空分生产工艺过程
空分流程简介
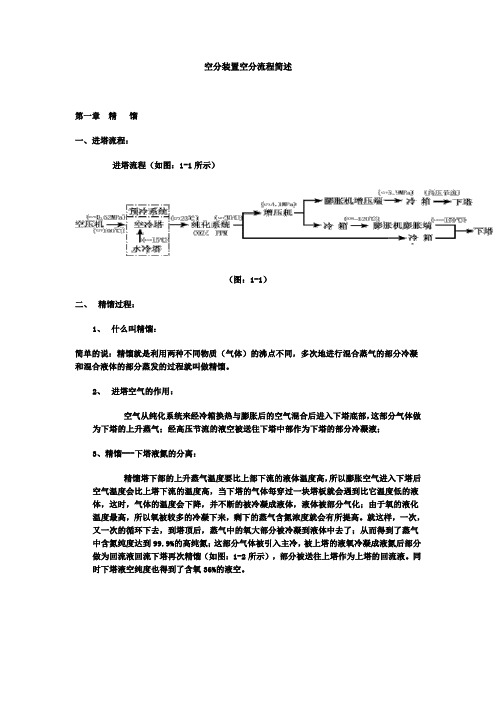
空分装置空分流程简述第一章精馏一、进塔流程:进塔流程(如图:1-1所示)(图:1-1)二、精馏过程:1、什么叫精馏:简单的说:精馏就是利用两种不同物质(气体)的沸点不同,多次地进行混合蒸气的部分冷凝和混合液体的部分蒸发的过程就叫做精馏。
2、进塔空气的作用:空气从纯化系统来经冷箱换热与膨胀后的空气混合后进入下塔底部,这部分气体做为下塔的上升蒸气;经高压节流的液空被送往下塔中部作为下塔的部分冷凝液;3、精馏---下塔液氮的分离:精馏塔下部的上升蒸气温度要比上部下流的液体温度高,所以膨胀空气进入下塔后空气温度会比上塔下流的温度高,当下塔的气体每穿过一块塔板就会遇到比它温度低的液体,这时,气体的温度会下降,并不断的被冷凝成液体,液体被部分气化;由于氧的液化温度最高,所以氧被较多的冷凝下来,剩下的蒸气含氮浓度就会有所提高。
就这样,一次,又一次的循环下去,到塔顶后,蒸气中的氧大部分被冷凝到液体中去了;从而得到了蒸气中含氮纯度达到99.9%的高纯氮;这部分气体被引入主冷,被上塔的液氧冷凝成液氮后部分做为回流液回流下塔再次精馏(如图:1-2所示),部分被送往上塔作为上塔的回流液。
同时下塔液空纯度也得到了含氧36%的液空。
(图:1-2)4、上塔精馏:将下塔液空经节流降压后送到上塔中部,作为上塔精馏原料;而从主冷部分抽出的液氮则成为上塔的回流液;与下塔精馏原理相同,液体下流时,经多次部分蒸发和冷凝,氮气较多的蒸发出来,于是下流液体中含氧浓度不断提高,到达上塔底部时,可以获得含氧99.9%的液氧;部分液氧作为产品抽出;由于下塔上升蒸气(纯氮气),被引入主冷冷凝,所以它将热量较多的传给了液氧,致使液氧复热蒸发作为上塔的上升气;在上升过程中,一部分蒸气冷凝成液体流下,另一部分蒸气随着不断上升,氮含量不断增加;到塔顶时,可得到99%以上的氮气。
第二章开车步骤一、启动步骤:1、空气压缩机;2、空气预冷系统;3、空气纯化系统;4、空气增压机;5、空气膨胀机;6、分馏塔系统操作。
空分的工艺流程

空分的工艺流程
《空分工艺流程》
空分是一种将空气中的氧气、氮气、稀有气体和其他成分通过物理分离的工艺。
空分工艺通常包括空气压缩、冷却凝华、蒸汽冷凝和分离等步骤。
首先,空气通常会被压缩到高压状态,以便进行后续的处理。
然后,被压缩的空气会在减压阀的作用下迅速减压并且冷却,在这个过程中会发生冷凝和液化。
接着,液化后的空气还会在蒸馏塔中进行进一步的分离工艺。
在蒸馏塔中,液化的空气会被升温并且进入一个叫做精馏塔的设备,通过塔内填料层的多级分馏逐步分离成不同的成分。
这些成分包括氧气、氮气、稀有气体等。
通过这种分馏过程,不同的气体可以被选择性地收集和提纯。
最终,通过这种工艺流程,空气中的各种成分可以被有效地分离和提纯,得到高纯度的氧气、氮气和其他气体产品。
这些高纯度的气体产品被广泛应用于医疗、工业、科学研究等领域。
总的来说,《空分工艺流程》是一种高效的气体分离技术,其具体步骤和设备设计可以根据需要进行调整和优化,以满足不同领域的需求。
空分工艺有哪些操作规程
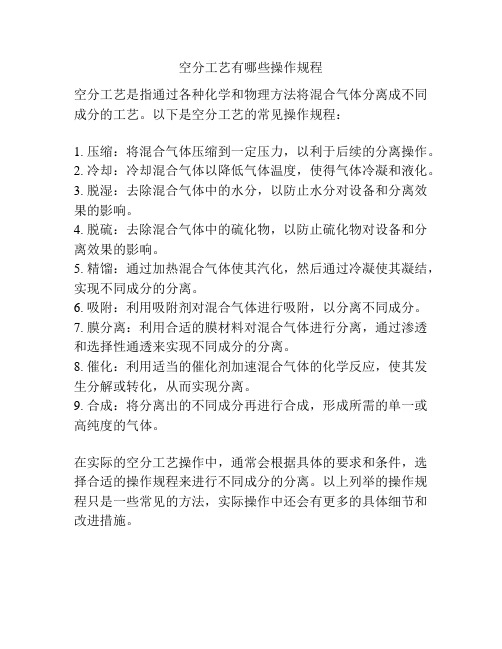
空分工艺有哪些操作规程
空分工艺是指通过各种化学和物理方法将混合气体分离成不同成分的工艺。
以下是空分工艺的常见操作规程:
1. 压缩:将混合气体压缩到一定压力,以利于后续的分离操作。
2. 冷却:冷却混合气体以降低气体温度,使得气体冷凝和液化。
3. 脱湿:去除混合气体中的水分,以防止水分对设备和分离效果的影响。
4. 脱硫:去除混合气体中的硫化物,以防止硫化物对设备和分离效果的影响。
5. 精馏:通过加热混合气体使其汽化,然后通过冷凝使其凝结,实现不同成分的分离。
6. 吸附:利用吸附剂对混合气体进行吸附,以分离不同成分。
7. 膜分离:利用合适的膜材料对混合气体进行分离,通过渗透和选择性通透来实现不同成分的分离。
8. 催化:利用适当的催化剂加速混合气体的化学反应,使其发生分解或转化,从而实现分离。
9. 合成:将分离出的不同成分再进行合成,形成所需的单一或高纯度的气体。
在实际的空分工艺操作中,通常会根据具体的要求和条件,选择合适的操作规程来进行不同成分的分离。
以上列举的操作规程只是一些常见的方法,实际操作中还会有更多的具体细节和改进措施。
空分车间生产工艺与原理

空分车间生产基本工艺与原理1、空分综述1.1、空气及空气分离空气存在于我们地球表面,属典型的多组分混合物,主要成分有氮气、氧气及惰性气体,按体积含量计,氧气占20.95%、氮气占78.09%、氩占0.932%,此外还有微量的氢、氖、氦、氪、氙、氡,以及不定量的水蒸汽及二氧化碳。
在标准状况下,空气液化温度为87.7K。
空气分离是指把空气通过一定的方法分离出氧气、氮气和惰性气体的过程。
目前分离的方法主要有深冷法、变压吸附法、膜分离法,它们各有自己的优缺点。
变压吸附法、膜分离法主要用于低纯度、小型空分设备;焦炉煤气制合成氨项目用产品气量大且纯度要求高,故采用深冷法。
深冷法基本原理是:将空气液化后,根据各组份沸点不同,通过精馏将各组分进行分离。
空气分离的主要产品为氧气及部分氮气。
1.2、空分装置简介1.2.1.装置特点我公司选用了由开封黄河制氧厂生产的第六代空分装置,流程上采用全低压、外压缩,不提氩的结构。
主要特点:⑴采用带自动反吹的自洁式空气过滤器,保证了运行周期及运行效果;⑵预冷系统利用多余的污氮气及氮气对水进行冷却,降低冷水机组热负荷,减小冷水机组功率选型,不但节能且充分利用了富余气体干基吸湿潜热;⑶采用分子筛吸附,大大简化空气净化工艺,延长了切换周期,减少加工空气切换损失。
利用分子筛所具有的选择性高吸附率,提高了净化效果,减少碳氢化合物、氮氧化物及二氧化碳进入液氧的量,确保主冷的安全同时延长装置大加温周期;⑷采用增压机制动的透平膨胀机,提高单位气体制冷量,减少膨胀空气对上塔精馏段的影响,优化了精馏操作;⑸分馏塔下塔采用高效塔板,上塔采用规整填料,降低精馏塔操作压力,提高了塔板和填料的精馏效率,保证了氧的提取率、降低制氧单耗;⑹设置液氧贮槽及汽化系统,加大主冷液氧排放量,杜绝碳氢化合物、氮氧化物及二氧化碳在液氧中析出,最大限度保证主冷安全。
液氧汽化系统为空分装置短停时系统用氧提供了方便,确保后工段工艺连续,减少后工段开停车损失;⑺装置采用DCS集散控制系统,使操作更加方便和稳定。
空分工艺流程简介
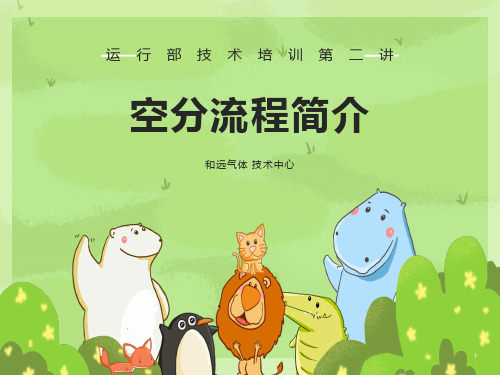
和远气体 技术中心
三、压缩系统
电机
压缩机头
润滑系统
冷却系统
电控、仪表系统
压缩系统
压缩系统将空气压缩到一定压力,为节流或膨胀产生冷量,为气体液化做准备。压缩系统耗电是空分系统耗能主要来源,无论从安全还是能耗角度来看,压缩系统地位都尤为突出突出,是制冷液化系统的心脏!
带动压缩机
压缩空气
润滑压缩机和电机轴承
污氮预冷水冷塔
换热效果
换热温差
换热系数
换热器材料结构
换热器是否结垢、阻塞
流体流动速度、流向
换热介质
水冷塔
空冷塔
和远气体 技术中心
四、冷却系统
冷箱内换热系统
主换热器
冷凝蒸发器
过冷器
是上塔底部液氧汽化、下塔顶部氮气液化,冷量自上塔传至下塔
回收返流气体的冷量
将空气冷却到所需状态
过冷去上塔夜空、液氮,减小节流气化率,增加回流液。
二、净化系统
和远气体 技术中心
净化系统主要由自洁式空气过滤器、纯化器组成。前者原理为过滤除尘,后者原理为吸附法除水蒸气、二氧化碳、碳氢化合物。具体的原理及操作,我们以后再讲,这里强调一下日常我们所要关注的内容。
1、流量(处理能力):选加工空气量的两倍; 2、压力损失; 3、除尘效率; 4、寿命
1、温度 2、压力 3、出纯化器后空气露点 4、出纯化器二氧化碳含量
三、压缩系统
1、活塞式压缩机从低压到超高压,适用范围广;效率高,排量范围广; 2、排气不稳定,脉动大;结构复杂,易损件多;活塞油润滑,导致空气带油。
压缩机应用实况
1、转速高,处理气量大,体积质量相对较小;结构简单;排气平稳,不受润滑油污染; 2、气量小的时侯效率低
空分工艺流程介绍07
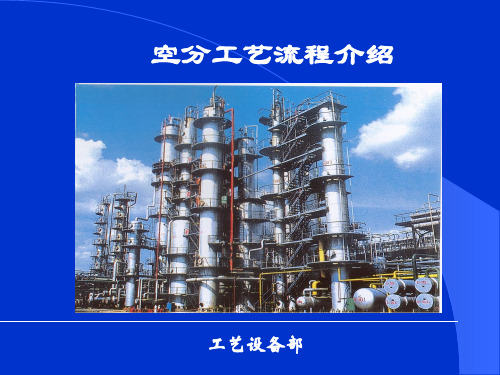
5.分子筛纯化系统
分子筛纯化系统由两台分子筛吸附器和 三台电加热器组成。
分子筛吸附器吸附空气中的水份、二氧 化碳和一些碳氢化合物,两台分子筛吸附 器一台工作,另一台再生,交替运行。再 生气的加热由电热器提供热量在其中完成。
6.分馏塔精馏系统 出分子筛吸附器的空气首先分为两部分:
第一部分直接进入主换热器冷却后进入 下塔;
第二部分通过空气增压机进一步压缩, 经增压机末级后冷却器冷却后再次分成两 部分。
一部分经膨胀机增压端增压并冷却后进 入主换热器,在主换热器合适的位置抽出, 进入膨胀机膨胀端膨胀后进入下塔参加精馏;
另一部分经过主换热器,然后经节流阀 节流成液体后进入下塔参加精馏。
下塔中的上升气体通过与回流液体接触 含氮量增加。所需的回流液氮来自下塔顶部 的冷凝蒸发器,在这里液氧得到蒸发,而气 氮得到冷凝。
利用双泵内压缩的流程使其投资低、安全 性能高、操作方便,还能控制优化。
二、工艺技术总述
本套制氧站工艺流程采用常温分子筛 预净化,空气增压透平膨胀机提供装置 所需冷量,双塔精馏,单泵内压缩流程, 同时设有液体贮存及汽化装置系统,整套 空分装置采用DCS系统控制。
三、总工艺流程图
四、工艺流程说明
空气经下塔初步精馏后,在下塔底部获 得液空,在顶部获得纯液氮。
6.1下塔从上到下产生以下产品或中间 产物:
·压力氮气 ·污液氮 ·富氧液空(36~40%) 下塔各产品去向如下:
①压力氮气:从下塔顶部抽出后经主换 复热后进入氮气压缩系统。
②污液氮:污液氮在过冷器中过冷后送 入上塔顶部作回流液。
1.流路简述 整套空分设备包括: 空气过滤系统、空气压缩系统、空气预 冷系统、分子筛纯化系统、分馏塔系统、 液体贮存系统、仪控系统、电控系统等八 大系统。
空分工艺流程
第三部分空分工艺流程的组成一、工艺流程的组织我国从1953年,在哈氧第一台制氧机,目前出现的全低压制氧机,这期间经历了几代变革:第一代:高低压循环,氨预冷,氮气透平膨胀,吸收法除杂质;第二代:石头蓄冷除杂质,空气透平膨胀低压循环;第三代:可逆式换热器;第四代:分子筛纯化;第五代:,规整填料,增压透平膨胀机的低压循环;第六代:内压缩流程,规整填料,全精馏无氢制氩;○全低压工艺流程:只生产气体产品,基本上不产液体产品;○内压缩流程:化工类:5~8:临界状态以上,超临界;钢铁类:3.0,临界状态以下;二、各部分的功用净化系统压缩冷却纯化分馏(制冷系统,换热系统,精馏系统)液体:贮存及汽化系统;气体:压送系统;○净化系统:除尘过滤,去除灰尘和机械杂质;○压缩气体:对气体作功,提高能量、具备制冷能力;(热力学第二定律)○预冷:对气体预冷,降低能耗,提高经济性有预冷的一次节流循环比无预冷的一次节流循环经济,增加了制冷循环,减轻了换热器的工作负担,使产品的冷量得到充分的利用;○纯化:防爆、提纯;吸附能力及吸附顺序为:;○精馏:空气分离换热系统:实现能量传递,提高经济性,低温操作条件;制冷系统:维持冷量平衡液化空气膨胀机方法节流阀膨胀机制冷量效率高:膨胀功W;冷损:跑冷损失 Q1复热不足冷损 Q2生产液体产品带走的冷量Q3第一节净化系统一、除尘方法:1、惯性力除尘:气流进行剧烈的方向改变,借助尘粒本身的惯性作用分离;2、过滤除尘:空分中最常用的方法;3、离心力除尘:旋转机械上产生离心力;4、洗涤除尘:5、电除尘:二、空分设备对除尘的要求对0.1以下的粒子不作太多要求,因过滤网眼太小,阻力大;对0.1以上的粒子要100%的除去;三、过滤除尘的两种过滤方式1、内部过滤:松散的滤料装在框架上,尘粒在过滤层内部被捕集;2、表面过滤:用滤布或滤纸等较薄的滤料,将尘粒黏附在表面上的尘粒层作为过滤层,进行尘粒的捕集;自洁式过滤器:1以上99.9%以上;阻力大于1.5KPa。
空分设备的工艺流程
空分设备的工艺流程
你知道吗,我刚接触这玩意儿的时候,那叫一个头大!感觉就像走进了一个迷宫,找不着北。
但慢慢地,我算是摸出了点门道。
先来说说空气过滤这一步吧,就好比给空气洗个澡,把那些杂质啥的都给弄出去。
这一步要是没做好,后面可就麻烦大啦!我记得有一次,就因为这过滤没弄好,唉,那设备闹脾气,可把我折腾惨了!
然后呢,就是压缩环节。
哇,那机器嗡嗡响,震得我耳朵都快聋啦!压缩的时候可得注意压力,不然就容易出岔子。
接下来是冷却,这一步就像是给热得发烫的家伙冲个凉水澡,让它冷静冷静。
我跟你说啊,有一回我不小心操作失误,温度没控制好,那后果不堪设想!
再往后就是精馏分离啦。
这可是个精细活儿,就像分宝贝似的,得小心翼翼。
我当初学这个的时候,那是绞尽脑汁啊,反复琢磨,才算是搞明白了。
对了,说到这,我想起个事儿。
有个同行跟我说,他有次居然把流程顺序给搞混了,哈哈,是不是特逗?
还有啊,这空分设备的发展也是日新月异。
想当年,技术可没现在这么先进,我们操作起来那叫一个费劲。
现在可好啦,各种新玩意儿不断,不过我这脑子有时候还真跟不上。
嗯...我这讲得是不是有点乱?不管啦,反正就是这么个大概意思。
要是您有啥不明白的,尽管问我!我这又扯远啦,咱接着说。
空分流程详细讲解
空分流程详细讲解
在化工生产中,空分技术是一项非常重要的工艺,它能够将空气中的氧气、氮
气等气体进行分离,以满足工业生产和生活需求。
下面我们将详细介绍空分的工艺流程。
首先,空分的工艺流程可以分为压缩、预冷、精馏、蒸汽回收等步骤。
1. 压缩空气从大气中获取,首先需要将其进行压缩,以增加气体分子的密度,提高分离效率。
压缩后的空气会进入压缩机,经过一系列压缩工艺,压缩比达到要求后,进入下一个环节。
2. 预冷压缩后的空气含有大量水分和杂质,需要通过冷却器进行预冷处理。
在预冷过程中,空气中的水分和杂质会凝结成液体,然后通过分离装置将其分离出去,以保证后续工艺的顺利进行。
3. 精馏精馏是空气分离的核心步骤,通过精馏塔将空气中的氧气、氮气等气体按照其沸点的不同进行分离。
在精馏塔内,气体混合物被加热至沸点,然后在不同高度上凝结成液体,从而实现气体的分离。
4. 蒸汽回收在精馏过程中,会产生大量的废热,为了提高能源利用效率,通常会将废热通过蒸汽回收装置进行回收利用。
蒸汽回收装置可以将废热转化为蒸汽,用于加热其他部分的工艺设备,实现能量的循环利用。
通过以上流程,空分技术能够高效地将空气中的氧气、氮气等气体进行有效分离,为工业生产和生活提供了重要的物质基础。
在实际应用过程中,还需要根据不同的需求和工艺要求进行调整和优化,以实现最佳的分离效果和能源利用效率。
空分技术作为一种成熟的工艺,在化工领域中扮演着至关重要的角色,不仅广
泛应用于气体生产、化工生产等领域,还在医疗、食品加工等领域有着重要的应用价值。
随着工业化进程的不断推进,空分技术将继续发挥重要作用,为人类的生产生活提供更广阔的发展空间。
空分工艺流程简介
设备紧凑,能耗低,操作简便。但膜材料性能要求较高,分离效率受膜材料影响较大。
03
空分设备组成及功能
空气压缩机
01
将大气中的空气吸入并进行压缩,提高空气的压力 和温度。
02
为后续的冷却、纯化和分离过程提供必要的动力。
03
通常采用多级压缩和级间冷却的方式,以提高压缩 效率和降低能耗。
冷却器与纯化器
原理
空分工艺主要基于空气中氧气、氮气等组分的沸点不同,通过精馏方法将其分 离。在低温条件下,空气被液化后送入精馏塔,经过多次部分汽化和部分冷凝, 实现各组分的分离。
空分工艺应用领域
冶金工业
用于高炉富氧炼铁、炼 钢吹氧等,提高产量和
降低能耗。
化学工业
石油工业
医疗保健
作为合成氨、合成甲醇 等化工过程的原料气。
分离过程
精馏塔分离
利用精馏塔中的温度梯度和浓度梯度,使空气组分在塔内多次部分汽化和部分冷凝,实现氧气、氮气等组 分的分离。
冷凝蒸发法
通过冷凝器将空气液化后,利用不同组分的沸点差异进行分离。液氧在冷凝蒸发器中蒸发,同时吸收热量, 使液氮冷凝成液体,从而实现氧氮分离。
产品输出与储存
产品输出
将分离得到的氧气ቤተ መጻሕፍቲ ባይዱ氮气等产品通过管道 输送至用户端或储存设备。
再生技术
采用加热、减压等方法对 吸附剂进行再生,恢复其 吸附性能。
膜分离法关键技术与参数
膜材料选择
选用具有高渗透性、选择 性和稳定性的膜材料,如 有机膜、无机膜等。
膜组件设计
通过合理的膜组件结构设 计和优化,提高膜分离效 率。
操作条件
控制适当的操作温度、压 力和膜两侧浓度差,以实 现目标组分的有效分离。
- 1、下载文档前请自行甄别文档内容的完整性,平台不提供额外的编辑、内容补充、找答案等附加服务。
- 2、"仅部分预览"的文档,不可在线预览部分如存在完整性等问题,可反馈申请退款(可完整预览的文档不适用该条件!)。
- 3、如文档侵犯您的权益,请联系客服反馈,我们会尽快为您处理(人工客服工作时间:9:00-18:30)。
氮压机岗位
任务是 将低压氮气经氮压机加压至< 3.0MPa后,再送往净化甲烷化配氮用; 经干螺杆氮压机加压至<0.8MPa用于 煤气化工段干灰脱除工序的气提、通气及 仪表气源; 经联合氮压机加压至<5.2MPa后送往煤气 化给料包调压、氧管线吹扫、煤进料罐加 速器的吹扫;加压至<7.2MPa后送往煤气 化及中高温高压过滤器、激冷器和合成气 冷却器的进口的反吹。
制冷系统
空分设备是 通过压缩空气在 膨胀机内进行绝 热膨胀,产生空 分装置所必需低 温,提供冷量。
热交换系统
空分的热平衡是通过制冷系统和 热交换系统来完成的。 经过初步降温、 净化后的常温空气在 主换热器中被低温氧 气、氮气、污氮气冷 却至液化点,同时氧、 氮、污氮气被空气加 热至常温。
精馏系统
空分生产的重点岗位
透平空压机岗位 分馏岗位 氧压机岗位 氮压机岗位
透平空压机岗位
岗位任务是:将空气经过三段(或五级、四 级)压缩至≤0.626MPa(表)并冷却后进 入空气冷却系统。
透平空气压缩机工作原理: 连续性气体在工作轮作用下,利用气流惯性力 在随后的减速运动中,使气体分子之间距离更加接 近而达到气体压力提高的目的。 主要设备及参数:
空分生产的主要设备
氧气压缩机 卧式往复氧压机7 台,四缸四级压缩, 用于加压氧气输送 1-5#机处理气量3500 m³ /h,6、7#处理气 量4000 m³ /h,终压 <4.325Mpa,电功率 800KW 运行模式六开一备
空分生产的主要设备
氮气压缩机
卧式往复氮压机7台,加压氮气输送 • 1#、2#、3#、4#、5#均为四缸三级压缩,处理气量3500 m³ /h,终压< 3.0Mpa,电功率630KW; • 6#氮压机为四缸四级压缩,处理气量3500 m³ /h,终压3.0Mpa,电功率 800KW; • 7#氮压机六缸四级压缩,处理气量14000 m³ /h,终压<3.0Mpa,电功率 2500KW。 运行模式一大四小二备
另一种采用的是第 六代空分设备,常温分 子筛净化,增压膨胀空 气进上塔,填料型上塔, 全精馏无氢制氩流程。 特点采用多项新技术, 节能效果显著,与第五 代空分设备相比装置总 能耗下降8%~10%,制氧 能耗为0.37~0.43 KW· 。 h/m³ 以 KDON10000/20000型空 分为代表,实际出氧 9500M3/h以上,纯度 99.6%,出氮19000M3/h 以上,纯度99.99%,出氩 200~300M3/h,纯度达 99.999%以上。
1台
1台
分馏岗位
岗位任务是将空压机送来的压缩原料空气经过冷却、净化、 液化、精馏等过程制取纯度达99.0%以上的低压氧气99.99% 的低压氮气、99.2%以上的液氧及纯度≥99.999%的液氩等产品。
本岗位包括空气预冷系统、分子筛纯化系统、增压膨胀 机系统及空气精馏系统。 主要技术工艺参数: 产品氧气纯度≥98.5% 出上塔污氮气纯度≤5%O2 产品氮气纯度≥99.99% 下塔液空纯度38%O2 空气吸附后的CO2含量<1ppm 膨胀机出口温度控制:
控制系统
大型空分设备都采用计算机集散控制 系统,实现自动控制。
空气分离的工艺流程
原料空气在过滤器中除去灰尘和机械杂质, 进入空压机压缩至<0.625Mpa后,送入空气冷 却塔进行清洗和预冷。压缩空气在空冷塔内自 下而上被循环水和低温水冷却降温至≤15℃。
出空冷塔的空气进入交替使用的分子筛吸 附器,除去水分、二氧化碳和乙炔等杂质。一 只工作的同时另一只利用污氮气加热、吹冷进 行再生活化,整个工作或再生时间约4小时。
空分生产的主要设备
联合氮压机
卧式往复联合氮 压机2台:加压氮 气输送 四缸二级压缩, 一级入口压力< 3.0Mpa;一级出口 压力< 5.2Mpa, 二级出口压力< 7.2Mpa,电功率 800KW。 运行模式 一开一备。
空分生产的主要设备
干螺杆氮气压缩机
仪表氮压机 3台, 提供仪表氮气 处理气量 2400m³ /h,出 口压力0.8Mpa, 电功率260KW。 运行模式二开一 备
在上塔底部获得氧气,经主换热器复热至
18℃后出冷箱作为产品输出。液氧产品从冷 凝蒸发器底部抽出,进入液氧贮槽。 从上塔中部抽取约11140m³ /h、含氩711%(含氧92%左右)的氩馏分送入粗氩塔。 粗氩塔在结构上分为两段,第二段粗氩塔底 部的液体经循环液氩泵加压至0.8Mpa被送入 第一段顶部作为回流液。经粗氩塔精馏得到 氩含量≥98.5%、氧含量≤2pmm流量约347 m³ /h的粗氩气,进入精氩塔中部。经精氩塔 精馏实现氩氮分离,在精氩塔底部得到含量 99.999%的精液氩。
空分设备的核心,实现低温分离的 重要设备。 采用高、低压两级精馏方式。由低压 塔、中压塔和冷凝蒸发器组成。 液化空气在精馏塔中被分离为纯净的 氧气、氮气。
产品输送系统
生产的氧气、氮气需要一定的压 力才能满足后工序的使用。 主要由各种不同规格的氧气压缩 机和氮气压缩机组成。
液体贮存系统
空分设备能生产一定的液氧和液氩 (氮)等产品,进入贮存系统,以备需要时 使用。 主要由各种不同规格的低温贮槽、低 温液体泵和汽化器组成。
Mpa 0.41 - 174.9
液化温度 ℃
- - 174.4 173.9
- - - - 173.4 173.0 172.5 171.7
影响产品产量和纯度的因素:
①加工空气量越多,气体产品越多,空气量受季节、 环境温度的影响,夏季相对冬季来讲,空气量要 少一些。 ②产品流量与产品纯度成反比,气体产品取出越多, 产品纯度就会下降。 ③膨胀空气量过大,不利于产品纯度提高。 ④精馏塔的精馏工况和精馏效率。 ⑤节流调节阀开度的影响。
净化后的加工空气分两股:一股经增压膨胀
机膨胀后送入上塔参与精馏。另一股进入主 换热器被返流气体冷却至液化温度-173℃后 进入下塔。 空气在下塔初步精馏后,在下塔底部获得含 氧38%的液空,在下塔顶部获得纯液氮。抽 取下塔液空、纯液氮进入上塔相应部位,在 上塔顶部获得纯氮气。经过冷器、主换热器 复热至18℃后出冷箱作为产品输出。
在标准状态下,空气液化温度172℃,氧的液化温度-182.8℃,氮的液 化温度-195.7℃,氩的液化温度-185.7℃。 氧氮沸点相差13℃,氩氮沸点相差 10℃,这就是能够利用低温精馏法将空气 分离成氧、氮和氩气的基础。
空分装置的工作过程
①空气的过滤和压缩; ②压缩空气的初步冷却; ③空气的净化即空气中微量水份、CO2、乙 炔和碳氢化合物的清除 ; ④空气被冷却到液化温度; ⑤冷量的制取; ⑥液化和精馏; ⑦危险杂质的排除。
制氧的工艺原理
低温精馏分离法制氧就是以自然 界中取之不尽、用之不竭的空气 为原料,先使空气在低温下液化, 然后在精馏塔中利用氧、氮各组 分沸点的不同,分离为氧气和氮 气。
干燥空气的组成
空气是一种均匀的多组分混合气体, 主要成分是氧、氮、氩,此外还有微量的 惰性气体。 根据地区条件不同,空气中含有不定 量的二氧化碳、水蒸汽以及乙炔等碳氢化 合物。 空气中氮占78.084%、氧占20.95%、氩 占0.932%。
氧压机岗位
岗位任务是将纯度≥99.0%的 低压氧气经氧压机 加压至<4.315MPa后送往煤气化供粉煤造气。
氧压机着火原因:
与氧气接触的零件脱脂不彻底,有油渍。 刮油器、挡油圈效果不好,造成活塞杆带油。 填料漏氧。 机组断水或水量不足。 工况波动大,压力温度不稳定,压缩比异常。 吸气温度高,造成排气温度高。 活塞杆温度高。 因各种原因引起火花。 内吹氮中断。
从上塔中上部引出污气,经过冷器、主换热
器复热后出冷箱,一部分进入蒸汽加热器作 为分子筛再生气体,一部分经污氮鼓风机加 压至0.050Mpa输出,其余气体送入水冷塔。
双环公司空分装置所采用的流程形式
一种采用的是第五代空分设备,常温分子筛净 化空气,增压膨胀空气进上塔的流程。 特点:氧提取率进一步提高,可达到 93%~97%、能耗进一步下降,约为 0.47~0.53KW· 。 h/m³ 以DON3200/4500型空分为代表,实际出氧 4000M3/h、纯度99.6%,出氮6000M3/h、纯度 99.99%。两套KDON4000/6000型、一套 KDON3200/5000型空分分别由原来三套 KDON3200/3200型石头蓄冷器流程相继改造而成。
空分生产工艺过程介绍
概
述
空分,顾名思义就是空气分离。 就是要设法将空气中的氧气分离出来, 因此也叫“制氧”。制氧机也被称作 “空气分离设备”。 由于氧、氮在工业生产和科学技术 发展中有重要的作用,工业上制氧的 方法有:化学法、电解法、吸附法和 低温精馏分离法。
空气分离目前主要采用低温 精馏分离法,特点是生产成本低、 技术成熟,不仅最经济,又能大量 生产氧、氮气,而且适合大规模工 业化生产,成为工业上制取氧气的 主要方法。
出口压力 Mpa 警戒温度 ℃ 液化温度 ℃ 压力 0.02 0.03 0.04 0.05 0.06 -187.5 0.53 0.55 0.07 -184.0 -186.9 0.57 - 171.2 -187.0 -186.4 -185.7 -185.2 -184.6 -190.0 -189.4 -188.7 -188.1 0.43 0.45 0.49 0.51
设备名称 空压机 型号 DA350—61 DA350—64 流量、电功率、排气压力 20000M3/h、2500Kwh 、0.63Mpa 20000M3/h、2500Kwh 、0.63Mpa 数量 3台 1台
5TYD144
4TYD122
20000M3/h、2500Kwh、 0.67Mpa
52000M3/h、5200Kwh、 0.61Mpa
7.2Mpa 送 煤气化
空分系统流程示意图
动力系统:指原料空气压缩机。