型芯零件数控铣削加工程序编制
数控铣床程序编制及操作

数控铣床程序编制及操作数控铣床程序编制及操作数控铣床是一种高精度、高效率的机床,能够对工件进行高精度的加工,其程序编制和操作是数控加工的关键环节。
本文将从数控铣床的概念、程序编制、操作等方面进行介绍。
一、数控铣床的概念数控铣床是一种采用计算机控制系统的机床,能够对工件进行三维雕刻、镂空、倒角、孔加工等复杂加工。
数控铣床具有高效精密、自动化程度高等特点,可以替代传统手工加工及普通机床加工,成为重要的制造技术手段之一。
二、数控铣床程序编制数控铣床程序编制是指将加工工艺要求汇总,导入计算机中进行处理,然后生成控制加工中心的一系列加工程序。
具体流程如下:1、了解零件图纸编制加工程序之前,必须对要加工的零件图纸进行仔细分析,了解零件的几何形状、尺寸、位置及精度要求等方面。
2、确定加工工艺根据了解的要求,确定零件加工所需的加工工艺,包括加工方式、刀具类型、加工顺序及加工方式等。
3、计算参数根据零件的各项几何数据和零件加工顺序,逐步确定加工过程中所需的各个参数,如切削深度、切削速度、进给速度、刀具的路径等。
4、程序编写在加工程序编辑器中输入计算所得的加工参数,用相应的语言编写加工程序,并检查程序的正确性。
5、加工模拟对编写好的程序,进行加工模拟,查看刀具路径、零件加工状态等,以确保程序的正确性。
6、工艺文件汇总将零件图纸、加工工艺、加工参数、程序和加工模拟结果等整理在一起,形成一个工艺文件。
三、数控铣床操作数控铣床的操作需要进行详细规范的流程和过程,下面进行具体介绍:1、准备工作使用机床轴手轮进行零点调整,确定坐标系原点。
安装夹具或者卡盘固定工件,进行工件定位。
清理工作区域,检查机床各部分、夹具和工件的紧固性。
2、程序传输使用U盘或者网口将编写好的加工程序传入数控铣床。
3、加工参数输入根据工艺文件所列出的加工参数,手动输入或使用数控铣床的自动输入功能,将刀具、切削速度、进给速度等参数输入到数控铣床控制系统中。
零件的数控铣削加工说课稿

《零件的数控铣削加工》说课稿一、课程定位与设计1、课程定位《零件的数控铣削加工》是数控技术专业的终端学习课程之一,该课程是以培养熟练掌握数控铣/加工中心操作、工艺制定、程序编制等高技能人才为目标,满足机械行业数控加工岗位需要而设置的一门基于工作过程导向,工学结合数控技术专业核心课程。
通过本课程教学,使学生掌握数控铣削编程技术,具有熟练操作数控铣床/加工中心的能力,培养学生掌握中等复杂程度零件加工的整个工作过程,使学生达到数控机床操作工中级以上水平,同时也为完成《CAD/CAM》等后续课程的学习起到重要支撑作用,将进一步培养学生机械行业职业素质,养成良好的机械加工职业习惯。
为后期进行的顶岗实习奠定良好基础;在校内生产性实训基地和企业实训基地中开展理论实践一体化教学,了解企业生产实际,接受职业熏陶,培养职业素养。
2、课程设计(1)课程设计思路根据数控技术专业毕业生就业面向和专业人才培养目标,采用基于工作过程课程开发方法,以工学结合为切入点,基于岗位能力分析,吸取工厂技术工人的实际经验,参照国家职业鉴定标准,以数控铣床/加工中心的典型零件加工为载体,以职业成长为主线,结合已有课程改革基础和现有教学条件,校企合作共同开发系统化的专业课程体系,通过校企合作实施工学结合方式的专业人才培养。
(2)课程设计方法《零件的数控铣削加工》课程设计按照岗位(群)工作分析及论证,典型工作开发及论证,课程设置开发及论证,单元(情境)教学设计的步骤进行。
采取能力递减法从毕业生就业岗位的实际工作归纳出典型工作,即按照生产(服务)管理流程,将实际工作中的各关联任务所需的技能进行归纳整合,形成具有职业特征,体现任务综合性,富有教学价值的理想工作,完成这些典型工作即能够胜任岗位工作要求。
采取能力递增法对这些典型工作进行教学加工,即按照从低端简单典型工作任务到高端复杂典型工作任务的顺序,完成专业技术课程设置与排序,体现单一到综合的能力形成规律。
数控技术 第二章 零件加工程序的编制

一 数控机床程序编制的内容和步骤
选择对刀点的原则: (1)为了提高零件加工精度,刀具的起点应尽量选在零件的设计
基准或工艺基准上。 (2)对刀点应选在对刀方便的位置,便于观察和检测。 (3)对刀点的选择应便于坐标值的计算。 (4)在加工中心上,由于加工过程中要进行换刀,每次换刀所选
择的换刀位置要在工件的外部,以免换刀时刀具与工件相碰。
加工过程中,工件、刀具、夹具、机床系统处于弹性变形的平 衡状态下,进给停顿时,切削力减小,会改变系统的平衡状态。刀 具会在进给停顿处的零件表面留下划痕,因此在轮廓加工中应避免 进给停顿。
一 数控机床程序编制的内容和步骤
3)要选择工件在加工后变形较小的路线。例如对细长零件或薄板零 件,应采用分几次走刀加工到最后尺寸。
此检查机床运动轨迹与动作的正确性。 在具有图形显示的机床上,用模拟刀具进行试削过程的
方法进行校验。
二 数控机床的编程方法
手动编程 定义:整个编程过程由人工完成。对编程人员的要求高 (熟悉数控代码功能、编程规则,具备机械加工工艺 知识和数值计算能力) 适用:① 几何形状不太复杂的零件; ② 三坐标联动以下加工程序
一 数控机床程序编制的内容和步骤
(一)分析零件图样和工艺处理 1 选择合适的对刀点 对刀点----刀具相对零件运动的起点,又称起刀点。 刀位点----刀具在机床上的位置是由刀位点的位置来表示的。 立铣刀、端铣刀和钻头而言,是指他们的底面中心; 球头铣刀,是指球头球心; 对车刀和镗刀是指它们的刀尖。
二 数控机床的编程方法
自动编程: 定义:编程人员根据零件图纸的要求,按照某个自动编程系 统的规定,将零件的加工信息用较简便的方式送入计算 机,编程系统将能根据数控系统的类型输出数控加工程 序。 适用: ① 形状复杂的零件 ② 虽不复杂但编程工作量很大的零件(如有数 千个孔的零件) ③ 虽不复杂但计算工作量大的零件(如非圆曲 线轮廓的计算)
数控加工程序编制铣削编程4孔类零件的程序编制
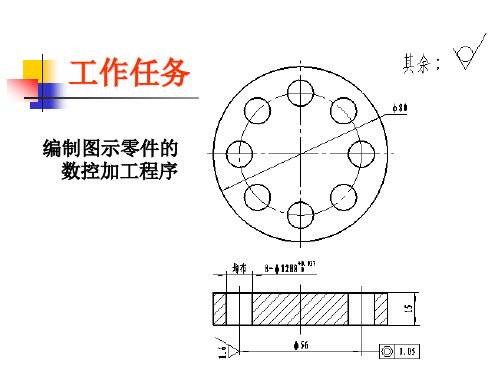
二、相关知识
(四)孔加工循环指令
举例:如图所示,用此程序加 工xy平面上在z轴方向排列的螺 纹孔M12x1。在此,出发点定 为x30y20,第一个孔与此参考 点的距离为20mm,其他的钻 孔相互间的距离也是20mm。 首先执行循环LCYC83加工孔, 然后运行循环LCYC84进行螺 纹切削。钻孔深度为80mm, 攻70mm。
LCYC60循环指令应用
二、相关知识
(四)孔加工循环指令
N10 G0 G54 G71 G17 G90 Tl Dl ;确定工艺参数 N20 S500 M3 y30 x20 z110 ;回到出发点(任意的) N30 R10l=75 R102=2 R103=72 R104=22 ;定义钻孔循环参数 N40 R105=l R107=82 R108=20 R109=10 ;定义钻孔循环参数 N50 R110=30 R111=10 R127=1 ;定义钻孔循环参数 N60 Rl15=83 R116=30 R117=20 R118=20 Rl19=5 R120=90 R121=20 N70 LCYC60 ;调用线性孔循环 N71 M05;
刀具,从而保孔的尺寸精度和表面粗糙度值。
二、相关知识
(三)孔加工刀具的选用
3)钻削速度V、进给量F的选择 F(mm/min)=S(r/min)×f(mm/r) S(r/min)=1000×V/(π×D) (r/min)
钻削进给量F参考值
加工材料
深 径 切削用
刀具直径do(mm)
比
量
灰铸铁
可锻铁、锰铸 铁
l/do
8 10 12 16 20 25 30 35 40
163~229HB (HT100、
HT150)
可锻铸铁 (≤229HB)
数控铣床的程序编制

前角
第4章 数控铣床和加工中心的程序编制
双负前角 双负前角的铣刀通常均采用方形(或长方形)无后 角的刀片,刀具切削刃多(一般为8个),且强度高、抗冲击 性好,适用于铸钢、铸铁的粗加工。由于切屑收缩比大,需 要较大的切削力,因此要求机床具有较大功率和较高刚性。 由于轴向前角为负值,切屑不能自动流出,当切削韧性材料 时易出现积屑瘤和刀具振动。
3) 铣小平面或台阶面时一般采用通用铣刀。
加工台阶面铣刀
第4章 数控铣床和加工中心的程序编制
4) 铣键槽时,为了保证槽的尺寸精度、一般用两刃键槽铣刀。
加工槽类铣刀
第4章 数控铣床和加工中心的程序编制
5)孔加工时,可采用钻头、镗刀等孔加工类刀具。 4.铣刀结构选择 1)平装结构(刀片径向排列)
平装结构铣刀
正负前角(轴向正前角、径向负前角) 这种铣刀综合了 双正前角和双负前角铣刀的优点,轴向正前角有利于切屑的 形成和排出;径向负前角可提高刀刃强度,改善抗冲击性能。 此种铣刀切削平稳,排屑顺利,金属切除率高,适用于大余 量铣削加工。WALTER公司的切向布齿重切削铣刀F2265就 是采用轴向正前角、径向负前角结构的铣刀。
槽铣刀的直径和宽度应根据加工工件尺寸选择,并保证 其切削功率在机床允许的功率范围之内
第4章 数控铣床和加工中心的程序编制
8.铣刀的最大切削深度 不同系列的可转位面铣刀有不同的最大切削深度。最大切
削深度越大的刀具所用刀片的尺寸越大,价格也越高,因此从 节约费用、降低成本的角度考虑,选择刀具时一般应按加工的 最大余量和刀具的最大切削深度选择合适的规格。当然,还需 要考虑机床的额定功率和刚性应能满足刀具使用最大切削深度 时的需要。 9.刀片牌号的选择
数控铣床和加工中心 加工:只需把工件的 基准面A加工好,可 在一次装夹中完成铣 端面、镗
数控铣程序编制教案
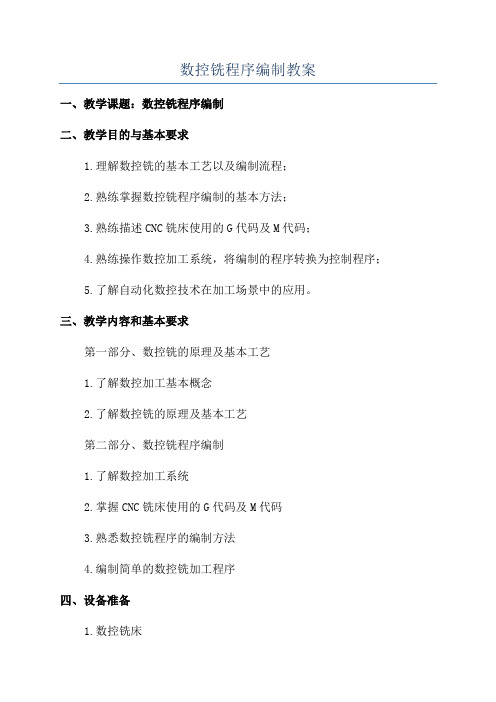
数控铣程序编制教案
一、教学课题:数控铣程序编制
二、教学目的与基本要求
1.理解数控铣的基本工艺以及编制流程;
2.熟练掌握数控铣程序编制的基本方法;
3.熟练描述CNC铣床使用的G代码及M代码;
4.熟练操作数控加工系统,将编制的程序转换为控制程序;
5.了解自动化数控技术在加工场景中的应用。
三、教学内容和基本要求
第一部分、数控铣的原理及基本工艺
1.了解数控加工基本概念
2.了解数控铣的原理及基本工艺
第二部分、数控铣程序编制
1.了解数控加工系统
2.掌握CNC铣床使用的G代码及M代码
3.熟悉数控铣程序的编制方法
4.编制简单的数控铣加工程序
四、设备准备
1.数控铣床
2.光学测量仪
3.加工软件
五、教学步骤
1.向学生介绍数控加工的基本概念,了解数控铣床的原理及基本工艺;
2.演示CNC铣床使用的G代码及M代码,详细讲解数控铣程序的编制
方法;
3.完成简单加工零件,并完成程序调试;
4.通过光学测量仪算出加工精度,精确测量零件大小;
5.讨论总结,引导学生了解自动化数控加工技术在加工场景中的应用
方式。
六、教学考核。
数控铣削加工工艺与编程实例
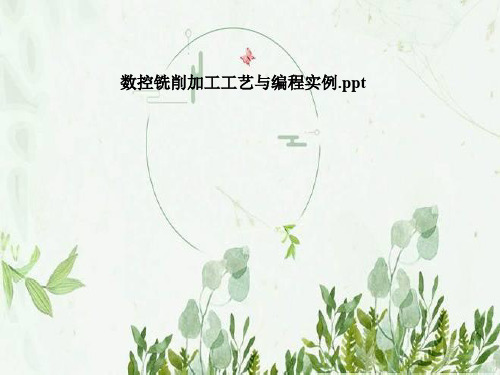
(3)工、量、刃具选择
(4)合理选择切削用量
2.编制参考程序 1)认真阅读零件图,确定工件坐标系。根据工件坐标系 建立原则,X、Y向加工原点选在φ60H7mm孔的中心, Z向加工原点选在B面(不是毛坯表面)。工件加工原点 与设计基准重合,有利于编程计算的方便,且易保证零 件的加工精度。Z向对刀基准面选择底面A,与工件的定 位基准重合,X、Y向对刀基准面可选择φ60H7mm毛坯 孔表面或四个侧面。 2)计算各基点(节点)坐标值。如图3-112所示各圆的 圆心坐标值见表3-32。
子程序:
3.6.4 加工中心零件的编程与操作
图3-105所示为端盖零件,其材料为45钢,毛坯尺寸为 160mm×160mm×19mm。试编写该端盖零件的加工 程序并在XH714加工中心上加工出来。
(1)加工方法 由图3-105可知,该盖板材料为铸铁,故毛坯为铸件,四 个侧面为不加工表面,上下面、四个孔、四个螺纹孔、 直径为φ60mm的孔为加工面,且加工内容都集中在A、 B面上。从定位、工序集中和便于加工考虑,选择A面为 定位基准,并在前道工序中加工好,选择B面及位于B面 上的全部孔在加工中心上一次装夹完成加工。 该盖板零件形状较简单,尺寸较小,四个侧面较光滑, 加工面与非加工面之间的位置精度要求不高,故可选机 用平口钳,以盖板底面A和两个侧面定位,用机用平口 钳的钳口从侧面夹紧。
3)参考程序:数控加工程序单见表3-33。
加工φ160mm中心线上孔的子程序的数控加工程序单见 表3-33。
加工φ100mm中心线上孔的子程序的数控加工程序单见 表3-33。
3.操作步骤及内容 1)机床上电。合上空气开关,按“NC启动”。 2)回参考点。选择“机械回零”方式,按下“循环启动”按钮,完成 回参考点操作。返回零点后,X、Y、Z三轴向负向移动适当距离。 3)刀具安装。按要求将所有刀具安装到刀库,注意刀具号是否正 确。 4)清洁工作台,安装夹具和工件。检查坯料的尺寸,确定工件的 装夹方式(用机用虎钳夹紧)。将机用虎钳清理干净装在干净的工 作台上,通过百分表找正、找平机用虎钳并夹紧,再将工件装正在 机用虎钳上,工件伸出钳口8mm左右。
数控铣加工中心程序的编制教案

干个指令字组成。指令字代表某一信息单元,每个指令字又由字母、数字、
符号组成。如:
O1234;
程序编号
N1 G90G54G00X0Y0;
程序段
N2 S800M03;
程序段
N3 Z100.0
程序段
N4 Z5.0;
程序段
N5 G01Z-10.0F100;
程序段
N6 G41X5.0Y5.0 D1 F200;
家对使用的编号的位数和数值范围将不同,通常用 4 位数字表示,即
“0001”~“9999”,但“8000”~“9999”已被生产厂家使用,不能作为编程号
使用,故编程号为“0001”~“7999”,并在数字前必须给出标识符号“O”。
第二行是一些准备工作,告知数控机床程序编制的方式、工件所在位置、
选用的坐标系等。N1 代表程序段号(简称顺序号),机床加工时并不起作
G90G00Z100.0;/*刀具首先快速移到 Z=100.0mm 高度的位置
X0.Y0.;
/*刀具接着快速定位到工件原点的上方
G00 指令一般在需要将主轴和刀具快速移动时使用,可以同时控制 1~3
轴,即可在 X 或 Y 轴方向移动,也可以在空间作三轴联动快速移动。而刀
具的移动速度又数控系统内部参数设定,在数控机床出厂前已设置完毕,
g代码的说明代码功能g00定位快速进给g43取消刀具长度补偿g01直线插补切削进给g44刀具长度正偏置刀具延长g02圆弧插补顺时针g49刀具长度负偏置刀具缩短g03圆弧插补逆时针g54g59工作坐标系g17xy平面选择g80固定循环取消g18zx平面选择g81钻孔固定循环g19yz平面选择g83深孔钻孔固定循环g40取消刀具半径补偿g90绝对坐标编程方式g41刀具半径左补偿g91相对坐标编程方式g42刀具半径右补偿注
- 1、下载文档前请自行甄别文档内容的完整性,平台不提供额外的编辑、内容补充、找答案等附加服务。
- 2、"仅部分预览"的文档,不可在线预览部分如存在完整性等问题,可反馈申请退款(可完整预览的文档不适用该条件!)。
- 3、如文档侵犯您的权益,请联系客服反馈,我们会尽快为您处理(人工客服工作时间:9:00-18:30)。
2020/10/22
6.确定加工顺序和选择刀具 加工顺序及加工刀具见表2-23。
序号
1 2 3 4 5 7 8 9
10 11
加工顺序
正六边形凸轮廓 4个角的压板槽 圆形凹模内轮廓
4×Φ9孔 Φ12H7孔 钻4×Φ9底孔 钻Φ12H7底孔 扩Φ12H7孔
Φ12H7倒角 铰Φ12H7孔
刀具
Φ16的4 刃平底立
表2-29 六角凸模零件轮廓粗、精加工主程序
2020/10/22
表2-29 六角凸模零件轮廓粗、精加工主程序
主程序
N240 M98 P00010011; N250 G51 X0 Y0 I1 J-1; N260 M98 P00010011; N270 G51 X0 Y0 I-1 J-1; N280 M98 P00010011; N290 G51 X0 Y0 I-1 J1; N300 M98 P00010011; N310 G50 ; N320 G00 Z200; N330 X-5 Y0; N340 Z5; N350 G01 Z0; N360 M98 P00040010; N370 G90 G41 G01 X15 Y0 D01 ;
N380 G03 I-15; N390 G40 G01 X0 Y0; N400 G00 Z200; N410 X-200 Y0; N420 G49;
注释
加工第四象限压板槽; X轴镜像; 加工第一象限压板槽; X、Y轴镜像; 加工第二象限压板槽; Y轴镜像; 加工第三象限压板槽; 取消比例缩放方式; 抬刀; 快速置位到16点上方; 快速下刀置安全平面; 直线插补下刀置Z0平面; 调用铣圆形型腔下刀槽子程序; 绝对输入,直线插补置18点并建立左刀补(粗加 工D01取8.2,精加工理论值8,要实测); 加工整圆; 直线插补置O点并取消半径补偿; 抬刀; 快速置位到换刀点(200,0); 取消长度补偿;
基点序号 4
X坐标值 -28.285
Y坐标值 0 0 0
Y坐标值 28.285
2020/10/22
4.编制程序
编制程序如下表所示。
表2-27 六角凸模零件圆形型腔下刀槽子程序
子程序
O0010; N10 G91 G01 X10 Z-0.5 ; N20 X-10 Z-0.5 ; N30 M99;
注释
Φ16立铣刀铣削六角凸模零件圆形型腔下刀槽子程序; 增量编程,从16点向X轴正方向进给10mm置17点并向Z轴负方向增量进给0.5mm; 从17点向Y轴负方向进给30mm返回16点并向Z轴负方向增量进给0.5mm; 子程序结束;
-40
0
13
19.29
-60
25.98
14
50
-60
-40
15
65
-60
基点序号 16 17 18
X坐标值 -5 5 15
基点序号 X坐标值
0
0
1
-28.285
模具制造技术
Y坐标值 0
-28.285
基点序号 X坐标值 Y坐标值
2
28.285 -28.285
3
28.285 28.285
表2-26 孔位坐标
模具制造技术
表2-28 六角凸模零件右下角压板槽加工子程序
注释
六角凸模零件右下角压板槽加工子程序; 绝对编程,快速置位到10点上方; 下刀置安全平面; 下刀置Z-6.8平面(精铣轮廓理论Z-7,要实测); G54工件坐标系绕点(50,-50)逆时针旋转45°; 直线插补置11点建立左刀补(粗加工D01取8.2,精加工理论值8,要实测); 插补置点12; 插补置点13; 插补置点14; 插补置点15并取消半径补偿; 取消工件坐标系旋转; 抬刀; 快速置位到O点上方; 子程序结束;
换T02号Φ16定心钻; 调用T02号刀正向长度补偿并开冷却液; 钻孔位0中心孔后返回初始平面; 钻孔位1中心孔后返回初始平面; 钻孔位2中心孔后返回初始平面; 钻孔位3中心孔后返回初始平面; 钻孔位4中心孔后返回初始平面; 快速置位到换刀点(200,0); 取消长度补偿; 换T03号Φ9钻头; 调用T03号刀正向长度补偿并开冷却液; 钻孔位0孔后返回初始平面; 钻孔位1孔后返回初始平面; 钻孔位2孔后返回初始平面; 钻孔位3孔后返回初始平面; 钻孔位4孔后返回初始平面; 快速置位到换刀点(200,0); 取消长度补偿;
2.确定编程方案及刀具路径
如图2-68所示,用Φ16立铣刀先从机床坐标系的原点开始快速定 位到1点的上方,快速下刀平面Z=-4,直线插补建立刀具半径补 偿置2点,然后利用极坐标编程法沿3-4-5-6-7-8-3-9点路线铣削, 从9-1点取消刀具半径补偿,在1-3点之间移动刀具中心位置并铣
削整圆去除多余毛坯余量后抬刀移至原点上方;从原点快速定位 10点上方,下刀至Z=-7平面,利用坐标旋转功能直线插补建立刀 具半径补偿置11点,然后沿11-12-13-14点路线铣削,从14-15点 取消刀具半径补偿,利用镜像功能铣削其他3个压板槽,抬刀快速 定位到16点的上方,快速下刀到安全平面Z=5,直线插补下刀到 Z=0平面,在16点和17点之间往复摆动下刀直至Z=-4平面,直线 插补建立刀具半径补偿置18点后加工整圆,从18-0点取消刀具半 径补偿,最后在0点抬刀置Z=200,快速移动到点(-200,0)上方 换刀,然后按照表2-24所示的工艺顺序进行孔系加工。
车间 模具实训基地 背吃刀量 备注 /mm
3.8
0.2
1 4.5 1.4
0.1
共页
第页
2020/10/22
(二)编制零件的数控加工程序
1.建立工件坐标系 在XY平面,把工件坐标系 的原点O建立在工件正中心。 Z轴的原点O在工件上表面。
模具制造技术
图2-68 六角凸模零件坐标系及加工进给路线图
2020/10/22
T01
刀
T02
Φ16定心 钻
T03 Φ9钻头
T04
Φ11.8钻 头
T05 Φ19钻头
T06 Φ12H7铰 刀
批准
零件材料
45
使用设备
VMC-480P3加工中心
主轴转速 /r.min-1
进给速度 /mm.r-1
600
150
700
100
800
70
700
70
300
60
200
40
150
70
年月日
零件图号 10-1004
模具制造技术
2020/10/22
5.确定加工方案 加工方案见表2-22。
表2-22 加工方案
加工部位 正六边形凸轮廓 4个角的压板槽 圆形凹模内轮廓
4×Φ9孔 Φ12H7孔
加工方案
运用极坐标编程
运用坐标旋转功能和镜像功能编程
运用子程序摆动下刀编程
钻中心孔 钻底孔
钻中心孔 钻底孔 扩孔 倒角
铰孔
模具制造技术
模具制造技术
2020/10/22
表2-29 六角凸模零件轮廓粗、精加工主程序
主程序
注释
N430 M06 T02; N440 G43 H02 M08; N450 G98 G81 X0 Y0 Z-9 R5 M03 S800 F70 ; N460 X-28.285 Y-28.285 Z-12; N470 X28.285 ; N480 Y28.285; N490 X-28.285; N500 G00 X-200 Y0; N510 G49; N520 M06 T03; N530 G43 H03 M08; N540 G98 G73 X0 Y0 Z-30 R5 Q5 M03 S700F70 ; N550 X-28.285 Y-28.285 ; N560 X28.285 ; N570 Y28.285; N580 X-28.285; N590 G00 X-200 Y0; N600 G49;
模具制造技术
2020/10/22
3.计算编程尺寸
各孔位坐标如表2-25、 26所示。
图2-69 六角凸模零件孔位坐标
表2-25 基点坐标
基点序号 X坐标值
1
65
2
40
3
25
9
40
10
65
图2-68六角凸模零件加工的进给路线图
Y坐标值 基点序号 X坐标值 Y坐标值
0
11
50
-40
-25.98
12
19.29
模具制造技术
注释
Φ16立铣刀铣六角凸模零件轮廓粗、精加工主程序; 换T01号Φ16立铣刀; 调用T01号刀正向长度补偿并开冷却液; 绝对输入,调用第一工件坐标系,快速置位到1点上方,主轴正转,转速600 r/min(精加工S取700 ); 下刀置Z-3.8平面(精铣轮廓理论Z-4,要实测); 以进给速度150 mm/min直线插补置2点建立右刀补(精加工时F取100,粗加工 D01取8.2,精加工理论值8,要实测); 插补置点3; 极坐标编程,插补置点4; 极坐标编程,插补置点5; 极坐标编程,插补置点6; 极坐标编程,插补置点7; 极坐标编程,插补置点8; 极坐标编程,插补置点3; 取消极坐标编程,插补置点9; 插补置点1并取消半径补偿; 去毛坯周边余量; 去毛坯周边余量; 去毛坯周边余量; 去毛坯周边余量; 去毛坯周边余量; 去毛坯周边余量; 插补置点1; 抬刀; 快速置位到O点上方;
铣刀
Φ16定心 钻
Φ9钻头
Φ11.8钻 头
Φ19钻头 Φ12H7铰
刀
刀具 编号
T01
T02
T03 T04 T05 T06
模具制造技术
7.填写工艺文件
根据上述分析与计算,填写 表2-24数控加工工艺卡片。
2020/10/22
单位名称
工序号
程序编号
O10/ O11/O12