结构碰撞分析
核筒悬挂结构碰撞问题的分析
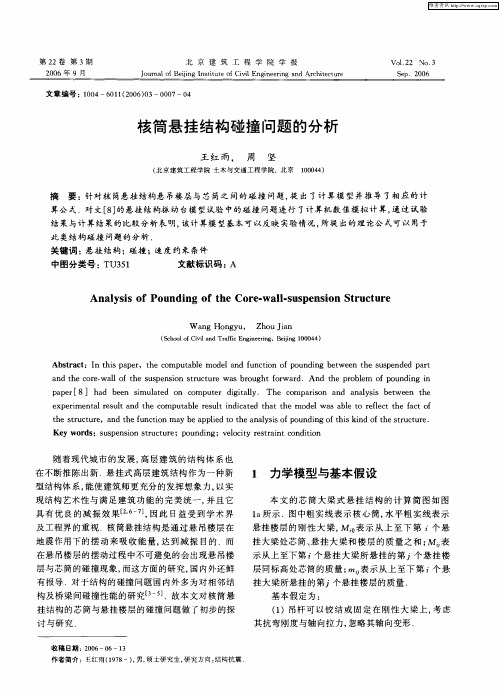
有报 导 .对 于结构 的碰撞 问题 国 内外 多为 对相 邻 结
示从上 至下 第 个悬 挂 大 梁所 悬挂 的 第 个 悬 挂 楼 层 同标高 处芯筒 的质 量 ; 表 示 从上 至下 第 i 悬 个 挂大 梁所 悬挂 的第 J个 悬挂 楼层 的质量 .
1 力学 模 型 与 基 本假 设
l 所 示 .图 中粗 实 线 表 示核 心 筒 , 平粗 实 线表 示 a 水 悬挂 楼层 的 刚 性 大 梁 , 表 示 从 上 至 下 第 i个 悬 M加
挂 大梁处 芯筒 、 挂 大 梁和 楼 层 的 质量 之 和 ; 表 悬 M
地 震作 用下 的摆 动来 吸 收能 量 , 到 减振 目的 .而 达
此 类结 构碰撞 问题 的分析 .
关键 词 :悬挂结 构 ;碰撞 ;速度 约束 条件
中图分类 号 : U3 1 T 5
文献 标识 码 : A
An l ss o u d n ft e Co e- l・ u pe so t u t r a y i f Po n i g o h r ・ wa ls s n i n S r c u e -
Vo . No. 122 3
S p.2 06 e 0
文章 编 号 :10 0 4—6 1 (0 6 0 —0 0 0 120 ) 3 0 7—0 4
核 筒 悬 挂 结 构 碰 撞 问 题 的分 析
王 红 雨 . 周 坚
( 京 建 筑 工 程 学 院 土 木 与 交 通 工 程 学 院 ,北 京 10 4 ) 北 0 0 4
e p r n a rs l a d t e c mp t b e r s l i d c td t a h d l s a l O rf c h a to x ei me t l e ut n h o u a l e u t n ia e h tt e mo e wa be t e l t t e f C f e t e s r c u e n h n t n ma e a pid t h n l s fp u d n ft i k n f h t u t r . h tu t r ,a d t e f c i y b p l O t ea ay i o o n i go h s i d o es r c u e u o e s t
机械结构的碰撞行为分析与优化设计

机械结构的碰撞行为分析与优化设计概述:机械结构的碰撞行为分析与优化设计是一门重要的工程学科。
在工程实践中,机械结构的碰撞行为会对结构的性能、寿命和安全性产生重要影响。
因此,通过对机械结构的碰撞行为进行分析与优化设计,可以提高结构的稳定性和可靠性,提升工程项目的成功率和经济性。
第一部分:碰撞行为分析的方法和技术进展1. 碰撞行为的基本概念碰撞行为是指两个或多个物体之间产生接触,并在力的作用下发生相互作用、改变运动状态的过程。
2. 数值模拟方法数值模拟方法是分析机械结构碰撞行为的常用手段。
其中有限元法是一种常用的数值模拟方法,通过将结构离散成多个小单元,利用数学模型对结构的动力学行为进行求解,从而得到结构的应力、应变、位移等重要参数。
3. 碰撞试验与数据采集技术碰撞试验是验证数值模拟结果的重要手段。
通过设计合理的试验方案和采用先进的数据采集技术,可以获取结构在碰撞过程中的各项参数,从而验证数值模拟结果的准确性。
第二部分:机械结构碰撞行为的影响因素1. 材料的特性材料的硬度、韧性、断裂韧度等特性对机械结构的碰撞行为产生直接影响。
合理选择材料以满足设计要求是优化机械结构碰撞行为的关键步骤。
2. 结构的几何形状结构的几何形状对碰撞行为产生重要影响。
合理设计结构的形状和尺寸可以提高碰撞时的能量吸收能力,减少结构的应力和变形。
3. 碰撞速度和角度碰撞速度和角度对机械结构的破坏程度和变形程度有较大影响。
通过对碰撞速度和角度进行合理的控制,可以减少结构的损伤,并提高结构的耐冲击性能。
第三部分:机械结构碰撞行为的优化设计方法1. 材料优化设计通过合理选择材料和表面处理,可以改善机械结构的碰撞行为。
例如,使用高抗冲击材料、提高材料的强度和韧性,可以有效提高机械结构的碰撞耐力。
2. 结构优化设计通过改变结构的几何形状和布局,可以提高机械结构的碰撞性能。
例如,增加结构的能量吸收区域、提高结构的刚度和强度,可以有效减少结构的损伤。
车辆碰撞后车身结构变形分析与改进
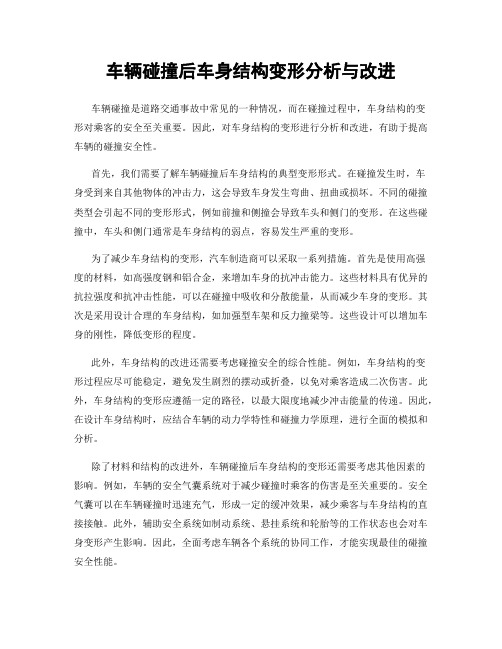
车辆碰撞后车身结构变形分析与改进车辆碰撞是道路交通事故中常见的一种情况,而在碰撞过程中,车身结构的变形对乘客的安全至关重要。
因此,对车身结构的变形进行分析和改进,有助于提高车辆的碰撞安全性。
首先,我们需要了解车辆碰撞后车身结构的典型变形形式。
在碰撞发生时,车身受到来自其他物体的冲击力,这会导致车身发生弯曲、扭曲或损坏。
不同的碰撞类型会引起不同的变形形式,例如前撞和侧撞会导致车头和侧门的变形。
在这些碰撞中,车头和侧门通常是车身结构的弱点,容易发生严重的变形。
为了减少车身结构的变形,汽车制造商可以采取一系列措施。
首先是使用高强度的材料,如高强度钢和铝合金,来增加车身的抗冲击能力。
这些材料具有优异的抗拉强度和抗冲击性能,可以在碰撞中吸收和分散能量,从而减少车身的变形。
其次是采用设计合理的车身结构,如加强型车架和反力撞梁等。
这些设计可以增加车身的刚性,降低变形的程度。
此外,车身结构的改进还需要考虑碰撞安全的综合性能。
例如,车身结构的变形过程应尽可能稳定,避免发生剧烈的摆动或折叠,以免对乘客造成二次伤害。
此外,车身结构的变形应遵循一定的路径,以最大限度地减少冲击能量的传递。
因此,在设计车身结构时,应结合车辆的动力学特性和碰撞力学原理,进行全面的模拟和分析。
除了材料和结构的改进外,车辆碰撞后车身结构的变形还需要考虑其他因素的影响。
例如,车辆的安全气囊系统对于减少碰撞时乘客的伤害是至关重要的。
安全气囊可以在车辆碰撞时迅速充气,形成一定的缓冲效果,减少乘客与车身结构的直接接触。
此外,辅助安全系统如制动系统、悬挂系统和轮胎等的工作状态也会对车身变形产生影响。
因此,全面考虑车辆各个系统的协同工作,才能实现最佳的碰撞安全性能。
综上所述,车辆碰撞后车身结构的变形分析与改进是提高乘客安全性的重要措施。
通过采用高强度材料、合理设计车身结构、考虑其他因素的影响等方法,可以有效地减少车身的变形,从而减少乘客的伤害。
此外,车身结构的改进还需要综合考虑车辆的各个系统,在碰撞时实现最佳的协同工作。
汽车碰撞防护结构设计与仿真分析

汽车碰撞防护结构设计与仿真分析随着汽车行业的快速发展,人们对汽车安全性能的要求也越来越高。
汽车碰撞防护结构是汽车 passively safety 的重要组成部分,其设计与仿真分析对于保护乘客在碰撞事故中的生命安全起着至关重要的作用。
本文将围绕汽车碰撞防护结构的设计原理、工程应用和仿真分析方法进行探讨。
汽车碰撞防护结构的设计原理是基于汽车碰撞事故的力学原理,主要目的是减轻碰撞时产生的冲击力和能量,保护车内乘员的安全。
设计师通常会采用吸能结构和衰减器来减少碰撞产生的冲击力。
吸能结构通常包括前部防撞梁、侧面加强梁和车顶梁等,它们能将部分冲击能量吸收并分散到整个结构。
而衰减器则通过变形吸收冲击力,并缓解乘员受到的冲击。
通过合理布置和设计这些防护结构,可以最大限度地保护乘员的安全。
工程应用方面,设计师需要考虑汽车碰撞防护结构的安全性、轻量化和制造成本等因素。
安全性是设计的首要考虑因素,因为碰撞防护结构的主要目标是保护乘员的生命安全。
在进行设计时,需要注意车身刚度、碰撞试验等方面的要求。
轻量化是当前汽车工业的重要发展方向,因为降低车身质量可以提高燃油经济性和行驶性能。
因此,在设计碰撞防护结构时,设计师要在保证安全性的前提下尽量减少结构的重量。
制造成本也是设计过程中的关键因素。
制造成本的降低可以使得汽车更加普及,因此设计师要在满足安全性和轻量化的前提下尽可能降低制造成本。
仿真分析在汽车碰撞防护结构的设计中起着重要的作用。
通过数字模拟,可以在不同碰撞情况下评估碰撞防护结构的性能,并进行优化设计。
在仿真分析中,设计师可以使用有限元分析方法对碰撞防护结构进行模拟。
有限元分析是一种数值计算方法,能够模拟材料和结构的力学行为,预测结构在不同加载条件下的响应。
这种方法可以帮助设计师了解碰撞防护结构在受到冲击时的应力、变形和能量吸收情况。
通过不断优化设计和吸收碰撞能量的路径,设计师可以提高碰撞防护结构的性能。
此外,利用仿真分析还可以进行碰撞事故模拟,并评估乘员的安全性能。
第八讲-车身结构分析汽车碰撞安全
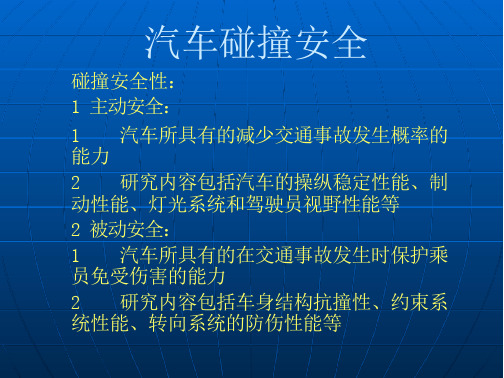
采用四舍五入的方法保留到小数点后两位。
腹部评分
1
该部位最高得分为 4 分,最低得分为 0 分。假
人腹部得分通过测量假人相关指标而产生,其评价指
标为腹部力,其对应最高分为 4 分,采用高性能限值和
低性能限值来计算。
2 高性能限值: 腹部力
1.0kN低性能限值: 腹部力
2.5kN
大小腿评分
1、大腿
1高性能限值:大腿压缩力 3.8kN; #
量不超出127mm
前视
侧视
抗压传递路线图
车门铰柱静力强度测试
按照国标GB15086-2013规定
1 车门铰柱可承受11000N的纵向载荷,铰柱机构不脱开; 2 车门铰柱可承受9000N的垂直向载荷,铰柱机构不脱落。
车顶抗压强度
对汽车碰撞性能提出的要求
翻滚试验示意图:台车
对汽车碰撞性能提出的要求
我国参照欧洲的ECE R94法规制定了国家强制标准GB 11551-2003 《乘用车正面碰撞的乘员保护》
GB 11551-2003
40%正面碰撞
(1) 试验车辆 40%重叠正面冲击固定可变形吸能壁 障。碰撞速度为 63~65km/h;
(2) 偏置碰撞车辆与可变形壁障碰撞重叠宽度应在 40%车宽±20mm 的范围内。
(1)移动台车前端加装可变形吸能壁障冲击试验车辆 驾驶员侧,移动壁障行驶方向与试验车辆垂直,移动壁 障中心线对准试验车辆R 点,碰撞速度为(试验速度 不得低于 50km/h);移动壁障的纵向中垂面与试验车 辆上通过碰撞侧前排座椅R 点的横断垂面之间的距离应 在±25mm内。
(2)在驾驶员位置放置一个EuroSID II 型假人, 用以 测量驾驶员位置受伤害情况。在第二排座 椅被撞击侧放置SID-IIs(D 版)假人,用以测量第二 排人员受伤害情况。(详见第四章规定的碰 撞试验方法)
两种截面结构车架纵梁轴向碰撞性能分析

对薄壁梁受轴 向冲击载荷状态下 的耐碰撞性能进 行数值模拟分析 , 是较精确和简便的仿真方法。
耐碰撞性薄壁梁 在轴 向冲击载荷作用下 的能量 吸
收 与变形 特性 。
1 研究背景
对 薄壁杆 件 受 轴 向 冲击 载 荷 状 态 下 的耐 碰 撞 性 能进 行 了数 值 模 拟 分 析 。 良好 的 吸能 结 构 能将
车以 4 8 k m / h的速 度 发 生 正 面碰 撞 时 ,其 前 端 纵 梁 吸 收约 5 0 % 一7 0 % 的碰 撞 能 ,车架 纵 梁 的碰 撞 性 能对 整车 的碰撞 性 能 具有 决 定 性 的影 响。 因此 , 设 计具 有较 高 吸 能 结 构 的前 纵 梁成 为 汽 车 碰撞 安
相关。
国 内外 的 学 者 对 薄 壁 直 梁 进 行 的实 验 与仿 真 研 究 大 多集 中在 正 方 形 、矩 形 、圆形 等 截 面 形 状 ቤተ መጻሕፍቲ ባይዱ
直梁 的研 究 ,对 锥 形 截 面 梁 的研 究 较 少 。本 文 针
考虑设 计 成 本 及 试 验 成 本 ,需 对 不 同 结 构 薄
两种 截 面结 构车 架 纵 梁 轴 向碰 撞性 能分 析
吕 松 郑 毅 郑卫 刚
1武汉理工大学能源与动力工程 学院 武汉 4 3 0 0 6 3 2武汉理工大 学工程 实训 中心
摘
武汉 4 3 0 0 6 3
要 :运 用非 线性有 限元理论建立 了方形 和方 锥形 2种 不 同截 面薄壁直 梁的有 限元 模型 ,研究 了这 2种
全性研 究 的一个 重要 内容 。
属薄 壁 构 件作 为传 统 、有 效 的缓 冲吸 能 装 置 , 已经在车身 吸能 体 系的设 计 中得 到 了广泛 的应
不同材质的车身结构在碰撞中的比较分析

不同材质的车身结构在碰撞中的比较分析车辆的安全性能一直是汽车制造商和车主所关注的重点之一。
在真实的道路环境中,车辆可能会遇到各种情况,如追尾、偏离道路或与其他车辆或障碍物相撞。
因此,车辆的结构和材料对于车辆的安全性能至关重要。
在本文中,我们将分析不同材质的车身结构在碰撞中的比较,有助于消费者更好地了解车辆安全性能的指标。
1. 钢质车身钢质车身一直是汽车制造商的首选,它的热熔焊接和机械封闭式焊接技术能够提高碰撞时的刚性,从而能够吸收和分散能量。
随着时间的推移和技术的进步,汽车制造商已经采用了更先进的超高强度钢和高强度钢来生产车身,以提高碰撞安全性能。
这些钢材是经过高度冷却和时效处理,以提高材料的强度和延展性。
相比之下,普通钢材在碰撞中的效果不如这些特殊钢材好,因为它们具有较低的强度和抗变形能力。
2. 铝质车身近年来,铝质车身开始受到汽车制造商的青睐,因为铝材可以在重量和强度之间寻找平衡,从而减少车重并提高燃油经济性。
然而,铝质车身在碰撞时可能不如钢质车身稳定。
铝材的强度较低,可能会被压扁或弯曲,从而增加了车内乘员的受伤风险。
值得注意的是,一些汽车制造商已经开始利用高强度铝制造汽车,以提高安全性能和降低车重。
但是,这些材料相对来说价格昂贵,造车成本更高。
3. 碳纤维复合材料车身碳纤维复合材料被用于生产高端跑车和赛车,因为它具有极高的强度和轻量化的特性,但成本高昂。
碳纤维复合材料在碰撞中的表现相当出色,因为它具有优越的能量吸收和分散能力。
在一些高速撞击试验中,使用碳纤维复合材料所制造的汽车可以有效地消除碰撞时产生的能量,从而使驾驶员和乘员获得更高的安全保障。
但是,由于成本限制,这种车身材料目前被应用在高端车型上。
在总体上,钢质车身似乎是最受欢迎的材料,因为它可以满足汽车安全、价格和经济性的需求。
然而,在技术不断革新的今天,其他车身材料也在不断出现和应用。
这样,我们便有了更多的选择和考虑因素。
总体来说,选择车型时,消费者应该优先考虑车辆的安全性能、车辆的标准和制造工艺。
汽车碰撞模拟仿真分析对车辆整体结构刚度的优化策略

汽车碰撞模拟仿真分析对车辆整体结构刚度的优化策略一、引言车辆碰撞安全一直是汽车设计中至关重要的考虑因素之一。
在汽车行业中,进行碰撞模拟仿真分析成为了一种有效的手段,可以在设计阶段对车辆进行安全性能评估和优化。
本文将探讨使用碰撞模拟仿真分析技术对车辆整体结构刚度进行优化的策略。
二、汽车碰撞模拟仿真分析原理汽车碰撞模拟仿真分析是通过建立数学模型,并利用计算机软件对车辆在各种碰撞情况下的动态响应进行预测和分析。
其中,对车辆整体结构刚度的优化是模拟仿真分析的重要一环。
三、车辆整体结构刚度的意义车辆整体结构刚度是指车身结构在受到碰撞时的抗变形性能,也是保证车辆乘员安全的重要指标之一。
较高的整体结构刚度可以有效降低车身的变形程度,减少乘员的受伤风险。
四、优化策略一:材料选择与加强合理的材料选择和加强可以显著提高车身整体结构的刚度。
通过使用高强度钢材料或复合材料等新型材料,并在关键连接部位进行加固设计,可以提高车身的刚度和耐久性。
五、优化策略二:结构设计与优化车辆整体结构的设计和优化是提高刚度的重要手段。
通过在设计阶段采用适当的结构形式,如选择合适的梁柱形式、增加加强筋等,可以有效提高车辆整体结构的刚度。
六、优化策略三:优化悬挂系统悬挂系统是车辆整体结构的一部分,也对刚度的提高起到重要作用。
通过优化悬挂系统的设计,如增加悬挂支撑件、调整悬挂参数等,可以改善车辆的悬挂刚度,进而提升整体结构的刚度。
七、优化策略四:合理分配车身刚度在设计车辆整体结构的同时,合理分配车身的刚度也是提高整体刚度的关键。
通过在不同区域设置合适的刚度分布,可以减少碰撞能量对车辆的影响,降低乘员受伤的可能性。
八、模拟仿真分析在刚度优化中的应用利用碰撞模拟仿真分析技术,可以在设计阶段对车辆整体结构进行虚拟碰撞测试,验证刚度优化策略的有效性。
此外,通过分析仿真结果,可以得出最佳的刚度优化方案,为车辆的实际制造提供有力的指导。
九、结论汽车碰撞模拟仿真分析对车辆整体结构刚度的优化策略有重要意义。
- 1、下载文档前请自行甄别文档内容的完整性,平台不提供额外的编辑、内容补充、找答案等附加服务。
- 2、"仅部分预览"的文档,不可在线预览部分如存在完整性等问题,可反馈申请退款(可完整预览的文档不适用该条件!)。
- 3、如文档侵犯您的权益,请联系客服反馈,我们会尽快为您处理(人工客服工作时间:9:00-18:30)。
l=length of the element c= E ρ
壳单元:
l=
A max(L1,L2,L3,L4)
,
c= E
L4
ρ(1- ν 2 )
L1
for
triangular
L3
shells:
l=
2A max(L1,L2,L3)
A
L2
文件系统
Jobname.K
• 在执行ANSYS SOLVE命令后自动生成的LS-DYNA 输入文件
注意: 临界时间步尺寸由LS-DYNA 自动计算。它依赖于单元长度和材料特性(音速) 它很少需要用户重新定义(后面将讨论)。
• LS-DYNA在计算所需时间步时检查所有单元. 为
达到稳定采用一个比例系数(缺省为0.9)来减小
时间步:
t 0.9cl
• 特征长度 l 和波速 c 取决于单元类型:
梁单元:
第5章 结构碰撞分析
显式和隐式方法的比较
静态
“准” 静态
动态
结构问题
SF=0
PUNCH BLANK
DIE
金属成形
SF» 0
碰撞问题
S F = ma
隐式方法
显式方法
隐式时间积分:
u tt
K
1
Fa t t
线性问题:
– 当[K] 是线性时无条件稳定 – 可以采用大的时间步
非线性问题:
– 通过一系列线性逼近(Newton-Raphson) 来获得解 – 要求对非线性刚度矩阵[K]求逆 – 收敛需要小的时间步 – 对于高度非线性问题无法保证收敛
MATSUM:
材料能量总结 (基于 Part ID 号)
SPCFORC:
单点 (节点) 约束反作用力
RCFORC:
接触面反作用力
RBDOUT:
刚体数据
NODOUT:
节点数据
ELOUT:
单元结果
etc....
Binout文件 D3Plot文件
• 材料特性 (*Mat)
• 初始条件
• 接触设定(*Contact)
• ANSYS
• ETA
• PATRAN
• OASYS –Primer
• HyperCrash
• ANSA
临界时间步
• 杆件的临界时间步长
– 自然频率:
c ωmax=2 l
其中
E c= ρ
(波传播速度)
• 临界时间步长:
l Δt=
c
– Courant-Friedrichs-Levy-准则
– Δt 为波传播杆长 l需要的时间
显式时间积分 • 用中心差分法在时间 t 求加速度:
at
M 1
F ext t
Fint t
其中
{Ftext}为施加外力和体力矢量, {Ftint}为下式决定的内力矢量:
F int BT
nd F hg F contact
• Fhg 为沙漏阻力 (见 单元 一章) ;Fcont 为接触力. • 速度与位移用下式得到:
• 包括存在于ANSYS数据库中的几何、载荷和材料数据
时间历程 ASCII 输出文件
• 包含显式分析的附加信息的特定文件
• 用户在求解前定义要输出的文件 (EDOUT command)
• ASCII 输出文件 (一些通过 POST26 中EDREAD命令可以获得的) 包括:
GLSTAT:
总体统计和能量
• 计算控制文件(计算步长,终止时间…….) (*Control)
• 输出控制 (*Байду номын сангаасatabase)
习题:方盒的跌落试验
vtt / 2 vtt / 2 at t t
utt ut vtt / 2 t tt / 2
其中 tt+t/2=.5(tt+ tt+ t) and tt- t/2=.5(tt- tt+ t)
概述
… 显式-隐式方法的比较
隐式时间积分
显式时间积分
• 对于线性问题,时间步可以 任意大(稳定)。
• 当时间步小于临界时间步时 稳定
• 对于非线性问题,时间步由 于收敛困难变小
t t crit 2
max
• 其中wmax = 最大自然角频率
• 由于时间步小,显式分析对瞬态问 题有效
• LS-DYNA
求解器
• PamCrash
• Radioss
• TNO-Madymo
DYNA的前后处理器
• LS-PrePOST