除非在有关章节中另有说明,防腐保护用的防腐衬里和包裹层的耐用性应不小于15年;设备、管道、平台扶梯及栏杆等暴露于空气中的外表面应进行防腐处理。
1.8.8振动:设备必须在符合有关规定允许的振动条件下运行,所有关于振动和平衡的说明应符合相关的规范和标准。
1.8.9通道1)对检修和巡视通道应进行设计,应设置到达阀门、检查门和其它运行点的平台。
2)所有设备的设计和布置应使得可以对它们在最少的时间内进行检查、维护和更换。
可能在运行期间更换的装置必须安全地封闭起来,更换工作必须以最少的费用实现,无需安装辅助平台或不损坏其它装置。
3)无辅助工具不能接近的装置必须配备适合的维护设施。